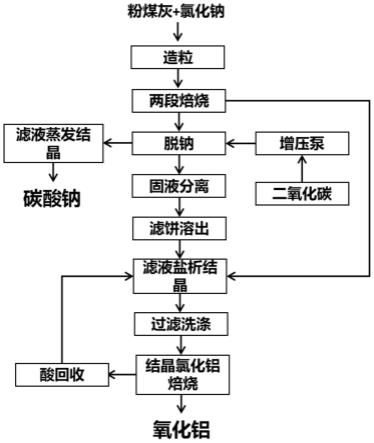
1.本发明涉及固废综合利用技术领域,具体而言,涉及一种从粉煤灰中提取氧化铝的方法。
背景技术:
2.固体废弃物粉煤灰、废水浓盐水、废气燃烧尾气是燃煤电厂的主要三种工业废弃物。电厂三废对环境、人类带来巨大的危害,因此,电厂三废综合治理日益变得尤为重要。目前,燃烧尾气经脱硫脱硝后,富含大量二氧化碳的气体直接排入大气;浓盐水则经简单处理后用作抑尘剂。而粉煤灰主要在建材、水泥、道路及堆场等方面进行综合利用,高附加值利用还处在研发阶段。
3.根据燃烧温度的不同,粉煤灰可分为循环流化床粉煤灰和煤粉炉粉煤灰。循环流化床粉煤灰的形成温度约为840℃,主要物相组成为非晶相,粉煤灰中氧化铝活性好,可直接用酸进行提取;煤粉炉粉煤灰的形成温度约为1300℃,矿物组成主要为莫来石,含少量石英和刚玉,活性差,较难直接用酸提取其中的氧化铝,需进行活化后再提取。粉煤灰提取氧化铝工业化大生产以传统碱法工艺为主,但因为粉煤灰中铝硅比较低,在碱性条件下,二氧化硅大量溶出,使得硅铝分离困难,需要使用复杂的工艺实现高含硅粉煤灰中铝的提取,导致生产成本高,渣量大。粉煤灰提铝特别是煤粉炉粉煤灰提取氧化铝技术存在产渣量大、二次污染严重、工艺流程复杂、能耗高、成本高等问题。随着现代材料技术的进步,粉煤灰酸法提取氧化铝工业化示范项目近年来逐渐兴起,但采用的原料多为循环流化床粉煤灰。煤粉炉粉煤灰的排放量是循环流化床粉煤灰的9倍左右,因此,只有实现煤粉炉粉煤灰的综合利用,才能实现粉煤灰真正广义上的综合利用。
技术实现要素:
4.本发明的主要目的在于提供一种从粉煤灰中提取氧化铝的方法,以解决现有技术中从粉煤灰中提取氧化铝的工艺复杂、生产成本高、环境污染大的问题。
5.为了实现上述目的,根据本发明的一个方面,提供了一种从粉煤灰中提取氧化铝的方法,包括以下步骤:步骤s1,将粉煤灰与含有氯化钠的盐水进行混合,制粒后得到粉煤灰颗粒;步骤s2,将粉煤灰颗粒在200~350℃的温度下进行低温流态化焙烧,然后在700~1100℃的温度下进行高温流态化焙烧,得到活化产物;步骤s3,将活化产物与水混合成料浆,然后在料浆中通入二氧化碳进行加压脱钠,得到含氧化铝滤饼和碳酸盐溶液;步骤s4,向含氧化铝滤饼中加入盐酸水溶液进行溶出,得到溶出液;将溶出液进行结晶,得到氯化铝晶体;焙烧氯化铝晶体,得到氧化铝。
6.进一步地,含有氯化钠的盐水来自于电厂废水,二氧化碳来自于电厂废气。
7.进一步地,步骤s1中,含有氯化钠的盐水中的氯化钠与粉煤灰的重量比为(0.5~20):1,优选地,含有氯化钠的盐水中的氯化钠与粉煤灰的重量比为(1~5):1。
8.进一步地,步骤s2中,低温流态化焙烧的温度为280~320℃,低温流态化焙烧的时
间为0.5~2h;高温流态化焙烧的温度为900~1100℃,高温流态化焙烧的时间为0.5~4h。
9.进一步地,步骤s2中,高温流态化焙烧的温度与低温流态化焙烧的温度差为750~900℃,高温流态化焙烧的时间与低温流态化焙烧的时间之比为(2~8):1。
10.进一步地,步骤s3中,料浆中活化产物的质量浓度为50~600g/l;优选地,料浆中活化产物的质量浓度为200~300g/l。
11.进一步地,步骤s3中,脱钠反应的温度为20~200℃,脱钠反应的压力为6~8mpa,脱钠反应的时间为1~48h;优选地,脱钠反应的温度为100~160℃,脱钠反应的时间为2~4h。
12.进一步地,步骤s4中,盐酸水溶液的质量百分比为20~38%,且溶出过程的液固比为(1~15):1,溶出过程的温度为10~200℃,溶出过程的时间为1~48h;优选地,盐酸水溶液的质量百分比为20~28%,且溶出过程的液固比为(2~5):1,溶出过程的温度为20~80℃,溶出过程的时间为1~3h。
13.进一步地,步骤s4中,在进行焙烧之前,还包括将氯化铝晶体用质量分数25~38%的浓盐酸水溶液进行洗涤的步骤。
14.进一步地,步骤s4中,焙烧过程的温度为800~1200℃,焙烧过程的时间为2~6h。
15.应用本发明的技术方案,通过设置两段焙烧,使用氯化钠实现对粉煤灰的活化,而不受粉煤灰原料中莫来石等难溶于酸的物相的限制,原料可以是煤粉炉粉煤灰、循环流化床粉煤灰,实现粉煤灰的资源化综合利用,随后通过加压脱钠,在高压下将粉煤灰中难以脱除的钠进行脱除,提高氧化铝产品的纯度。本发明的工艺简单,操作方便,尤其是优选使用的浓盐水可以来自于电厂废水,二氧化碳可以来自电厂废气,从而实现电厂三废(固废粉煤灰、废气二氧化碳、废水浓盐水)的回收利用,进一步降低成本,减少环境污染,更适合于工业化大生产。
附图说明
16.构成本技术的一部分的说明书附图用来提供对本发明的进一步理解,本发明的示意性实施例及其说明用于解释本发明,并不构成对本发明的不当限定。在附图中:
17.图1示出了根据本发明实施例1的氧化铝提取流程示意图。
具体实施方式
18.需要说明的是,在不冲突的情况下,本技术中的实施例及实施例中的特征可以相互组合。下面将参考附图并结合实施例来详细说明本发明。
19.正如本发明背景技术中所述,现有技术中存在从粉煤灰中提取氧化铝的工艺复杂、生产成本高、环境污染大的问题。粉煤灰中的硅铝氧化物主要存在于玻璃体和结晶矿物中,因此,必须设法破坏si-o-al和si-o-si网络结构和惰性物质晶体结构,从而释放出活性铝组分。煅烧是激活粉煤灰的一种有效手段,然而仅依赖于煅烧对粉煤灰的活化能力有限,活化后的粉煤灰中仍混有残余的化学活性较低的莫来石等结晶矿物,严重影响粉煤灰中铝组分的提取。目前常用碱熔法在提取前对粉煤灰进行活化,常用的活化剂为碳酸钠与氯化钠的混合物,或者氯化钙与氯化钠的混合物,这是因为需要先使用碳酸钠或者氯化钙将粉煤灰中的莫来石等低活性晶体转变为霞石,然后再用氯化钠辅助将霞石转变为活性更高的
方钠石和钠长石等。而在单独使用氯化钠进行碱熔活化时,难以将si-o-al和si-o-si网络结构完全破坏,粉煤灰中的莫来石和刚玉等稳定晶相几乎不能被转化,活化效果极差。发明人在实际生产过程中发现,可以通过设置两段不同温度的流态化焙烧,极大地增强氯化钠的活化作用,弥补其单独使用时的缺陷,从而可以直接使用电厂废水进行活化,进一步降低成本。
20.具体地,在本发明一种典型的实施方式中,提供了一种从粉煤灰中提取氧化铝的方法,包括以下步骤:步骤s1,将粉煤灰与含有氯化钠的盐水混合,制粒后得到粉煤灰颗粒;步骤s2,将粉煤灰颗粒在200~350℃的温度下进行低温流态化焙烧,然后在700~1100℃的温度下进行高温流态化焙烧,得到活化产物;步骤s3,将活化产物与水混合成料浆,然后在料浆中通入二氧化碳进行加压脱钠,得到含氧化铝滤饼和碳酸盐溶液;步骤s4,向含氧化铝滤饼中加入盐酸水溶液进行溶出,得到溶出液;将溶出液进行结晶,得到氯化铝晶体;焙烧氯化铝晶体,得到氧化铝。
21.本发明先将粉煤灰与含有氯化钠的盐水进行混合,制粒后得到粒度均匀的粉煤灰颗粒,随后进行两段流态化焙烧,先在200~350℃的温度下进行低温流态化焙烧,使粉煤灰中的莫来石和刚玉的一部分转化为霞石,另一部分转化为方钠石。然后在700~1100℃的温度下进行高温流态化焙烧,霞石和方钠石会进一步转化为反应活性较高的钠长石和钾长石。在两段焙烧过程中,氯化钠既作为助熔剂,又作为原料提供na
将粉煤灰中低活性的莫来石和刚玉转变为霞石和方钠石,更进一步转变为活性更高、更易进行铝组分提取的钠长石和钾长石,促进粉煤灰晶相转变,提高粉煤灰的活化水平,得到活化产物。随后将活化产物与水混合成料浆,通入二氧化碳进行加压脱钠,在加压条件下,料浆中钠与氧硅键、氧铝键解离,可溶性的钠盐脱离固相进入到液相当中,与溶液中溶解的二氧化碳和碳酸氢根进行结合,得到含氧化铝滤饼和碳酸盐溶液。最后向含氧化铝滤饼中加入盐酸水溶液进行溶出,得到溶出液;将溶出液进行结晶,得到氯化铝晶体;焙烧氯化铝晶体,得到氧化铝。
22.如背景技术所述,在传统碱法工艺提取氧化铝的过程中,由于粉煤灰中铝硅比较低,在碱性条件下,二氧化硅大量溶出,使得硅铝分离困难,需要使用浮选法、碱浸法和微生物法等复杂的工艺预先进行脱硅,才能实现高含硅粉煤灰中铝的提取,导致生产成本高,渣量大。而本发明由于采用了成本较低的氯化钠单独进行粉煤灰的活化,同时设置了两段流态化焙烧保证了活化效果,最后使用酸溶法进行铝的提取,无需预先进行脱硅,工艺简单,操作方便,在成本较低的同时,可以减少环境污染。此外,煤矸石、低品位铝土矿、赤泥、霞石矿和黏土矿和本发明粉煤灰极为相似,它们的主要成分都是氧化铝和二氧化硅,均为硅酸盐矿物,而且铝的活性都比煤粉炉粉煤灰强,因此本发明的技术方案也可应用于上述矿物原料。
23.粉煤灰的主要成分是氧化铝和二氧化硅,电厂废水的浓盐水主要包含质量分数95%以上的氯化钠,以及少量钾、钙和镁化合物,其中钾、钙和镁主要以离子形式存在,虽然钾、钙和镁离子对粉煤灰也具有一定的活化效果,但由于其含量很低,所以主要活化作用来自于浓盐水中的氯化钠。燃烧尾气主要成分是二氧化碳气体。在一种优选的实施方式中,所使用的含有氯化钠的盐水来自于电厂废水,二氧化碳来自于电厂废气。从而可以实现电厂三废(固废粉煤灰、废气二氧化碳、废水浓盐水)的回收利用,进一步降低成本的同时,减少环境污染。
24.在一种优选的实施方式中,步骤s1中,含有氯化钠的盐水中的氯化钠与粉煤灰的重量比为(0.5~20):1,优选地,含有氯化钠的盐水中的氯化钠与粉煤灰的重量比为(1~5):1,从而在保证粉煤灰完全活化的同时,减少氯化钠加入过多引起的浪费,进一步降低成本,同时进一步减少后续脱钠步骤的负担。造粒方式可以为挤压造粒,粉煤灰颗粒的粒径为1~10mm,在后续的两步焙烧过程中,颗粒可以在低温段与来自高温段的烟气进行热交换,进一步降低成本。
25.为了进一步提高浓盐水中氯化钠对粉煤灰中莫来石等低活性晶体的活化效果,在一种优选的实施方式中,步骤s2中,低温流态化焙烧的温度为280~320℃,低温流态化焙烧的时间为0.5~2h;高温流态化焙烧的温度为900~1100℃,高温流态化焙烧的时间为0.5~4h。上述焙烧均在流态化焙烧炉中进行,该条件下可以更完全地发挥氯化钠的助熔作用,实现晶型的转变,从而进一步提高活化效率。
26.出于在两步焙烧过程中使粉煤灰原料中的莫来石等低活性晶体尽可能地被活化的目的,在一种优选的实施方式中,步骤s2中,高温流态化焙烧的温度与低温流态化焙烧的温度差为750~900℃,高温流态化焙烧的时间与低温流态化焙烧的时间之比为(2~8):1;如此两步焙烧过程更加适配,能够更顺利地完成从低活性的莫来石和刚玉等晶体到高活性的钠长石、钾长石和钙长石等晶体的晶型转化,为后续溶出做准备。
27.脱钠过程需要在溶液中进行,以使得二氧化碳溶解充分发挥脱钠作用,在一种优选的实施方式中,步骤s3中,料浆中活化产物的质量浓度为50~600g/l;优选地,料浆中活化产物的质量浓度为200~300g/l,从而使得活化产物具有合适的浓度,能够进一步增加料浆中活化产物和溶解于料浆中的二氧化碳的接触面积,提高脱钠效率。
28.步骤s3中的料浆成分主要为钠长石和钾长石固体与水形成的浑浊液,呈弱碱性,其中的钠不容易脱除,所以脱钠工艺要比常规工艺条件更加苛刻,在一种优选的实施方式中,脱钠反应的温度为20~200℃,脱钠反应的压力为6~8mpa,脱钠反应的时间为1~48h;优选地,脱钠反应的温度为100~160℃,脱钠反应的时间为2~4h,在此过程中必须要把二氧化碳经过增压泵增压到6mpa以上,同时优选反应温度在100℃以上,以便加快反应速度,增大碱的转化回收率,更有效地进行脱钠。
29.上述脱钠步骤使用的二氧化碳可以采用工业二氧化碳尾气,比如电厂尾气,实现废物利用,降低成本的同时进一步减少环境污染。脱钠后得到的碳酸盐溶液可以进行制碱工序制得工业碱产品及回用水,增加附加价值,回用水也可以用于步骤s3中的料浆制备,进一步降低提取成本。霞石、白榴石、方钠石、方柱石与本发明脱钠料浆中的固体成分钠长石和钾长石类似,因此本发明的脱钠方案也可应用于上述矿物原料。
30.步骤s4中,含氧化铝的滤饼经过酸溶制得氧化铝产品、白泥产品的同时回收盐酸。为了在保证溶出效率的同时进一步降低成本,在一种优选的实施方式中,盐酸水溶液的质量百分比为20~38%,且溶出过程的液固比为(1~15):1,溶出过程的温度为10~200℃,溶出过程的时间为1~48h;优选地,盐酸水溶液的质量百分比为20~28%,且溶出过程的液固比为(2~5):1,溶出过程的温度为20~80℃,溶出过程的时间为1~3h。其中,盐酸水溶液可以采用两段焙烧得到的氯化氢气体进行制备,溶出液中也可以通入氯化氢气体进行盐析结晶,实现工艺副产物的回收利用,减少环境污染的同时进一步降低生产成本。此外,步骤s4在得到氧化铝产品的同时,得到的白泥副产物可用于制作分子筛、免烧砖和塑料填充剂,实
现了废物的二次利用。其中,液固比是指盐酸水溶液和含氧化铝的滤饼的重量比。
31.具体地,酸浸过程中所发生的主要化学反应如下:
32.al2o3 6hcl
→
2alcl3 3h2o
33.fe2o3 6hcl
→
2fecl3 3h2o
34.al6si2o
13
18hcl
→
6alcl3 (2-n)h2sio3 (7 n)h2o n
·
sio235.氧化铝的溶出率(r)计算公式为:
36.或
[0037][0038]
氯化铝焙烧过程中主要发生的化学方程式为:
[0039]
2alcl3·
6h2o
→
al2o3 6hcl
↑
9h2o
↑
[0040]
氧化铝提取率(t)的计算公式为:
[0041][0042]
本发明中al含量测定可依照以下方法进行:
[0043]
方法1:氟化钾置换edta容量法;
[0044]
方法2:电感耦合等离子体发射(icp-oes)法;
[0045]
方法3:x射线荧光光谱分析(xrf)法;
[0046]
具体参照国标gb/t14506.4-2010,gb/t6609,ys/t629-2007,ys/t630-2007。
[0047]
在一种优选的实施方式中,步骤s4中,在进行焙烧之前,还包括将氯化铝晶体用质量分数25~38%的浓盐酸水溶液进行洗涤的步骤,可以除去氯化铝晶体中残余可溶性杂质。
[0048]
为进一步提高焙烧得到的氧化铝产品的纯度,在一种优选的实施方式中,步骤s4中,焙烧过程的温度为800~1200℃,焙烧过程的时间为2~6h。
[0049]
以下结合具体实施例对本技术作进一步详细描述,这些实施例不能理解为限制本技术所要求保护的范围。
[0050]
实施例1
[0051]
粉煤灰为某电厂所排放的高铝煤粉炉粉煤灰,具体成分如表1所示:
[0052]
表1
[0053]
成分sio2al2o3caomgofe2o3tio2so4loi质量分数/%39.7648.102.241.251.981.21.753.3
[0054]
将粉煤灰与质量百分比30%的浓盐水混合均匀后挤压造粒(其中氯化钠与粉煤灰的重量比为3:1),得到6mm的颗粒于流态化焙烧炉中进行两段焙烧,低温段焙烧温度为300℃,焙烧时间0.5h;高温段焙烧温度为1100℃,焙烧时间4h,得到活化产物。将活化产物与水配制成固含200g/l的料浆,通入二氧化碳进行脱钠反应,脱钠温度160℃,脱钠压力8mpa,脱钠时间4h后,固液分离得到含氧化铝滤饼,将滤饼采用质量分数28%的盐酸水溶液进行酸溶,液固比4:1;溶出温度为100℃;溶出时间3h,得到溶出液进行盐析结晶,过滤得到结晶氯化铝,使用质量分数30%的浓盐酸洗涤2次,然后在1000℃焙烧4小时得到氧化铝,氧化铝溶
出率和纯度见表2。工艺流程图见图1。
[0055]
实施例2
[0056]
粉煤灰成分与实施例1相同。
[0057]
将粉煤灰与质量百分比30%的浓盐水混合均匀后挤压造粒(其中氯化钠与粉煤灰的重量比为1:1),得到10mm的颗粒于流态化焙烧炉中进行两段焙烧,低温段焙烧温度为320℃,焙烧时间0.5h;高温段焙烧温度为1100℃,焙烧时间2h,得到活化产物。将活化产物与水配制成固含300g/l的料浆,通入二氧化碳进行脱钠反应,脱钠温度100℃,脱钠压力6mpa,脱钠时间2h得到含氧化铝滤饼,将滤饼采用质量分数20%的盐酸水溶液进行酸溶,液固比5:1;溶出温度为80℃;溶出时间1h,得到溶出液进行盐析结晶,过滤得到结晶氯化铝,使用质量分数30%的浓盐酸洗涤2次,然后在1200℃焙烧2小时得到氧化铝,氧化铝溶出率和纯度见表2。
[0058]
实施例3
[0059]
粉煤灰成分与实施例1相同。
[0060]
将粉煤灰与质量百分比30%的浓盐水混合均匀后挤压造粒(其中氯化钠与粉煤灰的重量比为5:1),得到1mm的颗粒于流态化焙烧炉中进行两段焙烧,低温段焙烧温度为280℃,焙烧时间2h;高温段焙烧温度为900℃,焙烧时间4h,得到活化产物。将活化产物与水配制成固含600g/l的料浆,通入二氧化碳进行脱钠反应,脱钠温度200℃,脱钠压力8mpa,脱钠时间48h得到含氧化铝滤饼,将滤饼采用质量分数38%的盐酸水溶液进行酸溶,液固比2:1;溶出温度为20℃;溶出时间48h,得到溶出液进行盐析结晶,过滤得到结晶氯化铝,使用质量分数30%的浓盐酸洗涤2次,然后在800℃焙烧6小时得到氧化铝,氧化铝溶出率和纯度见表2。
[0061]
实施例4
[0062]
粉煤灰成分与实施例1相同。
[0063]
将粉煤灰与质量百分比30%的浓盐水混合均匀后挤压造粒(其中氯化钠与粉煤灰的重量比为0.5:1),得到6mm的颗粒于流态化焙烧炉中进行两段焙烧,低温段焙烧温度为350℃,焙烧时间0.5h;高温段焙烧温度为1100℃,焙烧时间1h,得到活化产物。将活化产物与水配制成固含50g/l的料浆,通入二氧化碳进行脱钠反应,脱钠温度20℃,脱钠压力8mpa,脱钠时间1h得到含氧化铝滤饼,将滤饼采用质量分数28%的盐酸水溶液进行酸溶,液固比15:1;溶出温度为10℃;溶出时间48h,得到溶出液进行盐析结晶,过滤得到结晶氯化铝,使用质量分数25%的浓盐酸洗涤2次,然后在1000℃焙烧4小时得到氧化铝,氧化铝溶出率和纯度见表2。
[0064]
实施例5
[0065]
实施例5与实施例1的区别在于,氯化钠与粉煤灰的重量比为20:1;低温段焙烧温度为200℃,高温段焙烧温度为700℃;溶出温度为200℃;溶出时间1h,结晶氯化铝使用质量分数38%的浓盐酸洗涤2次,氧化铝溶出率和纯度见表2。
[0066]
实施例6
[0067]
实施例6与实施例1的区别在于,氯化钠与粉煤灰的重量比为4:1;高温段焙烧温度为1100℃,焙烧时间2.5h;溶出温度为80℃,氧化铝溶出率和纯度见表2。
[0068]
实施例7
[0069]
实施例7与实施例1的区别在于,氯化钠与粉煤灰的重量比为4:1;高温段焙烧温度为1100℃,焙烧时间2.5h;料浆脱钠反应为140℃;溶出温度为60℃,氧化铝溶出率和纯度见表2。
[0070]
对比例1
[0071]
对比例1与实施例1的区别在于,将粉煤灰颗粒于流态化焙烧炉中在800℃焙烧时间8h,氧化铝溶出率和纯度见表2。
[0072]
对比例2
[0073]
对比例2与实施例1的区别在于,将料浆在常压下进行脱钠,氧化铝溶出率和纯度见表2。
[0074]
表2
[0075] 氧化铝溶出率(%)氧化铝纯度(%)实施例185.3%98.1%实施例286.5%98.4%实施例385.6%98.3%实施例480.1%92.2%实施例581.2%97.3%实施例686.2%98.5%实施例785.1%98.2%对比例155.4%90.4%对比例285.6%65.1%
[0076]
由表2可知,与对比例1相比,本发明的实施例通过设置两段焙烧,使用氯化钠实现对粉煤灰的活化,而不受粉煤灰原料中莫来石等难溶于酸的物相的限制,氧化铝溶出率均较高。与对比例2相比,本发明的实施例通过加压脱钠,在高压下将粉煤灰中难以脱除的钠进行脱除,提高了氧化铝产品的纯度。尤其是使用本发明优选工艺参数的实施例,氧化铝的溶出率和纯度均较佳。
[0077]
以上所述仅为本发明的优选实施例而已,并不用于限制本发明,对于本领域的技术人员来说,本发明可以有各种更改和变化。凡在本发明的精神和原则之内,所作的任何修改、等同替换、改进等,均应包含在本发明的保护范围之内。
再多了解一些
本文用于企业家、创业者技术爱好者查询,结果仅供参考。