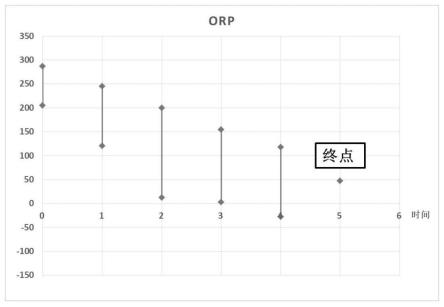
一种去除富铂族金属的铜阳极泥中snpbfe杂质的方法
技术领域
1.本发明属于冶金领域,尤其涉及一种铜阳极泥中杂质的去除方法。
背景技术:
2.铂族金属(pgm)含铂、钯、铑、锇、钌、铱6种元素,广泛应用于化工、汽车、航天等领域。我国铂族金属矿产资源储量仅350吨,每年从矿产资源中产出的铂族金属约3吨,但需求量超过180吨,高度依赖进口。从失效催化剂、电子废弃物等二次资源中回收pgm,是解决问题的有效途径。众多回收方案中,以铜为捕集剂的火法富集-电解-阳极泥分离提纯工艺具有较高的可行性和经济性。不同于以矿石为原料的铜冶炼工艺,该工艺的原料为铂族金属含量较高的失效催化剂、电子废弃物等二次资源,铜电解生成的阳极泥具有如下特点:(1)传统铜阳极泥中pgm含量《0.5%,而该工艺得到的铜阳极泥中pgm含量较高,一般》1%;(2)火法富集普遍协同处理失效催化剂与电子废弃物,二次资源中snpbfe等杂质进入铜中,导致电解得到的铜阳极泥中杂质含量较高,加重了后续湿法工序的负担。
3.目前,针对这种富pgm铜阳极泥处理的报道较少。传统铜阳极泥一般采用硫酸浸出除铜,此时snpbfe的硫酸浸出率较低,再采用氧化等高温工序去除其他杂质,最后提取贵金属。传统铜阳极泥成分异于pgm阳极泥(表1),处理方法不具有参考性。且pgm阳极泥中ptpdrh含量较高,若采用长流程的传统工艺将造成贵金属回收周期变长,工序变多,损耗变大,难以快速提取贵金属。
4.表1:铜冶炼产出的传统阳极泥与二次资源回收产出的阳极泥的成分对比(wt%)
[0005][0006]
发明人致力于研发铜为捕集剂的火法富集-电解-阳极泥分离提纯工艺,回收对象为失效催化剂等二次资源,深刻认识到火法富集要求较广原料适应性与湿法分离要求低杂质含量的矛盾。针对回收二次资源产生的富铂族金属的铜阳极泥,亟需一种高效低成本的方法,去除阳极泥中snpbfe等杂质,得到低杂质含量的残渣作为后续湿法工序的原料,提高ptpdrh分离提纯效率。
技术实现要素:
[0007]
本发明所要解决的技术问题是克服以上背景技术中提到的不足和缺陷,提供一种工艺流程短、去杂效率高的去除富铂族金属的铜阳极泥中snpbfe杂质的方法。为解决上述技术问题,本发明提出的技术方案为:
[0008]
一种去除富铂族金属的铜阳极泥中snpbfe杂质的方法,包括以下步骤:
[0009]
(1)将富铂族金属的铜阳极泥与盐酸溶液混合,搅拌浸出得到浸出体系;
[0010]
(2)向所述浸出体系中加入铁粉还原浸出体系中的ptpdrh,过滤得到含snpbfe杂质浸出液和残渣。
[0011]
上述去除富铂族金属的铜阳极泥中snpbfe杂质的方法中,优选的,富铂族金属的铜阳极泥为以铜为捕集剂,利用火法富集含铂族金属的二次资源后再经电解得到的铜阳极泥。
[0012]
上述去除富铂族金属的铜阳极泥中snpbfe杂质的方法中,优选的,富铂族金属的铜阳极泥中pt、pd、rh的质量之和占富铂族金属的铜阳极泥干重的5-60%。
[0013]
上述去除富铂族金属的铜阳极泥中snpbfe杂质的方法中,优选的,富铂族金属的铜阳极泥(湿重)与盐酸溶液的质量比为0.2-0.6,富铂族金属的铜阳极泥的含水率为30-70%,盐酸溶液的质量浓度为20-38%。盐酸量过少,阳极泥中的snpbfe无法充分浸出;盐酸量过多,现场挥发严重,作业环境恶劣。
[0014]
上述去除富铂族金属的铜阳极泥中snpbfe杂质的方法中,优选的,搅拌浸出与铁粉还原时控制温度为20-80℃,并控制搅拌浸出的时间为0.5-10h。搅拌浸出和铁粉还原时,浸出体系温度控制在20-80℃,温度过低,降低前期杂质snpbfe溶出和后期铁粉还原ptpdrh的效率;温度过高,盐酸溶液挥发严重,恶化作业环境。搅拌浸出时,浸出时间过短,阳极泥中的snpbfe无法充分浸出;浸出时间过长,阳极泥中ptpdrh大量溶出,加重铁粉还原的负担。
[0015]
上述去除富铂族金属的铜阳极泥中snpbfe杂质的方法中,优选的,所述铁粉的粒度为0.05-2mm。铁粉粒度过细,反应活性增加,与空气接触后易爆炸,不适于现场操作;铁粉粒度过粗,反应活性降低,导致还原所需时间变长,降低生产效率。
[0016]
上述去除富铂族金属的铜阳极泥中snpbfe杂质的方法中,优选的,所述铁粉分多次加入,且检测还原终点的氧化还原电位,控制还原终点时浸出体系(静置后的液相)的氧化还原电位orp在-100mv与100mv之间。orp低于-100mv,浸出体系液相中的杂质snpbfe易被还原进入残渣,导致后续湿法工序ptpdrh分离提纯效率降低;orp高于100mv,残渣中ptpdrh易溶出进入浸出体系的相液中,造成贵金属损失。
[0017]
不同以矿石为原料产生的传统铜阳极泥,本发明处理对象是以含铂族金属二次资源为原料产生的pgm阳极泥,其铂族金属含量远高于传统阳极泥,快速高效低损耗回收贵金属是首要目的,以资源循环为背景的该种pgm阳极泥被研究的较少。本发明考虑相对硫酸溶液,snpbfe更易在盐酸溶液中溶出,此时ptpdrh也会部分溶出;热力学上,铁的标准氧化还原电位为-0.45v,相对snpb较接近,相对ptpdrh较低,这表明采用铁粉可还原ptpdrh且使得snpbfe留在浸出液,从而实现杂质的去除。
[0018]
与现有技术相比,本发明的优点在于:
[0019]
1、相对于传统阳极泥采用硫酸脱铜-火法去除其他杂质的技术路线,本发明在一道工序内同时去除snpbfe杂质,且不使用火法设备,降低了设备初期投资。
[0020]
2、本发明克服了传统阳极泥硫酸浸出过程snpbfe浸出率低的缺点,本发明采用盐酸浸出提高snpbfe浸出率,之后利用铁粉的弱还原性,通过铁粉还原浸出体系中的ptpdrh,减少贵金属损失的同时,使得snpbfe留在浸出液,实现杂质去除。
[0021]
3、本发明的去除富铂族金属的铜阳极泥中snpbfe杂质的方法具有工艺流程短、杂质去除率高、贵金属损耗少等优势。
附图说明
[0022]
为了更清楚地说明本发明实施例或现有技术中的技术方案,下面将对实施例或现有技术描述中所需要使用的附图作简单地介绍,显而易见地,下面描述中的附图是本发明的一些实施例,对于本领域普通技术人员来讲,在不付出创造性劳动的前提下,还可以根据这些附图获得其他的附图。
[0023]
图1为实施例1中铁粉还原过程pgm(ptpdrh)浸出率的变化。
[0024]
图2为实施例1中铁粉还原过程杂质(snpbfe)浸出率的变化。
[0025]
图3为实施例1中铁粉还原过程浸出体系orp的变化。
[0026]
图4为实施例2中铁粉还原过程pgm(ptpdrh)浸出率的变化。
[0027]
图5为实施例2中铁粉还原过程杂质(snpbfe)浸出率的变化。
[0028]
图6为实施例2中铁粉还原过程浸出体系orp的变化。
具体实施方式
[0029]
为了便于理解本发明,下文将结合说明书附图和较佳的实施例对本发明作更全面、细致地描述,但本发明的保护范围并不限于以下具体的实施例。
[0030]
除非另有定义,下文中所使用的所有专业术语与本领域技术人员通常理解的含义相同。本文中所使用的专业术语只是为了描述具体实施例的目的,并不是旨在限制本发明的保护范围。
[0031]
除非另有特别说明,本发明中用到的各种原材料、试剂、仪器和设备等均可通过市场购买得到或者可通过现有方法制备得到。
[0032]
实施例1:
[0033]
一种去除富铂族金属的铜阳极泥中snpbfe杂质的方法,包括以下步骤:
[0034]
(1)将33kg(含水54%)pgm阳极泥、70kg盐酸(质量浓度36%)、83kg水加入带搅拌装置的设备,开启搅拌装置,使用插入式电阻丝加热浸出体系于70℃,加热搅拌条件下浸出2h;
[0035]
(2)分5批次向浸出体系加入粒度为0.1mm的铁粉,第一次加入1kg(对应0h),第二次加入0.5kg(对应1h),第三次加入0.65kg(对应2h),第四次加入0.25kg(对应3h),第五次加入0.21kg(对应4h),对铁粉加入前的浸出体系(0h、1h、2h取样,3h、4h未取样)和最终得到的浸出体系(5h)取样,通过icp分析化学成分,算出ptpdrh和snpbfe浸出率的变化,浸出率=(浸出液中元素浓度
×
浸出液体积)/(阳极泥中元素浓度
×
阳极泥质量),通过氧化还原电位orp仪(ag/agcl参比电极)检测添加铁粉前后浸出体系电位的变化;
[0036]
(3)采用固液分离器过滤,得到浸出液和残渣;
[0037]
(4)对残渣进行化学分析。
[0038]
由图1所示,铁粉还原了浸出体系中的pgm(ptpdrh),降低了过滤后贵金属在浸出液的损失。由图2所示,铁粉不会大量还原浸出体系中的杂质(snpbfe),这是由于铁粉是一种弱还原剂,其标准氧化还原电位为-0.45v,相对snpb较接近,相对ptpdrh较低。由图3所示,每次铁粉加入,都会导致浸出体系orp降低,随着铁粉不断加入,浸出体系的orp逐渐降低。图3中横坐标各时间点处对应的竖线为加入铁粉前后的orp变化示意图,前一次铁粉加入反应完毕后,下一次是否加入铁粉根据浸出体系的颜色与浸出体系中pgm的浓度来判断,
若浸出体系为肉眼可见的红色,则继续加入铁粉;若浸出体系的红色已不明显且浸出体系中pgm浓度小于10ppm,则不再加入铁粉。所有铁粉分次加入后,最终得到的浸出体系(静置后的液相)的orp在-100mv与100mv之间。
[0039]
由表2可知,通过该方法,处理后得到的残渣中ptpdrh浓度相对阳极泥更高(进一步富集)且杂质含量降低,这意味着较少杂质进入后续湿法工序,可提高ptpdrh分离提纯效率。
[0040]
表2:处理前pgm阳极泥和处理后残渣的成分对比
[0041][0042]
实施例2:
[0043]
一种去除富铂族金属的铜阳极泥中snpbfe杂质的方法,包括以下步骤:
[0044]
(1)将36kg(含水54%)pgm阳极泥、66kg盐酸(质量浓度36%)、78kg水加入带搅拌装置的设备,开启搅拌装置,使用插入式电阻丝加热浸出体系于70℃,加热搅拌条件下浸出2h;
[0045]
(2)分5批次向浸出体系加入粒度为0.1mm的铁粉,第一次加入1kg(对应0h),第二次加入0.73kg(对应1h),第三次加入0.34kg(对应2h),第四次加入0.07g(对应3h),第五次加入0.1kg(对应4h),对铁粉加入前的浸出体系(0h、1h、2h、4h取样,3h未取样)和最终得到的浸出体系(5h)取样,通过icp分析化学成分,算出ptpdrh和snpbfe浸出率的变化,浸出率=(浸出液中元素浓度
×
浸出液体积)/(阳极泥中元素浓度
×
阳极泥质量),通过氧化还原电位orp仪(ag/agcl参比电极)检测添加铁粉前后浸出体系电位的变化;
[0046]
(3)采用固液分离器过滤,得到浸出液和残渣;
[0047]
(4)对残渣进行化学分析。
[0048]
由图4所示,铁粉还原了浸出体系中的pgm(ptpdrh)。由图5所示,铁粉不会大量还原浸出体系中的杂质(snpbfe),杂质得以去除。由图6所示,每次铁粉加入,都会导致浸出体系orp降低,随着铁粉不断加入,浸出体系的orp逐渐降低。图6中,第5次加入铁粉(4h)前,浸出体系中红色已经不明显,但检测分析后浸出体系(静置后的液相)中pgm的浓度大于10ppm,因此仍需加入少量的铁粉反应。维持稳定后,浸出体系的红色已不明显且浸出体系中pgm浓度小于10ppm,因此不需再加入铁粉。反应终点(5h)浸出体系(静置后的液相)的orp在-100mv与100mv之间。
[0049]
由表3可知,处理后得到的残渣中ptpdrh浓度相对阳极泥更高(进一步富集)且杂质含量降低,这意味着较少杂质进入后续湿法工序,可提高ptpdrh分离提纯效率。
[0050]
表3:处理前pgm阳极泥和处理后残渣的成分对比
[0051]
再多了解一些
本文用于创业者技术爱好者查询,仅供学习研究,如用于商业用途,请联系技术所有人。