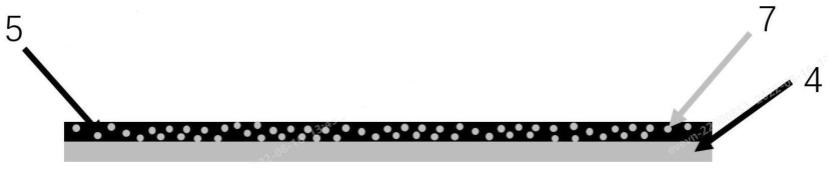
1.本发明属于锂离子电池技术领域,涉及一种锂离子电池。
背景技术:
2.锂离子电池因具有高能量密度、工作电压高和无记忆效应等优势,目前已普遍应用于日常便携式电子产品、动力电池和储能系统中。而锂离子电池会因热失控等原因,发生安全事故。目前通过采用阻燃型电解液、阻燃性隔膜、固态电解质、活性材料包覆阻燃物质以及极片涂覆安全涂层等方式,来提升锂离子电池的安全性能,但是目前需要既保证安全性能,同时不影响锂离子电池电化学性能的方法,来解决锂离子电池的安全问题。
3.安全涂层处于集流体和电化学活性物质层的中间,电解液浸润比较困难,而安全涂层中的活性材料占比较低,一些活性物质颗粒被粘结剂和导电剂包裹的较为严密。这些因素使得涂层中的活性物质中的锂离子嵌入和脱出困难,而不能嵌入和脱出的锂离子不能提供容量的同时有一定质量,并且安全涂层中的活性物质主要的成本来自于锂离子,造成锂资源的浪费。
4.cn109755465a公开了一种电极极片、电化学装置及安全涂层。该电极极片包括集流体、电极活性材料层和设置于集流体与电极活性材料层之间的安全涂层,所述安全涂层包含聚偏氟烯烃和/或聚偏氯烯烃高分子基体、导电材料和无机填料。其所述涂层中的活性物质锂离子嵌入和脱出困难,而不能嵌入和脱出的锂离子不能提供容量的同时有一定质量,并且安全涂层中的活性物质主要的成本来自于锂离子,造成锂资源的浪费。
5.cn103059613a公开了一种锂离子电池安全涂层,所述锂离子电池安全涂层使用的材料为碱金属氢氧化物、碱金属碳酸盐、碱金属碳酸氢盐中的一种或几种的混合,其公开的锂离子电池安全涂层具有受热分解吸热、晶体结构变化或者粉化和释放出水或者二氧化碳的功能,可以在电池过热的状态下降低电池温度,但是所述锂离子电池安全涂层会增加电池常温下的阻抗,导致倍率性能较差。
技术实现要素:
6.本发明的目的在于提供一种锂离子电池,本发明在正极极片中设置安全涂层,在负极极片中设置预锂化材料,安全涂层为不含锂的磷酸盐,在化成和循环过程中被负极的预锂化材料锂化,在体系配比合理的情况下,不仅能提升电池安全性,这种设计还可以降低电池的成本并提升能量密度;负极预锂化材料在对正极安全涂层中磷酸盐材料进行锂化的同时,还可以补充正负极生成sei膜和cei膜消耗的活性锂离子,提高电池能量密度。
7.为达到此发明目的,本发明采用以下技术方案:
8.第一方面,本发明提供了一种锂离子电池,所述锂离子电池包括正极极片和负极极片,所述正极极片包括正极集流体、正极活性物质层和设置于所述正极集流体和正极活性物质层之间的安全涂层,所述负极极片包括负极集流体、设置于所述负极集流体表面的负极活性物质层和预锂化材料。
9.本发明所述锂离子电池中,所述安全涂层中包括磷酸盐,负极端的预锂化材料放电过程中释放出的锂离子可以使安全涂层中能发挥容量的磷酸盐锂化为life
1-x-y
mn
xmy
po4等电化学活性物质。不能发挥容量的位点的活性物质则不会被锂化,通过体系优化使得补锂材料释放的锂离子刚好匹配可以被锂化的安全涂层活性材料,可以降低安全涂层的质量,进而降低电池的质量。由于不能发挥容量的磷酸盐不会被锂化,且负极端的预锂化材料分解率很高,而锂元素又是锂离子电池中价格最昂贵的物质。通过体系优化使得补锂材料释放的锂离子刚好匹配可以被锂化的安全涂层活性材料,可以降低新型电池结构的成本
10.优选地,所述预锂化材料设置于所述负极活性物质层内部、负极活性物质层和负极集流体之间或远离负极集流体一侧表面。
11.优选地,所述正极活性物质层、安全涂层、负极活性物质层和预锂化材料均包括粘结剂和导电剂。
12.优选地,所述粘结剂包括聚偏氟乙烯、改性聚偏氟乙烯、聚偏氯乙烯、改性聚偏氯乙烯、聚偏氟乙烯共聚物、聚偏氯乙烯共聚物、聚甲基丙烯酸甲酯或丁苯橡胶中的任意一种或至少两种的组合。
13.优选地,所述导电剂包括导电炭黑、乙炔黑、石墨、石墨烯、碳纳米管或碳纳米纤维中的任意一种或至少两种的组合。
14.优选地,所述正极活性物质层包括正极活性物质。
15.优选地,所述正极活性物质包括钴酸锂、锰酸锂、镍酸锂、镍锰酸锂、镍锰钴酸锂、镍锰铝酸锂、磷酸铁锂、磷酸钒锂、磷酸钴锂、磷酸锰锂、硅酸铁锂、硅酸钒锂、硅酸钴锂或硅酸锰锂中的任意一种或至少两种的组合。
16.优选地,所述安全涂层包括无机填料。
17.优选地,所述无机填料包括磷酸盐材料。
18.优选地,所述磷酸盐材料的化学式为fe
1-x-y
mn
xmy
po4,其中,0≤x≤1,0≤y≤0.1,0≤x y≤1,m包括sn、cr、mg、ti、al、zn、w、nb或zr中的任意一种或至少两种的组合。
19.优选地,所述负极活性物质层包括负极活性物质。
20.优选地,所述负极活性物质包括石墨类材料、硅材料、硅碳材料或钛酸锂中的任意一种或至少两种的组合。
21.优选地,所述石墨类材料包括人造石墨、天然石墨、硬碳、软碳或中间相碳微球中的任意一种或至少两种的组合。
22.优选地,所述预锂化材料包括惰性锂粉和/或锂箔。
23.需要说明的是,本技术所述预锂化材料若以混料方式加入负极活性物质层时,则不包括粘结剂和导电剂,只有作为预锂化材料层设置于负极活性物质层远离集流体一侧表面或负极活性物质层和集流体之间时,所述预锂化材料包括粘结剂和导电剂。
24.所述安全涂层的厚度为0.05~30μm,例如:1μm、2μm、5μm、10μm或20μm等,优选为1~6μm。
25.优选地,以所述安全涂层的质量为100%计,所述无机填料的质量占比为20~95%,例如:20%、25%、50%、80%或95%等,优选为60~85%。
26.优选地,所述粘结剂质量占比为5~65%,例如:5%、10%、20%、30%或65%等。
27.优选地,所述导电剂质量百分比为5~25%,例如:5%、10%、15%、20%或25%等。
28.优选地,所述无机填料的粒径为0.02~100μm,例如:0.02μm、0.1μm、0.5μm、1μm、10μm或100μm等,优选为0.1~1μm。
29.优选地,所述预锂化材料的容量c1,安全涂层中无机填料的容量c2,正极活性物质层中活性物质的容量c3,正极首效-负极首效=η,满足关系式c1=λ*c2 c3*η,其中0.5≤λ≤1,η<0时取0。
30.相对于现有技术,本发明具有以下有益效果:
31.(1)本发明在正极极片中设置安全涂层,在负极极片中设置预锂化材料,安全涂层为不含锂的磷酸盐,在化成和循环过程中被负极的预锂化材料锂化,在体系配比合理的情况下,不仅能提升电池安全性,这种设计还可以降低电池的成本并提升能量密度;负极预锂化材料在对正极安全涂层中磷酸盐材料进行锂化的同时,还可以补充正负极生成sei膜和cei膜消耗的活性锂离子,提高电池能量密度。
32.(2)本发明所述锂离子电池可以100%通过针刺和挤压测试,循环寿命可达534圈,容量可达4890mah。
附图说明
33.图1是实施例1所述锂离子电池的单面正极片侧视图,1-正极集流体,2-安全涂层,3-正极活性物质层。
34.图2是实施例1所述锂离子电池的单面负极片侧视图,4-负极集流体,5-负极活性物质层,6-预锂化材料。
35.图3是实施例2所述锂离子电池的单面负极片侧视图,4-负极集流体,5-负极活性物质层,7-以混料方式加入负极活性物质层的预锂化材料。
具体实施方式
36.下面通过具体实施方式来进一步说明本发明的技术方案。本领域技术人员应该明了,所述实施例仅仅是帮助理解本发明,不应视为对本发明的具体限制。
37.本发明实施例和对比例中,锂离子电池均通过如下方法制得:
38.1.1安全涂层制备
39.将一定配比的粘结剂材料、导电剂材料和无机填料分散于n-甲基-2-吡咯烷酮(nmp)中,搅拌均匀后涂布在正极集流体上,烘干后即得到安全涂层。
40.1.2带有安全涂层的正极片制备
41.正极极片:采用95%钴酸锂、2%pvdf、3%sp,nmp为溶剂,搅拌均匀后涂布在1.1中所述方法制备的正极集流体铝箔表面的安全涂层上,85℃烘烤后经过辊压、分条,再在85℃条件下烘烤4小时焊极耳、贴胶得到正极片。
42.1.3带有预锂化材料的负极片制备
43.惰性锂粉 石墨负极片:将惰性锂粉、活性物质石墨、导电剂、粘结剂、增稠剂按一定比例混合,(其中活性物质石墨、导电剂、粘结剂和增稠剂按质量比96.5:1.0:1.5:1.0,惰性锂粉加入量按c1=λ*c2 c3*η计算)加入nmp中混合均匀后,将所得浆料涂布在负极集流体铜箔上,87℃烘烤后经过辊压、分条,再在80℃烘烤12h后焊极耳制片得到负极片。
44.锂箔 石墨:将活性物质石墨、导电剂、粘结剂和增稠剂按质量比96.5:1.0:1.5:
1.0混合,加入去离子水中混合均匀后,将所得浆料将所得浆料涂布在负极集流体铜箔上,87℃烘烤后,经过辊压、分条,再在80℃烘烤12h后,将锂箔贴在负极膜片上(锂箔质量按c1=λ*c2 c3*η计算),在锂箔上施加一定压力并持续一段时间后,完成预锂化,最后焊极耳、贴胶得到负极片。
45.1.4锂离子电池制备
46.将隔离膜、负极片、隔离膜、正极片按顺序叠好,使隔离膜处于正极和负极片之间起到隔离作用,然后卷绕成裸电芯。之后经过入壳、注液、化成、封装工序完成锂离子电池的制备
47.实施例1
48.本实施例提供了一种锂离子电池,所述锂离子电池的参数如下:
49.所述锂离子电池包括正极极片、负极极片、隔膜和电解液,所述正极极片包括依次层叠设置的厚度为9μm的铝箔、厚度为3μm的安全涂层,其中的无机填料选择中值粒径为0.2μm的磷酸铁,所述安全涂层中磷酸铁、聚偏氟乙烯和导电炭黑的质量比为80:10:10,所述正极活性物质层中钴酸锂、聚偏氟乙烯和导电炭黑的质量比为97.6:1:1.4,正极活性物质层单面密度为180.0g/m2,a面涂膜长度为1118mm,b面长度为996mm,极片宽为76mm。所述正极极片的单面侧视图如图1所示,其中,1为正极集流体,2为安全涂层,3为正极活性物质层;
50.所述负极极片包括依次层叠设置的厚度为8μm的铜箔、单面密度为99.8g/m2的负极活性物质层和预锂化材料,a面涂膜长度1130mm,b面涂膜长度为1017mm,极片宽77.5mm,所述负极活性物质层中人造石墨、聚偏氟乙烯和导电炭黑的质量比为96:2:2,所述预锂化材料为惰性锂粉;
51.所述锂离子电池中,正极首效为97%,负极首效为92%,η=5%,λ=0.7,所述负极极片的侧视图如图2所示,其中,4为负极集流体,5为负极活性物质层,6为预锂化材料;
52.所述隔膜为9μm聚乙烯基膜双面涂胶1μm隔膜,所述电解液为1mol/l的lipf6/ec dmc emc电解液(ec为碳酸乙烯酯,emc为碳酸甲乙酯,dmc为碳酸二甲酯,ec、dmc和emc的体积比为1:1:1)。
53.实施例2
54.本实施例与实施例1区别仅在于,所述安全涂层的厚度为0.5μm,其他条件与参数与实施例1完全相同。
55.实施例3
56.本实施例与实施例1区别仅在于,所述安全涂层的厚度为10μm,其他条件与参数与实施例1完全相同。
57.实施例4
58.本实施例与实施例1区别仅在于,预锂化材料和安全涂层中无机填料的理论容量比为0.4:1(即λ=0.4),其他条件与参数与实施例1完全相同。
59.实施例5
60.本实施例与实施例1区别仅在于,预锂化材料和安全涂层中无机填料的理论容量比为1.2:1(即λ=1.2),其他条件与参数与实施例1完全相同。
61.实施例6
62.本实施例与实施例1区别仅在于,安全涂层中无机填料的粒径为0.05μm,其他条件
与参数与实施例1完全相同。
63.实施例7
64.本实施例与实施例1区别仅在于,安全涂层中无机填料的粒径为2μm,其他条件与参数与实施例1完全相同。
65.实施例8
66.本实施例与实施例1区别仅在于,负极预锂化材料为锂箔,其他条件与参数与实施例1完全相同。
67.对比例1
68.本对比例采用常规锂离子电池,即正极不加入安全涂层,负极不加入补锂剂,其他条件与参数与实施例1完全相同。
69.对比例2
70.本对比例与实施例1区别仅在于,正极极片中安全涂层的无机填料为与实施例1中磷酸铁摩尔数一致的磷酸铁锂,负极不设置预锂化材料,其中磷酸铁锂的摩尔量与实施例1中磷酸铁摩尔量相同,其他条件与参数与实施例1完全相同。
71.对比例3
72.本对比例与实施例1区别仅在于,负极不设置预锂化材料,其他条件与参数与实施例1完全相同。
73.性能测试:
74.1、针刺测试:
75.将二次电池以1c电流满充至充电截止电压,再恒压充电至电流降至0.05c,停止充电。用的耐高温钢针(针尖的圆锥角度为45
°
),以25mm/s的速度,从垂直于电池极板的方向贯穿,贯穿位置宜靠近所刺面的几何中心,钢针停留在电池中,观察电池1h内是否有燃烧、爆炸现象。
76.2、挤压测试:
77.将二次电池以1c电流满充至充电截止电压,再恒压充电至电流降至0.05c,停止充电。将电池至于两个平面内,垂直于极板方向进行挤压,两平板间施加13.0kn
±
0.78kn的挤压力。一旦压力达到最大值即可停止挤压试验,试验过程中电池不能发生外部短路。
78.3、循环性能测试
79.循环次数测试条件为:在25℃下,将二次电池进行1c/1c循环测试,充放电电压范围根据电池体系确定,容量衰减至首次放电比容量的80%时停止测试。
80.4、容量测试:
81.在25℃下,0.2c恒流充电至截止上限电压,再恒压充电值截止电流0.02c;搁置10min;0.2c恒流放电至截止下限电压,在截止电流0.02c记录放电容量即为电芯容量。
82.为了减小系统误差,每个实施例和对比例都制作50个电池进行测试,寿命和容量取平均值并取整数。
83.测试结果如表1所示:
84.表1
[0085] 针刺测试挤压测试循环寿命/圈容量/mah
实施例1100%通过100%通过5344891实施例292%ng86%ng5284905实施例3100%通过100%通过4234776实施例4100%通过100%通过5224735实施例562%ng48%ng3204884实施例6100%通过100%通过5414792实施例7100%通过100%通过4474815实施例8100%通过100%通过5464889对比例1100%ng100%ng5244885对比例2100%通过100%通过5314821对比例3100%通过100%通过5374703
[0086]
由表1可以看出,由实施例1和实施例2-3对比可得,本发明所述锂离子电池中,安全涂层的厚度会影响其性能,将安全涂层的厚度控制在1~6μm,所述锂离子电池的性能较好,若安全涂层的厚度过大,循环寿命和容量,而且会影响电池厚度,进而影响体积能量密度;若安全涂层的厚度过少,则安全涂层的功能无法发挥。
[0087]
由实施例1和实施例4-5对比可得,本发明所述锂离子电池中,预锂化材料的添加量会影响电池性能,所述预锂化材料容量c1,安全涂层中无机填料的容量c2,正极活性物质层中活性物质容量c3,正极首效-负极首效=η。c1=λ*c2 c3*η,其中λ=0.5~1时,所述锂离子电池的性能较好,若λ过大,则会导致循环寿命衰减过快并且严重影响安全测试通过率,这是由于活性锂过多导致化成和循环过程中形成锂枝晶,导致容量衰减并容易造成内短路;若λ过小,则会影响电池容量。
[0088]
由实施例1和实施例6-7对比可得,本发明所述锂离子电池中,安全涂层中无机填料的粒径会影响电池性能,若粒径过大,则在辊压过程中容易将铁锂压碎,失去电接触,影响电池性能;若粒径过小,则会导致粘结剂包裹活性材料,导致其容量无法发挥。
[0089]
由实施例1和实施例8对比可得,预锂化材料选择惰性锂粉或锂箔均可以在对正极安全涂层中磷酸盐材料进行锂化的同时,补充正负极生成sei膜和cei膜消耗的活性锂离子,提高电池能量密度。。
[0090]
由实施例1和对比例1-2对比可得,本发明在正极极片中设置安全涂层,在负极极片中设置预锂化材料,安全涂层为不含锂的磷酸盐,在化成和循环过程中被负极的预锂化材料锂化,在体系配比合理的情况下,不仅能提升电池安全性,这种设计还可以降低电池的成本并提升能量密度;负极预锂化材料在对正极安全涂层中磷酸盐材料进行锂化的同时,还可以补充正负极生成sei膜和cei膜消耗的活性锂离子,提高电池能量密度。
[0091]
由实施例1和对比例2和3对比可得,本发明中的电池体系在不加预锂化材料的情况下,能量密度明显低于有预锂化材料的体系,这是由于预锂化材料可以补充sei膜消耗的活性锂并且对磷酸铁进行锂化。
[0092]
申请人声明,以上所述仅为本发明的具体实施方式,但本发明的保护范围并不局限于此,所属技术领域的技术人员应该明了,任何属于本技术领域的技术人员在本发明揭露的技术范围内,可轻易想到的变化或替换,均落在本发明的保护范围和公开范围之内。
再多了解一些
本文用于创业者技术爱好者查询,仅供学习研究,如用于商业用途,请联系技术所有人。