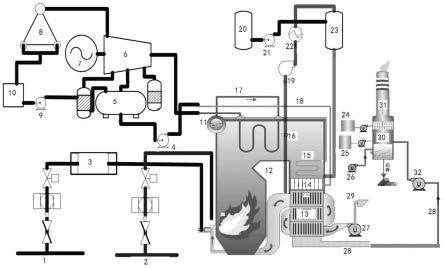
1.本发明涉及一种高效绿色回收利用钢铁工业高炉副产品的工艺,属于钢铁行业能源利用领域。
背景技术:
2.随着社会经济的不断发展,钢铁行业得到了迅猛发展,钢铁行业发展的同时,会产生多种钢铁工业副产品,如高炉煤气、焦炉煤气、转炉煤气、烧结烟气、焦炭显热、但在能源的综合利用特别是二次能源的开发利用方面还存在一定的差距,各种煤气对空排放、焦炭显热排放、烧结烟气乏热排放、饱和余热蒸汽对空排放,这些余热能源的排放,造成热能浪费的同时还会污染环境。其中工业排放是造成空气污染最重要的因素之一,减少工业污染物的排放也成为防治空气污染的重要举措。因此研究探索高效深度回收利用钢铁工业余热能源,是非常有必要的。
3.钢铁企业高炉、焦炉、转炉在生产冶炼过程中产生的高炉煤气、焦炉煤气、转炉煤气,除生产用少部分外,其余的过程很大部分都对空排放掉。近年来随着企业竞争力的提升与环保需求,开发回收这部分余热能源,保护环境技术势在必行。
4.目前,国内很多钢铁企业已经进行了高、焦、转炉煤气的回收利用技术,如燃气蒸汽循环发电、煤气锅炉燃烧回收技术,但现有的煤气锅炉及配套的汽轮发电机组蒸汽参数低,煤气锅炉发电机组热效率仅为23~30%,效率低经济性差;另外,现有煤气利用设备煤气锅炉未设置脱硫脱硝环保设施,不能满足当前超低排放要求,受环保指标制约多。目前在钢铁行业余热能源回收利用工艺技术领域,还未出现成熟、高效又环保的工艺应用技术,影响钢铁企业的可持续绿色发展。
技术实现要素:
5.为了克服上述不足,本发明旨在提供一种高效绿色回收利用钢铁工业高炉副产品的工艺,采用高效、环保的煤气回收利用工艺,将钢铁工业高炉生产过程中产生的高、焦、转炉煤气集中处理回收利用,转化为钢铁企业可以使用的能源,同时减少环境污染,各物质排放满足环保指标且优于超低排放控制标准:烟气排放口颗粒物<5mg/nm3、二氧化硫<35mg/nm3,氮氧化物<50mg/nm3。
6.本发明的技术构思:通过对高、焦、转炉煤气量及煤气品质的长期分析研究,结合现有的煤气处理技术,经过深入的探讨与调研,形成了现有的一套完整高效环保的煤气处理工艺技术,处理钢铁生产冶炼过程中产生的高、焦、转炉煤气,煤气来源:生产过程产生的高炉煤气、转炉煤气和焦炉煤气,除冶炼工艺生产自用外,剩余的富余煤气。煤气供给温度:夏季 30℃,冬季 15℃;煤气管网供给压力:8~10kpa;煤气含尘量:≤10mg/nm
³
。
7.本发明提供的一种高效绿色回收利用钢铁工业高炉副产品的工艺,包括以下内容:针对钢铁企业生产冶炼过程中产生的高、焦、转炉煤气,结合煤气流量与热值,采用相应
的组合工艺;80mw机组主蒸汽参数设计参数(17.5mpa、571℃)及相应的工艺关键控制指标;在煤气锅炉采用超低排脱硝脱硫环保技术。
8.本发明根据煤气成分和热值,结合国家标准、相关技术要求,通过研究与调研,采用“260t/h 超高温亚临界中间一次再热煤气锅炉 80mw小容量超高温亚临界高参数抽凝直接空冷汽轮机 静态励磁发电机组 煤气锅炉scr脱硝 石灰石-石膏湿法脱硫 高效除雾器除尘”工艺,其中煤气系统首次采用“双快切煤气冗余可靠阻断 煤气预加热”新型技术,最终实现高、焦、转炉煤气高效绿色回收利用。
9.本发明提供了一种高效绿色回收利用钢铁工业高炉副产品的工艺,包括余热能源回收工艺和高温烟气处理工艺,余热能源回收工艺包括煤气回收利用单元、蒸汽回收利用单元和发电单元;高温烟气处理工艺包括高温烟气的scr脱硝单元、湿法脱硫及硫化物处理单元、烟尘处理单元;钢铁企业生产过程中产生的高、焦、转炉煤气进入煤气母管,经过煤气加热器后进入煤气锅炉,通过燃烧向煤气锅炉锅膛喷射混合好的煤气,经点火装置后,在炉膛内燃烧放出来的热量,加热煤气锅炉受热面,以此来加热锅炉内的水到571℃蒸汽,进入蒸汽发电机组,推动叶片做功,带动发电机发电;煤气燃烧后产生的烟气经锅炉尾部的scr脱硝系统,去除烟气中氮氧化物,再进入湿法脱硫净化处理烟气中的硫后,进入三层高效除雾器,将脱硫后烟气中带灰尘雾气去除,经过除雾器净化后的烟气达到环保要求排出。
10.上述工艺中,所述煤气回收利用单元具体为:煤气回收利用单元包括煤气母管、煤气加热器和锅炉本体和辅助设备。煤气锅炉中炉膛、锅筒、燃烧器,水冷壁、过热器、省煤器、空气预热器、炉墙等构成生产蒸汽的核心部分。
11.本发明使用的原料为高炉、焦炉、转炉冶炼后产生的副产品,即生产使用后富余的高、焦、转炉煤气, 项目采用超高温亚临界、中间一次再热、平衡通风、单汽包、自然循环、全悬吊全钢架结构,紧身封闭布置的煤气锅炉,各煤气通过煤气管网进入煤气锅炉,通过燃烧产生蒸汽。蒸汽平均每小时的蒸发量260吨,最大连续蒸发量可达276吨,过热蒸汽压力可达17.5mpa,过热蒸汽温度可达571℃。
12.煤气加热器和锅炉连接的煤气管道上设置了快切阀、电动蝶阀、电动插板阀和手动阀门,为了保证锅炉事故时煤气的快速切断,高炉煤气总管快切阀采用液动执行机构,其它快切阀采用气动执行机构。为防止停炉检修时煤气泄漏,在煤气管道母管上还设置了盲板阀。另外,在煤气管道上还设置放散装置,便于吹扫、放散和防爆。
13.锅炉燃烧器为分层布置,可单独使用任何一支燃烧器,且燃烧稳定。锅炉燃烧器采用低氮燃烧器。锅炉前、后墙分别布置 3 层燃烧器,每层 2 只,共 12 支燃烧器。下面 2 层燃烧器为高转炉混合煤气燃烧器,最上面一层为焦炉煤气燃烧器,焦炉煤气燃烧器上方设置有燃尽风。 每组燃烧器前煤气支管设置快切阀,燃烧器火嘴支管依次为电动调节阀和两级气动快切阀。
14.上述工艺中,所述蒸汽回收利用单元和发电单元具体为:蒸汽回收利用单元包括蒸汽轮机;发电机和蒸汽轮机同轴连接;由燃气锅炉产生的蒸汽送入80mw超高温亚临界、中间一次再热、直接空冷、抽凝式汽轮机发电机组,将回收
煤气产生的蒸汽用于发电,为钢铁行业补给电量,充分回收冶炼产生的富余余热能源。
15.蒸汽轮机结构型式为双缸单排汽,高压部分采用双层缸结构,中低压部分采用前部高温区双层缸、整体上合缸的结构,由低压前缸、低压内缸和后汽缸组成,低压前缸、后汽缸通过垂直法兰螺栓连接为一体。高压主汽调节阀卧式布置在高压缸两侧,中压联合汽阀布置于低压前缸两侧。机组总长15m。高压通流部分设计为反向流动,高压进汽口布置在高压缸机尾区域,中压进汽口布置在低压缸前部,是整个机组工作温度最高的部位。来自锅炉过热器的新蒸汽通过2根主蒸汽管进入高压主汽调节阀,再经4根φ159x26高压主汽管和装在高压内外缸之间的4个高压进汽管分别从上下方向进入高压内缸中的喷嘴室,然后进入高压通流部分。再热蒸汽通过2根热段再热汽管进入中压联合汽阀,然后经2根φ430x55再热主汽管从低压前缸下半进入中低压通流部分。中低压部分共有16个压力级,蒸汽做功后,由后汽缸排汽口向下排入排气装置。
16.进一步地,在钢厂小容量的机组上使用电力行业中大容量机组(600mw超临界高温级及以上发电机组)等级的参数,特别是超高温(571℃)技术,打破了传统小型机组参数低、效率低的模式,大大提高了煤气的使用效率和机组的循环热效率。
17.本发明采用小容量高参数等级工艺,具有以下一些优点:(1)煤气高效深度利用,使用效率高。
18.(2)机组循环热效率高。
19.上述工艺中,高温烟气的scr脱硝(氮氧化物处理)单元的具体流程为:scr脱硝单元一部分设置在锅炉烟道中,一部分在炉外单独设置。scr炉内部包括催化剂、喷氨格栅、氨气喷射装置;炉外部分包括热解炉、增压风机、电加热及尿素溶液自备与输送系统。
20.脱硝系统采取选择性催化还原(scr)法来达到去除烟气中 no
x
的目的。scr反应器布置在锅炉两组省煤器之间,利用尿素溶液热解后通过喷管格栅喷入炉内(将尿素溶液经热解后,生成氨气,氨气进入炉内,进行脱硝),与设置锅炉两侧的scr催化剂进行反应,进而实现烟气脱硝的目的。化学反应原理:c0(nh2)2→
nh3 hcno(异氰氨)4no 4nh3 o2→
4n2 6h2o6no2 8nh3→
7n2 12h2o副作用方程式:so2 1/2o2→
so3nh3 so3 h2o
→
nh4hso4反应器的催化剂层进出口位置装有一个差压变送器,用于测量催化剂进出口压降。该压降不超过新装催化剂设计值的120%。本工程脱硝装置新装催化剂压降设计值为每层300pa,两层600pa,当压降超过720pa时,系统将发出差压高位报警信号。
21.scr 吹灰器用于清除催化剂表面的积灰。本工程采用声波吹灰方式。吹灰频率可根据反应器催化剂层间的压降变化情况进行合理设定。声波吹灰器的吹灰介质为压缩空气。 反应器设计 2 层催化剂,每层催化剂设置 3 台声波吹灰器,一台机组共 6 台声波吹灰器及一套压缩空气管路系统,声波吹灰器布置在反应器外侧墙和后墙。
22.scr催化剂为蜂窝式催化剂,安装在 scr 反应器内,催化剂进口和出口运行温度
不得超过 430
°
c(平均温度)。如果催化剂进口或出口的平均温度低于 260
°
c,停止氨喷入。入口或出口各设有3个测温计, 如果入口或出口的任何一个温度测量值低于 255
°
c,停止氨喷入。
23.上述工艺中,湿法脱硫及硫化物处理单元的具体流程为:锅炉炉膛内燃烧生成的高温烟气,经屏式过热器、高温过热器、再热器、低温过热器、高温级省煤器、scr 脱硝装置、低温级省煤器、空气预热器及煤气加热器后,经烟道由 2 台引风机送入脱硫装置,最后通过烟囱排到大气中。
24.本项目烟气脱硫工程,采用石灰石-石膏湿法烟气脱硫工艺。本系统脱硫有四层喷淋层,用来分层喷射浆液,达到分布浆液的目的;实际操作中可根据so2浓度,灵活调节喷淋层运行数量,单塔设置,烟囱和脱硫塔合一,锅炉烟气从引风机出口平烟道接入到脱硫塔,经过4层脱硫浆液循环喷淋层,将烟气中的so2吸收,形成亚硫酸钙。
25.本项目在煤气回收系统采用石灰石-石膏湿法烟气脱硫工艺,具有以下特点:(1)对煤气变化的适应性强。
26.(2)首次在煤气回收系统采用该脱硫工艺,对同类钢铁企业具有推广价值。
27.(3)so2排放浓度不大于20mg/nm
³
,脱硫效率大于92.4%。
28.上述工艺中,烟尘处理单元的具体流程为:在脱硫塔顶部设有三层高效除雾器;锅炉炉膛内燃烧生成的高温烟气,经湿法脱硫净化处理后的烟气中,含有大量的雾气,雾气中含有灰尘,进入三层高效除雾器,将脱硫后烟气中带灰尘雾气去除,经过除雾器净化后的烟气达到环保要求,由塔顶标高 60 米,直径φ3700mm的烟囱排出。
29.本发明主要创新点如下:(1)采用了双快切煤气冗余可靠阻断技术由于煤气腐蚀易造成阀门不严,经过综合研判和多年的实践运行经验,采用煤气系统快切冗余可靠切断技术,通过在高炉煤气、焦炉煤气系统总管设置大型快速切断装置,即蝶阀 盲板阀快速切断装置,然后在各火嘴部位设置两道快速切断阀门的方式,实现紧急故障情况下可以快速切断总管煤气和快速切断单个火嘴的双重快速切断,而且实现检修环节的有效可靠切断,确保煤气系统任何情况下能够完全可靠切断,实现设备本质化安全,使运行和检修环节安全有保障。解决了单个快切不严或者故障拒动的的问题。
30.采用双快切煤气冗余可靠阻断技术,具有以下优点:
①
煤气在故障情况下,能够快速阻断,安全系数高;
②
设备本质化安全提升,降低了高危作业人员中毒的风险。
31.(2)采用“煤气预加热”技术通过在尾部烟道设置煤气加热器,依靠自身的循环动力,用尾部烟气进行传热,将煤气由常温加热到140℃后进入炉膛燃烧,不仅降低了排烟温度,提高了锅炉效率,而且减少燃烧器区域的热量吸收,稳定了燃烧,同时还可以大大减缓煤气加热器后煤气管道的腐蚀速率,大大延长了煤气管道的使用寿命。
32.采用热管传热原理,实现烟气对煤气的加热。热管是一种具有高传热性能传热元件,它通过密闭真空管壳内工作介质的相变潜热来传递热量,具体如下:分离式热管换热器是利用工质的汽化—凝结来传递热量,所不同的只是将受热段
与放热段分离开来,用蒸汽上升管和冷凝液下降管将它们连接,组成了具有热管传热效应结构形式。
33.采用煤气预加热技术,具有以下优点:
①
排烟温度降低,锅炉效率提高;
②
燃烧稳定, 减缓煤气管道的腐蚀,延长煤气管道使用寿命。
34.本发明的有益效果:(1)本发明采用高效环保煤气回收处理工艺技术,将钢铁企业中各种煤气深度高效综合处理,循环热效率提升13%,年度发电量5.76亿kwh,较常规机组增加发电量1.9亿kwh。
35.(2)冬季可利用机组空冷乏汽为居民供热,满足太原市居民100万平方米的供热。
36.(3)该工艺技术回收钢铁企业余热能源的同时,消除污染,环保排放数据优于超低排放指标,氮氧化物排放小于30mg/nm3以下,二氧化硫排放小于20 mg/nm3以下,颗粒物排放3mg/nm3以下,达到政府的环保要求。
附图说明
37.图1为本发明的工艺流程图。
38.图中:1为高炉煤气母管,2为焦炉煤气母管,3为煤气加热器,4为给水泵,5为除氧器,6为蒸汽轮机,7为发电机,8为空冷岛,9为凝结水泵,10为排气装置,11为汽包,12为锅炉,13为空气预热器,14为scr催化剂,15为省煤器,16为过热器,17为饱和蒸汽管,18为给水管,19为增压风机,20为尿素罐,21为尿素输送泵,22为电加热装置,23为热解炉,24为工艺水箱,25为石灰石浆液罐,26为氧化风机,27为送风机,28为烟气,29为吸风口,30为脱硫塔,31为烟囱,32为引风机。
具体实施方式
39.下面通过实施例来进一步说明本发明,但不局限于以下实施例。
40.实施例1:本发明提供的高效绿色回收利用钢铁工业高炉副产品的工艺,包括余热能源回收工艺和高温烟气处理工艺,余热能源回收工艺包括煤气回收利用单元、蒸汽回收利用单元和发电单元;高温烟气处理工艺包括高温烟气的scr脱硝单元、湿法脱硫及硫化物处理单元、烟尘处理单元;钢铁企业生产过程中产生的高、焦、转炉煤气进入煤气母管,经过煤气加热器后进入煤气锅炉,通过燃烧向煤气锅炉锅膛喷射混合好的煤气,经点火装置后,在炉膛内燃烧放出来的热量,加热煤气锅炉受热面,以此来将锅炉内的水加热到571℃蒸汽,进入蒸汽发电机组,推动叶片做功,带动发电机发电;煤气燃烧后产生的烟气经锅炉尾部的scr脱硝单元,去除烟气中氮氧化物,再进入脱硫塔,经湿法脱硫净化处理烟气中的硫后进入三层高效除雾器,将脱硫后烟气中带灰尘雾气去除,经过除雾器净化后的烟气达到环保要求排出。
41.图1示出了本发明的工艺流程。结合附图1对该工艺具体描述如下:所述煤气回收利用单元具体为:
ꢀ
煤气回收利用单元包括煤气母管(对应图中的高炉煤气母管1和焦炉煤气母管2)、煤气加热器3和锅炉本体和辅助设备;煤气锅炉12中炉膛、锅筒、燃烧器、水冷壁、过热器、省煤器15、空气预热器13、炉墙构成生产蒸汽的核心部分;锅炉燃烧器为分层布置,锅炉燃烧器采用低氮燃烧器,锅炉前、后墙分别布置三层燃烧器,每层 2 只,共 12 支燃烧器,下面两层燃烧器为高转炉混合煤气燃烧器,最上面一层为焦炉煤气燃烧器,焦炉煤气燃烧器上方设置有燃尽风;本发明的原料为高炉、焦炉、转炉冶炼后产生的副产品,各煤气通过煤气管网进入煤气锅炉12,通过燃烧产生蒸汽;蒸汽平均每小时的蒸发量260吨,最大连续蒸发量可达276吨,过热蒸汽压力达17.5mpa,过热蒸汽温度达571℃。
42.进一步地,煤气加热器3和锅炉12连接的煤气管道上设置了快速切断装置,即蝶阀 盲板阀快速切断装置;快速切断装置包括快切阀、电动蝶阀、电动插板阀和手动阀门,高炉煤气总管快切阀采用液动执行机构;为防止停炉检修时煤气泄漏,在煤气管道母管上还设置了盲板阀;每组锅炉燃烧器前煤气支管设置快切阀,燃烧器火嘴支管依次为电动调节阀和两级气动快切阀。
43.所述蒸汽回收利用单元和发电单元具体为:蒸汽回收利用单元包括蒸汽轮机6;发电机7和蒸汽轮机6同轴连接;由燃气锅炉12产生的蒸汽送入80mw超高温亚临界、中间一次再热、直接空冷、抽凝式汽轮机发电机组,将回收煤气产生的蒸汽用于发电,为钢铁行业补给电量,充分回收冶炼产生的富余余热能源;蒸汽轮机6结构型式为双缸单排汽,高压部分采用双层缸结构,中低压部分采用前部高温区双层缸、整体上合缸的结构,由低压前缸、低压内缸和后汽缸组成,低压前缸、后汽缸通过垂直法兰螺栓连接为一体;高压主汽调节阀卧式布置在高压缸两侧,中压联合汽阀布置于低压前缸两侧;高压通流部分设计为反向流动,高压进汽口布置在高压缸机尾区域,中压进汽口布置在低压缸前部,是整个机组工作温度最高的部位;来自锅炉过热器的新蒸汽通过2根主蒸汽管进入高压主汽调节阀,再经4根φ159x26高压主汽管和装在高压内外缸之间的4个高压进汽管分别从上下方向进入高压内缸中的喷嘴室,然后进入高压通流部分;再热蒸汽通过2根热段再热汽管进入中压联合汽阀,然后经2根φ430x55再热主汽管从低压前缸下半进入中低压通流部分;中低压部分共有16个压力级,蒸汽做功后,由后汽缸排汽口向下排入排气装置10。
44.高温烟气的scr脱硝单元的具体流程为:scr脱硝单元一部分设置在锅炉烟道中,一部分在炉外单独设置;scr炉内部包括scr催化剂14、喷氨格栅、氨气喷射装置;炉外部分包括热解炉23、增压风机19、电加热装置22及尿素溶液自备与输送系统;脱硝单元采取选择性催化还原scr法来达到去除烟气中 no
x
的目的;scr反应器布置在锅炉两组省煤器之间,利用尿素溶液热解后通过喷管格栅喷入炉内(将尿素溶液经热解后,生成氨气,氨气进入炉内,进行脱硝),与设置在锅炉两侧的scr催化剂进行反应,进而实现烟气脱硝的目的。
45.进一步地,scr反应器的催化剂层进出口位置装有一个差压变送器,用于测量催化剂进出口压降;该压降不超过新装催化剂设计值的120%;脱硝装置新装催化剂压降设计值为每层300pa,两层600pa,当压降超过720pa时,系统将发出差压高位报警信号;
scr 吹灰器用于清除催化剂表面的积灰;采用声波吹灰方式;反应器设计 2 层催化剂,每层催化剂设置 3 台声波吹灰器,一台机组共 6 台声波吹灰器及一套压缩空气管路系统,声波吹灰器布置在反应器外侧墙和后墙;所述催化剂为蜂窝式催化剂,安装在 scr 反应器内,催化剂进口和出口运行温度不得超过430℃。
46.湿法脱硫及硫化物处理单元的具体流程为:锅炉炉膛内燃烧生成的高温烟气,经屏式过热器、高温过热器、再热器、低温过热器、高温级省煤器、scr 脱硝装置、低温级省煤器、空气预热器及煤气加热器后,经烟道由 2 台引风机送入脱硫装置,最后通过烟囱排到大气中。
47.具体地,烟气脱硫采用石灰石-石膏湿法烟气脱硫工艺;脱硫有四层喷淋层,用来分层喷射浆液,达到分布浆液的目的;实际操作中根据so2浓度灵活调节喷淋层运行数量,单塔设置,烟囱和脱硫塔合一,锅炉烟气从引风机出口平烟道接入到脱硫塔,经过4层脱硫浆液循环喷淋层,将烟气中的so2吸收,形成亚硫酸钙。
48.烟尘处理单元的具体流程为:在脱硫塔30顶部设有三层高效除雾器;锅炉炉膛内燃烧生成的高温烟气,经湿法脱硫净化处理后的烟气中,含有大量的雾气,雾气中含有灰尘,进入三层高效除雾器,将脱硫后烟气中带灰尘雾气去除,经过除雾器净化后的烟气达到环保要求,由塔顶标高 60 米,直径φ3700mm的烟囱31排出。
49.下面通过具体的实施过程来具体说明本发明的技术方案:本发明技术方案在太钢80mw机组顺利完成168小时试运。
50.本实施例提供的参数如下:煤气成分和热值如下表所示:本项目锅炉烟气参数:煤气回收利用设施参数:
蒸汽回收利用设施参数:氮氧化物处理设施参数:
硫化物处理设施参数:机组自168试运以来,运行稳定,各项性能指标均满足要求。
51.1) 烟气排放口颗粒物、二氧化硫、氮氧化物实测排放浓度范围分别为“nd(未检出)—1.4g/nm
3”、“nd(未检出)”、“14-20mg/nm
3”, 满足设计和排放要求。
52.2) 机组在考核工况下,试验负荷为80mw,纯烧高炉煤气设计工况下,对应锅炉热效率90.76%,煤气加热器排烟温度修正到140℃后对应锅炉热效率为90.94%,高于设计保证值90.00%,满足设计要求。
53.3) 在额定负荷工况(3vwo)下,试验电功率为81680.7kw,热耗率为8453.27 kj/
kwh,经系统及参数修正后,修正后电功率为91416.3 kw,修正后热耗率为8276.25 kj/kwh,修正后汽耗率为3.004 kg/kwh,试验时发电煤气单耗为2.817m3/ kwh,修正后发电煤气单耗为2.695m3/ kwh,供电煤气单耗为3.006 m3/ kwh。满足设计要求。
54.4) 在最大出力工况(4vwo)下,试验电功率为84900kw,试验主汽流量(dcs)为242100 kg/h,排汽压力为22.27kpa,经排汽压力修正后,电功率为86285 kw,满足机组最大出力负荷的要求。
55.5) 在额定工况和90%负荷情况下,全厂热效率分别为:38.7%和38.13%。
56.采用该工艺技术,将钢铁企业生产中产生的高炉煤气、焦炉煤气、转炉煤气进行综合处理,充分回收钢铁生产中的余热能源,将这部分余热能源转化为电能,最终排出物各环保指标满足且优于超低排放控制标准。
57.本实施例采用“260t/h 超高温亚临界中间一次再热煤气锅炉 80mw小容量超高温亚临界高参数抽凝直接空冷汽轮机 静态励磁发电机组 煤气锅炉scr脱硝 石灰石-石膏湿法脱硫 高效除雾器除尘”工艺,其中煤气系统首次采用“双快切煤气冗余可靠阻断 煤气预加热”新型技术,将钢铁企业高炉、焦炉、转炉冶炼过程中产生的余热能源高效绿色回收利用,转化为电能,供钢铁行业自用电,同时还利用空冷乏汽进行居民供热,满足城镇居民100万平方米的供热。
[0058] 本工艺技术应用后,煤气利用的安全可靠性提高;机组的循环热效率较现有机组的循环热效率提升13%,年度发电量较常规机组增加发电量1.9亿kwh;最重要的是环保排放数据优于超低排放指标,氮氧化物可控制小于20 mg/nm3以下,二氧化硫可控制小于20 mg/nm3以下,颗粒物排放可控制4mg/nm3以下;冬季可利用空冷乏汽进行居民供热,满足城镇居民100万平方米的供热。该工艺技术经济效益、环保效、社会效益显著。本技术在同行业内具有较广泛的推广意义。
再多了解一些
本文用于创业者技术爱好者查询,仅供学习研究,如用于商业用途,请联系技术所有人。