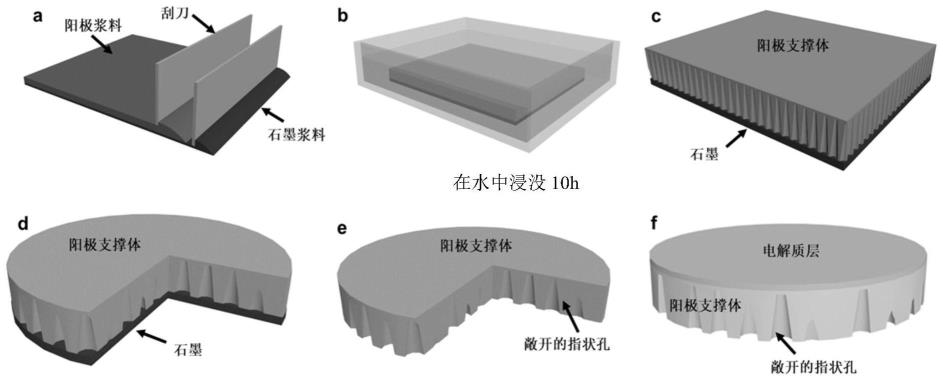
1.本发明属于陶瓷燃料电池技术领域,具体涉及一种直接氨燃料的中低温质子型陶瓷燃料电池及其制备方法。
背景技术:
2.燃料电池是一种可以直接将燃料所具有的化学能直接转换成电能的化学装置,又称电化学发电器。可以把燃料电池看作是一个“工厂”,它将燃料输送进来,同时将产生的电输出。只要不断的给它提供原料(燃料),它就会不断地生产产品(电)。它是继水力发电、热能发电和原子能发电之后的第四种发电技术。由于燃料电池是通过电化学反应把燃料的化学能中的吉布斯自由能部分转换成电能,不受卡诺循环效应的限制,因此燃料电池的能量利用效率要高于传统热机。另外,燃料电池用燃料和氧气作为原料,同时没有机械传动部件,故排放出的有害气体极少,使用寿命长。由此可见,从节约能源和保护生态环境的角度来看,燃料电池是最有发展前途的发电技术。根据电解质的不同,燃料电池可分为五大类型:碱性燃料电池(alkaline fuel cell,afc);质子交换膜燃料电池(proton exchange membrane fuel cell,pemfc);磷酸燃料电池(phosphoric acid fuel cell,pafc);熔融碳酸盐燃料电池(molten carbonate fuel cell,mcfc);固体氧化物燃料电池(solid oxide fuel cell,sofc)。其中,sofc能量转化效率高,燃料适用性广,无需贵金属催化剂,在分布式供能和热电联产等方面具有广阔的应用前景。
3.soc,也称为陶瓷电化学电池,可以在sofcs(用于能量转换)和固体氧化物电解电池(soecs,用于能量储存)的双重模式下运行。在这两种情况下,气体都需要通过电极在运输到反应三相界面处,因此电极必须是多孔的。在过去的几十年中,为了开发具有高表面积、燃料/产品进出反应位点的速度快以及热催化剂或电化学催化剂的高负载的分级多孔电极,人们付出了相当大的努力。层次结构的操作是高效能量存储和转换应用实现高性能的关键步骤之一。制备支撑电极的传统方法有:干压、柱塞挤压和流延成型。干压法的优点是:操作简单、成本低,常用于制备小型纽扣电池。柱塞挤压法制备的电极具有均匀的海绵状孔隙,孔径约为0.2μm。流延成型方法简单且应用广泛,适用于制备大面积陶瓷支撑体。但是,通过上述方法制备的sofc可能具有较大的传质阻力。为了促进气体传输,已经使用大孔电极设计和制备以获得较宽的气体扩散路径,从而降低气体传输的阻力。造孔剂(如石墨、尿素和淀粉)已被用于增加电极的孔隙率。虽然这种方法有效地增加了孔隙率,但一些不规则和锯齿状的孔隙往往表现出很大的曲折系数引入,未能降低气体扩散阻力。在更糟糕的情况下,电极的孔隙率不足或弯曲度高可能是电极内反应分布不均匀的原因,从而导致热应力。结果,电流密度分布不均匀,这可能会在电极中引起较大的局部过电位,从而对电池的性能和耐久性产生不利影响。
技术实现要素:
4.为了克服传统电极制备工艺的缺点和不足,本发明的目的是提供一种直接氨燃料
的质子型陶瓷燃料电池及其制备方法。本发明采用相转化法制备了便于气体传质的分级多孔结构的质子型陶瓷燃料电池的阳极支撑结构。本发明直接氨燃料的质子型陶瓷燃料电池包括阴极、电解质、过渡层和阳极,其中以prba
0.5
sr
0.5
co
1.5
fe
0.5o5 &
(pbscf)为阴极,bazr
0.1
ce
0.7y0.1
yb
0.1
(bzcyyb)为电解质,nio-bzcyyb(质量比为0.75-1.25:0.75-1.25)为过渡层,nio-bzcyyb(质量比为5.5-6.5:3-4.5)为阳极。本发明使用相转化工艺制备的阳极支撑体结构通常由表层和多孔亚层组成。多孔亚层有两种可能的孔隙结构:指状多孔结构和海绵状多孔结构。独特的指状多孔结构为燃料扩散到电极中的电化学活性位点提供了完美的通道,可以有效缓解浓差极化现象从而显着提高电化学性能。
5.本发明的目的通过以下技术方案实现:
6.一种直接氨燃料的质子型陶瓷燃料电池的制备方法,包括以下步骤:
7.1)采用相转化工艺将nio和bzcyyb制备成阳极;nio与bzcyyb的质量比为5.5-6.5:3-4.5;所述相转化工艺是指将nio和bzcyyb制备成阳极浆料;将石墨制备成石墨浆料;或者将nio和bzcyyb以及石墨制备成阳极混合浆料;然后将阳极浆料和石墨浆料或者阳极混合浆料成型,在水中浸泡,脱脂,获得阳极;
8.2)在阳极的一侧制备过渡层,在过渡层的一层制备电解质,在电解质的一侧制备阴极;所述过渡层的材料为nio与bzcyyb复合得到,nio与bzcyyb的质量比为0.75-1.25:0.75-1.25;所述电解质的材料为bzcyyb;所述阴极的材料为prba
0.5
sr
0.5
co
1.5
fe
0.5o5 &
(pbscf)。
9.所述相转化工艺制备阳极包括两种方法记为a方法或b方法;
10.a方法:将nio、bzcyyb、聚乙烯吡咯烷酮(pvp)、聚醚砜(pesf)和n-甲基吡咯烷酮(nmp)进行球磨,获得阳极浆料;将石墨、聚乙烯吡咯烷酮(pvp)、聚醚砜(pesf)和n-甲基吡咯烷酮(nmp)进行球磨,获得石墨浆料;随后将石墨浆料、阳极浆料依次在基体上流延,流延成型后浸入水中浸泡,完成相转化;然后去除基体,将成型的产物进行干燥,热处理,去除有机成分和石墨,获得阳极。
11.阳极浆料中聚乙烯吡咯烷酮(pvp)、聚醚砜(pesf)和n-甲基吡咯烷酮(nmp)的质量比为(0.1~0.3):1:(5~7);
12.nio与pvp的质量比为(10~20):(0.1~0.3);
13.nio与石墨的质量比为(5~8):1。
14.石墨浆料中石墨、聚乙烯吡咯烷酮(pvp)、聚醚砜(pesf)和n-甲基吡咯烷酮(nmp)的质量比为(2~3):(0.2~0.3):1:(5~8)。
15.石墨浆料流延后的高度为0.2~0.3毫米;阳极浆料流延后的高度为0.9-1.1mm。
16.所述浸泡的时间为8~12h。所述基体为玻璃基板。将干燥后的成型产物进行冲压成片状。所述热处理是指950~1050℃热处理1.5~2.5h,具体是指从室温缓慢升温至120℃,保温50min~70min,再缓慢升温至290~310℃,保温50min~70min,再缓慢升温至390~410℃,保温50min~70min,再缓慢升温至590~610℃,保温50min~70min,再升温至950~1050℃,保温110min~130min,最后以2~5℃/min速率降至室温。
17.b方法:将nio、bzcyyb、石墨、聚乙烯吡咯烷酮(pvp)、聚醚砜(pesf)和n-甲基吡咯烷酮(nmp)进行球磨,获得阳极混合浆料;将阳极混合浆料置于模具中或将模具浸泡于阳极混合浆料中,将成型的阳极混合浆料浸入水中浸泡,完成相转化;然后去除模具,将成型的
ceo
x
催化剂粉末。所述高温煅烧的条件为900-1000℃高温下煅烧2-5h。煅烧完成后,球磨,过筛。
29.硝酸铁和硝酸铈中fe:ce摩尔比为(5~7):(3~5),优选为(6~7):(3~4)。ce、fe总的金属离子:甘氨酸:一水合柠檬酸的摩尔比为(0.75-1.25):(0.5-1.0):(0.5-1.0)。
30.加入甘氨酸和柠檬酸前,溶液的温度升至80-100℃。
31.负载时,将fe-ceo
x
催化剂粉末、松油醇和乙基纤维素制备成浆料,然后涂覆在质子型陶瓷燃料电池阳极的一侧或内侧,加热处理。所述加热处理的条件为900~1000℃热处理1.5~2.5h。
32.在质子型陶瓷燃料电池阳极的一侧或内侧涂覆催化剂浆料前,可以在涂覆阴极浆料后,在阳极一侧或内侧涂覆催化剂浆料,然后一起加热处理。
33.所述直接氨燃料的质子型陶瓷燃料电池从下到上或从内到外依次包括阳极,过渡层,电解质,阴极。阳极为nio-bzcyyb(质量比为5.5-6.5:3-4.5,优选5.5-6.5:3.5-4.5),过渡层为nio-bzcyyb(质量比为0.75-1.25:0.75-1.25),电解质为bzcyyb,阴极为pbscf。
34.所述电解质为bazr
0.1
ce
0.7y0.1
yb
0.1
(bzcyyb)。
35.所述过渡层为ni-bzcyyb,质量比为0.75-1.25:0.75-1.25。
36.所述阳极为ni-bzcyyb,质量比为5.5-6.5:3-4.5(优选为5.5-6.5:3.5-4.5)构成的复合阳极。
37.本发明对相转化制备的管式sofc在氨气为燃料下进行了电化学性能进行了评价。本发明制备的电池具有较高的输出功率密度和较好的稳定性。
38.相转化时,当聚合物溶液(阳极浆料)浸入非溶剂浴(水)中时,溶剂(阳极浆料中的nmp)和非溶剂瞬间发生传质,使聚合物溶液从热力学稳定状态变为亚稳态或不稳定状态。不稳定的聚合物溶液会经历液-液相分离过程以降低其自由能。在液-液相分离过程中,最初的均相聚合物溶液被分成两种具有不同组成的液相,即贫聚合物相和富聚合物相,同时最终分别形成孔和膜。本发明是利用相转化工艺制备阳极支撑体。相转化法制备的电极的典型结构是表面为致密的皮肤层,中间为指状孔层,下层为海绵层。其中指状孔层在阳极支撑体中占比较大,而且它可以为气体传输提供通道。独特的指状多孔结构为燃料扩散到电极中的电化学活性位点提供了完美的通道,这被认为显著提高了电化学性能。本发明在利用相转化法制备片状sofc时,在流延阳极支撑体前,先流延了一层石墨浆料。目的是为了让石墨浆料进入到海绵层中。在高温热处理时,石墨将被完全除去,指状孔得以暴露出来,更加有利于传质。
39.与现有技术相比,本发明具有以下有益效果:
40.本发明的方法简单,相转化法制备的用于直接氨燃料的质子陶瓷型固体氧化物燃料电池具有较高的功率密度和良好的稳定性。如:fe-ceo
x
/(nio-bzcyyb(阳极,质量比为5.5-6.5:3-4.5)/nio-bzcyyb(阳极,质量比为0.75-1.25:0.75-1.25)/bzcyyb(电解质)/pbscf(阴极)的单电池在700℃的功率密度在氢气气氛下达到1.33w cm-2
,在氨气下达到1.06w cm-2
。在阳极内表面添加一层fe-ceo
x
催化剂可以在氨气到达阳极之前促进氨气分解,从而保护阳极。在氧化铈中掺入铁可以有效地阻碍铁和氨之间的反应,从而保护铁。
附图说明
41.图1为相转化结合流延技术制备片状sofc流程示意图;
42.图2为相转化技术制备管式sofc流程示意图;
43.图3为相转化结合流延制备的片状sofc在氨燃料下的输出功率表征;
44.图4为不同比例的fe-ceo
x
催化剂在600℃(a)和950℃(b)下煅烧后的xrd图谱;73表示fe:ce摩尔比为7:3;64表示fe:ce摩尔比为6:4;55表示fe:ce摩尔比为5:5;37表示fe:ce摩尔比为3:7;
45.图5为fe-ceo
x
催化剂在氨气或氢气气氛下处理10h后的xrd表征图谱;64表示fe:ce摩尔比为6:4;
46.图6为使用h2或纯nh3为燃料,分别对以fe或fe-ceo
x
作为催化剂的fe电池或fe-ceo
x
电池的单电池进行输出功率的测试;a为h2为燃料;b为纯nh3为燃料;
47.图7为不同比例的催化剂制备的单电池在700℃进行输出功率测试;
48.图8为以氨为燃料时,fe电池和fe-ceo
x
电池在650℃下在0.5a cm-2
的恒定电流密度下的短期稳定性测试曲线;
49.图9为ni-bzcyyb|bzcyyb|pbscf单电池在氨气气氛下测试后管状电池的截面sem图;(a)管的整体视图;(b)具有阴极(pbscf)、电解质(bzcyyb)、阳极功能层(afl)和阳极支撑层(asl)的电池的图像;(c)催化fe-ceo
x
层和asl的详细sem图像;(d)fe-ceo
x
层的近视图;其中,b和c分别为a中方框部分的放大图。
具体实施方式
50.下面结合具体实施例对本发明作进一步详细地描述,但本发明的实施方式不限于此。
51.图1为相转化结合流延技术制备片状sofc流程示意图;
52.图2为相转化技术制备管式sofc流程示意图。
53.实施例1
54.本实施例提供相转化法制备片状sofc(ni-bzcyyb(阳极)/(ni-bzcyyb(过渡层,质量比为1:1)/bzcyyb(电解质)/pbscf(阴极))的工艺,具体步骤如下:
55.1)采用固相法制备bzcyyb粉末:将54.644g高纯度碳酸钡(纯度为99.99%)、3.42g氧化锆(纯度为99.99%)、33.361g氧化铈(纯度为99.99%)、5.456g氧化镱(纯度为99.99%)和3.12g氧化钇(纯度为99.99%)粉末一同溶解在适量乙醇中,球磨24h混合均匀,将混合的溶液放于烘箱烘干后得到干燥的粉体,然后将干燥的粉体采用14mpa的压力压成片,置于马弗炉中于1100煅烧12h。然后将煅烧的后粉末加入乙醇中再次高能(500r/min)球磨4h,烘干后采用14mpa的压力压片,后再次置于马弗炉中于1100℃煅烧12h,得到纯钙钛矿相(在高温下只煅烧一次,获得的钙钛矿相不纯,因此,需要经历两次煅烧);将得到的粉加入乙醇高能(500r/min)球磨4h后,过160目的筛子即可得到所需的bzcyyb粉体;
56.2)制备阳极浆料:称取45g nio、21.7g bzcyyb、0.75g pvp、3g pesf、18g nmp,先高能球磨6h(转速为500r/min),再滚筒球磨一天(转速为220r/min),再高能球磨6h,继续滚筒球磨一天,即可获得阳极浆料;
57.3)制备分散剂:称取1g聚乙烯醇缩丁醛(pvb),1g三乙醇胺和8g乙醇,在70℃烘箱
中放置一周直到溶液呈粘稠状态;
58.4)制备电解质浆料:称取1.0g bzcyyb粉末,加入0.5g分散剂,10g乙醇,滚筒球磨一天,获得电解质浆料;
59.5)制备过渡层浆料:称取0.5g bzcyyb,0.5g nio粉末,加入0.5g分散剂,10g乙醇,滚筒球磨一天,获得电解质浆料;
60.6)制备石墨浆料:称取7g石墨,0.625g pvp,2.5g pesf,15g nmp,滚筒球磨一天,获得石墨浆料;
61.7)相转化结合流延技术制备阳极支撑体:首先,将石墨浆料流延在玻璃基板上,随后立即流延阳极浆料;刮刀的高度分别调整到0.25mm和1mm;将从流延成型获得的薄片立即与玻璃基板一起浸入水中10h,以完成相转化过程;
62.8)电池脱脂:取出薄片并在环境空气中干燥12h,然后冲压成片状(直径约1.5cm)并在1000℃预热2h;为了除去有机成分,同时保持良好的机械强度,应用了缓慢加热过程(从室温(20℃),升温到120℃(0.5℃/min),恒温1h;再升温到300℃(0.5℃/min),恒温1h。再升温到400℃(0.5℃/min),恒温1h,升温到600℃(0.5℃/min),恒温1h;升温到1000℃(2℃/min),恒温2h;再以3℃/min的速率降至室温);
63.9)滴涂过渡层和电解质浆料:将过渡层(100ul)和电解质浆料(80ul)滴涂在阳极基底(是指脱脂后的nio bzcyyb,脱脂完成后,石墨已经被去除)上(先将过渡层滴涂在脱脂后的阳极支撑体上,等过渡层风干以后(大约半个小时),再滴涂电解质浆料),并在1450℃下共烧结5h;在高温烧结过程中,电池堆叠(阳极对阳极,电解质一侧掩埋在bzcyyb粉末里)在一起以避免变形,并用新鲜的bzcyyb粉末掩埋以最小化ba蒸发的影响;
64.10)采用燃烧法制备阴极材料(prba
0.5
sr
0.5
co
1.5
fe
0.5o5 &
):称取8.7g pr(no3)3·
6h2o、2.614g ba(no3)2、2.116g sr(no3)2、8.731g co(no3)2·
6h2o和4.04g fe(no3)3·
6h2o,将其溶解在去离子水中;溶液加热到90℃;然后向溶液中加入甘氨酸和柠檬酸作为络合剂;pr、ba、sr、co、fe总的金属离子:甘氨酸:一水合柠檬酸的摩尔比为(0.75-1.25):(0.5-1.0):(0.5-1.0);将温度升高至140℃并恒温,直到所有的水分蒸干,形成凝胶状物质;将凝胶状物质转移到烘箱中并加热至300℃,保温7h,得到蓬松的阴极材料前驱体粉末;把前驱体粉末在950℃高温下煅烧,煅烧的时间为3h;将煅烧产物先高能球磨2h,再过160目筛网以获得精细pbscf粉末;
65.11)丝网印刷阴极:将由pbscf粉末、松油醇和乙基纤维素(重量比为1:0.76:0.04)组成的空气电极浆料丝网印刷在活性面积为0.28cm2的致密电解质上;然后在950℃下烧制2h以实现电解质和空气电极之间的良好结合。
66.图3为相转化结合流延制备的片状sofc在氨燃料下的输出功率表征。相转化结合流延技术制备的片状sofc可以在氨燃料下工作。在650℃时,输出功率密度达到0.8w cm-2
。
67.实施例2
68.在使用氨气为燃料时,由于镍基阳极与氨气的相互作用会导致阳极活性不足,耐久性降低。因此,在管状阳极支撑体内侧负载了一层fe-ceo
x
催化剂来保护阳极。fe-ceo
x
催化剂可以在氨气到达阳极之前使其分解成氮气和氢气来避免阳极被损害。本实施例提供相转化法制备管式sofc(fe-ceo
x
催化剂/ni-bzcyyb(阳极,质量比为6:4)/(ni-bzcyyb(过渡层,质量比为1:1)/bzcyyb(电解质)/pbscf(阴极))的工艺,具体步骤如下:
69.1)制备阳极浆料:称取32.4g nio、21.6g bzcyyb、7.5g石墨、0.75g pvp、3g pesf、18g nmp,先高能球磨4h(500r/min),再滚筒球磨2天(250r/min),即可获得阳极浆料;
70.2)制备分散剂:称取1g聚乙烯醇缩丁醛(pvb),1g三乙醇胺和8g乙醇,在70℃烘箱中放置一周直到溶液呈粘稠状态;
71.3)制备电解质浆料:称取1.0g bzcyyb粉末,加入0.5g分散剂,10g乙醇,滚筒球磨一天,即可获得电解质浆料;
72.4)制备过渡层浆料:称取0.5g bzcyyb,0.5g nio粉末,加入0.5g分散剂,10g乙醇,滚筒球磨一天,即可获得电解质浆料;
73.5)相转化技术制备阳极支撑体:将干净的玻璃棒(直径为4mm)浸泡在阳极浆料中,使其均匀地附着在棒上;然后将棒慢慢拉出,垂直放入去离子水中10h,以完成相转化过程,获得管状阳极支撑体;
74.6)电池脱脂:通过相转化获得的阳极支撑体在环境空气中干燥过夜,并在1000℃下预热2h,以除去有机组分并保持足够的机械强度;
75.7)浸渍过渡层和电解质浆料:在浸渍功能层浆料之前,用蜡密封管的一端,以防止过渡层浆料接触管内的阳极支撑;将阳极支撑体依次在过渡层浆料和电解质浆料中各自浸泡7次,然后在70℃的烘箱中加热以从管子中除去石蜡,随后在1450℃下共烧结5h;
76.8)涂覆阴极:将由1g pbscf、0.75g松油醇和0.05g乙基纤维素组成的阴极浆料刷涂在电解质表面上;涂覆阴极浆料时,每个管状电池上阴极浆料的宽度控制在5mm,电池的有效面积可以通过测量管的直径来计算;将电池加热至950℃保持2h,以实现电解质和阴极之间的良好粘附;
77.9)燃烧法制备不同摩尔比的fe-ceo
x
催化剂:以fe-ceo
x
催化剂(fe:ce=6:4)为例,称取8.709g fe(no3)3·
6h2o和7.827g 2.614g ce(no3)3将其溶解在100ml去离子水中,加热到90℃,当硝酸铁和硝酸铈完全溶解后,向溶液中加入甘氨酸(3.378g)和柠檬酸(9.375g)作为络合剂;将温度升高至140℃并恒温,直到所有的水分蒸干,形成凝胶状物质;将凝胶状物质转移到烘箱中并加热至300℃,保温6h,得到蓬松的阴极材料前驱体粉末;将前驱体粉末在950℃高温下煅烧,煅烧的时间为2h;将煅烧产物先高能球磨2h,再过160目筛网以获得精细fe-ceo
x
催化剂(fe:ce=6:4)粉末;将fe-ceo
x
催化剂(fe:ce=6:4)粉末、松油醇和乙基纤维素(重量比为1:0.76:0.04)在研钵中研磨1-2h,即可得到fe-ceo
x
催化剂(fe:ce=6:4)浆料;调整fe:ce的摩尔比为7:3,5:5,3:7,其他条件不变;或者调整煅烧温度为600℃,其他条件不变;
78.10)负载fe-ceo
x
催化剂:在涂覆阴极浆料后,在管内壁的一半涂满催化剂浆料(fe-ceo
x
复合物);含有阴极和催化剂浆料的电池在950℃下一起烧制2h;烧制完成后,在阳极一侧先集流,再涂覆催化剂浆料(负载催化剂的厚度约为30-50μm;第一遍催化剂只涂在了管子的一半区域,集流完成后,再把另一半涂敷催化剂)。
79.表征结果:
80.(1)xrd表征
81.图4为不同比例的fe-ceo
x
催化剂在600℃和950℃下煅烧后的xrd图谱。从图中可以看出,样品表现出良好的双钙钛矿相。fe-ceo
x
催化剂仅显示出ceo2的峰,而检测不到fe2o3的峰,这表明铁已经成功地结合到ceo2晶格中。当fe的比例高时(例如,fe:ce=7:3,摩
尔比),观察到低强度的峰,表明样品的结晶差。尽管如此,样品的主峰可以粗略地归因于ceo2,这表明fe的进一步增加可能导致掺入ceo2的失败。可见,通过溶液燃烧法成功合成了fe-ceo
x
复合催化剂,而不是单独的fe2o3和ceo2。与ceo2的峰相比,不同摩尔比的fe-ceo
x
复合催化剂的峰变宽,表明fe-ceo
x
复合催化剂的结晶度较低。尽管主要在催化剂中观察到来自ceo2的峰,但是在950℃煅烧后出现了强度较弱的fe2o3峰。fe比例超过7:3的复合材料显示出较强的fe2o3峰强度,表明在较高温度下的热处理导致fe从ceo2晶格中轻微分离,因此形成了少量的fe2o3。换句话说,即使在高温处理后,催化剂也可以很大程度上保持fe-ceo
x
复合物的形式。在950℃煅烧后的fe-ceo
x
催化剂的峰比在600℃煅烧后的峰窄且尖锐得多,这表明在高温处理后fe-ceo
x
催化剂的结晶度提高了。
82.图5为fe-ceo
x
催化剂在氨气和氢气气氛下处理10h后的xrd表征图谱。在氢气中还原10h后,可以从粉末中观察到fe,这表明苛刻的还原条件可以将fe从ceo2晶格中分离出来。当fe-ceo
x
催化剂在nh3中处理10h时,从xrd图中仅观察到fe2n的小峰。表明在氨气气氛中,来自fe-ceo
x
催化剂的fe可以大量保留在ceo2晶格中,fe2o3转化成了fe2n。fe-ceo
x
催化剂样品中少量的fe2n可归因于先前热处理中沉淀的相对少量的fe2o3。fe-ceo
x
催化剂中ce的存在被证明是对氨的稳定剂。在氧化铈中掺入铁可以有效地阻碍铁和氨燃料之间的反应,从而保护铁。
83.(2)输出功率表征
84.图6为以氢气或纯nh3为燃料,分别对以fe催化剂或fe-ceo
x
催化剂作为fe电池或fe-ceo
x
电池的单电池(两电池为fe|ni-bzcyyb(阳极,质量比为6:4)/(ni-bzcyyb(过渡层,质量比为1:1)/bzcyyb(电解质)/pbscf(阴极)的单电池,fe-ceo
x
|ni-bzcyyb(阳极,质量比为6:4)/(ni-bzcyyb(过渡层,质量比为1:1)/bzcyyb(电解质)/pbscf(阴极)的单电池)进行电化学测试,其中a为h2为燃料;b为纯nh3为燃料。fe电池的峰值功率密度(ppd)相对较低(使用纯氢作为燃料,在700℃时约0.96w
·
cm-2
,如图6中a所示)。以纯氢为燃料,fe-ceo
x
电池在700℃时的ppd约为1.33w
·
cm-2
,比相同条件下的fe电池高出38.5%。类似地,当氨用作燃料时,fe-ceo
x
电池的ppd(图6的b中,700℃时约1.06w
·
cm-2
)是fe电池的1.36倍(700℃时约0.78w
·
cm-2
)。由于fe-ceo
x
电池和fe电池的制备工艺和测试条件保持相同,因此fe-ce电池性能的显著提高可归因于fe-ceo
x
催化剂。
85.图7为不同比例的催化剂制备的电池的电化学性能图(在700℃进行输出功率测试)。无论是以氢气还是氨气为燃料,当fe-ceo
x
催化剂的比例为7:3(fe:ce摩尔比)和6:4(fe:ce摩尔比)时,电化学性能优于比例为5:5的fe-ceo
x
电池。
86.(3)长期稳定性表征
87.图8所示的是,当以氨为燃料时,fe电池和fe-ceo
x
电池在650℃下在0.5a cm-2
的恒定电流密度下的短期稳定性测试。fe-ceo
x
催化剂的比例为6:4(fe:ce摩尔比)时,电池在氨气气氛下的稳定性要远远高于其他电池。
88.(4)sem表征
89.图9为fe-ceo
x
(催化剂)/nio-bzcyyb(阳极,质量比为6:4)/nio-bzcyyb(过渡层,质量比为1:1)/bzcyyb(电解质)/pbscf(阴极)(实施例3制备的电池)在氨气气氛下测试后管状电池的截面sem图;(a)管的整体视图;(b)具有阴极(pbscf)、电解质(bzcyyb)、阳极功能层(afl)和阳极支撑层(asl)的电池的图像;(c)催化fe-ceo
x
层和asl的详细sem图像;(d)
fe-ceo
x
层的放大图。
90.从图9的b中可以看出bzcyyb和各层之间的边界非常清晰,表明电解质已经很好地附着在阳极或阴极上。从图9的c中可以看出,fe-ceo
x
催化剂(25-30μm)与阳极的海绵层结合良好。图9中d为催化剂层的放大图,可以看出铁离子结合到二氧化铈中并非常均匀地分散。
91.使用氨作为燃料的负载fe-ceo
x
催化剂层的质子陶瓷燃料电池的反应过程可分为五个步骤:(i)燃料气体被吸附在催化剂表面上;(ii)氨气分解成氮气和氢气;(iii)氢气经历电化学反应产生质子和电子;(iv)质子穿过质子导体电解质(bzcyyb)到达阴极(pbscf);以及(v)通过外部电路到达阴极的质子、氧化剂和电子反应生成水。如果阳极表面不加一层催化剂,ni会与氨气发生反应,破坏阳极表面,影响电池的活性和寿命。氨气可以在与阳极接触之前,在fe-ceo
x
催化剂层上被分解,从而减少镍基阳极和氨气的直接接触。
再多了解一些
本文用于企业家、创业者技术爱好者查询,结果仅供参考。