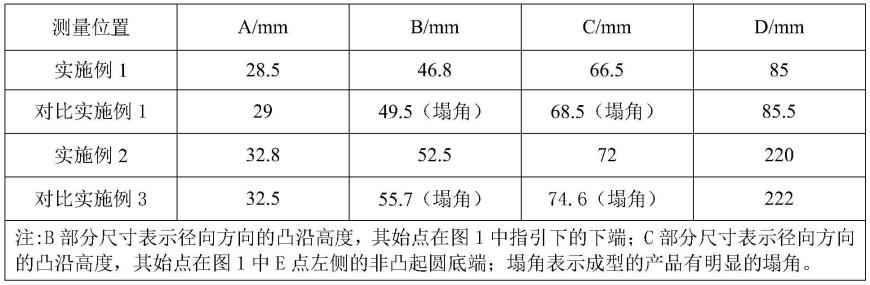
1.本发明属于精密塑性成形技术领域,具体涉及一种异形轴构件的多向异步加载镦锻成形方法。
背景技术:
2.异形轴(复杂)构件多作为设备或器械的主承力关重零部件使用,承受多种环境下的复杂应力,对性能要求很高,材料涉及各类结构钢、铝合金等多个领域。其传统制备方法一般是采用大直径棒料机械加工,但这种方法材料浪费巨大,效率极低,构件性能差,且对于大尺寸复杂构件无法批量生产;另一种方式则是采用卧式挤压机进行挤压,但这种方式一般针对回转类规则构件,对复杂的不规则构件,需要先采用卧式挤压机制坯,再采用模锻工艺进行多道次成形来制备,工序长、工艺复杂、设备要求高,关键点控制难度大,效率低下且制造周期长。
3.对于大尺寸(长度大于1300mm或者直径大于200mm)的异形轴类复杂构件(如40crnimo钢异形轴,具有间隔布置的两个非标环形凸起,两个非标环形凸起之间具有连接段,该连接段的轴线偏离异形轴构件主体轴线,且二者轴线平行),通常只能采用铸造工艺,但实际生产过程中,考虑到铸造构件性能不高的难题,一般是先通过铸造工艺制坯,再采用大吨位模锻锤进行锻打,锻出大致形状,最后通过机械加工完成制备。然而,通过该工艺做出的零件由于塑性变形量不大,其内部组织仍保留有铸态组织(其内部晶粒度通常为5级,刚好能够达到合格要求),所得构件性能依然不理想。
技术实现要素:
4.本发明目的在于提供一种异形轴构件的多向异步加载镦锻成形方法,至少能够解决现有方法制备的异形轴构件中心部位晶粒度级数低的问题。
5.为了实现上述目的,本发明采用如下所述技术方案。
6.一种异形轴构件的多向异步加载镦锻成形方法,其特征在于,步骤包括:步骤1,下料,将结构钢棒料锯切成坯料;步骤2,加热,将步骤1所得坯料加热至1000℃并保温40
±
10分钟;步骤3,将加热后的坯料放入模具中,合模,采用加载设备对坯料按照设定的加载曲线进行异步加载镦锻成形,并将成形后的构件放入空气中冷却;其中,加载设备包括位于入模具型腔上部的轴向左冲头、径向冲头和轴向右冲头,径向冲头下方设置有顶杆;加载曲线满足:在第0-2秒内,轴向左冲头、轴向右冲头的加载速度分别从零升至6mm/s,然后以6mm/s的加载速度保持9-10秒,接下来的2秒内,将两个冲头的加载速度降至零;在第2-4秒内,径向冲头的加载速度从零升至2mm/s;在第4-6秒内,径向冲头的加载速度保持2mm/s;在第6-7秒内,径向冲头的加载速度从2mm/s升至4mm/s;在第7-9秒内,径向冲头的加载速度保持4mm/s;在第9-11秒内,径向冲头的加载速度从4mm/s升至5mm/s,然后然后
以5mm/s的加载速度保持2秒,再将径向冲头的加载速度降至零。
7.进一步地,步骤3中,异步加载镦锻成形后的构件先保压30
±
5秒,然后放入空气中冷却。
8.作为优选方案,加载曲线满足:在第0-1秒内,轴向左冲头、轴向右冲头的加载速度分别从零升至6mm/s,然后以6mm/s的加载速度保持9秒,接下来的1秒内,将两个冲头的加载速度降至零;在第3-4秒内,径向冲头的加载速度从零升至2mm/s;在第4-6秒内,径向冲头的加载速度保持2mm/s;在第6-7秒内,径向冲头的加载速度从2mm/s升至4mm/s;在第7-9秒内,径向冲头的加载速度保持4mm/s;在第9-10秒内,径向冲头的加载速度从4mm/s升至5mm/s;在第11-12秒内,将径向冲头的加载速度降至零。
9.为进一步提高异形轴构件的成型质量,轴向左冲头、轴向右冲头均采用带电加热丝的冲头,加载过程中保持冲头的温度为400
±
10℃。
10.在本发明中,所述异形轴构件具有间隔布置的两个非标环形凸起,两个非标环形凸起之间具有连接段,该连接段的轴线偏离所述异形轴构件轴线,且二者轴线平行。
11.作为另一优选方案,加载曲线满足:在第0-1秒内,中心冲头的加载速度分别从零升至6mm/s,然后以6mm/s的加载速度保持1秒,接下来的1秒内,将两个冲头的加载速度降至零,然后在接下来的1秒内继续将中心冲头的加载速度分别从零升至6mm/s,然后以6mm/s的加载速度保持6秒,接下来的1秒内,将两个中心冲头的加载速度降至零;在第1-2秒内,轴向左冲头、轴向右冲头的加载速度分别从零升至6mm/s,然后以6mm/s的加载速度保持8秒,接下来的1秒内,将两个冲头的加载速度降至零;在第3-4秒内,径向冲头的加载速度从零升至2mm/s;在第4-6秒内,径向冲头的加载速度保持2mm/s;在第6-7秒内,径向冲头的加载速度从2mm/s升至4mm/s;在第7-9秒内,径向冲头的加载速度保持4mm/s;在第9-10秒内,径向冲头的加载速度从4mm/s升至5mm/s;在第11-12秒内,将径向冲头的加载速度降至零。
12.有益效果:本发明以简便的工艺就能成形出大尺寸的异形轴类复杂构件,制得的构件具有力学性能高、内部质量好,特别是解决了现有方法制备的异形轴类构件中心部位晶粒度级数低的问题,且具有材料利用率高、生产周期短、生产成本低、易于操作等优点。
附图说明
图1为实施例1中制得的异形轴构件示意图(主向和侧向视图);图2为实施例1中异步加载路线示意图;图3为实施例1中制备异形轴构件的状态示意图;图4为实施例2中制备异形轴构件的状态示意图;图5为实施例2中异步加载路线示意图;图6为实施例2中制得的异形轴构件示意图,其形状同实施例1中异形轴构件,但尺寸不同。
具体实施方式
13.以下实施例的说明只是用于帮助理解本发明的原理及其核心思想,并非对本发明
保护范围的限定。应当指出,对于本技术领域普通技术人员来说,在不脱离本发明原理的前提下,针对本发明进行的改进也落入本发明权利要求的保护范围内。实施例1
14.一种长轴(异性轴)构件的多向异步加载镦锻成形方法,该异形轴构件如图1所示,具有间隔布置的两个非标环形凸起,两个非标环形凸起之间具有连接段,该连接段的轴线偏离所述异形轴构件主体轴线,且二者轴线平行该方法的步骤包括:步骤1,下料,将的40crnimo结构钢棒料锯切成的坯料;步骤2,加热,将步骤1所得坯料加热至1000℃并保温40分钟;步骤3,将加热后的坯料放入模具中,合模,采用加载设备对坯料按照设定的加载曲线进行异步加载镦锻成形,异步加载镦锻成形后的构件先保压30
±
5秒,然后放入空气中冷却;其中,加载设备包括位于入模具型腔上部的轴向左冲头1、径向冲头3和轴向右冲头5,径向冲头3下方设置有顶杆4;加载过程中,如图3所示,编号2表示坯料,箭头表示加载方向,坯料中部区域穿过轴向左冲头1、轴向右冲头5的中间孔内,轴向左冲头和轴向右冲头均采用带电加热丝的冲头,加载过程中始终保持冲头的温度为400
±
5℃;其中,加载曲线/路线如图2所示,具体为:在第0-1秒内,轴向左冲头、轴向右冲头的加载速度分别从零升至6mm/s,然后以6mm/s的加载速度保持9秒,接下来的1秒内,将两个冲头的加载速度降至零;在第3-4秒内,径向冲头的加载速度从零升至2mm/s;在第4-6秒内,径向冲头的加载速度保持2mm/s;在第6-7秒内,径向冲头的加载速度从2mm/s升至4mm/s;在第7-9秒内,径向冲头的加载速度保持4mm/s;在第9-10秒内,径向冲头的加载速度从4mm/s升至5mm/s;在第11-12秒内,将径向冲头的加载速度降至零。实施例2
15.一种短轴(异性轴)构件的多向异步加载镦锻成形方法,该异形轴构件如图6所示,具有间隔布置的两个非标环形凸起,两个非标环形凸起之间具有连接段,该连接段的轴线偏离所述形轴构件主体轴线,且二者轴线平行该方法的步骤包括:步骤1,下料,将的40crnimo结构钢棒料锯切成的坯料;步骤2,加热,将步骤1所得坯料加热至1000℃并保温45分钟;步骤3,将加热后的坯料放入模具中,合模,采用加载设备对坯料按照设定的加载曲线进行异步加载镦锻成形,异步加载镦锻成形后的构件先保压30
±
5秒,然后放入空气中冷却;其中,加载设备包括位于入模具型腔上部的轴向左冲头1(简称左冲头)、径向冲头3(又称之为上冲头)和轴向右冲头5(简称右冲头),轴向左冲头1和轴向右冲头5中部分别设置有中心冲头6,径向冲头3下方设置有顶杆4;加载过程中,如图4所示,编号2表示坯料,箭头表示加载方向,坯料的左端部完全位于轴向左冲头1的型腔内,坯料的右端部完全位于轴向右冲头5的型腔内;轴向左冲头1和轴向右冲头5均采用带电加热丝的冲头,加载过程中始终保持冲头的温度为400
±
5℃;其中,加载曲线/路线如图5所示,具体为:
在第0-1秒内,中心冲头的加载速度分别从零升至6mm/s,然后以6mm/s的加载速度保持1秒,接下来的1秒内,将两个冲头的加载速度降至零,然后在接下来的1秒内继续将中心冲头的加载速度分别从零升至6mm/s,然后以6mm/s的加载速度保持6秒,接下来的1秒内,将两个中心冲头的加载速度降至零;在第1-2秒内,轴向左冲头、轴向右冲头的加载速度分别从零升至6mm/s,然后以6mm/s的加载速度保持8秒,接下来的1秒内,将两个冲头的加载速度降至零;在第3-4秒内,径向冲头的加载速度从零升至2mm/s;在第4-6秒内,径向冲头的加载速度保持2mm/s;在第6-7秒内,径向冲头的加载速度从2mm/s升至4mm/s;在第7-9秒内,径向冲头的加载速度保持4mm/s;在第9-10秒内,径向冲头的加载速度从4mm/s升至5mm/s;在第11-12秒内,将径向冲头的加载速度降至零。
16.对比实施例1:采用传统/常规模锻工艺制备相同材料和相同规格的前述40crnimo异形轴构件。
17.对比实施例2:采用传统/常规模锻工艺制备相同材料和相同规格的前述40crnimo异形轴构件。
18.将实施例1、实施例2所得异形轴构件清洗、喷砂后进行测量,其尺寸测量结果如表1所示,测量位置结合图1所示;采用传统热模锻工艺(对比实施例1、对比实施例2)制备相同规格的异形轴构件,其尺寸见表1。表1实施例1及对比实施例尺寸测量结果
19.采用实施例1中方案制备40crnimo异形轴构件时,加载设备的镦锻成形力实测为1200kn,采用实施例2中方案制备40crnimo异形轴构件时,加载设备的镦锻成形力实测为1680kn,加载过程中型腔充料饱满且便于加载;而对比实施例1中模锻成形力实测为2000kn,对比实施例2中模锻成形力实测为2500kn,且仍然有充型不满的情况。
20.实施例1所得异形轴构件的晶粒度不小于8级(其中,e部位为8级、f部位为8.5级、g部位为8级),满足高精密锻件的技术要求;而对比实施例1中所得异形轴构件的晶粒度均值为5.5级(其中,e部位为6级、f部位为5.5级、g部位为5级)。实施例2所得异形轴构件的晶粒度不小于8.5级(其中,e部位为8.5级、f部位为9级、g部位为9级),满足高精密锻件的技术要求;而对比实施例2中所得异形轴构件的晶粒度均值为5级(其中,e部位为5级、f部位为5级、g部位为5级)。相比之下,采用本发明方案能够一次性加热成形出无缺陷的异形轴构件,加载过程中的成形力小,所得异形轴构件的内部组织、合格率得到大幅提升。
21.采用本发明方案,能够顺利、快速地成形出轴类复杂的难变形构件,所得构件内部
组织和质量好,加载过程中的成形力小,且具有材料利用率高和加工效率高的优点;采用本发明方案,可大幅缩短异形轴类复杂构件的加工周期,简化生产工序(实施例1中方案的加工周期约4小时,对比实施例1中的加工周期约16小时),可操作强,成本低(采用实施例1、实施例2中方案,总加工制造费用分别约500元,适用于大规模生产;而采用对比实施例1、对比实施例2中方案,总加工制造费用分别约2400元)。
再多了解一些
本文用于创业者技术爱好者查询,仅供学习研究,如用于商业用途,请联系技术所有人。