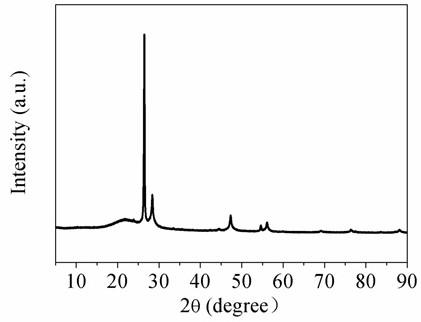
1.本发明涉及锂电池领域,具体涉及一种利用废旧负极制备碳硅复合负极材料的方法。
背景技术:
2.锂离子电池广泛采用的负极材料是石墨类碳材料,而石墨类负极材料的理论比容量只有372mah g-1
,限制了高能量密度电池的发展要求。在众多新开发的负极材料中,硅负极材料的理论比容量高达4200 mah g-1
,远高于石墨负极的容量,且其电压平台略高于石墨负极,充电时不会析锂,具有较好的安全性能,使其成为最有潜力代替石墨负极的材料。但是由于其在充/放电循环过程中发生的大体积变化,加速了电极材料的粉化和剥离,导致电池容量迅速衰减,同时这种巨大的体积变化,使得材料表面难以形成稳定的固体电解质膜(sei),伴随sei不断地破裂和形成,大量锂被消耗,电池容量不断衰减,循环性能变差。
3.另一方面,大量动力电池将面临退役报废后的处理问题,处理不当将造成严重资源浪费和环境污染。因此,从废旧锂离子电池中回收石墨材料,并用作高性能负极材料的原材料,不仅有助于解决环境污染问题,也具有重要的经济价值。
技术实现要素:
4.本发明的目的是提供一种利用废旧负极制备碳硅复合负极材料的方法,该方法从废旧负极得到石墨材料,并与微硅粉、沥青等原料一起制备出了比容量大、循环稳定性好的锂离子电池负极材料,工艺简单,成本低廉。
5.为了实现上述目的,本发明采取如下技术方案:一种利用废旧负极制备碳硅复合负极材料的方法,包括如下步骤:步骤s1:拆解出废旧锂离子电池的负极片置于水中并超声处理使负极材料与集流体分离,取出集流体后将液体过滤,得到第一含锂液体和第一滤渣;步骤s2:将所述第一滤渣用酸处理,过滤后得到第二含锂液体和第二滤渣,第二滤渣干燥后得到石墨材料;步骤s3:将所述石墨材料与微硅粉混合球磨,得到石墨微硅粉混合物;步骤s4:将所述石墨微硅粉混合物分散在有机溶剂中,加入沥青粉后搅拌得到浆料;步骤s5:将所述浆料喷雾干燥,得到沥青包覆的石墨微硅粉颗粒;步骤s6:将所述沥青包覆的石墨微硅粉颗粒在惰性气氛或还原性气氛中加热还原,将微硅粉中的二氧化硅还原成单质硅和sio
x
并实现沥青的碳化,得到还原产物;步骤s7:将所述还原产物酸化处理以进一步去除未反应的二氧化硅,水洗干燥后得到锂离子电池用碳硅复合负极材料。
6.优选的,所述步骤s1中,所述废旧锂离子电池的负极片与水的质量比为1-10:100,超声水浴的温度为 25-80 ℃,超声时间为 5-240 min,所述步骤s2中,所述酸为稀盐酸、稀
硫酸或稀硝酸中的至少一种,浓度为0.1~5 mol/l。
7.优选的,所述步骤s3中,所述石墨微硅粉混合物的粒径不大于10μm;所述石墨微硅粉混合物中石墨与微硅粉的质量比为10:1-40。
8.优选的,所述步骤s4中,所述有机溶剂为n-甲基吡咯烷酮、三氯甲烷、二硫化碳、甲苯、四氢呋喃、石油醚中的一种或者两种以上任意比例的混合物。
9.优选的,所述步骤s4中,所述沥青粉包括煤沥青粉、石油沥青粉、浸渍沥青粉、改质沥青粉、中间相沥青粉中的一种或几种以任意比例混合;沥青粉在有机溶剂中的重量分数为0.1-5%,沥青粉加入后超声搅拌0.5~2h使其完全溶解。
10.优选的,所述步骤s5中,喷雾干燥的参数设置为:进口温度120-200℃,出口温度75-110℃,雾化器工作压力为100-500 kpa,进料速率为30-500 ml/h。
11.优选的,所述步骤s6中,所述惰性气氛为高纯氮气或氩气,所述还原性气氛为氢气或氢气含量5-10%v/v的氩氢混合气,加热升温速率为2-10 ℃/min,热还原温度为600-1200℃,热还原时间为1-8h。
12.优选的,所述步骤s7中,酸化处理所用酸液为浓度为5-10wt.%hf水溶液,浓度为5-10wt.%hf水溶液与浓度为5~10wt.%盐酸的混合液或浓度为5-10wt.%hf水溶液与5-10wt.%硝酸的混合液,酸化处理的时间为0.5-10h。
13.优选的,还包括步骤s7:将所述第一含锂溶液和第二含锂液体合并后蒸发浓缩,然后加入饱和碳酸盐溶液,反应得到碳酸锂沉淀,洗涤干燥后得到碳酸锂粉末。
14.优选的,所述蒸发浓缩的温度为60-90 ℃,时间为30-300 min,所述碳酸盐饱和溶液为碳酸钠饱和溶液或碳酸钾饱和溶液。
15.本发明从废旧锂离子电池负极中回收石墨材料,并将粉碎的石墨材料与微硅粉混合并在有机溶剂中与沥青粉形成浆料,可以使沥青包覆在微硅粉和石墨粉上并经喷雾干燥形成均匀颗粒,经过还原后微硅粉中的主要成分二氧化硅被还原成单质硅及sio
x
,沥青在高温下发生碳化从而形成高电导率的无定型碳包覆层,形成稳定的sei膜,避免硅基材料的裸露。最后经酸化处理进一步除去对电化学性能无贡献的残留的二氧化硅并得到最终的负极材料。碳包覆si/sio
x
/石墨负极复合材料中的硅纳米粒子分布于碳包覆层和sio
x
基体中,为硅的体积膨胀提供多重的缓冲空间,提高了其首次库伦效率和循环稳定性,该负极复合材料具有分级多孔结构,有利于电子和离子的快速传输、材料压实密度大。包覆的沥青碳阻挡了石墨和硅基颗粒与电解液的直接接触,抑制了石墨材料的溶剂化分子的共插入现象,同时,这层无定形碳结构还能起到稳定石墨结构的作用,抑制充放电过程中的膨胀和剥落。
16.此外,本发明还具有如下有益效果:(1)本发明提出一种利用废旧锂离子电池负极和固废微硅粉制备硅碳复合材料的方法,其生产工艺简便、操作简单,生产成本低廉,适用于规模化工业生产。
17.(2)本发明以废旧锂离子电池的负极材料为原料,通过回收再利用合成新型硅碳复合材料,该工艺使废弃资源得以利用,对环境保护和资源再利用起重大作用;同时进一步降低硅碳复合材料制造成本,提高废弃石墨负极材料的应用价值。
18.(3)目前硅-碳负极材料常选用高纯微纳米硅为硅源,材料成本较高。本发明所使用的微硅粉为固体废弃物,其来源广泛、成本低廉,实现了微硅粉的真正高效再利用,具有很大的成本优势和应用前景。
19.(4)本发明中,通过逐步对废旧电池的分离,不仅回收再生了石墨,而且可以回收包括正极材料、铝塑膜、隔膜、集流体在内的其他电池部件,回收过程石墨材料未遭到破坏性处理。
附图说明
20.图1为本发明实施例2制备出的硅碳复合材料的xrd图;图2为本发明实施例2制备出的硅碳复合材料在5000倍放大倍率下的sem图;图3为本发明实施例2制备出的硅碳复合材料在10000倍放大倍率下的sem图;图4为本发明实施例2制备出的硅碳复合材料在200ma g-1
电流密度下的循环稳定曲线。
21.图5为本发明实施例2中回收的锂盐(li2co3)xrd谱图。
具体实施方式
22.为了进一步说明本发明,下面结合附图及具体实施例对本发明进行进一步的详细说明。
23.实施例1:将废旧锂离子电池进行放电、拆解和裁剪后得到的负极片,按照负极片与水质量比为 1:20,置于25℃去离子水中超声处理30 min,使负极材料与集流体分离,取出已分离的集流体,然后过滤得到含锂浸出液即第一含锂液体和第一滤渣。
24.将上一步骤中得到的第一滤渣置于1 mol/l 硫酸溶液处理,第一滤渣与酸溶液的固液质量比为1: 10,酸浸的温度为 25 ℃,时间为 120 min。过滤清洗、分别收集得到含锂浸出液即第二含锂液体和第二滤渣,滤渣干燥后得到纯化后的石墨材料。
25.将纯化后的石墨材料与微硅粉混合球磨、过筛后得到石墨微硅粉混合物;其中纯化石墨与微硅粉质量比2:1,球磨、过筛后混合粉体的粒径为1-5μm。
26.将沥青粉末搅拌溶解于三氯甲烷后,加入球磨、过筛后的石墨微硅粉混合物,充分混合后形成均匀稳定的浆料;沥青为软化点为105℃的煤焦油沥青。沥青粉末在有机溶剂中的重量分数为1%。
27.将混合好浆料通过喷雾干燥设备进行干燥处理,得到沥青包覆的石墨微硅粉颗粒(即类球形石墨/微硅粉@沥青颗粒粉体)。喷雾干燥机工作参数设置为:进口温度150℃,出口温度100℃,雾化器工作压力为100kpa,进料速率为60 ml/h。
28.将制得的石墨/微硅粉@沥青粉体材料置于气氛炉中,在气氛保护下恒温热还原后随炉冷却至室温(二氧化硅还原为单质硅及低价态硅的氧化物sio
x
);惰性气氛下为高纯氮气,加热升温速率为3 ℃/min,热还原温度为700℃,热还原时间为4h。热还原方式为碳热还原。
29.利用5wt.%hf酸水溶液对热还原后的产物进行常温浸泡处理,酸性溶液处理时间为 3 h,水洗后烘干,即得到锂离子电池用硅碳复合负极材料。
30.将上述步骤中回收的的含锂浸出液80 ℃下进行蒸发浓缩 60min后,加入饱和碳酸钠溶液,反应得到碳酸锂沉淀,洗涤干燥后得到碳酸锂粉末。
31.实施例2:
将废旧锂离子电池进行放电、拆解和裁剪后得到的负极片,按照负极片与水质量比为 1:10,置于40℃去离子水中超声处理30 min,使负极材料与集流体分离,取出已分离的集流体,然后过滤得到含锂浸出液即第一含锂液体和第一滤渣。
32.将上一步骤中得到的第一滤渣置于2 mol/l 硫酸溶液处理,第一滤渣与酸溶液的固液质量比为1: 5,酸浸的温度为 40 ℃,时间为 60 min。过滤清洗、分别收集得到含锂浸出液即第二含锂液体和第二滤渣,第二滤渣干燥后得到纯化后的石墨材料。
33.将纯化后的石墨材料与微硅粉混合球磨、过筛后得到石墨微硅粉混合物;其中纯化石墨与微硅粉质量比4:1,球磨、过筛后混合粉体的粒径为1-3μm。
34.将沥青粉末搅拌溶解于四氢呋喃后,加入球磨、过筛后的石墨微硅粉混合物,充分混合后形成均匀稳定的浆料;沥青为软化点为255℃的煤焦油沥青。沥青粉末在有机溶剂中的重量分数为2%。
35.将混合好浆料通过喷雾干燥设备进行干燥处理,得到沥青包覆的石墨微硅粉颗粒(即类球形石墨/微硅粉@沥青颗粒粉体)。喷雾干燥机工作参数设置为:进口温度140℃,出口温度90℃,雾化器工作压力为250kpa,进料速率为90 ml/h。
36.将制得的石墨/微硅粉@沥青粉体材料置于气氛炉中,在气氛保护下恒温热还原后随炉冷却至室温(二氧化硅还原为单质硅及低价态硅的氧化物sio
x
);气氛为氢气含量10%的氩氢混合气,加热升温速率为5 ℃/min,热还原温度为800℃,热还原时间为4h。热还原方式为碳热和氢气还原。
37.利用10wt.%hf酸水溶液对热还原后的产物进行常温浸泡处理,酸性溶液处理时间为2 h,水洗后烘干,即得到锂离子电池用硅碳复合负极材料。
38.将上述步骤中回收的的含锂浸出液(即第一含锂液体和第二含锂液体)90 ℃下进行蒸发浓缩 40min后,加入饱和碳酸钠溶液,反应得到碳酸锂沉淀,洗涤干燥后得到碳酸锂粉末。
39.实施例3:将废旧锂离子电池进行放电、拆解和裁剪后得到的负极片,按照负极片与水质量比为 1:15,置于40℃去离子水中超声处理20 min,使负极材料与集流体分离,取出已分离的集流体,然后过滤得到含锂浸出液即第一含锂液体和第一滤渣。
40.将上一步骤中得到的第一滤渣置于1 mol/l 硫酸溶液处理,第一滤渣与酸溶液的固液质量比为1: 20,酸浸的温度为60 ℃,时间为 120 min。过滤清洗、分别收集得到含锂浸出液即第二含锂液体和第二滤渣,第二滤渣干燥后得到纯化后的石墨材料。
41.将纯化后的石墨材料与微硅粉混合球磨、过筛后得到石墨微硅粉混合物;其中纯化石墨与微硅粉质量比5:1,球磨、过筛后混合粉体的粒径为2-10μm。
42.将沥青粉末搅拌溶解于二硫化碳后,加入球磨、过筛后的石墨微硅粉混合物,充分混合后形成均匀稳定的浆料;沥青为软化点为160℃的煤焦油沥青。沥青粉末在有机溶剂中的重量分数为0.5%。
43.将混合好浆料通过喷雾干燥设备进行干燥处理,得到沥青包覆的石墨微硅粉颗粒(即类球形石墨/微硅粉@沥青颗粒粉体)。喷雾干燥机工作参数设置为:进口温度160℃,出口温度100℃,雾化器工作压力为200kpa,进料速率为200 ml/h。
44.将制得的石墨/微硅粉@沥青粉体材料置于气氛炉中,在气氛保护下恒温热还原后
(111), (-202),(002),(-112),(020)和 (-311)晶面,表明沉淀回收的锂盐为li2co3,此外,没有观察到其他可能杂质的额外衍射峰。
再多了解一些
本文用于创业者技术爱好者查询,仅供学习研究,如用于商业用途,请联系技术所有人。