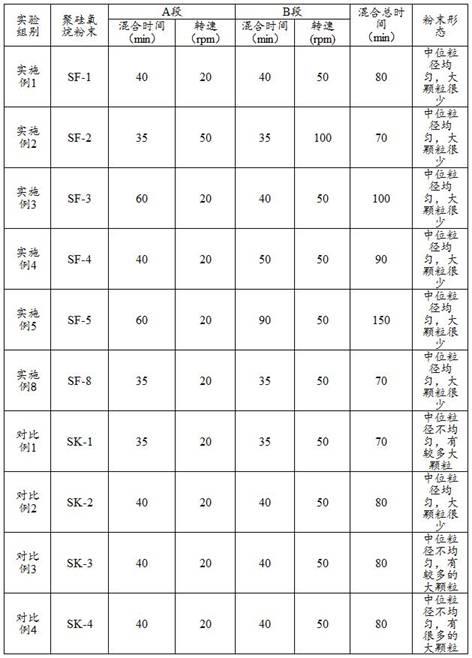
1.本发明涉及高分子材料的技术领域,具体而言,涉及一种超高分子量聚硅氧烷粉末及其制备方法。
背景技术:
2.聚硅氧烷因其独特的分子结构,具有分子链柔顺,极低的表面能,优良的耐高温、耐候性,相对低的反应性、惰性等特点,有机硅助剂作为热塑性塑料的一种加工助剂,较小的添加量,即可以达到明显的改性效果。
3.有机硅润滑剂是一种塑料润滑剂,包括硅酮母粒和硅酮粉,硅酮母粒是以聚硅氧烷为有活性成分,不同树脂为载体的母粒,硅酮母粒的出现克服了传统的有机硅塑料助剂与塑料难以均匀混合以及向制品表面迁移的缺点,容易添加;但是不同材料体系要选用不同载体的硅酮母粒,使得其应用范围受限。而聚硅酮粉即聚硅氧烷粉末是以聚硅氧烷为有活性成分,搭配二氧化硅或是其他无机填料制备而成的粉末,几乎适用于各种不同种类的热塑性树脂,而不用考虑适用的树脂载体。
4.聚硅氧烷粉末即硅酮粉是聚硅氧烷和二氧化硅组成的粉末,在其制备过程中,硅氧烷分子量越大,硅酮含量越高,其制备难度越大,现市面上普通的硅酮粉分子量均较低,且含量较低,在应用到热塑性树脂中,容易析出到制品表面,造成一系列的问题,应用受限。较低的硅酮含量导致可能引入过多的二氧化硅,也可能会给制品性能带来负面影响。
技术实现要素:
5.本发明的目的在于提供一种超高分子量聚硅氧烷粉末及其制备方法,其几乎适用于所有的热塑性树脂加工,能够提高热塑性树脂的加工流动性,且可以提高制品的表面爽滑性、降低表面摩擦系数以及改善耐磨耐刮性能。
6.本发明的实施例通过以下技术方案实现:本发明的超高分子量聚硅氧烷粉末的制备方法,包括如下制备步骤:(1)将二氧化硅a与聚硅氧烷加热混合,混合时间为35-60min;(2)向步骤(1)所获得的混合物中加入二氧化硅b,并继续混合均匀后捏合为粉体,混合时间为35-90min。
7.进一步地,各组分的质量份数为:聚硅氧烷30-70份,二氧化硅a 15-25份,二氧化硅b 25-55份。
8.进一步地,步骤(1)中二氧化硅a与聚硅氧烷混合温度为150-200℃,混合器的转速为20-50rpm;步骤(2)中混合器的转速为50-100rpm。其中升高混合器的温度从而使超高分子量聚硅氧烷粘度降低从而更易分散;先加入中位粒径大的二氧化硅增加与超高分子量聚硅氧烷的剪切,此时为低速混合,因为此时原料为胶状的硅氧烷和粉状的二氧化硅,低转速一是可以保证硅氧烷进入高结构性的粉体二氧化硅中,二是避免造成大的粉尘污染;第一步混合均匀后,再加入中位粒径小的二氧化硅进行二次分散从而保证超高分子量聚硅氧烷
在二氧化硅中分散均匀与彻底,此时需要高速混合,保证较大的剪切将步骤(1)中硅氧烷和二氧化硅的混合物和小中位粒径的二氧化硅能够混合均匀。
9.进一步地,步骤(1)中的所述聚硅氧烷为粘度为105~5
×
107mpa
·
s的线性聚硅氧烷,重均分子量为500000~1000000。
10.进一步地,步骤(1)中的所述二氧化硅a和步骤(2)中的所述二氧化硅b为使用表面改性剂对普通二氧化硅改性后所得到的。
11.进一步地,所述表面改性剂为氯硅烷类、偶联剂类、硅氧烷类化合物、醇酯类、有机酸、有机盐中的一种或多种。
12.更为具体地,所述偶联剂为硅烷偶联剂、钛酸酯偶联剂、铝酸酯偶联剂中的一种或多种。
13.进一步地,所述表面改性剂的用量为所述普通二氧化硅质量分数的0.1%~5%。
14.更为具体地,步骤(1)中的所述二氧化硅a的中位粒径为25~50μm,比表面积为100~200 m2/g,堆密度为0.2~0.4g/ml;步骤(2)中的所述二氧化硅b的中位粒径为1~5μm,比表面积为200~400 m2/g,堆密度为0.05~0.2g/ml。
15.本发明还提供了由上述超高分子量聚硅氧烷粉末的制备方法所制备得到的超高分子量聚硅氧烷粉末。
16.本发明实施例的技术方案至少具有如下优点和有益效果:本发明的超高分子量聚硅氧烷粉末的制备方法具有以下优势:1.普通二氧化硅表面含有大量羟基等极性基团,导致其极易吸附水分子、分散性较差、易发生二次聚集等问题,本发明通过将普通二氧化硅进行表面处理,使其与聚硅氧烷更好的相容分散。
17.2.通过制粉过程中工艺的配合,如升高混合器的温度从而使超高分子量聚硅氧烷粘度降低从而更易分散;先加入中位粒径大的二氧化硅增加与超高分子量聚硅氧烷的剪切,再加入中位粒径小的二氧化硅进行二次分散从而保证超高分子量聚硅氧烷在二氧化硅中分散均匀与彻底。
18.3.本发明的制备方法制备得到的无有机载体聚硅氧烷粉末,几乎适用于所有的热塑性树脂加工,能够提高热塑性树脂的加工流动性,且可以提高制品的表面爽滑性、降低表面摩擦系数以及改善耐磨耐刮性能等。
19.4.通过本发明的制备方法,可以制备得到超高分子量的聚硅氧烷粉末,同时方便根据具体的应用需求制备不同分子量,不同中位粒径分布的硅氧烷粉末产品。
具体实施方式
20.实施例1本实施例提供了一种超高分子量聚硅氧烷粉末制备方法,包括如下步骤:(1)将粘度为5
×
107mpa
·
s线性聚硅氧烷60份,二氧化硅a 20份于低速混合器中150℃混合40min(记为a段混合时间),混合器转速为20rpm。其中二氧化硅a中硅烷偶联剂的用量为普通二氧化硅用量的0.1%,二氧化硅a的中位粒径为25μm,比表面积为150m2/g,堆密度为0.2g/ml;
(2)向步骤(1)中的混合物中加入二氧化硅b 20份,继续在低速混合器中150℃混合40min(记为b段混合时间),混合器转速为50rpm;其中二氧化硅b中烷偶联剂的用量为普通二氧化硅用量的0.1%,二氧化硅b的中位粒径为5μm,比表面积为250m2/g,堆密度为0.05g/ml。制备的聚硅氧烷粉末记为sf-1。
21.实施例2本实施例提供了一种超高分子量聚硅氧烷粉末制备方法,其与实施例1的区别之处在于:a段混合时间35min,混合器转速为50rpm;b段混合时间35min,混合器转速为100rpm。制备的聚硅氧烷粉末记为sf-2。
22.实施例3本实施例提供了一种超高分子量聚硅氧烷粉末制备方法,其与实施例1的区别之处在于:a段混合时间60min。制备的聚硅氧烷粉末记为sf-3。
23.实施例4本实施例提供了一种超高分子量聚硅氧烷粉末制备方法,其与实施例1的区别之处在于:b段混合时间50min,制备的聚硅氧烷粉末记为sf-4。
24.实施例5本实施例提供了一种超高分子量聚硅氧烷粉末制备方法,其与实施例1的区别之处在于:a段混合时间60min,b段混合时间90min,制备的聚硅氧烷粉末记为sf-5。
25.实施例6本实施例提供了一种超高分子量聚硅氧烷粉末制备方法,包括如下步骤:(1)将粘度为5
×
107mpa
·
s线性聚硅氧烷30份,二氧化硅a 15份于低速混合器中150℃混合40min(记为a段混合时间);其中二氧化硅a中硅烷偶联剂的用量为普通二氧化硅用量的2.5%,二氧化硅a的中位粒径为30μm,比表面积为100m2/g,堆密度为0.3g/ml;(2)向步骤(1)中的混合物中加入二氧化硅b 25份,继续在低速混合器中150℃混合40min(记为b段混合时间)。其中二氧化硅b中烷偶联剂的用量为普通二氧化硅用量的2.5%,二氧化硅b的中位粒径为1μm,比表面积为400m2/g,堆密度为0.2g/ml。
26.实施例7本实施例提供了一种超高分子量聚硅氧烷粉末制备方法,包括如下步骤:(1)将粘度为5
×
107mpa
·
s线性聚硅氧烷70份,二氧化硅a 25份于低速混合器中150℃混合40min(记为a段混合时间);其中二氧化硅a中硅烷偶联剂的用量为普通二氧化硅用量的5%,二氧化硅a的中位粒径为50μm,比表面积为200m2/g,堆密度为0.4g/ml;(2)向步骤(1)中的混合物中加入二氧化硅b 55份,继续在低速混合器中150℃混合40min(记为b段混合时间)。其中二氧化硅b中烷偶联剂的用量为普通二氧化硅用量的5%,二氧化硅b的中位粒径为3μm,比表面积为200m2/g,堆密度为0.05g/ml。
27.实施例8本实施例提供了一种超高分子量聚硅氧烷粉末制备方法,其与实施例1的区别之处在于:低速混合器中的温度为200℃,a段混合时间35min,b段混合时间35min。制备的聚硅氧烷粉末记为sf-8实施例9本实施例提供了一种超高分子量聚硅氧烷粉末制备方法,其与实施例1的区别之
处在于:线性聚硅氧烷的粘度为105mpa
·
s。
28.对比例1本对比例提供了一种超高分子量聚硅氧烷粉末制备方法,其与实施例8的区别之处在于:低速混合器温度为室温不加热;制备的聚硅氧烷粉末记为sk-1。
29.对比例2本对比例提供了一种超高分子量聚硅氧烷粉末制备方法,其与实施例1的区别之处在于:聚硅氧烷的粘度为5
×
104mpa
·
s。制备的聚硅氧烷粉末记为sk-2。
30.对比例3本对比例提供了一种超高分子量聚硅氧烷粉末制备方法,其与实施例1的区别之处在于:先加入二氧化硅b,再加入二氧化硅a,其混合转速和时间不变。制备的聚硅氧烷粉末记为sk-3。
31.对比例4本对比例提供了一种超高分子量聚硅氧烷粉末制备方法,其与实施例1的区别之处在于:将二氧化硅a,二氧化硅b一起加入,先转速20rpm混合40min,后转速50rpm混合40min。混合转速制备的聚硅氧烷粉末记为sk-4。
32.实验例1成粉性能分别观察实施例1-5、8以及对比例1-4所制备得到的标记为sf-1,sf-2,sf-3,sf-4,sf-5,sf-8、sk-1,sk-2,sk-3,sk-4的超高分子量聚硅氧烷粉末的粉末形态。结果如下表1所示。
33.表1 实施例1-5、8和对比例1-4制备聚硅氧烷粉末时间和形态总结
通过实施例1-5的结果和对比例1-4的结果可以得知:采用本发明的方法,先加入部分比表面积低的二氧化硅a增加二氧化硅a和聚硅氧烷的之间的剪切,使得先预分散,再根据需要加入比表面积高的二氧化硅b进一步分散,可以制备出中位粒径均一的聚硅氧烷粉末产品。将普通二氧化硅进行改性,能够减少普通二氧化硅表面的硅醇基团,进而减少二氧化硅粒子间的氢键使得二氧化硅更容易分散,混合成均一的粉体所用时间更短,而对比例3将二氧化硅a,二氧化硅b加入顺序调换后,先加入的比表面积大的二氧化硅b在同样的时间内并不能与聚硅氧烷很好地分散,造成最终的粉体中大颗粒较多。对比例4一起一次性加入后混合,也不能使得二氧化硅和聚硅氧烷混合均匀,造成最终的粉体中会有很多的大颗粒存在。对比例1相较于实施例8,混合温度降低,使得最终的粉体中大颗粒,使得粒径不均匀。
34.在制备过程中通过调整工艺条件,实施例2对比实施例1,增加转速增加剪切后,也
可以缩短成粉时间;实施例8和实施例1对比,增加混合器的温度,进而降低超高分子量聚硅氧烷的粘度,使得聚硅氧烷更容易分散,混合成均一的粉体所用时间更短。
35.实验例2流变性能,光泽度和摩擦系数测试本实验例设置10组,各实验组的原料除聚硅氧烷粉末的选择有区别外,其他各原料均按下表2的配比称取(重量份数,下同),称取原料后将原料经过双螺杆混合造粒,然后加入到转矩流变仪毛细管挤出装置中,挤出口模为片材口模,测试流变性能。将粒子注塑成光板测试对pe膜的摩擦系数。各实验组的聚硅氧烷颗粒的选择如下表3所示(其中sf-1、sf-2、sf-3、sf-4、sf-5分别为通过实施例1-5所制备得到,sk-1、sk-2、sk-3、sk-4为通过对比例1-4所制备得到)。各实验组的流变性能的测试结果如表4所示。各实验组的摩擦系数结果如表5所示。
36.表2 加入双螺杆造粒机的各原料配比原料pcabsmbs抗氧剂黑色母聚硅氧烷颗粒配比67.52550.61.5无表3 各实验组的聚硅氧烷颗粒的选择
实验组别12345678910聚硅氧烷颗粒无sf-1sf-2sf-3sf-4sf-5sk-1sk-2sk-3sk-4聚硅氧烷颗粒的添加无222222222
表4 各实验组的流变性能评价
实验组别12345678910聚硅氧烷颗粒无sf-1sf-2sf-3sf-4sf-5sk-1sk-2sk-3sk-4挤出扭矩(nm)56-5948-5149-5248-5149-5248-5148-5947-5149-6048-59挤出压力(mpa)45-4740-4240-4240-4240-4240-4240-4738-4040-4739-48
表5 各实验组摩擦系数评价
实验组别12345678910聚硅氧烷颗粒无sf-1sf-2sf-3sf-4sf-5sk-1sk-2sk-3sk-4静摩擦系数0.4000.2750.2800.2700.2790.2810.3560.2500.3480.339动摩擦系数0.3560.2300.2340.2310.2400.2300.2780.2150.2670.261
由表4的实验结果可以得知:通过对比实验组1的结果和实验组2-6的结果可以得知:采用本发明的方法制备的超高分子量聚硅氧烷其作为润滑剂添加到热塑性树脂中可以有效降低加工过程中的扭矩,压力从而降低实际生产过程中的能耗。
37.对比实验组2-6和实验组7的结果可知,本发明的方法制备的超高分子量聚硅氧烷粉末性能优异,而实验组8,9,10的聚硅氧烷粉末制备方法使得其分散不均匀最终导致在热塑性树脂中的应用中也起不到好的效果,扭矩压力波动很大。
38.通过对比实验组2-6的结果和实验组8的结果可以得知,实验组8因其采用的低分子量的聚硅氧烷其扭矩压力均比超高分子量的聚硅氧烷要低,以上结果符合理论值。
39.由表5的实验结果可以得知:通过对比实验组1的结果和实验组2-8的结果可以得知:加入硅氧烷粉末后,基材的摩擦系数降低。实验组7,9,10因为聚硅氧烷粉末本身分散不好导致在热塑性树脂中分散
不好所以摩擦系数的降低并不显著,实验组8因为不是超高分子量的聚硅氧烷而具有更低的摩擦系数,以上结果符合理论值。
40.实验例3本实验例设置10组(原料与实验例2相同),将标记为sf-1、sf-2、sf-3、sf-4、sf-5、sk-1、sk-2、sk-3、sk-4的聚硅氧烷粉末分别加入到pp/poe/滑石粉(重量比71:8:20)体系中,注塑成2mm厚的平板做耐刮性能(大众pv3952,
△
l值越小,耐刮性能越好)和迁移测试(pv1306,6个周期,96h/周期),所得结果如下表6所示。
41.表6 各实验组的耐刮性能和迁移测试结果
实验组别12345678910聚硅氧烷颗粒无sf-1sf-2sf-3sf-4sf-5sk-1sk-2sk-3sk-4
△
l3.521.351.401.341.451.382.523.012.632.56表面发粘>6周期>6周期>6周期>6周期>6周期>6周期5周期3周期5周期5周期
由表6的实验结果可以得知:实验组2-6的聚硅氧烷粉末耐刮擦性较优,耐迁移性能佳,在整个发粘测试中,没有出现发粘现象;而实验组7,9,10因为聚硅氧烷粉末本身分散不好导致在热塑性树脂中分散不好而耐刮擦性能没有体现,实验组8因为不是超高分子量的聚硅氧烷导致耐刮擦性差和易析出。
42.综上,本发明的制备方法制备的超高分子量聚硅氧烷粉末中位粒径均匀,将其应用于树脂加工过程中,对树脂的流变性能、耐磨性能、耐刮性能等均有明显的提升,其不易析出满足实际使用性能。
43.以上仅为本发明的优选实施例而已,并不用于限制本发明,对于本领域的技术人员来说,本发明可以有各种更改和变化。凡在本发明的精神和原则之内,所作的任何修改、等同替换、改进等,均应包含在本发明的保护范围之内。
再多了解一些
本文用于创业者技术爱好者查询,仅供学习研究,如用于商业用途,请联系技术所有人。