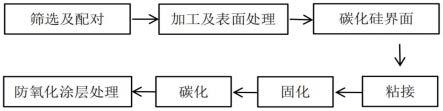
1.本发明涉及碳基复合材料修复处理技术领域,尤其涉及一种飞机碳/碳复合材料刹车盘修复方法及所用粘接剂。
背景技术:
2.碳基复合材料是当前以及未来几十年航空航天装备材料的主流,凭其质量轻、强度高、耐磨损、导热系数好及寿命长等一系列优良性能,作为航空刹车材料得到了广泛的应用。碳基复合材料刹车盘作为飞机起落制动装置的重要消耗部件,在经历多次反复刹车后,失效形式主要是磨损,材料基体结构及性能仍完好。由于碳刹车盘制备周期长、成本高,因此对磨损超差的碳基复合材料刹车盘进行修复再利用是必要的。
3.国外多家公司已实施旧碳基复合材料刹车盘二合一再生修复技术,但技术对外严格保密。国内从上世纪开始对民航飞机刹车盘采用二合一机械铆接和粘接技术进行修复。前者方法比较简单,其缺点是铆钉孔处存在应力集中,并且增加了构件重量;后者方法相对复杂,采用高温型粘接材料,通过成型固化及碳化处理使两片碳刹车盘整体结合在一起。采用该技术修复后的碳刹车盘整体性能好,不改变原碳刹车盘热物理性能及摩擦磨损性能,使飞机碳刹车盘的可维修率大大提高,这样,既减少了资源的浪费,同时也缩短了修理周期并节约成本。
4.但是诸多文献报道的粘接剂存在于碳/碳基体热膨胀系数不匹配及高温不稳定的问题,会引起粘接剂强度低、抗热震性能以及寿命不足。加之以往的报道主要针对民用飞机刹车盘进行修复,民用飞机正常刹车温度一般在500~600℃,而军用飞机正常刹车温度一般在600~750℃,因此对粘接剂及防氧化涂层提出了更高的要求。
技术实现要素:
5.为了解决上述技术问题,本发明提供了一种飞机碳/碳复合材料刹车盘修复方法及所用粘接剂,粘接剂具有高温、高强度、性能稳定、可靠性高的优点,在粘接面利用化学气相反应方法制备碳化硅界面,然后以聚硅氮烷树脂为基体,同步引入各种耐高温填料,经过研磨、混合、固化、碳化得到耐高温的陶瓷基粘接剂,经过该方法制备的陶瓷基粘接剂与碳基复合材料热膨胀系数接近,热匹配性良好,抗热震性能优异。
6.为实现此技术目的,本发明采用如下方案:
7.碳基复合材料用粘接剂,其特征在于,包括混合粉末和聚硅氮烷树脂溶液,室温条件下,将25~30wt.%的铝粉末、20~25wt.%的硅粉末、10~20wt.%的碳粉末、10~15wt.%的氮化铝粉、10~15wt.%的二硅化钼粉、10~15wt.%的二硼化锆粉,加入到球磨机中混合研磨制成混合粉末;将混合粉末与聚硅氮烷树脂溶液按照2~3:1的质量比同时加入到容器中搅拌配制得到粘接剂。
8.进一步地,聚硅氧烷树脂溶液由分子量为10~20万的聚硅氮烷树脂和二甲苯混合而成,其中聚硅氮烷树脂与二甲苯的质量比为1.5:1。
9.进一步地,铝粉粒度范围是200~325目,硅粉粒度范围是200~325目,碳粉粒度范围是300~400目,氮化铝粉粒度范围是300~400目,二硅化钼粉粒度范围是300~400目,二硼化锆粉粒度范围是150~325目。
10.进一步地,混合粉末在球磨机的研磨时间为50min。
11.进一步地,搅拌时间为1~2h。
12.飞机碳/碳复合材料刹车盘修复方法,按如下步骤进行:
13.s1、筛选与配对:目视检查碳盘表面形态,厚度超出标准碳盘半盘厚度4mm以上;
14.s2、加工及表面处理:将s1筛出的碳盘厚度加工至标准厚度的1/2,在粘接面加工沟槽,将加工后碳盘表面清理干净,置于装有无水乙醇的超声波清洗机中清洗,超声清洗干净后烘干冷却;
15.s3、碳化硅界面:按化学计量比称取硅粉和二氧化硅粉,搅拌均匀后铺在石墨坩埚内,将s3冷却后碳盘放置在石墨坩埚上,将石墨坩埚和碳盘一同进行高温处理,在粘接面实现碳化硅界面的制备;
16.s4、粘接:将权利要求1~5任一项所述的碳基复合材料用粘接剂涂抹在带有沟槽的粘接面上;将两片碳盘对准界面合拢,将合拢后碳盘置于热压机上,并施加压力,同时利用垫条控制胶层的厚度,胶层厚度控制在0.10~0.15mm;
17.s5、固化:将s4粘接好的碳盘静置12h后,以5℃/小时的速率升温至150~300℃后保温2小时完成粘接剂的固化,整个固化期间通过给粘接好的碳盘施加与s4同样的压力;
18.s6、碳化:将固化后的碳盘放入高温真空设备中,在-0.1mpa的真空环境下以50℃/小时的速率升温至1000~1200℃后保温2~4小时完成粘接剂的碳化;
19.s7、防氧化涂层处理:在碳盘非摩擦部位涂抹磷酸盐涂层,完成修复。
20.进一步地,s2中超声清洗时间为30~60min,超声清洗后烘干温度为100℃~120℃,烘干时间为3~5h。
21.进一步地,s3中高温处理温度为1600℃~1800℃,处理时间为1~2h。
22.进一步地,s3中化学计量比为硅粉过量5~10%,硅粉、二氧化硅粉粒度范围均为30~50目。
23.进一步地,s7中涂层处理步骤为:
24.s7-1、称料粉:按照比例称取10~15wt.%si粉、20~25wt.%aln粉、5~10wt.%b4c粉、2~5wt.%y2o3粉、10~15wt.%zno、15~20wt.%zn3(po4)2粉、20~25wt.%mg3(po4)2粉,放入玛瑙研钵中充分研磨混合30~60min;
25.s7-2、配料浆:向混合粉末中滴入质量浓度20~25wt.%磷酸溶液,混合后的粉末与磷酸溶液的重量比为1:(2.0~2.5),之后使用磁力搅拌器充分搅拌30-60min,配制成磷酸盐涂层料浆;
26.s7-3、涂刷:使用软毛刷蘸取调配好的涂层料浆,均匀涂刷在碳盘非摩擦部位,涂层厚度控制在0.05~0.1mm;
27.s7-4、烘干:将碳盘放置在100~120℃烘箱中,干燥处理3~5h,至表面干燥;
28.s7-5、热处理:烘干后的碳盘置于高温设备中,在氮气保护气氛下,以5℃/min的升温速率升至700~750℃,保温2h,降至室温后取出。
29.与现有技术相比,本发明的有益效果在于:
30.1、碳/碳复合材料粘接剂单压缩剪切强度高达18mpa;经rt-750℃循环50次,剪切强度达15mpa;经1200℃保温20h后其强度为15.4mpa,说明粘接剂具良好的耐热和抗热震性能。
31.2、经过100次不同能量刹车试验后,缩比件修复摩擦环动、静试环结构完整,没有分层、开胶,粘接剂没有熔化流出痕迹;同时非摩擦表面防氧化涂层未出现脱落现象,摩擦环未出现氧化迹象。
32.3、经过修复工艺处理的动、静摩擦环,在各种刹车条件下,摩擦曲线稳定且刹车平稳,摩擦系数均未发生变化,以上数据说明修复工艺可以满足碳刹车盘的刹车使用要求。
附图说明
33.图1为本发明实施例提供的一种飞机碳/碳复合材料刹车盘修复方法的工艺流程图;
34.图2为本发明实施例提供的粘接样品界面形貌;
35.图3为本发明实施例提供的粘接剂局部放大形貌;
36.图4为本发明实施例提供的试验后摩擦环外观照片;
37.图5为本发明实施例提供的试验后摩擦环无损探伤图。
具体实施方式
38.为充分了解本发明之目的、特征及功效,借由下述具体的实施方式,对本发明做详细说明,但本发明并不仅仅限于此。
39.实施例
40.室温条件下,采用千分之一天平称取25~30wt.%的铝粉末、20~25wt.%的硅粉末、10~20wt.%的碳粉末、10~15wt.%的氮化铝粉、10~15wt.%的二硅化钼粉、10~15wt.%的二硼化锆粉,全部置于球磨罐中,研磨球与物料重量比为2:1,先用药匙充分搅拌球和料,再在100~200r/min的转速下研磨混合50分钟,制成混合均匀的粉末。
41.铝粉粒度范围是200~325目,硅粉粒度范围是200~325目,碳粉粒度范围是300~400目,氮化铝粉粒度范围是300~400目,二硅化钼粉粒度范围是300~400目,二硼化锆粉粒度范围是150~325目。
42.将上述混合粉末与聚硅氮烷树脂溶液按照(2~3):1的质量比同时加入到容器(烧杯)中,采用恒速电动搅拌器在100~200r/min转速下搅拌1~2小时,配制得到碳基复合材料用粘接剂。聚硅氮烷树脂溶液由聚硅氮烷树脂与二甲苯以1.5:1质量比例搅拌混合制成。
43.一种飞机碳/碳复合材料刹车盘修复方法,按如下步骤进行:
44.s1、筛选与配对
45.首先,目视检查碳盘表面,应无氧化、无裂纹以及无掉块现象;
46.然后,用游标卡尺测量旧碳盘厚度,旧碳盘厚度>(标准碳盘半盘厚度 4mm),允许有可加工掉的缺陷。
47.最后,筛选合格的两片碳盘配成一对,记录编号。
48.s2、加工及表面处理
49.s2-1、将筛选并配对的碳盘厚度加工至标准厚度的1/2,碳盘上下表面平整;其中
一面作为粘接面,加工深度和宽度均为0.2mm的直线型沟槽,沟槽间间距30mm。
50.s2-2、使用吸尘器除去粘接面表面浮尘;再用清水冲刷,并用硬毛刷对粘接面进行清理,去除粘接面沟槽内残留的短纤维。
51.s2-3、将处理后的碳盘依次摆放在料筐内,将料筐置于超声波清洗机中,利用酒精清洗30~60min,注意碳盘与碳盘之间要有间隙。
52.s2-4、将清洗后的碳盘放入烘箱中自由升温至100~120℃,进行烘干3-5h处理,待碳盘冷却至室温后取出。
53.s3、碳化硅界面
54.s3-1、按(3~5):1比例称取硅粉和二氧化硅粉,搅拌均匀后平铺在石墨坩埚内;
55.s3-2、将碳盘放置石墨坩埚之上,碳盘粘接面向下;
56.s3-3、将石墨坩埚与碳盘整体置于高温炉内,1600~1800℃真空条件下,在粘接面区域实现碳化硅界面的制备,界面厚度在0.5mm~1.0mm,有助于缓解界面应力。
57.s4、粘接
58.s4-1、用腻子铲平面部分将配好的粘接剂缓慢均匀涂抹在碳盘粘接面,确保沟槽内填满粘接剂,每片碳盘粘接面以上至少涂抹5mm厚度的粘接剂,该步可通过定量来控制;
59.s4-2、将两片碳盘粘接面对准合拢并施压错动几次,排除涂抹粘接剂过程中产生的气泡,并将多余的粘结剂用小刀刮掉,保证碳盘表面的整洁度;
60.s4-3、将粘接碳盘置于热压机层板上,并施加2~3mpa的压力,同时利用垫条控制胶层的厚度,胶层厚度须控制在0.10~0.15mm。
61.s5、固化
62.将上述粘接好的碳盘静置12h后,以5℃/小时的速率升温至250~300℃后保温2小时,之后自由降温,完成粘接剂的固化,整个固化期间通过给粘接碳盘施加同样2~3mpa压力。
63.s6、碳化
64.将固化后的粘接碳盘平放入高温真空设备中,在-0.1mpa的真空环境下以50℃/小时的速率升温至1200℃后保温2~4小时完成粘接剂的碳化。
65.s7、防氧化涂层处理
66.s7-1、称料粉:按照比例称取10~15wt.%si粉(1~3μm)、20~25wt.%aln粉(1~3μm)、5~10wt.%b4c粉(1~3μm)、2~5wt.%y2o3粉(3~5μm)、10~15wt.%zno(分析纯)、15~20wt.%zn3(po4)2粉(分析纯)、20~25wt.%mg3(po4)2粉(分析纯),放入玛瑙研钵中充分研磨混合30~60min;
67.s7-2、配料浆:向混合粉末中滴入质量浓度20~25wt.%磷酸溶液,混合后的粉末与磷酸溶液的重量比为1:(2.0~2.5),之后使用磁力搅拌器充分搅拌30-60min,配制成磷酸盐涂层料浆;
68.s7-3、涂刷:使用软毛刷蘸取调配好的涂层料浆,均匀涂刷在碳盘非摩擦部位,涂层厚度控制在0.05~0.1mm;
69.s7-4、烘干:将碳盘放置在100~120℃烘箱中,干燥处理3~5h,至表面干燥,无光泽感;
70.s7-5、热处理:烘干后的碳盘置于高温设备中,在氮气保护气氛下,以5℃/min的升
温速率升至700~750℃,保温2h,降至室温后取出。
71.性能测试
72.1、单压缩剪切强度:参考qj 1634a《胶黏剂压缩剪切强度测试方法》标准,分别在常温、750℃、1200℃三种条件下测试粘接试样的单压缩剪切强度,粘接试样所采用的修复工艺与粘接碳盘一致,图2和图3分别为测试前粘接样品界面形貌和粘接剂局部放大形貌,其中图2b为图2a的放大图,图3b为图3a的放大图。另外,对经过室温-750℃热震50次后的试样也进行了常温单压缩剪切强度测试,具体数据如表1所示。
73.表1粘接碳盘试样性能
[0074][0075]
由表1可知:室温下粘接剂的粘接强度(单压缩剪切强度)高达18.0mpa;在750℃和1200℃真空条件下,其强度分别为16.7mpa和15.4mpa;在rt-750℃热震循环50次后,室温下其强度仍有15mpa。
[0076]
以上数据说明,该粘接剂具有较高的粘接强度,高温条件下粘接性能优异,同时也具有良好的抗热震性能。
[0077]
2、缩比件摩擦磨损测试(动态热冲击性能)
[0078]
从上述修复碳刹车盘上取缩比件摩擦环,并在摩擦环非摩擦面涂刷改性磷酸盐防氧化涂层后,进行摩擦磨损性能试验。参照hb5434.7-2004《航空机轮摩擦材料试验方法》,在mm-3000摩擦磨损试验机上对修复后摩擦环进行了摩擦磨损性能测试,主要是考核修复工艺对摩擦磨损性能的影响以及摩擦环的粘接特性,重点增加了大能量及高刹车压力条件的试验次数,以便更好的考核修复摩擦环在大能量高温度冲击下是否开裂。
[0079]
本次试验的摩擦环规格为(φ75~φ53)
×
14mm,试验条件及试验结果分别见表2和表3。
[0080]
表2摩擦试验条件
[0081][0082][0083]
表3摩擦试验结果
[0084][0085]
图3和图4分别为试验后摩擦环外观照片和试验后摩擦环无损探伤图。
[0086]
可见,经过100次不同能量及不同刹车压力刹车试验后,动、静试环结构完整,没有分层、开胶,粘接剂没有熔化流出痕迹。同时非摩擦表面防氧化涂层未出现脱落现象,摩擦环未出现氧化迹象。经过修复工艺处理的动和静摩擦环,在各种刹车条件下,摩擦曲线稳定且刹车平稳,摩擦系数均未发生变化。
[0087]
本发明主要分为两步进行:第一步在粘接面利用化学气相反应方法制备碳化硅界面,然后以聚硅氮烷树脂为基体,同步引入各种耐高温填料,经过研磨、混合、固化、碳化得到耐高温的陶瓷基粘接剂,经过该方法制备的陶瓷基粘接剂与碳基复合材料热膨胀系数接近,热匹配性良好,抗热震性能优异。与粘接剂相容性好的防氧化涂层主要采用一种改性的磷酸盐涂层。本发明所制备的粘接剂高温强度高、性能稳定,可靠性高;所制备的防氧化涂层与粘接剂相容性好、防水性强、抗热震性能优异、现场维护方便。
[0088]
最后,需要注意的是:以上列举的仅是本发明的优选实施例,当然本领域的技术人员可以对本发明进行改动和变型,倘若这些修改和变型属于本发明权利要求及其等同技术的范围之内,均应认为是本发明的保护范围。
再多了解一些
本文用于创业者技术爱好者查询,仅供学习研究,如用于商业用途,请联系技术所有人。