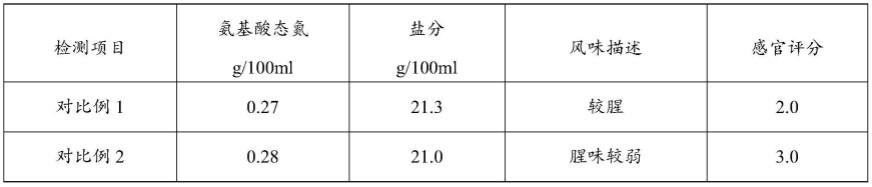
1.本发明涉及食品技术领域,尤其涉及一种海鲜汁的联合脱腥方法、海鲜汁。
背景技术:
2.现有食品除腥技术大部分从生产工艺后端进行发力,即对已有腥味物质进行后处理,以此降低海鲜汁中的腥味物质含量或者将腥味物质转化为其他腥味阈值较高的物质。例如:
①
利用不同种酵母、乳酸菌、曲霉等进行纯种发酵或者复合发酵,如申请号为202010266347.6的中国专利公开了一种利用耐盐酵母菌、戊糖片球菌进行复合发酵脱腥的方式,脱腥效果明显;
②
利用活性炭、活性白土、大孔树脂、离子交换树脂、壳聚糖等对腥味物质进行物理吸附,如申请号为201510986533.6的中国专利公开了一种利用活性炭进行鱼油脱腥的方式;
③
利用酒精、食醋、茶叶、紫苏等天然产物提取液、香辛料等对腥味物质进行掩盖,如申请号为202010162353.7的中国专利公开了一种利用食醋及紫苏等组成的脱腥液对罗非鱼加工副产物进行脱腥的方式;
④
利用环状糊精、卡拉胶、羧甲基纤维素、多孔淀粉等对腥味物质进行包埋;
⑤
利用以上技术中的2~3种进行联合脱腥,从而实现较好的脱腥效果,如申请号为201711479834.5的中国专利公开了一种利用酵母等菌种发酵联合环糊精包埋对鲣鱼蒸煮液进行联合脱腥的方式。
3.上述第
①
种利用菌种发酵的方式脱腥,因为发酵过程较难控制,过程中会产生大量副产物,容易改变产品本身的香型及产品特性;上述第
②
种活性炭等物理脱腥的方式在脱腥的过程中也会对产品本身的香气造成影响,另外也会造成氨基酸态氮等营养物质大量损失;上述第
③
种掩盖脱腥的方式容易在产品体系中引入配方外物质,易残留,后续去除较为困难,同时因为香辛料等物质风味较为浓郁,也会对产品固有的感官风味造成较大影响;而上述第
④
种包埋脱腥的方式可能因为载体或者包埋壁材等在产品的加工以及后续运输、贮存的过程中稳定性降低,从而导致腥味包埋效果减弱甚至丧失,影响产品品质。
技术实现要素:
4.本发明的目的在于克服上述现有技术的不足之处而提供一种海鲜汁的联合脱腥方法、海鲜汁,所述联合脱腥方法从海鲜汁的生产前端切入,利用定向酶解以及腥味物质本身的物料特性,在不改变产品香型、不造成产品营养损失、不引入其他配方外物质的基础上,从根本上降低产品腥味,提升产品品质。
5.为实现上述目的,本发明所采取的技术方案为:
6.一种海鲜汁的联合脱腥方法,所述联合脱腥方法包括如下步骤:
7.(1)将海鲜与水混合,进行打浆,得到海鲜浆a;
8.(2)在所述海鲜浆a中加入食盐,溶解均匀后得到海鲜浆b;
9.(3)在所述海鲜浆b中加入内切蛋白酶、风味蛋白酶进行酶解,得到海鲜汁c;
10.(4)对所述海鲜汁c进行灭酶,得到海鲜汁d;
11.(5)在所述海鲜汁d中加入食盐,溶解均匀后得到海鲜汁e。
12.本发明在酶解前首先对海鲜浆进行溶盐处理,除了可促进腥味物质析出外,还可以抑制酶解过程中微生物的增殖,降低三甲胺等腥味物质在酶解过程中的产生以及积累。此外,本发明通过选用内切蛋白酶和风味蛋白酶共同对海鲜浆进行酶解处理,可以切断肽链内部和末端的肽键,提高蛋白质水解效率,同时可以大幅减少苦味肽的产生。随后,再次添加食盐,除了可以促进腥味物质的进一步析出,还可以彻底抑制微生物的活动,减少后续加工、储存以及运输过程中腥味物质的产生。本发明通过上述方法制备出的海鲜汁腥味弱,同时还具有愉悦的风味。
13.所述海鲜包括但不限于贻贝、蛤蜊、牡蛎、虾、鱼等。
14.优选地,所述步骤(1)中,海鲜与水的质量比为(1~2):(1~4)。
15.优选地,所述步骤(2)中,以海鲜浆a的质量计,食盐的质量分数为2%~6%。
16.食盐的含量过高会抑制酶的活性,含量过低则难以促进腥味物质的析出,本发明通过实验发现,控制食盐的含量在上述范围内可以最大程度地降低海鲜中的腥味物质,达到良好的脱腥效果。
17.优选地,所述步骤(3)中,以海鲜浆b的质量计,内切蛋白酶的质量分数为0.5%~2%,风味蛋白酶的质量分数为0.01%~0.5%;所述酶解的温度为40℃~60℃,酶解的时间为2h~6h。
18.优选地,所述内切蛋白酶为动物水解酶、复合蛋白酶、木瓜蛋白酶中任意两种的复配物。复配物相比其他蛋白酶制剂酶解产生的腥臭味物质普遍更少,水解液具有较愉悦的风味。
19.进一步优选地,所述复配物中两种成分的质量比为(1~4):(1~4)。本发明通过实验发现,选用上述复配内切蛋白酶和风味蛋白酶进行酶解处理可以进一步提升酶解效率,降低苦味,优化海鲜汁的风味,并且还能保留较多的营养成分。
20.优选地,所述步骤(4)中,灭酶条件为:在80℃~100℃下蒸煮15min~40min。
21.优选地,所述步骤(5)中,以海鲜汁d的质量计,食盐的质量分数为10%~20%。
22.优选地,所述步骤(5)结束后,还包括步骤(6):对海鲜汁e进行真空脱腥,所述真空脱腥方法为:在-0.8bar~-0.4bar条件下处理40min~80min。以上述条件进行真空脱腥可以高效地脱除海鲜汁中的腥味。
23.通过对海鲜汁进行真空脱腥,可进一步有效去除海鲜汁中的腥臭味。
24.优选地,所述步骤(6)结束后,进行杀菌处理,在80~100℃条件下杀菌1~5h。
25.此外,本发明还公开了一种海鲜汁,所述海鲜汁采用上述联合脱腥方法制备所得。
26.相比于现有技术,本发明的有益效果为:
27.本发明从海鲜汁的生产前端进行脱腥处理,利用定向酶解及二次溶盐处理对海鲜汁进行联合脱腥,制备出的海鲜汁的腥味弱,并且具有愉悦的风味,脱腥效率高;同时,通过对酶的种类进行筛选,进一步降低了产品的腥味,并且还能保证产品中仍然含有丰富的营养物质。
具体实施方式
28.为更好地说明本发明的目的、技术方案和优点,下面将结合具体实施例对本发明作进一步说明。
29.下述实施例中的原料,如未作具体说明,均为购买所得。
30.动物水解酶:酶活:23万u/g;
31.木瓜蛋白酶:酶活:50万u/g;
32.复合蛋白酶:酶活:30万u/g;所述复合蛋白酶为菠萝蛋白酶、胰蛋白酶以2:1的质量比复合所得;
33.风味蛋白酶:酶活:2万u/g;所述风味蛋白酶是由米曲霉菌株发酵,经提纯所得;
34.中性蛋白酶:酶活:20万u/g;
35.实施例及对比例中使用的食盐、牡蛎均为同种物质。
36.实施例1
37.本发明所述海鲜汁的联合脱腥方法的一种实施例,本实施例所述联合脱腥方法包括如下步骤:
38.(1)将牡蛎和水按1:2的质量比进行打浆,得到海鲜浆a;
39.(2)在海鲜浆a中加入食盐,食盐的含量为海鲜浆a质量的4%,溶解均匀后得到海鲜浆b;
40.(3)在海鲜浆b中加入内切蛋白酶和风味蛋白酶,在50℃下酶解2h,得到海鲜汁c;以海鲜浆b的质量计,内切蛋白酶的质量分数为1%,风味蛋白酶的质量分数为0.25%;所述内切蛋白酶为木瓜蛋白酶和动物水解酶质量比为1:1的复配物;
41.(4)在90℃下对海鲜汁c进行蒸煮灭酶,得到海鲜汁d;蒸煮时间为30min;
42.(5)在所述海鲜汁d中加入食盐,食盐的含量为海鲜汁d质量的16%,搅拌均匀后得到海鲜汁e;
43.(6)将海鲜汁e加入真空罐中,在-0.6bar条件下进行真空脱腥,时间为60min;
44.(7)对真空脱腥后的海鲜汁进行杀菌处理,在90℃下保温3h,然后进行灌装。
45.实施例2
46.本发明所述海鲜汁的联合脱腥方法的一种实施例,本实施例所述联合脱腥方法包括如下步骤:
47.(1)将牡蛎和水按1:2的质量比进行打浆,得到海鲜浆a;
48.(2)在海鲜浆a中加入食盐,食盐的含量为海鲜浆a质量的2%,溶解均匀后得到海鲜浆b;
49.(3)在海鲜浆b中加入内切蛋白酶和风味蛋白酶,在40℃下酶解6h,得到海鲜汁c;以海鲜浆b的质量计,内切蛋白酶的质量分数为0.5%,风味蛋白酶的质量分数为0.5%;所述内切蛋白酶为复合蛋白酶和动物水解酶质量比为4:1的复配物;
50.(4)在80℃下对海鲜汁c进行蒸煮灭酶,得到海鲜汁d;蒸煮时间为40min;
51.(5)在所述海鲜汁d中加入食盐,食盐的含量为海鲜汁d质量的20%,搅拌均匀后得到海鲜汁e;
52.(6)将海鲜汁e加入真空罐中,在-0.8bar条件下进行真空脱腥,时间为40min;
53.(7)对真空脱腥后的海鲜汁进行杀菌处理,在80℃下保温5h,然后进行灌装。
54.实施例3
55.本发明所述海鲜汁的联合脱腥方法的一种实施例,本实施例所述联合脱腥方法包括如下步骤:
56.(1)将牡蛎和水按1:2的质量比进行打浆,得到海鲜浆a;
57.(2)在海鲜浆a中加入食盐,食盐的含量为海鲜浆a质量的6%,溶解均匀后得到海鲜浆b;
58.(3)在海鲜浆b中加入内切蛋白酶和风味蛋白酶,在60℃下酶解6h,得到海鲜汁c;以海鲜浆b的质量计,内切蛋白酶的质量分数为2%,风味蛋白酶的质量分数为0.01%;所述内切蛋白酶为复合蛋白酶和木瓜蛋白酶质量比为1:4的复配物;
59.(4)在100℃下对海鲜汁c进行蒸煮灭酶,得到海鲜汁d;蒸煮时间为15min;
60.(5)在所述海鲜汁d中加入食盐,食盐的含量为海鲜汁d质量的10%,搅拌均匀后得到海鲜汁e;
61.(6)将海鲜汁e加入真空罐中,在-0.4bar条件下进行真空脱腥,时间为80min;
62.(7)对真空脱腥后的海鲜汁进行杀菌处理,在100℃下保温1h,然后进行灌装。
63.实施例4
64.本发明所述海鲜汁的联合脱腥方法的一种实施例,本实施例所述联合脱腥方法包括如下步骤:
65.(1)将牡蛎和水按1:2的质量比进行打浆,得到海鲜浆a;
66.(2)在海鲜浆a中加入食盐,食盐的含量为海鲜浆a质量的2%,溶解均匀后得到海鲜浆b;
67.(3)在海鲜浆b中加入内切蛋白酶和风味蛋白酶,在40℃下酶解6h,得到海鲜汁c;以海鲜浆b的质量计,内切蛋白酶的质量分数为0.5%,风味蛋白酶的质量分数为0.5%;所述内切蛋白酶为木瓜蛋白酶;
68.(4)在80℃下对海鲜汁c进行蒸煮灭酶,得到海鲜汁d;蒸煮时间为40min;
69.(5)在所述海鲜汁d中加入食盐,食盐的含量为海鲜汁d质量的20%,搅拌均匀后得到海鲜汁e;
70.(6)将海鲜汁e加入真空罐中,在-0.8bar条件下进行真空脱腥,时间为40min;
71.(7)对真空脱腥后的海鲜汁进行杀菌处理,在80℃下保温5h,然后进行灌装。
72.实施例5
73.本发明所述海鲜汁的联合脱腥方法的一种实施例,本实施例所述联合脱腥方法包括如下步骤:
74.(1)将牡蛎和水按1:2的质量比进行打浆,得到海鲜浆a;
75.(2)在海鲜浆a中加入食盐,食盐的含量为海鲜浆a质量的8%,溶解均匀后得到海鲜浆b;
76.(3)在海鲜浆b中加入内切蛋白酶和风味蛋白酶,在40℃下酶解6h,得到海鲜汁c;以海鲜浆b的质量计,内切蛋白酶的质量分数为0.5%,风味蛋白酶的质量分数为0.5%;所述内切蛋白酶为复合蛋白酶和动物水解酶质量比为4:1的复配物;
77.(4)在80℃下对海鲜汁c进行蒸煮灭酶,得到海鲜汁d;蒸煮时间为40min;
78.(5)在所述海鲜汁d中加入食盐,食盐的含量为海鲜汁d质量的14%,搅拌均匀后得到海鲜汁e;
79.(6)将海鲜汁e加入真空罐中,在-0.8bar条件下进行真空脱腥,时间为40min;
80.(7)对真空脱腥后的海鲜汁进行杀菌处理,在80℃下保温5h,然后进行灌装。
81.对比例1
82.一种海鲜汁的联合脱腥方法,本方法包括如下步骤:
83.(1)将牡蛎和水按1:2的质量比进行打浆,得到海鲜浆a;
84.(2)在海鲜浆a中加入内切蛋白酶和风味蛋白酶,在50℃下酶解2h,得到海鲜汁b;以海鲜浆a的质量计,内切蛋白酶的质量分数为1%,风味蛋白酶的质量分数为0.25%;所述内切蛋白酶为中性蛋白酶;
85.(3)在90℃下对海鲜汁b进行蒸煮灭酶,得到海鲜汁c;蒸煮时间为30min;
86.(4)在所述海鲜汁c中加入食盐,食盐的含量为海鲜汁c质量的20%,搅拌均匀后得到海鲜汁d;
87.(5)海鲜汁d进行杀菌处理,在90℃下保温3h,然后进行灌装。
88.对比例2
89.一种海鲜汁的脱腥方法的一种实施例,本方法包括如下步骤:
90.(1)将牡蛎和水按1:2的质量比进行打浆,得到海鲜浆a;
91.(2)在海鲜浆a中加入内切蛋白酶和风味蛋白酶,在50℃下酶解2h,得到海鲜汁b;以海鲜浆a的质量计,内切蛋白酶的质量分数为1%,风味蛋白酶的质量分数为0.25%;所述内切蛋白酶为木瓜蛋白酶;
92.(3)在90℃下对海鲜汁b进行蒸煮灭酶,得到海鲜汁c;蒸煮时间为30min;
93.(4)在所述海鲜汁c中加入食盐,食盐的含量为海鲜汁c质量的20%,搅拌均匀后得到海鲜汁d;
94.(5)对海鲜汁d进行杀菌处理,在90℃下保温3h,然后进行灌装。
95.对比例3
96.一种海鲜汁的脱腥方法,本方法包括如下步骤:
97.(1)将牡蛎和水按1:2的质量比进行打浆,得到海鲜浆a;
98.(2)在海鲜浆a中加入内切蛋白酶和风味蛋白酶,在50℃下酶解2h,得到海鲜汁b;以海鲜浆a的质量计,内切蛋白酶的质量分数为1%,风味蛋白酶的质量分数为0.25%;所述内切蛋白酶为木瓜蛋白酶和动物水解酶质量比为1:1的复配物;
99.(3)在90℃下对海鲜汁b进行蒸煮灭酶,得到海鲜汁c;蒸煮时间为30min;
100.(4)在所述海鲜汁c中加入食盐,食盐的含量为海鲜汁c质量的20%,搅拌均匀后得到海鲜汁d;
101.(5)对海鲜汁d进行杀菌处理,在90℃下保温3h,然后进行灌装。
102.对比例4
103.一种海鲜汁的脱腥方法,本方法包括如下步骤:
104.(1)将牡蛎和水按1:2的质量比进行打浆,得到海鲜浆a;
105.(2)在海鲜浆a中加入内切蛋白酶和风味蛋白酶,在50℃下酶解2h,得到海鲜汁b;以海鲜浆a的质量计,内切蛋白酶的质量分数为1%,风味蛋白酶的质量分数为0.25%;所述内切蛋白酶为木瓜蛋白酶和动物水解酶质量比为1:1的复配物;
106.(3)在90℃下对海鲜汁b进行蒸煮灭酶,得到海鲜汁c;蒸煮时间为30min;
107.(4)在所述海鲜汁c中加入食盐,食盐的含量为海鲜汁c质量的20%,搅拌均匀后得到海鲜汁d;
108.(5)将海鲜汁d加入真空罐中,在-0.6bar条件下进行真空脱腥,时间为60min;
109.(6)对真空脱腥后的海鲜汁进行杀菌处理,在90℃下保温3h,然后进行灌装。
110.对比例5
111.一种海鲜汁的脱腥方法,本方法包括如下步骤:
112.(1)将牡蛎和水按1:2的质量比进行打浆,得到海鲜浆a;
113.(2)在海鲜浆a中加入食盐,食盐的含量为海鲜浆a质量的4%,溶解均匀后得到海鲜浆b;
114.(3)在海鲜浆b中加入内切蛋白酶和风味蛋白酶,在50℃下酶解2h,得到海鲜汁c;以海鲜浆b的质量计,内切蛋白酶的质量分数为1%,风味蛋白酶的质量分数为0.25%;所述内切蛋白酶为木瓜蛋白酶和动物水解酶质量比为1:1的复配物;
115.(4)在90℃下对海鲜汁c进行蒸煮灭酶,得到海鲜汁d;蒸煮时间为30min;
116.(5)在所述海鲜汁d中加入食盐,食盐的含量为海鲜汁d质量的16%,搅拌均匀后得到海鲜汁e;
117.(6)对海鲜汁e进行杀菌处理,在90℃下保温3h,然后进行灌装。
118.对比例6
119.一种海鲜汁的脱腥方法,所述方法包括如下步骤:
120.(1)将牡蛎和水按1:2的质量比进行打浆,得到海鲜浆a;
121.(2)在海鲜浆a中加入食盐,食盐的含量为海鲜浆a质量的2%,溶解均匀后得到海鲜浆b;
122.(3)在海鲜浆b中加入内切蛋白酶,在40℃下酶解6h,得到海鲜汁c;以海鲜浆b的质量计,内切蛋白酶的质量分数为0.5%;所述内切蛋白酶为木瓜蛋白酶;
123.(4)在海鲜汁c中加入风味蛋白酶,在40℃下酶解6h,得到海鲜汁d;以海鲜汁c的质量计,风味蛋白酶的质量分数为0.5%。
124.(5)在90℃下对海鲜汁d进行蒸煮灭酶,得到海鲜汁e;蒸煮时间为40min;
125.(6)在所述海鲜汁e中加入食盐,食盐的含量为海鲜汁e质量的20%,搅拌均匀后得到海鲜汁f;
126.(7)将海鲜汁f加入真空罐中,在-0.8bar条件下进行真空脱腥,时间为40min;
127.(8)对真空脱腥后的海鲜汁进行杀菌处理,在80℃下保温5h,然后进行灌装。
128.对实施例及对比例制备的海鲜汁进行性能测试。感官鉴评小组由10个小组成员(均为长期从事感官鉴评的专业人员,年龄25~35岁)组成。感官鉴评室的温度控制在25
±
1℃。评价样品时采用评分法,从0分到5分,0分表示产品腥味重,5分表示产品腥味很弱,风味愉悦,测试结果如表1所示。
129.表1
130.[0131][0132]
由表1可知,以实施例1~5所述脱腥方法处理后的海鲜汁基本无腥味,同时仍然含有丰富的营养物质。对比例1未进行一次溶盐以及真空脱腥,并且使用的内切蛋白酶为中性蛋白酶,脱腥效果较差,制备的海鲜汁仍然存在较重的腥味。对比例2~3未进行一次溶盐以及真空脱腥,仍然可以闻到一定的腥味。对比例4未进行一次溶盐,腥味去除效率低于本发明,仍然可以闻到细微的腥味。对比例5未进行真空脱腥,腥味去除效果相对较差,处理后的海鲜汁还存在微弱的腥味。对比例6分别以内切蛋白酶和风味蛋白酶进行去腥,其去腥工艺流程更为复杂,并且去腥效果不如本发明。
[0133]
此外,对比实施例2与实施例4的处理效果可以发现,当内切蛋白酶为两种酶复配的情况下,海鲜汁中的营养物质的含量明显更高。对比实施例2与实施例5的处理效果可以发现,溶盐处理时,盐含量会对海鲜汁中营养物质的含量产生较大的影响,在一次溶盐时食盐的质量分数为2%~6%、二次溶盐时食盐的质量分数为10%~20%的情况下,处理后的海鲜汁既无明显腥味,也含有较丰富的营养物质。
[0134]
最后所应当说明的是,以上实施例仅用以说明本发明的技术方案而非对本发明保护范围的限制,尽管参照较佳实施例对本发明作了详细说明,本领域的普通技术人员应当理解,可以对本发明的技术方案进行修改或者等同替换,但并不脱离本发明技术方案的实质和范围。
再多了解一些
本文用于创业者技术爱好者查询,仅供学习研究,如用于商业用途,请联系技术所有人。