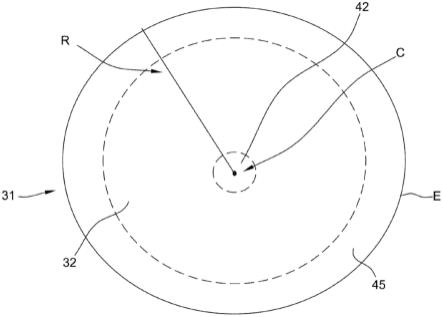
从soi结构移除氧化物膜的方法及制备soi结构的方法
1.相关申请案的交叉引用
2.本技术案主张2019年12月13日申请的第62/947,981号美国临时专利申请案的权利,所述申请案的全部内容以引用的方式并入本文中。
技术领域
3.本公开的领域涉及从绝缘层上硅(soi)结构移除氧化物膜的方法,且特定来说,本公开的领域涉及在沉积外延硅增厚层之前从soi结构剥离氧化物的方法。
背景技术:
4.绝缘层上硅结构可经受外延工艺,其中硅沉积于硅顶层以增加顶层的厚度。硅外延层的质量取决于其上沉积外延层的表面的质量。在沉积外延硅层之前,soi结构可经受退火。此退火可引起氧化物(sio2)形成于soi结构的表面上。通常在外延沉积之前从结构的顶面移除此氧化物。在一些例子中,在退火期间,阶地氧化物(即,较厚氧化物)形成于soi结构顶面的边缘附近。阶地氧化物可位于soi结构的边缘部分,其中归因于缺乏施体的圆形边缘附近的接合,整个施体被移除(即,裂解平面下方的施体)。阶地氧化物可为生长于把手晶片上的氧化物,其在移除施体之后残留。此阶地氧化物使氧化物移除变得复杂,因为氧化物跨晶片表面是不均匀的。
5.移除氧化物的常规方法可涉及浸渍剥离,其中晶片浸渍于湿式清洁器/蚀刻器中。这从包含背面的soi结构的所有表面移除氧化物。当处置soi结构时,背面氧化物可保护soi结构的底面不被擦损及损坏,且可充当背面密封件以防止外延期间污染或自动掺杂soi结构。掩模可用于保护背面氧化物。然而,掩模可引起顶部硅层损坏(例如在粘合及移除晶片带期间,其中将力施加于顶面以将粘着剂固定于带上或从背面移除粘合带)。掩模也会在带的边缘处遭受蚀刻泄漏,引起围绕式或延伸移除降解氧化物。
6.额外氧化物剥离方法可涉及晶片自旋,其中蚀刻溶液分布于晶片中心处,蚀刻溶液在晶片上“扇出”以移除氧化物。浸渍及晶片自旋两种技术引起氟化氢(hf)基蚀形成于硅顶层表面上。如图1中所展示,在制备soi结构期间,裂解接合晶片结构可引起空隙形成于硅层中。当顶层及电介质层的一部分与废施体结构一起拉起时,出现空隙。如图2中所展示,当空隙暴露于hf蚀刻溶液时,hf使硅顶层下方的电介质层降解,因为相较于硅,hf更容易蚀刻电介质材料(例如二氧化硅)。
7.需要用于移除soi结构的顶面上的氧化物的方法,此类方法能够在减少hf基蚀的同时移除阶地氧化物且能够保留背面氧化物。需要使用此类氧化物剥离方法来制备soi结构的方法。
8.本节旨在向读者介绍可与本公开的各种方面相关的本领域的各种方面,下文将描述及/或主张此类方面。此讨论被认为有助于向读者提供背景信息以便于更好地理解本公开的各种方面。因此,应了解,这些陈述应鉴于此来解读,而非被视为现有技术的认可。
技术实现要素:
9.本公开的一个方面涉及一种用于从绝缘层上硅结构移除氧化物膜的方法。提供绝缘层上硅结构。所述绝缘层上硅结构具有把手结构、硅顶层及安置于所述把手结构与所述硅层之间的电介质层。所述绝缘层上硅结构具有处于所述绝缘层上硅结构的顶面上的氧化物膜。所述绝缘层上硅结构具有从所述绝缘层上硅结构的中心延伸到周向边缘的半径r。将蚀刻溶液引导到所述绝缘层上硅结构的所述顶面的中心区域,同时自旋所述绝缘层上硅结构。将蚀刻溶液引导到所述绝缘层上硅结构的所述顶面的边缘区域,同时自旋所述绝缘层上硅结构。从所述中心区域向外径向安置所述边缘区域。
10.本公开的另一方面涉及一种用于制备绝缘层上硅结构的方法,所述绝缘层上硅结构包括硅顶层、把手结构及安置于所述硅顶层与把手结构之间的电介质层。将离子植入到施体结构中以形成所述施体结构中的裂解平面。提供把手结构。在接合之前,电介质层形成于施体结构及把手结构中的至少一者上。将所述施体结构接合到所述把手结构以形成包括所述施体结构、把手结构及安置于所述把手结构与所述施体结构之间的电介质层的接合晶片结构。在所述裂解平面处裂解所述接合晶片结构,使得施体结构的一部分保持接合到所述把手结构作为硅顶层,裂解形成包括所述把手结构、硅顶层及安置于所述把手层与硅顶层之间的电介质层的绝缘层上硅结构。使用在退火期间形成于所述绝缘层上硅结构的至少顶面上的氧化物来退火所述绝缘层上硅结构。所述绝缘层上硅结构的所述顶面的中心区域与蚀刻溶液接触,同时自旋所述绝缘层上硅结构。所述绝缘层上硅结构的所述顶面的边缘区域与所述蚀刻溶液接触,同时自旋所述绝缘层上硅结构。在接触所述绝缘层上硅结构的所述顶面的所述中心区域及所述边缘区域之后,外延硅层沉积于所述硅顶层。
11.注意,按照本公开的上述方面,特征存在各种改进。进一步特征也可并入本公开的上述方面中。这些改进及额外特征可个别存在或以任何组合存在。例如,按照本公开的任何所说明的实施例的下文讨论的各种特征可单独或以任何组合并入本公开的任何上述方面中。
附图说明
12.图1到2是展示hf基蚀形成于soi结构上的示意图;
13.图3是具有其上含电介质层的施体晶片的施体结构的横截面图;
14.图4是其上植入离子期间的施体结构的横截面图;
15.图5是接合到把手结构的施体结构的横截面图;
16.图6是在裂解平面处裂解施体结构之后的接合晶片结构的横截面图;
17.图7是soi结构的俯视图;
18.图8是具有及不具有阶地氧化物的沉积于soi结构上的外延层的厚度均匀性的曲线图;
19.图9是用于低温外延沉积及阶地氧化物(左面板)及无氧化物(中间面板及右面板)的高温外延沉积的顶部硅边缘的照片;
20.图10是外延沉积期间hf基蚀的示意图;
21.图11是在中心自旋蚀刻氧化物剥离工艺之后空隙处hf基蚀的照片;
22.图12是通过仅中心施配(图12a)及中心到边缘施配(图12b)产生的hf基蚀的图像;
23.图13是700ml/min流率下的边缘施配的缺陷图;
24.图14是400ml/min流率下的边缘施配的缺陷图;
25.图15是在lpd计数大于或等于1μm的情况下使阶地氧化物移除或不移除的soi顶部硅表面的sp1表面比较;
26.图16是使阶地氧化物移除或不移除的soi顶部硅表面的sp1表面比较,其中展示每个晶片的总缺陷面积(mm2);
27.图17是后外延顶部硅表面检验的sp1表面比较,其中颗粒数为0.2μm或更大;
28.图18是后外延顶部硅表面检验的sp1表面比较,其中展示总擦损长度;
29.图19是线末sp1表面检验比较,其中颗粒数为0.16μm或更大;
30.图20是线末sp1表面检验,其中颗粒数为0.5μm或更大;
31.图21是线末sp1表面检验,其中颗粒数为0.8μm或更大;
32.图22是晶片计数时的每个晶片的缺陷总面积的盒形图比较;及
33.图23是晶片计数时的0.8μm或更大的缺陷的每个晶片的缺陷计数的盒形图比较。
34.对应元件符号指示所有图中的对应部分。
具体实施方式
35.本公开的规定涉及从绝缘层上硅结构(本文中可指称“soi结构”或甚至更简单地指称“晶片”)剥离氧化物膜的方法。氧化物剥离方法的实施例可涉及中心到边缘(ce)自旋蚀刻,其中在第一阶段自旋结构的同时将蚀刻剂溶液分散于结构中心附近,且接着在第二阶段自旋结构的同时朝向结构边缘施配蚀刻剂。
36.用于形成绝缘层上硅结构的方法
37.本公开的用于移除氧化物的方法一般可与其中期望移除氧化物膜的任何接合晶片结构一起使用。在一些实施例中,所处理的结构可为绝缘层上硅结构。这些结构可包含把手晶片、硅层(有时指称“硅装置层”或“硅顶层”)及安置于把手晶片与硅层之间的电介质层。以下仅是用于制备绝缘层上硅结构的方法及系统的一个实例,除非另有陈述,否则可使用其它方法。
38.图3中展示可接合到把手结构以形成接合晶片结构的施体结构30的实例。施体结构30可由沉积于施体晶片12的前表面上的电介质层15形成。应了解,替代地,电介质层15可生长或沉积于把手晶片上或电介质层可生长于施体晶片及把手晶片两者上,且这些结构可接合于各种布置中的任何者中而不受限制。合适的施体晶片12可由硅、锗、硅锗、氮化镓、氮化铝、砷化镓、铟镓砷化物及其任何组合组成。在一些实施例中,施体晶片由单晶硅组成。
39.电介质层15可为适合于soi结构中的任何电绝缘材料,例如包括sio2、si3n4、氧化铝或氧化镁的材料。在一些实施例中,电介质层15是sio2(即,电介质层基本上由sio2组成)。在其中电介质层是二氧化硅(sio2)的实施例中,电介质层有时指称“埋入氧化物”或“box”层15。可根据本领域中任何已知技术(例如热氧化、湿氧化、热氮化或此类技术的组合)应用电介质层15。
40.如(例如)图4中所展示,离子(例如氢原子、氦原子或氢原子与氦原子的组合)可被植入于施体结构的前表面22下方的大体上均匀指定深度处以界定裂解平面17。应注意,当氦离子及氢离子被共同植入到结构中形成裂解平面17时,其可被同时或循序植入。在一些
实施例中,在沉积电介质层15之前植入离子。当在沉积电介质层15之前执行植入时,在足够低温下适当地执行在施体晶片12上后续生长或沉积电介质层以防止在施体层中沿平面17过早分离或裂解(即,在晶片接合工艺步骤之前)。
41.把手结构10(图5)可包含从用于制备多层结构的任何合适的材料(例如硅、碳化硅、蓝宝石、锗、硅锗、氮化镓、氮化铝、砷化镓、铟镓砷化物、石英及其组合)获得的把手晶片。把手结构10可包含经沉积于把手晶片上的电介质层,或如在其它实施例中,把手结构10仅由把手晶片组成(即,不包含电介质层)。把手晶片及施体晶片可为单晶硅晶片,且可为从根据常规柴氏长晶法生长的单晶锭上切下的单晶硅晶片。
42.如图5中所展示,施体结构的电介质层15的前表面是通过接合工艺适当地接合到把手结构10的前表面以形成接合晶片结构20。电介质层15及把手结构10可被接合在一起,同时通过将结构的表面暴露于含有(例如)氧气或氮气的等离子体来执行表面活化。接着将晶片压在一起,且接合界面18处的接合形成于此之间。一般来说,晶片接合可基本上使用本领域中已知的任何技术来实现,只要所采用以实现接合界面形成的能量足以确保在后续处理(即,通过沿施体晶片中的裂解平面或分离平面17分离来进行层转移)期间维持接合界面的完整性。
43.一旦经制备,那么将接合晶片结构20放置于裂解装置中以沿裂解平面将施体晶片的一部分与接合结构分离(即,裂解)以形成层状半导体结构(例如soi结构)。一般来说,裂解装置可包含使用本领域中已知技术(例如热及/或机械诱发的裂解技术)的此破裂。
44.参考图6,分离之后形成两个结构30、31。因为沿施体结构12中的裂解平面17(图5)发生接合晶片结构20的分离,所以施体结构的一部分留下两者的结构的部分(即,施体晶片的一部分沿电介质层15转移)。结构30包括施体晶片的一部分。结构31是soi结构且包含把手结构10、电介质层15及安置于电介质层15顶上的硅顶层25(裂解之后剩余的施体晶片部分)。在其中施体结构及把手结构均包含电介质层的实施例中,电介质层组合以形成soi结构的电介质层15。
45.用于沿裂解平面分离接合晶片结构的裂解装置可为机械裂解装置,其中分离单独或除退火之外通过机械力诱发或实现。例如,可将接合结构放置于夹具中,其中垂直于接合结构的相对侧施加机械力以将施体结构的一部分从接合结构中拉出。
46.实例裂解装置包含在接合晶片结构20的前裂解边缘附近施加机械力的吸力盖。分离施体晶片的部分可通过在裂解平面17的接合晶片的边缘处应用机械楔或刀片来启动,以启动沿裂解平面17扩散裂纹。由吸力盖施加的机械力接着将施体结构的部分从接合结构中拉出,因此形成soi结构。机械裂解装置可为市售,例如来自硅创世纪公司(silicon genesis corporation)(加利福尼亚州圣何塞(san jose,california))的脱胶及裂解工具。
47.在替代实施例中,裂解装置是热裂解装置,其中通过退火接合结构实现破裂。例如,在惰性(例如氩或氮)大气或环境条件下,可在约200℃到约800℃或从约250℃到约650℃的温度下执行至少约10秒、至少约1分钟、至少约15分钟、至少约1小时或甚至至少约3小时的周期(其中较高温度要求更短退火时间,且反之亦然)的热裂解。热裂解装置可为带炉,其中裂解的扩散实现于接合结构的前缘(即,在穿过炉的结构的行进方向中的前缘)且朝向接合晶片结构的后缘前进。也可使用其它类型的裂解装置。
48.soi结构31的层(把手结构10、电介质层15及硅顶层25)一般可具有允许层如本文中所描述那样作用的任何厚度。在一些实施例中,硅顶层25相对薄(例如约0.1μm到约0.3μm的厚度)且电介质层15相对厚(约1.0μm或更厚)。soi结构31具有从结构31的中心c延伸到周向边缘e的半径r(图7)。除非另有陈述,否则soi结构31可具有任何半径(例如约100mm、约150mm或更大)。
49.退火
50.soi结构31的裂解表面(即,施体晶片的薄装置层25)具有可由额外处理平滑化的粗糙表面。结构31可经受额外处理以产生具有用于其上制造装置及/或用于沉积增厚外延层的期望特征的层表面。
51.根据本公开的一些实施例,绝缘层上硅结构31经受预外延平滑退火(pesa)。平滑退火在结构31的顶面32(图7)上重新排序硅。在不受任何特定理论束缚的情况下,平滑退火还增强把手结构10与硅装置层25之间的氧化物到氧化物接合(即,在其中把手及施体晶片包含在其接合表面上的氧化物的实施例中)。在退火之前,结构31的表面32可任选地经历清洁及/或短暂蚀刻或平坦化。
52.在一些实施例中,在至少约900℃、至少约1000℃或至少约1050℃(例如约1050℃到约1150℃)的温度下执行绝缘层上硅结构31的退火。退火的长度可变动(例如0.5小时到16小时)且其中较高退火温度对应于较低退火周期,且反之亦然。实例环境包含o2、n2、h2、氩及其组合。退火引起氧化物形成于soi结构31的表面(即,退火期间的所有暴露表面)。氧化物的厚度可变动且在一些实施例中,其厚度从约0.001μm到约0.02μm。
53.一般来说,在绝缘层上硅结构31上形成的氧化物形成于结构的所有表面(顶面、底面及侧面(例如把手上斜面、顶点、下斜面))。在一些实施例中,朝向前表面32的周向边缘存在相对较厚氧化物(例如其中施体未接合而暴露埋入氧化物层)。此氧化物在本文中可指称“阶地氧化物”。阶地氧化物的宽度可随晶片的边缘形状而变动(例如宽度为1mm到3mm)。阶地氧化层的厚度可为把手结构经氧化所到的厚度。
54.氧化物移除
55.根据本公开的实施例,在沉积下文将描述的外延硅层之前,移除形成于绝缘层上硅结构31上的氧化物的至少一部分(例如至少部分或完全移除形成于结构31的表面32上的氧化物)。在本公开的一些实施例中,氧化物的至少一部分通过自旋蚀刻工艺移除,其中绝缘层上硅结构31随延伸穿过结构31的中心c(图7)的旋转轴旋转,其中轴垂直于结构31的表面32。
56.从旋蚀刻工艺可为两阶段工艺(即,至少两个阶段),其中将蚀刻溶液引导到soi结构(例如从结构的表面32上方喷射或以其它方式引导到表面32上),同时自旋soi结构。在第一阶段中,将蚀刻溶液引导到绝缘层上硅结构31的顶面33的中心区域42(由图7中的虚线束缚),同时自旋绝缘层上硅结构31。通过自旋结构31,蚀刻溶液在结构的表面上扇出,其允许从结构31的表面32蚀刻及移除(即,剥离)氧化物。就此来说,如本文中所使用的术语“蚀刻”及/或“剥离”不应被视为限制意义且除非另有陈述,否则可使用其中通过化学工艺(其中结构与溶液接触)从绝缘层上硅结构31的表面移除氧化物的任何工艺。
57.绝缘层上硅结构31的顶面31的中心区域42可相对狭窄(例如具有小于0.25*r或小于0.1*r的半径)以确保结构的中心区域与蚀刻溶液接触。在一些实施例中,在氧化物移除
的第一阶段期间,将蚀刻溶液引导到绝缘层上硅结构31的中心c。
58.在第一阶段蚀刻完成之后,第二阶段蚀刻开始,其中将蚀刻溶液引导到绝缘层上硅结构31的顶面32的边缘区域45,同时自旋绝缘层上硅结构31。从中心区域41向外径向安置边缘区域45。边缘区域45(由第二虚线所展示)从与结构31的中心c相距的距离延伸到其周向边缘e。例如,边缘区域可从与绝缘层上硅结构31的中心c相距0.66*r的距离开始且延伸到绝缘层上硅结构31的周向边缘e。在其它实施例中,边缘区域从与绝缘层上硅结构31的中心c相距0.80*r或甚至0.85*r的距离处开始且延伸到绝缘层上硅结构31的周向边缘e。酸施配于soi结构的顶面的点可通过径向重新定位通过其施配酸的转臂来改变(即,从第一阶段到第二阶段的转变)。
59.第一阶段(中心区域分布)及第二阶段(边缘区域分布)的相对长度可基于soi结构的所要质量选择。在一些实施例中,第一阶段是从0.5秒到10秒(例如3秒到5秒),第二阶段是从10秒到约20分钟(例如1分钟到大约15分钟或从约1分钟到约10分钟)。在一些实施例中,酸的流率在第二阶段中相对于第一阶段降低(例如第一阶段中的流率的90%或以下、75%或以下或50%或以下)。替代地或另外,当将蚀刻溶液从中心区域重新引导到边缘区域时(例如当转臂从中心区域移动到边缘区域时),可暂停蚀刻溶液的流动。
60.蚀刻工艺可包含额外阶段,其包含冲洗(例如使用臭氧去离子水)及氮气冲程以减少干燥时间。在一些实施例中,将蚀刻溶液引导到soi结构的第一阶段是将蚀刻溶液引导到中心区域42的唯一阶段。替代地或另外,可在两个或更多个阶段中将蚀刻溶液引导到边缘区域45(例如上文所描述的第二阶段,接着分布于中心处的冲洗阶段,接着其中将蚀刻溶液引导到边缘区域45的第四阶段)。
61.在一些实施例中,蚀刻溶液包含氢氟酸(hf)及乙酸。在一些实施例中,蚀刻溶液中氟化氢酸(49%)与乙酸(冰)的比率小于1:1、小于3:2、小于2:1、小于3:1或6:1或更小。任选地,蚀刻溶液可含有其它添加剂,例如各种表面活性剂、缓冲剂(例如氟化铵)、其它氧化酸(例如hcl)及/或其它氧化化合物(h2o2、臭氧等)。
62.在一些实施例中,相对于常规氧化物自旋蚀刻工艺,在将蚀刻溶液分布到中心区域及/或边缘区域的同时降低蚀刻溶液的流率。在一些实施例中,蚀刻溶液(例如具有hf及乙酸的溶液)的流率约为600ml/min或以下或约500ml或以下(例如约100ml/min到约600ml/min或约100ml/min到约400ml/min)。就此来说,在其中流率在蚀刻工艺期间改变的实施例中,上文所描述的流率可为在蚀刻溶液与soi结构接触时(例如,且不包含冲洗步骤)平均的时间平均流率。
63.用于自旋soi结构的合适的设备包含(例如)由entrepix公司(亚利桑那州菲尼克斯市(phoenix,az))销售的nexgen mg系列单晶片湿式蚀刻平台。也可从acm研发公司(acm research)(加利福尼州菲蒙市(fremont,california))、ap&s国际股份有限公司(ap&s international gmbh)(德国多瑙埃兴根(donaueschingen,germany))、decker anlagenbau股份有限公司(decker anlagenbau gmbh)(德国贝兴(berching,germany))、ked科技公司(ked tech)(密西西比州奥利夫布兰奇(olive branch,mississippi))、科林研发公司(lam research)(加利福尼州菲蒙市(fremont,california))、美国picotrack公司(picotrack usa)(加利福尼州圣克拉拉市(santa clara,california))、屏幕半导体解决方案公司(screen semiconductor solutions)(日本东京(kyoto,japan))、塔兹莫股份有限公司
(tazmo co.,ltd.)(加利福尼州菲蒙市(fremont,california))及维易科公司(veeco)(纽约莱恩维尤(plainview,new york))获得其它合适的设备。可在足以从soi结构的顶面移除氧化物而不促进表面上的空隙的hf基蚀的条件下,执行蚀刻工艺。例如且根据本公开的一些实施例,soi结构可以300rpm到2500rpm及以350ml/min到2500ml/min的酸施配率自旋。根据本公开的一些实施例,氧化物移除工艺不涉及掩蔽步骤及/或涉及soi结构的浸渍。
64.上文所描述的蚀刻工艺移除绝缘层上硅结构31的表面32上的氧化物的至少一部分。在一些实施例中,从结构的整个顶面32移除氧化物(即,移除阶地边缘氧化物)。蚀刻工艺也可从结构31的侧(例如把手上斜面、顶点、下斜面)移除全部或一部分氧化物。在自旋蚀刻期间,由于蚀刻溶液沿晶片的侧流动,所以结构的侧上的氧化物可被移除。当蚀刻溶液流过结构31的侧时,部分也可接触结构31的背面(例如通过毛细管作用)且移除晶片背面的边缘区域中的一部分氧化物(例如从0mm到1mm的背面)。
65.绝缘层上硅外延
66.一旦氧化物已经至少部分地从结构31的顶面32移除,那么硅外延层可被沉积于结构31的顶面32上以增加硅装置层的厚度。可由所属领域的技术人员可利用的任何外延工艺来沉积硅。在一些实施例中,外延工艺将硅层25的厚度增加到1μm或更大。
67.一般来说,可由所属领域的技术人员可用的任何已知方法沉积硅。例如,可使用金属有机化学汽相沉积(mocvd)、物理汽相沉积(pvd)、化学汽相沉积(cvd)、低压化学汽相沉积(lpcvd)、等离子体增强化学汽相沉积(pecvd)或分子束外延(mbe)来沉积硅。用于lpcvd或pecvd的硅前体包含甲基硅烷、四氢化硅(硅烷)、三硅烷、二硅烷、五硅烷、新戊硅烷、四硅烷、二氯硅烷(sih2cl2)、三氯氢硅(sihcl3)、四氯化硅(sicl4)等。例如,可通过在约550℃与约690℃之间(例如在约580℃与约650℃之间)的温度范围中热解硅烷(sih4)来将硅沉积于表面氧化层上。室压可在约70毫托到约400毫托的范围内。
68.与用于制备绝缘层上硅结构的常规方法相比,本公开的方法具有若干优点。自旋蚀刻工艺允许移除soi结构顶面及侧面上的氧化物,同时保持背面氧化物。当处置soi结构时,背面氧化物可保护soi结构的底面不被擦损及损坏,且可充当背面密封件以防止外延期间污染或自动掺杂soi结构。中心到边缘自旋刻蚀允许移除soi结构边缘附近的阶地氧化物,其改进朝向边缘的外延沉积。外延增厚的硅层可以改进均匀性及降低颗粒缺陷率为特征。例如,可减少或防止形成于顶部硅层的边缘处的多晶硅结节。此类结节给予化学可见模糊(顶部硅)边缘,通过前表面检验,可将所述边缘视为缺陷(污染)。在沉积硅外延层期间,结节或晶粒可从结构上剥落且落到soi结构内部中的顶部硅层上,导致lls缺陷,或在一些例子中导致多晶硅形成于顶部硅表面上。
69.阶地氧化物允许多晶硅形核及生长及脱落颗粒。因为此效应随温度升高而增加,所以降低或消除阶地氧化物允许使用更高温度外延,这也提高外延层的质量。
70.中心到边缘工艺还减少hf基蚀的程度,因为与蚀刻剂的接触时间缩短。可由使用较低蚀刻溶液速率(例如小于600ml/min或小于500ml/min)及/或相对较低乙酸浓度(例如小于1:1、小于3:2、小于2:1、小于3:1或6:1或更低)进一步降低hf基蚀。在中心刻蚀期间使用相对较低流率减小膜厚且缩短抗润湿时间,从而减少hf润湿表面的接触时间。由于表面活性剂浓度降低,所以乙酸浓度的降低被认为减少空隙区域的hf基蚀,从而增加hf与裸硅的接触角(且降低hf与硅氧化物的接触角)且增加基蚀区域中的毛细管压力。
71.中心到边缘酸处理工艺的实施例(其中在相对较短时间(例如小于10秒或小于5秒)内将酸引导到中心区域,接着移动到边缘区域施配以移除阶地氧化物)减少或消除边缘施配期间蚀刻溶液的飞溅。当蚀刻溶液在中心区域分布到边缘区域分布之间暂停时,可进一步减少飞溅。蚀刻剂的此暂停也可促进位于边缘区域的内部的晶片顶面的抗润湿,其进一步减少hf基蚀。减少或消除飞溅是有利的,因为飞溅形成可由废气截留的蚀刻气溶胶,引起烟雾增加。通常必须在将烟雾释放到大气中之前移除此类烟雾。蚀刻气溶胶也可进入废气流外部的工具,引起工具组件损坏且缩短工具的寿命。当由自动表面检验观察时,气溶胶也可引起晶片上的表面缺陷。飞溅还减少回收酸的体积,从而增加每个晶片的酸消耗。
72.实例
73.以下实例将进一步说明本公开的工艺。这些实例不应被视为限制意义。
74.实例1:有及无阶地氧化物的厚度均匀性及硅边缘质量
75.图8中展示生长于包含处于结构的表面上的阶地氧化物的绝缘层上硅结构的硅层上的外延层的厚度均匀性及生长于无阶地氧化物的绝缘层上硅结构的硅层上的外延层的厚度均匀性。消除阶地氧化物允许在更高温度下执行外延沉积,其中硅吸附原子可表面扩散且更易于并入或同化到单晶晶格结构中。如图8中所展示,无阶地(“无阶地氧化物”)的高温外延工艺比具有阶地氧化物(“具阶地氧化物”)的低温外延工艺更均匀。
76.图9展示外延沉积的后顶部硅的边缘。左面板是低温下的具有氧化物阶地边缘的顶部硅且两个右面板是高温epi下的无氧化物阶地边缘的顶部硅。具有阶地边缘的soi结构的顶部硅包含朝向顶部硅层的边缘的晶粒或结节。
77.实例2:无仅中心分布蚀刻剂溶液的hf基蚀
78.氧化物蚀刻溶液(3:4hf:乙酸的体积比(80%乙酸)相当于3.5:3.8:1hf:冰乙酸:水的比)被施配于自旋soi结构的中心处。soi结构在sez 223自旋蚀刻工具上以1900rpm自旋,其中酸施配率为1500ml/min。如图10中所展示,所得结构包括硅层中的空隙处的hf基蚀。
79.氧化物蚀刻溶液(6:1hf:乙酸的体积比(冰,100%))被施配于自旋soi结构的中心处。soi结构使用nexgen mg22自旋蚀刻机以700rpm自旋,其中酸施配率为2000ml/min。如图11中所展示,所得结构包括硅层中的空隙处的hf基蚀。如图11所展示,基蚀非常严重使得顶部硅不再得到很好支撑且开始剥落。图像上的基蚀呈现为围绕空隙(其较暗)的较浅色带。hf基蚀的边缘比具有粗糙或锯齿状边缘的空隙更为光滑及扩散。
80.实例3:比较使用仅中心及中心到边缘分布蚀刻剂溶液的hf基蚀
81.soi结构(直径200mm)根据以下表1的左面板中所展示的步骤剥离氧化物,其中酸仅分布于结构的中心。在hf:乙酸蚀刻(280秒)之后,使用臭氧去离子水冲洗结构且将其暴露于氮气。对soi结构重复这些循环(执行步骤1到3两次),其中总酸施配时间为560秒。
82.另一soi结构(直径200mm)由表1的右面板的步骤剥离氧化物。在3秒hf:乙酸蚀刻(其中酸分布于结构的中心)之后,转臂移动到距结构中心90mm处(距边缘10mm)且酸分布280秒。臭氧去离子水冲洗之后,在距结构中心90mm处重复hf:乙酸蚀刻(总酸施配时间563)。此接着另一冲洗及暴露到氮气。
[0083][0084]
表1:蚀刻配方,其涉及仅中心分布的蚀刻剂(左面板)及中心到边缘分布的蚀刻剂(右面板)。
[0085]
基蚀由软件处理工具(例如imagej)确定,其中在相应显微图(图12a及图12b)中测量基蚀面积(即,顶部硅的边缘与其中box无基蚀的点(基蚀的内部)之间)。测量线的平均长度(顶部硅的边缘长度与基蚀区域的内部长度之间的平均值)。将面积除以平均长度得到平均基蚀。图12a中展示由仅中心施配产生的基蚀且图12b中展示由中心到边缘施配产生的基蚀。由仅中心施配产生的hf基蚀是18.9μm,同时由中心到边缘施配产生的基蚀是2.6μm。
[0086]
实例4:中心到边缘工艺中流率的降低
[0087]
soi结构(200mm)以400rpm自旋,同时边缘以700ml/min的流率施配hf:乙酸溶液(距中心90mm,即距边缘10mm),持续60秒。另一soi结构(200mm)以400rpm自旋,同时边缘以400ml/min的流率施配hf:乙酸溶液(距中心90mm,即距边缘10mm),持续60秒。图13(400ml/min)及图14(700ml/min)中展示图像图(科磊公司(kla-tencor)spi-tbi图)。soi结构未进行中心蚀刻。
[0088]
图13及14中最左的图像是边缘氧化物剥离之前的晶片的sp1图。从左的第二图像是处理边缘氧化物剥离之后的sp1图。从左的第三图像是sc1及sc2清洁之后的sp1图。第四图像的(最右)图像是第二次清洁之后的图,其展示不可移除的缺陷。以400ml/min处理的晶片的sp1图(图14)展示较小缺陷率。
[0089]
实例5:中心到边缘自旋蚀刻与浸渍湿式清洗台的比较
[0090]
soi结构由中心到边缘分布的酸处理以使用标准清洁操作(在线性浸渍湿式清洗
台中进行sc1、sc2及臭氧浴清洁)(“qee(eos hte)”)移除阶地氧化物。在线性浸渍湿式清洗台中(在不移除阶地氧化物的情况下)处理soi结构以移除退火氧化物,接着相同标准清洁操作(“qeb(por)”)。
[0091]
图15及16展示两组结构的soi结构的可能性分布。使用统计假设测试(例如leven测试),其可展示颗粒计数(复合、正常模态、lpd-n)》1μm(cnl》1)(图15)或总面积计数(cntlarea)(图16)的分布对于两组结构来说没有差别。这是预期的,因为阶地氧化物剥离工艺不应影响表面。
[0092]
外延层沉积于相对高温下经历中心到边缘的氧化物剥离的soi结构上。外延层也沉积于由常规方法剥离氧化物(即,包含阶地氧化物)的soi结构上。每一结构的顶部硅层从0.15μm增加到1.0μm。使用科磊公司(kla tencor)sp1制备缺陷图。图17比较大小大于0.2μm(cop》0.2)的缺陷(复合斜向颗粒)且图18比较两组结构的总擦损长度(mm)(coscrlen)。在图17及18中,较低值(接近0)指示较小缺陷率(颗粒)。
[0093]
相同两群组晶片经受具有各种度量及检验的最终清洁及最终sp1表面检验。图19中展示粒径为0.16μm及以上的线末sp1表面检验且图20中展示0.5μm及以上的线末sp1表面检验,且图21中展示0.8μm及以上的线末sp1表面检验。在所有情况中,中心到边缘酸分布(eos hte)处理结构(即,已移除阶地氧化物的这些晶片)展示较低计数且这些差异在95%置信度水平处是统计上显著的。
[0094]
图22及23是比较在一定数量晶片上的使用中心到边缘酸分布(eos hte)的soi晶片与常规soi晶片(por)的盒形图。图22展示晶片组中每个晶片的缺陷的总面积且图23展示晶片组中缺陷为0.8μm或更大的每个晶片的缺陷计数。
[0095]
使用高温外延的具有低施配率(例如500ml/min或更少)的中心到边缘酸分布已被证明使用较低表面缺陷率将良率提高4%到6%。
[0096]
如本文中所使用,术语“约”、“大体上”、“基本上”及“近似”在与尺寸、浓度、温度或其它物理或化学性质或特性范围结合使用时意味着涵盖性质或特性范围的上限及/或下限中可存在的变动,包含(例如)从舍入、测量方法或其它统计变动所得的变动。
[0097]
当引入本公开或其实施例的元件时,冠词“一”及“所述”旨在意味着存在一或多个元件。术语“包括”、“包含”、“含有”及“具有”旨在具包含性且意味着除所列元件之外可存在额外元件。使用指示特定方向(例如“顶部”、“底部”、“侧面”等)的术语是为了便于描述且无需所描述项目的任何特定方向。
[0098]
由于可在不背离本公开的范围的情况下对上述构造及方法作出各种改变,因此旨在将以上描述中所含有及附图中所展示的所有物项解释为说明而非限制意义。
再多了解一些
本文用于企业家、创业者技术爱好者查询,结果仅供参考。