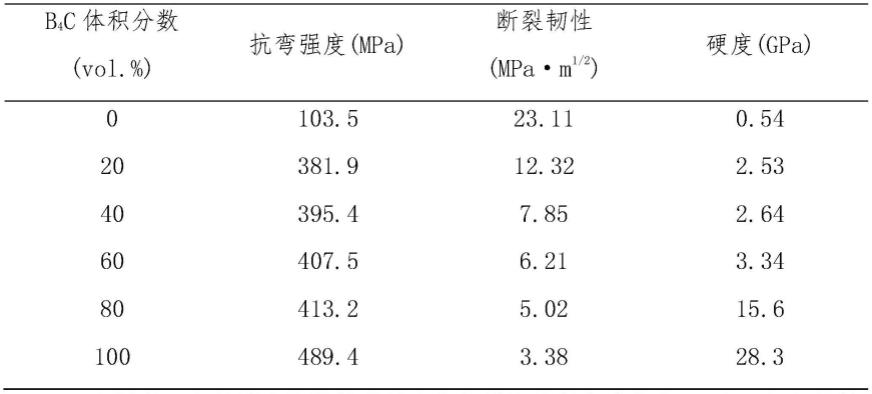
一种b4c/al仿贝壳梯度装甲及其制备方法
技术领域
1.本发明涉及一种装甲防护材料,具体涉及一种b4c/al仿贝壳梯度装甲及其制备方法。
背景技术:
2.随着反装甲武器技术的高速发展,武器装备的战场生存能力对装甲防护材料的性能提出了更高的要求,从而促进了装甲防护材料的更大发展。装甲防护材料正朝着强韧化、轻量化、多功能化和高效化的方向发展。陶瓷材料经过增韧被广泛应用于军事防护领域,当前市面上广泛使用的双叠层装甲面板、背板性能差异大,界面阻抗不匹配,抗弹性能未能得到充分发挥。相较陶瓷/金属双叠层装甲,同时保留了陶瓷高硬、高强与金属高韧、高抗拉的梯度装甲对防护装甲吸收能量、抗断裂等能力有极大的提高。除此之外,梯度装甲的陶瓷相含量沿防护装甲厚度方向连续变化,材料性能同样沿厚度方向连续变化,界面强度较之双叠层装甲有所提高。最后,相比于叠层复合材料尚需胶粘工艺,梯度复合材料的允许直接烧结成型,工艺也相对简单。梯度复合材料是性能优良的装甲防护材料,但由于国内应用于装甲领域的梯度复合材料较少,性能数据不全面,且结构单一,这极大限制了我国梯度陶瓷复合装甲的发展。因此,材料、结构逐渐成为开发新型梯度装甲领域的研究热点。
3.抗弹陶瓷中,b4c陶瓷硬度最高、密度最低,从性能上讲是最理想的装甲陶瓷,美国的黑鹰武装直升机的机身腹部和乘员座椅即采用了b4c和kevlar组成的复合装甲。然而性能优良的b4c陶瓷研究目前多停留在双叠层装甲领域,较差的韧性一直是制约b4c陶瓷应用的主要因素,b4c/al复合材料则可以改善这一不足,而通过复合不同体积分数b4c/al复合材料形成的b4c/al梯度装甲更是防护装甲未来发展趋势之一。
4.当前,b4c/al复合材料的制备多采用传统的热压烧结技术,其制备碳化硼陶瓷的烧结温度为2200~2300℃,保温时间0.5~2h。热压烧结长时间的高温烧结,使得试样显微组织晶粒粗大,在晶界处生成杂质相。除此之外,当材料中b4c含量超过30%时,在长时间高温烧结作用下,熔点低的金属铝不可避免析出,就会出现材料性能下降的趋势,甚至烧结制备失败,这一缺点同样会影响到b4c/al梯度装甲的烧结制备。
5.根据目前的研究表明,太原理工大学张鹏620℃,1h制备的20vol.%b4c/al,硬度仅为1.09gpa。高占平通过真空热压法在烧结温度、保温时间分别为650℃、1h的烧结条件下制备40vol.%b4c/al,硬度仅为1.36gpa。可以看出,由于热压真空烧结的长时间高温烧结会降低材料性能,以上研究人员在制备b4c/al复合材料时均采用低温烧结。然而,由于碳化硼颗粒的高熔点,过低的烧结温度并不能保证复合材料的致密度,随着b4c颗粒的持续增多,高含量b4c的b4c/al复合材料性能最终难以得到发挥,因此内有高含量b4c复合材料靶板层的b4c/al梯度装甲,存在着迎弹面靶板层硬度低,梯度装甲抗冲击性能差、多次受打击性能不理想以及烧结制备成功率低等问题。
技术实现要素:
6.本发明的目的是提供一种b4c/al仿贝壳梯度装甲及其制备方法,以克服现有技术针对内有高含量b4c复合材料靶板层的b4c/al梯度装甲的烧结制备问题,有效提高高含量b4c复合材料靶板层的b4c/al梯度装甲迎弹面靶板层硬度,梯度装甲抗冲击性能及多次受打击性能。
7.为了达到本发明的目的,本发明所采用的技术方案为:一种b4c/al仿贝壳梯度装甲的制备方法,其特征在于,包括以下步骤:
8.步骤一:将b4c和al粉末作为初始原料,初始原料按照b4c的体积比从100%到0%梯度均匀下降进行配比,添加初始原料的3%的ti粉作为添加剂,b4c含量占比为100%不添加ti粉,然后分别制成b4c的质量比均匀下降的n个级别的悬浮液,进行超声振动搅拌;
9.步骤二:将混合液体倒入球磨罐中,球磨12~15h。
10.步骤三:将球磨得到的浆料放入真空干燥箱中干燥3~5h,冷却后过筛,得到n种不同组分的精细混合粉体;
11.步骤四:将配比为100%的b4c精细混合粉体装入石墨模具,进行压片成型获得陶瓷生坯;
12.步骤五:对成型后的陶瓷生坯进行等离子烧结,获得b4c/al仿贝壳装甲的第1层靶板材料,从模具取出第1层靶板材料并研磨其表层石墨纸;
13.步骤六:将第1层靶板材料重新装入石墨模具,将获得的第2种b4c含量下降一级的混合粉体同样装入石墨模具,且装在第1层靶板材料上方,再次压片成型并等离子烧结;
14.步骤七:按照b4c含量由高到低将后几种混合粉体相继依次装入石墨模具,依据不同体积分数复合材料烧结温度区间存在的重合区域,将重合区域复合材料作为粘结层,在其基础上烧结其他熔点相对较低的靶板材料,最终实现b4c/al仿贝壳梯度装甲的烧结制备。
15.进一步的,上述步骤一中,悬浮液的介质为无水乙醇,超声振动搅拌时间为40~50min。
16.进一步的,上述步骤二中,选取无水乙醇作为球磨介质、氧化锆陶瓷作为磨球,球料比设置为8~10:1,球磨转速为200r/min。
17.进一步的,上述步骤三中,真空干燥箱中,设置干燥温度为140℃。
18.进一步的,上述步骤五中,第1层靶板材料的烧结参数为:30mpa,1200℃之前,以200℃/min升温,达到1200℃时,保温烧结1min;超过1200℃之后,以100℃/min升温至1700℃,保温烧结11min;后以100℃/min冷却至1000℃,最后随炉冷却至室温。
19.进一步的,上述步骤六中,第2层的烧结参数:30mpa,1200℃之前,以200℃/min升温,达到1200℃时,保温烧结1min;超过1200℃之后,以100℃/min升温至1400℃,保温烧结7min;后以100℃/min冷却至1000℃,最后随炉冷却至室温。
20.进一步的,上述上述精细混合粉体一共有6级,后面4层的烧结参数是:30mpa,保温时间分别为7min、11min、7min、7min,从1200℃起,梯度降低200℃。
21.进一步的,直到最后一层的压片成型前,所用的石墨模具的内径均为φ20mm,压头直径均为φ20mm,在压头1受力面上平行设置有凹槽2。
22.进一步的,上述制备方法制得的b4c/al仿贝壳梯度装甲。
23.与现有技术相比,本发明具有以下优点:
24.1、本发明的b4c/al仿贝壳梯度装甲使用al为基体相,b4c为增强相,加入少量的ti改善基体相与增强相之间的润湿性。通过石墨模具上的开槽压头,改进了靶板层间的结构,压头的1mm深的凹槽可在每一层靶板材料上形成凹槽,使每层靶板材料相互咬合,形成矿物桥互锁结构,同时通过等离子烧结法进行烧结,因此制得的产物致密度高、晶粒平均粒径分布均匀。
25.2、在本发明制备的b4c/al仿贝壳梯度装甲中,第1层靶板材料为抗弹陶瓷中密度最低、硬度最高的b4c陶瓷,在抗侵彻时起到对子弹的磨蚀作用。第2层靶板材料(80vol.%b4c/al复合材料)可以作为粘结层将第1层靶板材料的b4c与第3层靶板材料(60vol.%b4c/al复合材料)烧结为一体。除此之外,80vol.%b4c/al复合材料具有较高硬度同时具有一定的韧性,对第1层b4c陶瓷可以起到强力的支撑作用。同理,后面几层靶板材料同样作为内侧相应位置靶材材料的粘结层。
26.3、对结构的丰富是梯度装甲发展必不可少的一环,效仿自然生物材料结构,从而丰富梯度陶瓷复合装甲结构,是有效又合理的途径。在众多生物材料结构中,贝壳这种具有高强度、高韧性的天然陶瓷最具参考价值。贝壳结构是由角质层、棱柱层和珍珠层构成,足够数量的研究表明贝壳高韧性的力学性能主要源于其珍珠层文石晶体与有机基质的交替叠层排列方式。本发明的b4c/al仿贝壳梯度装甲层间结构为仿贝壳珍珠层的矿物桥互锁结构,矿物桥的存在阻碍裂纹扩展,增加裂纹偏转概率,而片层拔出必须使矿物桥剪切断裂,进一步增加了拔出阻力,有效增强了梯度装甲的韧性,提高抗侵彻性能。
27.4、本发明采用分步骤多段sps放电等离子烧结技术,相比传统的热压烧结技术,放电等离子烧结技术是在加压条件下向粉末颗粒之间直接通入脉冲电流实现均匀加热烧结,分步骤多段sps放电等离子烧结技术具有等离子烧结技术烧结温度低、保温时间短的优点,例如,在制备b4c陶瓷时,sps放电等离子烧结技术可以将烧结温度降低至1800℃以内,保温时间最多20min。采用本发明方法烧结制备的材料性能更加优越,也更加高效,可以实现梯度装甲的烧结制备。尤其是靶板面层与背层烧结工艺差距大时,分步骤多段等离子烧结技术具有重要意义。
28.5、本发明制备工艺制得的b4c/al仿贝壳梯度装甲材料具有较高的抗冲击性能和多次受打击性能,能够广泛应用于单兵防护、装甲车辆、航空航天、船舰等军事作战系统重要部分的防护。
附图说明
29.图1为不同组分b4c/al复合材料断口sem。(a)b4c;(b)80vol.%b4c/al;(c)60vol.%b4c/al;(d)40vol.%b4c/al;(e)20vol.%b4c/al;(f)al。
30.图2为石墨模具上的开槽压头图。
31.图3为b4c/al仿贝壳梯度装甲截面图。
具体实施方式
32.下面结合具体实施例和附图对本发明进行详细地说明。
33.本发明涉及的b4c/al仿贝壳梯度装甲的制备方法,是采用放电等离子烧结制备多
层不同组分b4c/al复合材料的首次尝试。超声振动搅拌工艺、球磨工艺、过筛工艺、等离子烧结工艺的调控,是b4c/al复合材料气孔少、晶粒平均粒径分布均匀的充分条件。致密和均匀的晶粒结构为其综合力学性能的优异性提供了可能,也未分步骤多段烧结以及矿物桥互锁结构的实现提供了可能,从而获得了一种简单、高效、高性能仿贝壳梯度装甲的制备方法。
34.实施例1:一种b4c/al仿贝壳梯度装甲的制备方法,具体包括以下步骤:
35.步骤一:将平均粒径为1μm,纯度为99%,b4c含量分别为100%、80%、60%、40%、20%、0%的六种级别的b4c/al复合材料作为初始原料,添加初始原料的3%的ti粉作为添加剂,b4c含量占比100%、0%的初始原料中不添加ti粉,按化学计量比计算出所需要的质量,然后进行称量。将称量好的原料分别以无水乙醇为介质制备成体积分数为2.0vol.%的悬浮液,超声振动搅拌40min;
36.步骤二:将超声振动搅拌均匀的悬浮液倒入球磨罐中,并加入适量的氧化锆球,球-料的质量比约为10:1,在行星式球磨机上球磨约12h;
37.步骤三:在zk-40型电热真空干燥箱中经过140℃干燥3h,真空干燥完成后冷却,使用120目筛子对其进行过筛,分别得到六种均匀的精细混合粉体;
38.步骤四:将干燥后的b4c粉末装入内径为φ20mm石墨模具,塞入石墨模具上的开槽压头,在压片机上以30mpa压力进行压实,制成高度为2mm的带槽柱状。
39.步骤五:将压片成型后的陶瓷生坯连同石墨模具一同放入等离子烧结炉(30mpa),进行烧结,获得b4c陶瓷。为了防止粉末晶粒长大,1200℃之前,以200℃/min升温;达到1200℃时,保温烧结1min,以消除空隙;超过1200℃之后,为了获得综合性能优异的陶瓷,需要使晶粒充分生长,因此降低升温速率,以100℃/min升温至1700℃,保温11min;最后以100℃/min冷却至1000℃,再随炉冷却至室温,即可得到仿贝壳梯度装甲第1层靶板材料,从模具取出第1层靶板材料并研磨其表层石墨纸。
40.步骤六:将获得的第1层靶板材料重新装入石墨模具,将干燥后的80vol.%b4c/al粉末同样装入石墨模具,且装在第1层靶板材料上方,塞入石墨模具上的开槽压头,再次压片成型并等离子烧结(30mpa),获得b4c/al仿贝壳装甲的前2层靶板材料。为了防止粉末晶粒长大,1200℃之前,以200℃/min升温;达到1200℃时,保温烧结1min,以消除空隙;超过1200℃之后,为了获得综合性能优异的陶瓷,需要使晶粒充分生长,因此降低升温速率,以100℃/min升温至1400℃,保温7min;最后以100℃/min冷却至1000℃,再随炉冷却至室温,即可得到仿贝壳梯度装甲前2层靶板材料,从模具取出前2层靶板材料并研磨其表层石墨纸。
41.步骤七:将获得的前2层靶板材料重新装入石墨模具,将干燥后的60vol.%b4c/al粉末同样装入石墨模具,且装在前2层靶板材料上方,塞入石墨模具上的开槽压头,再次压片成型并等离子烧结(30mpa),获得b4c/al仿贝壳装甲的前3层靶板材料。为了防止粉末晶粒长大,1000℃之前,以200℃/min升温;达到1000℃时,保温烧结1min,以消除空隙;超过1000℃之后,为了获得综合性能优异的陶瓷,需要使晶粒充分生长,因此降低升温速率,以100℃/min升温至1200℃,保温7min;最后以100℃/min冷却至1000℃,再随炉冷却至室温,即可得到仿贝壳梯度装甲前3层靶板材料,从模具取出前2层靶板材料并研磨其表层石墨纸。
42.将获得的前3层靶板材料重新装入石墨模具,将干燥后的40vol.%b4c/al粉末同样装入石墨模具,且装在前3层靶板材料上方,塞入石墨模具上的开槽压头,再次压片成型并等离子烧结(30mpa),获得b4c/al仿贝壳装甲的前4层靶板材料。为了防止粉末晶粒长大,800℃之前,以200℃/min升温;达到800℃时,保温烧结1min,以消除空隙;超过800℃之后,为了获得综合性能优异的陶瓷,需要使晶粒充分生长,因此降低升温速率,以100℃/min升温至1000℃,保温11min;最后以100℃/min冷却至800℃,再随炉冷却至室温,即可得到仿贝壳梯度装甲前4层靶板材料,从模具取出前4层靶板材料并研磨其表层石墨纸。
43.将获得的前4层靶板材料重新装入石墨模具,将干燥后的20vol.%b4c/al粉末同样装入石墨模具,且装在前4层靶板材料上方,塞入石墨模具上的开槽压头,再次压片成型并等离子烧结(30mpa),获得b4c/al仿贝壳装甲的前5层靶板材料。为了防止粉末晶粒长大,600℃之前,以200℃/min升温;达到600℃时,保温烧结1min,以消除空隙;超过600℃之后,为了获得综合性能优异的陶瓷,需要使晶粒充分生长,因此降低升温速率,以100℃/min升温至800℃,保温7min;最后以100℃/min冷却至600℃,再随炉冷却至室温,即可得到仿贝壳梯度装甲前5层靶板材料,从模具取出前5层靶板材料并研磨其表层石墨纸。
44.将获得的前5层靶板材料重新装入石墨模具,将干燥后的al粉末同样装入石墨模具,且装在前5层靶板材料上方,塞入正常压头,再次压片成型并等离子烧结,获得b4c/al仿贝壳装甲。为了防止粉末晶粒长大,400℃之前,以20℃/min升温;达到400℃时,保温烧结1min,以消除空隙;超过400℃之后,为了获得综合性能优异的陶瓷,需要使晶粒充分生长,因此降低升温速率,以20℃/min升温至600℃,保温7min;最后以20℃/min冷却至400℃,再随炉冷却至室温,即可得到仿贝壳梯度装甲样品。
45.图1所示为扫描电镜(sem)作用下的al、20vol.%b4c/al、40vol.%b4c/al、60vol.%b4c/al、80vol.%b4c/al、b4c等材料的断面微观形貌。纯al弯曲断裂在塑性变形过程中微小孔洞聚集、相互连结后形成较大面积的韧窝(见图1(a)),从图中可以看出纯al的断裂形式为较明显的韧性断裂。较之纯al,20vol.%b4c/al复合材料断面上韧窝的大小在减小的同时韧窝数量有所增多,除此之外,韧窝内和边缘存在众多细小的b4c颗粒对复合材料性能起增强作用(见图1(b))。当b4c/al复合材料中b4c含量达到40%时,断面上韧窝的大小再次减小,数量也再次增多,断面上b4c颗粒较之20vol.%b4c/al明显增多,复合材料表面b4c颗粒分布均匀,但仍存在少部分团聚区域,团聚部分存在少量气孔(见图1(c))。当b4c/al复合材料中b4c含量达到60%时,断面上韧窝进一步减小,较为平均的分布于团聚的b4c颗粒四周,形成众多微小的气孔。材料韧性下降的同时在硬度有所提高,但因众多气孔的存在材料的综合性能略有不足(见图1(d))。随着b4c含量增加到80%,b4c以较为致密的方式大面积出现,断面上韧窝近乎不可见融入其中,气孔较少,材料韧性下降硬度提高(见图1(e))。最后是纯b4c的断面微观形貌,b4c陶瓷在脉冲电流均匀加热,快速烧结,避免因持续高温烧结显微组织粗大生成的杂质相(见图1(f)),图中b4c陶瓷致密无明显气孔。
46.梯度装甲随着厚度变化靶板材料的性能也随之变化,制备工艺也随之改变,而仿贝壳梯度装甲的矿物桥互锁结构,需要本发明改进的一次sps放电等离子烧结法来实现。本发明创新性的采用分步骤多段烧结法,首先通过烧结制备不同组分的b4c/al复合材料,确定最优烧结温度、保温时间。然后优先烧结熔点高的靶板材料。进而依据不同体积分数复合材料烧结温度区间存在的重合区域,将重合区域复合材料作为粘结层,在其基础上烧结其
他熔点相对较低的靶板材料,最终实现仿贝壳梯度装甲的烧结制备。
47.表1所示为不同体积分数的b4c/al复合材料的力学性能。从表中可得,随着b4c颗粒体积分数的增加,b4c/al复合材料的抗弯强度总体也具有一个增大的趋势。其中,60vol.%b4c/al抗弯性能略有下降,这是由于1200℃未能使b4c足够致密,高温又使金属铝过于活跃,从团聚的b4c颗粒缝隙流出,形成较多的气孔。不同体积分数的b4c/al复合材料的硬度则是随着b4c颗粒体积分数的增加而逐步增加,断裂韧性则相反。
48.表1不同体积分数的b4c/al复合材料的力学性能。
[0049][0050]
太原理工大学博士陈洪胜采用真空热压烧结制备了部分b4c/al复合材料,表2所示为其制备的b4c/al复合材料的力学性能。
[0051]
表2部分热压烧结制备的b4c/al复合材料的力学性能。
[0052][0053]
对比两表所示的力学性能,本发明所采用放电等离子烧结b4c/al复合材料的性能远超热压烧结制备b4c/al复合材料,且对b4c含量超过40%的b4c/al复合材料做出制备尝试。研究发现,放电等离子烧结制备的b4c/al复合材料足以满足仿贝壳梯度装甲每层靶板材料的性能要求。
[0054]
参见图2,图2(b)是图2(a)的俯视图。石墨模具中包括压头1,本发明中,在压头1受力面上平行设置有凹槽2,本实施例中,压头的直径为20mm,所述凹槽深度为1mm,凹槽之间间距为4mm。
[0055]
参见图3,从图中可得,特制压头的1mm深的槽可在每一层靶板材料上形成凹槽,使
每层靶板材料相互咬合,形成矿物桥互锁结构。矿物桥的存在阻碍裂纹扩展,增加裂纹偏转概率,而片层拔出必须使矿物桥剪切断裂,进一步增加了拔出阻力,增强了梯度装甲的韧性。
[0056]
本发明的内容不限于实施例所列举,本领域普通技术人员通过阅读本发明说明书而对本发明技术方案采取的任何等效的变换,均为本发明的权利要求所涵盖。
再多了解一些
本文用于创业者技术爱好者查询,仅供学习研究,如用于商业用途,请联系技术所有人。