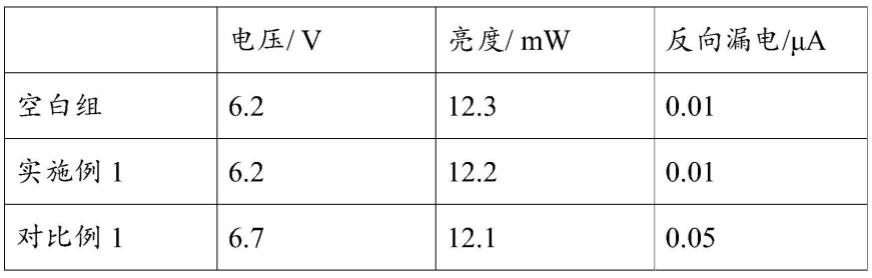
一种深紫外led芯片的返工方法
技术领域
1.本发明涉及半导体领域,特别是一种深紫外led芯片的返工方法。
背景技术:
2.目前,深紫外led在芯片生产过程中存在一定比例的外延片未能达到预期的制程要求,需要对这些不佳的外延片进行制程返工工序,但目前没有较好的制程返工手段,其原因在于,深紫外led外延片主要基于algan材料,在外延生长过程中含有大量的al,且深紫外led的p型层一般也为高al组分的algan,从而使得al容易残留在外延片的表层,对制程返工后的效果造成影响。如果使用强酸或者强碱浸泡外延片,以除去外延片表面多余的al,所需时间较长,则会对深紫外led外延片造成不可逆的损伤,从而对返工后的深紫外led外延片的发光效果造成影响。故需要提出一种新的返工方法用于解决现有返工手段的不足。
技术实现要素:
3.本发明的目的在于,提供一种深紫外led芯片的返工方法,用于解决深紫外led外延片采用制程返工方法易对外延片造成不可逆损伤的问题。
4.为解决上述技术问题,本发明提供了一种深紫外led芯片的返工方法,包括如下步骤:s1,清水冲洗待返工的深紫外led芯片后,进行一次酸浸泡处理;s2,对经过s1步骤后的深紫外led芯片进行表面刻蚀处理;s3,采用boe溶液浸泡经过s2步骤后的深紫外led芯片;s4,对经过s3步骤后的深紫外led芯片进行二次酸浸泡处理;s5,采用返工液浸泡经过s4步骤后的深紫外led芯片;s6,清水冲洗经过s4步骤后的深紫外led芯片,返回进行制程工序。
5.优选的,s1步骤和s6步骤中,采用99.99%的去离子水进行清水冲洗,且单次冲洗时间大于10min。
6.优选的,s1步骤中,采用王水进行一次酸浸泡处理,浸泡时间为2~4h。
7.优选的,s2步骤中,采用电感耦合等离子体刻蚀工艺或反应等离子体刻蚀工艺,对经过s1步骤后的深紫外led芯片表面金属和有机物进行刻蚀。
8.优选的,s2步骤中,采用等离子去胶机对经过s1步骤后的深紫外led芯片进行轰击,刻蚀时间为1~5000s。
9.优选的,s3步骤中,boe溶液为氟化铵腐蚀液,且氟化铵与溶剂的质量比为1:20,boe溶液的浸泡时间为1~5000s。
10.优选的,s4步骤中,采用ito溶液进行二次酸浸泡处理,ito溶液包括盐酸和三氯化铁,二次酸浸泡处理的时间为1~5000s。
11.优选的,ito溶液中盐酸的质量占比为5~30%,三氯化铁的质量占比为5~30%。
12.优选的,s5步骤中,返工液以质量百分数计包括如下组分:无机酸1~10%,氟化物1~10%,分散剂0.1~10%,溶剂70~80%。
13.优选的,s5步骤中,返工液浸泡时间为0.1~4h。
14.本发明的有益效果是:区别于现有技术的情况,本发明提供了一种深紫外led芯片
的返工方法,通过一次酸浸-表面刻蚀-boe溶液浸泡-二次酸浸-返工液浸泡的工艺,逐步除去待返工外延片的表层结构,同时避免对外延片造成不可逆的损伤,使经返工后的外延片发光效果接近与正常外延片的发光效果,有效避免了传统强酸或强碱浸泡时间长,易造成损伤的问题。
具体实施方式
15.下面将结合本发明实施例,对本发明实施例中的技术方案进行清楚、完整地描述,显然,所描述的实施例仅仅是本发明一部分实施例,而不是全部的实施例。基于本发明中的实施例,本领域普通技术人员在没有做出创造性劳动前提下所获得的所有其他实施例,均属于本发明保护的范围。
16.本发明所提供的深紫外led芯片的返工方法,包括如下步骤:
17.s1,清水冲洗待返工的深紫外led芯片后,进行一次酸浸泡处理。本步骤中,先采用99.99%的去离子水进行清水冲洗,可进行多次冲洗,且单次冲洗时间大于10min;然后采用王水进行一次酸浸泡处理,浸泡时间为2~4h。
18.s2,对经过s1步骤后的深紫外led芯片进行表面刻蚀处理。本步骤中,可采用电感耦合等离子体刻蚀工艺(icp)、反应等离子体刻蚀工艺(rie)等刻蚀工艺,对经过s1步骤后的深紫外led芯片表面金属和有机物进行刻蚀;例如,采用等离子去胶机对经过s1步骤后的深紫外led芯片进行轰击,刻蚀时间为1~5000s。
19.s3,采用boe溶液浸泡经过s2步骤后的深紫外led芯片。本步骤中,boe溶液为氟化铵腐蚀液,且氟化铵与溶剂的质量比为1:20,boe溶液的浸泡时间为1~5000s,采用boe溶液浸泡是为了除去深紫外led芯片的隔离层。
20.s4,对经过s3步骤后的深紫外led芯片进行二次酸浸泡处理。本步骤中,采用ito溶液进行二次酸浸泡处理,目的在于除去p型电极。其中,ito溶液包括盐酸和三氯化铁,二次酸浸泡处理的时间为1~5000s;ito溶液中盐酸的质量占比为5~30%,三氯化铁的质量占比为5~30%。
21.s5,采用返工液浸泡经过s4步骤后的深紫外led芯片。本步骤中,返工液以质量百分数计包括如下组分:无机酸1~10%,氟化物1~10%,分散剂0.1~10%,溶剂70~80%;返工液浸泡时间为0.1~4h,目的在于除去n型电极。
22.s6,清水冲洗经过s4步骤后的深紫外led芯片,返回进行制程工序。本步骤中,采用99.99%的去离子水再次进行清水冲洗,洗掉深紫外led芯片表面的残留溶液,可进行多次冲洗,且单次冲洗时间大于10min,洗净后的深紫外led芯片返回进行常规制程,从而实现对深紫外led芯片的制程返工。
23.下面通过具体实施例和对比例,对前述深紫外led芯片的返工方法的实施效果进行分析阐述。
24.实施例1
25.本实施例中深紫外led芯片的返工步骤具体如下:
26.(1)使用清水冲洗需要返工的外延片,冲洗2次,每次30min。
27.(2)使用王水对外延片进行一次酸浸泡处理,浸泡时间2h。
28.(3)使用等离子去胶机轰击经过一次酸浸泡处理后的外延片,刻蚀时间1800s。
29.(4)采用氟化铵、氢氟酸、溶剂配制boe溶液,氟化铵含量38%,氢氟酸含量2.42%,使用boe溶液浸泡经过刻蚀后的外延片,刻蚀时间1800s。
30.(5)采用盐酸、三氯化铁、溶剂配制ito溶液,盐酸含量14%,三氯化铁18%,使用ito溶液进行二次酸浸泡处理,浸泡时间1800s。
31.(6)采用溶剂、分散剂、无机酸、氟化物、水配制返工液,其中无机酸含量4%,氟化物含量4%,使用返工液对经过刻蚀后的外延片进行二次酸浸泡处理,浸泡时间4h。
32.(7)使用清水冲洗需要返工的外延片,冲洗2次,每次30分钟。返工流程结束后,重新进行正常芯片流片,重新制程后获得返工芯片样品。
33.空白组
34.将与实施例1中同批次符合制程要求的外延片样品作为空白组样品。
35.对比例1
36.基于实施例1的制备步骤,仅将(2)步骤中一次酸浸泡处理时间调整为1h,其他步骤工艺与实施例1一致。
37.对比例2
38.基于实施例1的制备步骤,仅将(2)步骤中一次酸浸泡处理时间调整为6h,其他步骤工艺与实施例1一致。
39.对比例3
40.基于实施例1的制备步骤,仅将(3)步骤出掉,在一次酸浸泡处理完成后直接进行boe溶液浸泡,其他步骤工艺与实施例1一致。
41.对比例4
42.基于实施例1的制备步骤,仅将(3)步骤中刻蚀时间调整为7200s,其他步骤工艺与实施例1一致。
43.对上述实施例1、空白组、对比例1~4中返工后的外延片样品进行测试,其结果如表1所示。对比空白组和实施例1的测试数据可知,采用实施例1返工步骤处理后的外延片性能与符合制程要求的外延片性能基本一致,则证明采用本发明的返工方法能够获得与正常外延片极其接近的发光效果。
44.将实施例1与对比例1、对比例2的测试数据进行对比。对比例1相对于实施例1的区别在于一次酸浸泡处理时间偏短,使得一次酸浸效果并不充分,存在一定残留,从而使对比例1的亮度不如实施例1,且对比例1表现出更大的反向漏电电流。对比例2相对于实施例1的区别在于一次酸浸泡处理时间过长,使其酸蚀效果过度,对外延片产生了不可逆的损伤,所以对比例2的亮度远不如对比例1和实施例1,且对比例2的反向漏电电流也大幅升高,对返工工序来说极为不利。由此可以看出,需要对一次酸浸泡处理的时间进行严格控制,才能获得配合后续步骤获得较好的处理效果。
45.将实施例1与对比例3、对比例4的测试数据进行对比。对比例3相对于实施例1的区别在于未进行表面刻蚀处理,由于表面刻蚀处理步骤的缺失,使其对深紫外led芯片表面金属和有机物难以充分去除,从而使对比例3的亮度不如实施例1。对比例4相对于实施例1的区别在于表面刻蚀处理时间过长,使其等离子体刻蚀过度,对外延片造成了不可逆的损伤,所以对比例4的亮度远低于实施例1,对返工工序来说极为不利。由此可以看出表面刻蚀处理步骤的必要性,且需要对刻蚀时间进行严格控制,才能获得配合后续步骤获得较好的处
理效果。
46.表1
[0047][0048][0049]
区别于现有技术的情况,本发明提供了一种深紫外led芯片的返工方法,通过一次酸浸-表面刻蚀-boe溶液浸泡-二次酸浸-返工液浸泡的工艺,逐步除去待返工外延片的表层结构,同时避免对外延片造成不可逆的损伤,使经返工后的外延片发光效果接近与正常外延片的发光效果,有效避免了传统强酸或强碱浸泡时间长,易造成损伤的问题。
[0050]
需要说明的是,以上各实施例均属于同一发明构思,各实施例的描述各有侧重,在个别实施例中描述未详尽之处,可参考其他实施例中的描述。
[0051]
以上所述实施例仅表达了本发明的实施方式,其描述较为具体和详细,但并不能因此而理解为对发明专利范围的限制。应当指出的是,对于本领域的普通技术人员来说,在不脱离本发明构思的前提下,还可以做出若干变形和改进,这些都属于本发明的保护范围。因此,本发明专利的保护范围应以所附权利要求为准。
再多了解一些
本文用于创业者技术爱好者查询,仅供学习研究,如用于商业用途,请联系技术所有人。