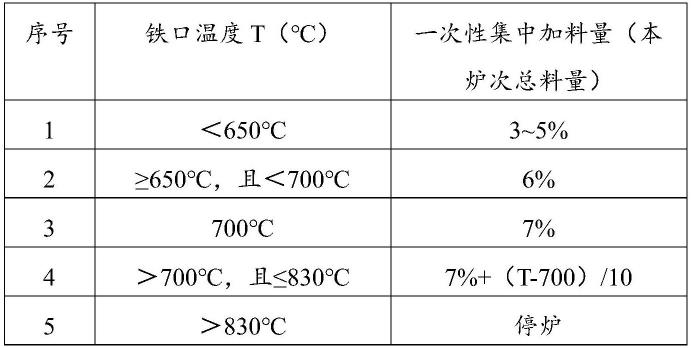
1.本发明属于钛白粉制备技术领域,具体涉及了一种用于钛渣炉炉底温度控制的加料方法。
背景技术:
2.现有技术在钛渣冶炼过程中,炉内长期处于较高的温度状态,对炉底炉墙冲击较大,虽炉墙使用耐火镁砖砌筑,但长期高功率送电生产,仍会使炉底死铁层趋活熔化、炉墙变薄,存在很大风险,生产中不得不采取停电凉炉的措施来抑制这种风险。凉炉短则5天,长则半月时间,不能满足连续生产的要求,严重影响生产及产量。
3.申请人自2014年开始采用钛铁矿由钛渣炉生产钛渣,一直采用传统的加料方式,即连续均匀加料,将本炉次总料量均匀分配到每小时。这种加料方式,存在很大缺陷:电炉出渣作业后渣液位相对较低,热量对炉底冲击很大,极易使炉底死铁层熔化,炉墙温度升高(尤其是铁口处温度迅速上升),甚至出现穿炉的风险。
技术实现要素:
4.本发明的目的就在于为解决现有技术的不足而提供一种用于钛渣炉炉底温度控制的加料方法。
5.本发明的目的是以下述技术方案实现的:
6.一种用于钛渣炉炉底温度控制的加料方法,包括以下步骤:
7.检测上一炉次出渣后液位最低时铁口温度t;
8.当所述铁口温度t<第一预设温度t1时,向钛渣炉内一次性集中加入第一预设料量m1,然后将本炉次剩余料量根据本炉次生产时间连续均匀给料;
9.当所述铁口温度t=第一预设温度t1时,向钛渣炉内一次性集中加入第二预设料量m2,然后将本炉次剩余料量根据本炉次生产时间连续均匀给料;
10.当所述铁口温度t>第一预设温度t1,且≤第二预设温度t2时,根据所述铁口温度t相比所述第一预设温度t1的增加量,以所述第二预设料量m2为起点,对应增加一次性集中加入的料量,然后将本炉次剩余料量根据本炉次生产时间连续均匀给料;
11.当所述铁口温度t>第二预设温度t2时,停炉停止加料。
12.优选的,所述第一预设温度t1为650~700℃,所述第一预设料量m1为本炉次总料量的3~6%;
13.所述第二预设料量m2为本炉次总料量的7~10%,所述铁口温度t每超过第一预设温度t
1 8~12℃时,加入的料量相比第二预设料量m2增加本炉次料量的0.8~1.2%;
14.所述第二预设温度t2为820~850℃。
15.优选的,所述向钛渣炉内一次性集中加入的料量上限不超过本炉次总料量的20%。
16.优选的,所述第一预设温度t1为700℃,所述第二预设温度t2为830℃;
17.根据检测得到的所述铁口温度t与一次性集中加料量对应关系如表1所示:
18.表1
[0019][0020]
优选的,所述一次性集中加料时间限定为≤15min。
[0021]
优选的,所述钛渣炉冶炼温度为1600~1700℃。
[0022]
优选的,所述向钛渣炉内加入的原料为粉状钛铁矿,所述粉状钛铁矿粒度为: 40目≤0,-160目≤20%。
[0023]
本技术采用先集中给料以及后连续给料结合的方式,可有效阻挡热量对炉底的冲击,使钛渣炉得以长期稳定运行。
具体实施方式
[0024]
本技术提供了一种用于钛渣炉炉底温度控制的加料方法,包括以下步骤:
[0025]
检测上一炉次出渣后液位最低时铁口温度t;
[0026]
当铁口温度t<第一预设温度t1时,向钛渣炉内一次性集中加入第一预设料量m1,然后将本炉次剩余料量根据本炉次生产时间连续均匀给料;
[0027]
当铁口温度t=第一预设温度t1时,向钛渣炉内一次性集中加入第二预设料量m2,然后将本炉次剩余料量根据本炉次生产时间连续均匀给料;
[0028]
当铁口温度t>第一预设温度t1,且≤第二预设温度t2时,根据铁口温度t相比第一预设温度t1的增加量,以第二预设料量m2为起点,对应增加一次性集中加入的料量,然后将本炉次剩余料量根据本炉次生产时间连续均匀给料;
[0029]
当铁口温度t>第二预设温度t2时,停炉停止加料。
[0030]
申请人在实际生产中发现,在出渣后,采用集中给料以及连续给料结合的方式,可有效减少高温对炉底的冲击。具体的,首先在出渣后一次性集中加入一定的钛铁矿,该加入的钛铁矿可以有效吸收并阻挡热量对炉底的冲击,然后再将本炉次剩余的料量连续均匀分配加入炉内。并同时对一次性集中加入的料量根据出铁口温度进行优化,当出铁口温度相对较低时,加入少量的钛铁矿即可有效吸收阻挡热量对炉底的冲击,当出铁口温度较高时,随着出铁口温度的升高,相应的增加该一次性集中加入的料量,以吸收多余的热量,但是当温度继续提高超过设定限值时,一方面在高温下生产容易出现事故,另一方面,一次性加入过多的钛铁矿将会产生堆料,影响正常冶炼。而且经过验证,一次性集中加料量主要与铁口温度有关,钛渣炉内径和出渣后液位对加料量影响不显著,当钛渣炉内径较大、或出渣后液
位较低时,一次性集中加料量可适当多添加一些。
[0031]
因此,本技术采用先集中给料以及后连续给料结合的方式,可有效阻挡热量对炉底的冲击,使钛渣炉得以长期稳定运行。
[0032]
上述第一预设温度t1、第一预设料量m1等参数可根据实际生产情况进行相应地调整。
[0033]
本技术提供一种优选的实施例,其中第一预设温度t1为650~700℃,第一预设料量m1为本炉次总料量的3~6%;
[0034]
第二预设料量m2为本炉次总料量的7~10%,铁口温度t每超过第一预设温度t
1 8~12℃时,加入的料量相比第二预设料量m2增加本炉次料量的0.8~1.2%;
[0035]
第二预设温度t2为820~850℃;在上述温度范围内,采用对应的一次性集中加料量可有效吸收热量,发挥作用。当温度大于820~850℃时,集中加料后仍不能抑制温度上升的趋势,就需要停炉,以防出现穿炉等恶性事故。若一次性集中加料量<3%,则钛渣炉出铁口温度将逐渐上升,得不到抑制。
[0036]
进一步优选的,本技术提供一种典型的实施例,其中第一预设温度t1为700℃,第二预设温度t2为830℃;
[0037]
根据检测得到的铁口温度t与一次性集中加料量对应关系如表1所示:
[0038]
表1
[0039][0040]
优选的,一次性集中加料时间限定为≤15min,进一步优选为3~5min。
[0041]
优选的,向钛渣炉内一次性集中加入的料量上限不超过本炉次料量的20%,经过试验验证,当钛铁矿一次性加料超过20%时,将会产生堆料,影响正常冶炼。
[0042]
优选的,钛渣炉冶炼温度为1600~1700℃。
[0043]
优选的,向钛渣炉内加入的原料为粉状钛铁矿,粉状钛铁矿粒度为: 40目≤0,-160目≤20%,相比块状料粉状钛铁矿可更好的熔化还原并吸收热量。
[0044]
实施例1
[0045]
申请人自2014年开始一直采用33mva全密闭电炉(炉膛砌筑内径9.8m,出渣后炉内液位一般为3.0m左右,冶炼温度1650℃左右)进行钛铁矿冶炼,加料一直采用传统的连续均匀给料方法,这种加料方式周期性地造成炉底活跃,炉墙温度升高,当铁口温度超过830℃停炉,每次停炉6~10d,每月影响产量2500吨左右,同时造成生产成本的大幅度增加,是制约钛渣生产的瓶颈。而在铁口温度超过600℃时,虽然未进行停炉,但是就存在穿炉的风险,
而且温度越高,风险越大。
[0046]
自2022年初采用本实施例提供的加料方法进行加料,具体如下:
[0047]
上一炉次出渣后,检测铁口温度t,采用表1所示的对照表首先进行一次性加料(粉状钛铁矿,粒度为 40目≤0,-160目≤20%),然后将本炉次剩余料量根据本炉次生产时间连续均匀给料,具体加料过程如下:
[0048]
第一炉次(本炉次总料量为150吨,生产时间为10h):上一炉次出渣后检测铁口温度为:720℃,在15分钟内一次性加入本炉次总料量9%的钛铁矿,将剩余91%的料量连续分配给剩下9.75h;
[0049]
第二炉次(本炉次总料量为150吨,生产时间为10h):上一炉次出渣后检测铁口温度为:705℃,在15分钟内一次性加入本炉次总料量7.5%的钛铁矿,将剩余92.5%的料量连续分配给剩下9.75h;
[0050]
第三炉次(本炉次总料量为150吨,生产时间为10h):上一炉次出渣后检测铁口温度为:680℃,在15分钟内一次性加入本炉次总料量6%的钛铁矿,将剩余94%的料量连续分配给剩下9.75h;
[0051]
第四炉次(本炉次总料量为150吨,生产时间为10h):上一炉次出渣后检测铁口温度为:650℃,在15分钟内一次性加入本炉次总料量6%的钛铁矿,将剩余94%的料量连续分配给剩下9.75h;
[0052]
第五炉次(本炉次总料量为150吨,生产时间为10h):上一炉次出渣后检测铁口温度为:630℃,在15分钟内一次性加入本炉次总料量5%的富钛料,将剩余95%的料量连续分配给剩下9.75h;
[0053]
……
[0054]
第八炉次(本炉次总料量为150吨,生产时间为10h):上一炉次出渣后检测铁口温度为:570℃,在15分钟内一次性加入本炉次总料量3%的富钛料,将剩余97%的料量连续分配给剩下9.75h;
[0055]
持续按照上述方法进行加料,连续运行半年,未发生因炉底活跃、铁口温度高而导致的停炉,目前铁口温度一直稳定维持在500℃左右。
[0056]
实施例2
[0057]
本实施例提供的加料方法,包括以下步骤:
[0058]
上一炉次(该钛渣炉规格同实施例1)出渣后,检测铁口温度为745℃,在15分钟内一次性加入本炉次总料量11.5%的钛铁矿(本炉次生产时间8h,总料量120吨),将剩余88.5%的料量连续分配给剩下7.75h,该炉次出渣后,检测铁口温度下降20℃,持续按照如表1所示的对照表进行加料,在12炉次后铁口温度稳定保持为500℃左右。
[0059]
实施例3
[0060]
本实施例提供的加料方法,包括以下步骤:
[0061]
上一炉次(该钛渣炉为33mva全密闭电炉,炉膛内径11.1m,出渣后炉内液位一般为3.0m左右,冶炼温度1650℃左右)出渣后,检测铁口温度为750℃,在15分钟内一次性加入本炉次总料量13%的钛铁矿(本炉次生产时间12h,总料量180吨),将剩余87%的料量连续分配给剩下11.75h,该炉次出渣后,检测铁口温度下降18℃,持续按照如表2所示的对照表进行加料,在15炉次后铁口温度稳定保持为500℃左右。
[0062]
表2
[0063][0064]
尽管已描述了本发明的优选实施例,但本领域内的技术人员一旦得知了基本创造性概念,则可对这些实施例作出另外的变更和修改。所以,所附权利要求意欲解释为包括优选实施例以及落入本发明范围的所有变更和修改。显然,本领域的技术人员可以对本发明进行各种改动和变型而不脱离本发明的精神和范围。这样,倘若本发明的这些修改和变型属于本发明权利要求及其等同技术的范围之内,则本发明也意图包含这些改动和变型在内。
再多了解一些
本文用于创业者技术爱好者查询,仅供学习研究,如用于商业用途,请联系技术所有人。