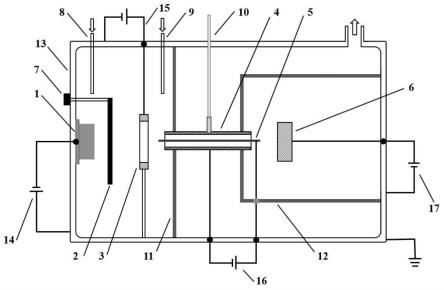
一种管内壁离子渗氮后原位沉积pvd涂层的装置及方法
技术领域
1.本发明涉及一种管内壁离子渗氮后原位沉积pvd涂层的装置及方法。
背景技术:
2.管筒件在城市地下水管道、石油天然气运输管道、军事器械的身管以及化学介质的传输管道等领域应用广泛。但在实际应用中,因为工作环境较为严苛,管筒件的内表面通常受到严重的高温氧化、摩擦磨损和腐蚀作用,容易产生裂纹,大大缩短了其服役年限或使用寿命,造成大量经济损失。考虑到成本和服役环境的特殊性等因素,仅仅依靠研发高性能的新材料显然不能满足发展需求,因此可以从材料表面改性的角度进行思考。这种技术可以在不改变基体材料成分的前提下,通过特定的技术手段来提高材料表面的理化性能。对于管状件而言,相比于外表面,内表面面临的工作环境更加恶劣,因而失效的概率更大。因此,对管筒件内表面进行表面改性强化,使其具有高硬度、优异的摩擦磨损性能和耐高温、耐腐蚀性能,这有着非常重要的现实意义。
3.对于管筒件内表面改性,最早人们提出用电镀和化学镀进行处理。其优势是原理简单、对于设备和操作的要求低,经济适用。但是对于均匀性的把控较弱;同时对mg、al等活泼金属无法进行电镀沉积;此外还要求镀层材料具有良好的导电性;产生的电解废液会对环境产生严重破坏等。近年来提出了等离子体浸没离子注入表面改性方法,尽管等离子体浸没离子注入在一定程度上解决了管筒件内表面改性处理的技术难题,使得改性质量得到了很大改善,但仍存在一些问题有待解决。主要是离子注入层较浅,目前能注入的元素仅限于n元素,且表面强化效果有限主要是注入层的硬度较低,仍不能满足日益苛刻的应用需求。涂层工艺可以使表面硬度提高到相当高的水平,但涂层厚度较薄,不能完全满足工业生产要求。另外,针对硬质涂层-钢基体体系而言,通常涂层与基体存在硬度差异大、弹性模量不匹配、塑性变形能力差等问题,类似“鸡蛋壳效应”。涂层在服役过程中,承受高载荷以及剧烈的摩擦磨损,往往易出现开裂、剥落,最终失效。为了解决单一表面处理技术的不足,korhnen等提出了把等离子体氮化与物理气相沉积(pvd)工艺结合起来的一种复合处理(pn-pvd)新技术。
4.目前,关于管内壁改性技术,通常将离子渗氮和涂层沉积工艺单独进行,一方面管内表面处理效率低,另一方面对于仅涂层沉积工艺,涂层与基体间缺乏梯度分布,涂层与基体之间界面结合强度较低,而对于离子渗氮工艺,基体氮化表面硬度低、耐磨性较差。
技术实现要素:
5.本发明目的是为了解决管内表面处理效率低以及涂层与基体之间界面结合强度较低、耐磨性较差的问题,提供一种管内壁离子渗氮后原位沉积pvd涂层的装置及方法。
6.本发明一种管内壁离子渗氮后原位沉积pvd涂层的装置包括金属阴极弧源、挡板、第一辅助阳极、管筒件、阳极杆、第二辅助阳极、ar进气管、n
2-h2混合气进气管、热电偶、第一绝缘屏蔽罩、第二绝缘屏蔽罩、真空室、金属阴极弧直流电源、第一辅助阳极直流电源、脉冲
偏压电源和第二辅助阳极直流电源;
7.真空室内设置第一绝缘屏蔽罩和第二绝缘屏蔽罩,第一绝缘屏蔽罩与真空室侧壁合围而成第一腔室,第二绝缘屏蔽罩与真空室另一侧壁合围而成第二腔室,第一腔室和第二腔室通过管筒件连通,第一腔室内设有金属阴极弧源和ar进气管,金属阴极弧源前方设置挡板,管筒件一端口和挡板之间设有第一辅助阳极,n
2-h2混合气进气管的进气口延伸到第一腔室内,且位于管筒件端口与第一辅助阳极之间,阳极杆贯穿于管筒件设置,第二腔室内设有第二辅助阳极,且第二辅助阳极位于管筒件正后方;真空室内设置热电偶,监测管筒件温度;
8.金属阴极弧直流电源的阴极与金属阴极弧源电连接,金属阴极弧直流电源的阳极接地;第一辅助阳极直流电源的阳极与第一辅助阳极电连接,第一辅助阳极直流电源的阴极接地;第二辅助阳极直流电源的阳极与第二辅助阳极电连接,第二辅助阳极直流电源的阴极接地;脉冲偏压电源的阴极与管筒件外壁电连接,脉冲偏压电源的阳极与阳极杆电连接。
9.本发明利用上述装置进行管内壁离子渗氮后原位沉积pvd涂层的方法,包括以下步骤:
10.一、预处理:将管筒件超声清洗干燥后置于真空室内,对真空室进行抽真空;
11.二、等离子体清洗刻蚀:通过ar进气管向真空室内通入高纯ar,气压控制在0.3~0.4pa,同时开启金属阴极弧直流电源、第一辅助阳极直流电源、脉冲偏压电源和第二辅助阳极直流电源,利用电弧增强辉光放电技术对管筒件内表面进行等离子体刻蚀清洗;其中金属阴极弧直流电源的电流为70~150a;第一辅助阳极直流电源的电流为30~70a;脉冲偏压电源的负偏压为-60~-500v,占空比在40%~80%;第二辅助阳极直流电源的电流为30~60a;
12.三、等离子体渗氮:停止ar通入,通过n
2-h2混合气进气管向真空室内通入工作气体a,真空室气压控制在0.3~1.2pa,保持金属阴极弧直流电源的电流为70~150a,第一辅助阳极直流电源的电流为30~70a,第二辅助阳极直流电源的电流为30~60a,调整脉冲偏压电源;在热电偶显示温度为350~500℃的条件下,利用电弧增强辉光放电技术进行等离子体渗氮30~240min;
13.四、原位pvd涂层沉积:停止h2通入,通入工作气体b,真空室气压控制在0.2~0.8pa,旋转挡板旋钮,控制挡板不遮挡金属阴极弧源;关闭第一辅助阳极直流电源,保持金属阴极弧直流电源的电流为70~150a和第二辅助阳极直流电源的电流为30~60a,调节脉冲偏压电源,在热电偶显示温度为300~500℃的条件下,在管筒件内表面进行涂层沉积30~300min;
14.五、冷却降温:对真空室进行冷却,管筒件在真空状态下随真空室冷却至70℃以下即可取出。
15.本发明具有如下的有益效果:
16.(1)本发明在同一真空室内连续进行管内表面渗氮和pvd涂层沉积过程,有效提高管内表面处理效率。
17.(2)离子清洗及渗氮过程中高密度的等离子体,可对管内壁产生轰击刻蚀作用,有效活化基体并提高渗氮速率,增强膜基结合力,且低气压下电弧增强辉光等离子体管内表
面处理可在较低的表面温度下进行,能够较好地控制管内表面成分、结构和涂层与基体之间的硬度梯度等性能,可大幅度提高膜基结合强度和涂层耐磨性,结合力可达到100n。
18.(3)通过在靶前设置辅助阳极,在较低的正电压下吸引靶前电子先向其运动,使电子更容易继续向管后辅助阳极运动,可在低气压下稳定放电。
附图说明
19.图1为本发明所述管内壁离子渗氮后原位沉积pvd涂层的结构示意图。
具体实施方式
20.具体实施方式一:本实施方式一种管内壁离子渗氮后原位沉积pvd涂层的装置包括金属阴极弧源1、挡板2、第一辅助阳极3、管筒件4、阳极杆5、第二辅助阳极6、ar进气管8、n
2-h2混合气进气管9、热电偶10、第一绝缘屏蔽罩11、第二绝缘屏蔽罩12、真空室13、金属阴极弧直流电源14、第一辅助阳极直流电源15、脉冲偏压电源16和第二辅助阳极直流电源17;
21.真空室13内设置第一绝缘屏蔽罩11和第二绝缘屏蔽罩12,第一绝缘屏蔽罩11与真空室13侧壁合围而成第一腔室,第二绝缘屏蔽罩12与真空室13另一侧壁合围而成第二腔室,第一腔室和第二腔室通过管筒件4连通,第一腔室内设有金属阴极弧源1和ar进气管8,金属阴极弧源1前方设置挡板2,管筒件4一端口和挡板2之间设有第一辅助阳极3,n
2-h2混合气进气管9的进气口延伸到第一腔室内,且位于管筒件4端口与第一辅助阳极3之间,阳极杆5贯穿于管筒件4设置,第二腔室内设有第二辅助阳极6,且第二辅助阳极6位于管筒件4正后方;真空室13内设置热电偶10,监测管筒件4温度;
22.金属阴极弧直流电源14的阴极与金属阴极弧源1电连接,金属阴极弧直流电源14的阳极接地;第一辅助阳极直流电源15的阳极与第一辅助阳极3电连接,第一辅助阳极直流电源15的阴极接地;第二辅助阳极直流电源17的阳极与第二辅助阳极3电连接,第二辅助阳极直流电源17的阴极接地;脉冲偏压电源16的阴极与管筒件4外壁电连接,脉冲偏压电源16的阳极与阳极杆5电连接。
23.具体实施方式二:本实施方式与具体实施方式一不同点在于所述金属阴极弧源1为多弧离子镀等离子体源。其它与具体实施方式一相同。
24.具体实施方式三:本实施方式利用上述装置进行不锈钢管内表面离子渗氮后原位沉积pvd涂层的方法为:
25.一、预处理:将管筒件4超声清洗干燥后置于真空室13内,对真空室13进行抽真空;
26.二、等离子体清洗刻蚀:通过ar进气管8向真空室13内通入高纯ar,气压控制在0.3~0.4pa,同时开启金属阴极弧直流电源14、第一辅助阳极直流电源15、脉冲偏压电源16和第二辅助阳极直流电源17,利用电弧增强辉光放电技术对管筒件4内表面进行等离子体刻蚀清洗;其中金属阴极弧直流电源14的电流为70~150a;第一辅助阳极直流电源15的电流为30~70a;脉冲偏压电源16的负偏压为-60~-500v,占空比在40%~80%;第二辅助阳极直流电源17的电流为30~60a;
27.三、等离子体渗氮:停止ar通入,通过n
2-h2混合气进气管9向真空室内13通入工作气体a,真空室13气压控制在0.3~1.2pa,保持金属阴极弧直流电源14的电流为70~150a,第一辅助阳极直流电源15的电流为30~70a,第二辅助阳极直流电源17的电流为30~60a,
调整脉冲偏压电源16;在热电偶10显示温度为350~500℃的条件下,利用电弧增强辉光放电技术进行等离子体渗氮30~240min;
28.四、原位pvd涂层沉积:停止h2通入,通入工作气体b,真空室13气压控制在0.2~0.8pa,旋转挡板旋钮7,控制挡板2不遮挡金属阴极弧源1;关闭第一辅助阳极直流电源15,保持金属阴极弧直流电源14的电流为70~150a和第二辅助阳极直流电源17的电流为30~60a,调节脉冲偏压电源16,在热电偶10显示温度为300~500℃的条件下,在管筒件4内表面进行涂层沉积30~300min;
29.五、冷却降温:对真空室13进行冷却,管筒件4在真空状态下随真空室13冷却至70℃以下即可取出。
30.具体实施方式四:本实施方式与具体实施方式一不同点在于步骤一中抽真空至真空度小于5
×
10-3
pa。其它与具体实施方式一相同。
31.具体实施方式五:本实施方式与具体实施方式一不同点在于步骤二中第一辅助阳极3的形状为环形。其它与具体实施方式一相同。
32.具体实施方式六:本实施方式与具体实施方式一不同点在于步骤三中的工作气体a为流量比为1~2:1~3的高纯n2和高纯h2的混合气体。其它与具体实施方式一相同。
33.具体实施方式七:本实施方式与具体实施方式一不同点在于步骤三中的工作气体a为高纯n2。其它与具体实施方式一相同。
34.具体实施方式八:本实施方式与具体实施方式一不同点在于步骤三中调节脉冲偏压电源16的脉冲偏压为-70v,占空比50%。其它与具体实施方式一相同。
35.具体实施方式九:本实施方式与具体实施方式一不同点在于步骤四中调节脉冲偏压电源16的脉冲偏压为-60v,占空比50%。其它与具体实施方式一相同。
36.具体实施方式十:本实施方式与具体实施方式一不同点在于步骤四中的工作气体b为高纯ar或高纯n2。其它与具体实施方式一相同。
37.本发明内容不仅限于上述各实施方式的内容,其中一个或几个具体实施方式的组合同样也可以实现发明的目的。
38.为验证本发明的有益效果进行了以下实验:
39.实施例1
40.本实施例管内壁离子渗氮后原位沉积pvd涂层的装置如图1所示金属阴极弧源1、挡板2、第一辅助阳极3、管筒件4、阳极杆5、第二辅助阳极6、ar进气管8、n
2-h2混合气进气管9、热电偶10、第一绝缘屏蔽罩11、第二绝缘屏蔽罩12、真空室13、金属阴极弧直流电源14、第一辅助阳极直流电源15、脉冲偏压电源16和第二辅助阳极直流电源17;
41.真空室13内设置第一绝缘屏蔽罩11和第二绝缘屏蔽罩12,第一绝缘屏蔽罩11与真空室13侧壁合围而成第一腔室,第二绝缘屏蔽罩12与真空室13另一侧壁合围而成第二腔室,第一腔室和第二腔室通过管筒件4连通,第一腔室内设有金属阴极弧源1和ar进气管8,金属阴极弧源1前方设置挡2,管筒件4一端口和挡板2之间设有第一辅助阳极3,n
2-h2混合气进气管9的进气口延伸到第一腔室内,且位于管筒件4端口与第一辅助阳极3之间,阳极杆5贯穿于管筒件4设置,第二腔室内设有第二辅助阳极6,且第二辅助阳极6位于管筒件4正后方;真空室13内设置热电偶10,监测管筒件4温度;
42.金属阴极弧直流电源14的阴极与金属阴极弧源1电连接,金属阴极弧直流电源14
的阳极接地;第一辅助阳极直流电源15的阳极与第一辅助阳极3电连接,第一辅助阳极直流电源15的阴极接地;第二辅助阳极直流电源17的阳极与第二辅助阳极3电连接,第二辅助阳极直流电源17的阴极接地;脉冲偏压电源16的阴极与管筒件4外壁电连接,脉冲偏压电源16的阳极与阳极杆5电连接。
43.利用上述装置进行不锈钢管内表面离子渗氮后原位沉积pvd涂层的方法为:
44.一、预处理:将φ40
×
130mm的304不锈钢管筒件4超声清洗干燥后置于真空室13内,不锈钢管筒件4两端口分别安装在第一绝缘屏蔽罩11、第二绝缘屏蔽罩12上的圆形开口处;对真空室13进行抽真空,真空度小于5
×
10-3
pa;
45.二、等离子体清洗刻蚀:通过ar进气管8向真空室13内通入流量为260sccm的高纯ar,调节气压为0.3pa;挡板2位于金属阴极弧源1正前方;同时开启金属阴极弧直流电源14、第一辅助阳极直流电源15、脉冲偏压电源16和第二辅助阳极直流电源17,金属阴极弧直流电源14的直流端电流为100a;第一辅助阳极直流电源15的直流端电流为30a;第二辅助阳极直流电源17的直流端电流为40a;控制脉冲偏压电源16的脉冲偏压为-150v,占空比为50%;利用电弧增强辉光放电技术对不锈钢管内表面进行30min等离子体刻蚀清洗;其中金属阴极弧源1为纯度99.90%的cr靶;
46.三、等离子体渗氮:停止ar通入,通过n
2-h2混合气进气管9向真空室13内通入流量比为100:200的高纯n2和高纯h2,调节真空室13气压为0.4pa;金属阴极弧直流电源14直流端电流100a、第一辅助阳极直流电源15的直流端电流30a和第二辅助阳极直流电源17的直流端电流40a保持恒定;调节脉冲偏压电源16的脉冲偏压为-70v,占空比50%,热电偶显示温度450℃,利用电弧增强辉光放电技术进行60min等离子体渗氮;
47.四、原位pvd涂层沉积:停止h2通入,通入流量为65sccm的高纯ar,控制真空室气压在0.1pa;挡板旋钮7旋转90
°
,控制挡板不遮挡金属阴极弧源;关闭第一辅助阳极直流电源15,金属阴极弧直流电源14的直流端电流100a和第二辅助阳极直流电源17的直流端电流40a保持恒定;调节脉冲偏压电源16的脉冲偏压为-60v,占空比50%,热电偶显示温度400℃,在不锈钢管内表面进行cr涂层沉积60min;
48.五、冷却降温:利用炉体冷却水循环系统对真空室13进行冷却,不锈钢管筒件4在真空状态下随真空室13冷却至70℃以下即可取出件。
49.对本实施例不锈钢管筒件4的膜基结合强度进行测试,以不进行渗氮只进行pvd涂层沉积的工件作为对照,膜基结合强度由40n增加至100n,耐磨性提高3倍。综上所述,本发明采用离子渗氮后原位沉积pvd涂层的一体化方法,可在管筒件内表面制备厚度可控的渗氮层,并原位沉积pvd涂层。涂层表面质量良好、硬度高、耐磨性好和膜基结合强度大。
再多了解一些
本文用于创业者技术爱好者查询,仅供学习研究,如用于商业用途,请联系技术所有人。