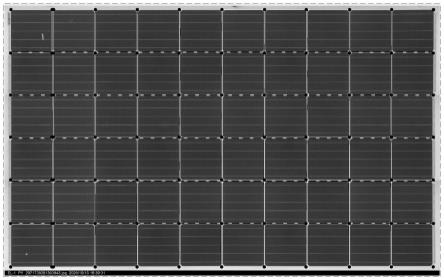
1.本发明涉及光伏组件尺寸检测技术领域,具体涉及一种光伏组件尺寸缺陷检测方法,尤其涉及一种基于图像边缘检测和深度学习的神经网络模型的光伏组件尺寸缺陷检测方法。
背景技术:
2.光伏组件的优质率、美观性,与光伏组件的电池片之间的间距直接相关,因为电池片之间的间距的不达标,轻则影响光伏组件美观,重则导致光伏组件上电池片间导电线排错,最终影响电池组件的使用寿命。然而,目前光伏组件尺寸缺陷需通过人工眼检,检查速度慢、容易疲劳,可能会漏掉部分光伏组件尺寸缺陷,导致不合格产品流入市场。
技术实现要素:
3.本发明的目的在于克服现有技术的缺陷,提供一种光伏组件尺寸缺陷检测方法,能准确、快速检测出光伏组件的尺寸缺陷。
4.为实现上述目的,本发明采用了如下技术方案:
5.一种光伏组件尺寸缺陷检测方法,包括以下步骤:
6.步骤1,获取待检测光伏组件的光伏组件图像并依据光伏组件图像获得光伏组件的各电池片的电池片坐标cell
nm
,电池片坐标cell
nm
为[x1,y1,x2,y2,rown,colm];依据所述电池片坐标cell
nm
,获取同一列中相邻电池片之间的串间距区域和同一行中相邻电池片之间的片间距区域;依据所述光伏组件图像、串间距区域和片间距区域,获取串间距区域图像和片间距区域图像;
[0007]
其中,(x1,y1)和(x2,y2)分别电池片的左上角和右下角的坐标,rown表示电池片位于第n行,colm表示电池片位于第m列,n和m均为≥1的整数;
[0008]
步骤2,依据所述串间距区域图像和片间距区域图像,计算串间距、片间距和错位值;若所述串间距在串间距阈值范围内则合格,片间距在片间距阈值范围内则合格,错位值在错位值阈值范围内则合格;
[0009]
其中,所述串间距为同一列中相邻电池片之间的间距,片间距为同一行中相邻电池片之间的间距,错位值表示呈田字形分布的四块电池片之间的错位程度。
[0010]
优选的,在步骤1中,依据所述电池片坐标cell
nm
,获取电池片的电池片高度cellheight和电池片宽度cellwidth;依据所述电池片坐标cell
nm
、电池片高度cellheight、电池片宽度cellwidth,获取串间距区域和片间距区域。
[0011]
优选的,所述串间距区域为[cell
nm
[x1],cell
nm
[y2]-cellheight//a,cell
nm
[x2],cell
(n 1)m
[y1] cellheight//a];
[0012]
其中,cell
nm
[x1]为第n行第m列的电池片的左上角的x坐标,cell
nm
[y2]为第n行第m列的电池片的右下角的y坐标,cell
nm
[x2]为第n行第m列的电池片的右下角的x坐标,cell
(n 1)m
[y1]第n 1行第m列的电池片的左上角的y坐标,15≤a≤25;依据所述串间距区域
在光伏组件图像上分割出串间距区域图像。
[0013]
优选的,所述片间距区域为[cell
nm
[x2]-cellwidth//b,cell
nm
[y1],cell
n(m 1)
[x1] cellwidth//b,cell
nm
[y2]];其中,cell
nm
[x2]为第n行第m列的电池片的右下角的x坐标,cell
nm
[y1]为第n行第m列的电池片的左上角的y坐标,cell
n(m 1)
[x1]为第n行第m 1列的电池片的左上角的x坐标,cell
nm
[y2]为第n行第m列的电池片的右下角的y坐标,4≤b≤8;
[0014]
依据所述片间距区域,在光伏组件图像上分割出片间距区域图像。
[0015]
优选的,在步骤1中,将所述光伏组件图像输入神经网络模型,得到各电池片的电池片坐标cell
nm
。
[0016]
优选的,步骤1还包括神经网络模型训练过程,包括以下步骤:获取多组光伏组件图像,通过labelimg软件在各光伏组件图像上将各电池片标记出来,作为训练数据对神经网络模型进行训练。
[0017]
优选的,所述步骤2包括以下子步骤:
[0018]
步骤2a,依据所述串间距区域图像,计算电池片的串间边缘线,依据串间边缘线计算相邻电池片之间的串间距;
[0019]
步骤2b,依据所述片间距区域图像,计算电池片的片间边缘线,依据片间边缘线计算相邻电池片之间的片间距;
[0020]
步骤2c,依据所述串间边缘线和片间边缘线,计算错位值;
[0021]
其中,所述串间边缘线为同一列的相邻电池片中,一电池片与另一电池片相对的边缘线;片间边缘线为同一行的相邻电池片中,一电池片与另一电池片相对的边缘线。
[0022]
优选的,所述步骤2a包括以下子步骤:
[0023]
步骤20a,将所述串间距区域图像,按照电池片宽度方向分割为3份,依次为首段图像,中段图像和尾段图像;
[0024]
步骤21a,分别将所述首段图像和尾段图像灰度化,获得首段灰度化图像和尾段灰度化图像;
[0025]
步骤22a,对所述首段灰度化图像的每行像素按横向求和,制成第一首段直方图,将像素和最大的一行的行数记为maxindex-col;对所述首段灰度化图像进行sobe1和闭运算,获得首段最终图像,对首段最终图像的每行像素按横向求和,制成第二首段直方图,分别计算第0至maxindex
col
行、第maxindex
col
至第二首段直方图最后一行的像素和最大值对应的行数位置,为两条首段边缘线,分别标记为shoubianyuanxian1和shoubianyuanxian2;
[0026]
重复上述过程,对所述尾段灰度化图像进行处理,得到两条尾段边缘线,分别标记为weibianyuanxian3和weibianyuanxian4;
[0027]
步骤23a,串间距=min(weibianyuanxian4-weibianyuanxian3,shoubianyuanxian2-shoubianyuanxian1)。
[0028]
优选的,所述步骤2b包括以下子步骤:
[0029]
步骤20b,将所述片间距区域图像,按照电池片高度方向分割为3份,依次为上段图像,中段图像和下段图像;
[0030]
步骤21b,分别将所述上段图像和下段图像灰度化,获得上段灰度化图像和下段灰度化图像;
[0031]
步骤22b,对所述上段灰度化图像的每列像素按纵向求和,制成第一上段直方图,
将像素和最大的一列的行数记为maxindex
row
;对所述上段灰度化图像进行sobe1和闭运算,获得上段最终图像,对上段最终图像的每列像素按纵向求和,制成第二上段直方图,分别计算第0至maxindex
row
列、第maxindex
row
至第二上段直方图最后一列的像素和最大值对应的列数位置,获得两条上段边缘线,分别标记为shangbianyuanxian5和shangbianyuanxian6;
[0032]
重复上述过程,对所述下段灰度化图像进行处理,得到两条下段边缘线,分别标记为xiabianyuanxian7和xiabianyaunxian8;
[0033]
步骤23b,片间距=min(xiabianyuanxina8-xiabianyuanxian7,shangbianyaunxian6-shangbianyuanxian5)。
[0034]
优选的,所述光伏组件中,呈田字形分布的四块电池片,分别为左上电池片、右上电池片、左下电池片和右下电池片,靠近十字形间隙的八条边缘线分别是:
[0035]
左上电池片和右上电池片的相对的两条下段边缘线,分别记为xiabianyuanxian70和xiabianyuanxian80;
[0036]
左下电池片和右下电池片的相对的两条上段边缘线,分别记为shangbianyuanxian50和shangbianyuanxian60;
[0037]
左上电池片和左下电池片的相对的两条尾段边缘线,分别记为weibianyuanxian30和weibianyuanxian40;
[0038]
右上电池片和右下电池片的相对的两条首段边缘线,分别记为shoubianyuanxian10和shoubianyuanxian20;
[0039]
则用于表示四块电池片的错位程度的错位值=max(xiabianyuanxian70-shangbianyuanxian50,xiabianyuanxian80-shangbianyuanxian60,weibianyuanxian30-shoubianyuanxian10,weibianyuanxian40-shoubianyuanxian20)。
[0040]
本发明光伏组件尺寸缺陷检测方法,通过对待检测光伏组件图像的处理,得出光伏组件的串间距、片间距和错位值等关键数据,能精准、快速检测到光伏组件的尺寸缺陷,保证了光伏组件的质量,避免不合格产品流入市场。此外,本发明光伏组件尺寸缺陷检测方法,通过神经网络模型对光伏组件图像进行处理,得到光伏组件的各电池片的电池片坐标cell
nm
,有利于提高光伏组件尺寸缺陷的检测效率。
附图说明
[0041]
图1是本发明光伏组件图像的示意图,光伏组件图像上应设有各电池片的电池片坐标cell
nm
;
[0042]
图2是本发明串间距区域的示意图;
[0043]
图3是本发明串间距区域图像的示意图,串间距区域图像按照电池片宽度方向被分为三份;
[0044]
图4a是本发明首段灰度化图像和尾段灰度化图像的示意图;
[0045]
图4b是本发明首段最终图像的示意图;
[0046]
图5是本发明第一首段直方图的示意图;
[0047]
图6是本发明第二首段直方图的示意图;
[0048]
图7是本发明片间距区域的示意图;
[0049]
图8是本发明片间距区域图像的示意图;
[0050]
图9是本发明呈田字形分布的四块电池片的示意图,示出了靠近十字形缝隙中心位置的八条边缘线;
[0051]
图10是本发明电池片的示意图,示出了电池片的八条边缘线。
具体实施方式
[0052]
以下结合附图1-10给出的实施例,进一步说明本发明的光伏组件尺寸缺陷检测方法的具体实施方式。本发明的光伏组件尺寸缺陷检测方法不限于以下实施例的描述。
[0053]
本发明光伏组件尺寸缺陷检测方法,包括以下步骤:
[0054]
步骤1,获取待检测光伏组件的光伏组件图像并依据光伏组件图像获得光伏组件的各电池片的电池片坐标cell
nm
,电池片坐标cell
nm
为[x1,y1,x2,y2,rown,colm];依据所述电池片坐标cell
nm
,获取同一列中相邻电池片之间的串间距区域和同一行中相邻电池片之间的片间距区域;依据所述光伏组件图像、串间距区域和片间距区域,获取串间距区域图像和片间距区域图像;
[0055]
其中,(x1,y1)和(x2,y2)分别电池片的左上角和右下角的坐标,rown表示电池片位于第n行,colm表示电池片位于第m列,n和m均为≥1的整数;
[0056]
步骤2,依据所述串间距区域图像和片间距区域图像,计算串间距、片间距和错位值;若所述串间距在串间距阈值范围内则合格,片间距在片间距阈值范围内则合格,错位值在错位值阈值范围内则合格;
[0057]
其中,所述串间距为同一列中相邻电池片之间的间距,片间距为同一行中相邻电池片之间的间距,错位值表示呈田字形分布的四块电池片之间的错位程度。
[0058]
本发明光伏组件尺寸缺陷检测方法,通过对待检测光伏组件图像的处理,得出光伏组件的串间距、片间距和错位值等关键数据,能精准、快速检测到光伏组件的尺寸缺陷,保证了光伏组件的质量,避免不合格产品流入市场。
[0059]
优选的,在步骤1中,将所述光伏组件图像输入神经网络模型,得到各电池片的电池片坐标cell
nm
。进一步的,步骤1还包括神经网络模型训练过程,包括以下步骤:获取多组所述光伏组件图像,通过labelimg软件在各光伏组件图像上将各电池片标记出来,得到标注好的光伏组件图片和标注生成的标注文件,作为训练数据对神经网络模型进行训练。本发明光伏组件尺寸缺陷检测方法,通过神经网络模型对光伏组件图像进行处理,得到光伏组件的各电池片的电池片坐标cell
nm
,有利于提高光伏组件尺寸缺陷的检测效率。
[0060]
需要指出的,所述神经网络模型可以通过yolo、maskrcnn、ssd、fastrcnn、fcos、centernet、conrnernet或rentina等目标检测网络经过训练后得到。
[0061]
以下为本发明光伏组件尺寸缺陷检测方法的一个实施例。
[0062]
本发明光伏组件尺寸缺陷检测方法,包括以下步骤:
[0063]
步骤1,获取待检测光伏组件的光伏组件图像并依据光伏组件图像获得光伏组件的各电池片的电池片坐标cell
nm
,电池片坐标cell
nm
为[x1,y1,x2,y2,rown,colm];依据所述电池片坐标cell
nm
,获取同一列中相邻电池片之间的串间距区域和同一行中相邻电池片之间的片间距区域;依据所述光伏组件图像、串间距区域和片间距区域,获取串间距区域图像和片间距区域图像;
[0064]
其中,(x1,y1)和(x2,y2)分别电池片的左上角和右下角的坐标,rown表示电池片
位于第n行,colm表示电池片位于第m列,n和m均为≥1的整数。
[0065]
具体的,如图1所示,为所述光伏组件图像上应设有各电池片的电池片坐标cell
nm
的示意图,光伏组件的电池片以6
×
10形式分布,即光伏组件上的电池片排布成6行、10列。
[0066]
优选的,在步骤1中,依据所述电池片坐标cell
nm
,获取电池片的电池片高度cellheight和电池片宽度cellwidth;依据所述电池片坐标cell
nm
、电池片高度cellheight和电池片宽度cellwidth,获取串间距区域和片间距区域。
[0067]
优选的,所述串间距区域为[cell
nm
[x1],cell
nm
[y2]-cellheight//a,cell
nm
[x2],cell
(n 1)m
[y1] cellheight//a];
[0068]
其中,cell
nm
[x1]为第n行第m列的电池片的左上角的x坐标,cell
nm
[y2]为第n行第m列的电池片的右下角的y坐标,cell
nm
[x2]为第n行第m列的电池片的右下角的x坐标,cell
(n 1)m
[y1]第n 1行第m列的电池片的左上角的y坐标,15≤a≤25。进一步的,a=20。
[0069]
优选的,所述片间距区域为[cell
nm
[x2]-cellwidth//b,cell
nm
[y1],cell
n(m 1)
[x1] cellwidth//b,cell
nm
[y2]];
[0070]
其中,cell
nm
[x2]为第n行第m列的电池片的右下角的x坐标,cell
nm
[y1]为第n行第m列的电池片的左上角的y坐标,cell
n(m 1)
[x1]为第n行第m 1列的电池片的左上角的x坐标,cell
nm
[y2]为第n行第m列的电池片的右下角的y坐标,4≤b≤8。进一步的,a=6。
[0071]
依据所述串间距区域和片间距区域,分别在光伏组件图像上分割出串间距区域图像和片间距区域图像。
[0072]
具体的,结合图1-3所示,以下将以[row1,col1]的电池片(即第1行第1列的电池片,记为cell
11
)和[row2,col1]的电池片(即第2行第1列的电池片,记为cell
21
)为例,说明获取串间距区域图像的过程:
[0073]
上述两块电池片的电池片坐标cell
nm
,分别为:
[0074]
cell
11
=[x1,y1,x2,y2,1,1],cell
21
=[x1,y1,x2,y2,2,1];
[0075]
电池片高度cellheight=cell
11
[y2]-cell
11
[y1];
[0076]
电池片宽度cellwidth=cell
11
[x2]-cell
11
[x1];
[0077]
串间距区域为[cell
11
[x1],cell
11
[y2]-cellheight//20,cell
11
[x2],cell
21
[y1] cellheight//20],依据串间距区域的上述四个坐标即可在光伏组件图像上分割出串间距区域图像(如图3所示)。
[0078]
具体的,结合图1、7-8所示,以下将以[row1,col1]的电池片(即第1行第一列的电池片,记为cell
11
)和[row1,col2]的电池片(即第1行第2列的电池片,记为cell
12
)为例,说明获取片间距区域图像的过程:
[0079]
上述两块电池片的电池片坐标cell
nm
,分别为:
[0080]
cell
11
=[x1,y1,x2,y2,1,1],cell
12
=[x1,y1,x2,y2,1,2];
[0081]
电池片高度cellheight=cell
11
[y2]-cell
11
[y1];
[0082]
电池片宽度cellwidth=cell
11
[x2]-cell
11
[x1];
[0083]
片间距区域为[cell
11
[x2]-cellwidth//6,cell
11
[y1],cell
12
[x1] cellwidth//6,cell
11
[y2]],依据片间距区域的上述四个坐标即可在光伏组件图像上分割出片间距区域图像(如图8所示)。
[0084]
优选的,在步骤1中,将所述光伏组件图像输入神经网络模型,得到各电池片的电
池片坐标cell
nm
。进一步的,步骤1还包括神经网络模型训练过程,包括以下步骤:获取多组光伏组件图像,通过labelimg软件在各光伏组件图像上将各电池片标记出来(即在labelimg软件中,使用creat\nrectbox功能,用鼠标在光伏组件图像上将各电池片框选出来),得到标注好的光伏组件图片和标注生成的标注文件,作为训练数据对神经网络模型进行训练。
[0085]
需要指出的,所述标注好的光伏组件图片与原来的光伏组件图像相同,只是相较于原来的光伏组件图像,增加了与光伏组件图像一一对应的标注文件,标注文件的名称为“图片名.xml”,以下为标注文件中内容的示例:
[0086]
[0087][0088]
优选的,所述神经网络模型可以通过yolo、maskrcnn、ssd、fastrcnn、fcos、centernet、conrnernet或rentina等目标检测网络经过训练后得到。
[0089]
步骤2,依据所述串间距区域图像和片间距区域图像,计算串间距、片间距和错位值;所述串间距在串间距阈值范围内则合格,片间距在片间距阈值范围内则合格,错位值在错位值阈值范围内则合格;
[0090]
其中,所述串间距为同一列中相邻电池片之间的间距,片间距为同一行中相邻电池片之间的间距,错位值表示呈田字型分布的四块电池片之间的错位程度。
[0091]
优选的,所述串间距阈值范围包括串间距最大值和串间距最小值,串间距最小值<串间距<串间距最大值,则该串间距合格。进一步的,0.01mm≤串间距最小值≤1mm,3.5mm≤串间距最大值≤5mm。
[0092]
优选的,所述片间距阈值范围包括片间距最大值和片间距最小值,片间距最小值《片间距《片间距最大值,则该片间距合格。进一步的,0.01mm≤片间距最小值≤1mm,3.5mm≤片间距最大值≤5mm。
[0093]
优选的,所述错位值阈值范围包括错位值最大值和错位值最小值,错位值最小值《错位值《错位值最大值,则该错位值合格。进一步的,2mm≤片间距最小值≤3mm,3mm≤片间距最大值≤4mm。
[0094]
优选的,步骤2包括以下子步骤:
[0095]
步骤2a,依据所述串间距区域图像,计算电池片的串间边缘线,依据串间边缘线计算相邻电池片之间的串间距;
[0096]
步骤2b,依据所述片间距区域图像,计算电池片的片间边缘线,依据片间边缘线计算相邻电池片之间的片间距;
[0097]
步骤2c依据所述串间边缘线和片间边缘线,计算错位值;
[0098]
其中,串间边缘线为同一列的相邻电池片中,一电池片与另一电池片相对的边缘线;所述片间边缘线为同一行的相邻电池片中,一电池片与另一电池片相对的边缘线。
[0099]
优选的,所述步骤2a包括以下子步骤:
[0100]
步骤20a,如图3所示,将所述串间距区域图像,按照电池片宽度方向分隔为3份,依次为首段图像、中段图像和尾段图像;
[0101]
步骤21a,如图4a所示,分别将所述首段图像和尾段图像灰度化,获得首段灰度化图像和尾段灰度化图像;
[0102]
步骤22a,对所述首段灰度化图像的每行像素按横向求和,制成第一首段直方图(如图5所示),将像素和最大的一行的行数记为maxindex
col
;对所述首段灰度化图像进行sobe1和闭运算(闭运算指先膨胀再腐蚀),获得首段最终图像(如图4b所示),对首段最终图像的每行像素按横向求和,制成第二首段直方图(如图6所示),分别计算第0至maxindex
col
行、第maxindex
col
至第二首段直方图最后一行的像素和最大值对应的行数位置,为两条首段边缘线,分别标记为shoubianyuanxian1和shoubianyuanxian2;
[0103]
重复上述过程,对所述尾段灰度化图像进行处理,得到两条尾段边缘线,分别标记为weibianyuanxian3和weibianyuanxian4;
[0104]
步骤23a,串间距=min(weibianyuanxian4-weibianyuanxian3,shoubianyuanxian2-shoubianyuanxian1)。
[0105]
具体的,如图4b所示,maxindex
col
=62;如图6所示,第二首段直方图上有两个峰值,分别与shoubianyuanxian1和shoubianyuanxian2对应,而且分别是首段最终图像的第54行、第71行的像素横向相加的结果。
[0106]
优选的,所述步骤2b包括以下子步骤:
[0107]
步骤20b,将所述片间距区域图像,按照电池片高度方向分割为3份,依次为上段图像,中段图像和下段图像;
[0108]
步骤21b,分别将所述上段图像和下段图像灰度化,获得上段灰度化图像和下段灰度化图像;
[0109]
步骤22b,对所述上段灰度化图像的每列像素按纵向求和,制成第一上段直方图,将像素和最大的一列的行数记为maxindex
row
;对所述上段灰度化图像进行sobe1和闭运算,获得上段最终图像,对上段最终图像的每列像素按纵向求和,制成第二上段直方图,分别计算第0至maxindex
row
列、第maxindex
row
至第二上段直方图最后一列的像素和最大值对应的列数位置,获得两条上段边缘线,分别标记为shangbianyuanxian5和shangbianyuanxian6;
[0110]
重复上述过程,对所述下段灰度化图像进行处理,得到两条下段边缘线,分别标记为xiabianyuanxian7和xiabianyaunxian8;
[0111]
步骤23b,片间距=min(xiabianyuanxina8-xiabianyuanxian7,shangbianyaunxian6-shangbianyuanxian5)。
[0112]
例如,所述第二上段直方图的内容为一个数组,类似如下所示:
[0113]
[143,132,134,243,123,135,
……
245,255,255,200,
……
233],数组中,每一个数字均与第二上段直方图中一列像素和对应;
[0114]
若maxindex
row
=5,则计算第0至maxindex
row
列的像素和最大值,即是计算第0至5列的像素和最大值,也即是计算上述数组中第1至5个数据中的最大数据;则计算第maxindex
row
至第二上段直方图最后一列的像素和最大值,即是计算第5至第二上段直方图最后一列的像素和最大值,也即是计算上述数组中第6至最后一个数据中的最大值。
[0115]
优选的,如图1所示,所述光伏组件中,每块电池片均与其他三块电池片相邻,四块电池片呈田字形分布,,四块电池片形成一个十字形间隙,呈田字形分布的四块电池片,分别为左上电池片、右上电池片、左下电池片和右下电池片,靠近十字形间隙的八条边缘线(如图9所示)分别是:
[0116]
左上电池片和右上电池片的相对的两条下段边缘线,分别记为xiabianyuanxian70和xiabianyuanxian80;
[0117]
左下电池片和右下电池片的相对的两条上段边缘线,分别记为shangbianyuanxian50和shangbianyuanxian60;
[0118]
左上电池片和左下电池片的相对的两条尾段边缘线,分别记为weibianyuanxian30和weibianyuanxian40;
[0119]
右上电池片和右下电池片的相对的两条首段边缘线,分别记为shoubianyuanxian10和shoubianyuanxian20;
[0120]
则用于表示四块电池片的错位程度的错位值=max(xiabianyuanxian70-shangbianyuanxian50,xiabianyuanxian80-shangbianyuanxian60,weibianyuanxian30-shoubianyuanxian10,weibianyuanxian40-shoubianyuanxian20)。
[0121]
优选的,如图10所示,所述光伏组件中,每块电池片均具有八条边缘线,分别是:
[0122]
位于电池片上边沿处的首段边缘线和尾段边缘线,分别记为t1和tr;
[0123]
位于电池片下边沿处的首段边缘线和尾段边缘线,分别记为b1和br;
[0124]
位于电池片左边沿处的上段边缘线和下段边缘线,分别记为1t和1b;
[0125]
位于电池片右边沿处的上段边缘线和下段边缘线,分别记为rt和rb;
[0126]
因此,所述光伏组件中,每块电池片以如下格式存储:
[0127]
[“x1”,y1”,x2”,y2”,row
n”,col
m”,t1,tr,b1,br,lt,lb,rt,rb]。
[0128]
以上内容是结合具体的优选实施方式对本发明所作的进一步详细说明,不能认定本发明的具体实施只局限于这些说明。对于本发明所属技术领域的普通技术人员来说,在不脱离本发明构思的前提下,还可以做出若干简单推演或替换,都应当视为属于本发明的保护范围。
再多了解一些
本文用于企业家、创业者技术爱好者查询,结果仅供参考。