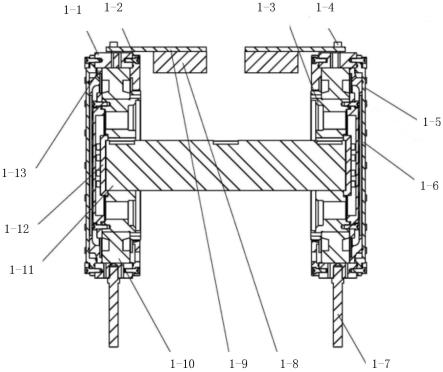
1.本发明涉及一种新型船舶滚动轴承常规寿命试验装置,属于船舶滚动轴承技术领域。
背景技术:
2.船舶滚动轴承具有尺寸大、受力复杂、滑油温度高等特点。目前,针对汽车轴承、轨道交通轴承国内已开发少量轴承试验设备,对轴向径向加载试验的大尺寸段船舶滚动轴承来说,尚未建立成熟的工况模拟寿命试验方法和装置。
3.本发明提出一种新型船舶滚动轴承常规寿命试验方法及装置,模拟船舶滚动轴承的载荷谱、转速谱、润滑、温度等试验参数,结合船舶滚动轴承的应用工况,开展船舶滚动轴承工况模拟寿命试验技术研究。
技术实现要素:
4.本发明专利涉及一种新型船舶滚动轴承常规寿命试验装置。
5.本发明的目的是这样实现的:包括驱动部件、试验单元、加载单元、润滑单元的四个部分,这种新型滚动轴承常规寿命试验装置是用于大型滚动轴承寿命试验。驱动部件为用变频器控制变频电机实现无级变速,通过多楔带与传动系统相连;加载单元采用新型伺服泵液压加载系统,实现对试验轴承的径向、轴向精准加载,通过油压传感器监控试验轴承所受的径向、轴向载荷,传感器与伺服泵形成闭环控制;润滑单元采用新型滚动轴承润滑系统,采用可编程控制系统实现对润滑流量、压力和高温加热的闭环控制及数据的实时监控;实验单元包括轴承座1-1、内端盖1-2、试验轴1-3、螺钉1-4、喷油盖1-5、内圈压盖1-6、拉杆1-7、限位块1-8、限位板1-9、试验轴承1-10、试验主轴1-11、轴头压盖1-12、外圈压盖1-13;试验轴承通过过渡配合套装在试验主轴1-11上,并由轴承压盖1-12通过螺钉将其轴向压紧在试验主轴1-11上,试验主轴1-11和试验轴1-3之间设置平键,试验轴承1-12的内圈通过过盈配合套装在试验轴(1-3)上,试验轴承1-10的内圈通过过盈配合套装在试验轴1-3上,试验轴承1-10的外圈通过间隙配合套装在轴承座1-1内,并由内端盖1-2和外圈压盖1-13通过螺钉从两侧将其压紧固定在轴承座1-1中;外圈压盖1-13与试验轴承1-10之间设置有喷油盖1-5;轴承座1-1上方设置有限位板1-9,通过限位螺钉1-4限制轴承座1-1发生旋转、偏摆或者轴向窜动,限位板1-9通过限位块1-8与床身部件固定连接;轴承座1-1通过其下方的拉杆1-7与加载机构相连。试验时,驱动部件和加载单元通过试验主轴1-11经试验轴1-3驱动试验轴承1-10的外圈施加径向力,润滑单元通过外圈压盖1-13经喷油盖1-5对试验轴承1-10进行喷油润滑。
6.进一步地,加载单元包括油箱2-1、过滤器2-2、油泵2-3、压力表2-4、安全阀2-5、单向阀2-6、电磁调压阀2-7、两位两通阀2-8、三位四通阀2-9、径向油缸2-10、轴向油缸2-11,油箱2-1储存油源,油泵2-3提供伺服系统动力源,过滤器2-2保证供油油路清洁防止油泵2-3堵塞,压力表2-4监测进油压力,安全阀2-5保证进油压力同时将多余油返回油箱,压力表
2-4和安全阀2-5实现稳定油压输出,单向阀2-6防止进油管路逆流,油路分为径向加载油路和轴向加载油路;电磁调压阀2-7接受信号控制油路通过与关闭,对供油压力精准控制;两位两通阀2-8控制是否实现压力监测;三位四通阀2-9实现正向加载和反向加载;径向油缸2-10和轴向油缸2-11对滚动轴承的径向、轴向进行加载。
7.进一步地,润滑单元包括油箱3-1、溢流阀3-2、节流阀3-3、流量计3-4、两位三通阀3-5、管路3-6、截止阀3-7、试验工装3-8、温度计3-9、加热器3-10、风冷却器3-11、压力表3-12、变频泵3-13、过滤器3-14、单向阀3-15、油冷却器3-16、油尺3-17,油箱3-1储存油源,油尺3-17对油箱油量进行监测;变频泵3-13提供伺服系统进油动力源和回油动力源;过滤器3-14保证供油油路清洁防止变频泵堵塞;节流阀3-3实现油路流量调节;流量计3-4对油路进行流量监测;溢流阀3-2失效油路压力调节,并将多余油返回油箱;压力表3-12对油路进行压力监测;两位三通阀3-5实现油路直接供给试验工装3-8或者对油路进行加热后供给试验工装。加热器3-10对油路进行温度调节,温度计3-9对温度进行监测,满足试验工装温度后截止阀3-7打通实现油路供给;风冷却器3-11和油冷却器3-16分别对回油管路和油箱实现冷却作用,单向阀3-15防止进油管路逆流,保护变频泵。
8.与现有技术相比,本发明的有益效果是:本发明根据轴承实际载荷工况进行模拟。通过设计试验轴和试验主轴,可以通过对试验轴尺寸的修改,适用于不同尺寸滚动轴承的安装。通过轴承座和内端盖内设置油道,与滚动轴承实际运行状况完全一致。试验主轴与驱动部件相连,提供试验装置的动力。
9.根据轴承实际载荷工况进行模拟。通过设计试验轴和试验主轴,可以通过对试验轴尺寸的修改,适用于不同尺寸滚动轴承的安装。通过轴承座和内端盖内设置油道,与滚动轴承实际运行状况完全一致。试验主轴与驱动部件相连,提供试验装置的动力。油泵2-3提供伺服系统动力源,采用压力表2-4和安全阀2-5实现稳定油压输出。采用径向油缸和轴向油缸2-10对滚动轴承的径向、轴向进行加载,控制精度高、操作灵活。采用电磁调压阀2-7对供油压力精准控制,实现滚动轴承精准加载。采用三位四通阀2-9实现正向加载和反向加载。根据轴承实际载荷工况提供润滑。润滑系统中采用变频泵3-13,润滑系统中供油压力和流量可以分别进行调节。润滑管路采用加热器3-10实现对轴承供油时温度调节。润滑系统分别采用风冷却器3-11和油冷却器3-16,分别对回油管路和油箱实现冷却作用。
附图说明
10.图1是本发明的结构示意图。
11.图2是本发明伺服泵加载系统图。
12.图3是本发明润滑系统图。
13.图1中:试验单元包括:轴承座1-1、内端盖1-2、试验轴1-3、螺钉1-4、喷油盖1-5、内圈压盖1-6、拉杆1-7、限位块1-8、限位板1-9、试验轴承1-10、试验主轴1-11、轴头压盖1-12、外圈压盖1-13。
14.图2中:加载单元包括:油箱2-1、过滤器2-2、油泵2-3、压力表2-4、安全阀2-5、单向阀2-6、电磁调压阀2-7、两位两通阀2-8、三位四通阀2-9、径向油缸2-10和轴向油缸2-11。
15.图3中:润滑单元包括:油箱3-1、溢流阀3-2、节流阀3-3、流量计3-4、两位三通阀3-5、管路3-6、截止阀3-7、试验工装3-8、温度计3-9、加热器3-10、风冷却器3-11、压力表3-12、
变频泵3-13、过滤器3-14、单向阀3-15、油冷却器3-16、油尺3-17。
具体实施方式
16.下面结合附图与具体实施方式对本发明作进一步详细描述。
17.本发明包括驱动部件、试验单元、加载单元、润滑单元的四个部分,根据轴承实际载荷工况进行模拟。通过设计试验轴和试验主轴,可以通过对试验轴尺寸的修改,适用于不同尺寸滚动轴承的安装。通过轴承座和内端盖内设置油道,与滚动轴承实际运行状况完全一致。试验主轴与驱动部件相连,提供试验装置的动力。试验单元的试验主轴两端堆成设置两个试验工位。
18.①
驱动部件。驱动部件为用变频器控制变频电机实现无级变速,通过多楔带与传动系统相连。
19.②
试验单元。针对大型滚动轴承尺寸,设计专用新型大型滚动轴承寿命试验工装,使其匹配本项目试验轴承的尺寸段。
20.③
加载单元。采用新型伺服泵液压加载系统,实现对试验轴承的径向、轴向精准加载,通过油压传感器监控试验轴承所受的径向、轴向载荷,传感器与伺服泵形成闭环控制,实现精确控制。
21.④
润滑单元。采用新型滚动轴承润滑系统,采用可编程控制系统实现对润滑流量、压力和高温加热的闭环控制及数据的实时监控。每一管路配置独立电机泵组、流量计等元件,以实现流量精确控制,同时满足后期扩展需求。轴承试验机润滑油高温加热,整体设计为一体化,可移动。每套试验轴承的流量可自动调整,计算机显示流量值,并可自动控制流量。润滑油压力可自动调整,计算机显示。油润滑加热可通过计算机自动控制,控制精度≤
±
1.5℃。润滑油温度保持恒温功能,油箱采用不锈钢材料。试验单元的润滑油通过回油泵抽回油箱,并配以风冷却和水冷却器。润滑油箱及管路采用不锈钢材料,耐压强度》4.0mpa,外配隔热保温和防漏油装置。系统能模拟润滑条件,显示供油温度、流量、压力、回油温度、油箱温度等。润滑油箱装有液位传感器和油标指示器,当润滑油箱油量不足时,具有报警指示及信号输出功能,供油和回油管路都应装有过滤器,供油管路装有流量计、温度计、压力表和阀门开关等,过滤器装有油滤堵塞报警装置。
22.本发明的一种新型船舶滚动轴承常规寿命试验方法及装置的试验单元根据轴承实际载荷工况进行模拟。通过设计试验轴和试验主轴,可以通过对试验轴尺寸的修改,适用于不同尺寸滚动轴承的安装。通过轴承座和内端盖内设置油道,与滚动轴承实际运行状况完全一致。试验主轴与驱动部件相连,提供试验装置的动力。试验单元的试验主轴两端堆成设置两个试验工位。试验轴承通过过渡配合套装在试验主轴1-11上,并由轴承压盖1-12通过螺钉将其轴向压紧在试验主轴1-11上,试验主轴1-11和试验轴1-3之间设置平键,以便将试验主轴1-11的旋转运动传递给试验轴1-3。试验轴承1-12的内圈通过过盈配合套装在试验轴(1-3)上,试验轴承1-10的内圈通过过盈配合套装在试验轴1-3上,试验轴承1-10的外圈通过间隙配合套装在轴承座1-1内,并由内端盖1-2和外圈压盖1-13通过螺钉从两侧将其压紧固定在轴承座1-1中。外圈压盖1-13与试验轴承1-10之间设置有喷油盖1-5。轴承座1-1上方设置有限位板1-9,通过限位螺钉1-4限制轴承座1-1发生旋转、偏摆或者轴向窜动,限位板1-9通过限位块1-8与床身部件固定连接;轴承座1-1通过其下方的拉杆1-7与加载机构
相连。试验时,驱动机构通过试验主轴1-11经试验轴1-3驱动试验轴承1-10的外圈施加径向力,润滑装置通过外圈压盖1-13经喷油盖1-5对试验轴承1-10进行喷油润滑。
23.一种新型船舶滚动轴承常规寿命试验方法及装置的加载单元:加载单元包括油箱2-1、过滤器2-2、油泵2-3、压力表2-4、安全阀2-5、单向阀2-6、电磁调压阀2-7、两位两通阀2-8、三位四通阀2-9、径向油缸2-10、轴向油缸2-11,油箱2-1储存油源。油泵2-3提供伺服系统动力源。过滤器2-2保证供油油路清洁防止油泵2-3堵塞。压力表2-4监测进油压力。安全阀2-5保证进油压力同时将多余油返回油箱。采用压力表2-4和安全阀2-5实现稳定油压输出。单向阀2-6防止进油管路逆流。此时油路分为径向加载油路和轴向加载油路。电磁调压阀2-7接受信号控制油路通过与关闭,对供油压力精准控制。两位两通阀2-8控制是否实现压力监测。采用三位四通阀2-9实现正向加载和反向加载。采用径向油缸2-10和轴向油缸2-11对滚动轴承的径向、轴向进行加载,控制精度高、操作灵活。
24.一种新型船舶滚动轴承常规寿命试验方法及装置的润滑单元:润滑单元包括油箱3-1、溢流阀3-2、节流阀3-3、流量计3-4、两位三通阀3-5、管路3-6、截止阀3-7、试验工装3-8、温度计3-9、加热器3-10、风冷却器3-11、压力表3-12、变频泵3-13、过滤器3-14、单向阀3-15、油冷却器3-16、油尺3-17,油箱3-1储存油源,油尺3-17对油箱油量进行监测。变频泵3-13提供伺服系统进油动力源和回油动力源。过滤器3-14保证供油油路清洁防止变频泵堵塞。节流阀3-3实现油路流量调节;流量计3-4对油路进行流量监测。溢流阀3-2失效油路压力调节,并将多余油返回油箱;压力表3-12对油路进行压力监测。两位三通阀3-5实现油路直接供给试验工装3-8或者对油路进行加热后供给试验工装。加热器3-10对油路进行温度调节,温度计3-9对温度进行监测,满足试验工装温度后截止阀3-7打通实现油路供给。润滑系统分别采用风冷却器3-11和油冷却器3-16,分别对回油管路和油箱实现冷却作用。单向阀3-15防止进油管路逆流,保护变频泵。
再多了解一些
本文用于创业者技术爱好者查询,仅供学习研究,如用于商业用途,请联系技术所有人。