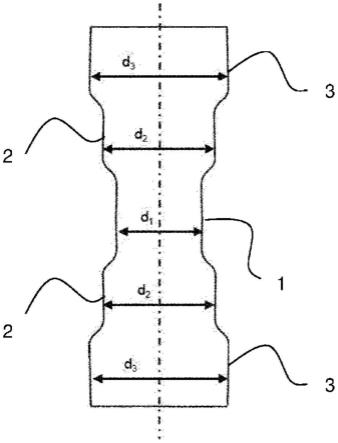
1.本发明涉及一种具有在机动车辆的纵向轴线上的工作方向的机动车辆碰撞盒。本发明还涉及此类部件的制造方法。
背景技术:
2.现有技术的机动车辆在其长度或最长尺寸的每个端部(前端和后端)配备有能量吸收元件作为碰撞保护零件。此类元件被称为碰撞管理系统或缓冲器系统,并且通常通过与两个现有技术的碰撞盒连接的一个横梁彼此附接,该碰撞盒继而与车身构造连接。由此,碰撞盒吸收冲击期间的碰撞动能。碰撞盒通过压缩或折叠而不可逆地塑性变形。因此,应在没有任何结构损坏或畸变的情况下保护车身本身。
3.作为机动车辆的一部分的部件碰撞盒通常具有不同的部分看似相反的特性,如实现高碰撞安全,同时轻质以减少燃料消耗量,从而减少co2排放,并且是高性价比的。此外,碰撞盒提供对行人的保护。进一步要求该部件易于与相邻零件组装,具有最佳的空间利用率,并且部件应在冲击之后容易地更换。“汽车维修研究理事会”开发称为rcar碰撞测试的测试场景,以评估以较低速度水平进行的后冲击碰撞和撞击之后的损坏和修复成本。此类测试的结果对乘客车辆的保险评级具有直接影响,并且因此对最终用户具有相当大的兴趣。
4.若干不同的几何形状已经用于设计用于机动车辆的碰撞盒。具有多室型材或盒形构造的圆形管和多边形管以及模块化设计在部件的纵向方向上可以是锥形渐缩的。虽然均匀管型材提供恒力吸收,但是对横向力和弯曲扭矩的抵抗低于其他几何形状的型材。管呈现为易于生产,并且因此呈现用于碰撞盒的最高性价比的几何形状。
5.响应于碰撞测试机构的增加的需求,诸如euro ncap和u.s.ncap,由设置在一起的两个半壳体提供的并且被分成不同长度区域的广泛型材形式是现今最常见的。为了允许所需碰撞行为,通过均匀折叠将凹坑或波纹引入到碰撞盒中。凹坑或波纹成形在产生的碰撞盒的型材或半壳体中是进一步的制造步骤,从而增加部件成本作为直接结果。
6.存在用于结合用于碰撞盒部件的轻质和碰撞安全的各种现有技术使用的解决方案。美国专利申请公开us2017113638a1描述了横梁,该横梁由轻金属合金制成并被构造作为空心型材以限定内部空间,并且具有顶梁和底梁,其中顶梁和/或底梁具有由呈取向到横梁的内部空间中的套环形式的边缘区限定的凹陷部。在横梁的端部处布置的是碰撞盒,该碰撞盒形成有凸缘,该凸缘的尺寸设定成在机动车辆纵向方向上与横梁的至少一个区域重叠。间隔件布置在横梁的内部空间中并且具有用于由套环形状锁合接合的倒角。紧固件被构造用于穿过凹陷部,并且由此在机动车辆竖直方向上延伸穿过间隔件和每个碰撞盒的凸缘。使用轻金属合金空心型材成本昂贵,并导致制造昂贵的部件。
7.在美国专利申请9663051b2中,将碰撞盒分成不同长度区域。与引入胎圈组合使用的锥形构型表示在制造碰撞盒期间的广泛努力并导致更高的部件成本。
8.在美国专利申请公开2017210319a1中提供制造碰撞盒的成本昂贵方式的另一个
示例,其中在碰撞盒的纵向方向上插入多个支承壁。该支承壁中的至少一个支承壁被设计为保险库。
9.美国专利申请公开2013119705a1公开了一种碰撞盒系统,其中多室型材集成附加支承元件以及紧固型材一起使用。同样,从美国专利申请公开2013048455a1已知的弱化工具和纵向裂缝的集成在部件制造期间表现出附加努力,从而导致更高的部件成本。
10.美国专利申请2011291431a1描述了一种使用锰-硼合金钢级的碰撞盒,该碰撞盒必须冲压硬化,并且进一步在300℃
–
450℃之间进行退火。此类等级的技术缺点在于,即使在其焊接区域中也是脆性的,这是因为其马氏体微结构具有比奥氏体的延展微结构等级显著更低的能量吸收势。此外,冲压硬化加进一步退火的制造工艺导致成本昂贵的生产,具有低效的循环时间、高投资成本和对寿命循环评估不令人满意的影响。美国专利申请2011291431a1指出屈服强度水平r
p0.2
=1,150mpa,其中伸长率a5=8%。这些值与由b
é
la bar
é
ny及其de专利申请854157c众所周知的为延展、可变形且比针对乘客室的车身的乘客安全区的强度低的部件的要求形成对比。在车辆前端和后端的方向上不断地或逐渐阶段地减小强度,并且由于此,汽车的前室和后端被认为是可变形区域。
11.大多数现有技术使用的碰撞盒系统都是机械解决方案,以便使冲击之后的修复或更换情况期间的成本最小化。其他系统也可用,例如使用从国际专利申请公开wo 2011073049a1中已知的传感器。此外,气动式或液压式阻尼器解决方案通常从技术视角是可能的,从而满足部件要求。
12.总之,不存在使用高性价比的管设计的现有技术的碰撞盒系统,该碰撞盒系统通过利用奥氏体钢的目标定向的应变硬化特性来满足实际碰撞要求以及如今的轻质oem的需求。此外,已知现有技术的无制造工艺,使用膨胀成形以形成碰撞盒部件。
技术实现要素:
13.本发明的一个目的是消除现有技术的一些缺点并且提供一种轻质且高性价比的具有在车辆的纵向轴线上的工作方向的机动车辆碰撞盒,该机动车辆碰撞盒由管例如圆形管或多边形管制造,该管通过使用甚至在成形之后利用应变硬化效应具有均匀奥氏体微结构的钢膨胀成不同强度和直径的不同区域。此外,根据车辆模型和其尺寸,本发明的碰撞盒易于组装和规模化。
14.本发明涉及一种具有在机动车辆的纵向轴线上的工作方向的机动车辆碰撞盒及其制造方法。本发明由独立权利要求中公开的内容限定。在从属权利要求中阐述了优选的实施方案。
具体实施方式
15.本发明涉及一种具有在车辆的纵向轴线上的工作方向的机动车辆碰撞盒,该机动车辆碰撞盒由管例如圆形管或多边形管制造,该管通过使用甚至在成形之后利用应变硬化效应具有均匀单相微结构例如均匀奥氏体微结构的钢膨胀成不同强度和直径的不同区域。本发明还涉及此类部件的制造方法。
16.实施方案描述了机动车辆碰撞盒。在一个实施方案中,机动车辆碰撞盒具有在车辆的纵向轴线上的工作方向。机动车辆碰撞盒由管制造,该管通过成形工艺膨胀成胀管,该
胀管包括具有不同材料强度和不同几何形状的至少两个区域。因此,在一个实施方案中,碰撞盒包括具有至少两个区域的胀管。区域中的每个区域具有不同材料强度和不同形状或几何形状。在一个实施方案中,管是圆形管。在另一个实施方案中,管是多边形管。针对本发明的目的,圆形管是其中管的内腔或内部空间以及管的外圆周两者都是圆形的并且具有非波动直径的管。在一个实施方案中,管的内部空间具有沿着管的长度基本上相同的直径,并且类似地,管具有沿着管的长度基本上相同的外径。
17.在另一个实施方案中,区域具有6.0n/mm3–
9.0n/mm3的强度[n/mm2]与直径[mm]的比率。通过根据din en 10216的方法测量强度,其中管的一个区域的钢拉伸测试在室温下在准静态条件下进行。稳定的单相钢的硬化行为从根据din en iso 6892-1:2017-02的拉伸测试已知,该拉伸测试在室温下在平板条件下和准静态条件下进行。通过了解平板条件下材料的应变硬化速率,可以计算与成形程度相关的管膨胀后的所得强度。
[0018]
在一个实施方案中,根据上文所描述的方法测量,不同区域之间的最小强度δ为δrm≥75mpa,优选地为δrm≥120mpa。优化区域之间的强度差以形成用于吸收碰撞动能的防撞缓冲区,如下面的实施方案中所描述,其中取决于分别最小直径,具有其不同区域的胀管首先由具有最小直径的区域折叠,然后由其他区域折叠。
[0019]
换句话说,在一个实施方案中,区域具有与区域的直径成反比例的可折叠性。这意味着具有最小直径的区域首先折叠,并且具有最大直径的区域在冲击上最后折叠。
[0020]
在另一个实施方案中,胀管被构造成通过在冲击之后达到系统的块长度,优选地,lb≥80mm,更优选地lb≥100mm,来提供残留安全区。这限制了将力传递到车辆的乘客室中。
[0021]
在一个实施方案中,纵向方向上的中心用作镜像轴线,并且区域以从外侧开始到中心的方式表征,区域的直径朝着中心减小。
[0022]
在一个优选的实施方案中,胀管的至少一个端部加宽以在管的端部的圆周周围提供凸缘,该凸缘基本上垂直于管盒的纵向轴线及其工作方向。凸缘提供用于将碰撞盒附接到相邻车辆零件例如附接到汽车的缓冲器或底盘的表面。凸缘可以例如作为圆角被焊接为搭接接头上,或者例如通过螺钉或其他机械附接件,如铆钉、钉子、螺母、螺栓等,以搭接接头状态机械附接到相邻车辆零件。此类附接构件提供简便的组装并且在将碰撞盒安装在机动车辆中时使下游的成本最小化。
[0023]
另外的实施方案涉及一种制造具有在车辆的纵向轴线上的工作方向的机动车辆碰撞盒的方法。在一个实施方案中,管被制造为纵向焊接管,优选地通过高频焊接制造为纵向焊接管。焊接管一般成本显著低于冷拔无缝管。焊接特别是高频焊接提供最高的生产速度。此外,高频焊接具有最低可能的热输入。该方法中的热输入集中在待焊接的表面处。热输入的这种集中使得用于焊接薄管的方法是理想的,例如具有0.8mm≤t≤2.5mm的钢厚度的管。减少热畸变并降低管的内部应力。
[0024]
在另一个实施方案中,管在机械漂移膨胀工艺机器中通过机械漂移膨胀工艺膨胀。机械漂移膨胀工艺机器相对廉价。机械漂移膨胀工艺机器可以用于测试焊缝的质量并进行膨胀成形步骤。
[0025]
在一个优选的实施方案中,机械漂移膨胀工艺机器使用用于碰撞盒的至少两个不同区域的至少两个不同的膨胀心轴。使用不同的心轴优化该工艺。
[0026]
在一个合适的实施方案中,机械漂移膨胀工艺机器具有镜像纵向轴线以形成对称
的碰撞盒。
[0027]
在一个实施方案中,管由应变可硬化的完全奥氏体钢、优选地奥氏体不锈钢制造,,该应变可硬化完全奥氏体钢具有通过根据din en iso 6892-1:2017-02在室温下在平板条件下和准静态条件下的拉伸测试测量的初始屈服强度r
p0.2
≥380mpa和初始伸长率a
80
≥40%。
[0028]
在一个具体实施方案中,管具有0.8mm≤t≤2.5mm的初始厚度,并且初始直径与厚度的比率为24≤r
d/t
≤125,更优选地介于40≤r
d/t
≤55之间。厚度和直径可以通过本领域技术人员已知的各种方式来测量,例如利用卡尺或利用机械外径测微计,进一步测量直径的方法可以是光学方法,诸如激光距离测量方法。所描述的厚度和内径的比率对于成形在轿车、卡车、公共汽车或农用车中使用的碰撞盒是最佳的。
[0029]
因此,另外的实施方案涉及胀管的用途。一个实施方案描述了胀管作为机动车辆中的碰撞盒的用途。在一个实施方案中,碰撞盒集成在其中的机动车辆是轿车、卡车、公共汽车或农用车辆。在另一个实施方案中,碰撞盒集成在其中的机动车辆是纯电动车辆。
[0030]
在另一个实施方案中,碰撞盒用作防撞护栏、防护轨中或轨道车辆内部的能量吸收元件。
[0031]
根据本发明的目的,胀管碰撞盒由纵向焊接连续管优选地圆形管制造,由此连续制造的管在第一步骤中切割成稍后需要的部件长度。然后,从管的至少一侧,优选地从管的两个端部,通过机械漂移膨胀工艺膨胀切割成部件长度的管。为了提供经济上有吸引力的部件,纵向焊接工艺优选地是高频焊接工艺,其进一步通过使用奥氏体钢在焊接区域中提供高延展性和电力传输。另选地,激光束焊接工艺可用于满足本发明的方法。
[0032]
切割管通过成形工艺优选地通过机械漂移膨胀工艺膨胀成材料强度和几何形状尤其是管直径不同的至少两个区域。通过使用具有冷可成形应变硬化机制的奥氏体钢,具有较高所得直径的较高膨胀区域提供较高强度水平。作为在机动车辆的纵向方向上冲击情况期间的所得行为,胀管碰撞盒将折叠在一起,由此具有最小直径并因此具有最低强度水平的区域将首先折叠。因为同时在该区域中存在最高伸长率,意味着将冲击动能转化为材料相关塑性变形的能量吸收势处于其最高。如果冲击力没有通过折叠第一区域而减轻,则在具有第二最小直径的区域中发生相同的效果,以此类推。在低能量冲击中,具有最低强度的具有最薄直径的区域将折叠。在较高能量的冲击中,增加的直径和增加的强度的区域也将相继折叠,使得能量可以被碰撞盒连续吸收。因此,碰撞盒吸收冲击动能,使得车身和特别是汽车中的乘员不受这些影响。
[0033]
对冲击的抵抗将利用本发明的碰撞盒和方法的两种方式增加:首先,以材料相关方式,因为使用的应变硬化奥氏体钢在由于其硬化机制而影响冲击期间将增加强度。利用这种效果,相应区域的屈服强度[n/mm2]与直径[mm]的比率可以定义为部件工程师的设计因素。对于本发明的方法,利用胀管碰撞盒和应变可硬化的奥氏体钢的组合,比率适于在6.0n/mm3–
9.0n/mm3之间。对冲击的抵抗将以第二种方式增加,这是几何形状相关的,因为较低直径区域连续折叠到较高直径区域导致更多材料必须在相应的下一折叠步骤期间折叠的效果。在结束时,达到部件条件,其中获得块长度lb,其可被定义为残留安全区,在该残留安全区处,表现对冲击的最大抵抗。优选地,碰撞盒的块长度达到长度为lb≥80mm更优选地长度为lb≥100mm。
[0034]
在一个优选的实施方案中,存在分别具有三个直径(d1,d2,d3)的三个区域(1,2,3),参见图1,因此纵向方向上的中心用作镜像轴线。区域以从外侧开始到中心的方式表征,区域的直径减小。为了实现不同区域的期望折叠行为,优选地由于管的膨胀工艺以这样的方式构造直径:不同区域之间的最小强度δ执行δrm≥75mpa,优选地执行δrm≥120mpa。
[0035]
利用上述构造方式,作为机械漂移膨胀工艺对管进行膨胀的必要机器必须充分适应设计要求。因此,机器设计有具有用于碰撞盒的至少两个不同区域的至少两个不同的膨胀心轴的工具。优选的是,总心轴工具能够成形成在镜像轴线的一侧,管插入到工具中。为了允许高车辆容积的快速且高性价比的生产,进一步优选地,机器具有镜像纵向轴线以形成对称的碰撞盒,从而能够从管的纵向轴线的两侧插入心轴工具,使得从两侧,管同时膨胀到其镜像轴线。
[0036]
为了允许与碰撞盒的相邻零件的连接,胀管的至少一个端部但优选地两个端部加宽以在管的端部的圆周周围提供凸缘,该凸缘基本上垂直于管盒的纵向轴线及其工作方向。凸缘提供用于将碰撞盒附接到相邻车辆零件例如附接到汽车的缓冲器或底盘的表面。凸缘可以例如作为圆角被焊接为搭接接头上,或者例如通过螺钉或其他机械附接件,如铆钉、钉子、螺母、螺栓等,以搭接接头状态机械附接到相邻车辆零件。此类附接构件提供简便的组装并且在将碰撞盒安装在机动车辆中时使下游的成本最小化。
[0037]
此类设计的益处在于,接头的位置和取向被优化以更好地抵抗从车辆的前部或后部冲击期间的应力。
[0038]
在管制造之前的初始材料形式是厚度t≤3.0mm、优选地介于0.8mm≤t≤2.5mm之间的平钢,并且通常以线圈或条带的形式提供给管制造商。其进一步适于限定管的初始直径与厚度的比率,该比率是24≤r
d/t
≤125,更优选地介于40≤r
d/t
≤55之间。单个管可以由片材或板制造,然而,使用条带和线圈作为用于连续管制造的起始材料提供了用于较大车辆容积的高性价比且大规模的工业碰撞盒制造。
[0039]
在一个实施方案中,使用冷可成形且应变可硬化机制的奥氏体钢,优选地不锈钢,该冷可成形且应变可硬化机制的奥氏体钢具有初始屈服强度r
p0.2
≥380mpa和初始伸长率a
80
≥45%。在另一个实施方案中,使用稳定的单相奥氏体钢,即使在成形和焊接之后的完全奥氏体钢提供twip(孪晶诱导塑性)应变硬化效应。
[0040]
为了提供与良好或最佳抗碰撞组合的轻质碰撞盒,意味着安全性,适于使用具有初始强度水平r
p0.2
≥380mpa、更优选地r
p0.2
≥450mpa的高强度钢。除了强度之外,膨胀管的延展性也是重要特性。在碰撞期间进一步需要材料的延展性作为部件的关键特性的能量吸收势。碰撞盒的能量吸收越高,传递到乘客室中并由此乘员上的力和加速度越低。由于碰撞盒材料的延展性,碰撞盒可以连续吸收冲击能量并且舒缓地减小对车辆中的乘员的力。因此,在断裂之后描述为伸长率的延展性的值为a
80
≥40%、优选地为a
80
≥50%适于本发明的初始材料。强度和伸长率的所需组合通过具有奥氏体微结构和应变硬化机制的钢(尤其是通过奥氏体不锈钢)给出,该钢具有铬含量cr≥10.5%。应变硬化的特性使得车辆工程师有可能在完成部件制造之后(在这种情况下,在膨胀管碰撞盒之后)达到最终强度-延展性组合。对于奥氏体钢,存在两种不同的硬化机制:第一硬化在包括制造的冷成形期间发生,并且第二硬化在部件的使用寿命期间发生碰撞冲击。具有亚稳态奥氏体微结构的钢具有trip(相变诱导塑性)的硬化效应,其中在成形载荷期间奥氏体改变为马氏体。对于本发明的方
法优选的是,使用具有所谓的twip(孪晶诱导塑性)硬化效应的具有完全奥氏体微结构的钢,其与介于20mj/m2与30mj/m2之间的特定堆垛层错能(sfe)组合。twip硬化奥氏体钢的益处在于,在胀管期间,微结构在没有脆性马氏体相的情况下保持在初始延展-奥氏体条件中,并且因此部件具有均匀微结构。
[0041]
此外,由于其天然和再钝化铬-氧化物表面层,奥氏体不锈钢提供比低或非合金钢显著更高的耐腐蚀性。因此避免了部件的附加浸涂工艺,并且因此降低了碰撞盒部件的总成本。此外,可以改善生命周期环境冲击。不锈钢碰撞盒部件是完全可再循环的;它可以在部件的寿命结束时在电弧炉中熔融。
[0042]
胀管碰撞盒可以在每个机动车辆中使用,优选地在轿车内部使用,但也可以在卡车、公共汽车或农用车辆内部使用。还可以通过将厚度和直径改变为较高值来调整本发明的方法,以能够在轨道车辆内部使用。此外,胀管碰撞盒也可以作为能量吸收元件集成到防撞护栏或防护轨系统中,以在撞击期间保护侵入车辆及其乘员。
附图说明
[0043]
参考附图更详细地示出了本发明。
[0044]
图1示出了通过侧视图示意性地示出的本发明的一个实施方案,
[0045]
图2示出了根据部件的纵向长度的部件强度的关系,
[0046]
图3通过侧视图示出了来自初始车辆安装的部件几何形状中的情况(左侧)和在冲击情况期间的成形行为(右侧),
[0047]
图4通过侧视图示出了在冲击达到块长度期间部件的行为,
[0048]
图5通过侧视图示出了胀管与相邻车辆零件的焊接连接。
[0049]
说明本发明的实施方案
[0050]
图1通过侧视图示出了制造之后的胀管碰撞盒。虚线展示纵向对称轴线。在本发明的该实施方案中,存在横向方向上对称的三个区域(1)、(2)、(3),由此具有最小直径d1的区域1(1)位于中心区域中。从中心到纵向外侧,区域的直径增加,展示为区域2(2)和区域3(3)。
[0051]
图2针对图1中示出的部件示出了在具有不同区域的部件的纵向方向上的强度的关系,由此过渡区域(4)位于来自图1的主要区域(1)、(2)和(3)之间。横向虚线(5)展示了其中区域变化并因此直径和强度变化进行的起始点。具有最小直径d1的区域1具有最低强度水平。随着直径增加,强度水平也增加。对于图1的实施方案,结果是存在命名为δrm(6)的两个强度差。每个直径之间的强度差基本上相同。
[0052]
图3示出了在从纵向侧的冲击情况期间部件的成形行为,由此来自图1的具有最低直径并因此具有最低强度水平的区域(1)折叠。根据具体强度水平,具有较高直径的区域将在具有较低直径的区域上方滑动。
[0053]
图4示出了来自图3的在被称为块长度lb(7)的其结束位置处的正在进行的冲击,其中部件的能量吸收耗尽。块长度lb(7)进一步等于残留安全区,其他部件可以位于该残留安全区中并且不会受到冲击的影响。
[0054]
图5示出了本发明的一个优选的实施方案,其中胀管的至少一个端部以这样的方式加宽:端部(8)在管碰撞盒的纵向轴线及其工作方向上弯曲,以能够在搭接接头(9)上接
合到相邻车辆零件(10)。接合可以作为圆角被执行为焊接,或类似于作为搭接接头如螺纹连接被执行为机械接合。
再多了解一些
本文用于企业家、创业者技术爱好者查询,结果仅供参考。