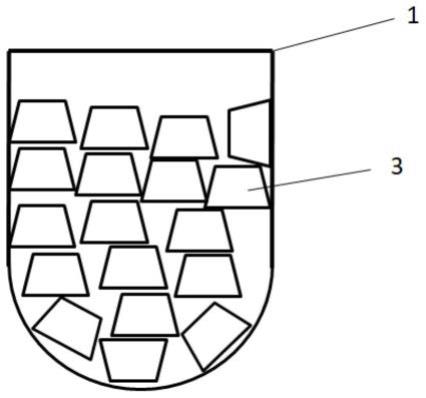
1.本发明涉及高纯铝熔炼技术领域,具体涉及一种降低高纯铝熔体中不熔物含量的方法。
背景技术:
2.高纯铝是高技术高附加值材料,通常把纯度(铝含量)大于99.8%的纯铝叫做高纯铝。高纯铝由于具有很好的导电性、可塑性、光反射性、延展性和耐蚀性以及极低的导磁性,广泛应用于汽车电子、消费电子、工业电子、新能源汽车等领域。
3.高纯铝作为集成电路用导线材料,对其内部的不熔物含量、缺陷要求极高,否则在溅射过程中极易出现异常放电、喷溅以及微颗粒含量过高等异常问题。因此,在原材料的熔炼过程中要尽可能避免引入不熔物,尤其是在向坩埚中装料的阶段减少引入不熔物。目前已有的装料过程一般是将铝锭加工成500
×
130
×
70mm的船型锭,然后装填入坩埚中,铝锭尖锐的边角容易划到坩埚壁,将不熔物引入铝液中,并且冶炼过程中大约需要装填70块左右船型锭,装填效率比较低。
4.cn106756097a公开了一种高纯铝的制备方法,该制备方法首先将高纯铝原料在真空熔炼炉中熔炼,取出后水淬;然后进行冷轧处理后,装入石英舟中;将装入铝锭的石英舟再次放入真空熔炼炉内进行脱氧处理;最后降温得到高纯铝。以上制备方法操作复杂,并且难以避免在填料过程中引入不熔物。
5.cn112126797a公开了一种高纯铝的制备方法,该方法通过将铝矾土矿破碎并与氢氧化钠混合制备铝酸盐,然后通入一氧化碳使氯酸盐水解得到碳酸铝沉淀,再依次经过煅烧和电解,得到产品。该方法得到的高纯铝纯度仅达到4n以上,难以满足高水平集成电路的需要。
6.因此,提供一种降低高纯铝熔体中不熔物含量的方法具有重要意义。
技术实现要素:
7.针对以上问题,本发明的目的在于提供一种降低高纯铝熔体中不熔物含量的方法,与现有技术相比,本发明提供的方法能够有效避免在装料过程中引入不熔物,避免在溅射过程中发生异常放电、喷溅以及微颗粒含量过高等异常问题。
8.为达到此发明目的,本发明采用以下技术方案:
9.本发明提供一种降低高纯铝熔体中不熔物含量的方法,所述方法包括以下步骤:
10.(1)将铝锭依次进行机加工、清洗和干燥,得到预处理铝锭;所述预处理铝锭的底部为圆弧形;
11.(2)将步骤(1)得到的所述预处理铝锭依次经过第一熔炼、第二熔炼和第三熔炼,得到高纯铝熔体。
12.本发明一方面将铝锭的底部加工成圆弧形,与坩埚内底部的尺寸相匹配,可以有效解决装料过程中对坩埚的损伤,避免引入不熔物杂质,同时提升装填效率;另一方面采用
第一熔炼、第二熔炼和第三熔炼依次加入预处理铝锭并进行分步熔炼,首先通过第一熔炼得到熔化的部分铝液,然后再分别加入预处理铝锭进行第二熔炼和第三熔炼,第一熔炼产生的部分铝液加速后续铝锭的熔化,同时避免了对坩埚的刮擦,进一步减少了不熔物的引入。本发明提供的方法相较于已有的船型锭的装填方法,大大减少了高纯铝熔体中的不熔物,并且提高了装料效率。
13.本发明中,所述“高纯”指的是纯度≥5n5。
14.优选地,步骤(1)所述预处理铝锭的纯度≥99.9995%,例如可以是99.9995%、99.9996%、99.9997%或99.9998%,但不限于所列举的数值,数值范围内其它未列举的数值同样适用。
15.优选地,步骤(1)所述清洗包括依次进行的水洗和酸洗。
16.优选地,步骤(1)所述水洗包括依次进行的第一水洗和第二水洗。
17.优选地,所述第一水洗的时间为5-10min,例如可以是5min、6min、7min、8min、9min或10min,但不限于所列举的数值,数值范围内其它未列举的数值同样适用。
18.优选地,所述第二水洗的时间为5-10min,例如可以是5min、6min、7min、8min、9min或10min,但不限于所列举的数值,数值范围内其它未列举的数值同样适用。
19.优选地,步骤(1)所述酸洗的酸液包括硝酸。
20.优选地,所述酸液的质量浓度为1-5%,例如可以是1%、2%、3%、4%或5%,但不限于所列举的数值,数值范围内其它未列举的数值同样适用。
21.优选地,所述酸洗的时间为5-10min,例如可以是5min、6min、7min、8min、9min或10min,但不限于所列举的数值,数值范围内其它未列举的数值同样适用。
22.优选地,步骤(1)所述干燥的时间为5-10min,例如可以是5min、6min、7min、8min、9min或10min,但不限于所列举的数值,数值范围内其它未列举的数值同样适用。
23.本发明中,干燥后的铝锭采用塑料膜袋进行包装,避免不熔物和不纯物附着在表面,待装料时再去除塑料膜袋。
24.优选地,步骤(2)所述第一熔炼包括:将一块步骤(1)得到的所述预处理铝锭放入坩埚,加热,进行第一熔炼至熔化。
25.本发明中,所述坩埚的表面涂有一层氧化铝,厚度一般为0.4-0.6mm,起到防护隔绝的作用。
26.优选地,所述第一熔炼的熔炼温度为740-760℃,例如可以是740℃、742℃、744℃、746℃、748℃、750℃、752℃、754℃、756℃、758℃或760℃,但不限于所列举的数值,数值范围内其它未列举的数值同样适用。
27.本发明优选控制第一熔炼的熔炼温度在特定范围,可以进一步促进铝锭熔化的同时,降低熔体中不熔物的含量。
28.优选地,所述第一熔炼的时间为5-6h,例如可以是5h、5.2h、5.4h、5.6h、5.8h或6h,但不限于所列举的数值,数值范围内其它未列举的数值同样适用。
29.本发明优选控制第一熔炼的熔炼时间在特定范围,可以进一步促进铝锭熔化的同时,降低熔体中不熔物的含量。
30.优选地,步骤(2)所述第二熔炼包括:将一块步骤(1)得到的所述预处理铝锭再次放入坩埚,进行第二熔炼至熔化。
31.优选地,所述第二熔炼的时间为2-3h,例如可以是2h、2.2h、2.4h、2.6h、2.8h或3h,但不限于所列举的数值,数值范围内其它未列举的数值同样适用。
32.优选地,步骤(2)所述第三熔炼包括:将一块步骤(1)得到的所述预处理铝锭再次放入坩埚,进行第三熔炼至熔化。
33.优选地,所述第三熔炼的时间为2-3h,例如可以是2h、2.2h、2.4h、2.6h、2.8h或3h,但不限于所列举的数值,数值范围内其它未列举的数值同样适用。
34.作为本发明的优选技术方案,所述方法包括以下步骤:
35.(1)将铝锭进行机加工成底部为圆弧形,然后依次进行一次水洗5-10min,二次水洗5-10min,酸洗5-10min,然后干燥5-10min,得到预处理铝锭;
36.所述酸洗的酸液包括硝酸,质量浓度为1-5%;
37.(2)将一块步骤(1)得到的所述预处理铝锭放入坩埚,加热,在740-760℃下进行第一熔炼至熔化5-6h,然后将一块步骤(1)得到的所述预处理铝锭再次放入坩埚,进行第二熔炼至熔化2-3h,之后将一块步骤(1)得到的所述预处理铝锭再次放入坩埚,进行第三熔炼至熔化2-3h,得到高纯铝熔体。
38.相对于现有技术,本发明具有以下有益效果:
39.(1)本发明通过将铝锭的底部形状与坩埚的内底部形状相匹配,可以有效解决装料过程中对坩埚的损伤,避免引入不熔物杂质,同时提升装填效率。
40.(2)本发明通过依次进行第一熔炼、第二熔炼和第三熔炼能够加速铝液熔化,进一步避免了对坩埚的刮擦,减少了不熔物的引入。
附图说明
41.图1是本发明实施例1中所述预处理铝锭进行第一熔炼前的装填示意图;
42.图2是本发明对比例1中所述预处理船型锭的装填示意图;
43.其中,1-坩埚;2-预处理铝锭;3-预处理船型锭。
具体实施方式
44.下面通过具体实施方式来进一步说明本发明的技术方案。本领域技术人员应该明了,所述实施例仅仅是帮助理解本发明,不应视为对本发明的具体限制。
45.实施例1
46.本实施例提供一种降低高纯铝熔体中不熔物含量的方法,所述方法包括以下步骤:
47.(1)将铝锭进行机加工成底部为圆弧形,然后依次进行一次水洗7min,二次水洗7min,酸洗7min,然后干燥7min,得到预处理铝锭;
48.所述酸洗的酸液为硝酸,质量浓度为3%;
49.(2)将一块步骤(1)得到的所述预处理铝锭放入坩埚,装填示意图如图1所示,加热,在750℃下进行第一熔炼至熔化5.5h,然后将一块步骤(1)得到的所述预处理铝锭再次放入坩埚,进行第二熔炼至熔化2.5h,之后将一块步骤(1)得到的所述预处理铝锭再次放入坩埚,进行第三熔炼至熔化2.5h,得到高纯铝熔体。
50.实施例2
51.本实施例提供一种降低高纯铝熔体中不熔物含量的方法,所述方法包括以下步骤:
52.(1)将铝锭进行机加工成底部为圆弧形,然后依次进行一次水洗5min,二次水洗10min,酸洗5min,然后干燥10min,得到预处理铝锭;
53.所述酸洗的酸液为硝酸,质量浓度为1%;
54.(2)将一块步骤(1)得到的所述预处理铝锭放入坩埚,加热,在740℃下进行第一熔炼至熔化6h,然后将一块步骤(1)得到的所述预处理铝锭再次放入坩埚,进行第二熔炼至熔化2h,之后将一块步骤(1)得到的所述预处理铝锭再次放入坩埚,进行第三熔炼至熔化3h,得到高纯铝熔体。
55.实施例3
56.本实施例提供一种降低高纯铝熔体中不熔物含量的方法,所述方法包括以下步骤:
57.(1)将铝锭进行机加工成底部为圆弧形,然后依次进行一次水洗10min,二次水洗5min,酸洗10min,然后干燥5min,得到预处理铝锭;
58.所述酸洗的酸液为硝酸,质量浓度为5%;
59.(2)将一块步骤(1)得到的所述预处理铝锭放入坩埚,加热,在760℃下进行第一熔炼至熔化5h,然后将一块步骤(1)得到的所述预处理铝锭再次放入坩埚,进行第二熔炼至熔化3h,之后将一块步骤(1)得到的所述预处理铝锭再次放入坩埚,进行第三熔炼至熔化2h,得到高纯铝熔体。
60.实施例4
61.本实施例提供一种降低高纯铝熔体中不熔物含量的方法,与实施例1的相比的区别仅在于所述第一熔炼的温度为700℃。
62.实施例5
63.本实施例提供一种降低高纯铝熔体中不熔物含量的方法,与实施例1的相比的区别仅在于所述第一熔炼的温度为800℃。
64.实施例6
65.本实施例提供一种降低高纯铝熔体中不熔物含量的方法,与实施例1的相比的区别仅在于所述第一熔炼的时间为2h。
66.对比例1
67.本对比例提供一种高纯铝熔体的制备方法,与实施例1相比的区别仅在于:
68.步骤(1):将铝锭加工为500
×
130
×
70mm的船型锭,然后依次进行第一水洗、第二水洗、酸洗和干燥,得到预处理船型锭;
69.步骤(2):将步骤(1)中所有的预处理船型锭(与实施例1中步骤(2)加入预处理铝锭的总量相等)放入坩埚,装填示意图如图2所示,加热,在750℃下进行熔炼至熔化10.5h。
70.实施例1-6和对比例1中取出高纯铝熔体后观察坩埚表面是否存在划痕,结果如表1所示。
71.对实施例1-6和对比例1所制备的高纯铝熔体中不熔物的含量进行分析,结果如表1所示。
72.表1
[0073] 坩埚表面是否有划痕不熔物含量/%实施例1否<0.5%实施例2否<0.5%实施例3否<0.5%实施例4否<1%实施例5否<1%实施例6否<1%对比例1是>1%
[0074]
通过上述实施例和对比例的结果可知,本发明提供的方法,通过将铝锭底部形状与坩埚的内底部形状相匹配,以及采用一次熔炼、二次熔炼和三次熔炼,能够避免了对坩埚的刮擦,减少了不熔物的引入。
[0075]
申请人声明,以上所述仅为本发明的具体实施方式,但本发明的保护范围并不局限于此,所属技术领域的技术人员应该明了,任何属于本技术领域的技术人员在本发明揭露的技术范围内,可轻易想到的变化或替换,均落在本发明的保护范围和公开范围之内。
再多了解一些
本文用于创业者技术爱好者查询,仅供学习研究,如用于商业用途,请联系技术所有人。