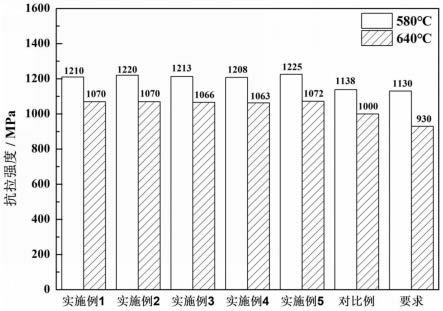
1.本发明涉及耐热钢制造工艺领域,尤其涉及一种高性能马氏体耐热钢及其制备方法。
背景技术:
2.发动机承力件在服役过程中需承受的离心负荷、振动负荷、外物冲击、环境侵蚀和不稳定热应力等,工作环境较为恶劣。此前主要采用俄罗斯的эп479合金制作发动机承力件,国内生产的发动机承力件的性能无法达到设计要求。有研究人员依据有关的俄罗斯标准进行该材料的试制,但在试制过程中发现,材料在550℃~590℃回火的室温性能满足设计要求,640℃~660℃回火后除室温疲劳性能外,室温拉伸性能、室温冲击韧性以及在长期高温服役后的室温力学性能均无法满足设计要求。
3.鉴于上述情况,亟待研发一款性能优异的发动机承力件用马氏体耐热钢,寻求一种合理的制备方法,既能确保马氏体耐热钢的稳定化生产,又能使其力学性能满足发动机承力件的设计要求。
4.常见的马氏体耐热不锈钢通过时效处理析出富铜相和二次硬化相,提高材料的力学性能。但脱铜问题是一个世界性难题,目前,未有一种能够广泛用于生产的脱铜方法。本发明取缔了富铜相时效强化的设计思路,通过提高钢中碳元素和钼元素含量,析出不易长大的m2c 型碳化物,抑制m
23
c6型碳化物的形成长大,不仅降低钢中铜元素的用量,还能进一步提高材料塑韧性,满足发动机承力件的设计要求。
技术实现要素:
5.为实现高端发动机承力件用钢国产化,本发明提供了一种高性能马氏体耐热钢及其制备方法,通过设计合金成分,提高钢中碳元素和钼元素含量,并采用真空感应冶炼、电渣重熔、热加工锻造、热加工轧制、去应力退火制备而成,不仅使该高性能马氏体耐热钢满足设计所需的力学性能,还能够实现稳定化生产,满足当前国内发动机承力件对于高性能马氏体耐热钢的现实需求。
6.为了实现上述目的,本发明采用如下的技术方案:
7.本发明的第一方面提供了一种高强度铁素体不锈钢,包括按质量百分比计的以下成分: c:0.06~0.20%、si≤0.60%、mn≤0.60%、s:≤0.020%、p:≤0.030%、cr:15.00~16.50%、ni:2.00~2.50%、mo:0.90~1.30%、v:0.10~0.20%、n:0.03~0.10%,余量为fe。
8.优选地,所述高强度铁素体不锈钢包括按质量百分比计的以下成分:c:0.12~0.18%、 si:0.20~0.40%、mn:0.45~0.58%、s:≤0.015%、p:≤0.020%、cr:15.10~15.80%、ni:2.20~ 2.50%、mo:1.10~1.30%、v:0.10~0.20%、n:0.03~0.10%,余量为fe。
9.以易切削钢为代表的发明往往着重于某一元素对材料的作用,本发明更强调各元
素之间的协调和配合,本优选组分是经多轮次生产数据总结而得到的。
10.优选地,所述高性能马氏体耐热钢在不同热处理条件下需同时满足如下两项性能指标:
11.(1)在550℃~590℃回火/时效后,其屈服强度≥930mpa,抗拉强度≥1130mpa,延伸率≥12%,断面收缩率≥58%,u型缺口冲击吸收能量≥55j,硬度为302~375hb。
12.(2)在640℃~680℃回火/时效后,其屈服强度≥735mpa,抗拉强度≥930mpa,延伸率≥14%,断面收缩率≥55%,u型缺口冲击吸收能量≥55j,硬度为277~341hb。
13.本发明的第二方面提供一种高性能马氏体耐热钢的制备方法,原料根据本发明第一方面所述的高性能马氏体耐热钢的成分进行配比,然后依次经真空感应冶炼、电渣重熔、热加工锻造、热加工轧制和去应力退火制得高性能马氏体耐热钢。
14.s1,真空感应冶炼、模铸,将所述原料采用真空感应炉熔炼成钢液,并调整钢液中的各成分至目标值后控温出钢,出钢温度≥1540℃;
15.s2,电渣重熔、去应力退火,采用caf
2-al2o3渣系进行电渣重融,随后在730~830℃进行去应力退火;
16.s3,精整、锻造、去应力退火,对所述铸锭精整后,在1120~1200℃条件下进行高温均匀化处理,然后在温度≤1100℃条件下锻造加工成锻件;随后在630~700℃进行去应力退火;
17.s4,热轧、去应力退火,将所述锻件加热至1120~1200℃温度后进行轧制得到轧件,控制终轧温度900℃~1200℃;所述轧件在630~700℃进行去应力退火得到高性能马氏体耐热钢。
18.优选地,所述步骤s1中,出钢时,控制所述钢液中的成分按质量百分数计在以下范围内:c≤0.03wt%,si≤0.40wt%,mn≤0.50wt%,cr:19.00~21.00wt%,ni:17.00~19.00wt%, mo:5.50~7.50wt%,cu:0.50~1.00wt%,余量为fe。
19.优选地,所述步骤s1中,熔炼全程真空度应低于7.0
×
10-2
mbar。
20.优选地,所述步骤s1中,浇铸前进行2~4次搅拌,控制搅拌功率在0~250kw之间周期变化。
21.优选地,所述步骤s2中,caf
2-al2o3渣系中caf2的含量为60~75%,渣量应≥35kg。
22.优选地,所述步骤s2中,去应力退火保温时间为10~18小时。
23.优选地,所述步骤s3中,所述高温均匀化过程中,保温时间≥1小时。在不考虑氧化烧损和成本的条件下,一般来说,高温均匀化处理的保温时间越长越好。
24.优选地,所述步骤s3中,所述锻造过程中,采用2火次以上进行锻造,终锻温度800℃~ 1100℃,最后一火变形量≥20%。由于锻造温度需小于1100℃,锻造过程中温度只会降低,所以锻件终轧温度低于其加热温度(1100)。
25.优选地,所述步骤s3中,去应力退火保温时间为20~30小时。
26.优选地,所述步骤s4中,加热时间≥2小时。
27.优选地,所述步骤s4中,所述轧制采用2火次轧制。
28.优选地,所述步骤s4中,去应力退火保温时间为20~30小时。
29.本发明中热处理工艺参数范围是基于材料的重量、尺寸(厚度)而选择的。锻造工艺参数是通过理论计算和实验验证得到的。
30.本发明的高性能马氏体耐热钢的成分设计的原则如下:
31.c:碳是钢中常见的元素,可以通过固溶强化或通过形成碳化物,有效提高材料的力学性能,但过高的碳元素含量将降低钢中m6c型碳化物的含量,提高钢中m
23
c6型碳化物的含量,从而降低基体中固溶的铬元素含量,影响材料的强韧性配比和耐腐蚀性能;此外碳元素还能提高钢中碳元素含量将提高室温条件下奥氏体含量,降低铁素体含量,然而其影响程度相对较小;综上所述,本发明将钢中碳含量不得高于0.20%。
32.si:硅元素是矿石原料中常见的合金元素,硅易与氧原子结合形成二氧化硅,提高钢的抗氧化性能,提高氧化膜的耐腐蚀性能和抗点蚀性能;其具备较强的固溶强化效果,过量的 si元素含量将大幅提高材料的脆性,所以,本发明将钢中硅元素含量的上限值定为0.60%。
33.mn:众所周知,提高钢的抗点蚀和抗裂纹腐蚀性能。然而提高锰元素含量将降低钢的耐腐蚀性能和焊接性能,并与s元素形成mns夹杂物,控制合金的再结晶结构;因此,本发明将钢中锰含量不得高于0.60%。
34.cr:铬是不锈钢中主要的合金元素,钢中铬元素含量与钢的耐腐蚀性能之间存在1/8定律,提高钢中的铬元素含量是提升钢的耐腐蚀性能最有效的办法。然而铬元素是强烈的铁素体形成元素,过高的铬元素含量将提高钢中高温铁素体含量,并促进m
23
c6型碳化物的形成,不利于材料的力学性能和耐腐蚀性能。因此,本发明将钢中铬元素含量限制为15.00~ 16.50%。
35.ni:镍元素是奥氏体形成元素,提高镍元素含量将提高钢中残余奥氏体含量,少量的残余奥氏体可以阻碍裂纹的扩展,有利于提高材料的韧性;但在凝固过程中,镍元素易于偏析,影响材料的组织均匀性,所以,本发明将钢中镍元素含量限制为2.00~2.50%。
36.mo:钼元素是不锈钢中主要的合金元素,钼元素能提高钝化膜中铬原子的密度,进一步提高钝化膜的抗点蚀能力,延长点蚀的孕育期;此外,钼的原子尺寸较大,扩散激活能较高,延迟m
23
c6型碳化物析出,有利于提高碳化物的析出强化效果;但在凝固过程中,过高的钼元素含量将大幅降低马氏体开始转变温度,降低钢中马氏体含量,使时效后材料无法达到目标硬度,因此,本发明将钢中钼元素含量限制为0.90~1.30%。
37.n:提高本钢中的氮元素含量将提高钢中铁素体含量,有利于提高材料的冲击韧性;但是氮在钢中容易出现偏析和气孔,降低铸件的探伤合格率。所以,本发明将钢中氮元素含量限制为0.03~0.10%。
38.与现有技术相比,本发明的有益效果为:
39.本发明的高性能马氏体耐热钢及其制备方法通过设计合金成分,并采用真空感应冶炼、电渣重熔、热加工锻造、热加工轧制、去应力退火制备而成,不仅降低钢中铜元素的用量,还能进一步提高材料塑韧性,满足发动机承力件用钢的设计要求。
附图说明
40.通过阅读参照以下附图对非限制性实施例所作的详细描述,本发明的其它特征、目的和优点将会变得更明显:
41.图1为本发明实施例1~5以及对比例在室温且不同热处理工艺下的屈服强度对比图。
42.图2为本发明实施例1~5以及对比例在室温且不同热处理工艺下的抗拉强度对比图。
43.图3为本发明实施例1~5以及对比例在室温且不同热处理工艺下的延伸率对比图。
44.图4为本发明实施例1~5以及对比例在室温且不同热处理工艺下的断面收缩率对比图。
45.图5为本发明实施例1~5在不同热处理室温且工艺下的冲击吸收能量对比图。
46.图6为本发明实施例1~5以及对比例在室温且不同热处理工艺下的布氏硬度对比图。
具体实施方式
47.下面结合具体实施例对本发明进行详细说明。以下实施例将有助于本领域的技术人员进一步理解本发明,但不以任何形式限制本发明。
48.本发明所提供的高性能马氏体耐热钢,包括按质量百分比计的以下成分:c:0.06~ 0.20%、si≤0.60%、mn≤0.60%、s:≤0.020%、p:≤0.030%、cr:15.00~16.50%、ni:2.00~ 2.50%、mo:0.90~1.30%、v:0.10~0.20%、n:0.03~0.10%,余量为fe。在进一步的优选方案中,该高性能马氏体耐热钢包括按质量百分比计的以下成分:c:0.12~0.18%、si:0.20~ 0.40%、mn:0.45~0.58%、s:≤0.015%、p:≤0.020%、cr:15.10~15.80%、ni:2.20~2.50%、 mo:1.10~1.30%、v:0.10~0.20%、n:0.03~0.10%,余量为fe。原料选用硅铁矿、金属 mn、金属cr、金属ni、金属mo和钒铁矿,不刻意添加s和p元素。
49.上述高性能马氏体不锈钢通过以下制备方法制得,将硅铁矿、金属mn、金属cr、金属 ni等根据高性能马氏体不锈钢的成分配比得到原料,然后依次经真空感应冶炼、电渣重熔、热加工锻造、热加工轧制和去应力退火制得高性能马氏体不锈钢;具体制备方法如下:
50.(1)真空感应冶炼、模铸,将所述原料采用真空感应炉熔炼成钢液,并调整钢液中的各成分至目标值后控温出钢,出钢温度≥1540℃;
51.(2)电渣重熔、去应力退火,采用caf
2-al2o3渣系进行电渣重融,随后在730~830℃进行去应力退火;
52.(3)精整、锻造、去应力退火,对所述铸锭精整后,在1120~1200℃条件下进行高温均匀化处理,然后在温度≤1100℃条件下锻造加工成锻件;随后在630~700℃进行去应力退火;
53.(4)热轧、去应力退火,将所述锻件加热至1120~1200℃温度后进行轧制得到轧件,控制终轧温度≥900℃;所述轧件在630~700℃进行去应力退火得到高性能马氏体耐热钢。
54.上述过程中制备的高性能马氏体耐热钢不锈钢在不同热处理条件下同时满足如下两项性能指标:
55.(1)在550℃~590℃回火/时效后,其屈服强度≥930mpa,抗拉强度≥1130mpa,延伸率≥12%,断面收缩率≥58%,u型缺口冲击吸收能量≥55j,硬度为302~375hb。
56.(2)在640℃~680℃回火/时效后,其屈服强度≥735mpa,抗拉强度≥930mpa,延伸率≥14%,断面收缩率≥55%,u型缺口冲击吸收能量≥55j,硬度为277~341hb。
57.下面结合具体例子进一步对本发明的高性能马氏体耐热钢及其制备方法进行说明。
58.实施例1
59.本实施例中高性能马氏体耐热钢的成分及质量分数如表1所示;
60.本实施例中的高性能马氏体耐热钢采用一下步骤制备而成:
61.(1)原料配比:硅铁矿、金属mn、金属cr、金属ni等根据表1中实施例1的高性能马氏体耐热钢的成分进行配比得到原料;
62.(2)真空感应冶炼:将上述配比的原料添加至真空感应炉中冶炼,熔炼全程真空度≤ 5.0
×
10-2
mbar,在浇铸前需要进行3次搅拌,其中搅拌功率在0~250kw之间周期变化;
63.(3)电渣重熔:采用caf
2-al2o3渣系进行电渣重融渣系中caf2的含量为65%,渣量应为40kg,随后在750℃进行去应力退火,去应力退火保温时间为16小时;
64.(4)热加工锻造:对所述电渣锭精整后加热至1150℃后进行高温均匀化处理,保温时间1.5小时,然后在温度1060℃条件下2火次锻造加工成锻件,终锻温度为850℃;随后在 650℃进行去应力退火,退火保温时间为25小时;
65.(5)热加工轧制:将所述锻件加热至1150℃,加热时间为2小时,随后进行2火次轧制得到轧件,终轧温度为850℃;
66.(6)去应力退火:所述轧件在650℃进行去应力退火,退火保温时间为25小时,得到高性能马氏体耐热钢。
67.经检测,上述制备的高性能马氏体耐热钢的性能如下:
[0068][0069]
实施例2
[0070]
本实施例中高性能马氏体耐热钢的成分及质量分数如表1所示;
[0071]
本实施例中的高性能马氏体耐热钢采用一下步骤制备而成:
[0072]
(1)原料配比:硅铁矿、金属mn、金属cr、金属ni等根据表2中实施例1的高性能马氏体耐热钢的成分进行配比得到原料;
[0073]
(2)真空感应冶炼:将上述配比的原料添加至真空感应炉中冶炼,熔炼全程真空度≤ 4.5
×
10-2
mbar,在浇铸前需要进行4次搅拌,其中搅拌功率在0~250kw之间周期变化;
[0074]
(3)电渣重熔:采用caf
2-al2o3渣系进行电渣重融渣系中caf2的含量为72%,渣量为 45kg,随后在780℃进行去应力退火,去应力退火保温时间为15小时;
[0075]
(4)热加工锻造:对所述电渣锭精整后加热至1180℃后进行高温均匀化处理,保温时间为2小时,然后在温度为1070℃条件下2火次锻造加工成锻件,终锻温度为870℃;随后在680℃进行去应力退火,退火保温时间为27小时;
[0076]
(5)热加工轧制:将所述锻件加热至1180℃,加热时间为2小时,随后进行2火次轧制得到轧件,终轧温度为900℃;
[0077]
(6)去应力退火:所述轧件在680℃进行去应力退火,退火保温时间为27小时,得到高性能马氏体耐热钢。
[0078]
经检测,上述制备的高性能马氏体耐热钢的性能如下:
[0079][0080]
实施例3
[0081]
本实施例中高性能马氏体耐热钢的成分及质量分数如表1所示;
[0082]
本实施例中的高性能马氏体耐热钢采用一下步骤制备而成:
[0083]
(1)原料配比:硅铁矿、金属mn、金属cr、金属ni等根据表1中实施例3的高性能马氏体耐热钢的成分进行配比得到原料;
[0084]
(2)真空感应冶炼:将上述配比的原料添加至真空感应炉中冶炼,熔炼全程真空度≤ 7.0
×
10-2
mbar,在浇铸前需要进行2次搅拌,其中搅拌功率在0~250kw之间周期变化;
[0085]
(3)电渣重熔:采用caf
2-al2o3渣系进行电渣重融渣系中caf2的含量为63%,渣量为 50kg,随后在740℃进行去应力退火,去应力退火保温时间为14小时;
[0086]
(4)热加工锻造:对所述电渣锭精整后加热至1160℃后进行高温均匀化处理,保温时间为1.5小时,然后在温度为1090℃条件下2火次锻造加工成锻件,终锻温度为850℃;随后在640℃进行去应力退火,退火保温时间为23小时;
[0087]
(5)热加工轧制:将所述锻件加热至1160℃,加热时间为2小时,随后进行2火次轧制得到轧件,终轧温度为850℃;
[0088]
(6)去应力退火:所述轧件在640℃进行去应力退火,退火保温时间为23小时,得到高性能马氏体耐热钢。
[0089]
经检测,上述制备的高性能马氏体耐热钢的性能如下:
[0090][0091]
实施例4
[0092]
本实施例中高性能马氏体耐热钢的成分及质量分数如表1所示;
[0093]
本实施例中的高性能马氏体耐热钢采用一下步骤制备而成:
[0094]
(1)原料配比:硅铁矿、金属mn、金属cr、金属ni等根据表1中实施例4的高性能马氏体耐热钢的成分进行配比得到原料;
[0095]
(2)真空感应冶炼:将上述配比的原料添加至真空感应炉中冶炼,熔炼全程真空度
应≤4.5
×
10-2
mbar,在浇铸前需要进行4次搅拌,其中搅拌功率在0~250kw之间周期变化;
[0096]
(3)电渣重熔:采用caf
2-al2o3渣系进行电渣重融渣系中caf2的含量为72%,渣量为 38kg,随后在780℃进行去应力退火,去应力退火保温时间为12小时;
[0097]
(4)热加工锻造:对所述电渣锭精整后加热至1170℃后进行高温均匀化处理,保温时间为1.5小时,然后在温度为1080℃条件下2火次锻造加工成锻件,终锻温度为900℃;随后在680℃进行去应力退火,退火保温时间为27小时;
[0098]
(5)热加工轧制:将所述锻件加热至1170℃,加热时间为2.5小时,随后进行2火次轧制得到轧件,终轧温度为900℃;
[0099]
(6)去应力退火:所述轧件在680℃进行去应力退火,退火保温时间为27小时,得到高性能马氏体耐热钢。
[0100]
经检测,上述制备的高性能马氏体耐热钢的性能如下:
[0101][0102]
实施例5
[0103]
本实施例中高性能马氏体耐热钢的成分及质量分数如表1所示;
[0104]
本实施例中的高性能马氏体耐热钢采用一下步骤制备而成:
[0105]
(1)原料配比:硅铁矿、金属mn、金属cr、金属ni等根据表1中实施例5的高性能马氏体耐热钢的成分进行配比得到原料;
[0106]
(2)真空感应冶炼:将上述配比的原料添加至真空感应炉中冶炼,熔炼全程真空度应≤6.5
×
10-2
mbar,在浇铸前需要进行2次搅拌,其中搅拌功率在0~250kw之间周期变化;
[0107]
(3)电渣重熔:采用caf
2-al2o3渣系进行电渣重融渣系中caf2的含量为65%,渣量为 45kg,随后在740℃进行去应力退火,去应力退火保温时间为16小时;
[0108]
(4)热加工锻造:对所述电渣锭精整后加热至1140℃后进行高温均匀化处理,保温时间为2小时,然后在温度为1070℃条件下2火次锻造加工成锻件,终锻温度为850℃;随后在650℃进行去应力退火,退火保温时间为22小时;
[0109]
(5)热加工轧制:将所述锻件加热至1140℃,加热时间为2.5小时,随后进行2火次轧制得到轧件,终轧温度为850℃;
[0110]
(6)去应力退火:所述轧件在650℃进行去应力退火,退火保温时间为22小时,得到高性能马氏体耐热钢。
[0111]
经检测,上述制备的高性能马氏体耐热钢的性能如下:
[0112][0113]
对比例
[0114]
本对比例为17-4ph钢,其成分及质量分数如表1所示;
[0115]
经检测,其性能如下:
[0116][0117]
表1实施例1~5制备的铁素体不锈钢以及对比例中的铁素体不锈钢的成分(wt%)
[0118][0119][0120]
由图1,明显可以看出,实施例1~5制备的高性能马氏体耐热钢不锈钢的屈服强度略低于对比例,但其性能远超叶片钢设计性能要求;由图2可知,实施例1~5制备的高性能马氏体耐热钢的抗拉强度远高于对比例和设计性能要求;由图3可知,实施例1~5制备的高性能马氏体耐热钢的延伸率高于对比例,远超设计性能要求;由图4可知,实施例1~5 制备的高性能马氏体耐热钢的断面收缩率满足设计性能要求;由图5可知,实施例1~5制备的高
性能马氏体耐热钢的冲击吸收能量远高于设计性能要求;由图6可知,实施例1~5 制备的高性能马氏体耐热钢的布氏硬度远高于对比例和设计性能要求。
[0121]
综上所述,本发明的高性能马氏体耐热钢及其制备方法通过设计合金成分,并采用真空感应冶炼、电渣重熔、热加工锻造、热加工轧制、去应力退火制备而成,不仅降低增碳对材料耐腐蚀性能的影响,还能进一步提高材料塑韧性,满足发动机承力件用钢的设计要求。
[0122]
综上所述,上述实施例仅用于说明本发明的技术方案而非限制,尽管参照较佳实施例对本发明进行了详细说明,本领域的普通技术人员应当理解,可以对本发明的技术方案进行修改或者等同替换,而不脱离本发明技术方案的宗旨和范围,其均应涵盖在本发明的权利要求范围当中。
再多了解一些
本文用于创业者技术爱好者查询,仅供学习研究,如用于商业用途,请联系技术所有人。