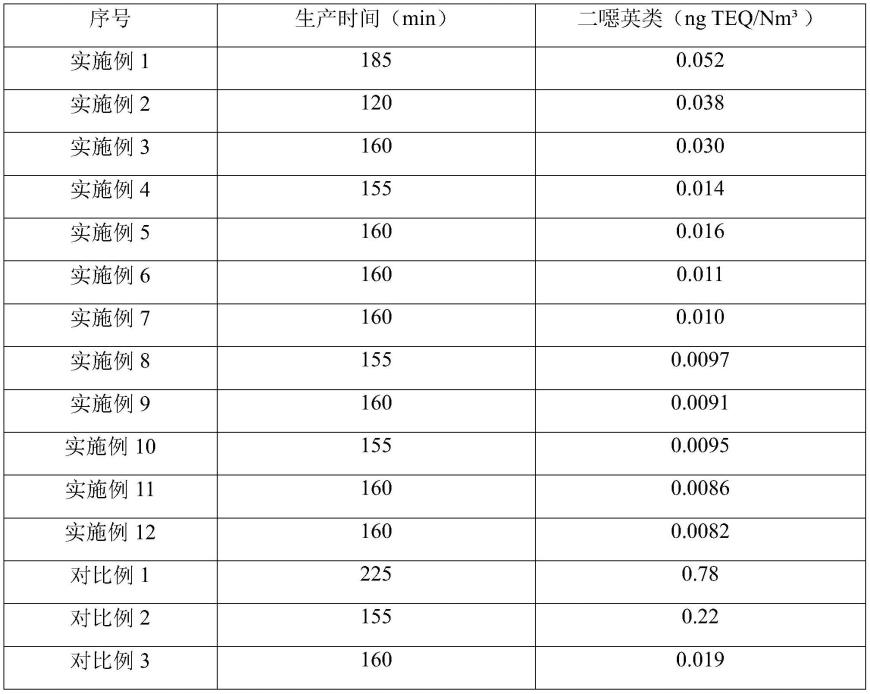
1.本技术涉及有机硅行业裂解废液处理技术领域,更具体地说,它涉及一种有机硅行业裂解液焚烧工艺。
背景技术:
2.目前有机硅行业在生产过程中会产生大量的有机废气、废液,这些废气和废液中含有一氯甲烷、四甲基硅烷、甲基氯二硅烷高沸物等有害成分,其处理方式如直接进入废水处理厂,不仅处理效果不佳,而且也不经济,浪费了大量的资源,产生的副产物也难以处理。
3.对于上述问题,技术人员开发出利用焚烧工艺对裂解废液进行处理,将裂解废液通过密闭管道输送至焚烧车间废液储罐内,然后由雾化喷枪打入焚烧炉内在900-1000℃的温度下,将氯硅烷高温分解,生成容易处理的二氧化硅、氯化氢气体和少量氯气等物质。但由于有机硅废液中会夹带颗粒状固体,废液长时间放置后会逐渐凝固形成渣浆,使用管道输送很难完成投料过程。并且,由于裂解废液成分复杂,处理过程中烟气内也容易产生二噁英类有毒有害物质,以及后续酸性气体的处理不恰当都会造成二次污染的情况。
4.随着工艺的不断发展和改进,目前常用的二噁英去除工艺是采用活性炭喷射吸附加布袋除尘器来脱除烟气中的二噁英,但是这种去除方式只能在工艺后端进行操作,而且处理成本和处理难度都比较大,并且对于前端焚烧工艺中产生的二噁英没有很好的抑制作用,烟气中产生的二噁英总量仍然处于较高水平。
技术实现要素:
5.为了降低焚烧工艺中烟气内二噁英的含量,本技术提供一种有机硅行业裂解废液焚烧工艺。
6.本技术提供一种有机硅行业裂解废液焚烧工艺,采用如下的技术方案:一种有机硅行业裂解废液焚烧工艺,包括如下步骤:s1:将裂解废液封装后直接加入回转窑内进行焚烧,然后再进入二级燃烧室内进行过氧燃烧;s2:将步骤s1中燃烧后的产生的烟气经过换热冷却后降温至500-600℃,然后急冷后降温至180-200℃;s3:将步骤s2中急冷降温后的烟气经过旋风分离处理后得到飞灰和分离烟气,分离烟气经过干法脱酸处理得到脱酸烟气,然后将脱酸烟气经过活性炭吸附处理后得到吸附烟气,然后将吸附烟气经过碱洗脱酸处理后外排即可。
7.通过采用上述技术方案,由于有机硅行业的裂解废液成分比较复杂,会夹带很多颗粒状固体,在放置储存过程中非常不稳定,容易发生凝固结块现象,使用管道输送很难完成投料作业。若采用雾化喷枪的方式打入回转窑,会经常发生严重堵塞现象,无法进行正常生产。另外,若采用隔膜泵进行投料,长时间运行后也会对隔膜泵产生损害,而且渣浆与水接触后会放出大量的热并产生酸性气体,使用常规的进料方式都存在危险性。本技术中对
裂解废液采用整体封装后通过移动设备从回转窑的边门投入窑内进行焚烧,可以将液态、半固态渣浆、固态等不同形态的裂解废液进行高效稳定的投料作业,满足生产需求,整体生产效率更高。
8.并且,裂解废液先采用回转窑焚烧,可以将大部分的有机物裂解,并在回转窑的带动下充分的与燃烧气体接触,减少二噁英组分的产生。然后未充分燃烧的有机物和烟气中夹带的颗粒悬浮有机物进入二级燃烧室内,利用二级燃烧室内强烈的过氧燃烧作用充分的将有机物销毁分解,同时强烈的高温过氧燃烧可以将已有的二噁英分解掉,进一步控制二噁英组分的含量。
9.另外,从回转窑和二级燃烧室排出的高温烟气在经过换热冷却后降低温度,此时烟气中的二噁英前驱体容易再次合成二噁英组分,本技术中采用急冷的方式使得烟气温度迅速降温至180-200℃,可以大大抑制烟气中二噁英的再合成,从而整体上降低烟气中二噁英组分的含量,有利于后续的处理,节省后端活性炭吸附工艺的投入量,更加节能环保。
10.优选的,所述回转窑的倾斜角度为1.5-2.5度。
11.通过采用上述技术方案,优化和调整回转窑的倾斜角度,使裂解废料沿回转窑以合适的速度向回转窑下方移动,能够与燃烧气体充分的接触,保证有机物的分解程度,在一定程度上抑制二噁英前驱体等组分的产生。
12.优选的,所述回转窑的转速为0.063-0.63r/min。
13.通过采用上述技术方案,对回转窑的转速进行优化,申请人发现采用上述转速可以使裂解废液以合适的抛落速度与燃烧气体接触,可以使焚烧过程中产生的部分二噁英组分和二噁英前驱体分解,有利于降低烟气中二噁英的含量。
14.优选的,所述回转窑的进口温度为800-900℃,出口温度为900-1100℃。
15.通过采用上述技术方案,优化和调整回转窑的进口温度和出口温度,合适的温度可以加快烟气中产生的二噁英组分再次分解,同时抑制烟气中飞灰表面的异相催化反应,减少二噁英前驱体的合成量,抑制和阻断后续二噁英组分的合成,降低后续烟气中的二噁英含量。
16.优选的,所述回转窑内物料最大停留时间为100-150min。
17.通过采用上述技术方案,调整回转窑内物料的最大停留时间,在保证能源成本的前提下尽可能的使有机物和烟气中的二噁英组分充分分解。
18.优选的,所述步骤s2中,急冷降温包括如下步骤:1)、将处理液经过雾化后形成喷淋水雾;2)、使换热冷却后的烟气与喷淋水雾混合后进行热交换降温;所述处理液主要由如下重量份数的原料制成:水500-650份、乙二胺四乙酸二钠钙15-20份、季铵碱5-10份、氨基噻二唑3-7份、促进剂2-5份。
19.通过采用上述技术方案,本技术将处理液经过雾化后形成喷淋水雾,喷淋水雾与高温烟气充分接触后,可以迅速的降温至180-200℃,抑制二噁英前驱体的氧化反应和缩合反应。同时,季铵碱、氨基噻二唑在促进剂的催化作用下可以与二噁英前驱体中的卤素发生交换,夺取并捕集氯离子等活性基元。
20.另外,氨基噻二唑还可以与氯离子发生氮烷基化反应,降低氯苯类、多氯苯酚类物质的合成量。并且乙二胺四乙酸二钠钙、季铵碱可以汲取氯气、氯化氢气体,减少分散性氯
源,抑制促进剂对烟气中原有二噁英前驱体的合成催化作用,同时保证季铵碱、氨基噻二唑对结合氯源的消除作用,进而大大降低烟气在中高温过程中二噁英组分的合成量。
21.优选的,所述季铵碱为四丁基氢氧化铵、四丙基氢氧化铵、四甲基氢氧化铵中的至少一种。
22.通过采用上述技术方案,优化和调整季铵碱的种类,提升季铵碱对烟气中结合氯源的捕集和结合能力。
23.优选的,所述季铵碱由四丁基氢氧化铵、四甲基氢氧化铵按摩尔比(2.5-3):1组成。
24.通过采用上述技术方案,试验和优化季铵碱的组成配比,平衡季铵碱的空间位阻和化学交换能力,进一步提升季铵碱的氯源清除性能,抑制二噁英组分的合成。
25.优选的,所述促进剂由铜粉、碳酸钾按摩尔比(0.65-1):1组成。
26.通过采用上述技术方案,优化和调整促进剂的组成配比,在保证促进剂对结合氯源清除的促进作用的同时,大大降低对原有二噁英前驱体的催化作用,使得整体烟气中二噁英组分的合成过程得以有效抑制。
27.优选的,所述原料中还包括0.8-1.5重量份数的邻苯甲酰磺酰亚胺。
28.通过采用上述技术方案,本技术发现加入邻苯甲酰磺酰亚胺后,在中高温的反应条件下,邻苯甲酰磺酰亚胺分子上的氮原子可以与氯苯类、多氯苯酚类二噁英前驱体进行卤素结合,从而抑制和阻断二噁英组分的合成路线,进一步降低烟气在中高温过程中二噁英组分的合成量。
29.综上所述,本技术具有以下有益效果:1、由于本技术采用整体封装的方式将裂解废液投入回转窑内,可以适用各种形态的有机硅行业裂解废液,然后经过回转窑和二次燃烧室充分焚烧,使得有机物得以充分裂解,产生的高温烟气经过换热降温和急冷降温后,可以大大抑制烟气中二噁英在中高温阶段的二次合成量。
30.2、本技术中优选采用雾化喷淋工艺使处理液与高温烟气充分接触,利用汽化换热作用快速的降低烟气的温度,同时处理液中的季铵碱、氨基噻二唑在促进剂的催化作用下对二噁英前驱体中的结合氯源进行交换、捕集,抑制和阻断二噁英组分的二次合成路线,大大降低了烟气中二噁英的含量。
31.3、采用本技术的有机硅行业裂解废液焚烧工艺高效的处理各种有机硅行业裂解废液,同烟气中的二噁英含量很低,更加绿色环保。
具体实施方式
32.以下结合实施例对本技术作进一步详细说明。
33.本技术实施例及对比例的原料除特殊说明以外均为普通市售。实施例
34.实施例1本实施例的有机硅行业裂解废液焚烧工艺,包括如下步骤:s1:将渣浆状的裂解废液用200l容量的塑料桶封装,然后通过电动葫芦缓慢吊入回转窑的边门内进行焚烧,回转窑的倾斜度设计为1.5度,转速为0.063r/min;封装后的裂
解废液向回转窑的下方不断移动,此时回转窑的进口温度为800℃,出口温度为900℃,物料最大停留时间为150min,使裂解废液内的有机物质被销毁,剩余未充分燃烧的有机物和气体中的悬浮颗粒所夹带的有机物进入二级燃烧室,二级燃烧室内通入二次风强烈混合,并且停留时间超过2秒,使二级燃烧室内形成过氧燃烧,以使裂解废液完全燃烧;回转窑的炉排和二级燃烧室产生的炉渣经过出渣机排出,采用机械方式统一收集至太空编织吨包,定期处置;s2:步骤s1中燃烧后产生的烟气经过余热锅炉换热冷却后从1100℃降温至500℃,然后进入急冷塔,急冷塔内设有雾化喷淋装置,雾化喷淋装置将水雾化形成水雾,高温烟气与雾化喷淋水雾直接接触,烟气可以在1秒钟内与水雾接触蒸发汽化进行热交换,然后降温至180℃;s3:步骤s2中急冷降温后的烟气进入旋风分离器内进行分离处理得到飞灰和分离烟气,大颗粒的飞灰被捕集至下方的灰斗内,烟气经管道进入干法脱酸塔内进行干法脱酸处理,在干法脱酸塔内投加消石灰,分离烟气与投加的消石灰充分混合反应;通过给料机控制消石灰的投加量,并采用变频器控制给料机的转速,以使投加量更加精准;通过活性炭输送风机将活性炭粉末输送至干法脱酸塔出口烟道中,依靠烟气气流冲击使得活性炭粉末均匀分散在烟气中,对烟气内的重金属以及二噁英进行吸附处理得到吸附烟气,吸附后的活性炭颗粒附着在袋式除尘器的滤袋壁上,然后随着布袋除尘器清灰单独出灰排出。
35.经过活性炭吸附处理后的吸附烟气输送至碱洗脱酸塔内,碱洗脱酸塔内循环有碱液,碱液使烟气温度降低至70℃,同时对烟气中的酸性气体作进一步去除,最后经80m高烟囱排放即可。
36.本实施例的有机硅行业裂解废液焚烧工艺中,余热锅炉、急冷塔、旋风除尘器采用直接出灰的方式,并设有锁风装置,防止扬尘,采用太空编织吨包进行收集,定期处理;布袋除尘器单独出灰,每个集灰斗采用自动出灰方式并配置加热装置,采用机械方式统一收集至太空编织吨包,定期处置。
37.实施例2本实施例的有机硅行业裂解废液焚烧工艺与实施例1的不同之处在于:1)、步骤s1中,回转窑的倾斜度设计为2.5度,转速为0.63r/min;封装后的裂解废液向回转窑的下方不断移动,此时回转窑的进口温度为900℃,出口温度为1100℃,物料最大停留时间为100min。
38.2)、步骤s2中,将步骤s1中燃烧后产生的烟气经过余热锅炉换热冷却后从1100℃降温至600℃,然后进入急冷塔,急冷塔内设有雾化喷淋装置,雾化喷淋装置将水雾化形成水雾,高温烟气与雾化喷淋水雾直接接触,烟气可以在1秒钟内与水雾接触蒸发汽化进行热交换,然后降温至200℃。
39.其余的与实施例1中相同。
40.实施例3本实施例的有机硅行业裂解废液焚烧工艺与实施例1的不同之处在于:1)、步骤s1中,回转窑的倾斜度设计为2度,转速为0.35r/min;封装后的裂解废液向回转窑的下方不断移动,此时回转窑的进口温度为850℃,出口温度为1000℃,物料最大
停留时间为120min。
41.2)、步骤s2中,将步骤s1中燃烧后产生的烟气经过余热锅炉换热冷却后从1100℃降温至550℃,然后进入急冷塔,急冷塔内设有雾化喷淋装置,雾化喷淋装置将水雾化形成水雾,高温烟气与雾化喷淋水雾直接接触,烟气可以在1秒钟内与水雾接触蒸发汽化进行热交换,然后降温至195℃。
42.其余的与实施例1中相同。
43.实施例4本实施例的有机硅行业裂解废液焚烧工艺与实施例3的不同之处在于:步骤s2中,急冷降温包括如下步骤:1)、配置好处理液,然后将处理液用雾化喷淋装置形成处理液雾体喷入急冷塔内;2)、使换热冷却后的烟气与处理液雾体混合后进行热交换;本实施例的处理液由如下重量的原料制成:水500kg、乙二胺四乙酸二钠钙15kg、季铵碱5kg、氨基噻二唑3kg、促进剂2kg。
44.其中,季铵碱为四甲基氢氧化铵。促进剂为铜粉。
45.其余的与实施例3相同。
46.实施例5本实施例的有机硅行业裂解废液焚烧工艺与实施例3的不同之处在于:步骤s2中,急冷降温包括如下步骤:1)、配置好处理液,然后将处理液用雾化喷淋装置形成处理液雾体喷入急冷塔内;2)、使换热冷却后的烟气与处理液雾体混合后进行热交换;本实施例的处理液由如下重量的原料制成:水650kg、乙二胺四乙酸二钠钙20kg、季铵碱10kg、氨基噻二唑7kg、促进剂5kg。
47.其中,季铵碱为四丙基氢氧化铵。促进剂为pb粉。
48.其余的与实施例3相同。
49.实施例6本实施例的有机硅行业裂解废液焚烧工艺与实施例3的不同之处在于:步骤s2中,急冷降温包括如下步骤:1)、配置好处理液,然后将处理液用雾化喷淋装置形成处理液雾体喷入急冷塔内;2)、使换热冷却后的烟气与处理液雾体混合后进行热交换;本实施例的处理液由如下重量的原料制成:水600kg、乙二胺四乙酸二钠钙18kg、季铵碱8.5kg、氨基噻二唑5kg、促进剂3.5kg。
50.其中,季铵碱为四丙基氢氧化铵。促进剂为pb粉。
51.其余的与实施例3相同。
52.实施例7本实施例的有机硅行业裂解废液焚烧工艺与实施例6的不同之处在于:处理液的原料中,季铵碱由四丁基氢氧化铵、四甲基氢氧化铵按摩尔比2.5:1组成,其余的与实施例6相同。
53.实施例8本实施例的有机硅行业裂解废液焚烧工艺与实施例6的不同之处在于:处理液的
原料中,季铵碱由四丁基氢氧化铵、四甲基氢氧化铵按摩尔比3:1组成,其余的与实施例6相同。
54.实施例9本实施例的有机硅行业裂解废液焚烧工艺与实施例8的不同之处在于:处理液的原料中,促进剂由铜粉、碳酸钾按摩尔比1:1组成,其余的与实施例8相同。
55.实施例10本实施例的有机硅行业裂解废液焚烧工艺与实施例8的不同之处在于:处理液的原料中,促进剂由铜粉、碳酸钾按摩尔比0.65:1组成,其余的与实施例8相同。
56.实施例11本实施例的有机硅行业裂解废液焚烧工艺与实施例10的不同之处在于:处理液的原料中还包括有0.8kg的邻苯甲酰磺酰亚胺,其余的与实施例10相同。
57.实施例12本实施例的有机硅行业裂解废液焚烧工艺与实施例10的不同之处在于:处理液的原料中还包括有1.5kg的邻苯甲酰磺酰亚胺,其余的与实施例10相同。
58.对比例对比例1本对比例的有机硅行业裂解废液焚烧工艺与实施例1的不同之处在于:1)、步骤s1中,将裂解废液过滤后得到液态物料和固态物料,将固态骨料经皮带输送机送入回转窑内,将液态物料用隔膜泵送入回转窑内。
59.2)、步骤s2中,将步骤s1中燃烧后产生的烟气经过余热锅炉换热冷却后从1100℃降温至200℃。
60.其余的与实施例1中相同。
61.对比例2本对比例的有机硅行业裂解废液焚烧工艺与实施例3的不同之处在于:步骤s2中,急冷降温包括如下步骤:1)、配置好处理液,然后将处理液用雾化喷淋装置形成处理液雾体喷入急冷塔内;2)、使换热冷却后的烟气与处理液雾体混合后进行热交换;本对比例的处理液由如下重量的原料制成:水515kg、季铵碱5kg、氨基噻二唑3kg、促进剂2kg。
62.其中,季铵碱为四甲基氢氧化铵。促进剂为铜粉。
63.对比例3本对比例的有机硅行业裂解废液焚烧工艺与实施例3的不同之处在于:步骤s2中,急冷降温包括如下步骤:1)、配置好处理液,然后将处理液用雾化喷淋装置形成处理液雾体喷入急冷塔内;2)、使换热冷却后的烟气与处理液雾体混合后进行热交换;本对比例的处理液由如下重量的原料制成:水505kg、乙二胺四乙酸二钠钙15kg、氨基噻二唑3kg、促进剂2kg。
64.其中,促进剂为铜粉。
65.对比例4
本对比例的有机硅行业裂解废液焚烧工艺与实施例3的不同之处在于:步骤s2中,急冷降温包括如下步骤:1)、配置好处理液,然后将处理液用雾化喷淋装置形成处理液雾体喷入急冷塔内;2)、使换热冷却后的烟气与处理液雾体混合后进行热交换;本对比例的处理液由如下重量的原料制成:水503kg、乙二胺四乙酸二钠钙15kg、季铵碱5kg、促进剂2kg。
66.其中,季铵碱为四甲基氢氧化铵。促进剂为铜粉。
67.对比例5本对比例的有机硅行业裂解废液焚烧工艺与实施例3的不同之处在于:步骤s2中,急冷降温包括如下步骤:1)、配置好处理液,然后将处理液用雾化喷淋装置形成处理液雾体喷入急冷塔内;2)、使换热冷却后的烟气与处理液雾体混合后进行热交换;本对比例的处理液由如下重量的原料制成:水508kg、乙二胺四乙酸二钠钙15kg、促进剂2kg。
68.其中,促进剂为铜粉。
69.对比例6本对比例的有机硅行业裂解废液焚烧工艺与实施例3的不同之处在于:步骤s2中,急冷降温包括如下步骤:1)、配置好处理液,然后将处理液用雾化喷淋装置形成处理液雾体喷入急冷塔内;2)、使换热冷却后的烟气与处理液雾体混合后进行热交换;本对比例的处理液由如下重量的原料制成:水508kg、氢氧化钙15kg。氢氧化钙的平均粒径为200nm。
70.性能检测试验检测方法取渣浆状的有机硅行业裂解废液,按照实施例1-12以及对比例1-6的有机硅行业裂解废液焚烧工艺测试处理每吨裂解废液所需时间;按照标准hj-77.2-2008测试外排烟气中二噁英类物质的含量,折算为相当于2,3,7,8-四氯代二苯并-对-二噁英毒性的等价浓度(teq),综合测试结果如表1所示。
71.表1实施例1-12以及对比例1-6的有机硅行业裂解废液焚烧工艺综合测试数据
分析实施例1-3以及对比例1并结合表1可以看出,通过采用整体封装的投料方式,可以将各种形态的有机硅裂解废液进行处理,整体的生产效率大大提升,同样处理一吨物料实施例3相较于对比例1的生产时间节省了约28.9%。并且,相较于常规的冷却方式,采用一次换热降温加二次急冷降温处理后,抑制了在中高温阶段二噁英组份的二次合成,可以看出实施例3相较于对比例1中的二噁英含量从0.78ng降低至0.030ng,远低于国家标准规定的0.5ng,也低于欧盟标准规定的0.1ng,更加绿色环保。
72.分析实施例4-6、对比例2-6并结合表1可以看出,采用本技术的处理液雾化后与高温烟气进行混合,一方面可以迅速降低烟气温度,另一方面可以对烟气中结合氯以及游离氯进行有效的捕集,抑制和阻断二噁英前驱体的二次合成过程,大大降低了了烟气中二噁英的含量。并且,申请人发现当仅添加乙二胺四乙酸二钠钙后,虽然对游离的氯源有一定的中和和消除作用,但是对结合氯并没有很好的效果。另外,当仅加入季铵碱和氨基噻二唑后,虽然结合氯含量得到有效控制,但同时促进剂的催化最有没有得到抑制,导致二噁英含量有小幅上升。并且,相较于常规的氢氧化钙吸附剂,本技术的处理液处理后的烟气二噁英含量下降了约57.7%,去除效果非常明显。
73.分析实施例7-8、实施例9-10并结合表1可以看出,优化和调整季铵碱以及促进剂的组成配比,进一步提升处理液的除氯效果,将烟气中的结合氯源和游离氯源含量降低至
较低水平,阻碍二噁英组分的二次合成过程。可以看出,相较于实施例6,实施例10烟气中二噁英的含量下降至0.0095ng。
74.分析实施例11、实施例12并结合表1可以看出,通过加入邻苯甲酰磺酰亚胺,利用氮原子在高温条件下的高活性对含氯二噁英前驱体进行卤素结合,进一步阻断二噁英的合成,降低烟气中二噁英的总量。
75.本具体实施例仅仅是对本技术的解释,其并不是对本技术的限制,本领域技术人员在阅读完本说明书后可以根据需要对本实施例做出没有创造性贡献的修改,但只要在本技术的权利要求范围内都受到专利法的保护。
再多了解一些
本文用于创业者技术爱好者查询,仅供学习研究,如用于商业用途,请联系技术所有人。