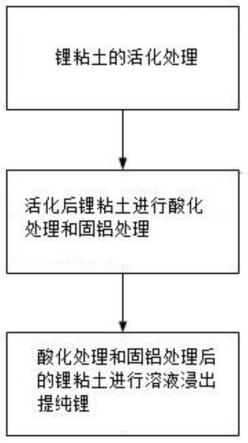
1.本发明涉及金属冶炼技术领域,尤其涉及一种含锂粘土提纯锂的方法。
背景技术:
2.自然界锂资源通常可以分为盐湖卤水型、硬岩型和黏土型三大类。目前,世界范围内开采利用最多的是盐湖卤水型锂矿和硬岩型锂矿。黏土型锂矿发现较晚,还未进行大规模的开发利用,但已有锂资源的分布格局和现实需求,使得该类型锂矿受到高度重视。该类型锂矿提纯锂工艺可以归纳为直接浸出法、助剂焙烧法和氯化硫化法。直接浸出法是相对焙烧浸出而言的,主要是指直接向未经过高温焙烧的矿石中添加浸出剂而进行的提取工艺。主要包括水浸法、硫酸浸出法等。对于火山岩黏土型锂矿,较为有效的锂提取工艺主要集中在使用助剂和矿样混合焙烧(或制粒焙烧),然后采用水浸得到含锂溶液。常用的助剂包括:氢氧化物、碳酸盐、硫酸盐、氯化物以及石灰石、石膏等天然物料或工业副产物。氯化硫化法即将样品置于hcl或so2氛围中焙烧一段时间后,再对充分氯化或硫化后的黏土锂矿样品进行水浸的一种工艺方法。每种浸出工艺都有其固有缺点,水浸出法浸出效率较低、酸浸出法浸出液铝含量高,除杂锂损失率高、硫酸盐焙烧法焙烧温度高,能源消耗大、氯化硫化法对设备腐蚀严重,环保压力较大。
3.根据目前公开的资料,盐湖卤水型锂资源由于锂元素基本在溶液中,分离较为容易,但盐湖卤水型锂资源丰度低,处理成本较高,且工艺较为成熟,进一步降低开发成本潜力较低,进一步开发利用潜力有限;硬岩型和黏土型锂资源由于丰度高、储量大,如何改进开发提纯工艺、降低开发成本成为日益关注的焦点。硬岩型锂资源作为目前已经广泛开发的来源,由于形成地质原因其自身具有密实的结构,在提纯锂元素时引入杂质量较少,已经被广泛应用;但由于硬岩型锂资源对矿脉要求较高,实际可供开采的矿脉有限,并属于不可持续的资源,且矿脉开采难以避免对环境的不良影响。不同的是,黏土型锂资源由于自身结构松散、杂质溶出率高和回收率低,之前一直被认为是不具备开发价值的来源;但黏土型锂资源由于矿脉形成时间短、形成条件较为不苛刻,一直是具有巨大储量的宝藏。目前还未有已经运行的工程技术方案用于含锂粘土中锂的提取,绝大部分技术处于实验室阶段。含锂粘土中铝、氟含量高,锂含量低,常规焙烧-酸浸工艺大气氟污染严重、浸出液铝含量高导致除杂锂损失大,亟需改进含锂粘土锂提取工艺。
技术实现要素:
4.本发明的目的在于解决背景技术中的至少一个技术问题,进一步降低含锂粘土提取锂过程中杂质引入、降低有毒物质(例如氟)的污染并进一步提高锂的纯度和收率,本发明提供一种含锂粘土提纯锂的方法。
5.为实现上述发明目的,本发明提供一种含锂粘土提纯锂的方法,包括以下步骤:含锂粘土的活化处理;活化后含锂粘土进行酸化处理和固铝处理;酸化处理和固铝处理后的含锂粘土进行溶液浸出提纯锂。
6.本发明的一个方面,所述活化处理的试剂为硫酸盐;所述含锂粘土为火山岩黏土型锂矿、碳酸盐黏土型锂矿或贾达尔锂硼矿;所述硫酸盐与所述含锂粘土的质量比范围为0-0.5:1;所述硫酸盐为硫酸钠、硫酸钾、硫氢酸钠、硫氢酸钾、硫酸钙、硫酸亚铁、硫酸铁中的一种或多种。
7.本发明的一个方面,所述活化处理为机械力化学活化;所述机械力化学活化的时间10min-120min;所述机械力化学活化通过搅拌磨机、行星磨机、振动磨机或者滚筒磨机实现。
8.本发明的一个方面,所述固铝处理采用含钙矿石、含钙盐、含钙无机碱、含钙无机氧化物中的一种或多种;所述固铝处理使用的试剂与所述活化后含锂粘土的质量比范围为0.01-0.5:1;和,所述固铝处理使用的试剂作为减少氟溶出的固氟试剂使用。
9.本发明的一个方面,所述固铝处理采用碳酸钙、方解石、石灰石、氧化钙、氢氧化钙中的一种或多种。
10.本发明的一个方面,所述酸化处理使用浓硫酸、柠檬酸、草酸中的任一种;所述酸化处理使用的试剂与所述活化后含锂粘土的质量比范围为0-1:1。
11.本发明的一个方面,所述酸化处理和固铝处理的同时需要温度为 300℃-1000℃,时间为10min-480min的热处理;通过隧道窑、酸化焙烧回转窑、链篦机回转窑或者夹套反应釜实现所述热处理。
12.本发明的一个方面,所述溶液浸出提纯锂的浸出温度为10℃-50℃,浸出时间30min-480min,浸出液固比1-10;所述溶液浸出提纯锂的原料液为水或酸;通过夹套反应釜、搅拌槽或者加压反应釜实现所述溶液浸出提纯锂。
13.本发明的一个方面,所述溶液浸出提纯锂的操作为:所述溶液浸出提纯锂的原料液浸出后第一次固液分离得到浸出液,将所述浸出液循环用于酸化处理和固铝处理后的含锂粘土的浸出,所述浸出液中累积的锂浓度》10g/l后,向所述浸出液添加双氧水和氢氧化钠混合液进行第一次除杂和第二次固液分离;所述第一次除杂除去的杂质包含铝和铁。
14.本发明的一个方面,所述第二次固液分离后还可以向所述第二次固液分离的分离液加入碳酸钠或碳酸钾后沉淀、第三次固液分离制备粗制碳酸锂。
15.本发明的一个方面,所述第三次固液分离的分离液可以用于酸化处理和固铝处理后含锂粘土的浸出提纯锂或除水后作为资源回收。
16.本发明的一个方面,所述粗制碳酸锂还可以经饱和碳酸锂溶液洗涤后,加入二氧化碳处理后过滤精制得精制碳酸锂溶液
17.本发明的一个方面,所述精制碳酸锂溶液还可以经阳离子树脂二次除杂和进一步除水后制备高纯度碳酸锂;所述二次除杂杂质包含:镁和钙;所述高纯度碳酸锂质量组成满足以下条件:li2co3≥99.5%。
18.有益效果
19.根据本发明的技术方案,能够有效地对天然含锂黏土和已经经过提纯锂以后的分离出来的物料的渣滓进行进一步锂提取,将含锂粘土中的锂浸出回收,使得最终被分离的含锂粘土的含锂量显著降低,保证矿产资源的高效利用,有效节约资源,解决了含锂粘土提纯锂存在的杂质多、有毒物质(例如氟)的污染和锂收益率低的问题,进一步拓展了锂元素来源,保证锂矿含锂粘土中锂的浸出率》90%,锂综合回收率》80%,制得li2co3产品中,
li2co3≥99.5%,含锂粘土中锂资源得到有效回收利用:
20.1.采用硫酸盐处理使得在微观层面,含锂粘土含锂物质微粒表面和晶格发生变化,含有锂的晶格位置被硫酸盐中阳离子替换进而完成锂的转移,由原本较稳定相态分散至较不稳定的相态(例如离子态),有利于进一步的收集和分离,较普通的混匀高温焙烧工艺可以加快硫酸盐和稳定状态锂的反应速率;
21.2.进一步地,在机械力化学处理设备作用下,有助于提高硫酸盐和锂原料反应效率,在微观层面摩擦碰撞有利于含锂物质微粒粉碎、破坏和细化,增大含锂物质微粒比表面积,进一步增大反应速率,增大锂元素收率;
22.3.加入固铝试剂可以有效减小浸出时铝离子浸出率和浸出液中铝离子浓度,有助于减小锂提取过程中损失并提高锂的综合回收率;
23.4.加入固铝试剂同时可以起到固氟作用,减小氟的挥发率,减少氟排放和对大气的污染。
附图说明
24.图1示意性表示根据本发明的含锂粘土提纯锂的方法的流程图;
25.图2示意性表示根据本发明的一种实施例的含锂粘土提纯锂的方法的流程图;
26.图3示意性表示根据本发明实施例1中的含锂粘土提纯锂的方法的流程图;
27.图4示意性表示根据本发明实施例2中的含锂粘土提纯锂的方法的流程图。
具体实施方式
28.现在将参照示例性实施例来论述本发明的内容。应当理解,论述的实施例仅是为了使得本领域普通技术人员能够更好地理解且因此实现本发明的内容,而不是暗示对本发明的范围的任何限制。
29.如本文中所使用的,术语“包括”及其变体要被解读为意味着“包括但不限于”的开放式术语。术语“基于”要被解读为“至少部分地基于”。术语“一个实施例”和“一种实施例”要被解读为“至少一个实施例”。
30.图1示意性表示根据本发明的含锂粘土提纯锂的方法的流程图;图2示意性表示根据本发明的一种实施方式的含锂粘土提纯锂的方法的流程图。结合图1 和图2所示,根据本发明的含锂粘土提纯锂的方法,包括以下步骤:
31.a.将含锂粘土与硫酸盐添加剂混合均匀,进行机械力化学活化;
32.b.将活化后的含锂粘土与酸混合,将混合后的含锂粘土与酸进行热处理,热处理过程同时进行固铝处理;
33.c.将步骤b处理后的含锂粘土进行溶液浸出提纯锂;
34.d.提纯锂后的第一次固液分离得到浸出液和浸出渣,浸出液循环使用用于c 步的浸出,浸出液中锂浓度》10g/l后提纯锂后的浸出液添加双氧水和氢氧化钠沉淀铝、铁杂质进行第一次除杂;第一次除杂的杂质经第二次固液分离去除后,第二次固液分离的分离液中添加碳酸钠或碳酸钾,然后经第三次固液分离得到粗制碳酸锂和沉锂余液,沉锂余液回用于步骤c浸出提纯锂或者采用蒸发结晶获得混合硫酸盐回用;
35.e.粗制碳酸锂利用饱和碳酸锂溶液洗涤后调浆通入二氧化碳氢化,除去不溶性碳
酸盐,过滤制得精制碳酸锂溶液;
36.f.精制碳酸锂溶液通过阳离子树脂深度除钙、镁,然后焙烧获得电池级碳酸锂。
37.在本实施方式中,硫酸盐添加剂与含锂粘土的质量比范围为0-0.5:1,机械力化学活化时间10min-120min;
38.b步骤中的酸为浓硫酸、柠檬酸、草酸中任一种,酸与含锂粘土的质量比范围为0-1:1;浓硫酸为95%以上的浓硫酸,柠檬酸和草酸为固体)
39.热处理的温度为300℃-1000℃,热处理时间为20min-480min。
40.固铝试剂与活化后的含锂粘土的质量比范围为0.01-0.5:1。
41.浸出液原料液选用水或酸,浸出温度为10℃-40℃,浸出时间30min-480min,浸出液固比1-10;酸为5%-50%浓度的硫酸溶液。
42.在本实施方式中,硫酸盐添加剂为硫酸钠、硫酸钾、硫氢酸钠、硫氢酸钾、硫酸钙、硫酸亚铁、硫酸铁中的一种或几种的组合。
43.固铝试剂为碳酸钙、方解石、石灰石、氧化钙、氢氧化钙中的一种或几种的组合。
44.含锂粘土为火山岩黏土型锂矿、碳酸盐黏土型锂矿或和贾达尔锂硼矿。
45.在本实施方式中,通过搅拌磨机、行星磨机、振动磨机或者滚筒磨机实现第一物料进行机械力化学活化;
46.通过隧道窑、酸化焙烧回转窑、链篦机回转窑或者夹套反应釜实现热处理;
47.通过夹套反应釜、搅拌槽或者加压反应釜实现水浸出或者酸浸出;
48.通过板框压滤机、精密过滤器或者带式过滤机实现所述固液分离。
49.根据本发明的上述方案,采用机械力化学结合热处理两种工艺的优势,能够有效地对含锂粘土进行锂提取,降低含锂粘土热处理焙烧温度,将含锂粘土中锂的浸出回收,使得最终被分离的含锂粘土的含锂量显著降低,同时通过加入独特的固铝和固氟工艺,可以进一步降低浸出液中杂质离子(例如氟和铝)的含量,保证浸出液中杂质离子含量低,避免浸出液纯化过程锂损失过高和对环境污染,保证矿产资源的高效利用,有效节约资源,保证了含锂粘土锂浸出率》90%,浸出液铝离子浓度《1g/l,锂综合回收率》70%,碳酸锂纯度≥99.5%,碳酸锂产品达到电池级碳酸锂行业标准(y/s 582-2006),含锂粘土中锂资源得到有效回收利用。
50.为便于理解,本发明列举以下实施例。本领域技术人员将会理解,以下实施例仅为本发明的优选实施例,仅用于帮助理解本发明,因而不应视为限定本发明的范围。
51.试验方法
52.锂黏土或锂矿石中氟元素测试方法:参照gb/t15555.12-1995固体废弃物中氟化物测定离子选择性电极法。
53.浸出液中氟元素测试方法:gb/t 5009.167-2003反相高效液相色谱法。
54.锂黏土或锂矿石中锂元素测试方法:锂矿石、铷矿石、铯矿石化学分析方法第1部分:锂量测定gb/t 17413.1-2010。
55.锂黏土、锂矿石或锂矿石浸出渣中氧化铝测试方法:gb t 6730.56-2004,铁矿石铝含量的测定火焰原子吸收法。
56.浸出液中铝离子浓度测试方法:石墨炉原子吸收法。
57.浸出液中锂元素测试方法:火焰原子吸收法。
58.铝浸出率=浸出液中铝离子浓度
×
浸出液体积/(含锂原料质量
×
含锂原料铝含量)
×
100%;铝浸出率为浸出液中锂浓度》10g/l时,根据浸出液中铝离子浓度计算得出。
59.氟挥发率=(含锂原料氟含量-处理后浸出渣氟含量)/含锂原料氟含量
×
100%;含锂原料氟含量与处理后含锂原料氟含量均以烘干后的含锂原料或处理后含锂原料干重量计。
60.锂浸出率=浸出液中锂离子浓度
×
浸出液体积/(含锂原料质量
×
含锂原料锂元素含量)
×
100%。
61.上述含锂原料为本技术公开的锂黏土或锂矿石中任一种,如无特殊说明,所述含锂原料处理方式为本技术公开的任一种对含锂原料处理,回收和收集锂或锂化合物的方法。
62.实施例1
63.采用常规焙烧-水浸工艺对比河南某含锂粘土(火山岩黏土型锂矿)、江西某锂云母浸出渣、四川某锂辉石的浸出率和浸出液铝离子浓度及浸出渣氟含量。热处理条件:硫酸钠添加量20%,焙烧温度950℃,水浸温度25℃。氢氧化钠和双氧水用量均为10g/l,浸出液选用水。采用图3所示的工艺流程,处理江西某锂云母浸出渣、四川某锂辉石作为对照;同时设置空白对照,采用相同的河南某含锂粘土,采用图2所示的工艺流程,其中不包含酸化处理过程,和图3所示的工艺流程相比仅仅增加了固铝试剂(碳酸钙)处理过程;表1示出了原料组成和铝浸出率具体参数,表2示出了本实施例四个实验组的试剂和工艺条件:
[0064][0065]
表1
[0066][0067]
表2
[0068]
表1所示:相同工艺条件下,含锂粘土铝浸出率最高,且浸出液中铝离子浓度最高。这是因为含锂粘土松软结构内部晶体结构不紧密,杂质元素更容易浸出;而锂云母浸出渣和锂辉石等锂矿石在地质形成时经过高压,甚至高温高压共同作用,晶体结构和质地更为紧密,具有杂质元素(尤其是铝)低浸出率的优势。而过高的铝杂质在后续除杂会产生大量非晶态氢氧化铝,会吸附固定锂造成大量锂损失。
[0069]
在本实施例中,采用附图2或附图3提供的方法对锂云母、锂辉石、含锂粘土进行处理,试验结果如下表3所示:
[0070][0071]
表3
[0072]
本实施例中未添加固铝钙剂的河南某含锂粘土,相比较锂云母浸出渣和锂辉石,含锂粘土中的氟挥发严重,对空气造成一定污染,锂浸出率较高,但浸出液中铝离子浓度和沉锂余液铝离子浓度较高导致锂综合回收率较低;而空白添加有固铝试剂碳酸钙,其浸出液和沉锂余液中铝离子含量显著降低,氟挥发率也显著降低。
[0073]
实施例2
[0074]
进一步地,为了验证机械力化学活化处理方式对含锂粘土的锂综合回收率影响,设置实验组1和实验组2:实验组1使用附图2方法进行处理,且处理过程不包含酸化处理和添加固铝试剂过程;实验组2使用附图4方法进行处理。区别在于,实验组1经过机械力化学活化5min,而实验组2未经过机械力化学活化,其余条件相同。
[0075]
如表4所示,实验组1和实验组2采用相同的河南某含锂粘土(碳酸盐黏土型锂矿),氢氧化钠和双氧水用量均为5g/l,浸出液选用5%稀硫酸,如表5 所示,在相同条件下热处理:硫酸钠添加量20%,焙烧温度950℃,水浸温度25℃。
[0076][0077]
表4
[0078][0079]
表5
[0080]
在本实施例中,采用附图2和附图4方法对本发明提供的含锂粘土进行处理,试验结果如下表6所示:实验组1采用机械力化学活化处理后,锂浸出率和锂综合回收率均较未采用机械力化学活化处理实验组2显著提高,同时沉锂余液中铝离子浓度没有显著变化,这说明机械力化学活化处理的引入有助于提高硫酸盐和锂原料反应效率,且不会对锂综合回收率带来不利影响。
[0081][0082]
表6
[0083]
实施例3
[0084]
某贵州含锂粘土含氧化锂(贾达尔锂硼矿,氧化锂含量0.45%,含氧化铝量 19%,氟含量1.5%,铝物相铝矾土),采用图2所示的工艺流程,具体参数如下表7所示,酸化处理选用柠檬酸,固铝试剂选用氧化钙,氢氧化钠和双氧水用量均为3g/l,浸出液选用质量分数25%稀硫酸,采用相同工艺处理四川某锂辉石浸出渣(氧化锂含量0.5%,含氧化铝量27%,氟含量0.5%,铝物相铝硅酸盐)、宜春某铁锂云母(氧化锂含量2.5%,含氧化铝量31%,氟含量3.5%,铝物相铁锂云母)作为对照:
[0085][0086]
表7
[0087]
在本实施例中,采用本发明提供的上述锂矿含锂粘土提纯锂的方法对锂辉石浸出渣、铁锂云母、含锂粘土进行处理,试验结果如下表8所示:
[0088][0089]
表8
[0090]
由上可知,本发明提供的上述含锂粘土提纯锂的方法处理含锂粘土,含锂粘土锂浸出率》90%,沉锂余液铝离子浓度《1g/l,锂综合回收率》84%,氟挥发率≦6%,含锂粘土中锂资源得到有效回收,氟元素挥发得到有效抑制。
[0091]
实施例4
[0092]
某云南含锂粘土含氧化锂(氧化锂含量0.54%,含氧化铝量25%,氟含量2.1%,铝物相铝矾土、云母)(碳酸盐黏土型锂矿),采用图2所示的工艺流程,酸化处理选用草酸,氢氧化钠和双氧水用量均为5g/l,浸出液选用质量分数50%稀硫酸,固铝试剂选用氢氧化钙,具体参数如下表9所示,采用相同工艺处理九江某铁锂云母浸出渣(氧化锂含量0.48%,含氧化铝量25%,氟含量3.5%,铝物相铝硅酸盐)、非洲某磷锂铝石(氧化锂含量4.5%,含氧化铝量24%,氟含量0.8%,铝物相磷锂铝石)作为对照,具体结果如下表10所示:
[0093][0094]
表9
[0095]
在本实施例中,采用本发明提供的上述锂矿含锂粘土提纯锂的方法对锂云母含锂粘土进行处理,试验结果如下表6所示:
[0096][0097]
表10
[0098]
由上可知,本发明提供的上述含锂粘土提纯锂的方法处理含锂粘土,含锂粘土锂浸出率》90%,沉锂余液铝离子浓度《1g/l,锂综合回收率》84%,氟挥发率≦5%,含锂粘土中锂资源得到有效回收,氟元素挥发得到有效抑制。
[0099]
实施例5
[0100]
某含锂粘土(贾达尔锂硼矿)含氧化锂0.3%,采用图2所示的工艺流程,酸化处理选用质量分数95%浓硫酸,氢氧化钠和双氧水用量为10g/l,浸出液选用水,具体参数如下表11所示:
[0101][0102]
表11
[0103]
在本实施例中,采用本发明提供的上述锂矿含锂粘土提纯锂的方法对透锂长石含锂粘土进行处理,试验结果如下表12所示:
[0104][0105]
表12
[0106]
由上可知,本发明提供的上述含锂粘土提纯锂的方法处理含锂粘土,含锂粘土锂浸出率》90%,沉锂余液铝离子浓度《1g/l,锂综合回收率》70%,含锂粘土中锂资源得到有效回收。
[0107]
最后说明的是,以上优选实施例仅用以说明本发明的技术方案而非限制,尽管通过上述优选实施例已经对本发明进行了详细的描述,但本领域技术人员应当理解,可以在形式上和细节上对其作出各种各样的改变,而不偏离本发明权利要求书所限定的范围。
再多了解一些
本文用于企业家、创业者技术爱好者查询,结果仅供参考。