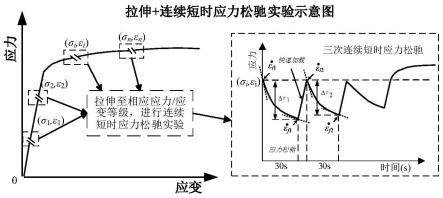
1.本发明涉及塑性成形基础理论与建模技术领域,具体而言,涉及一种考虑温度历程的铝合金蠕变时效形性协同预测方法。
背景技术:
2.蠕变时效成形(creepageforming,caf)工艺通过将可热处理铝合金构件变形加载后升温至时效温度,并保持一段时间(10-20h),在此过程中材料发生蠕变变形以及时效强化,同时实现最终构件成形以及性能提升,极其适用于航空航天大型蒙皮、壁板等小变形量薄壁构件精确制造。由于材料蠕变过程中仅有部分弹性变形转化为蠕变(塑性变形),因此该工艺存在极大回弹,且成形过程中铝合金内部析出相及位错增殖受应力、温度及时间耦合影响,强度性能变化极大。如何实现其成形过程变形及性能的协同预测,是实现工艺设计与应用的关键。
3.实际caf工艺过程中,构件加载后经历升温、保温及降温阶段,复杂温度历程导致其内部蠕变及析出演变复杂。现有描述蠕变时效行为的模型仅考虑单一温度下材料蠕变变形及时效强化演变,仅能实现单一温度下保温过程caf工艺变形及性能演变预测,对升温及降温阶段缺乏考虑,同时若更换成形温度,相关模型与参数即无法适用。现有研究表明,caf过程中升温及降温过程对材料变形及时效有明显影响,变形影响幅度可超过20%;同时,为提升工艺效率,现有研究也提出了变温度下caf新工艺路径。然而现有蠕变时效材料本构模型无法满足完整caf工艺流程以及变温caf新工艺过程中构件变形及性能演变的有效预测,极大制约了该工艺在航空航天领域的未来推广应用。
4.为此提出一种考虑温度历程的铝合金蠕变时效形性协同预测方法,以解决上述提出的问题。
技术实现要素:
5.本发明旨在提供一种考虑温度历程的铝合金蠕变时效形性协同预测方法,以解决或改善上述技术问题中的至少之一。
6.有鉴于此,本发明的第一方面在于提供一种考虑温度历程的铝合金蠕变时效形性协同预测方法。
7.本发明的第一方面提供了一种考虑温度历程的铝合金蠕变时效形性协同预测方法,包括如下步骤:s1,在带加热炉的单向拉伸试验机上,在不同温度下,分别对铝合金材料进行单轴拉伸-连续短时应力松驰试验,获得相应温度下材料初始状态下的短时应力松驰曲线数据;s2,在带加热炉的单向拉伸试验机上,在不同温度下,分别对铝合金材料进行应力松驰试验和单轴拉伸-连续短时应力松驰试验,获取铝合金材料在相应温度下不同应力松驰时效状态后的连续短时应力松驰实验数据;s3,基于s1和s2获得的试验数据,分析并计算获得铝合金材料在不同温度、不同应力等级或应变等级、不同应力松驰时间下的材料的变形激活能q;s4,建立考虑温度、变形和时间的激活能变化模型,以及以激活能为变量的铝
合金蠕变变形模型;s5,建立基于铝合金析出动力学以及应力耦合影响的考虑温度影响的铝合金析出相演变模型及铝合金强化预测模型;s6,在带加热炉的单向拉伸试验机上进行不同温度、不同应力等级或应变等级下的蠕变时效和应力松驰试验,获得相应温度和变形等级下的铝合金材料的蠕变曲线、应力松驰曲线和性能演变曲线数据;s7,基于s6中获得的试验数据,对s5中的铝合金强化预测模型进行参数拟合校准和验证;s8,通过所述铝合金蠕变变形模型及强化预测模型对铝合金蠕变时效形性进行预测。
8.本发明提供的一种考虑温度历程的铝合金蠕变时效形性协同预测方法,考虑温度影响下对材料激活能变化影响,从而实现对蠕变或应力松驰变形机理的理解与预测;
9.同时考虑温度对析出相演变影响,同步实现了考虑温度影响下的材料微观结构及其强化特性预测。
10.开发的预测模型可实现升温-保温-降温全流程caf工艺以及变温caf新工艺形性协同预测,对caf工艺全流程及其改进高效率caf工艺精确预测及其构件制造的数值模拟均有重要指导意义。
11.具体地,选择的温度范围为20℃-200℃;
12.具体地,在s2步骤中,在达到指定应力松驰时间后(根据工艺要求整体时间t,选取0.3t,0.5t,t三个时间点);
13.具体地,在s7步骤中,基于实验数据,开展上述方程参数拟合校准及验证。基于三个不同变形等级下蠕变或应力松驰及屈服强度演变数据,采用粒子群优化算法,对上述蠕变及屈服强度方程进行拟合,校准获得其中非温度相关的材料常数;
14.进一步基于三个不同温度同变形等级下蠕变或应力松驰及屈服强度演变数据,对上述材料温度相关的材料常数进行拟合与校准,获得全部所需要材料常数。利用第四个温度及应力等级数据对获得的材料常数进行验证,验证相关材料常数和方程的有效性。
15.另外,根据本发明的实施例提供的技术方案还可以具有如下附加技术特征:
16.上述任一技术方案中,所述单轴拉伸-连续短时应力松驰实验的步骤,具体包括:s101,采用准静态的方式,通过单向拉伸试验机对材料拉伸至指定的变形等级,停止拉伸,保持短时间的应力松弛,记录应力随时间降低的数据;s102,采用快速加载的方式,通过单向拉伸试验机对材料拉伸至s101停止拉伸时的单向拉伸机所记录的应力等级,停止拉伸,保持短时间的应力松弛,记录应力随时间变化的数据;s103,重复步骤s101-s102两次;s104,选取下一级的变形等级,重复步骤s101-s103,直至拉伸达到最高的应变等级,结束实验;其中,所述变形等级包括应力等级和应变等级,位于弹性区域的所述应力等级由低到高至少设置三级,位于塑性区域的所述应变等级由低到高至少设置三级,所述短时间取10s-30s。
17.在该技术方案中,准静态即为应变速率10-3
~10-4
/s,单向拉伸至指定应力等级(弹性区域)或应变等级(塑性区域);
18.快速加载即为应变速率10-1
~10-2
/s,实验过程中弹性区域指定至少三级应力等级,塑性区域指定至少三级应变等级,且拉伸试验机对材料拉伸的应力等级由低到高逐级增高,应力等级或塑性区域根据实际需求进行设定和调整,采用多次的多级拉伸可保证实验中的材料整体不会发生大的断裂或者内部以及表面的裂缝,造成后期实验的终端。
19.具体地,在步骤s102中,当拉伸目标为应变等级时,通过单向拉伸试验机对材料拉
伸至s101停止拉伸时的单向拉伸机所记录的应力等级,其中的应力等级为相应应变等级对应的应力等级,且应力等级单向拉伸机会在实验中进行记录。
20.上述任一技术方案中,所述s3的步骤,具体包括:s301,基于s2中的实验数据,采用下述方式进行拟合,以获得此材料状态、此温度及应力等级下内应力分量σi:其中,t为应力松驰时间、σ0为初始应力等级、σ为随时间变化的应力数据、a和b为待拟合常数、σi为内应力分量,且与有效应力σe共同组成整体应力,表示为σ=σi σe;v302,提取s101中的第一次应力松驰结束时的应变速率以及s102中的第二次应力松驰开始时的应变速率,利用下述方程,拟合获得此状态下材料的激活体积数据v:其中,t为温度,为第二次应力松驰开始时的应变速率,为第一次应力松驰结束时的应变速率,δσ为第一次应力松驰过程整体应力变化量,c为待拟合常数;s303,基于s302中的内应力分量σi、有效内应力分量σe和激活体积v,通过下述公式计算获得材料在不同应力松驰时间、温度及应力状态下的激活能q:q=(δg
0-vσe);其中,δg0为材料在绝对零度下的吉布斯自由能,v为激活体积,σe为有效应力。
21.在该技术方案中,基于上述中的不同材料状态、不同温度、不同变形等级下获得的三次短时应力松驰曲线中的第一次应力松驰曲线数据,利用其方程进行拟合,获得此材料状态、此温度及变形等级下内应力分量σi;
22.由于应力松驰时间短(10-30s),且松驰后重新加载速率高,加载过程材料仍处于弹性变形,可近似认为该过程中材料内部状态(如位错等)未发生较明显变化,因此基于上述不同材料状态、不同温度、不同变形等级下获得的三次短时应力松驰曲线,提取第一次应力松驰结束时的应变速率以及后续快速加载后第二次应力松驰开始时的应变速率,利用其方程拟合获得此状态下材料的激活体积数据v;
23.基于上述中获得的不同状态下材料的内应力分量σi,有效内应力分量σe,以及激活体积v,通过其方程q=(δg
0-vσ
*
),计算获得铝合金在不同应力松驰时间、温度及变形状态下的激活能q。
24.上述任一技术方案中,所述s4的步骤,具体包括:s401,建立激活能随温度以及应力松驰过程中变形状态下的模型;s402,建立包含激活能变化的变量的铝合金蠕变变形材料模型,通过步骤s401中激活能随时间、温度以及变形等级的变化,以实现所述铝合金蠕变变形模型对各类温度及变形变化历程的模拟预测。
25.在该技术方案中,由于材料激活能受不同温度及变形状态的影响,因此建立激活能随温度以及应力松驰过程中变形状态下的模型,以解决了现有方法仅能实现单一恒定温度下铝合金蠕变时效预测的局限性;
26.然后建立考虑激活能变化的铝合金蠕变变形材料模型,借助激活能受时间、温度以及变形等级的变化影响,实现该蠕变变形方程对各类温度及变形变化历程的模拟预测。
27.上述任一技术方案中,所述步骤s401,具体包括:a.激活能随温度变化q0(t)模型为:q0(t)=(1-k1t/tm)q0;其中,tm为材料融化温度、t为蠕变温度、q0为参考激活能、k1为材
料常数;b.激活能随变形变化模型为:其中,k2为常数、为塑性应变速率。
28.在该技术方案中,q0和k1通过步骤s303中不同应力松驰温度下获得的激活能q的数据拟合获得,通过在激活能随温度变化q0(t)模型加入温度变量,使得整体模型能够充分考虑到温度对材料激活能的影响;
29.k1可通过步骤s303中不同应力松驰温度下获得的激活能q的数据拟合获得,通过在激活能随变形变化模型加入变形状态的变量,使得整体模型能够充分考虑到变形状态对材料激活能的影响。
30.上述任一技术方案中,所述步骤s402,具体包括:a.蠕变变形模型为:其中,为位错密度、r为空气常数、k3,k4为材料常数、为蠕变应变速率;b.材料常数k3设置为随温度而变化,具体为下述公式:其中,k
30
为材料常数,qa为相对应的激活能量;c.位错密度的演变方程为下述公式:为相对应的激活能量;c.位错密度的演变方程为下述公式:其中,k5、k6和m1为待拟合材料常数。
31.在该技术方案中,设立材料的蠕变变形模型,对各类温度及应力变化历程进行模拟预测,并对模型中随温度变化的材料常数k3及位错密度采用公式进行求解。
32.上述任一技术方案中,所述s5的步骤,具体包括:s501,对蠕变时效成形过程的析出相演变模型进行简化处理,仅考虑蠕变时效过程中材料内部析出相的形核以及生长阶段;s502,建立所述时效过程的微观结构演变影响下的材料屈服强度方程。
33.在该技术方案中,由于铝合金caf工艺过程一般需确保成形后材料性能为强化状态,因此其时效处理后多为峰值时效或近峰值状态。在此过程中材料内部析出相多处于形核与生长阶段,粗化部分较少,因此,在caf过程析出演变模型中做简化处理。仅考虑蠕变时效过程中材料内部析出相的形核以及生长阶段。
34.上述任一技术方案中,所述步骤s501,具体包括:a.析出相形核过程析出数量n演变方程,具体为下述公式:其中,z为铝的晶格常数、γ为析出比能量、v为铝的摩尔体积、k为波尔兹曼常数、c(t)为随时效时间变化的材料固溶度、ce为相应温度下平衡态下的固溶度、δg为吉布斯自由能、d
eff
为扩散常数;b.析出相形核及生长过程析出相等效尺寸演变方程,通过等效平均尺寸r代表材料内部析出相大小,具体为下述公式:其中,ci(r)为随析出相等效平均尺寸r变化的材料固溶度;c.基于上述获得的析出相数量及尺寸,采用下述公式计算析出体积分数:
其中,f为析出体积分数、n为单位体积内析出相的总数量;d.材料内部的固溶度,具体采用下述公式计算:其中,c0为铝合金中固溶原子初始固溶度。
35.在该技术方案中,扩散常数d
eff
修正为由材料自扩散能量以及沿位错线扩散能量的综合值;
36.在析出相形核过程中析出数量n演变方程中加入材料内部的固溶度c(t),可使得方程同时考虑温度对固溶演变影响。
37.上述任一技术方案中,所述步骤s502,具体包括:a.析出相强化σ
p
主要由析出相尺寸决定,方程具体为:其中,m为泰勒因子,取值为2、b为伯氏矢量,取值为0.28nm、l为析出相平均间距、f(r)为析出相第二相平均强度;b.固溶强化由固溶度决定,所述固溶强化的方程为:σ
ss
=c
ss
c(t)
2/3
;其中,c
ss
为材料常数,σ
ss
为固溶强化度;c.位错强化由位错密度决定,所述位错强化的方程为:其中,α为材料常数,σ
dis
为位错强化分量,g为剪切模量,ρ为位错密度;d.材料整体屈服强度计算方程,具体为:
38.在该技术方案中,析出相平均间距l可采用公式表达,具体为:其中,f为析出相体积分数;
39.f(r)根据析出相大小,其强化机理与表达形式均不一样,析出相较小时表现为剪切强化,析出相较大时表现为绕过强化机制,机制转变通过临界半径rc来表示,f(r)计算方程为:
[0040][0041]
其中,k、β为待确定常数,与临界半径关系为
[0042]
上述任一技术方案中,d
eff
定义为下述公式:定义为下述公式:其中,q
diff
为材料自扩散能量,q
pipe
为沿位错扩散能量,d0及d
p0
分别为扩散系数,通过查阅相应材料手册及文献获得。
[0043]
本发明与现有技术相比所具有的有益效果:
[0044]
现有描述蠕变时效行为的模型仅考虑单一温度下保温过程caf工艺变形及性能演变预测,无法实现对升温及降温阶段、变温caf等新型工艺中材料变形及性能的有效预测。
[0045]
主要原因在于现有模型未准确理解温度引起的材料变形及强化机理。
[0046]
本发明考虑温度影响下对材料激活能变化影响,从而实现对蠕变或应力松驰变形机理的理解与预测;同时考虑温度对析出相、固溶等演变影响,同步实现了考虑温度影响下的材料微观结构及其强化特性预测。
[0047]
开发的统一模型可实现升温-保温-降温全流程caf工艺以及变温caf新工艺形性协同预测,对caf工艺全流程及其改进高效率caf工艺精确预测及其构件制造的数值模拟均有重要指导意义。
[0048]
根据本发明的实施例的附加方面和优点将在下面的描述部分中变得明显,或通过根据本发明的实施例的实践了解到。
附图说明
[0049]
附图仅用于示出具体实施例的目的,而并不认为是对本发明的限制。
[0050]
图1为本发明的拉伸-连续短时应力松驰实验方法示意图;
[0051]
图2为本发明的应力松驰 拉伸-连续短时应力松驰实验方法示意图;
[0052]
图3为本发明的不同温度下铝锌镁合金中有效应力分量计算及其结果曲线示意图;
[0053]
图4为本发明的不同温度下铝锌镁合金中激活能演变实验和预测数据曲线示意图;
[0054]
图5为本发明的不同温度下、不同应力等级下实验和预测的铝锌镁合金应力松驰曲线示意图;
[0055]
图6为本发明的不同温度下、不同应力等级下实验和预测的铝锌镁合金强度曲线示意图;
[0056]
图7为本发明的特定变温蠕变时效路径下铝锌镁合金温度及强度变化预测曲线示意图;
[0057]
图8为本发明的特定变温蠕变时效路径下铝锌镁合金温度及蠕变应变变化预测曲线示意图。
具体实施方式
[0058]
为了可以更清楚地理解本发明的上述目的、特征和优点,下面结合附图和具体实施方式对本发明进行进一步的详细描述。需要说明的是,在不冲突的情况下,本技术的实施例及实施例中的特征可以相互组合。
[0059]
在下面的描述中阐述了很多具体细节以便于充分理解本发明,但是,本发明还可以采用其他不同于在此描述的其他方式来实施,因此,本发明的保护范围并不受下面公开的具体实施例的限制。
[0060]
实施例1
[0061]
本发明第一方面的实施例,如图1-8所示,提供基于一种考虑温度历程的铝合金蠕变时效形性协同预测方法。本实例所用样品为商用7b04铝锌镁合金,其中,该方法包括:
[0062]
步骤一:在带加热炉的单向拉伸试验机上进行不同温度下(115℃、140℃、165℃)材料单轴拉伸至不同应力等级下的连续短时应力松驰实验,如图1所示,过程如下:
[0063]
1)以应变速率5x10-4
/s单向拉伸至指定应力等级(弹性区域:200mpa,300mpa,350mpa)或应变等级(塑性区域:1%.2%,6%)后,试验机横梁停止运动,保持30s进行应力松驰,试验机记录应力随时间降低数据;而后以应变速率10-2
/s快速加载至原应力等级,试验机横梁随即停止运动,再次进行30s短时应力松驰,记录应力随时间变化数据;依次重复
进行三次短时应力松驰实验;
[0064]
2)而后材料继续以准静态拉伸,直至拉伸至下一级指定应力等级或应变等级(200mpa,300mpa,350mpa,1%.2%,6%),重复开展三次短时应力松驰实验;
[0065]
3)重复上述过程,直至拉伸达到最大指定塑性应变等级(6%),结束实验;
[0066]
步骤二:在带加热炉的单向拉伸试验机上进行不同温度下(115℃、140℃、165℃)材料应力松驰实验,在达到指定应力松驰时间后(0.5min,10min,30min,2h,4h),卸载力;而后参考步骤一中具体方案,开展此状态下材料的单向拉伸 连续短时应力松驰实验,如图2所示,获取材料在不同应力松驰时效状态后的连续短时应力松驰实验数据。
[0067]
步骤三:分析并计算获得铝合金材料在不同温度及不同应力或应变等级下材料的变形激活能q,过程如下:
[0068]
1)基于上述不同材料状态、不同温度、不同变形等级下获得的三次短时应力松驰曲线中的第一次应力松驰曲线数据,利用如下方程进行拟合,获得此材料状态、此温度及变形等级下内应力分量σi:
[0069][0070]
其中t为应力松驰时间,σ0为初始应力等级,σ为随时间变化的应力数据,a和b为待拟合常数;σi为内应力分量,其与有效应力σe共同组成整体应力,表示为σ=σi σe,如图3所示;
[0071]
2)基于上述不同材料状态、不同温度、不同变形等级下获得的三次短时应力松驰曲线,提取第一次应力松驰结束时的应变速率以及后续快速加载后第二次应力松驰开始时的应变速率,利用下述方程,拟合获得此状态下材料的激活体积数据v:
[0072][0073]
其中t为温度,为第二次应力松驰开始时的应变速率,为第一次应力松驰结束时的应变速率,δσ为第一次应力松驰过程整体应力变化量,c为待拟合常数。
[0074]
3)基于上述获得的不同状态下材料的内应力分量σi,有效内应力分量σe,以及激活体积v,通过q=(δg
0-vσe)获得铝合金在不同应力松驰时间、温度及变形状态下的激活能q,其中,δg0为材料在绝对零度下的吉布斯自由能,v为激活体积,σe为有效内应力分量;如图4所示。
[0075]
步骤四:建立考虑不同温度及变形等级影响下的激活能变化模型,以及考虑激活能变化的铝合金蠕变变形模型,过程如下:
[0076]
1)材料激活能受不同温度及变形状态的影响,建立激活能随温度以及应力松驰过程中变形状态下的模型。激活能随温度变化q0(t)模型为:
[0077]
q0(t)=(1-k1t/tm)q0[0078]
其中tm为材料融化温度,q0为参考激活能,k1为材料常数,通过上述不同应力松驰温度下获得的激活能数据拟合获得,见表1,预测结果如图4所示。另外激活能随变形变化模型为:
[0079][0080]
其中,k2为常数,通过上述不同应力松驰时间下获得的激活能数据拟合获得,见表1。
[0081]
2)建立考虑激活能变化的铝合金蠕变变形材料模型,通过上述激活能随时间、温度以及变形等级的变化,实现该蠕变变形方程对各类温度及应力变化历程的模拟预测,过程如下:
[0082]
a)蠕变变形模型为:
[0083][0084]
其中为位错密度,r为空气常数,k3,k4为材料常数。
[0085]
b)上述蠕变模型中,材料常数k0设置为随温度而变化,表述为:
[0086][0087]
其中,k
30
为材料常数,qa为相对应的激活能量;
[0088]
c)蠕变时效过程中位错密度演变方程为:
[0089][0090]
其中k5,k6,m1为待拟合常数。
[0091]
步骤五:建立基于铝合金析出动力学以及应力耦合影响下的考虑温度影响的铝合金析出相演变及其强化预测模型,过程如下:
[0092]
1)建立蠕变时效过程中材料内部析出相形核以及生长阶段相关模型,包括:
[0093]
a)析出相形核过程析出数量n演变方程:
[0094][0095][0096]
其中,z为铝的晶格常数,γ为析出比能量,v为铝的摩尔体积,k为波尔兹曼常数,c(t)为随时效时间变化的材料固溶度,ce为相应温度下平衡态下的固溶度,可由计算获得,其中c
e0
,qc由特定材料决定,见表2。d
eff
为扩散常数,考虑蠕变时效过程中应力与温度的耦合效应,d
eff
修正为由材料自扩散能量以及沿位错扩散能量的综合值,定义为:
[0097][0098]
其中q
diff
为材料自扩散能量,q
pipe
为沿位错扩散能量,d0及d
p0
分别为扩散系数,通过查阅相应材料手册及文献获得,见表2。
[0099]
b)析出相形核及生长过程析出相等效尺寸演变方程,通过等效平均尺寸r代表材料内部析出相大小:
[0100][0101][0102]
c)基于上述获得的析出相数量及尺寸,计算析出体积分数为:
[0103][0104]
d)进一步计算材料内部固溶度为:
[0105][0106]
2)建立上述时效过程微观结构演变影响下的材料屈服强度方程,包括:
[0107]
a)析出相强化σ
p
主要由析出相尺寸决定,其方程为:
[0108][0109]
其中m为泰勒因子,取值为2;b为伯氏矢量,取值为0.28nm;l为析出相平均间距,表示为f(r)为析出相第二相平均强度,计算方程为:
[0110][0111]
其中k,β为待确定常数,与临界半径关系为rc对于特定铝合金通过查阅相关文献获得,见表2。
[0112]
b)固溶强化方程为,σ
ss
=c
ss
c(t)
2/3
,其中c
ss
为材料常数,σ
ss
为固溶强化度;
[0113]
c)位错强化方程为,其中α为材料常数,其中,α为材料常数,σ
dis
为位错强化分量,g为材料剪切模量,ρ为位错密度;
[0114]
d)材料整体屈服强度计算方程为,
[0115]
步骤六:在带加热炉的单向拉伸试验机上开展不同温度(115℃、140℃、155℃、165℃、175℃)及不同应力等级下(200mpa、250mp、300mpa、370mpa、390mpa、410mpa)应力松驰实验,获得相应温度和应力等级下材料的应力松驰曲线以及性能演变曲线数据,见图5与图6。
[0116]
步骤七:基于实验数据,开展上述方程参数拟合校准及验证。基于三个不同应力等级下(250mp、300mpa、370mpa)应力松驰及屈服强度演变数据,采用粒子群优化算法,对上述蠕变及屈服强度方程进行拟合,校准获得其中非温度相关的材料常数,见表1;进一步基于三个不同温度(115℃、140℃、165℃)同应力等级(250mpa)下应力松驰及屈服强度演变数
据,对上述材料温度相关的材料常数进行拟合与校准,获得全部所需要材料常数。利用其它温度及应力等级数据对获得的材料常数进行验证,验证相关材料常数和方程的有效性,预测结果如图5和图6所示。
[0117]
利用上述拟合并验证后的材料模型以及材料常数,即可对不同温度历程下材料蠕变/应力松驰时效过程蠕变变形/应力松驰及时效强化演变进行模拟预测,如图7和8所示。
[0118]
表1:拟合获得的材料常数
[0119]
k1(-)k2(-)k
30
(s-1
)k4(mpa-1
)k5(s-1
)k6(s-1
)qa(kj/mol)m1(-)0.710.910.040.0282200.02120.701.02tm(k)q0(kj/mol)γ(j/m2)d0(m2/s)d
p0
(m2/s)c
ss
(mps)β(-) 930234.700.150.6*10-8
1*10-8
8400.36 [0120]
表2:依据7b04铝锌镁材料特性查阅资料及参考文献获得的材料常数
[0121][0122]
以上所述的实施例仅是对本发明的优选方式进行描述,并非对本发明的范围进行限定,在不脱离本发明设计精神的前提下,本领域普通技术人员对本发明的技术方案做出的各种变形和改进,均应落入本发明权利要求书确定的保护范围内。
再多了解一些
本文用于创业者技术爱好者查询,仅供学习研究,如用于商业用途,请联系技术所有人。