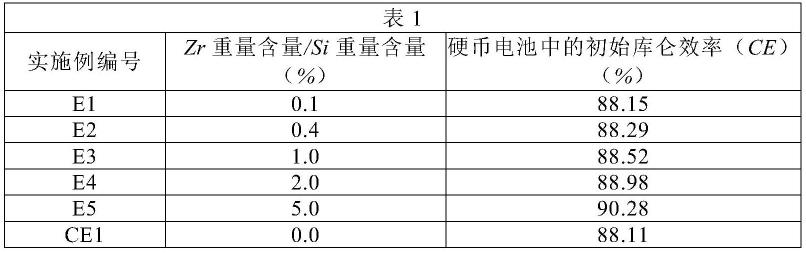
在蓄电池的负电极中使用的粉末、用于制备此类粉末的方法以及包含此类粉末的蓄电池
1.技术领域和
背景技术:
2.本发明涉及在蓄电池的负电极中使用的粉末、用于制备此类粉末的方法以及包含此类粉末的蓄电池。
3.锂离子(li离子)蓄电池是当前性能最佳的蓄电池并且已经成为便携式电子设备的标准。此外,这些蓄电池已经渗透到其他行业如汽车和电存储行业并得以快速发展。此类蓄电池的有利优势为高能量密度结合良好的动力性能。
4.li离子蓄电池通常包含多个所谓的li离子电池,这些电池又包含正电极(也称为阴极)、负电极(也称为阳极)和浸入电解质中的隔板。使用电化学活性材料如锂钴氧化物或锂钴镍锰氧化物作为阴极并使用天然或人造石墨作为阳极,开发了便携式应用最常用的li离子电池。
5.已知,影响蓄电池性能并且具体地讲蓄电池能量密度的重要限制性因素之一是阳极中的活性材料。因此,为了改善能量密度,过去几年已经研究了在负电极中使用包含硅的电化学活性材料。
6.在本领域中,含si基电化学活性粉末的蓄电池的性能一般通过全电池的所谓循环寿命来量化,该全电池的所谓循环寿命被定义为包含此类材料的电池在达到其初始放电容量的80%之前可以被充电和放电的次数或循环数。因此,大多数硅基电化学活性粉末的工作都集中于改善循环寿命上。
7.在阳极中使用硅基电化学活性材料的缺点是它在充电期间的大的体积膨胀,当锂离子(例如通过合金化或插入)完全掺入阳极的活性材料中(这一过程通常被称为锂化)时,该体积膨胀高至300%。在锂掺入期间硅基材料的大的体积膨胀可引起硅基颗粒中的应力,这继而可导致硅材料的机械降解。在周期性重复li离子蓄电池的充电和放电期间,硅基电化学活性材料的重复机械降解可使蓄电池的寿命减少至无法接受的水平。
8.另外,与硅相关联的负面效应是可能在阳极上形成厚sei(固体电解质界面)。sei是电解质和锂的一种复杂的反应产物,并因此致使可参与电化学反应的锂的损失,进而导致较差的循环性能,即每次充电-放电循环的容量损失。厚sei可进一步增大蓄电池的电阻,从而限制可达到的充电和放电速率。
9.原则上,sei形成是自我终止的过程,一旦在硅基材料的表面上形成“钝化层”就停止该过程。
10.然而,由于硅基颗粒的体积膨胀,硅基颗粒和sei两者可能在放电(锂化)和再充电(脱锂)期间被损坏,从而释放新的硅表面并导致开始形成新的sei。
11.为了解决上述缺点,通常使用复合粉末。在这些复合粉末中,通常使用将纳米级的硅基域与至少一种适用于保护硅基域免受电解质分解并适应体积改变的组分混合。此类组分可以是碳基材料,优选地形成基质。
12.例如在us 2009/0162750中提及了此类复合粉末,其中公开了硅颗粒,该硅颗粒由直径为5nm至200nm的结晶颗粒和厚度为1nm至10nm的非晶表面层构成,该非晶表面层由至
少一种金属氧化物形成,该金属氧化物在通过金属元素的氧化产生金属氧化物时的吉布斯自由能小于将硅氧化时的吉布斯自由能。在wo 2012/000858中,公开了亚微米级si基粉末,其具有介于20nm与200nm之间的平均初级粒度,以及表面层,其包含0《x《2的sio
x
并且具有介于0.5nm与10nm之间的平均厚度。在ep 3525267中,公开了硅基颗粒,其具有基于数量的分布,具有d50,从而小于8%的颗粒具有大于d50两倍的尺寸。在novel nanostructured sio2/zro
2 based electrodes with enhanced electrochemical performance of lithium-ion batteries,electrochemica acta 218(2016)47-53中,公开了由sio2/zro2制成并形成si-o-zr键的阳极材料。
13.尽管使用了此类复合粉末,但在含si基电化学活性粉末的蓄电池性能方面仍然存在改善的空间。
14.与阳极中存在细硅基颗粒相关联的另一个缺点是这些硅基颗粒在其表面上具有氧化物层。根据粒度和制造硅基颗粒的方式,这可能导致硅基颗粒中的氧含量为很少重量%至最多15重量%或甚至更高。
15.当用于蓄电池时,硅基颗粒中包含的氧将与锂反应,这将导致部分锂转化为氧化锂(li2o)。由于商业蓄电池中锂的量受限于阴极中包含的锂,因此当这种锂的一部分不可逆地转化为不能用于进一步充电/放电循环的氧化锂时,蓄电池的初始不可逆容量损失增加。
16.因此,可被用于减少硅基颗粒的氧含量的任何措施都将直接有助于减少转化为氧化锂的锂量,并且因此减少含有此类硅基颗粒的蓄电池的初始不可逆容量损失(即初始库仑效率的增加)。
17.本发明的目的是提供一种稳定的电化学活性硅基粉末,其包含具有减少的氧量的硅基颗粒,硅基粉末一旦用于li离子蓄电池的负电极中就是有利的,因为其允许实现该蓄电池的减少的初始不可逆容量损失。
技术实现要素:
18.该目的通过提供根据实施方案1的硅基粉末来实现,该硅基粉末一旦用于li离子蓄电池的阳极,就允许实现较高初始库仑效率(ce),如与比较例1相比在实施例1至5中所展示出的,以及与比较例2相比在实施例6所展示出的。
19.本发明涉及以下实施方案:
20.实施方案1
21.在第一方面,本发明涉及一种适用于蓄电池的负电极的硅基粉末,所述硅基粉末包含硅基颗粒和非硅基颗粒,所述硅基颗粒具有基于数量的粒度分布,其具有ds50值,所述ds50值为至多200nm,所述硅基粉末具有至多20重量%的氧含量,所述硅基粉末包含来自一组金属的一种或多种元素m,所述金属具有在温度t下由其零价态形成氧化物的标准吉布斯自由能,该标准吉布斯自由能低于在相同温度下由零价硅形成sio2的标准吉布斯自由能,所述温度t等于或高于573k且低于1373k,所述硅基粉末中所述一种或多种元素m的含量为所述硅基粉末中si含量的至少0.10重量%,所述一种或多种元素m存在于非硅基颗粒中。
22.换句话讲,根据实施方案1所述的硅基粉末包含硅基颗粒和非硅基颗粒两者,后者含有一种或多种元素m。
23.适用于蓄电池的负电极中的粉末意指包括电化学活性颗粒的电化学活性粉末,该电化学活性颗粒能够分别在蓄电池的负电极的锂化和脱锂期间储存和释放锂离子。此类粉末可以等效地称为“活性粉末”。
24.所谓硅基粉末(或颗粒),意指包含硅作为主金属(或半金属)元素或作为唯一金属(或半金属)元素的粉末(或颗粒)。硅主要以硅金属(或半金属)形式存在,其中可能已经添加少量其他材料以改善特性,或其可含有一些不可避免的杂质,如氧。相对于硅基粉末(或颗粒)的总重量,此类硅基粉末(或颗粒)中的平均si含量可以为60重量%或更多,或者可以为70重量%或更多,或者可以为80重量%或更多。
25.硅基颗粒可具有任何形状,例如基本上球形,但也可是不规则形状、杆形、板形等。
26.来自一组金属的元素m可以例如为zr、al、mg、ti和ca,所述金属在温度t下由其零价态形成氧化物的标准吉布斯自由能低于在相同温度t下由零价硅形成sio2的标准吉布斯自由能,温度t等于或高于573k且低于1373k。
27.为了避免疑义,将清楚的是,在本文件中,词语“硅”是指呈其金属、零价态形式的元素si,而符号si是指与其氧化态无关的元素硅。其他元素(如zr、al、mg、ca、ti)的情况与该情况类似,其中金属的全名是指呈其金属、零价态形式的元素,而元素的符号是指与其氧化态无关的元素。
28.在制备实施方案1所述的硅基粉末期间,从原始硅基粉末开始,一种或多种元素m将与原始硅基颗粒中包含的氧反应,例如与存在于原始硅基颗粒的表面层中的氧(以硅氧化物sio
x’的形式,其中0《x'《2)反应,以形成一种或多种金属m氧化物和氧含量降低的硅基颗粒。这可以例如通过例如在高能量球磨机中,将原始硅基粉末与特定量的m基粉末强烈混合来实现,所述m基粉末包含具有mo
y’表面层的m基颗粒,其中0≤y'《2。因此,硅基粉末中的硅基颗粒具有平均摩尔组成为sio
x
的表面层,其中0≤x《x’,并且硅基粉末中的m基颗粒具有平均摩尔组成为moy的表面层,其中0≤y'《y。
29.所谓平均摩尔组成为sio
x’的表面层(其中0《x'《2),意指在分析的粉末样品的至少3个不同点(或位置)中的每一个处通过xps分析确定的摩尔组成的平均值。同样适用于平均摩尔组成mo
y’(0≤y'《2)和本文件中提及的任何其他平均摩尔组成。
30.实施方案1的硅基粉末中的一种或多种元素m的含量需要为si含量的至少0.10重量%,以确保获得在硅基颗粒的氧减少方面的显著效果。
31.所谓颗粒的表面层,意指颗粒核的表面上的层,核是金属,例如si或zr。表面层一般为氧化物层,其具有组成ao
x
,其中a为构成颗粒核的金属,并且x小于在完全氧化层的情况下其可能具有的最大值。颗粒的表面层通常具有不超过颗粒核的直径的十分之一的厚度。在本发明中,颗粒的表面层具有不超过20nm的厚度,优选地不超过10nm的厚度。
32.值得一提的是,原始硅基粉末与m基粉末的研磨不应太强烈,以避免形成sim合金,例如sizr合金,所述sim合金是电化学惰性的,因此将降低获得的硅基粉末的比容量。
33.不同于硅基颗粒的颗粒中存在一种或多种元素m具有两个优点。首先,避免了制备si-m金属合金的处理步骤,并且其次,如果需要,其允许稍后从硅基粉末中去除金属m氧化物颗粒,这将导致硅基粉末中的非电化学活性颗粒的量较低,因此导致蓄电池中硅基粉末的比容量较高。
34.使用合适的技术分析表面层的组成,例如x-射线光电子能谱(xps)或核磁共振
(nmr)。这些技术允许当从具有带sio
x’表面层的硅基颗粒的原始硅基粉末开始制备根据实施方案1所述的硅基粉末时,量化sio
x
和moy表面层的x值和y值,或者至少定量地比较sio
x’和sio
x
中的x’和x,以确定硅基颗粒的氧含量的降低。
35.实施方案2
36.在根据实施方案1所述的第二实施方案中,硅基颗粒具有平均摩尔组成为sio
x
的表面层,其中0≤x《1。
37.实施方案3
38.在根据实施方案1或2所述的第三实施方案中,当考虑除氧之外的所有元素时,所述非硅基颗粒中的所述一种或多种元素m的含量为至少60重量%。
39.非硅基颗粒中的一种或多种元素m的过低含量将需要较高浓度的非硅基颗粒存在于硅基粉末中,以便实现期望的技术效果。由于非硅基颗粒是电化学惰性的,因此这将降低硅基粉末的比容量(以mah/g为单位)。
40.实施方案4
41.在根据实施方案1至3中任一项所述的第四实施方案中,其中所述非硅基颗粒具有粒度分布,其具有d
ns
50,所述d
ns
50值为至多500nm。
42.较大尺寸的非硅基颗粒将具有较小的表面积,并且因此对硅基颗粒中包含的氧的反应性较低。因此,为了实现期望的技术效果,需要较高浓度的非硅基颗粒存在于硅基粉末中,这将降低硅基粉末的比容量(以mah/g为单位)。
43.实施方案5
44.在根据实施方案1至4中任一项所述的第五实施方案中,所述硅基粉末中的所述一种或多种元素m的含量为所述硅基粉末中si含量的至少0.40重量%且为si含量的至多5重量%。
45.应避免一种或多种元素m的含量过高,以防止硅基粉末被不有助于蓄电池中的比容量的材料过高稀释。
46.实施方案6
47.在根据实施方案1至5中任一项所述的第六实施方案中,一种或多种元素m的组包括zr。
48.换句话讲,金属元素m中的至少一种是zr。优选地,至少50重量%的金属元素m是zr,并且更优选地至少75重量%的金属元素m是zr。
49.更优选地,除了不可避免的金属杂质之外,一种或多种元素m的组仅包含zr作为金属元素。
50.这可能是有利的,因为处于其金属态的zr比许多其他元素(例如al、ca和mg)更硬,所述其他元素在温度t下由其零价态形成氧化物的标准吉布斯自由能低于在相同温度t下由零价硅形成sio2的标准吉布斯自由能,温度t等于或高于573k且低于1373k。zr粉末将不粘附到研磨介质或混合容器的壁上,并且因此将最终与硅基粉末混合,然而对于al、ca和mg粉末,可能存在材料的损失,这本身是不可取的,而且还难以控制最终将在最终硅基粉末中的此类金属的量。
51.因此,锆以可接受的成本提供实用性和相对容易的可获得性的最佳平衡。
52.优选地,zr的含量为所述硅基粉末中si含量的至少0.40重量%,并且为所述硅基
粉末中si含量的至多5重量%。
53.实施方案7
54.在根据实施方案1至6中任一项所述的第七实施方案中,当考虑除氧之外的所有元素时,所述硅基粉末中的si含量为至少90重量%。
55.实施方案8
56.在根据实施方案1至8中任一项所述的第八实施方案中,所述硅基粉末具有体积粒度分布,所述体积粒度分布具有平均初级粒度d
av
,d
av
大于或等于17nm且小于或等于172nm。
57.硅基粉末的平均初级粒度d
av
可基于离心沉降光测仪(cps)分析或显微镜分析来确定,或者可假设球形颗粒具有相等尺寸,根据rouquerol等人,在adsorption by powders and porous solids(1999)中的公式,由粉末的比表面积来计算,
[0058][0059]
其中p是指粉末的理论密度(2,33g/cm3),并且bet是指通过brunauer-emmett-teller的n2吸附方法(bet技术)确定的粉末比表面积(m2/g)。
[0060]
换句话讲,基于上述方程,具有平均初级粒度d
av
大于或等于17nm并且小于或等于172nm的颗粒的硅基粉末等同于具有高于或等于15m2/g且低于或等于150m2/g的bet比表面积的粉末。
[0061]
实施方案9
[0062]
在第二方面,本发明涉及一种用于制备根据权利要求1至8中任一项所述的硅基粉末的方法,所述方法包括以下步骤:
[0063]
a.提供包含硅基颗粒的粉末,其具有体积粒度分布,所述体积粒度分布具有d
vs
50值,所述d
vs
50值为至多200nm,并且具有平均摩尔组成为sio
x
的表面层,其中0《x《2,优选地0《x《1,
[0064]
b.提供m基粉末,其包含来自一组金属的一种或多种元素m的m基颗粒,所述金属具有在温度t下由其零价态形成氧化物的标准吉布斯自由能,该标准吉布斯自由能低于在相同温度下由零价硅形成sio2的标准吉布斯自由能,所述温度t等于或高于573k且低于1373k,所述m基颗粒具有体积粒度分布,其具有dm50值,所述dm50值为至多500nm,
[0065]
c.将所述硅基粉末与所述m基粉末混合以获得中间混合物,
[0066]
d.研磨所述中间混合物,由此获得硅基颗粒和m基颗粒的最终混合物,
[0067]
e.在等于或高于573k且低于1373k的温度下,在保护气氛下对最终混合物进行热处理,然后进行冷却步骤至室温。
[0068]
优选地,m基粉末包含zr作为主金属元素。更优选地,除了不可避免的金属杂质外,m基粉末仅包含zr作为金属元素。
[0069]
所谓主金属元素,意指与m基粉末中存在的其他金属元素相比,金属元素占大多数存在或具有最大含量。
[0070]
实施方案10
[0071]
在第三方面,本发明涉及一种适用于蓄电池的负电极的复合粉末,所述复合粉末包含复合颗粒,所述复合颗粒包含基质材料和根据实施方案1至8中任一项所述的硅基粉
气体。将这些气体引导到红外测量池中。将观察到的信号重新计算成氧含量。
[0090]
比表面积(bet)的测定
[0091]
使用micromeritics tristar 3000bet表面积分析仪,用brunauer-emmett-teller(bet)方法测量比表面积。2g的待分析的粉末首先在120℃的烘箱中干燥2小时,随后用n2吹扫。然后,在测量之前,将粉末在120℃的真空中脱气1小时,以便去除所吸附的物种。
[0092]
电化学性能的测定
[0093]
实施例和反例中粉末的电化学性能通过以下方法测定。对于根据实施方案1至9所述的粉末,因为必须避免与空气或氧气的任何接触,以便不重新氧化硅基颗粒,所以电极和电池的整个制备在含有干燥氩气的手套箱内进行(《3ppm h2o且《3ppm o2)。对于复合粉末,由于硅基颗粒嵌入保护基质中,因此电极的制备可在空气中进行。
[0094]
首先使用45μm筛来筛分待测试的粉末。然后将它们与炭黑混合,任选地与碳纤维和粘合剂混合。在根据实施方案1至9所述的硅基粉末的情况下,粘合剂是溶解在n-甲基-2-吡咯烷酮(nmp)中的聚偏二氟乙烯(pvdf),浓度为nmp中的8重量%pvdf。电极的组成为50重量份粉末/25重量份碳黑/25重量份pvdf。
[0095]
在复合粉末的情况下,粘合剂是溶解于水中的羧甲基纤维素钠(cmc)粘合剂,浓度为2.5重量%。电极的组成为89重量份复合粉末/1重量份碳黑/2重量份碳纤维/8重量份cmc。
[0096]
在两种情况下,在pulverisette 7行星式球磨机中以250rpm将这些组分混合30分钟。用乙醇清洁的铜箔用作集电器。将所混合的组分200μm厚的层涂覆在铜箔上。将涂覆的铜箔在70℃下真空干燥45分钟。在干燥后的带涂层铜箔中打出一个1.27cm2圆并用作硬币电池的电极,将锂金属用作反电极。电解质是溶解在ec/dec 1/1 2%vc 10%fec溶剂中的1m li pf6。
[0097]
所有硬币电池使用高精度蓄电池测试仪(maccor 4000系列)使用下文所描述的程序进行循环,其中“cc”代表“恒定电流”,而“cv”代表“恒定电压”。
[0098]
·
循环1:
[0099]
ο搁置6小时
[0100]
ο在c/10时cc锂化至10mv,然后cv锂化直至c/100
[0101]
ο搁置5分钟
[0102]
ο在c/10时cc脱锂至1.5v
[0103]
ο搁置5分钟
[0104]
·
从循环2开始:
[0105]
ο在c/2时cc锂化至10mv,然后cv锂化直至c/50
[0106]
ο搁置5分钟
[0107]
ο在c/2时cc脱锂至1.2v
[0108]
ο搁置5分钟
[0109]
针对初始循环以及后续循环进行计算的硬币电池的库仑效率(ce)是在给定循环下脱锂时的容量与锂化时的容量的比率。就库仑效率而言,初始循环是最重要的循环,因为sei形成的反应对ce具有巨大影响。通常,对于硅基粉末,初始循环时的库仑效率可以低至80%(或甚至更低),这对应于20%的硬币电池的不可逆容量损失,这是巨大的。目标是在初
始循环时达到至少90%ce,为此减少电化学活性材料中存在的氧的量具有有益效果。
[0110]
为了达到期望的电池容量,蓄电池制造商需要使用附加的阴极材料补偿由阳极引起的初始循环时的不可逆损失,这表示显著的附加成本和能量密度的损失。因此,即使在初始循环时获得很少ce增益,其乘以数百万个制备的电池,也是显著的。
[0111]
粒度分布的测定
[0112]
经由对硅基粉末(或复合粉末)的横截面的电子显微镜分析(sem或tem)与图像分析组合来测定硅基粉末以及根据本发明的复合粉末中包含的硅基颗粒和/或非硅基颗粒的基于数量的粒度分布。
[0113]
为此,按照下文详述的程序制备硅基粉末(或复合粉末)的横截面,其包括硅基颗粒和非硅基颗粒的多个横截面。
[0114]
将500mg待分析的粉末嵌入7g树脂(buehler epoxicure 2)中,该树脂由4份环氧树脂(20-3430-128)和1份环氧硬化剂(20-3432-032)的混合物组成。在至少8小时期间干燥所得的1”直径的样品。然后,首先使用struers tegramin-30机械地抛光,直至达到最大5mm的厚度,然后通过离子束抛光(横截面抛光器jeol sm-09010)在6kv下进一步抛光约6小时,以获得抛光的表面。最后使用cressington 208碳涂覆机通过碳溅射12秒将碳涂层施加在该抛光的表面上,以获得将通过sem(或tem)分析的样品,也称为“横截面”。
[0115]
硅基颗粒(或非硅基颗粒)的尺寸被认为等同于硅基颗粒(或非硅基颗粒)的离散横截面的周长上两点之间的最大直线距离,也称为d
max
。
[0116]
出于以非限制性方式说明测定硅基颗粒(非硅基颗粒)的基于数量的粒度分布的目的,下文提供了基于sem的程序。
[0117]
1.采集包含硅基颗粒和非硅基颗粒的硅基粉末(或复合粉末)的横截面的多个sem图像。
[0118]
2.调整图像的对比度设置和亮度设置,以容易地可视化硅基颗粒和非硅基颗粒的横截面。由于其不同的化学组成,亮度的差异允许容易的区分两种类型的颗粒,并且在复合粉末的情况下,容易的区分两种类型的颗粒与基质。
[0119]
3.使用合适的图像分析软件,从所采集的sem图像中的一个或若干个中选择硅基颗粒的至少1000个离散横截面和非硅基颗粒的至少100个离散横截面,其不与硅基颗粒或非硅基颗粒的另一横截面重叠。硅基颗粒或非硅基颗粒的这些离散横截面可选自包含硅基颗粒和非硅基颗粒的粉末的一个或多个横截面。
[0120]
4.对于硅基颗粒的至少1000个离散横截面中的每一个和非硅基颗粒的至少100个离散横截面中的每一个,使用合适的图像分析软件测量硅基颗粒和非硅基颗粒的离散横截面的d
max
值。
[0121]
然后计算使用上文所述方法测定的硅基颗粒的基于数量的粒度分布的ds10、ds50和ds90值,以及非硅基颗粒的基于数量的粒度分布的d
ns
10、d
ns
50和d
ns
90。这些基于数量的粒度分布可经由众所周知的数学方程容易地被转化为基于重量或体积的粒度分布。
[0122]
另选地,硅基粉末的基于体积的粒度分布可通过离心沉降与离心沉降光测仪dc20000(cps instruments,inc,usa)来测定。
[0123]
仪器配备有内半径为4.74cm的中空聚碳酸酯盘。旋转速度设定为20000rpm,这对应于约1.9x 105m/s2的离心加速力。
[0124]
盘填充有16ml线性密度梯度(10%至5%)的halocarbon 1.8(三氟氯乙烯-pctfe)的2-丁氧基乙酸乙酯(casrn 112-07-2)溶液。
[0125]
作为参考材料,为计算沉降常数,使用平均直径为0.52μm且比密度为3.515g/cm3的金刚石颗粒。
[0126]
样品制备:
[0127]
使用超声(branson sonifier 550w)制备待分析的粉末在异丙醇中的10重量%悬浮液。将悬浮液用丁氧基乙酸乙酯稀释至最终浓度为0.05重量%的硅。
[0128]
将0.050ml所得样品注入盘中,并且将吸光度记录为470nm波长下的时间函数。
[0129]
利用内置算法(dccs软件)并使用以下参数,将所得时间-吸光度曲线转换为粒度分布(质量或体积):
[0130]
·
旋转流体密度:2.33g/cm3[0131]
·
旋转流体折射率:1.482
[0132]
·
硅密度:2.33g/cm3[0133]
·
硅折射率:4.49
[0134]
·
硅吸附系数:17.2k
[0135]
按照用户指令,通过激光衍射sympatec(sympatec-helos/bfs-magic 1812)测定复合粉末的基于体积的粒度分布。将以下设置用于测量:
[0136]-分散系统:sympatec-rodos-m
[0137]-分散器:sympatec-vibri 1227
[0138]-镜头:r2(0.45-87.5μm范围)
[0139]-分散:3巴的压缩空气
[0140]-光学浓度:3-12%
[0141]-开始/停止:2%
[0142]-时基:100ms
[0143]-进给率:80%
[0144]-光圈:1.0mm
[0145]
必须注意的是,进给率和光圈设置可以随光学浓度而变化。
[0146]
然后计算使用上文所述的方法测定的硅基粉末的基于体积的粒度分布的d
vs
10、d
vs
50和d
vs
90值,以及复合粉末的基于体积的粒度分布的dc10、dc50和dc90值。
[0147]
分析包含一种或多种元素m的颗粒
[0148]
包含一种或多种元素m的颗粒的定位基于sem-eds(能量-色散x射线光谱)显微镜分析与si、o、c和m元素的映射来进行。
[0149]
按照先前描述的程序制备横截面,并且然后使用得自jeol的feg-sem jsm-7600f进行分析,其配备有得自bruker的eds检测器xflash 5030-127(30mm2,127ev)。来自该检测器的信号由得自bruker的quantax 800eds系统进行处理。
[0150]
通过在几毫米的工作距离处施加15kv的电压来产生放大。当将值添加到来自光学显微镜的图像时记录来自反向散射电子的图像。
[0151]
为了确定氧是否与元素m或si键合,通过x-射线光电子能谱(xps)分析,使用配备有聚焦单色化al ka辐射的phi quantera sxm光谱仪来确定元素m或si的氧化态。使用的飞
离角为45
°
,分析深度低于10nm,并且光斑直径为200pm。灵敏度极限介于0.1%与0.5%原子之间。将multipak软件用于数据处理。
[0152]
xps分析还允许确定平均摩尔组成,即分别在sio
x
和sio
x’表面层中的x、x’的平均值,以及分别在moy和mo
y’表面层中的y和y’的平均值,并且估计那些表面层的厚度。
[0153]
另选地,tem-eels(电子能量损失光谱)设备或核磁共振(nmr)设备可用于相同目的。
[0154]
反例和实施例的实验制备
[0155]
根据本发明的实施例1(e1)
[0156]
为制备来自实施例1的硅基粉末,首先通过使用氩气作为等离子体气体施加60kw射频(rf)电感耦合等离子体(icp)获得硅粉末,以约50g/h的速率向氩气注入微米级硅粉末前体,从而获得高于2000k的普遍(即,在反应区中)温度。在该第一工艺步骤中,前体变得完全蒸发。在第二工艺步骤中,将18nm3/h的氩气流用作紧邻反应区下游的急冷气体,以使气体的温度降低至低于1600k,从而导致成核成金属亚微米硅粉末。最后,在100℃的温度下通过在5分钟内添加100l/h含1摩尔%氧的n2/o2混合物进行钝化步骤。
[0157]
获得的硅粉末的比表面积(bet)测量为83m2/g。获得的硅粉末的氧含量测量为8.7重量%。硅粉末的粒度分布测定为:d
vs
10=63nm,d
vs
50=113nm,d
vs
90=205nm且d
avs
=119nm。
[0158]
然后在手套箱(干燥ar气氛,《3ppm h2o且《3ppm o2)内,在fritsch pulverisette 7行星式球磨机中,将这种硅粉末与锆粉末(american elements,平均粒度为50nm-100nm)混合以避免氧气污染,其使用600rpm的旋转速度、具有适于广口瓶的尺寸的不锈钢球、20:1的球粉质量比(bpr)和240分钟的研磨时间。锆粉末的重量为硅粉末重量的0.0913%,使得zr的按重量计含量为所得混合物中存在的si的按重量计含量的0.1%。
[0159]
在773k下,在置于手套箱中(干燥ar气氛,《3ppm h2o且《3ppm o2)的烘箱中,进一步给予所得混合粉末热处理并持续2小时,随后冷却至室温。
[0160]
基于sem分析,在该过程期间尚未显著修改硅颗粒和锆颗粒的平均尺寸。这意指d
vs
10、d
vs
50、d
vs
90、d
avs
值和ds10、ds50、d
s 90、d
av
值可分别被认为是相等的。类似地,dm10、dm50、dm90值和d
ns
10、d
ns
50、d
ns
90值可分别被认为是相等的。
[0161]
混合物的氧含量测量为8.7重量%,从而意指没有发生附加的氧吸收。混合物的比表面积(bet)测量为83m2/g,从而意指相对于si,0.1%的zr含量不改变bet值。
[0162]
基于获得的硅基粉末的xps分析,至多10nm深度的锆颗粒的表面被完全氧化,从而意指锆处于氧化态 iv。所得粉末的横截面的sem-eds分析也证实氧存在于锆颗粒的核中。仍然基于xps分析,所得硅基粉末的硅颗粒的sio
x
表面层中的平均x值低于硅颗粒通过等离子体产生之后和硅颗粒与锆颗粒混合之前其sio
x’表面层中的平均x'值。
[0163]
根据本发明的实施例2-5(e2-e5)
[0164]
为了制备实施例2至5的硅基粉末,使用与实施例1相同的程序,不同的是在混合步骤期间使用不同量的锆粉末。这些量为:实施例2为0.4重量%、实施例3为1.0重量%、实施例4为2.0重量%且实施例5为5.0重量%,由此这些量表示为与存在于最终硅基粉末中的si量相比的百分比。
[0165]
不根据本发明的反例1(ce1)
[0166]
为了制备反例1的硅基粉末,使用与实施例1相同的程序,不同的是不添加锆粉末。为了确保实施例与反例之间的最大可比性,仍然在该程序中执行提及的在773k下的加热步骤。
[0167]
所有获得的硅基粉末(e2至e5和ce1)的氧含量均测量为8.7重量%。所有获得的硅基粉末(e2至e5和ce1)的比表面积(bet)值均在介于82m2/g和85m2/g之间的范围内。
[0168]
粉末的电化学测试
[0169]
根据上文指定的程序在硬币电池中测试制备的粉末。获得以下结果:
[0170]
表1:包含粉末e1、e2、e3、e4、e5和ce1的硬币电池的性能
[0171][0172]
可以看出,对于使用根据本发明的硅基粉末(e1至e5)作为阳极材料的硬币电池,初始库仑效率(ce)随添加的zr量而增加。
[0173]
这通过以下事实解释:由于混合以及部分由于后续加热,存在于硅颗粒表面处的氧的一部分被转移到存在的锆颗粒。这减少了在阳极的初始锂化期间转化为氧化锂的锂量,从而降低了初始不可逆容量损失并增加了电池的初始库仑效率(ce)。
[0174]
根据本发明的实施例6(e6)
[0175]
为了制备实施例6的复合粉末,在手套箱内部,由26g来自实施例4(e4)的硅基粉末和32g石油基沥青粉末制备共混物。
[0176]
在n2下将该共混物加热至450℃,使得沥青熔化,并且在等待60分钟的时间段之后,通过以1000rpm操作的cowles溶解型混合器在高剪切下混合30分钟。
[0177]
将由此获得的硅基粉末e4在沥青中的混合物在n2下冷却至室温,并且一旦固化,就磨成粉并在400目筛上筛分,以制备中间复合粉末。
[0178]
然后将16g中间复合粉末与24.6g石墨在滚转工作台上混合3小时,然后将所得混合物通过研磨机,使其解聚。在这些条件下,获得良好的混合,但石墨不会变得嵌入沥青中。
[0179]
如下对获得的来自e4的粉末、沥青和石墨的混合物进一步给予热后处理:将该产物放入管式炉的石英坩埚中,以3℃/min的加热速率加热至1000℃并在该温度下保持两小时,然后冷却。所有这些都是在氩气气氛下进行的。
[0180]
最终在研钵中手动压碎经焙烧的产物,并在325目筛上筛分以形成最终复合粉末。
[0181]
通过xrf测量该复合粉末中的总si含量为20.3重量%,其具有 /-0.3重量%的实验误差。这对应于基于加热时沥青的约40重量%的重量损失和加热其他组分时不显著的重量损失的计算值。该复合粉末的氧含量测量为2.0重量%。该复合材料的zr含量测量为0.41重量%,这意指2.0%的zr/si比率未改变。获得的复合粉末的比表面积(bet)测量为3.6m2/g。
[0182]
不根据本发明的反例2(ce2)
[0183]
为了制备反例2的复合粉末,使用与实施例6相同的程序,不同的是使用反例1(ce1)的粉末代替实施例4(e4)的粉末。该复合粉末的氧含量测量为2.0重量%,并且bet值测量为3.5m2/g。
[0184]
复合粉末的电化学测试
[0185]
根据上文指定的程序在硬币电池中测试制备的复合粉末。获得以下结果:
[0186]
表2:含有粉末e6和ce2的硬币电池的性能
[0187][0188]
可以看出,使用根据本发明的复合粉末作为阳极材料的硬币电池的初始库仑效率(ce)显著高于使用不根据本发明的复合粉末的硬币电池的初始库仑效率。换句话讲,对于根据本发明的硅基粉末观察到的优点在将硅基粉末整合到复合结构中时被保持。
再多了解一些
本文用于企业家、创业者技术爱好者查询,结果仅供参考。