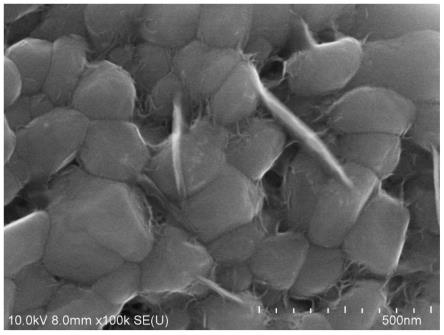
1.本发明涉及锂离子电池正极材料技术领域,特别涉及一种表面包覆锂离子导体的体相掺杂三元正极材料及其制备方法和应用。
背景技术:
2.随着新能源汽车市场对续航里程要求越来越高,锂离子动力电池也不断地向更高能量密度的方向发展,这就要求正极材料也要具有更高的能量密度。然而,目前已商业化的三元正极材料已经不能满足锂离子动力电池对能量密度的需求。增加镍元素的含量可以提高三元正极材料的能量密度,进而提高动力电池的能量密度。但与目前已商业化的成熟三元正极材料相比,由于镍含量的大幅升高使其循环稳定性和热稳定性变得更差。
3.体相掺杂结合表面包覆改性可以进一步改善高镍三元正极材料的电化学性能及安全性能。然而,目前的掺杂和包覆双改性工艺是独立进行的,例如,专利cn109879331a公开了一种将三元正极材料氢氧化物前驱体、锂源以及掺杂元素氧化物混合后高温固相烧结,先制备出掺杂型的三元正极材料,再通过溶胶-凝胶法或高温固相法合成出磷酸盐锂离子导体(li
1 aaad2-a
(po4)3,经高温烧结制备出了体相多元素掺杂且表面包覆磷酸盐锂离子导体的三元正极材料;专利cn108878799a公开了一种通过原位掺杂共沉淀-高温固相法获得掺杂型的镍钴锰酸锂三元正极材料,再通过模板-溶胶/凝胶-低温回火工艺于掺杂型正极材料表面包覆具有高速锂离子和电子通道的介孔硅酸铝锂包覆层,制备出体相掺杂多元素且表面包覆介孔硅酸铝锂锂离子导体(lialsi2o6)的三元正极材料。然而,以上分别进行掺杂和包覆的方案都存在着过程繁琐,所得产品结构不稳定的缺陷,导致三元正极材料的电化学稳定性不佳。
技术实现要素:
4.有鉴于此,本发明目的在于提供一种表面包覆锂离子导体的体相掺杂三元正极材料及其制备方法和应用,方法简单,所得三元正极材料的结构稳定性好,电化学稳定性高。
5.为了实现上述发明目的,本发明提供以下技术方案:
6.本发明提供了一种表面包覆锂离子导体的体相掺杂三元正极材料的制备方法,包括以下步骤:
7.将可溶性镍盐、可溶性钴盐和水混合,得到混合盐溶液;所述混合盐溶液中镍离子与钴离子的摩尔比为0.9~1:0.01~0.1;
8.将所述混合盐溶液、vib族金属源、沉淀剂、络合剂和水混合,进行共沉淀反应,得到氢氧化物前驱体,所述vib族金属源为钼源或钨源;
9.将所述氢氧化物前驱体、掺杂元素的可溶性盐与溶剂混合,进行水解反应,得到表面包覆锂离子导体前躯体的氢氧化物前驱体;所述掺杂元素为b、ti、al、nb、sb、sn、si、ge和zr的一种或几种;所述溶剂为水和/或醇;
10.将所述表面包覆锂离子导体前躯体的氢氧化物前驱体进行加热氧化,得到氧化物前驱体;
11.将所述氧化物前驱体与锂盐混合,进行烧结,得到表面包覆锂离子导体的体相掺杂三元正极材料。
12.优选的,所述沉淀剂为氢氧化钠、氢氧化钾、碳酸钠和碳酸氢钠中的一种或几种;
13.所述络合剂为氨水、乙二胺四乙酸二钠、柠檬酸、柠檬酸钠、草酸和草酸钠中的一种或几种。
14.优选的,所述混合盐溶液中的总金属离子与vib族金属源中vib族金属离子的摩尔比为0.93~0.99:0.01~0.07;
15.所述沉淀反应的温度为35~85℃,时间为5~80h。
16.优选的,所述氢氧化物前驱体中的总金属离子与掺杂元素离子的摩尔比为0.95~0.995:0.005~0.05。
17.优选的,所述水解反应的温度为60~95℃,时间为1~5h。
18.优选的,所述加热氧化的温度为400~600℃,时间为1~10h。
19.优选的,所述氧化物前驱体中总金属离子与锂盐中锂离子的摩尔比为1:1~1.3;
20.所述烧结的温度为600~820℃,时间为10~20h。
21.本发明提供了上述制备方法制备得到的表面包覆锂离子导体的体相掺杂三元正极材料,包括体相掺杂的三元正极材料和包覆在所述体相掺杂的三元正极材料表面的锂离子导体层;
22.所述体相掺杂的三元正极材料包括三元正极材料基体和体相掺杂于所述三元正极材料基体中的掺杂元素,所述三元正极材料的化学组成为lini
x
coymo
1-x-y
o2或lini
x
coyw
1-x-y
o2,其中0.9≤x《1.0,0.01≤y《0.1,且x y《1;
23.所述掺杂元素为b、ti、al、nb、sb、sn、si、sc、y、ge和zr的一种或几种;
24.所述锂离子导体层的化学组成为li3bo3、li2wo4、li2moo4、li2tio3、lialo2、linbo3、lisbo3、li2sno3、li4sio4、li2geo3、li2zro3、li3po4、li
1.3
al
0.3
ti
1.7
(po4)3、li
1.8
sc
0.8
ti
1.2
(po4)3和li
1.4y0.4
ti
1.6
(po4)3中的一种或几种。
25.优选的,所述掺杂元素与三元正极材料基体中金属元素的摩尔比为0.01~1:100;
26.所述锂离子导体层在表面包覆锂离子导体的体相掺杂三元正极材料中的含量为0.1~10wt.%。
27.本发明提供了上述表面包覆锂离子导体的体相掺杂三元正极材料在锂离子动力电池中的应用。
28.本发明提供了一种表面包覆锂离子导体的体相掺杂三元正极材料的制备方法,包括以下步骤:将可溶性镍盐、可溶性钴盐和水混合,得到混合盐溶液;所述混合盐溶液中镍离子与钴离子的摩尔比为0.9~1:0.01~0.1;将所述混合盐溶液、vib族金属源、沉淀剂、络合剂和水混合,进行共沉淀反应,得到氢氧化物前驱体,所述vib族金属源为钼源或钨源;将所述氢氧化物前驱体、掺杂元素的可溶性盐与溶剂混合,进行水解反应,得到表面包覆锂离子导体前躯体的氢氧化物前驱体;所述掺杂元素为b、ti、al、nb、sb、sn、si、ge和zr的一种或几种;所述溶剂为水和/或醇;将所述表面包覆锂离子导体前躯体的氢氧化物前驱体进行加热氧化,得到氧化物前驱体;将所述氧化物前驱体与锂盐混合,进行烧结,得到表面包覆锂
离子导体的体相掺杂三元正极材料。本发明以镍(ni)和钴(co)元素为基体,通过共沉淀法均匀融入钼(mo)或钨(w)元素,在液相状态下先将钼或钨元素均匀沉积于镍钴钼或镍钴钨氢氧化物前驱体中,再通过水解法于镍钴钼或镍钴钨氢氧化物前驱体的表面均匀包覆锂离子导体前驱体,在后续混锂烧结过程中,钼或钨元素融入正极材料基体一次颗粒的亚表层,改变正极材料基体一次颗粒的表面能,在正极材料表面形成大长径比粒细化的一次晶粒和更多晶界,有利于缓解二次颗粒内部微应力。同时,钼或钨元素的融入能使正极材料基体一次颗粒亚表层的阳离子有序排列,水解过程中,表面锂离子导体前驱体包覆层部分掺杂元素融入正极材料的体相中,部分掺杂元素与锂源反应形成致密锂离子导体包覆层,进一步改善正极材料体相和表面结构稳定性,从而提高三元正极材料的电化学稳定性。本发明制备得到的表面包覆锂离子导体的体相掺杂三元正极材料体相掺杂元素均匀,表面锂离子导体包覆层均匀、致密,不但能够有效地抑制三元正极材料在充放电过程中由于体积膨胀而在二次球形颗粒内部产生的大量微裂纹,还能够很好地抑制电解液对三元正极材料的腐蚀及副反应的发生,同时锂离子导体包覆层还能够提高锂离子在电极与电解液界面的扩散性,进而有效改善材料的倍率性能、循环寿命及安全性能。
29.同时,本发明在三元正极材料烧结过程中即可在体相和亚表面中掺杂入新元素,同时在二次颗粒的表面包覆锂离子导体包覆层,操作简单,可以有效解决传统分别进行掺杂和包覆的方法操作复杂、掺杂元素分布不合理、包覆结构不稳定的缺陷。且本发明提供的方法绿色环保、适合于工业化生产,是一种具有产业化前景的高性能锂离子电池正极材料新技术。
附图说明
30.图1为实施例1制备所得的表面包覆氧化氢氧化钛的氢氧化镍钴钼前驱体材料的sem图像;
31.图2为实施例1制备所得的体相钛掺杂且表面包覆偏钛酸锂的镍钴钼酸锂正极材料的sem图像;
32.图3为实施例1制备所得的体相钛掺杂且表面包覆偏钛酸锂的镍钴钼酸锂正极材料的xrd谱图;
33.图4为利用本发明实施例1制备所得的体相钛掺杂且表面包覆偏钛酸锂的镍钴钼酸锂正极材料制作的cr2025扣式电池在电流密度0.1c,电压2.7~4.3v条件下的首次充放电曲线图;
34.图5为利用本发明实施例1制备所得的体相钛掺杂且表面包覆偏钛酸锂的镍钴钼酸锂正极材料制作的cr2025扣式电池的倍率循环性能曲线图;
35.图6为利用本发明实施例1制备所得的体相钛掺杂且表面包覆偏钛酸锂的镍钴钼酸锂正极材料制作的cr2025扣式电池在电流密度1.0c,电压2.7~4.3v条件下的循环曲线图;
36.图7为实施例2制备所得的表面包覆氢氧化硅的氢氧化镍钴钼前驱体材料的sem图像;
37.图8为实施例2制备所得的体相硅掺杂且表面包覆硅酸锂的镍钴钼酸锂正极材料的sem图像;
38.图9为实施例2制备所得的体相硅掺杂且表面包覆硅酸锂的镍钴钼酸锂正极材料的xrd谱图;
39.图10为利用本发明实施例2制备所得的体相硅掺杂且表面包覆硅酸锂的镍钴钼酸锂正极材料制作的cr2025扣式电池在电流密度0.1c,电压2.7~4.3v条件下的首次充放电曲线图;
40.图11为利用本发明实施例2制备所得的体相硅掺杂且表面包覆硅酸锂的镍钴钼酸锂正极材料制作的cr2025扣式电池的倍率循环性能曲线图;
41.图12为利用本发明实施例2制备所得的体相硅掺杂且表面包覆硅酸锂的镍钴钼酸锂正极材料制作的cr2025扣式电池在电流密度1.0c,电压2.7~4.3v条件下的循环曲线图;
42.图13为实施例3制备所得的表面包覆氢氧化钛的氢氧化镍钴钨前驱体材料的sem图像;
43.图14为实施例3制备所得的体相钛掺杂且表面包覆偏钛酸锂的镍钴钨酸锂正极材料的sem图像;
44.图15为实施例3制备所得的体相钛掺杂且表面包覆偏钛酸锂的镍钴钨酸锂正极材料的xrd谱图;
45.图16为利用本发明实施例3制备所得的体相钛掺杂且表面包覆偏钛酸锂的镍钴钨酸锂正极材料制作的cr2025扣式电池在电流密度0.1c,电压2.7~4.3v条件下的首次充放电曲线图;
46.图17为利用本发明实施例3制备所得的体相钛掺杂且表面包覆偏钛酸锂的镍钴钨酸锂正极材料制作的cr2025扣式电池的倍率循环性能曲线图;
47.图18为利用本发明实施例3制备所得的体相钛掺杂且表面包覆偏钛酸锂的镍钴钨酸锂正极材料制作的cr2025扣式电池在电流密度1.0c,电压2.7~4.3v条件下的循环曲线图;
48.图19对比例1制备所得的氢氧化镍钴钼前驱体材料的sem图像;
49.图20为对比例1制备所得的镍钴钼酸锂正极材料的sem图像;
50.图21为对比例1制备所得的镍钴钼酸锂正极材料的xrd谱图;
51.图22为利用本发明对比例1制备所得的镍钴钼酸锂正极材料制作的cr2025扣式电池在电流密度0.1c,电压2.7~4.3v条件下的首次充放电曲线图;
52.图23为利用本发明对比例1制备所得的镍钴钼酸锂正极材料制作的cr2025扣式电池的倍率循环性能曲线图;
53.图24为利用本发明对比例1制备所得的镍钴钼酸锂正极材料制作的cr2025扣式电池在电流密度1.0c,电压2.7~4.3v条件下的循环曲线图;
54.图25为对比例2制备所得的氢氧化镍钴钨前驱体材料的sem图像;
55.图26为对比例2制备所得的镍钴钨酸锂正极材料的sem图像;
56.图27为对比例2制备所得的镍钴钨酸锂正极材料的xrd谱图;
57.图28为利用本发明对比例2制备所得的镍钴钨酸锂正极材料制作的cr2025扣式电池在电流密度0.1c,电压2.7~4.3v条件下的首次充放电曲线图;
58.图29为利用本发明对比例2制备所得的镍钴钨酸锂正极材料制作的cr2025扣式电池的倍率循环性能曲线图;
59.图30为利用本发明对比例2制备所得的镍钴钨酸锂正极材料制作的cr2025扣式电池在电流密度1.0c,电压2.7~4.3v条件下的循环曲线图。
具体实施方式
60.本发明提供了一种表面包覆锂离子导体的体相掺杂三元正极材料的制备方法,包括以下步骤:
61.将可溶性镍盐、可溶性钴盐和水混合,得到混合盐溶液;所述混合盐溶液中镍离子与钴离子的摩尔比为0.9~1:0.01~0.1;
62.将所述混合盐溶液、vib族金属源、沉淀剂、络合剂和水混合,进行共沉淀反应,得到氢氧化物前驱体,所述vib族金属源为钼源或钨源;
63.将所述氢氧化物前驱体、掺杂元素的可溶性盐与溶剂混合,进行水解反应,得到表面包覆锂离子导体前躯体的氢氧化物前驱体;所述掺杂元素为b、ti、al、nb、sb、sn、si、ge和zr的一种或几种;所述溶剂为水和/或醇;
64.将所述表面包覆锂离子导体前躯体的氢氧化物前驱体进行加热氧化,得到氧化物前驱体;
65.将所述氧化物前驱体与锂盐混合,进行烧结,得到表面包覆锂离子导体的体相掺杂三元正极材料。
66.本发明将可溶性镍盐、可溶性钴盐和水混合,得到混合盐溶液。在本发明中,所述可溶性镍盐优选为硫酸镍、硝酸镍和乙酸镍中的一种或几种;所述可溶性钴盐优选为硫酸钴、硝酸钴和乙酸钴中的一种或几种。在本发明中,当所述可溶性镍盐或可溶性钴盐为上述中的两种以上时,本发明对不同种类的可溶性镍盐或可溶性钴盐的配比没有特殊的限定,任意配比均可。
67.在本发明中,所述混合盐溶液中镍离子与钴离子的摩尔比为0.9~1:0.01~0.1,优选为0.92~0.95:0.05~0.08。
68.本发明对所述混合的方式没有特殊的要求,使用本领域技术人员熟知的混合方式即可,具体的如搅拌混合。
69.在本发明中,所述混合盐溶液中镍和钴总金属离子摩尔浓度优选为0.3~3.0mol
·
l-1
,更优选为1.6~2mol
·
l-1
,进一步优选为1.9~2mol
·
l-1
。
70.得到所述混合盐溶液后,本发明将所述混合盐溶液、vib族金属源、沉淀剂、络合剂和水混合,进行共沉淀反应,得到氢氧化物前驱体。在本发明中,所述vib族金属源为钼源或钨源。在本发明中,所述钼源优选为三氧化钼、钼酸钠和钼酸铵中的一种或几种;所述钨源优选为三氧化钨、钨酸钠和钨酸钾中的一种或几种。
71.在本发明中,所述vib族金属源优选以碱性溶液的形式提供。在本发明中,vib族金属源碱性溶液的制备方法,优选包括以下步骤:
72.将vib族金属源、无机碱和水混合,得到vib族金属源碱性溶液。
73.在本发明中,所述无机碱优选为氢氧化钠、氢氧化钾、碳酸钠和碳酸氢钠中的一种或几种。当所述无机碱为上述中两种以上时,本发明对不同种类碱的配比没有特殊的限定,任意配比均可。
74.在本发明中,所述vib族金属源碱性溶液中,无机碱的质量浓度优选为1~
20wt.%,更优选为5~8wt.%。在本发明中,所述vib族金属源碱性溶液中,所述vib族金属源的浓度优选为0.01~1.5mol
·
l-1
,更优选为0.25~0.35mol
·
l-1
。
75.在本发明中,所述沉淀剂优选为氢氧化钠、氢氧化钾、碳酸钠和碳酸氢钠中的一种或几种;当所述沉淀剂为上述中两种以上时,本发明对不同种类沉淀剂的配比没有特殊的限定,任意配比均可。在本发明中,所述沉淀剂优选以溶液的形式提供,所述沉淀剂溶液的质量浓度优选为1~40%,更优选为5~10%,进一步优选为7~9%。
76.在本发明中,所述络合剂优选为氨水、乙二胺四乙酸二钠、柠檬酸、柠檬酸钠、草酸和草酸钠中的一种或几种。当所述络合剂为上述中两种以上时,本发明对不同种类络合剂的配比没有特殊的限定,任意配比均可;在本发明中,所述络合剂优选以溶液的形式提供,所述络合剂溶液的摩尔浓度优选为1~10moll-1
,更优选为5~9moll-1
,进一步优选为5.5~6.5moll-1
。
77.在本发明中,所述混合盐溶液中的总金属离子与vib族金属源中vib族金属离子的摩尔比优选为0.93~0.99:0.01~0.07,更优选为0.95:0.05。
78.在本发明中,所述混合盐溶液、vib族金属源、沉淀剂、络合剂和水混合后,所得混合液中vib族金属源离子的摩尔浓度优选为0.01~1.5mol
·
l-1
,更优选为0.25~0.35mol
·
l-1
。
79.在本发明中,所述混合的方式优选为搅拌混合。在本发明中,所述混合具体优选为:
80.将混合盐溶液、含钼或钨元素的碱溶液、沉淀剂溶液和络合剂溶液同时以一定速率滴加入不锈钢共沉淀反应釜中,并持续搅拌,调节沉淀剂溶液的滴加速率以控制反应溶液的ph值为10.5~12.5,更优选为12.2~12.3,调节络合剂溶液的滴加速率以控制反应釜中络合剂浓度为0.1~1.0moll-1
,更优选为0.45~0.55moll-1
;所述滴加的速率优选为0.5~50.0ml
·
min-1
,更优选为1~20ml
·
min-1
。
81.在本发明中,所述共沉淀反应过程中,ph值优选为10.5~12.5,更优选为12.2~12.3,络合剂浓度优选为0.1~1.0mol
·
l-1
,更优选为0.45~0.55mol
·
l-1
;所述共沉淀反应的温度优选为35~85℃,更优选为55~65℃,搅拌速度优选为600~1200rpm,更优选为1100~1200rpm,反应时间优选为5~80h,更优选为40~50h。
82.所述共沉淀反应后,本发明优选对所得共沉淀反应物进行陈化。在本发明中,所述陈化的温度优选为室温,时间优选为2h。所述陈化后,本发明优选对所得陈化产物进行后处理,在本发明中,所述后处理优选包括以下步骤:
83.对所述陈化产物进行固液分离,所得固体依次进行洗涤和干燥,得到氢氧化物前驱体固体。
84.在本发明中,所述固液分离的方式优选为抽滤。在本发明中,所述洗涤优选为:将所得固体用去离子水抽滤冲洗至滤液ph值为8.0~9.8,更优选为9.2~9.3。在本发明中,所述干燥优选为鼓风干燥;所述干燥的温度优选为80~120℃,更优选为90~100℃;时间优选为6~35h,更优选为15~20h。
85.在本发明中,所述氢氧化物前驱体的形貌为球形或类球形;所述氢氧化物前驱体的化学组成为ni
x
coymo
1-x-y
(oh)z或ni
x
coyw
1-x-y
(oh)z(其中,0.9≤x《1.0,0.01≤y《0.1,2≤z<3)。
86.得到所述氢氧化物前驱体后,本发明将所述氢氧化物前驱体、掺杂元素的可溶性盐与溶剂混合,进行水解反应,得到表面包覆锂离子导体前躯体的氢氧化物前驱体。在本发明中,所述氢氧化物前驱体优选以分散液的形式提供。在本发明中,所述氢氧化物前驱体分散液的溶剂优选为去离子水、乙醇、乙二醇、丙醇和异丙醇的一种或几种;当所述溶剂为上述中的两种以上时,本发明对不同种类溶剂的配比没有特殊的限定,任意配比均可。在本发明中,所述氢氧化物前驱体分散液中氢氧化物前驱体与溶剂的质量比优选为1:1~1:10,更优选为1:2~1:7,进一步优选为1:3~1:5。
87.在本发明中,所述掺杂元素为b、ti、al、nb、sb、sn、si、ge和zr的一种或几种。在本发明中,所述掺杂元素的可溶性盐优选为硼酸钠、硫酸氧钛、钛酸四丁酯、硫酸铝、异丙醇铝、铌酸铵、硅酸钠和正硅酸四乙酯中的一种或几种。
88.在本发明中,所述溶剂为水和/或醇。在本发明中,所述醇优选为乙醇、乙二醇、丙醇和异丙醇的一种或几种。在本发明中,当所述溶剂为水和醇时,本发明对水和醇的质量比没有特殊的要求。
89.在本发明中,所述掺杂元素的可溶性盐优选以水和/或醇溶液的形式提供。
90.在本发明中,所述混合的方式优选为:在搅拌的条件下,将掺杂元素的可溶性盐溶液加至氢氧化物前驱体分散液中。在本发明中,所述掺杂元素的可溶性盐溶液的加入速率优选为0.1~1mlmin-1
。在本发明中,所述搅拌的速率优选为200~600rpm。
91.在本发明中,所述氢氧化物前驱体中的总金属离子与掺杂元素离子的摩尔比为0.95~0.995:0.005~0.05。,更优选为0.96~0.98:0.02~0.04。
92.在本发明中,所述水解反应的温度优选为60~95℃,更优选为90~90℃;时间优选为1~5h,更优选为2~3h。
93.所述水解反应后,本发明优选对所得水解反应液进行后处理,所述后处理优选包括以下步骤:通过滤纸抽滤固液分离,去离子水冲洗至滤液ph值小于9.0,100℃真空干燥24h。
94.得到所述表面包覆锂离子导体前躯体的氢氧化物前驱体后,本发明将所述表面包覆锂离子导体前躯体的氢氧化物前驱体进行加热氧化,得到氧化物前驱体。在本发明中,所述加热氧化的气氛优选为空气。在本发明中,所述加热氧化的温度优选为400~600℃,更优选为400~500℃;保温时间优选为1~10h,更优选为3~5h。
95.所述加热氧化后,本发明将所述氧化物前驱体与锂盐混合,进行烧结,得到表面包覆锂离子导体的体相掺杂三元正极材料。在本发明中,所述锂盐优选为氢氧化锂、碳酸锂、醋酸锂和硝酸锂中的一种或几种;当所述锂盐为上述中的两种以上时,本发明对不同种类锂盐的配比没有特殊的限定,任意配比均可。
96.在本发明中,所述混合的方式优选为球磨混合。在本发明中,所述球磨混合的球磨介质优选为聚四氟乙烯小球;所述球磨介质的直径优选为1~20mm,更优选为6~10mm;所述球磨的转速优选为100~500rpm,更优选为250~300rpm;时间优选为10~100min,更优选为30~60min。
97.在本发明中,在本发明中,所述烧结优选在空气或氧气气氛中进行,所述烧结的温度优选为600~820℃,更优选为690~730℃;保温时间优选为10~20h,更优选为10~18h,进一步优选为10~12h。在本发明中,升温至所述烧结温度的升温速率优选为0.5~10℃
min-1
,更优选为0.5~5℃min-1
,进一步优选为1~2℃min-1
。
98.所述烧结后,本发明优选对所得烧结产物进行破碎分级,得到表面包覆锂离子导体的体相掺杂三元正极材料。在本发明中,所述表面包覆锂离子导体的体相掺杂三元正极材料的粒径优选为1~15μm,更优选为5~10μm。本发明对所述破碎分级的过程没有特殊的限定,按照本领域熟知的过程进行即可。
99.本发明提供了上述制备方法制备得到的表面包覆锂离子导体的体相掺杂三元正极材料,包括体相掺杂的三元正极材料和包覆在所述体相掺杂的三元正极材料表面的锂离子导体层;
100.所述体相掺杂的三元正极材料包括三元正极材料基体和体相掺杂于所述三元正极材料基体中的掺杂元素,所述三元正极材料的化学组成为lini
x
coymo
1-x-y
o2或lini
x
coyw
1-x-y
o2,其中0.9≤x《1.0,0.01≤y《0.1;作为本发明的具体实施例,所述三元正极材料的化学组成为lini
0.9
co
0.09
mo
0.01
o2、lini
0.95
co
0.03
mo
0.02
o2、lini
0.98
co
0.01
mo
0.01
o2、lini
0.9
co
0.09w0.01
o2、lini
0.93
co
0.05w0.02
o2或lini
0.97
co
0.02w0.01
o2。
101.所述掺杂元素为b、ti、al、nb、sb、sn、si、sc、y、ge和zr的一种或几种;
102.所述锂离子导体层的化学组成为li3bo3、li2wo4、li2moo4、li2tio3、lialo2、linbo3、lisbo3、li2sno3、li4sio4、li2geo3、li2zro3、li3po4、li
1.3
al
0.3
ti
1.7
(po4)3、li
1.8
sc
0.8
ti
1.2
(po4)3和li
1.4y0.4
ti
1.6
(po4)3中的一种或几种。
103.在本发明中,所述掺杂元素与三元正极材料基体中金属元素的摩尔比优选为0.01~1:100,更优选为0.05~0.5:100。
104.在本发明中,所述锂离子导体层在表面包覆锂离子导体的体相掺杂三元正极材料中的含量优选为0.1~10wt.%,更优选为0.5~8wt.%,进一步优选为1~5wt.%。在本发明中,所述锂离子导体层的厚度优选为1~100nm,优选为10~80nm,进一步优选为30~50nm。
105.在本发明中,所述表面包覆锂离子导体的体相掺杂三元正极材料的粒径优选为1~15μm,更优选为5~10μm。在本发明中,所述表面包覆锂离子导体的体相掺杂三元正极材料的振实密度优选为2.0~3.0gcm-3
,能量密度优选为820~920wh
·
kg-1
。
106.本发明提供了上述表面包覆锂离子导体的体相掺杂三元正极材料在锂离子动力电池中的应用。本发明对所述应用的方法没有特殊的限定,按照本领域熟知的方法应用即可。
107.下面结合实施例对本发明提供的表面包覆锂离子导体的体相掺杂三元正极材料及其制备方法和应用进行详细的说明,但是不能把它们理解为对本发明保护范围的限定。
108.实施例1
109.将硫酸镍和硫酸钴按n(ni):n(co)=0.9:0.09混合,配制成5.5l金属离子总浓度为1.9mol
·
l-1
的水溶液,将三氧化钼溶解于6.0wt.%的氢氧化钠溶液中配制成0.55l钼元素摩尔浓度为0.182mol
·
l-1
的碱溶液,将氢氧化钠(沉淀剂)配制成9.0l质量浓度为10.0%的水溶液,氨水配制成8.0l摩尔浓度为7.0mol
·
l-1
的水溶液,然后将混合盐溶液、钼元素的碱溶液与氢氧化钠溶液、氨水溶液并流滴加到共沉淀反应釜中并持续搅拌,滴加速率为2ml
·
min-1
,控制反应釜温度为55℃,搅拌速度为1200rpm,ph=12.3,络合剂浓度为0.57mol
·
l-1
,进行共沉淀反应50h后,得到镍钴钼氢氧化物前驱体浆料,陈化2h后固液分离,将所得固体反复用水抽滤洗至滤液ph值为9.5,过滤后,100℃鼓风干燥16h,得到镍钴钼
氢氧化物前驱体;
110.将制得的10g镍钴钼氢氧化前驱体分散于30ml乙醇中,搅拌速度控制在500rpm。再往前驱体悬浮液中滴加入分散有钛酸四丁酯的乙醇混合液(ti的加入量可以根据化学计量比计算,一般占总材料摩尔比的2.0%),并继续搅拌3h,将悬浮液加热到80℃使乙醇挥发。待乙醇挥发后得到表面包覆氢氧化钛的氢氧化镍钴钼前驱体粉末;
111.将所述表面包覆氢氧化钛的镍钴钼氢氧化物前驱体于400℃条件下预氧化6h,得到表面包覆氧化钛的镍钴钼氧化物前驱体,将氢氧化锂与表面包覆氧化钛的镍钴钼氧化物前驱体按锂与前驱体中金属离子总量摩尔比1.07:1混合,用10mm的聚四氟乙烯小球进行球磨混合60min,球磨转速为280rpm,将所得混合物于730℃条件下烧结12h,烧结料经破碎分级后,得到体相钛(ti)掺杂且表面包覆偏钛酸锂(li2tio3)的镍钴钼酸锂粉末。
112.其中,表面包覆氧化钛的镍钴钼氧化物前驱体的sem图像如图1所示;由图1可以看出,氢氧化钛包覆层均匀致密。
113.体相钛掺杂且表面包覆偏钛酸锂的镍钴钼酸锂正极材料的sem图像如图2所示。由图2可以看出,该正极材料一次颗粒粒径约为0.2μm,部分钛元素成功融入正极材料中,部分钛元素在球形颗粒表面形成偏钛酸锂包覆层,没有出现其他杂质相,包覆层厚度约为5nm。
114.体相钛掺杂且表面包覆偏钛酸锂的镍钴钼酸锂正极材料的xrd谱图如图3所示。由图3可以看出,部分钛元素成功融入正极材料中。
115.根据gbt5162-2006检测正极材料的振实密度,振实密度为2.6gcm-3
。
116.以所得体相钛(ti)掺杂且表面包覆偏钛酸锂(li2tio3)的镍钴钼酸锂正极材料为正极,金属锂为负极,1.2m的lipf6(ec:emc=3:7(vol),2.0wt%的vc)为电解液,并采用celgard2320隔膜组装成cr2025扣式半电池,在2.7~4.3v电压区间内进行性能测试。
117.所得纽扣电池在电流密度0.1c,电压2.7~4.3v条件下的首次充放电曲线图如图4所示,倍率循环性能曲线图如图5所示,循环曲线图如图6所示。
118.由图4~6可知,30℃条件下,该正极材料的首次放电比容量为220.65mahg-1
,对应的能量密度约为820wh
·
kg-1
,首次充放电效率为87.90%,5.0c放电比容量保持率为83.91%,1.0c充/放电循环100次后放电比容量保持率为92.36%,表明该体相钛(ti)掺杂且表面包覆偏钛酸锂(li2tio3)的镍钴钼酸锂的三元正极材料具有较好的倍率及循环性能。
119.实施例2
120.将硫酸镍和硫酸钴按n(ni):n(co)=0.9:0.09混合,配制成5.5l金属离子总浓度为1.9mol
·
l-1
的水溶液,将钼酸铵溶解于6.0wt.%的氢氧化钠溶液中配制成0.55l钼元素摩尔浓度为0.182mol
·
l-1
的碱溶液,将氢氧化钠(沉淀剂)配制成9.0l质量浓度为10.0%的水溶液,氨水配制成8.0l摩尔浓度为7mol
·
l-1
的水溶液,然后将混合盐溶液、钼元素的碱溶液与氢氧化钠溶液、氨水溶液并流滴加到共沉淀反应釜中并持续搅拌,滴加速率为2ml
·
min-1
,控制反应釜温度为55℃,搅拌速度为1200rpm,ph=12.3,络合剂浓度为0.57mol
·
l-1
,进行共沉淀反应50h后,得到镍钴钼氢氧化物前驱体浆料,陈化2h后固液分离,将所得固体反复用水抽滤洗至滤液ph值为9.5,过滤后,100℃鼓风干燥16h,得到镍钴钼氢氧化物前驱体;
121.将制得的10g镍钴钼氢氧化前驱体分散于30ml丙醇中,搅拌速度控制在500rpm。再往前驱体悬浮液中滴加入分散有正硅酸四乙酯的丙醇混合液(si的加入量占总材料摩尔比
的3.0%),并继续搅拌3h,将悬浮液加热到90℃使丙醇挥发。待丙醇挥发后得到表面包覆氢氧化硅的氢氧化镍钴钼前驱体粉末;
122.将所述表面包覆氢氧化硅的镍钴钼氢氧化物前驱体于400℃条件下预氧化6h,得到表面包覆氧化硅的镍钴钼氧化物前驱体,将氢氧化锂与表面包覆氧化硅的镍钴钼氧化物前驱体按锂与前驱体中金属离子总量摩尔比1.07:1混合,用10mm的聚四氟乙烯小球进行球磨混合60min,球磨转速为280rpm,将所得混合物于730℃条件下烧结12h,烧结料经破碎分级后,得到体相硅(si)掺杂且表面包覆硅酸锂(li4sio4)的镍钴钼酸锂粉末。
123.其中,表面包覆氧化硅的镍钴钼氧化物前驱体的sem图像如图7所示;由图7可以看出,氢氧化硅包覆层均匀致密。
124.体相硅(si)掺杂且表面包覆硅酸锂(li4sio4)的镍钴钼酸锂正极材料的sem图像如图8所示。由图8可以看出,该正极材料一次颗粒粒径约为0.3μm,部分硅元素在球形颗粒表面形成硅酸锂包覆层,没有出现其他杂质相,包覆层厚度约为2nm。
125.体相硅(si)掺杂且表面包覆硅酸锂(li4sio4)的镍钴钼酸锂正极材料的xrd谱图如图9所示。由图9可以看出,部分硅元素成功融入正极材料中。
126.根据gbt5162-2006检测正极材料的振实密度,振实密度为2.5gcm-3
。
127.按照实施例1的方式将所得体相硅掺杂且表面包覆硅酸锂的镍钴钼酸锂正极材料组装成cr2025扣式半电池,在2.7~4.3v电压区间内进行性能测试。
128.所得纽扣电池在电流密度0.1c,电压2.7~4.3v条件下的首次充放电曲线图如图10所示,倍率循环性能曲线图如图11所示,循环曲线图如图12所示。
129.由图11~12可知,30℃条件下,该正极材料的首次放电比容量为226.56mahg-1
,对应的能量密度约为850wh
·
kg-1
,首次充放电效率约为89.87%,5.0c放电比容量保持率为87.68%,1.0c充/放电循环100次后放电比容量保持率为77.78%,表明体相硅(si)掺杂且表面包覆硅酸锂(li4sio4)改性可以显著提高基准镍钴钼酸锂三元正极材料的倍率及循环性能。
130.实施例3
131.将硫酸镍和硫酸钴按n(ni):n(co)=0.92:0.07混合,配制成5.0l金属离子总浓度为1.6mol
·
l-1
的水溶液;将钨酸钠溶解于5.0wt.%的氢氧化钠溶液中配制成0.5l钨元素摩尔浓度为0.182mol
·
l-1
的碱溶液,将氢氧化钾配制成6.0l质量浓度为8.0wt.%的水溶液,氨水配制成7.0l摩尔浓度为6.5mol
·
l-1
的水溶液;将混合盐溶液、钨元素的碱溶液与氢氧化钠溶液、氨水溶液并流滴加到共沉淀反应釜中并持续搅拌,滴加速率为3ml
·
min-1
,控制反应釜温度为60℃,搅拌速度为1000rpm,ph=12.2,络合剂浓度为0.55mol
·
l-1
,反应进行60h后,得到镍钴钨氢氧化物前驱体浆料,陈化1h后固液分离,反复抽滤水洗至滤液ph值为9.3,过滤,90℃鼓风干燥18h,得到镍钴钨氢氧化物前驱体;
132.将制得的20g镍钴钨氢氧化前驱体分散于50ml异丙醇中,搅拌速度控制在600rpm。再往前驱体悬浮液中滴加入分散有钛酸四丁酯的异丙醇混合液(ti的加入量占总材料摩尔比的1.0%),并继续搅拌2h,将悬浮液加热到95℃使异丙醇挥发。待异丙醇挥发后得到表面包覆氢氧化钛的氢氧化镍钴钨前驱体粉末;
133.将所述表面包覆氢氧化钛的镍钴钨氢氧化物前驱体于450℃条件下预氧化3h,得到表面包覆氧化钛的镍钴钨氧化物前驱体,将氢氧化锂与表面包覆氧化钛的镍钴钨氧化物
前驱体按锂与前驱体中金属离子总量摩尔比1.05:1混合,用5mm的聚四氟乙烯小球进行球磨混合50min,球磨转速为250rpm,将混合物于710℃条件下烧结24h,烧结料经破碎分级后,得到体相钛(ti)掺杂且表面包覆偏钛酸锂(li2tio3)的镍钴钨酸锂粉末。
134.其中,表面包覆氢氧化钛的氢氧化镍钴钨前驱体的sem图像如图13所示;由图13可以看出,氢氧化钛包覆层均匀致密。
135.体相钛(ti)掺杂且表面包覆偏钛酸锂(li2tio3)的镍钴钨酸锂正极材料的sem图像如图14所示。由图14可以看出,该正极材料一次颗粒粒径约为0.1μm,部分钛元素在球形颗粒表面形成偏钛酸锂包覆层,没有出现其他杂质相,包覆层厚度约为6nm。
136.体相钛(ti)掺杂且表面包覆偏钛酸锂(li2tio3)的镍钴钨酸锂正极材料的xrd谱图如图15所示。由图15可以看出,部分钛元素成功融入正极材料中。
137.根据gbt5162-2006检测正极材料的振实密度,振实密度为2.3gcm-3
。
138.按照实施例1的方式将所得体相钛掺杂且表面包覆偏钛酸锂的镍钴钨酸锂正极材料组装成cr2025扣式半电池,在2.7~4.3v电压区间内进行性能测试。
139.所得纽扣电池在电流密度0.1c,电压2.7~4.3v条件下的首次充放电曲线图如图16所示,倍率循环性能曲线图如图17所示,循环曲线图如图18所示。
140.由图14~16可以看出,30℃条件下,该正极材料的首次放电比容量为219.92mahg-1
,对应的能量密度为830wh
·
kg-1
,首次充放电效率为84.86%,5.0c放电比容量保持率约为87.65%,1.0c充/放电循环100次后放电比容量保持率为103.23%,表明该体相钛(ti)掺杂且表面包覆偏钛酸锂(li2tio3)的镍钴钨酸锂三元正极材料具有较好的倍率及循环性能。
141.对比例1
142.按照实施例1的方式制备镍钴钼氢氧化物前驱体;
143.将所述镍钴钼氢氧化物前驱体于400℃条件下预氧化6h,得到镍钴钼氧化物前驱体,将氢氧化锂与镍钴钼氧化物前驱体按锂与前驱体中金属离子总量摩尔比1.07:1混合,用10mm的聚四氟乙烯小球进行球磨混合60min,球磨转速为280rpm,将所得混合物于730℃条件下烧结12h,烧结料经破碎分级后,得到镍钴钼酸锂粉末。
144.其中,镍钴钼氢氧化物前驱体的sem图像如图19所示;由图19可以看出,该前驱体材料二次颗粒由片状一次颗粒紧密堆积而成,表面无其它包覆物。
145.镍钴钼酸锂正极材料的sem图像如图20所示。由图20可以看出,该正极材料一次颗粒粒径约为0.2μm。
146.镍钴钼酸锂正极材料的的xrd谱图如图21所示。由图21可以看出,该正极材料为层状结构、结晶性良好且没有其它杂质峰。
147.根据gbt5162-2006检测正极材料的振实密度,振实密度为2.4gcm-3
。
148.按照实施例1的方式将所得镍钴钼酸锂正极材料组装成cr2025扣式半电池,在2.7~4.3v电压区间内进行性能测试。
149.所得纽扣电池在电流密度0.1c,电压2.7~4.3v条件下的首次充放电曲线图如图22所示,倍率循环性能曲线图如图23所示,循环曲线图如图24所示。
150.由图22~24可以看出,30℃条件下,该对比正极材料的首次放电容量为216.29mahg-1
,对应的能量密度约为820wh
·
kg-1
,首次充放电效率为88.15%,5.0c放电容量保持率为81.03%,1.0c充/放电循环100次后放电容量保持率为75.03%。
151.对比例2
152.按照实施例3的方式制备镍钴钨氢氧化物前驱体。
153.将所述镍钴钨氢氧化物前驱体于450℃条件下预氧化3h,得到镍钴钨氧化物前驱体,将氢氧化锂与镍钴钨氧化物前驱体按锂与前驱体中金属离子总量摩尔比1.05:1混合,用5mm的聚四氟乙烯小球进行球磨混合50min,球磨转速为250rpm,将混合物于710℃条件下烧结24h,烧结料经破碎分级后,得到镍钴钨酸锂粉末。
154.其中,镍钴钨氢氧化物前驱体的sem图像如图25所示;由图25可以看出,该前驱体材料二次颗粒由片状一次颗粒紧密堆积而成,表面无其它包覆物。
155.镍钴钨酸锂正极材料的sem图像如图26所示。由图26可以看出,该正极材料一次颗粒粒径约为0.1μm。
156.镍钴钨酸锂正极材料的xrd谱图如图27所示。由图27可以看出,该正极材料为层状结构、结晶性良好且没有其它杂质峰。
157.根据gbt5162-2006检测正极材料的振实密度,振实密度为2.3gcm-3
。
158.按照实施例1的方式将所得镍钴钨酸锂正极材料组装成cr2025扣式半电池,在2.7~4.3v电压区间内进行性能测试。
159.所得纽扣电池在电流密度0.1c,电压2.7~4.3v条件下的首次充放电曲线图如图28所示,倍率循环性能曲线图如图29所示,循环曲线图如图30所示。
160.由图28~30可以看出,30℃条件下,该对比正极材料的首次放电容量为216.98mahg-1
,对应的能量密度约为820wh
·
kg-1
,首次充放电效率为87.95%,5.0c放电容量保持率为80.66%,1.0c充/放电循环100次后放电容量保持率为79.53%。
161.以上所述仅是本发明的优选实施方式,应当指出,对于本技术领域的普通技术人员来说,在不脱离本发明原理的前提下,还可以做出若干改进和润饰,这些改进和润饰也应视为本发明的保护范围。
再多了解一些
本文用于创业者技术爱好者查询,仅供学习研究,如用于商业用途,请联系技术所有人。