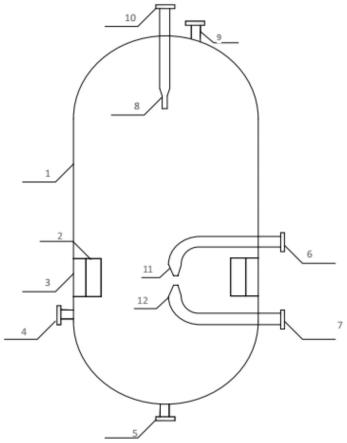
1.本发明涉及石油化工、煤化工技术领域,具体涉及一种羰基合成反应器及其工作方法。
背景技术:
2.醋酸作为一种重要的化学中间体和化工产品,主要用于生产醋酸乙烯单体、对苯二甲酸、醋酸酯类、醋酸酐、卤代乙酸、醋酸纤维素及其它醋酸衍生物等。此外,醋酸还可进一步加工成农药、医药、染料、合成纤维和粘合剂等多种产品。甲醇羰基合成法是工业上生产醋酸的主要方法,液相甲醇进料和气相co进料在催化剂体系中合成醋酸,采用此法生产的醋酸已占全球醋酸总产量的80%以上,成为醋酸生产的主要工艺。传统的羰基合成醋酸使用的反应器中多采用机械搅拌,由于甲醇羰基反应是强腐蚀环境,设备易腐蚀、需要使用进口锆材,而搅拌釜制造和维护费用较高,同时机械搅拌存在振动大、密封易泄露的问题,难以长期稳定安全运行,需要找到替代搅拌釜的气液混合手段。
3.针对该问题,近年来,使用流体搅拌代替机械搅拌是一种重要的改进方向。由专利cn202020145192.6和cn202110014036.5可知,可以通过近壁的多个缩径式喷头喷射的反应循环液与气体分布器组合来代替机械搅拌混合反应原料和循环母液。专利cn201320103329.1和cn201310072175.9中描述,反应釜底部的中心喷嘴可以在圆环形气体分布器的作用下,混合气液两相,促进了气液两相的传质,但是竖直向上的射流对于气泡在径向上的分散有限,效果不太理想。cn201811224192.9中描述,在反应釜顶部设置至少两个靠近内壁的喷头,底部设置气体分布器,来实现流体搅拌的目的。喷头的偏心设置产生偏流现象,导致了反应器内气液分散不均,搅拌效果较传统搅拌釜的搅拌效果差。
4.综上所述,目前使用的流体搅拌技术较传统机械搅拌搅拌效果差,气液混合程度低,装置生产效率低。
技术实现要素:
5.针对上述现有技术中存在的技术问题,本发明的目的是提供一种羰基合成反应器及其工作方法,采用本发明提供的反应器,不仅可以避免机械搅拌存在的机械密封泄露问题,同时降低了设备维护成本,与此同时可加强反应器内的气液混合传质效果,提高了反应速率与原料利用率,实现装置长期安全稳定运行的目的。
6.本发明可通过以下技术方案实现:
7.本发明首先提供了一种羰基合成反应器,其包括反应器壳体、至少一个与壳体相切的液体入口、顶部液体入口、循环液出口、反应液出口、气体出口、两个co入口;两个co入口位于反应器壳体内的端部分别设有第一喷嘴和第二喷嘴;所述第一喷嘴和第二喷嘴出口相向设置,且位于同一竖直线上。
8.作为本发明的优选方案,所述第一喷嘴和第二喷嘴出口的co流量以一定的脉冲频率发生周期性变化,且二者存在相位差π。
9.作为本发明的优选方案,液体入口位于反应器壳体内的端部设有第三喷嘴;所述第一喷嘴和第三喷嘴的出口竖直向下,第二喷嘴的出口竖直向上。
10.作为本发明的优选方案,第三喷嘴的出口位于液面下方0.1~0.5倍液位高度。
11.作为本发明的优选方案,所述液体入口的布置高度处于所述第一喷嘴和第二喷嘴之间。
12.作为本发明的优选方案,所述液体入口设有3个,且位于反应器壳体同一高度,3个液体入口在圆周方向上互成120
°
。
13.作为本发明的优选方案,所述3个液体入口分别为甲醇进液口、催化剂母液进液口和稀酸混合液进液口。
14.作为本发明的优选方案,所述反应器壳体由反应釜筒体和上下半球形/椭球形封头构成。
15.作为本发明的优选方案,所述第一喷嘴和第二喷嘴的间距为反应釜直径的0.01~0.2倍。
16.本发明的优选方案中:所述循环液出口和所述反应液出口位于所述与壳体相切的液体入口下方。
17.优选地,循环液出口位于反应器底部。
18.本发明技术方案中:所述与壳体相切的液体入口位于筒体距底部1/2~1/3处。
19.本发明技术方案中:所述与壳体相切的液体入口上装有起旋器。
20.优选地,所述起旋器的径向厚度为反应釜直径的0.03~0.2倍。
21.优选地,所述co入口的端部喷嘴的喷口直径为反应釜直径的0.01~0.1倍。
22.优选地,所述co入口的端部喷嘴的喷口间距为反应釜直径的0.01~0.2倍。
23.本发明技术方案中,所述co入口端部喷嘴出口的co流量以一定的脉冲频率发生变化,且二者存在相位差π。
24.优选地,co流量变化频率为2~20hz。
25.本发明技术方案中,所述顶部液体入口的端口喷嘴位于液面下方。
26.优选地,所述顶部液体入口的端口喷嘴位于液面下方0.1~0.5倍液位高度。
27.优选地,所述co入口端部的喷嘴流速为8~25m/s。
28.优选地,所述顶部液体入口端部的喷嘴流速为8~25m/s。
29.优选地,所述起旋器内液体流速为5~15m/s。
30.本发明还提供了一种基于上述的反应器的羰基合成方法:
31.co气体从两个co入口进入反应器,并在第一喷嘴和第二喷嘴处对喷;第一喷嘴和第二喷嘴出口的co流量以一定的脉冲频率发生周期性变化,且二者存在相位差π,第一喷嘴和第二喷嘴流量的变化使得喷溅的co气体上下摆动,产生大量co小气泡,促进co气体在整个反应釜中均匀分布;
32.甲醇、催化剂母液和稀酸混合液分别由三个液体入口沿着壳体切线方向进入反应器;在起旋器的作用下呈涡旋式流动,与co小气泡相切运动,气泡受到剪切作用形成更小的气泡,利于气液传质过程;
33.顶部甲醇液体射流搅拌混合液,使得co气体分布均匀,同时下沉的甲醇液体与上升的co气体上下相互运动,二者混合均匀,利于反应速率的提升。
34.与现有技术相比,本发明的有益效果为:本发明通过co气体脉冲对喷,混合液涡旋流动,甲醇进料液射流搅拌,并与起旋器相配合,改善了co气体以及原料液在反应釜内的分布。整个反应釜中没有传统搅拌部件,既消除了机械搅拌存在的机械密封泄露问题,保障了装置的安全运行,又避免搅拌釜的维修与替换,降低了维护成本,降低装置功耗。在高速气体对喷形成微小气泡,并在涡旋液体的剪切作用下,反应釜内的气泡进一步减小,提高了气液传质效率与速率,使得产能提升。
附图说明
35.图1是本发明提供的一种羰基合成反应器的结构示意图。
36.图2是本发明提供的一种起旋器的结构示意图。
37.图3是本发明提供的一种喷嘴结构示意图。
38.其中:1-反应器壳体;2-起旋器;3-至少一个与壳体相切的液体入口;4-反应液出口;5-循环液出口;6-上部co入口;7-下部co入口;8-第三喷嘴(顶部液体入口端部喷嘴);9-气体出口;10-顶部液体入口;11-第一喷嘴(上部co入口端部喷嘴);12-第二喷嘴(下部co入口端部喷嘴)。
具体实施方式
39.下面结合实施例对本发明提供的羰基合成反应器做进一步说明,但本发明的保护范围不限于此:
40.图1所示为本发明提供的一种羰基合成反应器,包括反应器壳体1、起旋器2、至少一个与壳体相切的液体入口3、反应液出口4、循环液出口5、上部co入口6、下部co入口7、气体出口9、顶部液体入口10;所述的反应器主体由反应釜筒体和上下半球形/椭球形封头构成;所述液体入口3设有3个,分别为甲醇进液口、催化剂母液进液口和稀酸混合液进液口,且位于反应器壳体同一高度互成120
°
,其中液体入口与壳体相切;所述顶部液体入口位于反应釜内的端口设有第三喷嘴8;所述上部co入口位于反应釜内的端口设有第一喷嘴11;所述下部co入口位于反应釜内的端口设有第二喷嘴12;所述第三喷嘴8和第一喷嘴11的出口竖直向下,第二喷嘴12的出口竖直向上,第一喷嘴11和第二喷嘴12相向设置,且位于同一竖直线上;所述液体入口3轴向位置处于所述第一喷嘴11和第二喷嘴12之间;所述第一喷嘴11和第二喷嘴12出口的co流量以一定的频率发生周期性变化,且二者存在相位差π,两者变化周期相同。循环液从所述循环液出口5流出后经外循环换热器冷却后再通过顶部液体入口10或液体入口3返回反应釜;甲醇原料液、催化剂母液和稀酸混合液分别由三个液体入口3沿着壳体切线方向进入反应器。其中,催化剂母液是指从闪蒸罐底部返回反应釜的液体。在反应压力2.8mpa、温度190℃条件下,通入反应釜的甲醇和co在催化剂的作用下反应生成醋酸,同时产生少量副产物醋酸甲酯。
41.采用上下两股co气体对喷,气体经撞击分散从中心向四周溅射,同时由于两者存在相位差π,当上进气口流量最大时,下进气口流量最小。当下进气口流量最小时,上进气口流量最大。两者变化导致喷溅的气体也上下摆动,在混合液中产生大量小气泡,有利于co气体在整个反应釜中均匀分布。混合液从两侧通入,在起旋器的作用下呈涡旋式流动,与小气泡相切运动,气泡受到剪切作用形成更小的气泡,有利于气液传质过程,提升反应速率。顶
部甲醇液体射流搅拌混合液,使得co气体分布均匀,同时下沉的甲醇液体与上升的co气体上下相互运动,二者混合均匀,有利于反应速率的提升。
42.作为一种具体的实施方法,第一喷嘴11和第二喷嘴12的co流量控制方式为正弦函数。
43.作为一种具体的实施方法,所述液体入口3位于筒体距底部1/2~1/3处;所述起旋器2的径向厚度为反应釜直径的0.03~0.2倍;所述的上部co入口端部喷嘴11和下部co入口端部喷嘴12的喷口直径为反应釜直径的0.01~0.1倍;所述的上部co入口端部喷嘴11和下部co入口端部喷嘴12的喷口间距为反应釜直径的0.01~0.2倍;所述喷嘴8的出口位于反应釜液面下方,优选为液面下方0.1~0.5倍液位高度;所述的喷嘴11和喷嘴12出口的co流量以一定的频率发生变化,且二者存在相位差π,优选变化频率为2~20hz。
44.在一个优选的实施案例中,所述顶部液体入口端口喷嘴8出口流速为8~25m/s。
45.在一个优选的实施案例中,所述co入口端口喷嘴11和喷嘴12出口流速为8~25m/s。
46.在一个优选的实施案例中,所述起旋器内液体流速为5~15m/s。
47.实施例1
48.采用如图1所示羰基合成反应器,反应釜筒体高5m,直径3m,半球形封头直径3m,反应釜液位高度5.5m。起旋器(如图2所示)直径为2.4m,上部co入口端部喷嘴11和下部co入口端部喷嘴12的喷口直径为100mm,上部co入口端部喷嘴11和下部co入口端部喷嘴12的喷口间距为200mm,喷嘴8出口位于反应釜液面下方1.2m。喷嘴11和喷嘴12出口的co流量以5hz的脉冲频率发生变化,且二者存在相位差π,两喷嘴的出口流速变化范围为8-15m/s;顶部液体入口端口喷嘴8出口流速为8m/s;甲醇原料液、催化剂母液和稀酸混合液分别由三个液体入口3沿着壳体切线方向进入反应器,在起旋器的作用下呈涡旋式流动,起旋器内液体流速为10m/s。循环液从循环液出口5流出经外循环换热器冷却后通过顶部液体入口10进入反应釜,co气体原料从上部co入口6和下部co入口7进入反应釜,反应液从反应液出口4排出。在反应压力2.8mpa、温度190℃条件下,在催化剂系统中,甲醇与co生成醋酸,并产生少量醋酸甲酯,运行结果表明,反应釜运行平稳,反应釜底部温度波动在2℃以内,副产物醋酸甲酯含量为0.52%。
49.对比例1
50.在与实施例1相同的温度、压力和催化体系下,与实施例1的区别仅在于co全部从喷嘴12进入反应器;甲醇原料液、催化剂母液和稀酸混合液分别由三个液体入口3沿着壳体切线方向直接进入反应器。运行结果表明,反应釜运行波动较大,反应釜底部温度波动在8-10℃以内,副产物醋酸甲酯含量为1.54%。
51.实施例2
52.在与实施例1相同的温度、压力和催化体系下,与实施例1的区别仅在于上部co入口端部喷嘴11和下部co入口端部喷嘴12的间距为500mm。运行结果表明,反应釜运行平稳,反应釜底部温度波动在4℃以内,副产物醋酸甲酯含量为0.78%。
53.实施例3
54.在与实施例1相同的温度、压力和催化体系下,与实施例1的区别仅在于喷嘴11和喷嘴12出口的co流量以10hz的脉冲频率发生变化,所述顶部液体入口端口喷嘴8出口流速
为12m/s。运行结果表明,反应釜运行平稳,反应釜底部温度波动在1℃以内,副产物醋酸甲酯含量为0.42%。
55.以上所述仅为本发明的优选实施例,并不用以限制本发明,凡在本发明的精神和原则之内所作的任何修改、等同替换、改进等,均应包含在本发明的保护范围之内,本发明请求保护的技术内容已经全部记载在权利要求中。
再多了解一些
本文用于企业家、创业者技术爱好者查询,结果仅供参考。