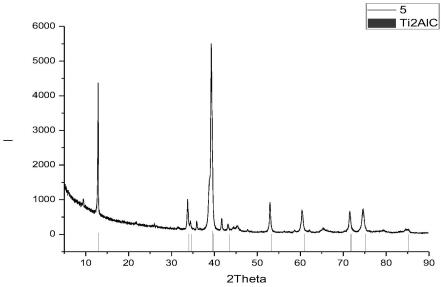
一种制备ti2alc/b4c复相陶瓷的方法
技术领域
1.本发明涉及一种制备复相陶瓷的方法,属于粉末冶金领域。
背景技术:
2.mn 1axn(m为过渡金属,a为主族元素,x为c或n,n=1-3,简称max相)相陶瓷是1967年被发现,2000年才被首次命名为max相的三元陶瓷,是一类具有金属和陶瓷双重特性的结构/功能一体化材料。ti2alc作为max相陶瓷兼有了金属和陶瓷的许多优良性能,诸如导电、导热、抗热震、可加工性以及高热稳定性和良好的抗氧化性能等,因而使其成为制备高温发动机的理想材料之一。与其他陶瓷相比,高纯度ti2alc陶瓷较难合成,往往伴随着一定量的副相产物如tic,这在某种程度上限制了其作为高温结构材料的应用。因而,因而如何制备高纯度ti2alc陶瓷粉体以及通过添加较为硬质的第二相合成复合材料来改善其性能,已成为一个新的研究热点。
3.碳化硼(b4c)具有密度低、熔点高、硬度高(仅次于金刚石和氮化硼)、模量高、强耐磨性、抗氧化性好、热稳定性好、耐酸腐蚀性好以及优良的中子吸收性能等特点,被认为是最有应用潜力的先进结构陶瓷材料之一。由于碳化硼硬度高,其对于动能弹和弹药碎片的防御能力很强,而且碳化硼质量较轻,是制备防弹衣、防护装甲的理想材料,并得到了广泛的关注。然而,由于碳化硼的脆性以及纯b4c陶瓷的烧结机制为体扩散和晶界扩散,晶界移动阻力较大,难以烧结致密,影响了其在防弹领域的应用。
4.目前提高碳化硼陶瓷的韧性除了改善烧结机制、烧结工艺方法之外,很重要的就是选择第二相材料加入到碳化硼陶瓷中,通过第二相增韧改善复合材料性能,在保证碳化硼陶瓷固有性能的前提下提高整体复合材料的韧性,这将为该类材料的具体应用提供有利条件;为解决b4c陶瓷的脆断性问题,选择引入了性能优异的高纯度ti2alc陶瓷,制备了ti2alc/b4c复相陶瓷。由于加入第二相ti2alc陶瓷,可以在较低烧结温度下进行,可以有效抑制b4c晶粒长大,同时通过ti2alc层状结构,强化ti2alc与b4c之间的界面结合,从而达到提高碳化硼复相陶瓷韧性的目的,适当的添加ti2alc第二相陶瓷在不降低碳化硼陶瓷固有性能基础上提高其韧性,有望解决一直困扰纯碳化硼陶瓷的脆性问题。
技术实现要素:
5.本发明为解决由于碳化硼的脆性以及纯b4c陶瓷的烧结机制为体扩散和晶界扩散,晶界移动阻力较大,难以烧结致密的问题,进而提出一种制备ti2alc/b4c复相陶瓷的方法。
6.本发明为解决上述问题采取的技术方案是:本发明的具体步骤为:
7.步骤一、采用自蔓延燃烧法制备陶瓷粉体;
8.步骤二、采用热压烧结工艺将制备的陶瓷粉体致密化,制备出高密度块体材料。
9.进一步的,步骤一中自蔓延燃烧法制备陶瓷粉体的步骤如下:
10.步骤a、将ti粉、铝粉、石墨粉放入混料罐中,用无水乙醇进行湿混,无水乙醇的体
积不大于混料罐容积的三分之二,ti粉、铝粉、石墨粉的体积不大于混料罐容积的二分之一,用碳化硼混料球,其料球质量比为1:3,混合时间为8~20小时,转速为40~80转/min,得到的混合粉末放置于真空烘箱中在50℃下烘干,筛分后待用;
11.步骤b、将混合好的粉末从真空烘箱中取出,以松装方式装入橡胶包套袋子中,装入粉体不断敦实,成型后的坯体的相对密度30%,袋子敞口密封扎实;
12.步骤c、将装有粉末的橡胶包套袋子放入真空负压罐中,对设备抽真空负压,进行冷等静压压坯,;
13.步骤d、将真空等静压后的粉末坯体从橡胶包套中取出来放入燃烧合成反应装置中,对装置进行2次抽真空充氩气后,通过引燃剂点火发生燃烧合成反应,在15~30秒燃烧反应完成,制得具有ti2alc陶瓷;
14.步骤e、将燃烧合成得到的陶瓷进行在破碎机上进行破碎,破碎成粒径大约1mm左右,再将该颗粒在进行酸洗后洗净烘干,最后再进行气流磨研磨成10~40μmti2alc粉末。
15.进一步的,步骤a中所述ti粉、铝粉、石墨的摩尔比为(2~3.0):(1.0~2.2):1;ti粉的纯度为99.9%,粒径为40μm;铝粉的纯度为99.99%,粒径为20μm;石墨粉的纯度为99.99%,粒径为40μm。
16.进一步的,步骤b中橡胶包套直径为5cm,装粉高度为15cm。
17.进一步的,步骤c中控制负压不大于-50kpa,保压时间为5~10min。
18.进一步的,步骤e中酸洗使用的洗液为盐酸加稀硝酸混合液。
19.进一步的,步骤二中采用热压烧结工艺将制备的陶瓷粉体致密化,制备出高密度块体材料的具体步骤如下:
20.步骤a、混料:称取步骤一中的制备的ti2alc粉末与b4c混合,混合后方球磨机中干混,混合后的原料进行筛分,并放入真空烘箱中烘干待用;
21.步骤b、成型:将步骤a中混合好的原料放入钢模模具中,在干粉自动成型液压机上预压成型;
22.步骤c、烧结:将成型后的原料坯体放入真空热压烧结炉中的石墨模具中,采用两阶段热压烧结工艺和两段升温保温法获得ti2alc/b4c复相陶瓷材料。
23.进一步的,步骤a中球磨机中料球比为1:5,干混时间为12~24小时,球磨机的转速为100~300转/min,真空烘箱中的温度为60℃。
24.进一步的,步骤b中钢膜模具的内直径为80mm,自动成型液压机施加的压力为3~5mpa,成型后的坯体相对密度为55%,坯体为高度50mm。
25.进一步的,步骤c中两阶段热压烧结工艺和两段升温保温法的第一阶段的升温速率为5~15℃/min,温度为400~600℃,压力为40~80mpa,保温保压时间为1.0~2.0h;第二阶段的升温速率为10~25℃/min,温度为1000~1800℃,压力为40~80mpa,保温保压时间为2.0~2.5h。
26.本发明的有益效果是:本发明优点是制粉工艺简便、快速、节能、低成本,采用真空等静压方法压制坯体有利于粉体在燃烧合成过程中燃烧波的均匀性和燃烧速度的稳定性,这种方法制备的三元陶瓷粉体纯度高达99.8%,采用特殊热压工艺制备的ti2alc/b4c复相陶瓷高致密、高纯度、高成品率,层状ti2alc陶瓷的加入提高了b4c陶瓷的韧性,使得该复相陶瓷具有优异的力学性能,作为抗打击、抗冲击材料使用具有广阔应用前景。
附图说明
27.图1是ti2alc陶瓷粉体的xrd示意图;
28.图2是ti2alc/b4c复相陶瓷的xrd示意图;
29.图3是ti2alc/b4c复相陶瓷的xrd示意图;
30.图4是ti2alc/b4c复相陶瓷sem扫描电镜照片示意图;
31.图5是ti2alc/b4c复相陶瓷sem扫描电镜照片示意图;
32.图6是本发明的能谱图。
具体实施方式
33.具体实施方式一:结合图1至图6说明本实施方式,本实施方式所述一种制备ti2alc/b4c复相陶瓷的方法是通过如下步骤实现的:
34.步骤一、采用自蔓延燃烧法制备陶瓷粉体;
35.步骤二、采用热压烧结工艺将制备的陶瓷粉体致密化,制备出高密度块体材料。
36.具体实施方式二:结合图1至图6说明本实施方式,本实施方式所述一种制备ti2alc/b4c复相陶瓷的方法的步骤一中自蔓延燃烧法制备陶瓷粉体的步骤如下:
37.步骤a、将ti粉、铝粉、石墨粉放入混料罐中,用无水乙醇进行湿混,无水乙醇的体积不大于混料罐容积的三分之二,ti粉、铝粉、石墨粉的体积不大于混料罐容积的二分之一,用碳化硼混料球,其料球质量比为1:3,混合时间为8~20小时,转速为40~80转/min,得到的混合粉末放置于真空烘箱中在50℃下烘干,筛分后待用;
38.步骤b、将混合好的粉末从真空烘箱中取出,以松装方式装入橡胶包套袋子中,装入粉体不断敦实,成型后的坯体的相对密度30%,袋子敞口密封扎实;
39.步骤c、将装有粉末的橡胶包套袋子放入真空负压罐中,对设备抽真空负压,进行冷等静压压坯,;
40.步骤d、将真空等静压后的粉末坯体从橡胶包套中取出来放入燃烧合成反应装置中,对装置进行2次抽真空充氩气后,通过引燃剂点火发生燃烧合成反应,在15~30秒燃烧反应完成,制得具有ti2alc陶瓷;
41.步骤e、将燃烧合成得到的陶瓷进行在破碎机上进行破碎,破碎成粒径大约1mm左右,再将该颗粒在进行酸洗后洗净烘干,最后再进行气流磨研磨成10~40μmti2alc粉末。
42.具体实施方式三:结合图1至图6说明本实施方式,本实施方式所述一种制备ti2alc/b4c复相陶瓷的方法的步骤a中所述ti粉、铝粉、石墨的摩尔比为(2~3.0):(1.0~2.2):1;ti粉的纯度为99.9%,粒径为40μm;铝粉的纯度为99.99%,粒径为20μm;石墨粉的纯度为99.99%,粒径为40μm。
43.具体实施方式四:结合图1至图6说明本实施方式,本实施方式所述一种制备ti2alc/b4c复相陶瓷的方法的步骤b中橡胶包套直径为5cm,装粉高度为15cm。
44.具体实施方式五:结合图1说明本实施方式,本实施方式所述一种制备ti2alc/b4c复相陶瓷的方法的步骤c中控制负压不大于-50kpa,保压时间为5~10min。
45.具体实施方式六:结合图1至图6说明本实施方式,本实施方式所述一种制备ti2alc/b4c复相陶瓷的方法的步骤e中酸洗使用的洗液为盐酸加稀硝酸混合液。
46.具体实施方式七:结合图1至图6说明本实施方式,本实施方式所述一种制备
ti2alc/b4c复相陶瓷的方法的步骤二中采用热压烧结工艺将制备的陶瓷粉体致密化,制备出高密度块体材料的具体步骤如下:
47.步骤a、混料:称取步骤一中的制备的ti2alc粉末与b4c混合,混合后方球磨机中干混,混合后的原料进行筛分,并放入真空烘箱中烘干待用;
48.步骤b、成型:将步骤a中混合好的原料放入钢模模具中,在干粉自动成型液压机上预压成型;
49.步骤c、烧结:将成型后的原料坯体放入真空热压烧结炉中的石墨模具中,采用两阶段热压烧结工艺和两段升温保温法获得ti2alc/b4c复相陶瓷材料。
50.具体实施方式八:结合图1至图6说明本实施方式,本实施方式所述一种制备ti2alc/b4c复相陶瓷的方法的步骤a中球磨机中料球比为1:5,干混时间为12~24小时,球磨机的转速为100~300转/min,真空烘箱中的温度为60℃。
51.具体实施方式九:结合图1至图6说明本实施方式,本实施方式所述一种制备ti2alc/b4c复相陶瓷的方法的步骤b中钢膜模具的内直径为80mm,自动成型液压机施加的压力为3~5mpa,成型后的坯体相对密度为55%,坯体为高度50mm。
52.具体实施方式十:结合图1至图6说明本实施方式,本实施方式所述一种制备ti2alc/b4c复相陶瓷的方法的步骤c中两阶段热压烧结工艺和两段升温保温法的第一阶段的升温速率为5~15℃/min,温度为400~600℃,压力为40~80mpa,保温保压时间为1.0~2.0h;第二阶段的升温速率为10~25℃/min,温度为1000~1800℃,压力为40~80mpa,保温保压时间为2.0~2.5h。
53.实施例
54.自蔓延燃烧法制备高纯ti2alc陶瓷粉体实施例
55.实施例1
56.步骤一、将ti粉(平均粒径≤45μm,纯度大于99.9%)、铝粉(平均粒径≤20μm,纯度大于99.99%)和石墨粉(平均粒径≤40μm,纯度为99.99%)按照摩尔比为2:1.2:1,用无水乙醇做介质进行湿混,球磨的转速为60转/min,球磨混合的时间为18h,取出后放入50℃烘箱烘干,再进行筛分备用;
57.步骤二、取一定重量的混合粉末装入直径5cm的橡胶包套袋子中,粉体敦实密封,将装有粉末的橡胶包套袋子放入真空负压罐中,控制负压为-50kpa以下,保压时间为5min,进行冷等静压压坯;
58.步骤三、将真空等静压后的坯体从橡胶包套中取出来放入燃烧合成反应装置中,对装置进行2次抽真空充氩气后,通过引燃剂点火发生燃烧合成反应,在15秒种左右燃烧反应完成,制得具有一定密实度的ti2alc陶瓷粉体;
59.步骤四、将燃烧合成得到的陶瓷进行在破碎机(颚式破碎机,型号100*60)上进行破碎,破碎成粒径大约1mm左右,再将该颗粒在进行酸洗(盐酸加稀硝酸)后洗净烘干,最后再进行气流磨研磨成10μm的粉体。
60.实施例2
61.步骤一、将ti粉(平均粒径≤45μm,纯度大于99.9%)、铝粉(平均粒径≤20μm,纯度大于99.99%)和石墨粉(平均粒径≤40μm,纯度为99.99%)按照摩尔比为2.5:2:1,用无水乙醇做介质进行湿混,球磨的转速为60转/min,球磨混合的时间为18h,取出后放入50℃烘
箱烘干,再进行筛分备用;
62.步骤二、取一定重量的混合粉末装入直径5cm的橡胶包套袋子中,粉体敦实密封,将装有粉末的橡胶包套袋子放入真空负压罐中,控制负压为-50kpa以下,保压时间为5min,进行冷等静压压坯;
63.步骤三、将真空等静压后的坯体从橡胶包套中取出来放入燃烧合成反应装置中,对装置进行2次抽真空充氩气后,通过引燃剂点火发生燃烧合成反应,在15秒种左右燃烧反应完成,制得具有一定密实度的ti2alc陶瓷粉体;
64.步骤四、将燃烧合成得到的陶瓷进行在破碎机(颚式破碎机,型号100*60)上进行破碎,破碎成粒径大约1mm左右,再将该颗粒在进行酸洗(盐酸加稀硝酸)后洗净烘干,最后再进行气流磨研磨成10μm的粉体。
65.实施例3
66.步骤一、将ti粉(平均粒径≤45μm,纯度大于99.9%)、铝粉(平均粒径≤20μm,纯度大于99.99%)和石墨粉(平均粒径≤40μm,纯度为99.99%)按照摩尔比为2:1:1,用无水乙醇做介质进行湿混,球磨的转速为60转/min,球磨混合的时间为18h,取出后放入60度烘箱烘干,再进行筛分备用;
67.步骤二、取一定重量的混合粉末装入直径5cm的橡胶包套袋子中,粉体敦实密封,将装有粉末的橡胶包套袋子放入真空负压罐中,控制负压为-50kpa以下,保压时间为5min,进行冷等静压压坯;
68.步骤三、将真空等静压后的坯体从橡胶包套中取出来放入燃烧合成反应装置中,对装置进行2次抽真空充氩气后,通过引燃剂点火发生燃烧合成反应,在15秒种左右燃烧反应完成,制得具有一定密实度的ti2alc陶瓷粉体;
69.步骤四、将燃烧合成得到的陶瓷进行在破碎机(颚式破碎机,型号100*60)上进行破碎,破碎成粒径大约1mm左右,再将该颗粒在进行酸洗(盐酸加稀硝酸)后洗净烘干,最后再进行气流磨研磨成10μm的粉体。
70.对比实施例1、2、3原料配比
71.实施例1、2、3的制备方法基本相同,不同之处仅在于,所述ti粉、铝粉和石墨粉摩尔比选择为“2:1.2:1、2.5:2:1、2:1:1”;
72.对比实施例1、2、3测试材料纯度
73.对实施例1、2、3制备的ti2alc陶瓷粉体的xrd图,如图1所示。由图1可以看出,本发明制备的ti2alc陶瓷粉体纯度均比较高,但实施例2方法制备的ti2alc粉体的纯度最高,基本无杂质,接近100%纯度,这是目前报道制备ti2alc的最高纯度。
74.热压烧结制备ti2alc/b4c复相陶瓷
75.实施例4
76.步骤一、将自蔓延燃烧法制备ti2alc陶瓷粉体(平均粒径≤10μm,纯度大于99.8%)、b4c粉(平均粒径10μm,纯度大于99.9%)按照重量比(wt%)为1:99进行配料,干式球磨,球料比为5:1,以300r/min转速球磨24h;
77.步骤二、称取混合好的ti2alc、b4c原料300g放入φ80mm的钢模模具中,在4mpa压力预压成型;
78.步骤三、将预压成型坯体放入真空热压烧结炉中,在真空条件下采用两段升温工
艺进行热压烧结,第一阶段为升温速率为10℃/min,温度为600℃,压力为50mpa,保温保压时间为1.5h;第二阶段为升温速率为15℃/min,温度为1300℃,压力为70mpa,保温保压时间为2.0h后,随炉冷却至室温,获得综合性能优异的ti2alc/b4c复相陶瓷材料。
79.实施例5
80.步骤一、将自蔓延燃烧法制备ti2alc陶瓷粉体(平均粒径≤10μm,纯度大于99.8%)、b4c粉(平均粒径≤10μm,纯度大于99.9%)按照重量比(wt%)为5:95进行配料,干式球磨,球料比为5:1,以300r/min转速球磨24h;
81.步骤二、称取混合好的ti2alc、b4c粉体原料300g放入φ80mm的钢模模具中,在4mpa压力预压成型;
82.步骤三、将预压成型坯体放入真空热压烧结炉中,在真空条件下采用两段升温工艺进行热压烧结,第一阶段为升温速率为10℃/min,温度为850℃,压力为50mpa,保温保压时间为2.0h;第二阶段为升温速率为15℃/min,温度为1800℃,压力为80mpa,保温保压时间为2.0h后,随炉冷却至室温,获得综合性能优异的ti2alc/b4c复相陶瓷材料。
83.实施例6
84.步骤一、将自蔓延燃烧法制备ti2alc陶瓷粉体(平均粒径≤10μm,纯度大于99.8%)、b4c粉体(平均粒径≤10μm,纯度大于99.9%)按照重量比(wt%)为10:90进行配料,干式球磨,球料比为5:1,以300r/min转速球磨24h;
85.步骤二、称取混合好的ti2alc、b4c粉体原料300g放入φ80mm的钢模模具中,在4mpa压力预压成型;
86.步骤三、将预压成型坯体放入真空热压烧结炉中,在真空条件下采用两段升温工艺进行热压烧结,第一阶段为升温速率为10℃/min,温度为800℃,压力为50mpa,保温保压时间为2.0h;第二阶段为升温速率为15℃/min,温度为1450℃,压力为75mpa,保温保压时间为2.0h后,随炉冷却至室温,获得综合性能优异的ti2alc/b4c复相陶瓷材料。
87.通过xrd及扫描电镜得到了本发明所有的ti2alc/b4c复相陶瓷的相组成及形貌特征,结果标明,所有制备的材料符合其本征特性要求。
88.表1 ti2alc/b4c复相陶瓷纯度及性能
[0089][0090]
以上所述,仅是本发明的较佳实施例而已,并非对本发明作任何形式上的限制,虽然本发明已以较佳实施例揭露如上,然而并非用以限定本发明,任何熟悉本专业的技术人员,在不脱离本发明技术方案范围内,当可利用上述揭示的技术内容做出些许更动或修饰为等同变化的等效实施例,但凡是未脱离本发明技术方案内容,依据本发明的技术实质,在本发明的精神和原则之内,对以上实施例所作的任何简单的修改、等同替换与改进等,均仍
属于本发明技术方案的保护范围之内。
再多了解一些
本文用于创业者技术爱好者查询,仅供学习研究,如用于商业用途,请联系技术所有人。