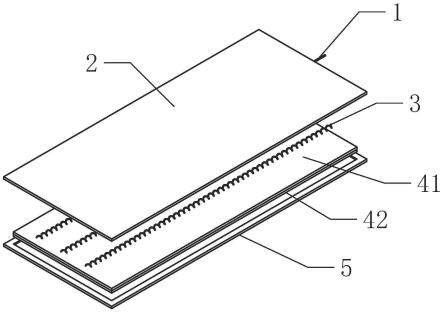
1.本发明涉及均热板技术领域,尤其涉及一种螺旋形支撑柱-吸液芯一体烧结均热板及其制备方法。
背景技术:
2.随着5g技术的快速普及,个人pc,移动设备等向着小型化,集成化发展。这些设备的高速运行带来了严重的散热问题。同时led屏的使用,导致大面积散热需求不断增加。均热板是一种利用内部工作流体相变驱动的被动式散热装置,目前已广泛应用于手机、电脑、电池热管理等各个行业。
3.相比传统的热管,均热板结构上通常由外壳、吸液芯、支撑柱和注液管组成,其内填充一定量的液体工质。在工作过程中,均热板蒸发器不断吸收热源的放出热量,使得内部的液体工质蒸发,然后通过压力差,蒸汽流向冷凝器,蒸汽在冷凝器遇冷放热凝结成液体。最后通过吸液芯提供强大的毛细力将液体引流到蒸发器,此过程不断循环。整个过程不需要外力驱动,这使得均热板被广泛的使用在各个行业。相比传统的热管只能通过一维传热,均热板是一种高效的二维传热设备,这使得它的均温性非常好,更大面积的冷凝器能更快速的转移热源放出的热量,保证电子元器件的稳定运行。
4.常见的均热板外壳一般由导热系数较高的铜和铝加工而成,既保证了较好的传热特性又保证了均热板的结构强度。吸液芯一般由金属粉末烧结、沟槽加工或丝网加工而成。金属粉末烧结吸液芯一般毛细力较大但渗透率较小,沟槽或丝网吸液芯渗透率较大但毛细力较差,为了提高吸液芯的毛细力,现在主要吸液芯由多种工艺复合加工而成。支撑柱主要防止均热板在工作时压力变化而变形,材料和外壳一般相同。液体工质主要由去离子水、甲醇、乙醇等组成。
5.目前均热板按照内腔结构主要可分为上下分层结构和间距结构。其中上下分层结构需要单独的支撑柱来保证均热板的正常运行。而间距结构吸液芯同时承担了毛细驱动作用和支撑作用,因此不需要单独设计支撑柱结构,但间距结构使得大量的蒸汽只能沿着吸液芯的排列方向流动,传热方式主要以一维传热为主。而上下分层结构在支撑柱的优化下拥有更好的均温性。随着均热板厚度的降低,支撑柱对蒸汽压降的影响越大。平衡支撑效应和蒸汽压降的主要方法是减小支撑柱的直径和间距。常见的支撑柱形状有圆形,方形,菱形。支撑柱排列方式有顺序排列,交叉排列等。相比顺序排列交叉排列对蒸汽压降的影响更大。支撑柱形状对蒸汽压降的影响大小顺序为:菱形》方形》圆形。虽然圆形支撑柱能够满足较高的均热板散热需求,但是这些支撑柱主要以刻蚀,冲压等工艺在下壳板加工成型为主,目前支撑柱的高度和直径普遍小于1mm,所需工艺精度较高,难度较大,而且现有的支撑柱引起的通道阻力较大。
技术实现要素:
6.针对现有技术的不足,本发明提供了一种螺旋形支撑柱-吸液芯一体烧结均热板
及其制备方法。
7.本发明在均热板内腔使用了上下分层结构,使得均热板更好的发挥出二维传热的优势,均热板的均温性更好。支撑柱设计成螺旋结构,不仅保证了均热板工作时的结构稳定性,同时降低了蒸汽流动阻力。支撑柱-吸液芯一体烧结技术降低了工艺技术要求,同时螺旋支撑柱外表面同时与上壳板和吸液芯相切,形成近零度角,起到了引流作用,可更快的将冷凝液体引流回蒸发器。均热板的整个上壳板的外表面直接作为冷凝器,增大了冷凝受冷面积,加快了蒸汽的冷凝速度,提高了整个相变传热过程。
8.本发明的技术方案如下:一种螺旋形支撑柱-吸液芯一体烧结均热板,包括充液管、上壳板、支撑柱、复合吸液芯和下壳板,所述支撑柱为多条螺旋支撑柱,螺旋支撑柱与复合吸液芯通过一体烧结工艺将螺旋支撑柱固定在复合吸液芯上,制成螺旋形支撑柱-吸液芯一体结构。
9.作为优选,所述螺旋支撑柱的排列方式为横向、纵向或者沿对角布置;螺旋支撑柱占均热板蒸汽通道横截面积的3%-10%。
10.作为优选,所述螺旋支撑柱由细铜丝通过绕簧工艺制成螺旋结构,所述螺旋支撑柱的外径等于均热板蒸汽通道厚度,细铜丝的丝径不大于蒸汽通道厚度的30%,相邻细铜丝的节距不小于外径。
11.作为优选,所述螺旋形支撑柱与吸液芯一体烧结是指:在烧结复合吸液芯的同时,将制成的多个螺旋支撑柱铺设在待烧结的吸液芯上层,一同放入石墨模具中850-950℃烧结,使得支撑柱与吸液芯成为一体结构;相邻所述螺旋支撑柱的间距为螺旋支撑柱外径的2倍-10倍。
12.作为优选,所述复合吸液芯为拥有多种孔隙率的吸液芯复合烧结而成,所述螺旋形支撑柱-吸液芯一体结构经过二次烧结工艺固定在壳板上。
13.作为优选,所述复合吸液芯为上下分层结构,上层采用孔隙率100-300目的铜网,下层采用孔隙率80-150微米的铜粉末烧结泡沫铜,或者上层使用较大铜粉直径的铜粉,下层使用较小铜粉(80-150微米)直径的铜粉复合烧结,上层选用的铜粉直径比下层使用的铜粉直径至少大20μm。
14.作为优选,所述均热板蒸汽通道厚度不小于0.3mm,复合吸液芯的截面积占均热板内部空腔截面积的40%-80%(空腔为上壳板和下壳板形成的密闭空间,截面积比是按照图2侧边视图来计算)。
15.作为优选,所述上壳板和下壳板由铜片通过冲压、刻蚀或者cnc加工形成中心凹槽,边缘凸起结构;
16.所述上壳板和下壳板密封形成的空腔内填充有液体工质,填充的液体工质体积占复合吸液芯空隙体积的60-90%。
17.作为优选,所述二次烧结工艺是指将烧结好的螺旋形支撑柱-吸液芯一体结构与上壳板、下壳板组装在一起,再次放入烧结炉中850-950℃烧结,将支撑柱和吸液芯与上壳板、下壳板固定贴合。
18.本发明第二方面,还提供所述螺旋形支撑柱-吸液芯一体烧结均热板的制备方法,所述方法包括以下步骤:
19.s1.通过冲压或者cnc加工上、下壳板,上壳板的一个边上留充液管焊接口;
20.s2.选取细铜丝缠绕成螺旋状,再按照所需外径、节距和长度拉伸成螺旋支撑柱;
21.s3.将螺旋支撑柱、铜网和铜粉置于乙醇中超声清洗,然后用去离子水冲洗干净;
22.s4.将清洗好的螺旋支撑柱、铜网和铜粉放入干燥箱中烘干取出,先在石墨模具里铺设一层铜粉,再将铜网铺在铜粉之上,然后按照排列需求将螺旋支撑柱铺在铜网之上,最后放于烧结炉中于氮气氢气保护气氛下850-950℃烧结,待自然冷却后取出,得到螺旋形支撑柱-吸液芯一体结构;
23.s5.将螺旋形支撑柱-吸液芯一体结构置于乙醇中超声清洗,然后用去离子水冲洗干净,置于干燥箱中干燥;
24.s6.将加工好的上、下壳板置于乙醇中超声清洗,然后用去离子水冲洗干净,置于干燥箱中干燥;
25.s7.将螺旋形支撑柱-吸液芯一体结构铺设在下壳板凹槽内,组装好上壳板,然后放入石墨模具,压紧石墨模具,再放在烧结炉中于氮气氢气保护气氛下850-950℃烧结,待自然冷却后取出;
26.s8.在上壳板预留的充液口焊接充液管,再将上下壳板的接触边缘密封焊接;
27.s9.将充液管连接真空泵抽取内腔空气,抽完后关闭真空泵,再从充液管注入一定量液体工质,待液体工质完全进入内腔,再次打开真空泵抽取真空,最后将多余充液管用冷焊机焊断密封,即得所述均热板。
28.本发明提供的多螺旋形支撑柱-吸液芯一体烧结均热板及其制备方法,通过支撑柱的优化设计,减小了蒸汽通道阻力,尤其螺旋结构设计降低了蒸汽由中心向四周流动阻力,同时保证了均热在工作时结构的稳定性,在螺旋支撑柱的加工制造时只需将铜丝缠绕拉伸,降低了工艺加工的难度。通过一体烧结工艺,将支撑柱固定在吸液芯上。与在上壳板和下壳板通过刻蚀、激光加工、cnc加工支撑柱相比,支撑柱与吸液芯一体烧结技术大大降低了设备需求与工艺成本,此种加工工艺只需在烧结炉中烧结吸液芯时一体烧结成型,同时保证了一定的机械强度。
29.作为进一步优选,所述细铜丝的丝径为0.08-0.13mm,缠绕拉伸得到外径0.6-1.0mm、节距1.5-2.5mm的螺旋支撑柱。
30.与现有技术相比,本发明的有益效果在于:本发明中设计的螺旋形支撑柱降低了蒸汽的流动阻力,使得蒸汽能快速流向冷凝器冷凝,加快了相变传热过程。
31.本发明设计的支撑柱吸液芯一体烧结工艺,可在烧结吸液芯的同时将螺旋支撑柱铺设在吸液芯上一同烧结固定,与在壳板上加工支撑柱相比,降低了工艺要求,缩减了生产流程。
32.本发明设计的多孔隙率吸液芯结构,优化了液体流道,保证吸液芯有较大的毛细力的同时提高了吸液芯的渗透率,尤其是在靠近蒸汽通道的一侧增大了孔隙率,有利于蒸汽快速排出,流向蒸汽通道。
33.本发明的二次烧结工艺可以减小吸液芯与壳板之间的热阻,同时将支撑柱与壳板固定在一起,增加了支撑柱的支撑作用,有效防止均热板发生鼓包,凹陷现象。
附图说明
34.图1为本发明实施例1中均热板爆炸图;
35.图2为本发明实施例1中均热板结构正视剖面图;
36.图3为本发明实施例1中均热板结构左视剖面图;
37.图4为本发明所述支撑柱等间距横向排列俯视图;
38.图5为本发明实施案例2中支撑柱由中心向边缘排列的俯视图;
39.图6不同类型支撑柱压降对比图;
40.图7不同充液率下sscvc3总热阻和热端温度:(a)不同充液率下的总热阻,(b)不同充液率下热端温度;
41.图8不同充液率下sscvc4总热阻和热端温度:(a)不同充液率下的总热阻,(b)不同充液率下热端温度;
42.图9不同充液率下sscvc5总热阻和热端温度:(a)不同充液率下的总热阻,(b)不同充液率下热端温度;
43.图10不同充液率下sscvc6总热阻和热端温度:(a)不同充液率下的总热阻,(b)不同充液率下热端温度;
44.图11不同支撑柱数量均热板的总热阻和热端温度:(a)不同支撑柱数量均热板的总热阻,(b)不同支撑柱数量均热板的热端温度;
45.图中标记:1-充液管,2-上壳板,3-螺旋支撑柱,4-复合吸液芯,41-铜网,42-铜粉烧结泡沫铜,5-下壳板。
具体实施方式
46.下面对本发明的具体实施方式作进一步的说明,但以下实施案例仅为了更好地解释本发明,实施案例不是本发明的全部,本发明并不局限于以下技术方案。
47.实施例1
48.(1)壳板加工:通过将0.2mm厚的铜片冲压加工得到槽深0.5mm,槽边长100
×
40mm长方形上壳板1、下壳板5,在凸起边缘留2mm宽的焊接带,再裁剪多余部分,再在上壳板边上压出直径约为0.5mm小槽作为充液管焊接口。
49.(2)支撑柱加工:将0.11mm丝径的铜丝缠绕拉伸得到外径0.8mm、节距2mm的螺旋支撑柱3,螺旋支撑柱的长度为100mm,支撑柱占均热板蒸汽通道横截面积比为3.6%。
50.(3)吸液芯:将120μm直径的球形紫铜粉平铺在尺寸为100mm
×
40mm,深0.3mm的石墨模具中,再裁剪200目,厚0.2mm,尺寸为110mm
×
50mm的铜网41铺在铜粉上烧结得到复合吸液芯4,复合吸液芯4中铜粉烧结泡沫铜42位于下方,铜网41在上方。复合吸液芯4的截面积占均热板内部空腔蒸汽通道截面积的50%。
51.(4)一体烧结:按照图4的横向排列方式排列3条螺旋支撑柱,相邻支撑柱间隔10mm。压好石墨模具,放入920℃的真空管式炉中烧结,将螺旋支撑柱、铜网和泡沫铜烧结在一起,烧结完成后剪掉多余的铜网,得到吸液芯尺寸为100mm
×
40mm
×
0.5mm。
52.(5)组装:将烧结好的支撑柱-复合吸液芯一体结构裁去多余铜网边缘,按照图1方式组装在一起,再次高温烧结,使吸液芯和支撑柱与壳板更好的接合,降低热阻,增大结构稳定性。
53.(6)注液密封:使用钎焊将上下壳板的边缘焊接密封,加焊充液管,抽真空后填充甲醇作为工作流体,通过冷焊机焊断充液管密封制成所述均热板,如图2-图3所示。
54.实施例2
55.本实施例中,均热板外形为正方形结构,螺旋支撑柱采用中心向四周分散的排列方式,如图5所示,螺旋支撑柱采用与铜粉一体烧结工艺,具体实施步骤如下:
56.(1)上壳板尺寸:厚度为0.8mm,外边长为64mm,内凹槽边长60mm,深0.6mm,充液管焊接口直径0.5mm。下壳板尺寸:厚度为0.8mm,外边长为64mm,内凹槽边长60mm,深0.6mm。
57.(2)将0.11mm丝径的铜丝缠绕拉伸得到外径0.8mm、节距2mm的螺旋支撑柱,考虑到支撑柱与铜粉一体烧结时会嵌入铜粉一部分,所以实际烧结时螺旋支撑柱的外径比理论大0-0.3mm。
58.(3)先在边长为60mm的正方形石墨模具中铺一层直径为120μm的球形紫铜粉,再平铺一层直径为160μm的球形紫铜粉,得到多孔隙率吸液芯,吸液芯总厚度为0.6mm。
59.(4)将制备好的螺旋支撑柱按照图5所示的排列方式铺设在待烧结的铜粉上,盖好石墨模具。
60.(5)将整个模具放入920℃的真空管式炉中烧结一小时,烧结时全程通氮气。烧结完成后待自然冷却后取出。
61.(6)将烧结好的支撑柱-吸液芯一体结构与上壳板、下壳板组装在一起,放入900℃的烧结炉中再次烧结,使得吸液芯与下壳板,支撑柱与上壳板紧密连接,降低热阻,期间同样通氮气保护。
62.(7)使用钎焊将上下壳板焊接密封,同时焊接好充液管,并检查气密性。
63.(8)按照抽真空,注液,再抽真空的步骤填充80%充液率的去离子水。二次抽真空结束后使用冷焊将多余的充液管焊断,完成注液,制成所述的均热板。
64.通过以上的螺旋形支撑柱-吸液芯一体烧结均热板及其制备方法,通过支撑柱的优化设计,减小了蒸汽通道阻力,尤其螺旋结构设计降低了蒸汽由中心向四周流动阻力,同时保证了均热板在工作时结构的稳定性,在螺旋支撑柱的加工制造时只需将铜丝缠绕拉伸,降低了工艺加工的难度。与在上壳板和下壳板通过刻蚀、激光加工、cnc加工支撑柱相比,支撑柱与吸液芯一体烧结技术大大降低了设备需求与工艺成本,此种加工工艺只需在烧结炉中烧结吸液芯时一体烧结成型,同时保证了一定的机械强度。不同均热板外形可以搭配的不同的支撑柱排列方式,适用于不同的需求场合,生产成本低,实用性强。多孔隙率吸液芯,有利于蒸汽快速流向蒸汽通道,同时快速冷却回流到蒸发器,加快了两相流循环,提高了传热性能。
65.实施例3效果验证
66.不同类型支撑柱压降对比。
67.支撑柱结构保证蒸汽通道稳定的同时增加了蒸汽流动阻力。通过压差实验测试支撑柱结构类型对蒸汽通道压降的影响,支撑柱参数如表1。为方便测试,简化实验为测试水流经蒸汽通道时的压降来表征通道阻力。设置水流速度为2l/min。
68.表1支撑柱参数及实验条件
[0069][0070]
压降测试实验结果如图6所示,作为参考的sc0最大压降为2.835kpa,排列了3行螺旋形支撑柱的ssc3的最大压降为3.566kpa,3行圆柱形支撑柱的csc3的最大压降为3.585kpa,csc3与ssc3的压降增大了0.019kpa;4行螺旋形支撑柱的ssc4的最大压降为3.826kpa,4行圆柱形支撑柱的csc4的最大压降为4.089kpa,csc4比ssc4的压降增大了0.263kpa;5行螺旋形支撑柱的ssc5的最大压降为4.097kpa,5行圆柱形支撑柱的csc5的最大压降为5.081kpa,csc5比ssc5的压降增大了0.984kpa;6行螺旋形支撑柱的ssc6的最大压降为4.369kpa,6行圆柱形支撑柱的csc6的最大压降为6.114kpa,csc6比ssc6的压降增大了1.745kpa;数据显示,在相同的支撑柱行数和间距下,螺旋形支撑柱的压降总要小于圆柱形支撑柱,且增加支撑柱行数时,螺旋形支撑柱的压降整体变化幅度较小,而圆柱形支撑柱变化幅度较大。所以在相同的支撑柱行数时螺旋形支撑柱引起的通道阻力要比圆柱形支撑柱引起的通道阻力小。
[0071]
均热板热阻测试:将ssc3、ssc4、ssc5、ssc6组装成对应的结构的均热板,测试了均热板的热阻及热源温度。对应支撑柱行数的均热板分别命名为sscvc3、sscvc4、sscvc5和sscvc6。
[0072]
(1)sscvc3(支撑柱占均热板蒸汽通道横截面积比为4.2%)
[0073]
当螺旋支撑柱设置为3行时,不同充液率下的总热阻如图7(a)所示。在60%充液率时均热板最低热阻为0.3955℃/w,但随着功率上升,均热板发生局部干涸,导致总热阻不断上升。70%充液率虽然起始热阻相对较大,但在39w时达到最低热阻,所以在图7(b)热端温度变化曲线中可以看出,在较大功率时70%对热源温度控制要更好。
[0074]
(2)sscvc4(支撑柱占均热板蒸汽通道横截面积比为5.58%)
[0075]
当螺旋支撑柱为4行时,不同充液率下的总热阻如图8(a)所示。在80%充液率时均热板最低热阻为0.31046℃/w。同时在48w时,能将热源温度控制在53.45℃,可满足大部分散热需求。
[0076]
(3)sscvc5(支撑柱占均热板蒸汽通道横截面积比为6.98%)
[0077]
当螺旋支撑柱为5行时,不同充液率下的总热阻如图9(a)所示。在90%充液率时均热板最低热阻为0.38153℃/w。在48w时,能将热源温度控制在56.33℃。
[0078]
(4)sscvc6(支撑柱占均热板蒸汽通道横截面积比为8.37%)
[0079]
当螺旋支撑柱为6行时,不同充液率下的总热阻如图10(a)所示。在70%充液率时均热板最低热阻为0.38123℃/w,之后热阻快速上升,而80%充液率在启动时热阻较高,但在加热功率达到42.82w时最低热阻为0.51741℃/w,虽然小于70%时的最低热阻但是在高功率段热源温度控制效果好于其他充液率。不同行数支撑柱热阻及热端温度
[0080]
对比各个测试样本在不同充液率下的热阻和热端温度,选取达到最低热阻的充液率作为均热板最佳充液率。图11对比了最佳充液率下不同支撑柱数量对均热板热阻的影响。可以清晰的看出,4行螺旋形支撑柱的sscvc4除了在启动时热阻略高于sscvc3和sscvc6,其余各个功率段的热阻均小于其他组,且最低热阻能达到0.31046℃/w,其次是5行螺旋形支撑柱sscvc5。而支撑柱数量较少的sscvc3和支撑柱数量较多的sscvc6的整体热阻较高。从热端温度图中也能看出,sscvc4对热源的散热效果最好,sscvc3和sscvc6较差。虽然从压降测试中增加支撑柱的数量会增大蒸汽通道阻力。一定数量的支撑柱还起到了引流的作用,可快速将冷凝器的冷凝工质引流回蒸发器。螺旋结构的支撑柱与冷凝器和吸液芯的接触点可以形成近0
°
角,增加了毛细作用。而支撑柱较多时,支撑柱的对蒸汽通道的阻力大于了引流作用,所以总热阻会增大。
[0081]
综上,本发明通过对支撑柱的优化设计,将细铜丝制成螺旋结构作为均热板的支撑柱,保证均热板内腔结构不变形的同时降低了均热板内蒸汽横向和径向流动的阻力。通过一体烧结技术将支撑柱固定在吸液芯上,简化了在壳板上加工支撑柱的工序,通过二次烧结工艺将支撑柱和吸液芯与上下壳板接合,保证了均热板的结构稳定性,降低了均热板的热阻,同时降低了生产成本,实用性强。多孔隙率吸液芯的设计加快了蒸汽流向蒸汽通道的速度,同时上层较大的孔隙率有利于冷凝器液体的快速回流,加快了两相流传热过程,提高了均热板的传热性能。
[0082]
以上所述实施例仅为本发明的具体几个实施例,不代表本发明的全部内容,实施例不是对本发明的限制。任何在本发明上构思、结构上的修改、改进等均应包含在本发明的保护范围内。
再多了解一些
本文用于创业者技术爱好者查询,仅供学习研究,如用于商业用途,请联系技术所有人。