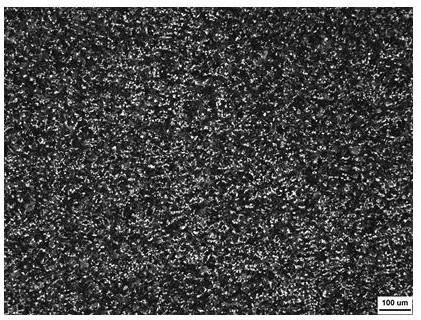
1.本发明属于冶金技术领域,涉及一种电机转轴用非调质钢的生产方法。
背景技术:
2.化石能源使用导致的全球环保压力越来越大,这推动了新能源特别是电力能源的高速发展。在电力能源的使用中,不可避免的需要使用电机。目前电机的制造,国际先进水平主要体现在电机的可靠性高,寿命长,通用化程度高,电机效率不断提高,噪声低,重量轻,电机外形雅观,绝缘等级采用f级和h级,而且也考虑电体制造成本的降低等。
3.在材料的使用上,普通电机转轴主要使用的是国标的碳素结构钢及合金结构钢如45、40cr等,这种类型的钢种都需要进行调质热处理效率相对于非调质钢来说较低,且成本较高,最重要的是减少热处理环节,更加环保。开发和推广的使用非调质钢来替代普通碳素结构钢和合金结构钢生产电机转轴是大有前景的。普通的中碳非调质钢,如国标f45mnvs系列,抗拉强度一般能够达到700~800mpa,但普遍冲击韧性和疲劳寿命较差,常温下的冲击韧性在30-40j,疲劳寿命也仅能够达到5万次左右。
技术实现要素:
4.本发明旨在一种电机转轴用非调质钢的生产方法,其代表钢种为fyz48直径范围φ20~100mm,屈服强度在500mpa以上,抗拉强度在800~850mpa,常温1/2半径处冲击韧性40j以上,经疲劳寿命台架实验,其疲劳寿命能达到10万次,能够很好的满足中高端电机转轴使用需求。
5.本发明的技术方案:一种电机转轴用非调质钢的生产方法,采用工艺路线为转炉 真空脱气 连铸 轧制 保温缓冷。钢的组成重量百分比为c=0.45%~0.51%,si=0.30%~0.60%,mn=0.70%~1.00%,p≤0.025%,s=0.025%~0.035%,nb=0.018%~0.023%,ti=0.010%~0.040%,cr=0.10%~0.30%,v=0.13%~0.15%,n=0.0100%~0.0200%,cu≤0.35%,mo≤0.25%,其余为fe和不可避免的杂质;关键工艺步骤包括:(1)加热:连铸坯加热温度1180~1220℃,均热段时间≥90min,总加热时间≥270min。
6.(2)轧制:粗轧采用大压下量热轧,开轧温度≥980℃,前2道次压下量25%~30%;终轧采用双相区轧制,kocks机组出成品,开启中间水箱,控制终轧温度760-800℃。
7.(3)控制冷却:轧后冷床使用保温罩缓慢冷却,下冷床后入缓冷坑保温缓冷。
8.发明原理:本发明在成分设计上以提高圆钢的力学性能及冲击韧性为目的。再通过高的加热温度及长的加热时间控制圆钢横截面上的偏析,避免成品圆钢带状组织过高。通过粗轧高温大压下量充分破碎晶粒,促进心部金属流动。采用水箱冷却控制终轧温度来实现双相区轧制,并配合冷床保温及入坑缓冷,从而达到提高成品圆钢组织中铁素体的含量,细化圆钢
晶粒,并使强化元素v、nb、ti充分析出,来增加圆钢总体的强度及韧性。
9.本发明化学成分设计重点考虑细化晶粒及v/n复合强化,使得成品圆钢具有高强度和良好的韧性,兼顾一定的切削性能。组织设计则是以细珠光体加铁素体为基体的韧性组织,添加了多种细化晶粒的元素。含v钢中添加n,其沉淀强化的作用明显提高。n含量从50ppm增加到250ppm时,钢的屈服强度提高100~150mpa,即10ppm的n提高钢的屈服强度约5mpa。随条件的不同,n的作用大小也不会相同,但增加含v非调质钢中n的含量,对提高钢的强度特别是提高屈服强度的作用是明显的。
10.采用中碳锰的成分设计,一定c含量能适当的提高提高强度和降低ar3温度,但对钢的韧性不利,因此通过转炉出钢[c]≤0.008%等手段控制最终碳含量≤0.50%;锰是弱碳化物形成元素,它可以降低奥氏体转变温度,细化铁素体晶粒,对提高成品强度和韧性有益,因此,在成分设计时,锰设计下限0.70%,但mn含量过高易导致中心偏析,对疲劳性能有害,故锰设计上限1.00%。
[0011]
为了确保冲击韧性,钢水必须具有较高的纯净度。p为有害杂质元素,通过控制转炉出钢时p≤0.010%,并通过lf rh复合精炼工艺,白渣保持时间≥20min,精炼渣碱度cao/sio2≥2.5,vd炉保真空时间18~25min等手段控制,使终点磷含量p≤0.025%,并降低钢水中其他杂质和有害气体含量。硫含量0.025%~0.035%,适当添加部分硫来达到增加圆钢切削性能的目的。
[0012]
为了提高力学性能、细化晶粒提高冲击韧性,在c-mn钢固溶强化的基础上,复合添加nb、ti等合金元素,充分发挥细化晶粒、沉淀强化和相变强化等作用以达到高强度高韧性、细晶粒目的。
[0013]
nb作为一种重要的微合金元素,添加0.02%以上的nb,可形成细小的碳化物和氮化物,抑制奥氏体晶粒的长大,并且结合开轧温度≥980℃,末三道次压下率≥16%等手段,细化原始奥氏体晶粒,终轧温度控制在760~800℃,抑制奥氏体的再结晶,保持变形效果从而细化晶粒。但当nb含量大于0.05%时,碳氮化铌等会大量在成品圆钢中析出并长大,显著影响其性能。
[0014]
钢中进行微ti处理,添加0.008以上的ti有利于加热温度在1180℃~1220℃之间时形成tin钉扎晶界,抑制奥氏体晶粒过分长大,并且在轧制过程中细化晶粒,改善圆钢的冲击性能和焊接性能的作用;但ti含量大于0.02%时,会形成部分ti复合夹杂物,反而成为钢中的断裂源,对钢的冲击及疲劳性能非常有害。
[0015]
本发明的有益效果:1)本发明自创中碳高锰、nb-v-ti-n多元微合金化成分设计体系,lf rh复合精炼技术,严格控制p含量和钢水的纯净度,适当添加s元素,并采用高温大压下、双相区控轧等一系列轧制新技术,成功开发了以细珠光体加铁素体组织为机体的高强度、高屈服、高疲劳寿命、易切削加工圆钢,为电机转轴用钢替代升级奠定了基础。
[0016]
2)本发明生产的圆棒,替代传统的热处理工艺国标材,充分发挥设备优势,生产φ20~100mm规格,代表钢种为fyz48直径范围φ20~100mm,屈服强度在500mpa以上,抗拉强度在800~850mpa,常温1/2半径处冲击韧性80j以上,经疲劳寿命台架实验,其疲劳寿命能达到10万次,能够很好的满足中高端电机转轴使用需求。
[0017]
3)本发明利用一般钢厂现有设备和工艺条件,既不增加投资和生产成本,又提高
了生产效率,节能减耗,广泛应用于机械加工各个领域,替代部分需调质热处理的合金结构钢。
附图说明
[0018]
图1为本发明实施例1的圆钢金相组织图(100x-1/2r)。
[0019]
图2为本发明实施例1的圆钢金相组织图(500x-1/2r)。
具体实施方式
[0020]
下面结合实施例对本发明的内容作进一步说明:实施例1:一种电机转轴用非调质钢的生产方法,钢的化学成分组成重量百分比为c=0.48%,si=0.52%,mn=0.91%,p=0.010%,s=0.025%,cr=0.22%,v=0.14%,n:0.0142%,nb=0.020%,ti=0.012%,其余为fe和不可避免的杂质;转炉出钢p=0.008%,c=0.008%,采用lf rh精炼工艺,lf炉精炼全程吹氩,造渣脱氧,白渣保持时间21min,精炼渣碱度cao/sio2=3.5;rh真空脱气处理,在真空度0.5tor以下,真空保持时间23min,出站钢水n=180ppm,h=1.5ppm,o=16ppm;连铸采用全程保护浇铸,中包过热度23℃,连铸坯尺寸280
×
280mm;关键工艺步骤包括:(1)加热:温度1190~1200℃,均热时间93min。
[0021]
(2)轧制:开轧温度1070℃,粗轧前2道次压下率分别为28%,26%;终轧采用kocks机组出成品,终轧温度760-800℃。
[0022]
(3)冷却:轧后冷床使用保温罩缓慢冷却,下冷床后入缓冷坑保温缓冷,入坑温度420℃,在坑时间26h。
[0023]
圆钢力学性能见表1所示。
[0024]
实施例2:一种电机转轴用非调质钢的生产方法,钢的化学成分组成重量百分比为c=0.47%,si=0.50%,mn=0.89%,p=0.010%,s=0.029%,cr=0.21%,v=0.14%,n:0.0135%,nb=0.020%,ti=0.013%,,其余为fe和不可避免的杂质;冶炼转炉出钢p=0.008%,c=0.008%,采用lf rh精炼工艺,lf炉精炼全程吹氩,造渣脱氧,白渣保持时间21min,精炼渣碱度cao/sio2=3.5;rh真空脱气处理,在真空度0.5tor以下,真空保持时间23min,出站钢水n=185ppm,h=1.5ppm,o=19ppm;连铸采用全程保护浇铸,中包过热度25℃,连铸坯尺寸280
×
280mm;关键工艺步骤包括:(1)加热:温度1180~1200℃,均热时间90min。
[0025]
(2)轧制:开轧温度1060℃,粗轧前2道次压下率分别为28%,26%;终轧采用kocks机组出成品,终轧温度760-800℃。
[0026]
(3)冷却:轧后冷床使用保温罩缓慢冷却,下冷床后入缓冷坑保温缓冷,入坑温度400℃,在坑时间24h。
[0027]
圆钢力学性能见表1所示。
[0028]
实施例3:一种电机转轴用非调质钢的生产方法,钢的化学成分组成重量百分比为c=0.47%,si=0.53%,mn=0.92%,p=0.010%,s=0.027%,cr=0.21%,v=0.14%,n:0.0122%,nb=0.020%,ti=
0.011%,其余为fe和不可避免的杂质;冶炼转炉出钢p=0.008%,c=0.008%,采用lf rh精炼工艺,lf炉精炼全程吹氩,造渣脱氧,白渣保持时间21min,精炼渣碱度cao/sio2=3.5;rh真空脱气处理,在真空度0.5tor以下,真空保持时间23min,出站钢水n=173ppm,h=1.5ppm,o=14ppm;连铸采用全程保护浇铸,中包过热度24℃,连铸坯尺寸280
×
280mm;关键工艺步骤包括:(1)加热:温度1190~1210℃,均热时间97min。
[0029]
(2)轧制:开轧温度1070℃,粗轧前2道次压下率分别为28%,26%;终轧采用kocks机组出成品,终轧温度760~800℃。
[0030]
(3)冷却:轧后冷床使用保温罩缓慢冷却,下冷床后入缓冷坑保温缓冷,入坑温度450℃,在坑时间24h。
[0031]
圆钢力学性能见表1所示。
[0032]
实施例4:一种电机转轴用非调质钢的生产方法,钢的化学成分组成重量百分比为c=0.48%,si=0.50%,mn=0.90%,p=0.010%,s=0.030%,cr=0.18%,v=0.14%,n:0.0119%,nb=0.020%,ti=0.012%,其余为fe和不可避免的杂质;冶炼转炉出钢p=0.008%,c=0.008%,采用lf rh精炼工艺,lf炉精炼全程吹氩,造渣脱氧,白渣保持时间21min,精炼渣碱度cao/sio2=3.5;rh真空脱气处理,在真空度0.5tor以下,真空保持时间23min,出站钢水n=168ppm,h=1.5ppm,o=19ppm;连铸采用全程保护浇铸,中包过热度25℃,连铸坯尺寸280
×
280mm;关键工艺步骤包括:(1)加热:温度1190~1200℃,均热时间98min。
[0033]
(2)轧制:开轧温度1070℃,粗轧前2道次压下率分别为28%,26%;终轧采用kocks机组出成品,终轧温度760-800℃。
[0034]
(3)冷却:轧后冷床使用保温罩缓慢冷却,下冷床后入缓冷坑保温缓冷,入坑温度400℃,在坑时间26h。
[0035]
圆钢力学性能见表1所示。
[0036]
表1 实施例中圆钢的力学性能。
[0037]
从表1测试结果可见,采用本发明的方法生产的圆棒,当直径达到60mm时,屈服强度仍能达到500mpa以上,抗拉强度820-840mpa,面缩和延伸率优良,常温冲击韧性能达到80j以上。金相组织检验见图1,组织以珠光体为主占比70%左右,剩余为铁素体组织,平均晶粒度7.0~8.0级别,保证了热轧态圆钢具有良好的韧性和强度。
再多了解一些
本文用于企业家、创业者技术爱好者查询,结果仅供参考。