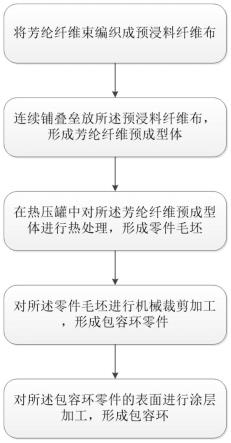
1.本技术属于发动机机匣制造技术领域,具体涉及一种发动机机匣用复合材料包容环制造方法及发动机机匣。
背景技术:
2.涡扇发动机的明显外观特点之一是具有较大的进口迎风面积。迎风面积的增加提高了发动机的进气量和发动机推力,同时也明显增加发动机吸入外来物体,打伤叶片的可能。随着涵道比的增大,转子叶片的尺寸也相应增大,大尺寸叶片在高速、高压的恶劣环境下工作时,受到飞鸟、冰块、砂石、轮胎碎片、地面杂物等外来物撞击或因为叶片材料疲劳等原因导致意外断裂脱离时,就会在巨大的离心力作用下高速撞击到机匣上,若机匣不能阻挡飞出的叶片,就会导致非包容事故,轻者飞机失去部分动力,重者金属碎片击穿飞机的机舱、油箱、液压管路和控制电路等,导致机毁人亡的事故发生。
3.目前,具备包容能力的发动机机匣通常为钛合金、铝合金、钢等单一金属材料机匣、全尺寸碳纤维复合材料机匣,以及内表面粘贴芳纶复合材料包容环或外表面缠绕芳纶纤维包容环的金属机匣。
4.钛合金、铝合金、钢等单一金属材料机匣较重;全尺寸碳纤维复合材料包容机匣较厚,制造成本较高;外表面缠绕芳纶纤维包容环的金属机匣需要在金属机匣制造完成后再缠绕芳纶纤维,生产效率较低,同时为保证整体包容性,要减少结构打孔,因而螺栓连接孔、安装外部管路和附件布局需要重新调整,影响发动机装配。
技术实现要素:
5.为了解决上述问题,本技术提供了一种发动机机匣用复合材料包容环制造方法及发动机机匣,满足发动机结构对转动叶片的包容能力,解决全尺寸单一金属包容机匣重量大、全尺寸碳纤维复合材料包容机匣厚度大、制造成本高,以及金属外壁包覆复合材料机匣生产效率较低,发动机装配复杂的问题。
6.本技术第一方面提供了一种发动机机匣用复合材料包容环制造方法,包括:
7.步骤s1、将芳纶纤维束编织成预浸料纤维布;
8.步骤s2、连续铺叠垒放所述预浸料纤维布,形成芳纶纤维预成型体;
9.步骤s3、在热压罐中对所述芳纶纤维预成型体进行热处理,形成零件毛坯;
10.步骤s4、对所述零件毛坯进行机械裁剪加工,形成包容环零件,使得所述包容环的轴向方向为所述芳纶纤维预成型体的铺层方向;
11.步骤s5、对所述包容环零件的表面进行涂层加工,形成包容环。
12.优选的是,步骤s1之前,进一步包括,通过热固性树脂浸渍所述芳纶纤维束。
13.优选的是,所述热固性树脂包括环氧树脂、双马树脂或聚酰亚胺树脂。
14.优选的是,步骤s5中,所述涂层加工包括:
15.在所述包容环零件的外表面涂敷防湿热涂层;
16.在所述包容环零件的内表面涂敷易磨耗涂层;
17.在所述包容环零件的前表面安装螺接金属防护边。
18.优选的是,在所述包容环零件的内表面涂敷易磨耗涂层之后进一步包括,对所述易磨耗涂层进行机械组合加工,使其具有符合发动机机匣内表面的型面。
19.本技术第二方面提供了一种发动机机匣,包括如上所述的发动机机匣用复合材料包容环制造方法所制造出的包容环,以及套设在所述包容环外的金属机匣。
20.优选的是,所述包容环通过胶粘剂粘接在所述金属机匣的内表面上。
21.本技术通过采用高强度、高韧性芳纶纤维增强复合材料制造包容环,可以根据包容环耐温要求更换为环氧树脂、双马树脂或聚酰亚胺树脂。由独立制造的包容环实现对叶片的包容能力。通过采用芳纶纤维材料,能够在减少铺层数量、减少制造工序、减少原材料制造成本和零件制造成本的同时,满足发动机结构对转动叶片的包容能力,解决全尺寸单一金属包容机匣重量大、全尺寸碳纤维复合材料包容机匣厚度大、制造成本高,以及金属外壁包覆复合材料机匣生产效率较低,发动机装配复杂的问题。
附图说明
22.图1是本技术发动机机匣用复合材料包容环制造方法的一优选实施的流程图。
23.图2是纤维编织结构示意图。
24.图3是风扇包容机匣结构示意图。
25.其中,1-防湿热涂层,2-易磨耗涂层。
具体实施方式
26.为使本技术实施的目的、技术方案和优点更加清楚,下面将结合本技术实施方式中的附图,对本技术实施方式中的技术方案进行更加详细的描述。在附图中,自始至终相同或类似的标号表示相同或类似的元件或具有相同或类似功能的元件。所描述的实施方式是本技术一部分实施方式,而不是全部的实施方式。下面通过参考附图描述的实施方式是示例性的,旨在用于解释本技术,而不能理解为对本技术的限制。基于本技术中的实施方式,本领域普通技术人员在没有做出创造性劳动前提下所获得的所有其他实施方式,都属于本技术保护的范围。下面结合附图对本技术的实施方式进行详细说明。
27.本技术提供了一种发动机机匣用复合材料包容环制造方法及发动机机匣,满足发动机结构对转动叶片的包容能力,解决全尺寸单一金属包容机匣重量大、全尺寸碳纤维复合材料包容机匣厚度大、制造成本高,以及金属外壁包覆复合材料机匣生产效率较低,发动机装配复杂的问题。
28.本技术第一方面提供了一种发动机机匣用复合材料包容环制造方法,如图1所示,主要包括:
29.步骤s1、将芳纶纤维束编织成预浸料纤维布;
30.步骤s2、连续铺叠垒放所述预浸料纤维布,形成芳纶纤维预成型体;
31.步骤s3、在热压罐中对所述芳纶纤维预成型体进行热处理,形成零件毛坯;
32.步骤s4、对所述零件毛坯进行机械裁剪加工,形成包容环零件,使得所述包容环的轴向方向为所述芳纶纤维预成型体的铺层方向;
33.步骤s5、对所述包容环零件的表面进行涂层加工,形成包容环。
34.在一些可选实施方式中,步骤s1之前,进一步包括,通过热固性树脂浸渍所述芳纶纤维束。
35.在该实施例中,如图2所示,包容环采用多层芳纶纤维增强热固性聚合物树脂纤维层固化成型而成,每层芳纶纤维层由高性能热固性树脂浸渍的高强度、高韧性芳纶纤维束编织成预浸料纤维布。
36.在一些可选实施方式中,所述热固性树脂包括环氧树脂。
37.本技术采用环氧树脂能够充分利用了其优良的物理机械和电绝缘性能、与各种材料的粘接性能。可以理解的是,环氧树脂是一种高分子聚合物,是指分子中含有两个以上环氧基团的一类聚合物的总称。它是环氧氯丙烷与双酚a或多元醇的缩聚产物。由于环氧基的化学活性,可用多种含有活泼氢的化合物使其开环,固化交联生成网状结构,因此它是一种良好的热固性树脂。
38.备选实施方式中,还可以采用双马树脂或聚酰亚胺树脂。
39.本技术在步骤s3中通过热压罐对所述芳纶纤维预成型体进行热处理,其主要方式为将铺放成型的复合材料包容环预成型体放置在热压罐内,然后在一定真空度下保持一定的高温高压条件对其进行固化成型,形成零件毛坯。
40.在一些可选实施方式中,步骤s5中,所述涂层加工包括:
41.在所述包容环零件的外表面涂敷防湿热涂层;
42.在所述包容环零件的内表面涂敷易磨耗涂层;
43.在所述包容环零件的前表面安装螺接金属防护边。
44.如图3所示,对所述包容环零件的外表面涂敷防湿热涂层1,外表面涂敷易磨耗涂层2,增强其耐磨、耐腐蚀性能。
45.在一些可选实施方式中,在所述包容环零件的内表面涂敷易磨耗涂层之后进一步包括,对所述易磨耗涂层进行机械组合加工,使其具有符合发动机机匣内表面的型面。
46.本技术第二方面提供了一种发动机机匣,包括如上所述的发动机机匣用复合材料包容环制造方法所制造出的包容环,以及套设在所述包容环外的金属机匣。
47.在一些可选实施方式中,所述包容环通过胶粘剂粘接在所述金属机匣的内表面上。
48.本技术在实现机匣包容的同时,比各种全尺寸单一金属包容机匣重量轻;比全尺寸全碳纤维复合材料包容机匣体积小,原材料成本低,制造成本低;比缠绕纤维的金属复合机匣制造成本低,制造工期短。
49.本技术的包容环可单独成型,也可以与金属机匣组合加工,原材料成本低,零件制造成本低、工艺性好。能够避免为安装发动机附件和外部管路,固定打孔带来的降低结构包容性的影响,同时减少结构整体装配技术难度。
50.本技术通过采用高强度、高韧性芳纶纤维增强复合材料制造包容环,可以根据包容环耐温要求更换为环氧树脂、双马树脂或聚酰亚胺树脂。由独立制造的包容环实现对叶片的包容能力。通过采用芳纶纤维材料,能够在减少铺层数量、减少制造工序、减少原材料制造成本和零件制造成本的同时,满足发动机结构对转动叶片的包容能力,解决全尺寸单一金属包容机匣重量大、全尺寸碳纤维复合材料包容机匣厚度大、制造成本高,以及金属外
壁包覆复合材料机匣生产效率较低,发动机装配复杂的问题。
51.虽然,上文中已经用一般性说明及具体实施方案对本技术作了详尽的描述,但在本技术基础上,可以对之作一些修改或改进,这对本领域技术人员而言是显而易见的。因此,在不偏离本技术精神的基础上所做的这些修改或改进,均属于本技术要求保护的范围。
再多了解一些
本文用于创业者技术爱好者查询,仅供学习研究,如用于商业用途,请联系技术所有人。