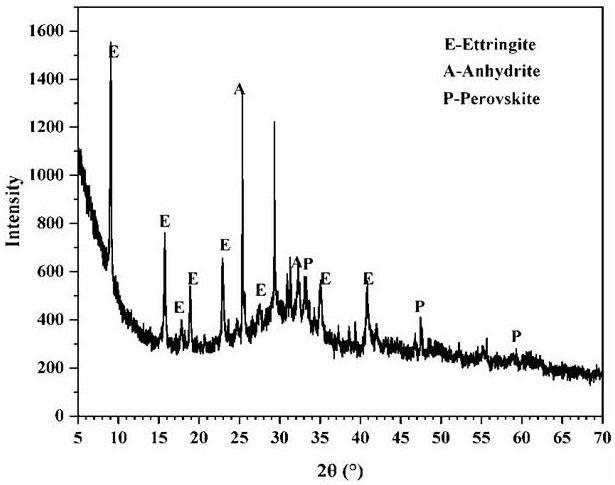
1.本发明涉及混凝土制备材料技术领域,具体涉及一种耐热混凝土胶凝材料及其制备方法、应用。
背景技术:
2.耐热混凝土是一种能长期在200℃~900℃状态下使用且能保持所需的物理力学性能和体积稳定性的混凝土,该混凝土采用的胶凝材料有水硬性和气硬性胶凝材料两大类,其中水硬性胶凝材料有普通硅酸盐水泥、矿渣硅酸盐水泥、以及铝酸盐水泥;气硬性胶凝材料一般有水玻璃和磷酸或磷酸二氢铝等。制备600℃以下耐热混凝土,通常使用普通硅酸盐水泥做胶凝材料,使用适宜的骨料、掺合料以及外加剂拌合就基本可以满足工程需要,如需耐受温度再高,就需要选用铝酸盐水泥等作为胶凝材料。
3.公告号为“cn104529323a”,名称为“一种用普通硅酸盐水泥制备全重矿渣集料的耐热混凝土”的专利申请文件,于2015年4月22日公开了一种采用普通硅酸盐水泥,再加入适量高炉重矿渣骨料、矿渣微粉、粉煤灰、二氧化硅微粉、三聚磷酸钠、偏磷酸钠制备耐热混凝土的方案,得到的耐热混凝土在700℃,保温3h后具有较好的强度,在该方案中使用到了矿渣作为骨料,使用冶金固废矿渣微粉、粉煤灰、二氧化硅微粉、普通硅酸盐水泥作为胶凝材料,使用三聚磷酸钠和偏磷酸钠作为分散剂及高温稳定剂,该方法使用了重矿渣(未水淬、慢冷获得的渣),该渣水化活性低,矿渣利用效果差,在此仅作为骨料使用。按照该专利所述其使用胶凝材料为矿渣微粉、粉煤灰、二氧化硅微粉、普通水泥,按照其配合比普通水泥、矿渣微粉最大使用量各20%,粉煤灰、微硅粉最大使用量10%,按照质量份数2:2:1:1混合制得的胶凝材料,按照gb/t17671-2021水泥胶砂强度检验方法进行试验,一般情况下,胶砂强度无论早期还是后期强度,都不会高,配制混凝土时胶凝材料使用量增大以及使用无机或有机分散减水剂后,或许能达到一个较高的强度水平。所述专利虽然使用了大量的工业固废,但资源利用效率并不高,但对就地使用难以处置的“高炉重矿渣”仍不失为一种好的方法。
4.如于2019年3月12日公开的公告号为“cn109455988a”,名称为“一种400℃耐热胶凝材料的制备方法”的专利文献,公开了一种采用高炉矿渣、氧化锆研磨体以及分散剂和促溶剂制备400℃耐热胶凝材料的方法。可知该方案中,主要采用的是高炉矿渣来制备400℃耐热胶凝材料,该专利方案中采用了高炉矿渣来制备胶凝材料,制备和使用过程较为繁琐,采用湿磨超细粉磨及掺入活化外加剂(机械及化学活化),然后再掺入硅酸盐水泥激发高炉矿渣活性,掺量约为矿渣使用量的10%~20%,经过细磨的矿渣中位粒径d50达到2.2μm~2.8μm,矿渣激活程度仍然相对较低,水化产物基本上是c-s-h,该专利所述方案生成较多水滑石,水滑石在空气中低于200℃加热时,只有层间自由水会被脱除,整体的层状结构基本不受影响;但250℃~450℃时,层板羟基也开始脱水,层状结构中失去更多的水分,因此耐热性能也是有限的。
技术实现要素:
5.四川攀枝花、乐山地区较多矿渣固废资源,在研发多组分协同矿渣基固废胶凝材料的同时,发现使用该胶凝材料除了在常温下具备优异的物理性能以外,在高温下仍具有较好的耐热性能,因此较为深入研究了其水化物的热稳定性及耐热性能。
6.本发明的目的在于提供一种耐热混凝土胶凝材料及其制备方法、应用,以粒化高炉矿渣为主要矿渣基材料,可以使用钛矿渣、硅锰渣进行部分替代,替代量可达40%,另外,使用的石膏优选天然硬石膏,也可以使用改性脱硫石膏、改性磷石膏进行替代,可对西南地区攀枝花、乐山沙湾等地钢铁企业产出的大量含高钛矿渣、工业副产品石膏资源实现有效的综合利用,不仅能满足绝大多数常规工程应用,还可用于200℃~500℃耐热混凝土工程。
7.本发明通过下述技术方案实现:一种耐热混凝土胶凝材料的应用,采用包括矿渣基材料、石膏、硫铝酸盐水泥熟料制得的胶凝材料,能在200℃~500℃的耐热混凝土工程中应用。
8.一种耐热混凝土胶凝材料的制备方法,如前述的胶凝材料,按重量百分比计,取包括以下原料:矿渣基材料:68%~85%;石膏:12%~25%;硫铝酸盐水泥熟料:3%~7%;按前述原料比例,将矿渣基材料、石膏和硫铝酸盐水泥熟料单独粉磨后均匀混合或者共同粉磨制得。
9.优选的,所述硫铝酸盐水泥熟料中无水硫铝酸钙和硅酸二钙含量之和不应小于60%,且无水硫铝酸钙含量不应小于25%,硅酸二钙含量不应小于25%。
10.所述矿渣基材料为粒化高炉矿渣、钛矿渣、硅锰渣等组成的混合物。
11.根据按总胶凝材料重量百分比计,所述矿渣基材料中,粒化高炉矿渣的含量》30%,钛矿渣与硅锰渣的含量为《40%,所述粒化高炉矿渣符合gb/t 203中的规定。
12.所述钛矿渣为高炉冶炼生铁时所得的含有硅酸盐和硅铝酸盐的熔融物,经淬冷成粒后tio2含量大于10%的矿渣;所述的硅锰渣是冶炼硅锰合金时经氧化钙还原后形成的一种工业副产品,从矿物成分上看,硅锰渣主要由casio3、caal2o4、ca2al2sio4、ca2mgsio7和mgsio3组成。
13.所述矿渣基材料、石膏和水泥熟料的比表面积均不小于420m2/kg。
14.所述石膏选自天然硬石膏、改性脱硫石膏、改性磷石膏中的至少一种。
15.所述脱硫石膏和磷石膏均为灼烧温度为650℃~850℃,保温时间大于20min的条件下得到改性石膏。
16.一种耐热混凝土胶凝材料,采用前述的制备方法得到的耐热混凝土胶凝材料。
17.本发明与现有技术相比,具有以下优点及有益效果:(1)本方案中,采用的制备原料中水泥熟料非常少(重量百分比不高于7%),得到的胶凝材料,具有低水化热、高强、高折压比、耐腐蚀等性能,且仍能适用于200℃~500℃的耐热混凝土工程。
18.(2)该混凝土胶凝材料采用具有一定矿物组成的硫铝酸盐水泥熟料作为激发材料之一,有别于使用硅酸盐熟料或者水泥做激发剂,能在水化过程一开始就能产生大量的钙
矾石,水化初期几乎没有c-s-h水化产物,直至水化后期28d才有少量出现。该品种水泥的一天强度较通用水泥偏低,但三天以后强度增进迅速,28d抗压、抗折强度远远高于通用水泥,且水化热极低,折压比远高于其他品种水泥。
19.(3)采用本方案,胶凝材料制备过程涉及的固废使用量可大于70%以上,若石膏类组分使用改性固废石膏,固废使用量甚至可达到95%,除常温下具有各种优异物理性能外,还能满足200℃~500℃范围的耐热混凝土施工要求。同时,因大量使用固废,该胶凝材料具有较低的碳排放,吨产品碳排放仅为通用硅酸盐水泥的四分之一,具有较好的经济和社会效益。
附图说明
20.图1是胶凝材料水化28d后水化物衍射物图。由图可知,水化物主要是钙矾石、未反应的石膏以及钙钛石。
21.图2 是胶凝材料标养60天后水化物tg图。
22.图3是不同养护龄期、加热方式、加热温度条件下的水化物衍射物图。
23.图4是采用实施例7中的胶凝材料制得的耐热混凝土试件分别300℃、500℃、700℃、900℃条件下加热后的实物图。
24.图5是图4中第7、8号试件的放大图。
具体实施方式
25.下面结合实施例对本发明作进一步地详细说明,但本发明的实施方式不限于此。
26.应该指出,以下详细说明都是示例性的,旨在对所要求的本发明提供进一步的说明,除非另有说明,本文使用的所有技术和科学术语具有与本发明所属技术领域的普通技术人员通常理解的相同含义。
27.本发明中,所述粒化高炉矿渣为符合标准gb/t 203《用于水泥中的粒化高炉矿渣》要求的矿渣。
28.本发明在此基础上引入了钛矿渣、硅锰渣等固废与粒化高炉矿渣配合使用。通过钛矿渣、硅锰渣等的掺入,扩大了惰性及活性较差的材料的使用范围,提高了固废的使用量。在该水泥体系中粒化高炉矿渣激发效果优异,高掺钛矿渣、硅锰渣、粉煤灰等后也依然能够保持较高水平的物理强度。
29.本方案得到的胶凝材料的水化产物早期主要为钙矾石(aft),该水化产物在100℃左右可发生脱水,有研究发现即便在一定温度脱水后的钙矾石在回水以后,试件物理强度能够继续保持,甚至还略有升高,这是该类水泥水化物的一个很重要的特性之一。该胶凝材料水化物中几乎没有氢氧化钙,因此避免了高温下氢氧化钙分解导致的强度降低等问题。
30.下面以几个典型实施例来列举说明本发明的具体实施方式,当然,本发明的保护范围并不局限于以下实施例。
31.实施例1-12:主要涉及一种耐热混凝土胶凝材料,按下表1所示进行原料配置。
32.表1 原料配置表
上述原料配置表中,其中矿渣基材料为粒化高炉矿渣、钛矿渣、硅锰渣等组成的混合物。粒化高炉矿渣为符合标准 gb/t 203《用于水泥中的粒化高炉矿渣》要求的矿渣;钛矿渣为高炉冶炼生铁时所得的含有硅酸盐和硅铝酸盐的熔融物,经淬冷成粒后tio2含量大于10%的矿渣;硅锰渣是冶炼硅锰合金时经氧化钙还原后形成的一种工业副产品,从矿物成分上看,硅锰渣主要由casio3、caal2o4、ca2al2sio4、ca2mgsio7和mgsio3组成。
33.改性脱硫石膏和改性磷石膏为脱硫石膏和磷石膏在灼烧温度为650℃~850℃,保温时间大于20min的条件下得到改性石膏。
34.所述硫铝酸盐熟料中的主要矿物包括:、c2s、c4af、caso4、ct和f-cao,熟料,、c2s含量之和不应小于60%,且含量不应小于25%,硅酸二钙含量不应小于25%。其中,为无水硫铝酸钙,c2s为硅酸二钙,c4af为铁铝酸四钙,caso4为硫酸钙,f-cao为游离氧化钙,ct为钙钛石。
35.另外,矿渣基材料、石膏和水泥熟料的比表面积均不小于420m2/kg。
36.上述所使用的材料可根据易磨性差异的不同分类进行单独或者混合粉磨,然后再进行混拌,得到耐热混凝土胶凝材料,可用于200℃~500℃的耐热混凝土工程中。
37.需要说明的是,本发明所涉及的胶凝材料除上述实施例所涉及的原料外,还可选择性的添加一些外加化学试剂,诸如碳酸盐、柠檬酸、亚硝酸盐等,以调整胶凝材料的标准稠度用水量、凝结时间、提高早期强度等。
38.实施例13:本实施例主要涉及一种耐热混凝土胶凝材料的制备方法,具体包括以下步骤:s1:先将实施例1-12中的矿渣基材料所采用的原料分别进行烘干粉磨,考虑到各材料易磨性不一致性,可以根据实际情况将所使用材料单独或者混合粉磨,如粒化高炉矿渣与钛矿渣、硅锰渣等按照适当比例进行粉磨,石膏与熟料按照适当比例混合后进行粉磨。使得粉磨的矿渣基材料比表面积要求大于420m2/kg;石膏以及水泥熟料粉磨至比表面积大于420m2/kg。
39.s2:将粉磨好的材料按照比例使用混拌设备充分混合后即得所需胶凝材料。
40.下述以一个具体地实施方式进一步说明本方案。在制备上述实施例1-12所述胶凝
材料时,矿渣类使用立式磨进行烘干粉磨,比表面积控制450
±
10m2/kg,磨制的矿粉水份小于1.0%,石膏类、硫铝熟料单独粉磨,比表面积控制430
±
10m2/kg,再将粉磨好的上述材料按照比例使用混拌设备充分混合后即得胶凝材料。如果石膏类是改性石膏,可以与熟料按比例配比进行混合粉磨。
41.取上述实施例1-12制得的一种耐热混凝土胶凝材料进行以下试验:按照《水泥胶砂强度检验方法(iso法)》gb/t 17671对胶凝材料检测3d、7d、28d、60d抗折抗压强度,检测结果如下表2所示。
42.表2 标准养护的抗折、抗压强度数据从上述表2可知,实施例1-12得到的胶凝材料的强度数据来看,粒化高炉矿渣的配比低,钛矿渣、硅锰渣比例相对比例过大,且硫铝熟料配比低,表现出各龄期强度都很低,甚至28天抗压强度达不到40mpa,虽然60天强度能有较大增长,但早期强度过低,凝结时间过长,会严重影响胶凝材料的使用。实施例6中粒化高炉矿渣比例提高至80%,各龄期强度表现优异,如果再适当提高硫铝熟料的配比至5%,效果更为理想。实施例7-11在粒化高炉矿渣、钛矿渣掺量相对不变的情况下使用了不同的石膏,使用改性磷石膏要比使用脱硫石膏和天然石膏的强度稍微高一些。实例12只使用了粒化高炉矿渣,未掺钛矿渣及硅锰渣,硫铝熟料及石膏掺加适宜,物理强度表现优异。
43.图2是实施例7中得到的胶凝材料按照0.3的水胶比成型净浆试块,使用净浆在常温(20℃)的标养60天后水化物tg图。由图2可知,水化物在80℃前就有7.47%质量损失,主要为自由水和 c-s-h失水,100℃左右有8.05%左右的质量损失,为钙矾石部分失水,100℃-400℃有3.44%的质量损失,直至900℃有约4.91%质量损失,主要为非晶态物质失水。
44.按照实施例12配制混凝土并进行耐热混凝土相关指标检测。
45.混凝土配合比如表4所示(按质量分数比计),检测结构如表5所示。
46.其中烘干强度:经标养后的试块,置于电热恒温干燥箱中,保持110℃
±
5℃下烘干24小时,冷却至室温,然后试压一组得到的强度值。
47.残余强度:经烘干后的试块置于箱式电炉中加热,按2℃/min~3℃/min匀速升温至
设定温度(200℃、300℃、400℃、500℃),恒温3h后,自然冷却至室温,立即送压得到的强度值。
48.表4表5线变化率经检测均小于1.0%。
49.再按照实施例7配制混凝土并进行耐热混凝土相关指标检测。
50.混凝土配合比如表6所示(按质量分数比计),检测结构如表7所示。
51.表6表7线变化率经检测均小于1.0%由表5、7可知,前述实施例12及实施例7制得的胶凝材料按照yb/t 4252-2011《耐热混凝土应用技术规程》拌制的热耐热混凝土经过500℃高温加热3小时冷却后,强度保损失率分别为12.5%、20.8%,可保证满足大于设计强度的50%指标要求,安全用于500℃耐热混凝土工程。
52.图4是采用实施例7中的胶凝材料制得的耐热混凝土试件,在标养28d后,经110℃烘箱烘干24小时并按照2℃/min~3℃/min升温速率分别在300℃、500℃、700℃、900℃温度下加热3h后自然冷却的实物图;图5是图4中第7、8号试件的放大图。由图3-4可知,在900℃时出现了轻微裂痕,在300℃~700℃条件下形态较完整,无裂纹,线变化率小于
±
1.0%,可见本方案制备方法得到的胶凝材料可安全用于500℃耐热混凝土工程中。
53.现有技术中,已有专家、学者对钙矾石(c3a
·
3caso4·
32h2o)作为水化产物进行了大量研究,钙矾石晶体形状为六角形棱柱体,由柱和平行于柱的c轴之间的沟槽组成,沟槽之间有so
42-和h2o分子,柱的组成为{ca6[a1(oh)6]2·
24ho}
6
,沟槽中的物质为[(so4)3·
2h2o]
6-,每个柱由一个铝氧八面体[al(oh)6]
3-和三个钙多面体交替重迭而成,铝八面体中每个a1
3
连接6个oh-,两个a1
3
连接12个oh-,即6个结晶水,铝八面体和钙多面体构成了钙矾石结构基本单元,每个ca
2
除了与4个oh-相连外,还连接4个水分子,三个ca
2
连接12个水分子,6个ca
2
连接24个水分子,其中12个水分子与ca
2
之间的键长较短,结合较牢固,称为主顶点水。另外12个水分子与ca
2
之间的键长较长,键强较弱,称为副顶点水。沟槽中2个h2o与柱的结合力很弱,与主顶点水的连接很弱,容易失去。钙矾石40℃受热时,至多失去沟槽内
的两个水分子,对钙矾石结构没有影响,60℃受热,可失去1.5个副顶点水,结构也没有什么变化,80℃受热,xrd衍射峰变矮,94℃受热一小时,钙矾石特征峰几乎完全消失。100℃受热一天钙矾石特征峰完全消失,钙矾石已变为无定型物质,未发现单硫型或者其他物质的特征峰。200℃、300℃、400℃乃至500℃为无定型结构,400℃时结晶水数为1.9个,温度升至600℃,结晶水只存在1.2个,al-oh继续被破坏,结构呈现根本性破坏,950℃时[al(oh)6]
3-结构完全破坏,最终转变为、硬石膏和f-cao。
[0054]
通过实验室试验证明:含以钙矾石为主要水化产物的混凝土试件在烘箱110℃度烘干24小时检测,钙矾石峰仍然存在,但峰形变矮了,烘箱加热直至140℃~150℃,钙矾石峰才基本消失。另外试件在100℃沸煮8小时,钙矾石xrd衍射峰基本保持不变,试件强度基本保持。说明在湿热环境中,钙矾石是稳定的。
[0055]
由本方案制得的水硬性胶凝材料的水化产物主要为钙矾石,使用该水泥制备耐热混凝土,随着加热温度的上升,虽然钙矾石衍射峰消失,但试件仍然保持较高的物理强度,特别的当加热温度上升至400℃时,强度还有所上升。直至500℃时,残余强度仍然保持较高水平,并且试件完好,未出现开裂现象。经测试900℃时残余强度相对较低,原因是高温下,胶凝物质有继续分解,加之骨料与水化物膨胀率差异大等原因,结构破坏程度较大。
[0056]
图3是试件不同养护龄期、加热方式、加热温度条件下的水化物衍射物图。其中,1#是试件20℃标准养护箱标养60d的水化物衍射物图,2#是试件20℃标准养护箱标养90d的水化物衍射物图,3#是试件标养60d后在100℃沸煮箱沸煮24h的水化物衍射物图,4#是试件标养60d后110℃烘箱加热24h的水化物衍射物图,5#是试件标养60d后150℃烘箱加热16h的水化物衍射物图,6#是试件标养60d后400℃节能箱式电阻炉加热3h的水化物衍射物图。
[0057]
由图3中1#、2#、3#图示可知:钙矾石ettringite的峰基本保持一致,经过沸煮后水化物基本无变化,表明100℃湿热环境下,钙矾石是基本稳定的。在110℃干燥环境下,钙矾石峰形变矮,说明有部分钙矾石分解,部分结晶水失水。150℃干燥环境下,钙矾石峰基本消失,400℃、500℃、700℃衍射谱线均基本与5#谱线保持一致,主要为硬石膏和钙钛石衍射峰,其余为非晶态物质,钙钛石(perovskite)较为稳定地存在于各龄期及各试验环境条件下水化物中。
[0058]
进一步验证,采用本方案得到的胶凝材料,可用于200℃~500℃的耐热混凝土工程中,制得的混凝土耐热性能好,物理强度表现突出,常温下自身具有低水化热、高折压比、耐腐蚀等优异性能。
[0059]
以上所述,仅是本发明的较佳实施例,并非对本发明做任何形式上的限制,凡是依据本发明的技术实质对以上实施例所作的任何简单修改、等同变化,均落入本发明的保护范围之内。
再多了解一些
本文用于创业者技术爱好者查询,仅供学习研究,如用于商业用途,请联系技术所有人。