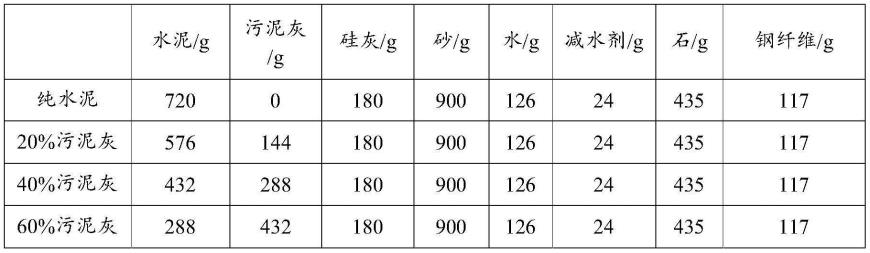
1.本发明涉及水泥基复合材料相关技术领域,具体地说是涉及一种利用污泥灰制备的水泥基复合材料及其制备方法。
背景技术:
2.污泥是污水经处理后的产物,特点是含水率极高且含有大量有机物。根据《住房和城乡建设部城乡建设统计年鉴》,2020年,我国污泥(按含水率80%计算),达到7168万吨,预计到2060年可达到7亿吨。
3.作为污泥处理的有效手段,焚烧可实现污泥的减量化,方便污泥的后续处理。污泥焚烧的基本原理是在高温条件下,使存在于污泥中的有机成分全部分解成二氧化碳、水等小分子气相物质。相比于污泥其他处理方式,焚烧处理的优势包括以下几点:第一,使得污泥中有机质得到最彻底的分解,消除了有机物对环境潜在的威胁;第二,减少污泥的体积,方便处置;第三,处置时间较短,不会造成污泥长期的堆存。
4.火力发电作为我国主要发电形式,对我国发展起着举足轻重的作用。但火力发电存在一些弊端,首先,燃煤会产生大量的so2等酸性气体,引发酸雨,造成烟气污染;同时,由于火力发电的主要燃烧物为煤炭,煤炭资源作为不可再生资源,大量燃煤造成资源的浪费,不利于可持续发展。
5.为了减少火力发电中煤的消耗,实现火力发电的可持续发展,燃煤耦合污泥燃烧技术越来越受到人们的关注。干化后的污泥用于电厂燃煤锅炉焚烧,不仅减少了煤的消耗,同时,实现了污泥的有效处置。
6.但现有技术中,污泥经焚烧后产生的污泥灰主要处置方式为填埋处置,填埋处置不仅占用大量土地资源,同时,污泥灰中含有大量重金属物质,若处理不当,污泥灰内的重金属物质会对周边土壤及地下水造成污染。因此,实现污泥灰资源化再利用具有重要意义。
技术实现要素:
7.针对现有技术之不足,本发明的一个方面公开了一种利用污泥灰制备水泥基复合材料的方法。
8.所述利用污泥灰制备水泥基复合材料的方法主要为:将普通硅酸盐水泥中20%-60%的水泥熟料等质量替换为污泥灰,即制得该利用污泥灰制备水泥基复合材料。
9.根据本发明的一个优选实施方式,将普通硅酸盐水泥中20%的水泥熟料等质量替换为污泥灰,即制得该利用污泥灰制备的水泥基复合材料。
10.根据本发明的一个优选实施方式,将普通硅酸盐水泥中40%的水泥熟料等质量替换为污泥灰,即制得该利用污泥灰制备的水泥基复合材料。
11.根据本发明的一个优选实施方式,将普通硅酸盐水泥中60%的水泥熟料等质量替换为污泥灰,即制得该利用污泥灰制备的水泥基复合材料。
12.根据本发明的一个优选实施方式,所述污泥灰为污泥燃煤耦合后产生的污泥灰。
13.根据本发明的一个优选实施方式,所述污泥灰的粒径小于0.1mm。
14.根据本发明的一个优选实施方式,所述污泥灰中石英含量为46wt%;所述污泥灰中氧化铝的含量27wt%;所述污泥灰中氧化钙的含量9wt%;所述污泥灰中三氧化二铁9wt%。
15.本发明的另一个方面公开了一种利用污泥灰制备的水泥基复合材料。
16.所述利用污泥灰制备的水泥基复合材料由如上任意一项所述的利用污泥灰制备水泥基复合材料的方法制备而成。
17.与现有技术相比,本发明实施例的利用污泥灰制备的水泥基复合材料具有如下有益效果:
18.本发明实施例的利用污泥灰制备的水泥基复合材料将污泥灰进行筛分后,作为水泥掺合料部分替代水泥熟料,然后将得到的掺污泥灰的水泥基复合材料制成所需的制品。与原有技术相比,首先,本发明充分实现污泥灰的资源化利用,减少水泥用量,水泥替代率最高可达60%以上;其次,污泥灰无需经过其他处理方式,仅需进行简单筛分处理,并未使用和产生对环境有害的物质,资源化利用方便,可操作性和可复制性强,耗能低,符合绿色环保的要求;最后,将污泥灰用于水泥基材料,由于水泥的固化作用,可减少污泥灰内重金属对环境的影响。因此,将污泥灰作为水泥掺和料,首先,可以减少水泥用量,从而减少碳排放和能源消耗;其次,由于水泥基材料的固化作用,可将污泥灰内的重金属固化于水泥基材料内部,实现污泥灰的无害化处置;最后,可以实现污泥灰的资源化利用,保护环境,节约土地资源。
19.另外,根据gb/t17671-1999《水泥胶砂强度检验方法(iso法)》和gb/t2419-2005《水泥胶砂流动度测定方法》,掺污泥灰的超高性能混凝土经过蒸压养护后,即使替代率达到60%,2天的抗压强度仍能达到150mpa以上,2天的抗折强度与不掺污泥灰的对照组相比,基本持平,满足超高性能混凝土对掺污泥灰水泥作为胶凝材料的强度的要求;工作性能随着污泥灰替代率的增加,有一定程度的改善,当替代率达到60%时,工作性能改善10%。
20.本发明的一部分附加特性可以在下面的描述中进行说明。通过对以下描述和相应附图的检查或者对实施例的生产或操作的了解,本发明的一部分附加特性对于本领域技术人员是明显的。本发明披露的特性可以通过对以下描述的具体实施例的各种方法、手段和组合的实践或使用得以实现和达到。
附图说明
21.在此所述的附图用来提供对本发明的进一步理解,构成本发明的一部分,本发明的示意性实施例及其说明用于解释本发明,并不构成对本发明的限定。在各图中,相同标号表示相同部件。其中,
22.图1是根据本发明的一些实施例所示的利用污泥灰制备水泥基复合材料的方法的流程示意图;
23.图2是根据本发明的一些实施例所示的利用污泥灰制备的水泥基复合材料不同替代率的流动度的示意图;
24.图3是根据本发明的一些实施例所示的利用污泥灰制备的水泥基复合材料不同替代率的抗压强度的示意图;
25.图4是根据本发明的一些实施例所示的利用污泥灰制备的水泥基复合材料不同替代率的抗折强度的示意图。
具体实施方式
26.为了使本技术领域的人员更好地理解本发明方案,下面将结合本发明实施例中的附图,对本发明实施例中的技术方案进行清楚、完整地描述,显然,所描述的实施例仅仅是本发明一部分的实施例,而不是全部的实施例。基于本发明中的实施例,本领域普通技术人员在没有做出创造性劳动前提下所获得的所有其他实施例,都应当属于本发明保护的范围。
27.需要说明的是,在不冲突的情况下,本发明中的实施例及实施例中的特征可以相互组合。
28.下面将参考附图并结合实施例来详细说明本发明。
29.本发明实施例的一个方面公开了一种利用污泥灰制备水泥基复合材料的方法。
30.如图1所示,该利用污泥灰制备水泥基复合材料的方法主要包括:将普通硅酸盐水泥中20%-60%的水泥熟料等质量替换为污泥灰,即制得该利用污泥灰制备的水泥基复合材料。
31.例如,可以将普通硅酸盐水泥中20%的水泥熟料等质量替换为污泥灰,即制得该利用污泥灰制备的水泥基复合材料。
32.又例如,可以将普通硅酸盐水泥中40%的水泥熟料等质量替换为污泥灰,即制得该利用污泥灰制备的水泥基复合材料。
33.再例如,可以将普通硅酸盐水泥中60%的水泥熟料等质量替换为污泥灰,即制得该利用污泥灰制备的水泥基复合材料。
34.其中,污泥灰可以采用污泥燃煤耦合后产生的污泥灰。污泥灰中石英含量为46wt%;污泥灰中氧化铝的含量27wt%;污泥灰中氧化钙的含量9wt%;污泥灰中三氧化二铁9wt%。
35.具体的,通过x射线衍射(x-ray diffraction,简称xrd)分析和x射线荧光光谱(x-ray fluorescence,简称xrf)分析污泥灰中的矿物组成成分,分析结果得出:污泥灰中主要含有46wt%石英、27wt%氧化铝、9wt%氧化钙、9wt%三氧化二铁。由于污泥灰是污泥高温处理后得到的,处理温度达到1000℃以上,高温处理使得污泥灰内的石英、氧化铝等含有大量活性,因此具有一定的火山灰效应以及填充效应,可在一定程度上加快水泥水化速度,同时其填充效应可在一定程度提高超高性能混凝土内部结构致密性。本发明实施例便是基于此机理对污泥燃煤耦合后产生的污泥灰进行资源化利用,达到减少水泥用量的目的。
36.其中,污泥灰的粒径小于0.1mm。具体的,将污泥灰进行筛分,保证所有颗粒均可通过0.1mm的筛网,粒径均小于0.1mm。
37.本发明实施例的另一个方面公开了一种利用污泥灰制备的水泥基复合材料。
38.该利用污泥灰制备的水泥基复合材料由上述利用污泥灰制备水泥基复合材料的方法制备而成。
39.下面通过具体实施例说明本发明实施例的利用污泥灰制备的水泥基复合材料的性能。
40.具体的,将筛分后污泥灰作为水泥掺合料,分别以20%、40%、60%的替代率等质量替代水泥熟料(根据《gb175-2007通用硅酸盐水泥》规范中的42.5r普通硅酸盐水泥,化学成分如表1所示)后,得到掺污泥灰水泥,作为制备超高性能混凝土的胶凝材料。
41.表1水泥熟料化学成分
42.化学成分sio2al2o3caofe2o3mgoso3其他质量分数(%)23.06.062.54.30.91.12.2
43.根据gb/t17671-1999《水泥胶砂强度检验方法(iso法)》,用污泥灰制备掺污泥灰超高性能混凝土,水泥熟料制备纯水泥超高性能混凝土,配合比如表2所示。
44.表2掺污泥灰超高性能混凝土配合比设计
[0045][0046]
超高性能混凝土尺寸为40mm
×
40mm
×
160mm的棱柱体,具体制备流程如下:
[0047]
1、配料:按表2中的配比准备好对应质量的水泥、污泥灰、硅灰、水、减水剂、砂、石、钢纤维;
[0048]
2、搅拌:首先将水泥、硅灰、砂、石(纯水泥超高性能混凝土)或水泥、硅灰、污泥灰、砂、石(掺污泥灰超高性能混凝土)倒入搅拌锅中,把搅拌锅放在搅拌机的固定架上,上升至固定位置;启动搅拌机,低速搅拌240s后,将水和减水剂混合搅拌均匀,先倒入70%的水和减水剂,搅拌120s,再将剩余的30%水和减水剂倒入搅拌锅中,搅拌120s;搅拌完成后,将钢纤维缓慢加入搅拌锅中,加入钢纤维后,把机器转至高速搅拌,搅拌时间为300s。各个搅拌阶段,时间误差应在
±
1s以内;
[0049]
3、测试流动度:跳桌第一次使用时先空跳一个周期25次,随后将拌好的浆体分两层迅速装入试模(由截锥圆模和模套组成。金属材料制成,内表面加工光滑。圆模尺寸为:高度60mm士0.5mm;上口内径70mm士0.5mm;下口内径100mm士0.5mm;下口外径120mm;模壁厚大于5mm。),第一层装至截锥圆模高度约三分之二处,用小刀在相互垂直两个方向各划5次,用捣棒由边缘至中心均匀捣压15次;随后,装第二层胶砂,装至高出截锥圆模约20mm,用小刀在相互垂直两个方向各划5次,再用捣棒由边缘至中心均匀捣压10次。捣压后胶砂应略高于试模。捣压深度,第一层捣至胶砂高度的二分之一,第二层捣实不超过已捣实底层表面。装胶砂和捣压时,用手扶稳试模,不要使其移动。捣压完毕,取下模套,将小刀倾斜,从中间向边缘分两次以近水平的角度抹去高出截锥圆模的浆体,并擦去落在桌面上的浆体。将截锥圆模垂直向上轻轻提起。立刻开动跳桌,以每秒钟一次的频率,在25s
±
1s内完成25次跳动。
[0050]
4、用振动台成型:将搅拌锅内的浆体倒入40mm
×
40mm
×
160mm的棱柱体模具中,将模具放到振动台上,启动振动台;振动完毕后,取下棱柱体模具,用刮平尺刮去其高出试模的浆体并抹平;接着在试模上做标记或用字条表明试件编号;待浆体初凝后盖上塑料薄膜。
[0051]
5、拆模:试件静置24h后拆模;
[0052]
6、养护:养护方式采用蒸压养护,超高性能混凝土浇筑完成后24h拆模,拆模后样品放入蒸压釜中,以1.0mpa,180℃的条件,养护8小时,测定其2天的抗压与抗折强度。
[0053]
养护2天后,根据gb/t 17671-1999《水泥胶砂强度检验方法(iso法)》的要求测定超高性能混凝土强度。
[0054]
结果显示:流动度随着污泥灰替代率的增加,有一定程度的改善,当替代率达到60%时,工作性能改善10%以上,不同替代率的流动度如图2所示;掺污泥灰的超高性能混凝土经过蒸压养护后,即使替代率达到60%,2天的抗压强度仍能达到150mpa,2天的抗折强度与不掺污泥灰的对照组相比,基本持平,满足超高性能混凝土对掺污泥灰水泥作为胶凝材料的强度的要求,不同替代率的强度性能指标如图3、图4所示。
[0055]
本实施例中的钢纤维水泥基复合材料是一种高强度、高韧性、低孔隙率的超高强水泥基复合材料,其抗压强度最高可达800mpa。主要应用于高层建筑、大跨度结构等领域。但在钢纤维水泥基复合材料中,为了达到高强的目的,水泥通常为600kg/m3—1000kg/m3,大约是水泥基材料用量的两倍。水泥业是一个碳排放和能源消耗均很高的行业,水泥在生产过程中排放的co2占人类活动总co2排放的5%—8%,能源消耗占工业能源消耗的12%—15%。co2所产生的温室效应引起全球变暖,从而导致冰川融化海平面上升,土地荒漠化进一步加重,破坏地球生态平衡。
[0056]
本发明实施例将污泥灰作为水泥掺和料,首先,可以减少水泥用量,从而减少碳排放和能源消耗;其次,由于水泥基材料的固化作用,可将污泥灰内的重金属固化于水泥基材料内部,实现污泥灰的无害化处置;最后,可以实现污泥灰的资源化利用,保护环境,节约土地资源。
[0057]
需要注意的是,本说明书中公开的所有特征,或公开的所有方法或过程中的步骤,除了互相排斥的特征和/或步骤以外,均可以以任何方式组合。
[0058]
另外,上述具体实施例是示例性的,本领域技术人员可以在本发明公开内容的启发下想出各种解决方案,而这些解决方案也都属于本发明的公开范围并落入本发明的保护范围之内。本领域技术人员应该明白,本发明说明书及其附图均为说明性而并非构成对权利要求的限制。本发明的保护范围由权利要求及其等同物限定。
再多了解一些
本文用于创业者技术爱好者查询,仅供学习研究,如用于商业用途,请联系技术所有人。