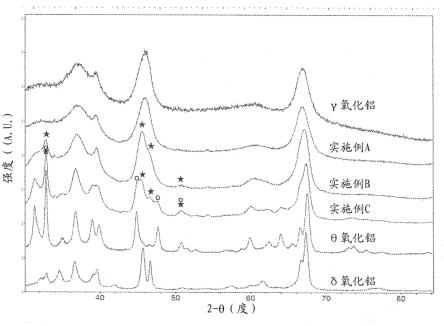
具有最小化芳族化合物产量的脱氢催化剂
1.优先权声明
2.本技术要求2020年3月13日提交的美国申请16/818,061的优先权,该申请全文并入本文。
3.本发明涉及一种烃脱氢方法,其在所选操作条件下使用层状催化剂组合物以用于增加总正烯烃选择性并降低不可取的芳族化合物选择性。
4.基于铂的催化剂用于多种烃转化工艺。在许多应用中还使用促进剂和改性剂。一种此类烃转化工艺是烃(具体地讲烷烃,诸如转化为异丁烯的异丁烷)的脱氢。例如,美国专利3,878,131(和相关美国专利3,632,503和3,755,481)公开了一种催化剂,其包含铂金属、氧化锡组分和氧化锗组分。所有组分均匀分散在整个氧化铝载体中。美国专利3,761,531(和相关美国专利3,682,838)公开了一种催化复合材料,其包含铂族组分、第iva族(iupac 14)金属组分(例如锗)、第va族(iupac 15)金属组分(例如砷、锑)以及碱金属或碱土金属组分,其全部分散在氧化铝载体材料上。同样,所有组分均匀分布在载体上。
5.美国专利6,177,381描述了一种层状催化剂组合物和用于制备该催化剂的方法。美国专利6,177,381的实施例7描述了使用烃进料测试催化剂a、b、e和f的脱氢活性。注入基于烃重量计2000ppm的水浓度。催化剂a、b、e和f的失活速率分别为0.052℉/hr、0.032℉/hr、0.050℉/hr和0.033℉/hr。
6.美国专利6,756,515描述了使用层状催化剂组合物的脱氢方法,该层状催化剂组合物包含内核(诸如α-氧化铝)以及与内核结合的由外部难熔无机氧化物(诸如γ-氧化铝)构成的外层。外层具有均匀分散于其上的铂族金属(诸如铂)以及促进剂金属(诸如锡)。组合物是有效的催化剂,但是期望开发改善总正烯烃的收率并降低需要去除的不可取芳族化合物的催化剂和方法。
技术实现要素:
7.本发明涉及一种催化剂复合材料,其具有层状组合物,该层状组合物包含内核、粘结到内核的外层,该外层包含一种或多种过渡型氧化铝,该过渡型氧化铝具有介于32.0
°
2θ和70.0
°
2θ之间的至少两个衍射角峰,其中该范围内的第一衍射角峰在32.7
±
0.4
°
2θ处,第二衍射角峰在50.8
±
0.4
°
2θ处,并且该外层具有小于100微米的厚度且具有均匀分散于其上的至少一种铂族金属和至少一种促进剂金属,并且该至少一种铂族金属的浓度为基于元素计每平方米外层的表面积0.00006克至0.0005克的铂族金属,所述层状组合物还具有分散于其上的至少一种改性剂金属,该内核难熔无机氧化物和外部难熔无机氧化物为不同的材料。
8.在一个广泛的实施方案中,本发明是一种烃脱氢方法,其包括使烃料流与层状组合物在脱氢条件下接触以得到脱氢产物,该层状组合物包含内核、与内核结合的外层,该外层包含一种或多种过渡型氧化铝,该过渡型氧化铝具有介于32.0
°
2θ和70.0
°
2θ之间的至少两个衍射角峰,其中该范围内的第一衍射角峰在32.7
±
0.4
°
2θ处,第二衍射角峰在50.8
±
0.4
°
2θ处,并且该外层具有小于100微米的厚度且具有均匀分散于其上的铂催化剂和至少
一种促进剂金属,并且铂催化剂的浓度为基于元素计每平方米外层的表面积0.00006克至0.0005克的铂族金属,层状组合物还具有分散于其上的至少一种改性剂金属,该内核难熔无机氧化物和该外部难熔无机氧化物为不同的材料,层状组合物还具有基于元素计每立方厘米所述层状组合物0.0010克至0.0060克铂族金属的至少一种铂族金属的载量。
附图说明
9.附图示出在实施例1至3中制备的材料和两种不同形式的氧化铝的x射线衍射。
具体实施方式
10.本发明涉及一种使用层状催化剂组合物的脱氢方法。该层状催化剂组合物包含内核,该内核由相对于外层具有显著更低吸附能力的材料构成。一些内核材料也基本上不被液体渗透,例如,金属,其包括但不限于铝、钛和锆。内核材料的示例包括但不限于难熔无机氧化物、碳化硅和金属。难熔无机氧化物的示例包括但不限于α氧化铝、θ氧化铝、堇青石、氧化锆、二氧化钛以及它们的混合物。优选的无机氧化物为α氧化铝。
11.形成内核的这些材料可形成为各种形状,诸如丸粒、挤出物、球体或不规则形状的颗粒,但是不是所有材料都可形成为每种形状。内核的制备可通过本领域已知的方法进行,诸如油滴、压力模塑、金属成型、造粒、制粒、挤出、轧制方法和球形造粒。球形内核是优选的。内核(无论是球形的还是不是球形的)具有0.05mm至5mm,并且优选地0.8mm至3mm的有效直径。对于非球形内核而言,有效直径被定义为成形制品在其被模塑成球体时的直径。一旦制备内核,就将其在400℃至1500℃的温度下煅烧。
12.内核现在涂覆有难熔无机氧化物层,该难熔无机氧化物与可用作内核的无机氧化物不同并且将被称为外部难熔无机氧化物。这种外部难熔氧化物是具有良好孔隙率的,具有至少50m2/g,并且优选地至少150m2/g的表面积,0.2g/ml至1.0g/ml的表观堆积密度的物质,并且选自:γ氧化铝、δ氧化铝、η氧化铝、θ氧化铝、二氧化硅/氧化铝、沸石、非沸石分子筛(nzms)、二氧化钛、氧化锆以及它们的混合物。应当指出的是,二氧化硅/氧化铝不是二氧化硅和氧化铝的物理混合物,而是意指已经共胶化或共沉淀的酸性和无定形材料。该术语在本领域中是众所周知的,参见例如美国专利3,909,450;3,274,124;和4,988,659,所述专利文献全部以引用方式并入。沸石的示例包括但不限于沸石y、沸石x、沸石l、沸石β、镁碱沸石、mfi、丝光沸石和毛沸石。非沸石分子筛(nzms)是含有除铝和硅之外的元素的那些分子筛,并且包括美国专利4,440,871中描述的硅铝磷酸盐(sapo)、美国专利4,793,984中描述的elapo、美国专利4,567,029中描述的meapo。
13.通过形成外部难熔氧化物的浆料,然后通过本领域众所周知的方式用该浆料涂覆内核来施加层。无机氧化物的浆料可通过本领域众所周知的方式制备,这通常涉及使用胶溶剂。例如,过渡型氧化铝中的任一者可与水和酸(诸如硝酸、盐酸或硫酸)混合以得到浆料。另选地,铝溶胶可通过例如将铝金属溶于盐酸中并且然后将铝溶胶与氧化铝粉末混合来制备。
14.还需要浆料含有有助于层材料粘附到内核的有机粘结剂。这种有机粘结剂的示例包括但不限于聚乙烯醇(pva)、羟丙基纤维素、甲基纤维素和羧甲基纤维素。添加到浆料中的有机粘结剂的量将从浆料的0.1重量%至3重量%显著变化。可通过在磨损测试期间损失
的层材料的量,即磨损损失来测量外层与内核结合的强度。通过搅拌催化剂、收集细粒并计算磨损损失来测量由于磨损导致的第二难熔氧化物的损失。已经发现,通过使用如上所述的有机粘结剂,磨损损失小于外层的10重量%。最后,外层的厚度在5微米至150微米之间变化。一微米等于10-6
米。
15.取决于外部难熔无机氧化物的粒度,可能需要研磨浆料以便减小粒度并且同时得到较窄的粒度分布。这可通过本领域已知的方式(诸如球磨)并持续30分钟至5小时,且优选地1.5小时至3小时的时间来完成。已经发现,使用具有窄粒度分布的浆料改进外层与内核的结合。
16.不希望受任何特定理论束缚,似乎粘结剂如pva有助于在外层材料与内核之间形成互锁键。这种情况是通过pva降低核的表面张力还是通过一些其他机制发生尚不清楚。清楚的是,观察到由于磨损导致的外层损失显著减少。
17.浆料还可含有选自氧化铝粘结剂、二氧化硅粘结剂或它们的混合物的无机粘结剂。二氧化硅粘结剂的示例包括二氧化硅溶胶和硅胶,而氧化铝粘结剂的示例包括氧化铝溶胶、勃姆石和硝酸铝。无机粘结剂在成品组合物中转化为氧化铝或二氧化硅。按氧化物并基于浆料的重量计,无机粘结剂的量在2重量%至15重量%之间变化。
18.用浆料涂覆内核可通过诸如辊涂、浸渍、喷涂等方式来实现。一种优选的技术涉及使用内核颗粒的固定流化床并将浆料喷涂到床中以均匀地涂覆颗粒。层的厚度可显著变化,但通常为40微米至150微米。应当指出的是,最佳层厚度取决于外部难熔氧化物的选择。一旦内核涂覆有外部难熔无机氧化物层,就将所得层状载体在100℃至320℃的温度下干燥1小时至24小时的时间,并且然后在400℃至1100℃的温度下煅烧0.5小时至10小时的时间,以有效地将外层粘结到内核并且提供层状催化剂载体。当然,干燥和煅烧步骤可组合成一个步骤。
19.当内核由难熔无机氧化物(内部难熔氧化物)构成时,外部难熔无机氧化物必须与内部难熔氧化物不同。另外,需要内部难熔无机氧化物相对于外部难熔无机氧化物对催化金属前体具有显著更低的吸附能力。
20.获得层状催化剂载体后,催化金属可通过本领域已知的方式分散在层状载体上。因此,铂族金属、促进剂金属和改性剂金属可分散在外层上。铂族金属包括铂、钯、铑、铱、钌和锇。促进剂金属选自:锡、锗、铼、镓、铋、铅、铟、铈、锌以及它们的混合物,而改性剂金属选自:碱金属、碱土金属以及它们的混合物。
21.这些催化金属组分可以本领域已知的任何合适方式沉积在层状载体上。一种方法涉及用一种或多种金属的可分解化合物的溶液(优选地含水的)浸渍层状载体。所谓可分解意指在加热时金属化合物转化为金属或金属氧化物并释放副产物。该铂族金属的可分解化合物的例示为氯铂酸、氯铂酸铵、溴铂酸、二硝基二氨基铂、四硝基铂酸钠、三氯化铑、六铵基氯化铑、羰基氯化铑、六硝基铑酸钠、氯钯酸、氯化钯、硝酸钯、二氨合氢氧化钯、四氨合氯化钯、六氯铱(iv)酸、六氯铱(iii)酸、六氯铱酸铵(iii)、水合六氯铱酸铵(iv)、四氯化钌、六氯钌酸盐、氯化六氨合钌、三氯化锇和氯化锇铵。可分解的促进剂金属化合物的例示为促进剂金属的卤化物盐。优选的促进剂为锡,并且优选的可分解化合物为氯化亚锡或氯化锡。
22.在本发明的实践中可用作改性剂金属的碱金属和碱土金属包括锂、钠、钾、铯、铷、铍、镁、钙、锶和钡。优选的改性剂金属为锂、钾、钠和铯,其中锂和钠是尤其优选的。碱金属
和碱土金属的可分解化合物的示例为卤化物、硝酸盐、碳酸盐或氢氧化物化合物,例如氢氧化钾、硝酸锂。
23.可使用一种常见溶液浸渍所有三种类型的金属,或者可以按任何顺序依次浸渍所有三种类型的金属,但不一定具有相同的结果。优选的浸渍程序涉及使用带蒸汽夹套的旋转干燥器。将载体浸入容纳在干燥器中的含有期望金属化合物的浸渍溶液中,并且通过干燥器的旋转运动使载体在其中翻滚。通过将蒸汽施加于干燥器夹套,加快与翻滚载体接触的溶液的蒸发。使所得复合材料在环境温度条件下干燥,或在80℃至350℃的温度下干燥,然后在200℃至700℃的温度下煅烧1小时至4小时的时间,从而将金属化合物转化为金属或金属氧化物。应指出,对于铂族金属化合物而言,优选在400℃至700℃的温度下进行煅烧。
24.在一种制备方法中,首先将促进剂金属沉积到层状载体上并且如上所述煅烧,然后通过使用含有改性剂金属的化合物和铂族金属化合物的水溶液将改性剂金属和铂族金属同时分散到层状载体上。如上所述用溶液浸渍载体,然后在400℃至700℃的温度下煅烧1小时至4小时的时间。
25.一种另选的制备方法涉及将一种或多种金属组分添加到外部难熔氧化物,然后将其以层的形式施加到内核上。例如,可将促进剂金属的可分解盐,例如氯化锡(iv)添加到由γ氧化铝和铝溶胶构成的浆料中。此外,可将改性剂金属或铂族金属或上述两者添加到浆料中。因此,在一种方法中,在以层的形式将第二难熔氧化物沉积到内核上之前,将所有三种催化金属沉积到外部难熔氧化物上。同样,可以任何顺序将三种类型的催化金属沉积到外部难熔氧化物粉末上,但不一定具有相同的结果。
26.另一种制备方法涉及首先将促进剂金属浸渍到外部难熔氧化物上并且如上所述进行煅烧。接下来,使用含有促进剂金属的外部难熔氧化物制备浆料(如上所述),并且通过上述方式施加到内核。最后,将改性剂金属和铂族金属同时浸渍到含有促进剂金属的层状组合物上,并且如上所述煅烧以得到期望的层状催化剂。
27.作为制备层状催化剂组合物的最终步骤,在氢或其他还原气氛下还原催化剂组合物,以便确保铂族金属组分处于金属状态(零价)。还原在还原环境(优选地干燥氢气)中在100℃至650℃的温度下进行0.5小时至10小时的时间。促进剂和改性剂金属的状态可以为金属(零价)、金属氧化物或金属氧氯化物。
28.层状催化剂组合物还可含有卤素组分,其可以为氟、氯、溴、碘或它们的混合物,其中优选氯和溴。相对于整个催化剂组合物的重量,该卤素组分以0.03重量%至1.5重量%的量存在。卤素组分可通过本领域众所周知的方式施加,并且可在制备催化剂组合物期间在任何点时进行,但不一定具有相同的结果。优选在已添加所有催化组分之后在用氢气处理之前或之后添加卤素组分。
29.尽管在优选的实施方案中,所有三种金属均匀地分布在外部难熔氧化物的整个外层中并且基本上仅存在于外层中,但是改性剂金属可存在于在外层和内核两者中也在本发明的界限内。这是由于当核不是金属核时,改性剂金属可迁移到内核的事实。
30.尽管每种金属组分的浓度可显著变化,但是期望铂族金属以基于元素计催化剂整个重量的0.01重量%至5.0重量%,优选地0.05重量%至2.0重量%的浓度存在。促进剂金属以整个催化剂的0.01重量%至5.0重量%的量存在,然而改性剂金属以整个催化剂的0.01重量%至5重量%的量存在。最后,铂族金属与促进剂金属的原子比在0.05至5之间变
化。具体地讲,当促进剂金属为锡时,原子比为0.1:1至5:1,并且优选地0.5:1至3:1。当促进剂金属为锗时,该比为0.25:1至5:1,并且当促进剂金属为铼时,该比为0.05:1至2.75:1。
31.当铂族金属是铂时,该浓度为基于元素且基于外层的重量计,0.01重量%至5.0重量%的铂。对于外层中的铂族金属的给定浓度而言,存在铂族金属与促进剂金属的优选原子比。例如,当铂浓度为基于元素且基于外层的重量计介于0.5重量%和3重量%之间的铂时,优选的铂与锡的原子比介于0.5:1至1.3:1之间,其随铂浓度增加而增加。当铂族金属是铂时,该载量为基于元素计每立方厘米催化剂0.0010克至0.0060克铂。
32.另外,用于本发明方法的层状催化剂在外层中具有铂族金属的临界浓度。该浓度通常为基于元素计每平方米外层的表面积0.00006克至0.0005克的铂族金属。优选每单位表面积较高浓度的铂族载量。较高浓度可通过具有较薄的外层厚度和/或具有较低表面积的氧化铝相形成。通常,过渡型氧化铝(即δ和θ)具有比γ氧化铝更低的表面积。因此,外部δ氧化铝和/或θ氧化铝层的每平方米表面积的铂族浓度高于具有相同外层厚度的γ氧化铝上的铂族浓度。层状催化剂的外层具有较大孔径与δ氧化铝和/或θ氧化铝,这导致芳族化合物产量最小化。
33.可按照bet表面积测量方法通过氮吸附来测量氧化铝载体的表面积。使用了来自麦克默瑞提克公司(micromeritics)的氮吸附bet测量装置asap 2010,并且使用了din 66131的多点bet测量技术。可使用在0.1g至1.0g的范围内的样品量。对于表面积测量,可在来自吸附等温线的0.05至0.25的相对压力范围(p/p0)内获取5个或更多个测量点。在一个实施方案中,氧化铝外层t具有大于70m2/g或大于80m2/g或大于90m2/g的表面积。在一个示例性实施方案中,氧化铝外层具有70m2/g至170m2/g的表面积。
34.氧化铝外层可基本上包含δ氧化铝和/或θ氧化铝。所谓“基本上δ氧化铝和/或θ氧化铝”意指氧化铝外层包含大于99重量%、或大于97重量%或大于95重量%的量的δ氧化铝和/或θ氧化铝。氧化铝外层的氧化铝微晶可包含100%的δ氧化铝和/或θ氧化铝微晶。
35.可通过严格控制层状催化剂所经历的最高煅烧温度,由氧化铝前体产生结晶氧化铝的δ氧化铝和/或θ氧化铝形式。任何合适的氧化铝前体可用于制备本公开的氧化铝外层。在一个实施方案中,氧化铝前体可以是勃姆石。代替在500℃至700℃的温度下的典型γ氧化铝转化,申请人已经发现为制备δ氧化铝和/或θ氧化铝外层,应将煅烧温度严格控制为750℃至1100℃或800℃至1050℃。此类煅烧温度产生包含δ氧化铝和/或θ氧化铝微晶的氧化铝外层。另外,此类煅烧温度提供具有大于70m2/g、或大于80m2/g或大于90m2/g的表面积的δ氧化铝和/或θ氧化铝外层。在一个示例性实施方案中,氧化铝前体可在750℃至1100℃的温度下煅烧10分钟至240分钟的时间,以产生包含δ氧化铝和/或θ氧化铝的氧化铝外层。在文献中已知(氧化铝特性,《技术论文》第10期,由newsome,j w;heiser,h w;russell,a s;stumpf,h c第2次修订(alumina properties.technical paper no.10.2
nd revision by newsome,j w;heiser,h w;russell,a s;stumpf,h c)),当在较高温度下煅烧氧化铝时,氧化铝的孔径较大。因此,δ氧化铝和/或θ氧化铝外层的孔径通常大于γ氧化铝的孔径。
36.可以至少三种方式容易地确定外层中铂族金属的浓度。首先,可基于用于制备层状催化剂的成分的重量来计算浓度。其次,在先前已经制备层状催化剂并且内部难熔无机氧化物与外部难熔无机氧化物不同的情况下,然后可将内层难熔无机氧化物与外部难熔无机氧化物分离,并且铂族金属可通过已知的化学和/或机械方法单独回收。然后,可以根据
回收的铂族金属的重量和回收的内部难熔无机氧化物的重量来确定铂族金属的重量浓度。最后,也可以对层状催化剂样品使用采用扫描电子显微镜的能量色散x-射线光谱或波长色散谱(epma)。
37.获得层状催化剂后,可将其用于烃脱氢工艺中。在保持于脱氢条件下的脱氢区中,使可脱氢烃与本发明催化剂进行接触。该接触可在固定催化剂床系统、移动催化剂床系统、流化床系统等中或者以间歇式操作来实现。固定床系统是优选的。在该固定床系统中,将烃进料流预热至期望的反应温度,并且然后流到含有固定催化剂床的脱氢区。脱氢区本身可包括一个或多个分开的反应区,它们之间具有加热装置,以确保可以在每个反应区的入口处保持期望的反应温度。可使烃以向上、向下或径向流动流方式与催化剂床接触。烃通过催化剂床径向流动是优选的。当烃与催化剂接触时,烃可以是液相、混合气-液相或气相。优选地,其呈气相形式。
38.可脱氢的烃包括具有2个至30个或更多个碳原子的烃,包括正链烷烃、异链烷烃、烷基芳族化合物、环烷烃和烯烃。优选的一组烃是具有2个至30个碳原子的正链烷烃的组。特别优选的正链烷烃是具有9个至16个碳原子的正链烷烃。其他特别优选的链烷烃为具有9个至16个碳原子的一甲基链烷烃和二甲基链烷烃。前述烃中的每一者可单独存在或以与任何其他前述烃中的一种或多种的混合物形式存在。
39.脱氢条件包括400℃至900℃的温度、1kpa至1013kpa的压力以及0.1hr-1
至100hr-1
的液时空速(lhsv)。如本文所用,缩写“lhsv”意指液时空速,其被定义为每小时液体的体积流速除以催化剂体积,其中液体体积和催化剂体积采用相同的体积单位。通常,对于链烷烃而言,分子量越小,则实现相当的转化率所需的温度越高。将脱氢区中的压力保持在可行的尽可能低的水平,与设备限制一致,以使化学平衡优势最大化。
40.来自脱氢区的流出物料流通常将含有未转化的可脱氢烃、氢气以及脱氢反应的产物。这些产物包括期望的烯烃和不可取的轻馏分、芳族化合物等。通常将这种流出物流冷却并传递到氢气分离区,以将富氢气气相与富烃液相分离。通常,通过合适的选择性吸附剂、选择性溶剂、一种或多种选择性反应或者通过合适的分馏方案进一步分离富烃液相。回收未转化的可脱氢烃,并且可将其再循环到脱氢区。脱氢反应的产物作为最终产物或作为制备其他化合物的中间产物回收。必须使脱氢区中的芳族化合物形成(或收率)最小化,使得芳族化合物浓度不在再循环流中积聚并且不增加用于将其去除的选择性吸附剂和溶剂的大小(和成本)。
41.本发明的新型层状催化剂提供了脱氢区中的较少的芳族化合物的形成。每平方米外层表面积的铂族浓度为0.00006至0.0005与外层中包含δ氧化铝和/或θ氧化铝的组合物的组合导致形成更少的芳族化合物。虽然催化剂活性仍然通过us6,756,515中所述的每立方厘米催化剂或千克外层具有显著的活性金属铂载量来保持,但是通过平均孔径大于γ氧化铝层中的平均孔径的δ氧化铝和/或θ氧化铝外层,可使得对芳族化合物形成的选择性较低。芳族产物通过期望烯烃的连续脱氢形成。δ氧化铝和/或θ氧化铝中的较大氧化铝孔使得烯烃更快扩散,并且因此不经历不可取的脱氢成为芳族化合物。
42.可在使可脱氢烃流到脱氢区之前、同时或之后将其与稀释剂材料混合。稀释剂材料可以是氢气、蒸汽、甲烷、乙烷、二氧化碳、氮气、氩气等或它们的混合物。氢气是优选的稀释剂。通常,当利用氢气作为稀释剂时,其用量应足以确保氢气与烃的摩尔比为0.1:1至40:
1,当摩尔比范围为1:1至10:1时可获得最佳结果。传递到脱氢区的稀释剂氢气料流通常将是在氢分离区中与来自脱氢区的流出物分离的再循环氢气。
43.例如,可将水或在脱氢条件下分解以形成水的材料(诸如醇、醛、醚或酮)连续或间歇地添加到脱氢区中,其量为以基于当量水计算提供小于10000重量ppm,优选地小于5000重量ppm,更优选地小于3000重量ppm,并且可能甚至小于1000重量ppm的烃进料流。本发明的方法可在没有水或分解以形成水的材料被添加到脱氢区中的情况下操作。
44.以下实施例是在本发明的例证中提供的,并且不旨在对如所附权利要求中示出的本发明的一般广泛范围进行不当限制。
45.实施例1
46.氧化铝球体通过众所周知的油滴方法制备,该方法描述于美国专利2,620,314中。该方法涉及通过将铝溶解于盐酸中来形成铝水溶胶。将六亚甲基四胺添加到溶胶中以在将液滴分散到维持在93℃的油浴中时将溶胶凝胶化成球体。将液滴保留在油浴中,直到它们凝固并形成水凝胶球体。在将球体从热油中去除后,将它们在135℃下加压老化,并且用稀氢氧化铵溶液洗涤,在110℃下干燥,并在650℃下煅烧2小时以得到γ氧化铝球体。然后将煅烧的氧化铝压碎成粒度小于200微米的细粉。
47.接下来,通过将假勃姆石和去离子水混合并搅拌以均匀地分配锡组分来制备浆料。向该混合物中添加上述制备的氧化铝粉末和50%氯化锡(iv)水溶液,并且将浆料球磨240分钟,从而将最大粒度减小至小于50微米。通过使用制粒和涂覆设备将这种浆料喷涂到平均直径为1.6mm的堇青石核上,得到25微米的外层。在过程结束时,留下一些未涂覆核的浆料。该层状球形载体在900℃下煅烧,以便将外层中的假勃姆石和γ氧化铝转化为δ氧化铝,并将氯化锡转化为氧化锡。
48.通过使载体与含有氯化锂和氯铂酸的水溶液(1:1溶液:载体体积比)接触(基于载体重量计),使用旋转浸渍器用锂和铂浸渍煅烧的层状载体。使用旋转浸渍器加热浸渍的复合材料直到没有溶液残留,在315℃下干燥,并且在540℃下煅烧,并在500℃下在氢气中还原。相对于整个催化剂,在该实施例中制备的所得催化剂含有0.1重量%至0.2重量%铂、0.1重量%至0.2重量%锡和0.1重量%至0.2重量%锂。这些催化剂被识别为催化剂a、b、c和d。催化剂a、b、c和d的特性总结在表1中。
49.表1
50.51.实施例2
52.在实验室规模装置中测试来自实施例1的催化剂a、b、c和d的脱氢活性。在1.27cm反应器中,放置5cc催化剂,并且在138kpa(或20psig)的压力、4:1的烃摩尔比,以及28hr-1
的液时空速(lhsv)下,使由8.8重量%至9.3重量%n-c
10
、40.0重量%至41.8重量%n-c
11
、38.6重量%n-c
12
、8.6重量%至10.8重量%n-c
13
、0.3重量%至0.8重量%n-c
14
以及1重量%至1.4重量%的非正构体构成的烃进料流过催化剂。通过调节反应器温度,将产物中的总正烯烃浓度(tno%)维持在10重量%。
53.将氢气和烃进料在反应器的上游合并以形成合并的进料,并且使合并的进料在进入反应器之前蒸发。在该示例中,以基于合并进料中烃的重量剂,2000重量-ppm的水浓度测试催化剂。表2中呈现了四种列出的催化剂在48小时时对于料流所收集的产物液体的结果。
54.通过在高效液相色谱(hplc)系统上利用反冲洗来分析进料和产物料流的芳族化合物含量,该高效液相色谱(hplc)系统使用正己烷溶剂作为流动相和折射率检测器。
55.正链烷烃转化率%=(进料中的正链烷烃-产物中的正链烷烃)
×
100%/进料中的正链烷烃。芳族化合物选择性%=(产物中的芳族化合物-进料中的芳族化合物)
×
100%/正链烷烃转化率。
56.即使催化剂b示出比催化剂a更低的芳族化合物选择性,但其芳族化合物选择性仍然高于来自催化剂c和d的那些芳族化合物选择性。因此,一种或多种过渡型氧化铝相(δ氧化铝和/或θ氧化铝)以层的形式和高pt密度(氧化铝层中的pt克数/层表面积(g/m2))组合实现最少的芳族化合物形成。
57.表2
58.样品id芳族化合物选择性(%)催化剂a2.18催化剂b1.80催化剂c1.60催化剂d1.62
59.实施例3
60.通过如图中所示的x射线分析确定本公开的四种催化剂a、b、c和d的氧化铝层的结构或δ氧化铝的存在。尝试仅通过将1cc的经煅烧碱放入不具有研磨介质的小研磨容器中去除外层材料。取决于由外层产生粉末的速度,将样品研磨并持续不同的时间量。来自四种催化复合材料的粉末被标记为样品a、b、c和d。
61.样品a、b、c和d的x-射线图案使用标准x-射线粉末衍射技术获得。辐照源是高强度的x-射线管,其在40kv和44ma下操作。来自铜k-α辐照的衍射图通过合适的基于计算机的技术获得。在8
°
2θ至90
°
2θ下连续扫描平坦的压缩粉末样品。由表示为2θ的衍射峰的位置获得晶面间距(d),其单位为埃,其中2θ是如由数字化数据所观察到的布拉格角。如本领域技术人员将理解的,衍射角(2θ)的确定经历人为误差和机械误差两者,误差的组合可赋予每个报告的2θ值
±
0.4
°
2θ的不确定度。
62.具体的实施方案
63.虽然结合具体的实施方案描述了以下内容,但应当理解,该描述旨在说明而不是限制前述描述和所附权利要求书的范围。
64.本发明提供了一种催化剂复合材料,其具有层状组合物,该层状组合物包含内核、与内核结合的外层,该外层包含一种或多种过渡型氧化铝,该过渡型氧化铝具有介于32.0
°
2θ和70.0
°
2θ之间的至少两个衍射角峰,其中该范围内的第一衍射角峰在32.7
±
0.4
°
2θ处,第二衍射角峰在50.8
±
0.4
°
2θ处,并且该外层具有小于100微米的厚度且具有均匀分散于其上的至少一种铂族金属和至少一种促进剂金属,并且该至少一种铂族金属的浓度为基于元素计每平方米外层的表面积0.00006克至0.0005克的铂族金属,层状组合物还具有分散于其上的至少一种改性剂金属,内核难熔无机氧化物和外部难熔无机氧化物为不同的材料。本发明的一个实施方案是本段中的先前实施方案至本段中的第一实施方案中的一者、任一者或所有实施方案,其中x-射线衍射图具有介于43
±
0.4
°
2θ至49
±
0.4
°
2θ之间的至少2个峰和/或肩部。本发明的一个实施方案是本段中的先前实施方案至本段中的第一实施方案中的一者、任一者或所有实施方案,其中外层具有介于5微米至65微米之间的厚度。根据权利要求1所述的催化剂复合材料,其中所述外层具有介于5微米至39微米之间的厚度。本发明的一个实施方案是本段中的先前实施方案至本段中的第一实施方案中的一者、任一者或所有实施方案,其中外层中的氧化铝具有70m2/g至170m2/g的表面积。根据权利要求1所述的催化剂复合材料,其中所述外层中的所述氧化铝具有80m2/g至130m2/g的表面积。本发明的一个实施方案是本段中的先前实施方案至本段中的第一实施方案中的一者、任一者或所有实施方案,其中外层中的氧化铝具有90m2/g至110m2/g的表面积。本发明的一个实施方案是本段中的先前实施方案至本段中的第一实施方案中的一者、任一者或所有实施方案,其中内核选自:α氧化铝、金属、θ氧化铝、碳化硅、堇青石、氧化锆、二氧化钛以及它们的混合物。本发明的一个实施方案是本段中的先前实施方案至本段中的第一实施方案中的一者、任一者或所有实施方案,其中铂族金属选自:铂、钯、铑、铱、钌、锇以及它们的混合物。本发明的一个实施方案是本段中的先前实施方案至本段中的第一实施方案中的一者、任一者或所有实施方案,其中促进剂金属选自:锡、锗、铼、镓、铋、铅、铟、铈、锌以及它们的混合物。本发明的一个实施方案是本段中的先前实施方案至本段中的第一实施方案中的一者、任一者或所有实施方案,其中促进剂金属选自:碱金属、碱土金属以及它们的混合物。本发明的一个实施方案是本段中的先前实施方案至本段中的第一实施方案中的一者、任一者或所有实施方案,其中铂族金属是铂。本发明的一个实施方案是本段中的先前实施方案至本段中的第一实施方案中的一者、任一者或所有实施方案,其中促进剂金属是锡。本发明的一个实施方案是本段中的先前实施方案至本段中的第一实施方案中的一者、任一者或所有实施方案,还包含0.01重量%至1.0重量%的铂族金属、0.01重量%至1.0重量%的促进剂金属和0.01重量%至1.0重量%的改性剂金属。
65.在本发明的另一个实施方案中,提供了一种烃脱氢方法,其包括使烃料流与层状组合物在脱氢条件下接触以得到脱氢产物,层状组合物包含内核、与内核结合的外层,该外层包含一种或多种过渡型氧化铝,该过渡型氧化铝具有介于32.0
°
2θ和70.0
°
2θ之间的至少两个衍射角峰,其中该范围内的第一衍射角峰在32.7
±
0.4
°
2θ处,第二衍射角峰在50.8
±
0.4
°
2θ处,并且该外层具有小于100微米的厚度且具有均匀分散于其上的铂催化剂和至少一种促进剂金属,并且铂催化剂的浓度为基于元素计每平方米外层的表面积0.00006克至0.0005克的铂族金属,该层状组合物还具有分散于其上的至少一种改性剂金属,内核难熔无机氧化物和外部难熔无机氧化物为不同的材料,层状组合物还具有基于元素计每立方厘
米层状组合物0.0010克至0.0060克铂族金属的至少一种铂族金属的载量。本发明的一个实施方案是本段中的先前实施方案至本段中的第一实施方案中的一者、任一者或所有实施方案,其中脱氢条件包括400℃至900℃的温度和1kpa至1013kpa的压力。本发明的一个实施方案是本段中的先前实施方案至本段中的第一实施方案中的一者、任一者或所有实施方案,其中烃料流包含至少一种选自正链烷烃、异链烷烃、烷基芳族化合物、环烷烃和烯烃的c2-c30烃。本发明的一个实施方案是本段中的先前实施方案至本段中的第一实施方案中的一者、任一者或所有实施方案,其中烃料流包含一甲基链烷烃或二甲基链烷烃。本发明的一个实施方案是本段中的先前实施方案至本段中的第一实施方案中的一者、任一者或所有实施方案,其中烃料流包含具有2个至16个碳原子的正链烷烃。本发明的一个实施方案是本段中的先前实施方案至本段中的第一实施方案中的一者、任一者或所有实施方案,其中烃料流包含选自正链烷烃、一甲基链烷烃和二甲基链烷烃的c9-c16烃。
66.尽管没有进一步的详细说明,但据信,本领域的技术人员通过使用前面的描述可最大程度利用本发明并且可容易地确定本发明的基本特征而不脱离本发明的实质和范围以作出本发明的各种变化和修改,并且使其适合各种使用和状况。因此,前述优选的具体的实施方案应理解为仅例示性的,而不以无论任何方式限制本公开的其余部分,并且旨在涵盖包括在所附权利要求书的范围内的各种修改和等效布置。
67.在前述内容中,所有温度均以摄氏度示出,并且所有份数和百分比均按重量计,除非另外指明。
再多了解一些
本文用于创业者技术爱好者查询,仅供学习研究,如用于商业用途,请联系技术所有人。