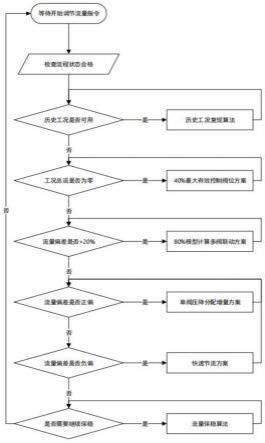
1.本发明涉及天然气管道流量计检定技术领域,尤其是涉及一种基于复合智能算法的天然气计量流量调节工艺。
背景技术:
2.天然气计量检定站工艺流程较为复杂,因设计不同阶段技术要求不同,各检定站工艺存在一定差异,国内工艺较为复杂的天然气检定站检定管路系统和稳流时间最长的检定装置及系统,其工艺系统主要包括进站出站管线、过滤分离装置、稳压装置、流量调节装置、各级计量标准装置、检定台位、氮气置换系统、esd紧急截断系统和放空排污管线等,站内各部分工艺管线相互联通,形成整体系统,检定流程涉及工艺流程切换导通、进站平压与压力调节、导通检定管路、目标流量调节、检定过程流态稳定、检定参数设置、检定过程结果及证书结果的判断与处理等繁杂的操作。
3.上述中的现有技术方案存在以下缺陷:工艺管路附加管容大,调节阀组进行流量控制过程响应时间长,小流量点全站无压差,被检表流量变化较工作级时滞影响明显等具有代表性的控制问题,检定过程流程导通、标准装置管路选择、流量调节等操作均需要人工逐步完成,尤其压力、流量调节需要检定员凭借多年的工作经验进行调节阀动作控制及精确调节。
技术实现要素:
4.本发明的目的是提供一种借助智能算法结合不同工况条件控制调节检定流量来提升检定系统可靠性、缓解检定压力、保障安全生产的基于复合智能算法的天然气计量流量调节工艺。
5.为实现上述目的,本发明提供了如下技术方案:
6.一种基于复合智能算法的天然气计量流量调节工艺,其步骤如下:
7.s1:设置需检定设备和配套设备对流量计开展检定和校准作业,具体由进岀站管线、过滤分离装置、调压阀组、流量调节阀组、背压阀组、压缩机、分析小屋、各级标准装置和检定台位组成;
8.a1:为了采集现场的检定流程与现场检定的数据,实现与现场的设备通信,首先调研站控系统中全部数据点,设计了现场数据采集与控制关键点位,形成智能检定通信关键点位表;
9.a2:根据工艺调研结果,确定4个计算边界,结合上述静态数据和实时数据采集信息,构建与现场实际设备对应的1:1水力仿真模型;
10.s2:根据水力仿真模型进行水利模拟,对于不同口径的被检表,有着不同的检定工艺流程与被检流量点,设定两端定压的边界条件进行模拟,给定现场检定的流程,通过调节模型调节阀的开度与球阀的开关,进行现场流量到达被检流量点后的工况进行水力模拟,从而获得不同口径被检流量计的检定流程、阀门开度与被检流量点水力特点;
11.s3:根据站内管道实际情况模拟工况参数并检定,利用摩阻系数灵敏度系数法得出对校正节点压力或流量较为敏感的管道,通过调整敏感管道的摩阻系数,按一定规则对管道摩阻系数进行分组校正;
12.b1:对于站内的管道,在按照天然气流量站功能块划分为进站过滤调压区、标准表区、检定台位区与流量调节阀组区之后,将各个区域等效为不同的分区模型来处理,构成整个水力模拟的简化模型;
13.b2:为使简化模型达到计算的快速性对各区域中的管道和阀进行合并处理,并对分区域处理以后各部分仪表也做出了相应的筛选,从而提高简化后模型的准确性,对现场已有的历史数据,通过关键阀门的开关状态记录下已有的标准表与检定台位的流程,并通过输气管道的基本计算公式将各个不同流程下的摩阻系数计算出来,对于往后再有此工况时,直接调用出此种工况下所对应的摩阻系数计算,并对计算出的流量实时的与现场流量进行比对,若是超过一定的值或是之前没有该流程,直接实时计算摩阻系数,并将该值储存下来,以此来提高在线仿真的准确性;
14.s4:对阀门特性进行测试,并制作相应的特征曲线,对现场的大小流量调节阀组进行实验方案的设计,通过现场阀门特性实验得出拟合计算阀门流通系数的压力、流量和阀门开度等关键参数,在此拟合得出的流通系数,用作控制算法验证;
15.s5:设计状态预测控制算法,根据天然气流量计检定站场的性质,按照各个部分的功能特性与流程组合对该天然气流量计检定站场进行分区域处理,将天然气流量计检定站场中的选择标准表区域与选择检定台位区域划分为一个区域,将调节阀区域划分为另一个区域,根据区域划分情况建立状态预测模型;
16.c1:在对流量计进行检定时,关注的物理量为流经工作级标准表与被检表的流量,通过分析现场已有的历史数据,识别不同口径标准表的检定流程,作为后续对现场数据进行仿真模拟的工况分类依据,并通过算法结合站场工艺流程,进一步提取对应流程数据并统一合并,形成不同口径被检表所涉及检定流程的记录,提取现场的一部分数据,按照阀位的组合形式,识别出结果;
17.c2:根据识别的结果,计算多种流程下对应的摩阻系数,并将每组流程的平均摩阻系数作为该流程下初始的摩阻系数值,并通过系统采集到调节阀前后的压力,流经调节阀的总流量,阀门进口的温度,压缩因子与相对密度,得到调节阀的流通系数,针对不同的被检流量点,按照不同的流量对调节阀各拟合一组流通系数,用来模拟仿真,获得模拟仿真图;
18.c3:由于管道的物理参数会随着管道的运行时间和状态发生缓慢的变化,若视为固定值或仅仅是位置的函数,则会对仿真的精度造成影响,所以引入记忆因子,以加权的方法来逐步减轻过去数据和估计的作用,并采用前一个值仿真流量值与实际流量值的比例来修正下一时刻点的仿真流量,获得最准确的状态预测模型;
19.c4:通过建立的状态预测模型,结合状态预测模型的原理出发,建立阀门控制算法的机理模型,通过调节阀前后的压力、目标流量、阀门的流通系数使用阀的公式计算调节阀大阀的开度,对其计算出来的开度进行取整,对于未能调到的流量继续使用阀的公式计算小阀的开度,依次类推,计算最小阀的开度,并对每个被检表的检定流量点进行逐个计算;
20.s6:仿真模型与控制器搭建,根据站场当前各点参数情况,寻找检定流量与调节阀
控制开度之间的关系,使用bp神经网络通过正向传播和反向传播这两个过程的交替进行,在权向量空间执行误差函数梯度下降策略,动态迭代一组权向量,使网络误差函数达到最小值,从而完成信息提取和记忆过程;
21.d1:天然气流量计检定控制器的功能是根据当前工况和目标流量,给出四个调节阀的开度,阀门组合和进站压力作为工况判断参数与检定流量(目标流量)作为bp神经网络的输入,而四个阀的开度作为输出,构建控制神经网络模型,并使用控制器进行验证,控制器给出方案与实际方案基本一致;
22.s7:智能检定系统建立,控制器启动后工作在指令检定状态,在此种状态下,智能控制器监听等待检定客户端发送检定任务,当检定客户端将一个检定任务的全部信息(包含被检表信息、检定任务信息和流量点等)发送至智能控制器后,智能控制器进行流程检查,流程检查一方面进行阀位状态和初始状态的检查保证接管控制时管路组合安全合理,另一方面针对性选择不同的运行参数集,参与模型预测和水力仿真;
23.e1:阀位合格后进入历史工况复现算法,进行阀位组合生成并运用历史数据库数据进行修正,完成第一次多阀联调,在历史工况控制效果不佳或基于bp神经网络的控制器阀位方案明显失效时,使用流动预测结果进行第二次多阀联调;
24.e2:在两次多阀联调后剩余控制区间使用较为保守的单阀控制算法进行流量实时控制,快速节流控制或单阀压降分分配增量方案进行流量的降低或提升,完成流量调整后发送开始检定标志,检定客户端进行流量计检定并连续进行下一次检定。
25.进一步的,所述s1中进岀站管线、过滤分离装置、调压阀组、流量调节阀组、背压阀组、压缩机、分析小屋、各级标准装置和检定台位满足各标准装置对音速喷嘴、超声、涡轮等流量计开展检定和校准作业的工艺要求。
26.进一步的,所述a2中1:1水力仿真模型使用水力仿真软件进行建模。
27.进一步的,所述b1中分区模型的分区具体为将进站过滤调压区、标准表区和检定台位区统一成为一个分区,作用为流程的切换,对于调节阀的区域,作为另一个子分区,作用为调节通过检定台位的流量,并通过这两个分区的并联连接构成整个水力模拟的简化模型。
28.综上所述,本发明的有益技术效果为:
29.1、采用了神经网络模型进行预测,对常规工况下,站场的状态进行仿真预测,对特殊工况下,站场的状态进行仿真预测,在历史工况控制效果不佳或基于bp神经网络的控制器阀位方案明显失效时,使用40%最大有效控制阀方案进行控制,通过状态预测控制算法进作为第一次多阀联调,产生多情况预测保证准确度的效果;
30.2、采用了识别所有流程摩阻作为数据库备用,根据目标流量的检定流程选取出标准表加检定台位的摩阻,通过目标流量与该检定流程下的摩阻,使用输气管道计算公式,通过调节阀前后的压力、目标流量、阀门的流通系数使用阀的公式计算调节阀大阀的开度,对其计算出来的开度进行取整,对于旁通的流量,通过总流量减去目标流量得到旁通流量,通过阀门公式,计算大阀的开度,取整,然后用小阀来进行下一步的调节,重复上述步骤,对每个被检表的检定流量点进行逐个计算,产生逐一检测的效果;
31.3、采用了状态预测控制算法,主要使用阀门特性测试成果和水力模型计算方法,进行快速节流控制或单阀压降分分配增量方案进行流量的降低或提升,产生快速节流控制
的效果。
附图说明
32.图1为本发明大流量调节测阀示意图;
33.图2为本发明小流量调节测阀示意图;
34.图3为本发明控制系统计算逻辑示意图;
35.图4为本发明出站压力预测网络数据示意图;
36.图5为本发明干线总流预测网络数据示意图;
37.图6为本发明工作级控制逻辑示意图。
具体实施方式
38.实施例一
39.以下结合附图对本发明方法作进一步详细说明。
40.一种基于复合智能算法的天然气计量流量调节工艺,其步骤如下:
41.s1:设置需检定设备和配套设备对流量计开展检定和校准作业,具体由进岀站管线、过滤分离装置、调压阀组、流量调节阀组、背压阀组、压缩机、分析小屋、各级标准装置和检定台位组成,满足各标准装置对音速喷嘴、超声、涡轮等流量计开展检定和校准作业的工艺要求,工作级标准装置共包含246台球阀、24台调节阀以及116段高压天然气管路,分析了设备台账信息,利用静态数据建立管道仿真模型;
42.a1:为了采集现场的检定流程与现场检定的数据,实现与现场的设备通信,首先调研站控系统中全部数据点,设计了现场数据采集与控制关键点位,形成智能检定通信关键点位表;
43.a2:根据工艺调研结果,确定4个计算边界,结合上述静态数据和实时数据采集信息,构建与现场实际设备对应的1:1水力仿真模型,使用水力仿真软件进行建模;
44.s2:根据水力仿真模型进行水利模拟,对于不同口径的被检表,有着不同的检定工艺流程与被检流量点,设定两端定压的边界条件进行模拟,给定现场检定的流程,通过调节模型调节阀的开度与球阀的开关,进行现场流量到达被检流量点后的工况进行水力模拟,从而获得不同口径被检流量计的检定流程、阀门开度与被检流量点水力特点,通过水力仿真对水力工况的模拟,掌握不同口径被检流量计的检定流程、阀门开度与被检流量点水力特点,通过逐步调整水力模型中各段各部分的管道物性参数与缓变参数,使模型的仿真结果与现场最大限度一致,为智能控制器的方案制定和有效性测试提供必要的仿真环境,通过仿真模型建立,对检定站工艺水力模拟达到的要求的精度,最小相对误差约为0.41%,最大约为1.16%,满足仿真精度的要求,该机理模型可作为智能控制研究的基础及辅助智能控制实现的仿真数字模型;
45.s3:根据站内管道实际情况模拟工况参数并检定,利用摩阻系数灵敏度系数法得出对校正节点压力或流量较为敏感的管道,通过调整敏感管道的摩阻系数,按一定规则对管道摩阻系数进行分组校正,对现场已有的历史数据,通过关键阀门的开关状态记录下已有的标准表与检定台位的流程,并通过输气管道的基本计算公式将各个不同流程下的摩阻系数计算出来,对于往后再有此工况时,直接调用出此种工况下所对应的摩阻系数计算,并
对计算出的流量实时的与现场流量进行比对,若是超过一定的值或是之前没有该流程,直接实时计算摩阻系数,并将该值储存下来,以此来提高在线仿真的准确性,本部分的理论依据如下:根据质量守恒方程、动量守恒方程与能量守恒方程,建立起用来描述天然气在检定站场的管道的流动的流速、密度、温度、压力和高程等量之间的相互关系,其基本公式如下:
[0046][0047][0048][0049]
为了方便建立计算等效管道摩阻系数的模型,作以下假设:
①
筛选scada系统所采集上来的点,以在现场设备不动作的前提下,一段时间内流量变化微小的流量作为稳态点,即此时刻,天然气在检定站内管道中稳定流动,管路中流量与压力只是位置的函数,它不随时间的变化而改变;
②
由于天然气检定站场一般面积不大,且有相关的遮光棚,假设天然气在管道的流动为等温流动,因此不考虑能量方程的影响;
③
管道起伏不大为水平管道,即ds=0,在实际工作中,为了计量交接的方便,使用工程标准状况下的体积流量,考虑局部阻力,将气体状态方程p=ρzrt代入上面方程组,则方程组可简化为下式来反算该部分的摩阻系数:
[0050][0051]
式中,q为工程标准状况(压力p0=1.01325
×
105pa,温度t0=293k)下的体积流量,m3/s;pq为进口压力,pa;pz为出口压力,pa;d为管道内径,m;λ为水力摩阻系数;z为天然气管输条件(平均压力和平均温度)下的压缩因子;δ
*
为天然气的相对密度;t为输气温度,t=273 t
pj
,为输气管的平均温度,℃;l为管段的长度,m,
[0052]
在对天然气流量计检定站各个区域等效时,采用威莫斯公式与水平输气管的流量基本计算公式来推导:
[0053][0054]
例如对于两条1米的平行管线用一条新的管线代替,如果pq,pz,q,l相同,则等效为一根管道的管径为:
[0055][0056][0057]
式中,λ为水力摩阻系数,d为管道管径,m;de为等效管道管径,m,
[0058]
阀门流通系数是衡量调节阀流通能力的指标,常作为选用调节阀的口径以及研究阀门的内部结构、判断影响阀门稳定性的因素,相对于阀门内部的流动状态,管道流动仿真更加关注阀门前后流动参数的变化,通过调节阀开度的变化对站内压力与流量的控制,为了建模仿真出与能匹配现场工况的模型,阀门的流通系数是阀门工艺仿真的关键参数,对
于含有调节阀的站内流量控制管路,在进行仿真模拟时,调节阀可以作为一个局部阻力元件处理,因此对于调节阀流通系数的辨识,转化为辨识出在此处的局部摩阻,从而提高仿真的准确性,
[0059]
流通系数为衡量阀的流通能力的重要指标,按照经典计算方法,需要提供每个阀的流量、阀前后的压力、密度和温度等参数,对于并联调节阀,只有总流量,无法采用以往的方式计算现场运用时的流通系数,因此,本部分从阀的流通系数出发,运用最小二乘拟合多阀并联情况下,总流量与各个并联阀之间开度的关系,从其中辨识出各个调节阀的流通系数,然后,将辨识出的流通系数带入水力仿真软件sps,来检验辨识出的流通系数的准确性,结果表明,辨识出的流通系数,带入sps中调节阀的流通系数,进行仿真计算出的流量与现场的流量基本一致,
[0060]
(1)单阀流通系数的计算
[0061]
从阀的流通系数推导的基本原理出发,把调节阀的节流模转化为简单的节流模式,对于不可压缩流体的伯努利方程如下:
[0062][0063]
其中:v1、v2为阀门前、后流体速度,m/s;p1、p2为阀门前、后压力pa(绝对);γ1、γ2为阀门前后流体重度,n/m3;g为重力加速度,g=9.81m/s2;v为缩流速度,m/s,ε为阻力系数,
[0064]
由连续性方程可得:
[0065]
v1=v2[0066]
γ1=γ2[0067][0068]
其中:q为体积流量,m3/s,a为管道的横截面积m2,
[0069]
令得全开时的流通系数公式为:
[0070][0071]
对于气体,因为有压缩性,由于考虑的角度不同而有不同的计算公式,通过查阅sps帮助文档,当为非阻塞流时sps中气体调节阀计算的公式为:
[0072][0073]
其中:q为标准状态下的体积流量,m3/h;z为上游温度和平均压力下的压缩系数;g为天然气相对于空气的比重;t为上游的温度,k;pu进口压力,pd出口压力,pa;cf临界流量系数,取值为1;n单位转换系数,此单位下取值为0.0346,cv为全开时的流通系数,因此对于单阀流通系数的计算,当已知标况下的体积流量,压缩因子,天然气相对于空气的比重,上游的温度以及进出口的压力时,就可以通过上式计算出阀门全开时的流通系数,
[0074]
(2)多阀并联流通系数的辨识
[0075]
对于等百分比阀,不同开度下阀门的流通系数如下式计算:
[0076][0077]
对于气体的过阀流量,由以下的公式计算
[0078][0079][0080][0081][0082][0083]
其中:q为标准状态下流经并联阀门总的体积流量,m3/h;z为上游温度和平均压力下的压缩系数;g为天然气相对于空气的比重;t为上游的温度,k;p1进口压力,p2出口压力,pa;n单位转换系数,此单位下取值为0.0346,cv为全开时的流通系数
[0084]
用sps建立模型来获取公式拟合所需要的进出阀的压力、标准状态下的流量、阀门进口的温度、压缩因子与相对密度,并对于获取到的数据,按照以上公式采用最小二乘法进行拟合,从而来辨识出多个调节阀在全开时的流通系数,并将拟合求得的流通系数给到sps中调节阀的物性参数进行计算
[0085]
从sps中提取出的数据用公式直接拟合阀的流通系数,所计算出的流量与sps计算出的基本一致,拟合的流通系数与实际设置的流通系数误差在1%左右,满足模拟的要求;
[0086]
管道运行过程中摩阻系数的影响因素相当复杂,往往会受到管壁物理特性、流体性质及流态变化的影响,考虑到进行模型简化的时候忽略了部分管道,在不同的流量下,经过管道的摩阻不同,因此对于不同的流量大小,整个仿真模型的摩阻也不相同,为了使模拟得更加准确,将不同流量下的变化反应在阀门上面,通过对不同流量下,现场数据的拟合,正演得到不同流量下,阀门全开时的流通系数,并将拟合得到的阀门流通系数输入到sps的调节阀参数中,进行以流量作为输出的模拟仿真,在对流量进行分段拟合后,针对现场数据的拟合程度大大增加,仿真所得出的稳态点的数据在绝大部分点已和现场一致,因此,这种方法取代传统一组参数到底的做法,可以极大提高仿真精度,对控制方案的验证可以达到较为理想的效果,通过现场scada系统所采集上来的实际运行数据,将从现场所采集上来的阀前后的压力、温度与三个调节阀的开度作为边界条件,输入点的间隔与现场scada系统采集数据的时间间隔保持一致,每隔0.2s输入一次数据,根据不同的流量大小更新阀门的流通系数的值,从而使得该模型仿真的适应性更广,精度更加准确;
[0087]
基于实时更新边界条件的仿真,所得出的瞬态点的数据在绝大部分点已和现场一致,对于现场出现异常工况(8100m3/h处),此处由于scada采集数据的问题导致出现异常工
况,水力仿真的结果与所采集上来的数有较大的偏差,起到了一定的监测异常数据的作用,通过调节阀的开度和流量与压力等工艺参数与调节阀的流通系数的关系,建立出了辨识并联调节阀流通系数的方式,为了实现调节阀的精确建模,需要在合并水力单元的情况下,有针对性的压缩边界条件,结合管段和阀门等水力元件的动态调整,实现现场状况实时的仿真达到一定的精度,基于最小二乘拟合辨识流动参数,sps建模使用辨识出的流通系数进行流量的仿真方法,解决了传统长输管道未曾涉及到的输气站场精细建模在线仿真的问题;
[0088]
b1:对于站内的管道,在按照天然气流量站功能块划分为进站过滤调压区、标准表区、检定台位区与流量调节阀组区之后,将各个区域等效为不同的分区模型来处理,构成整个水力模拟的简化模型,分区模型的分区具体为将进站过滤调压区、标准表区和检定台位区统一成为一个分区,作用为流程的切换,对于调节阀的区域,作为另一个子分区,作用为调节通过检定台位的流量,并通过这两个分区的并联连接构成整个水力模拟的简化模型;
[0089]
b2:为使简化模型达到计算的快速性对各区域中的管道和阀进行合并处理,并对分区域处理以后各部分仪表也做出了相应的筛选,从而提高简化后模型的准确性,对现场已有的历史数据,通过关键阀门的开关状态记录下已有的标准表与检定台位的流程,并通过输气管道的基本计算公式将各个不同流程下的摩阻系数计算出来,对于往后再有此工况时,直接调用出此种工况下所对应的摩阻系数计算,并对计算出的流量实时的与现场流量进行比对,若是超过一定的值或是之前没有该流程,直接实时计算摩阻系数,并将该值储存下来,以此来提高在线仿真的准确性;
[0090]
s4:对阀门特性进行测试,并制作相应的特征曲线,对现场的大小流量调节阀组进行实验方案的设计,通过现场阀门特性实验得出拟合计算阀门流通系数的压力、流量和阀门开度等关键参数,在此拟合得出的流通系数,用作控制算法验证,参照图1,流程准备:使用fv7242作旁通阀,使用fv7212、fv7222、fv7232作调节阀,选用核查标准fe4102,
[0091]
①
将fv7242开至100%,将fv7222开至50%,等待30s后,将fv1005开至0%,流量稳定后,记录当前时刻、核查表流量和表中压力表数据,
[0092]
②
调整fv7242开度,使流量达到400m3/h,流量稳定后,记录当前时刻、fv7242开度和表中压力表数据,
[0093]
③
保持fv7242开度不变,以十开度为间隔逐步调节fv7232开度,并在每一步调节后等待至流量稳定,(如果流量大于1500m3/h,即停止2.3中继续增大的实验点)流量稳定后,记录当前时刻、核查表流量和表中压力表数据,
[0094]
④
保持fv7242开度不变,以十开度为间隔逐步调节fv7212开度,并在每一步调节后等待至流量稳定,流量稳定后,记录当前时刻、核查表流量和表中压力表数据,
[0095]
⑤
保持fv7242开度不变,以十开度为间隔逐步调节fv7222开度,并在每一步调节后等待至流量稳定,流量稳定后,记录当前时刻、核查表流量和表中压力表数据,
[0096]
⑥
保持fv7242开度不变,以十开度为间隔逐步调节fv7212开度,并在每一步调节后等待至流量稳定,流量稳定后,记录当前时刻、核查表流量和表中压力表数据,
[0097]
⑦
保持fv7242开度不变,以十开度为间隔逐步调节fv7222开度,并在每一步调节后等待至流量稳定,流量稳定后,记录当前时刻、核查表流量和表中压力表数据,
[0098]
流程准备:将核查表切换至核查标准fe4101后进行后续测试,
[0099]
⑧
将核查表切换至核查标准fe4101后,保持fv7242开度不变,以十开度为间隔逐
步调节fv7232开度,并在每一步调节后等待至流量稳定,流量稳定后,记录当前时刻、核查表流量和表中压力表数据,
[0100]
⑨
将fv7212、fv7222全关,将fv7232、fv7242全开后,切换fv7232为旁通阀,切换fv7242为调流阀,以十开度为间隔逐步调节fv7242开度,并在每一步调节后等待至流量稳定,流量稳定后,记录当前时刻、核查表流量和表中压力表数据,
[0101]
⑩
保持fv7242全开,关闭fv7232待稳定后记录数据;
[0102]
小流量调节阀组区阀门特性测试,参照图2,使用fv7242作旁通阀,使用fv7112、fv7122、fv7132、fv7142作调节阀,选用核查标准fe3101,按照每个阀门间隔10开度的原则进行流量测试,注意过阀流量应在超声流量计量程范围内进行,pt3003、pt5901和pt7301压变均为表压表,需将压力数值增加当地大气压,根据ptdn压力表在10点00分至11点8分测量当地大气压强的平均值0.104979mpa,进行处理,管道中使用高压天然气作为实流测试介质,其组分由气相色谱分析仪实时测试,通过现场记录操作时间与数据特性,对实验过程数据进行筛选,每个测试点位取两个典型稳态工况进行计算,得到《小流量调节阀组区调节阀特性测试数据》、《大流量调节阀组区调节阀特性测试数据》,通过并联调流阀(fv7212、fv7222与fv7232)前后的压力、温度与流经并联调节阀的总流量与三个阀门的开度,拟合出阀门开度、阀前后压力、温度与流经并联阀总流量的关系,拟合出的三个条流阀阀门的流通系数;
[0103]
最小二乘参数辨识出来的fv7212、fv7222与fv7232阀门流通系数分别为:10.5754,195.2593和791.8621,对于旁通阀fv7242,针对fv7242前后的压力与流通系数,进行直接拟合,从而确定fv7242阀门的流通系数拟合cvo数值224.975612779881,通过以上拟合,得出四个调流阀(fv7112、fv7122、fv7132与fv7142)的流通系数,分别为:0.9,15.9和30.08和143.4,对现场的大小流量调节阀组进行实验方案的设计,通过现场阀门特性实验得出拟合计算阀门流通系数的压力、流量和阀门开度等关键参数,在此拟合得出的流通系数,用作控制算法验证;
[0104]
s5:设计状态预测控制算法,根据天然气流量计检定站场的性质,按照各个部分的功能特性与流程组合对该天然气流量计检定站场进行分区域处理,将天然气流量计检定站场中的选择标准表区域与选择检定台位区域划分为一个区域,将调节阀区域划分为另一个区域,根据区域划分情况建立状态预测模型,现场实际所采集上来的数据可以看出,由于检测仪表本身也存在一定的不确定度,所以如果各个点取值过近,由于仪表本身不确定度的影响,可能使计算出现反向流动的可能,或者流量波动较大,而使得模型的校准产生困难,因此,将天然气站场划分为几个区域之后,便避免了由于仪表的波动而造成的影响,从而提高了简化模型的准确性,对于现场的操作原则,经常将旁通调节阀置于一个固定的阀位来进行流量的旁通调节,在对流量计进行检定时,关注的物理量为流经工作级标准表与被检表的流量,因此对该部分通过当量管法对标准表与检定台位处的管线进行了处理,通过分析现场已有的历史数据,识别不同口径标准表的检定流程,作为后续对现场数据进行仿真模拟的工况分类依据,通过算法结合站场工艺流程,识别scada系统采集上来的关键阀开闭数据,将各种检定流程确定下来,进一步提取对应流程数据并统一合并,形成不同口径被检表所涉及检定流程的记录,提取现场的一部分数据,按照阀位的组合形式,识别出来的结果,所导入的数据中,对于标准表与检定台位的选取从而来确定检定的流程,在选取的数据
中,经统计共有19种操作流程,计算多种流程下对应的摩阻系数,对于每种流程下的摩阻系数趋于一个相对稳定值,因此将每组流程的平均摩阻系数作为该流程下初始的摩阻系数值;
[0105]
对于调节阀区域的处理,通过scada系统采集到调节阀前后的压力,流经调节阀的总流量,阀门进口的温度,压缩因子与相对密度,得到三个调节阀的流通系数,由于考虑到不同流量下,调节阀区域管道处的摩阻不同,因此针对不同的被检流量点,按照不同的流量对调节阀各拟合一组流通系数,用来模拟仿真,使得计算的结果更加准确;
[0106]
由于管道的物理参数会随着管道的运行时间和状态发生缓慢的变化,如管径、内壁粗糙度等,若视为固定值或仅仅是位置的函数,则会对仿真的精度造成影响,因此,需对所建模型的缓变参数进行修正,对缓变参数的修正来说,这是一个随时间推移不断观测、不断估计的过程,即新的、即时数据,应该比原来的、很久以前的观测和估计更重要,因此,这里引入记忆因子,考虑加权的方法来逐步减轻过去数据和估计的作用,在此基础上,对各个流程采用时间窗的形式来修正不同流程下的摩阻,对于按时间窗修正管段的摩阻系数,以记忆因子的方法来修正摩阻系数,采取三个参数迭代修正的方式进行修正,由老到新,
[0107]
为了使预测流量的准确性进一步的提高,对于仿真结果进行进一步的处理,采用前一个值仿真流量值与实际流量值的比例来修正下一时刻点的仿真流量;
[0108]
c1:在对流量计进行检定时,关注的物理量为流经工作级标准表与被检表的流量,通过分析现场已有的历史数据,识别不同口径标准表的检定流程,作为后续对现场数据进行仿真模拟的工况分类依据,并通过算法结合站场工艺流程,进一步提取对应流程数据并统一合并,形成不同口径被检表所涉及检定流程的记录,提取现场的一部分数据,按照阀位的组合形式,识别出结果;
[0109]
c2:根据识别的结果,计算多种流程下对应的摩阻系数,并将每组流程的平均摩阻系数作为该流程下初始的摩阻系数值,并通过系统采集到调节阀前后的压力,流经调节阀的总流量,阀门进口的温度,压缩因子与相对密度,得到调节阀的流通系数,针对不同的被检流量点,按照不同的流量对调节阀各拟合一组流通系数,用来模拟仿真,获得模拟仿真图;
[0110]
c3:由于管道的物理参数会随着管道的运行时间和状态发生缓慢的变化,若视为固定值或仅仅是位置的函数,则会对仿真的精度造成影响,所以引入记忆因子,以加权的方法来逐步减轻过去数据和估计的作用,并采用前一个值仿真流量值与实际流量值的比例来修正下一时刻点的仿真流量,获得最准确的状态预测模型;
[0111]
c4:通过建立的状态预测模型,结合状态预测模型的原理出发,建立阀门控制算法的机理模型,通过调节阀前后的压力、目标流量、阀门的流通系数使用阀的公式计算调节阀大阀的开度,对其计算出来的开度进行取整,对于未能调到的流量继续使用阀的公式计算小阀的开度,依次类推,计算最小阀的开度,并对每个被检表的检定流量点进行逐个计算,
[0112]
(1)调流阀流通系数的推导
[0113]
有总流量时阀门流通系数的反算q
总(过站流量)
=q
总(flow-total)
q
总(旁通流量)
[0114]
对于气体的过阀流量,由以下的公式计算
[0115]
[0116][0117][0118][0119]
对于等百分比阀,不同开度下阀门的流通系数如下式计算:
[0120][0121]
将(5.38)带入(5.39)得到下式:
[0122][0123]
其中:q为标准状态下流经并联阀门总的体积流量,m3/h;z为上游温度和平均压力下的压缩系数;g为天然气相对于空气的比重;t为上游的温度,k;p1进口压力(调节阀前压力),p2出口压力(调节阀后压力),pa;n单位转换系数,此单位下取值为0.0346,c
vo
为全开时的流通系数,x为开度,0-1制,
[0124]
通过稳态数据点拟合曲线可以将三个调流阀的流通系数确定下来,
[0125]
(2)旁通阀流通系数的推导
[0126]
对于气体的过阀流量,由以下的公式计算
[0127][0128][0129][0130]
对于等百分比阀,不同开度下阀门的流通系数如下式计算:
[0131][0132]
对于线性阀(fv1814a),不同开度下阀门的流通系数如下式计算:
[0133]
cv(x)=c
vo
×
x
[0134]
得到下式:
[0135][0136]
其中:q为标准状态下流经并联阀门总的体积流量,m3/h;z为上游温度和平均压力下的压缩系数;g为天然气相对于空气的比重;t为上游的温度,k;p1进口压力(标准表前压力),p2出口压力(调节阀后压力),pa;n单位转换系数,此单位下取值为0.0346,c
vo
为全开时
的流通系数,x为开度,0-1制,
[0137]
通过稳态数据点拟合曲线可以将两个旁通阀的流通系数确定下来,
[0138]
(3)标准表与检定台位摩阻系数的计算
[0139]
通过数据的驱动,将流程反应在摩阻上面,通过识别scada系统采集上来的关键阀的开关情况的数据,就可以将各种检定流程唯一确定下来,将各个流程下的摩阻通过以下公式计算:
[0140][0141]
式中,q为输气管在工程标准状况下的体积流量,m3/s;pq为输气管道起点压力,pa;pz为输气管计算段的终点压力,;d为输气管内径,;λ为水力摩阻系数;z为天然气在管输条件(平均压力和平均温度)下的压缩因子;δ
*
为天然气的相对密度;t为输气温度,t=273 t
pj
,为输气管的平均温度,℃;l为输气管计算段的长度,m;
[0142]
如图3所示,
①
当为小压差工况且总流量一定时,假设进出站的压力保持不变,总流量保持不变,即p1、p2与q为定值,
[0143]
②
阀门特性实验的数据拟合出,fv7212、fv7222、fv7232、fv7242与fv1005的cvo,
[0144]
③
通过旁通当前的开度,计算旁通处的流量,继而通过当前的旁通流量与调节流量之和求出总流量q,
[0145]
④
识别所有的流程的,将各个流程下,标准表加检定台位的摩阻作为数据库备用,
[0146]
⑤
根据目标流量的检定流程选取出标准表加检定台位的摩阻,通过目标流量、p1与该检定流程下的摩阻,使用输气管道计算公式,求得调节阀前的压力p3,
[0147]
⑥
根据首先开大阀的原则,通过调节阀前后的压力、目标流量、阀门的流通系数使用阀的公式计算调节阀大阀的开度,对其计算出来的开度进行取整,对于未能调到的流量继续使用阀的公式计算小阀的开度,依次类推,计算最小阀的开度,
[0148]
⑦
对于旁通的流量,通过总流量减去目标流量得到旁通流量,
[0149]
⑧
同样,先开大阀的原则,先只开大阀,通过阀门公式,计算大阀的开度,取整,然后用小阀来进行下一步的调节,
[0150]
⑨
重复
⑥
~
⑧
,对每个被检表的检定流量点进行逐个计算;
[0151]
s6:仿真模型与控制器搭建,根据站场当前各点参数情况,寻找检定流量与调节阀控制开度之间的关系,使用bp神经网络通过正向传播和反向传播这两个过程的交替进行,在权向量空间执行误差函数梯度下降策略,动态迭代一组权向量,使网络误差函数达到最小值,从而完成信息提取和记忆过程,
[0152]
bp神经网络是一种按误差逆传播算法训练的多层前馈网络,是目前应用最广泛的神经网络模型之一,其基本原理是通过样本数据的训练,不断修正网络权值和阈值使误差函数沿负梯度方向下降,逼近期望值,bp神经网络能学习大量的输入-输出模式映射关系,而无需事前揭示描述这种映射关系的数学方程;
[0153]
bp算法由数据流的正向传播和误差信号的反向传播两个过程构成,正向传播时,传播方向为输入层到隐含层再到输出层,每层神经元的状态只影响下一层神经元,设bp神经网络的输入层有n个节点,隐含层有l个节点,输出有m个节点,输入层和隐含层之间的权值wik,隐含层和输出层之间的权值为wkj,隐含层的传递函数为f1,输出层的传递函数为
f2,则隐含层节点的输出为:
[0154][0155]
输出层节点的输出为:
[0156][0157]
这样bp神经网络就完成了n维向量对m维向量的近似映射,若在输出层得不到期望的输出,则转向误差信号的反向传播流程,设有p个学习样本,记作x1,x2,
…
,xq,
…
,xp,其中将第q个样本xq代入网络后得到一组输出yq,采用平方型误差函数,于是得到第q个样本的误差eq:
[0158][0159]
式中:为期望输出,对于p个学习样本,全局误差为:
[0160][0161]
采用累计误差bp算法调整权值wkj,使全局误差e变小,即:
[0162][0163]
式中:η为学习率,定义误差信号δ
yj
为:
[0164][0165][0166][0167]
式中:sj为节点j的净输入,
[0168]
由上式可得权值wkj调整公式为:
[0169][0170]
权值wik的调整类似于wkj,其调整公式为:
[0171][0172]
通过正向传播和反向传播这两个过程的交替进行,在权向量空间执行误差函数梯度下降策略,动态迭代一组权向量,使网络误差函数达到最小值,从而完成信息提取和记忆过程;
[0173]
d1:天然气流量计检定控制器的功能是根据当前工况和目标流量,给出四个调节阀的开度,阀门组合和进站压力作为工况判断参数与检定流量(目标流量)作为bp神经网络的输入,而四个阀的开度作为输出,构建控制神经网络模型,并使用控制器进行验证,控制器给出方案与实际方案基本一致,bp神经网络对于此类复杂的非线性映射关系有着较好的适用性,同时对于长期运行的检定站,存在着大量的历史检定数据,可供神经网络训练,为了提高神经网络预测的准确性,首先需要对数据中存在的无效值、错误值和重复值以及采集中的噪声进行处理,然后使用清洗后的数据对神经网络进行训练,将调节阀门状态和站场工艺参数条件作为输入,检定流量作为输出,构建检定站神经网络仿真模型,选取70%作为训练数据,15%作为验证数据,剩余15%作为测试数据进行bp神经网络训练;
[0174]
所用计算机cpu配置为amd 3600,内存为16gb,系统为windows 10,通过大量的尝试,最终确定神经网络结构为5层网络,其中隐层3层的神经元个数分别为60,200,80,训练时间为4分12秒,以相关系数r作为bp神经网络训练效果的评价指标,r越接近1,其训练效果越好,回归系数(r值)超过0.99,拟合效果较好,从数据集中均匀选取3000个点进行结果验证,仿真检定流量与实际检定流量也基本一致,证明了该神经网络仿真模型的准确性,通过神经网路建立的仿真模型,对检定流量的仿真基本一致,经数据分析,该段数据仿真的绝对误差平均值为21.733m3/h,绝对误差的最大值为313.1358m3/h,绝对误差的最小值为0.0041m3/h,该段数据的相对误差的平均值0.09,相对误差的最大值为2.2,相对误差的最小值为1.573
×
10-6;
[0175]
天然气流量计检定控制器的功能是根据当前工况和目标流量,给出四个调节阀的开度,该控制器模型是2.7.3节仿真模型的逆模型,阀门组合和进站压力作为工况判断参数与检定流量(目标流量)作为bp神经网络的输入,而四个阀的开度作为输出,构建控制神经网络模型,对样本进行处理后,选取70%作为训练数据,15%作为验证数据,剩余15%作为测试数据进行bp神经网络训练,通过大量的尝试,最终确定神经网络结构为7层网络,其中隐层4层的神经元个数分别为20,50,40,10,花费时间6分19秒,该神经网络r值为0.96117,说明拟合效果较好,从数据集中均匀选取3000个点进行结果验证,控制器给出方案与实际方案也基本一致,证明了该神经网络控制器的可用性;
[0176]
调节阀前压力预测
[0177]
在调节阀模型中,由于现场的测量仪表的位置与水力模型的位置不一致,在数值上有一定的偏差,为了缩小模型的偏差,让模型的输出值更加精确,使之能更好的应用于现场,在此采用bp神经网络,对调节阀前压力进行预测,神经网络对数据的要求点高,因此对神经网络的输入与输出的选择上显得尤为重要,在此,选择的输入为进站压力,流程(一种方法为标准表与检定的台位的选择,在此以数字编码来确定;另一种方法为通过摩阻系数来表征流程),流量,温度,模型的输出为调节阀前的压力,通过这样的方法来对任意流程任意流量调节阀前压力预测,通过上述的分析可以看出在对检定的流程进行确定之后,对计算调节阀开度的关键参数:调节阀前压力的识别,拟合的程度高,能为计算各个检定流量点调节阀阀门开度的计算算法提供有力支撑;
[0178]
检定流量预测
[0179]
由于机理模型在不同的条件下,有不同的模型方程,所以将机理模型处理的不好的地方,采用神经网络模型进行预测,这样,在宏观的尺度上,所建立的预测模型,既结合了“白箱”的机理模型,对常规工况下,站场的状态进行仿真预测;又结合了“黑箱”的神经网络模型,对特殊工况下,站场的状态进行仿真预测,通过“灰箱”的方式来做到仿真预测,通过bp神经网络,对dn250流程下,所有fv1005全关下的工况进行预测仿真,dn250流程下所有数据的神经网络模型,将dn250流程下所有的数据按7:3来分,70%的80%与20%用来做学习和学习的校验,30%用来做外延性测试,对于所有的数据的70%进行仿真学习,对于数据的30%进行预测输出,bp神经网络的预测性波动不大,但是得考虑到神经网络的更新频率,输入输出的变化,因此对于bp神经网络模型,可以针对特殊的工况来进行机理模型的补充,
[0180]
采用lstm(长短期记忆)神经网络来进行分析,同样也是采用70%的90%与10%用来做学习和学习的校验,30%的用来做外延性测试,lstm神经网络对于处理时序处理有一定的优势,从整体的数据上来看,处理的结果也要优于bp神经网络,但是由于其输出极度依赖近前数据,导致输出的波动频率过高,并不适用于检定站的现场应用;
[0181]
出站压力和工况总流预测
[0182]
如图4所示,为了加快调阀速度,解决在达到目标流量范围后,流量不稳定的情况,通过确定大旁通1005阀的开度,来使整个调阀系统完整且闭环,在其中需要对目标点下的pt8206的压力值进行预测,从而使得fv1005可控;
[0183]
如图5所示,为了加快调阀速度,解决在达到目标流量范围后,流量不稳定的情况,通过确定大旁通1005阀的开度,来使整个调阀系统完整且闭环,为了结合预测pt8206的神经网络可用,上述两个神经网络从数据角度解决了大时滞系统的控制预测困难,作为机理模型的辅助数据源,起到了降低控制时滞和提高预测精度的作用
[0184]
s7:智能检定系统建立,控制器启动后工作在指令检定状态,在此种状态下,智能控制器监听等待检定客户端发送检定任务,当检定客户端将一个检定任务的全部信息(包含被检表信息、检定任务信息和流量点等)发送至智能控制器后,智能控制器进行流程检查,流程检查一方面进行阀位状态和初始状态的检查保证接管控制时管路组合安全合理,另一方面针对性选择不同的运行参数集,参与模型预测和水力仿真,如图6所示,工作级控制器全部算法搭载于smartcalibration2.0.8智能控制器软件中,部署在e1000服务器中,使用moubustcp协议实现站控、检定客户端的数据交互和指令传输;
[0185]
e1:阀位合格后进入历史工况复现算法,进行阀位组合生成并运用历史数据库数据进行修正,完成第一次多阀联调,在历史工况控制效果不佳或基于bp神经网络的控制器阀位方案明显失效时,使用流动预测结果进行第二次多阀联调;
[0186]
e2:在两次多阀联调后剩余控制区间使用较为保守的单阀控制算法进行流量实时控制,快速节流控制或单阀压降分分配增量方案进行流量的降低或提升,完成流量调整后发送开始检定标志,检定客户端进行流量计检定并连续进行下一次检定,
[0187]
本具体实施方式的实施例均为本发明的较佳实施例,并非依此限制本发明的保护范围,故:凡依本发明的结构、形状、原理所做的等效变化,均应涵盖于本发明的保护范围之内。
再多了解一些
本文用于创业者技术爱好者查询,仅供学习研究,如用于商业用途,请联系技术所有人。