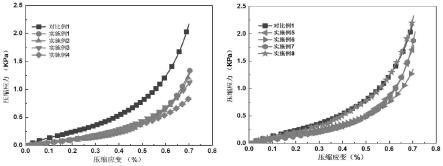
1.本发明属于复合材料及保温降噪材料交叉技术领域,具体涉及一种轻质聚酰亚胺复合海绵及其制备方法。
背景技术:
2.聚酰亚胺泡沫、气凝胶等多孔材料具有高的孔隙率和优异的隔热与吸音特性,是实现轨道交通、航天航海领域运载装备向大型化、轻量化发展的重要基础材料。然而,现有聚酰亚胺海绵的制备方法主要包含溶剂缩聚发泡和冷冻干燥两类。其中,以“一步法”和“两步法”为主的溶剂缩聚发泡因其工艺成熟、产品性能稳定,是聚酰亚胺海绵的主流制备方法。为了进一步赋予聚酰亚胺海绵更多特殊性能,拓展聚酰亚胺海绵在特殊领域应用并满足性能需求,常将无机材料与聚酰亚胺进行复合,利用无机材料自身优势弥补聚酰亚胺性能缺陷,实现材料性能提升与拓展的目的。然而,在溶剂缩聚发泡制备聚酰亚胺海绵海绵过程中,无机材料表面较少的化学基团使其在复合过程中结合较差,对复合海绵材料强度有不利影响,同时,无机材料在缩聚发泡过程中存在分散难且分布不均等问题。因此,选用不同形貌无机材料、表面改性、冷冻干燥和添加增强组分,是改善无机材料结合弱、分散难的有效手段。通过将无机微粒分散后与聚酰亚胺前驱体混合,经冷冻干燥与热亚胺化处理可得到均匀的无机/有机聚酰亚胺复合海绵,解决了传统缩聚发泡法中无机材料分散难、结合弱的问题,使得冷冻干燥在无机/有机聚酰亚胺复合海绵制备方面表现出更大优势。然而,冷冻干燥法制备无机/有机聚酰亚胺海绵存在样品尺寸受限、制备时间长和能耗过大的问题。
技术实现要素:
3.为了克服上述现有技术的缺点,本发明的目的在于提供一种轻质聚酰亚胺复合海绵及其制备方法,用以解决了现有聚酰亚胺有机/无机复合材料制备过程中,无机材料分散难、结合弱及制备效率低等问题,为轻质聚酰亚胺隔热吸音材料的高效制备、性能调控及进一步发展应用,提供了新的方法与可能性。
4.为了达到上述目的,本发明采用以下技术方案予以实现:
5.本发明公开了一种轻质聚酰亚胺复合海绵的制备方法,包括以下步骤:
6.s1:将聚酰亚胺纤维放置在十二烷基苯磺酸钠溶液中加热,随后进行洗涤、干燥处理,得到已处理的聚酰亚胺纤维;将芳纶纤维进行疏解分散、浓缩,得到芳纶纤维浆料;
7.s2:将芳纶短切浆料、氢氧化钾和二甲基亚砜混合,进行去质子化反应和原位还原反应,得到芳纶纳米纤维;将芳纶纳米纤维洗涤后,得到芳纶纳米纤维分散液;
8.s3:将无机多孔粉体分散液和s2中得到的芳纶纳米纤维分散液进行混合,得到纳米纤维/粉体分散液;
9.s4:将已处理的聚酰亚胺纤维和芳纶纤维浆料置于发泡容器中进行混合,得到混合溶液,随后再向混合溶液中加入去离子水与表面活性剂,得到混合纤维浆料a;并在搅拌
的过程中,向混合纤维浆料a中加入s3中得到的纳米纤维/粉体分散液,发泡后得到泡沫纤维浆料b;
10.s5:将泡沫纤维浆料b进行滤水成形、干燥后,得到一种良好隔热吸音特性的轻质聚酰亚胺复合海绵。
11.进一步地,s1中,所述聚酰亚胺纤维和十二烷基苯磺酸钠溶液的用量比为(20~50)g:(3~5)l;所述十二烷基苯磺酸钠溶液的浓度为1.2
×
10-3
mol/l~1.5
×
10-3
mol/l;所述芳纶纤维包括芳纶沉析纤维或芳纶浆粕纤维;所述芳纶纤维浆料的固含量为5%~15%;所述加热的温度为70℃~90℃,洗涤的时间为20min~30min。
12.进一步地,s2中,所述芳纶短切纤维、氢氧化钾和二甲基亚砜的用量比为(2~5)g:1g:(250~500)ml;所述芳纶纳米纤维分散液的固含量为1%~5%。
13.进一步地,s3中,所述无机多孔粉体分散液是由无机多孔粉体和水按照(1:200)~(4:200)的质量比混合后,通过超声分散处理得到的;所述超声分散处理的工艺参数为:超声处理的功率为800w~1200w,超声处理的时间为15min~30min;所述无机多孔粉体为二氧化硅气凝胶、多孔硅酸钙和活性炭中的一种。
14.进一步地,s3中,所述纳米纤维/粉体分散液的固含量为0.75%~3%,所述纳米纤维/粉体分散液中的纳米纤维绝干质量与无机粉体的质量比为(1:0.25)~(1:1)。
15.进一步地,s4中,所述已处理的聚酰亚胺纤维和芳纶纤维浆料的质量比为3:1;所述搅拌的时间为10min~30min,搅拌的转速为4000rpm~6000rpm。
16.进一步地,所述表面活性剂为十二烷基硫酸钠,所述混合纤维浆料a中表面活性剂的浓度为0.3g/l~2.5g/l。
17.进一步地,s4中,加入去离子水后,混合纤维浆料a的质量浓度为1%~5%。
18.进一步地,s5中,所述干燥的温度为105℃~120℃,所述干燥的时间为120min~180min。
19.本发明还公开了采用上述制备方法制备得到的轻质聚酰亚胺复合海绵,所述轻质聚酰亚胺复合海绵的密度为10mg/cm3~15mg/cm3,导热系数为0.031w/(m
·
k)~0.035w/(m
·
k),降噪系数为0.41~0.53。
20.与现有技术相比,本发明具有以下有益效果:
21.本发明公开了一种轻质聚酰亚胺复合海绵的制备方法,本发明通过引入芳纶纤维,增强了纤维间界面结合能力,实现了与多孔粉体的吸附与结合,提高了制备过程中无机材料分散再系统中的分散程度和结合强度;同时,采用的多孔粉体自身的多孔结构与大的比表面积可作为热量与声波传递过程中的有效屏障,进而提升纤维多孔材料内部界面热阻并削弱了声波的传输与穿透,显著提升轻质聚酰亚胺复合海绵的隔热吸音性能,通过设计多尺度结构与功能粉体增强相结合,实现了轻质复合海绵内部结构与性能调控,解决了现有聚酰亚胺有机/无机复合材料制备过程中,无机材料分散难、结合弱及制备效率低等问题,为轻质聚酰亚胺隔热吸音材料的高效制备、性能调控及进一步发展应用,提供了新的方法与可能性。本发明公开的方法,在聚酰亚胺轻质多孔材料高效、绿色、可回收制备方面的成功,对材料的进一步可持续发展具有重要意义。
22.本发明还公开了采用上述制备方法制备得到的轻质聚酰亚胺复合海绵,通过相关实验证明,本发明公开的轻质聚酰亚胺复合海绵密度低且具有泡沫多孔材料绝热防护、吸
声降噪、阻尼减振等功能,可实现船舶、航空、航天等领域大型装备结构减重与节能降噪。另外,密度与导热系数相接近,吸音性能较优,
附图说明
23.图1为本发明制备得到的轻质聚酰亚胺复合海绵的制备流程示意图;
24.图2为本发明所用的层状多孔硅酸钙的扫描电镜图;
25.图3为本发明制备得到的轻质聚酰亚胺复合海绵的隔热吸音机理示意;
26.图4为不同实施例制备得到的复合海绵的力学性能对比示意图;
27.图5为不同实施例制备得到的复合海绵的吸音性能对比示意图;
28.图6为不同实施例制备得到的复合海绵的隔热性能对比示意图
具体实施方式
29.为使本领域技术人员可了解本发明的特点及效果,以下谨就说明书及权利要求书中提及的术语及用语进行一般性的说明及定义。除非另有指明,否则文中使用的所有技术及科学上的字词,均为本领域技术人员对于本发明所了解的通常意义,当有冲突情形时,应以本说明书的定义为准。
30.本文描述和公开的理论或机制,无论是对或错,均不应以任何方式限制本发明的范围,即本发明内容可以在不为任何特定的理论或机制所限制的情况下实施。
31.本文中,所有以数值范围或百分比范围形式界定的特征如数值、数量、含量与浓度仅是为了简洁及方便。据此,数值范围或百分比范围的描述应视为已涵盖且具体公开所有可能的次级范围及范围内的个别数值(包括整数与分数)。
32.本文中,若无特别说明,“包含”、“包括”、“含有”、“具有”或类似用语涵盖了“由
……
组成”和“主要由
……
组成”的意思,例如“a包含a”涵盖了“a包含a和其他”和“a仅包含a”的意思。
33.本文中,为使描述简洁,未对各个实施方案或实施例中的各个技术特征的所有可能的组合都进行描述。因此,只要这些技术特征的组合不存在矛盾,各个实施方案或实施例中的各个技术特征可以进行任意的组合,所有可能的组合都应当认为是本说明书记载的范围。
34.下面结合具体实施例,进一步阐述本发明。应理解,这些实施例仅用于说明本发明而不用于限制本发明的范围。此外应理解,在阅读了本发明讲授的内容之后,本领域技术人员可以对本发明作各种改动或修改,这些等价形式同样落于本技术所附权利要求书所限定的范围。
35.下列实施例中使用本领域常规的仪器设备。下列实施例中未注明具体条件的实验方法,通常按照常规条件,或按照制造厂商所建议的条件。下列实施例中使用各种原料,除非另作说明,都使用常规市售产品,其规格为本领域常规规格。在本发明的说明书以及下述实施例中,如没有特别说明,“%”都表示重量百分比,“份”都表示重量份,比例都表示重量比。
36.本发明公开的一种良好隔热吸音特性的轻质聚酰亚胺复合海绵的制备方法,通过引入芳纶纳米纤维与多孔粉体,实现纤维间界面结合增强与多孔粉体的吸附与结合;同时,
多孔粉体(二氧化硅气凝胶、层状多孔硅酸钙)自身的特殊多孔结构与大的比表面积可作为热量与声波传递过程中的有效屏障,进而提升纤维多孔材料内部界面热阻并削弱了声波的传输与穿透,显著提升轻质聚酰亚胺复合海绵的隔热吸音性能。
37.本发明通过设计多尺度结构与功能粉体增强相结合,实现了轻质复合海绵内部结构与性能调控,解决了现有聚酰亚胺有机/无机复合材料制备过程中,无机材料分散难、结合弱及制备效率低等问题,为轻质聚酰亚胺隔热吸音材料的高效制备、性能调控及进一步发展应用,提供了新的方法与可能性。
38.图1为本发明制备得到轻质聚酰亚胺复合海绵的制备流程示意图,包括以下步骤:
39.步骤1:首先将聚酰亚胺纤维经十二烷基苯磺酸钠溶液加热洗涤处理,干燥后得到已处理的聚酰亚胺纤维;将芳纶纤维进行疏解分散、浓缩,得到芳纶纤维浆料;
40.步骤2:将步骤1中得到的芳纶纤维浆料、氢氧化钾和二甲基亚砜按一定质量比混合,经去质子化过程与原位还原过程获得芳纶纳米纤维,洗涤后得到芳纶纳米纤维分散液;
41.步骤3:将无机多孔粉体和水通过超声分散处理进行混合,配置成一定固含量的无机多孔粉体分散液,并和步骤2中得到的芳纶纳米纤维分散液进行混合,得到一定固含量的纳米纤维/粉体分散液;
42.步骤4:将步骤1中得到的已处理的聚酰亚胺纤维、芳纶纤维浆料置于发泡容器中进行混合,得到混合溶液,随后再向混合溶液中加入去离子水与表面活性剂,得到混合纤维浆料a;对混合纤维浆料a进行搅拌,并在搅拌的过程中,向混合纤维浆料a中加入步骤3中得到的纳米纤维/粉体分散液,得到泡沫纤维浆料b;
43.步骤5:将步骤4得到的泡沫纤维浆料b转移到滤水成形容器中,并干燥后,得到一种轻质聚酰亚胺复合海绵。
44.实施例1
45.一种轻质聚酰亚胺复合海绵的制备方法,包括以下步骤:
46.s1:将50g聚酰亚胺纤维放置在5l浓度为1.5
×
10-3
mol/l的十二烷基苯磺酸钠溶液中在70℃下加热,随后进行洗涤25min、干燥处理,得到已处理的聚酰亚胺纤维;将芳纶纤维进行疏解分散、浓缩,得到固含量为5%芳纶纤维浆料;
47.s2:将1.0g芳纶短切纤维、0.5g氢氧化钾和500ml二甲基亚砜混合,经去质子化过程与原位还原过程获得芳纶纳米纤维,洗涤后得到固含量为1%的芳纶纳米纤维分散液;
48.s3:将二氧化硅气凝胶配置成固含量为0.5%的二氧化硅气凝胶分散液并在1000w条件下超声分散25min,随后将二氧化硅气凝胶分散液和s2中得到的芳纶纳米纤维分散液混合,得到固含量为0.75%的纳米纤维/二氧化硅气凝胶分散液;
49.s4:将s1中得到的3g已处理的聚酰亚胺纤维和1g固含量为5%的芳纶纤维浆料置于发泡容器中进行混合,得到混合溶液,随后向混合溶液中加入0.12g十二烷基硫酸钠(sds)和去离子水,得到质量分数为2%的混合纤维浆料a;在混合纤维浆料a的搅拌过程中加入s3中得到的纳米纤维/粉体分散液,并在4000rpm持续搅拌条件下发泡20min得到泡沫纤维浆料b;
50.s5:将泡沫纤维浆料b进行滤水成形,随后在105℃下干燥120min后,得到一种轻质聚酰亚胺复合海绵。
51.利用多功能材料试验机、热常数分析仪及阻抗管对本实施所制得的轻质聚酰亚胺
复合海绵,检测结果见图2与表1。
52.实施例2
53.s1:将40g聚酰亚胺纤维放置在5l浓度为1.3
×
10-3
mol/l的十二烷基苯磺酸钠溶液中在80℃下加热,随后进行洗涤30min、干燥处理,得到已处理的聚酰亚胺纤维;将芳纶纤维进行疏解分散、浓缩,得到固含量为10%芳纶纤维浆料;
54.s2:将1.0g芳纶短切纤维、0.5g氢氧化钾和500ml二甲基亚砜混合,经去质子化过程与原位还原过程获得芳纶纳米纤维,洗涤后得到固含量为2%的芳纶纳米纤维分散液;
55.s3:将二氧化硅气凝胶配置成固含量为1%的二氧化硅气凝胶分散液并在1200w条件下超声分散20min,随后将二氧化硅气凝胶分散液和s2中得到的芳纶纳米纤维分散液混合,得到固含量为1.25%的纳米纤维/二氧化硅气凝胶分散液;
56.s4:将s1中得到的3g已处理的聚酰亚胺纤维和1g固含量为的10%芳纶纤维浆料置于发泡容器中进行混合,得到混合溶液,随后向混合溶液中加入0.06g十二烷基硫酸钠(sds)和去离子水,得到质量分数为3%的混合纤维浆料a;在混合纤维浆料a的搅拌过程中加入s3中得到的纳米纤维/粉体分散液,并在6000rpm持续搅拌条件下发泡20min得到泡沫纤维浆料b;
57.s5:将泡沫纤维浆料b进行滤水成形,随后在120℃下干燥180min后,得到一种轻质聚酰亚胺复合海绵。
58.利用多功能材料试验机、热常数分析仪及阻抗管对本实施所制得的轻质聚酰亚胺复合海绵,检测结果见图2与表1。
59.实施例3
60.s1:将30g聚酰亚胺纤维放置在3l浓度为1.4
×
10-3
mol/l的十二烷基苯磺酸钠溶液中在70℃下加热,随后进行洗涤30min、干燥处理,得到已处理的聚酰亚胺纤维;将芳纶纤维进行疏解分散、浓缩,得到固含量为15%芳纶纤维浆料;
61.s2:将1.0g芳纶短切纤维、0.5g氢氧化钾和500ml二甲基亚砜混合,经去质子化过程与原位还原过程获得芳纶纳米纤维,洗涤后得到固含量为3%的芳纶纳米纤维分散液;
62.s3:将二氧化硅气凝胶配置成固含量为1.5%的二氧化硅气凝胶分散液并在800w条件下超声分散30min,随后将二氧化硅气凝胶分散液和s2中得到的芳纶纳米纤维分散液混合,得到固含量为1.75%的纳米纤维/二氧化硅气凝胶分散液;
63.s4:将s1中得到的3g已处理的聚酰亚胺纤维和1g固含量为的15%芳纶纤维浆料置于发泡容器中进行混合,得到混合溶液,随后向混合溶液中加入0.24g十二烷基硫酸钠(sds)和去离子水,得到质量分数为4%的混合纤维浆料a;在混合纤维浆料a的搅拌过程中加入s3中得到的纳米纤维/粉体分散液,并在4000rpm持续搅拌条件下发泡20min得到泡沫纤维浆料b;
64.s5:将泡沫纤维浆料b进行滤水成形,随后在110℃下干燥150min后,得到一种轻质聚酰亚胺复合海绵。
65.利用多功能材料试验机、热常数分析仪及阻抗管对本实施所制得的轻质聚酰亚胺复合海绵,检测结果见图2与表1。
66.实施例4
67.s1:将20g聚酰亚胺纤维放置在3l浓度为1.5
×
10-3
mol/l的十二烷基苯磺酸钠溶液
在90℃下加热,随后进行洗涤30min、干燥处理,得到已处理的聚酰亚胺纤维;将芳纶纤维进行疏解分散、浓缩,得到固含量为20%芳纶纤维浆料;
68.s2:将1.0g芳纶短切纤维、0.5g氢氧化钾和500ml二甲基亚砜混合,经去质子化过程与原位还原过程获得芳纶纳米纤维,洗涤后得到固含量为4%的芳纶纳米纤维分散液;
69.s3:将二氧化硅气凝胶配置成固含量为2%的二氧化硅气凝胶分散液并在1200w条件下超声分散20min,随后将二氧化硅气凝胶分散液和s2中得到的芳纶纳米纤维分散液混合,得到固含量为2.5%的纳米纤维/二氧化硅气凝胶分散液;
70.s4:将s1中得到的3g已处理的聚酰亚胺纤维和1g固含量为的20%芳纶纤维浆料置于发泡容器中进行混合,得到混合溶液,随后向混合溶液中加入0.12g十二烷基硫酸钠(sds)和去离子水,得到质量分数为5%的混合纤维浆料a;在混合纤维浆料a的搅拌过程中加入s3中得到的纳米纤维/粉体分散液,并在6000rpm持续搅拌条件下发泡25min得到泡沫纤维浆料b;
71.s5:将泡沫纤维浆料b进行滤水成形,随后在120℃下干燥140min后,得到一种轻质聚酰亚胺复合海绵。
72.利用多功能材料试验机、热常数分析仪及阻抗管对本实施所制得的轻质聚酰亚胺复合海绵,检测结果见图2与表1。
73.实施例5
74.s1:将50g聚酰亚胺纤维放置在5l浓度为1.5
×
10-3
mol/l的十二烷基苯磺酸钠溶液中在80℃下加热,随后进行洗涤30min、干燥处理,得到已处理的聚酰亚胺纤维;将芳纶纤维进行疏解分散、浓缩,得到固含量为5%芳纶纤维浆料;
75.s2:将1.0g芳纶短切纤维、0.5g氢氧化钾和500ml二甲基亚砜混合,经去质子化过程与原位还原过程获得芳纶纳米纤维,洗涤后得到固含量为1%的芳纶纳米纤维分散液;
76.s3:将多孔硅酸钙配置成固含量为0.5%的硅酸钙分散液并在1000w条件下超声分散25min,随后将硅酸钙分散液和s2中得到的芳纶纳米纤维分散液混合,得到固含量为0.75%的纳米纤维/硅酸钙分散液;
77.s4:将s1中得到的3g已处理的聚酰亚胺纤维和1g固含量为的5%芳纶纤维浆料置于发泡容器中进行混合,得到混合溶液,随后向混合溶液中加入0.12g十二烷基硫酸钠(sds)和去离子水,得到质量分数为2%的混合纤维浆料a;在混合纤维浆料a的搅拌过程中加入s3中得到的纳米纤维/硅酸钙粉体分散液,并在4000rpm持续搅拌条件下发泡20min得到泡沫纤维浆料b;
78.s5:将泡沫纤维浆料b进行滤水成形,随后在105℃下干燥120min后,得到一种轻质聚酰亚胺复合海绵。
79.利用多功能材料试验机、热常数分析仪及阻抗管对本实施所制得的轻质聚酰亚胺复合海绵,检测结果见图2与表1。
80.实施例6
81.s1:将40g聚酰亚胺纤维放置在5l浓度为1.5
×
10-3
mol/l的十二烷基苯磺酸钠溶液中在80℃下加热,随后进行洗涤30min、干燥处理,得到已处理的聚酰亚胺纤维;将芳纶纤维进行疏解分散、浓缩,得到固含量为10%芳纶纤维浆料;
82.s2:将1.0g芳纶短切纤维、0.02g氢氧化钾和500ml二甲基亚砜混合,经去质子化过
程与原位还原过程获得芳纶纳米纤维,洗涤后得到固含量为2%的芳纶纳米纤维分散液;
83.s3:将多孔硅酸钙配置成固含量为1%的硅酸钙分散液并在1200w条件下超声分散20min,随后将硅酸钙分散液和s2中得到的芳纶纳米纤维分散液混合,得到固含量为1.25%的纳米纤维/硅酸钙粉体分散液;
84.s4:将s1中得到的3g已处理的聚酰亚胺纤维和1g固含量为的10%芳纶纤维浆料置于发泡容器中进行混合,得到混合溶液,随后向混合溶液中加入0.06g十二烷基硫酸钠(sds)和去离子水,得到质量分数为3%的混合纤维浆料a;在混合纤维浆料a的搅拌过程中加入s3中得到的纳米纤维/硅酸钙粉体分散液,并在6000rpm持续搅拌条件下发泡20min得到泡沫纤维浆料b;
85.s5:将泡沫纤维浆料b进行滤水成形,随后在105℃下干燥120min后,得到一种轻质聚酰亚胺复合海绵。
86.利用多功能材料试验机、热常数分析仪及阻抗管对本实施所制得的轻质聚酰亚胺复合海绵,检测结果见图2与表1。
87.实施例7
88.s1:将30g聚酰亚胺纤维放置在4l浓度为1.2
×
10-3
mol/l的十二烷基苯磺酸钠溶液中80℃下加热,随后进行洗涤30min、干燥处理,得到已处理的聚酰亚胺纤维;将芳纶纤维进行疏解分散、浓缩,得到固含量为15%芳纶纤维浆料;
89.s2:将1.0g芳纶短切纤维、0.5g氢氧化钾和500ml二甲基亚砜混合,经去质子化过程与原位还原过程获得芳纶纳米纤维,洗涤后得到固含量为3%的芳纶纳米纤维分散液;
90.s3:将多孔硅酸钙配置成固含量为1.5%的硅酸钙分散液并在800w条件下超声分散30min,随后将硅酸钙分散液和s2中得到的芳纶纳米纤维分散液混合,得到固含量为1.75%的纳米纤维/硅酸钙粉体分散液;
91.s4:将s1中得到的3g已处理的聚酰亚胺纤维和1g固含量为的15%芳纶纤维浆料置于发泡容器中进行混合,得到混合溶液,随后向混合溶液中加入0.24g十二烷基硫酸钠(sds)和去离子水,得到质量分数为4%的混合纤维浆料a;在混合纤维浆料a的搅拌过程中加入s3中得到的纳米纤维/硅酸钙粉体分散液,并在4000rpm持续搅拌条件下发泡20min得到泡沫纤维浆料b;
92.s5:将泡沫纤维浆料b进行滤水成形,随后在105℃下干燥180min后,得到一种轻质聚酰亚胺复合海绵。
93.利用多功能材料试验机、热常数分析仪及阻抗管对本实施所制得的轻质聚酰亚胺复合海绵,检测结果见图2与表1。
94.实施例8
95.s1:将20g聚酰亚胺纤维放置在3l浓度为1.5
×
10-3
mol/l的十二烷基苯磺酸钠溶液中在70℃下加热,随后进行洗涤20min、干燥处理,得到已处理的聚酰亚胺纤维;将芳纶纤维进行疏解分散、浓缩,得到固含量为20%芳纶纤维浆料;
96.s2:将1.0g芳纶短切纤维、0.5g氢氧化钾和500ml二甲基亚砜混合,经去质子化过程与原位还原过程获得芳纶纳米纤维,洗涤后得到固含量为4%的芳纶纳米纤维分散液;
97.s3:将多孔硅酸钙配置成固含量为2%的硅酸钙分散液并在1200w条件下超声分散20min,随后将硅酸钙分散液和s2中得到的芳纶纳米纤维分散液混合,得到固含量为2.5%
的纳米纤维/硅酸钙分散液;
98.s4:将s1中得到的3g已处理的聚酰亚胺纤维和1g固含量为的20%芳纶纤维浆料置于发泡容器中进行混合,得到混合溶液,随后向混合溶液中加入0.12g十二烷基硫酸钠(sds)和去离子水,得到质量分数为5%的混合纤维浆料a;在混合纤维浆料a的搅拌过程中加入s3中得到的纳米纤维/硅酸钙粉体分散液,并在6000rpm持续搅拌条件下发泡25min得到泡沫纤维浆料b;
99.s5:将泡沫纤维浆料b进行滤水成形,随后在150℃下干燥120min后,得到一种轻质聚酰亚胺复合海绵。
100.利用多功能材料试验机、热常数分析仪及阻抗管对本实施所制得的轻质聚酰亚胺复合海绵,检测结果见图2与表1。
101.对比例1
102.一种轻质聚酰亚胺复合海绵的制备方法,包括以下步骤:
103.s1:将50g聚酰亚胺纤维放置在5l浓度为1.5
×
10-3
mol/l的十二烷基苯磺酸钠溶液中加热,随后进行洗涤、干燥处理,得到已处理的聚酰亚胺纤维;将芳纶纤维进行疏解分散、浓缩,得到固含量为10%芳纶纤维浆料;
104.s2:将1.0g芳纶短切纤维、0.5g氢氧化钾和500ml二甲基亚砜混合,经去质子化过程与原位还原过程获得芳纶纳米纤维,洗涤后得到固含量为1%的芳纶纳米纤维分散液;
105.s3:将s1中得到的3g已处理的聚酰亚胺纤维和1g固含量为的10%芳纶纤维浆料置于发泡容器中进行混合,得到混合溶液,随后向混合溶液中加入0.06g十二烷基硫酸钠(sds)和去离子水,得到质量分数为2%的混合纤维浆料a;在混合纤维浆料a的搅拌过程中加入s2中得到的芳纶纳米纤维分散液,并在4000rpm持续搅拌条件下发泡30min得到泡沫纤维浆料b;
106.s4:将泡沫纤维浆料b进行滤水成形,随后在120℃下干燥150min后,得到一种轻质聚酰亚胺复合海绵。
107.利用多功能材料试验机、热常数分析仪及阻抗管对本实施所制得的良好隔热吸音特性的轻质聚酰亚胺复合海绵,检测结果见图2与表1。
108.表1:不同实施例制备得到的复合海绵的性能对比
[0109][0110][0111]
表1所示为不同实施例制备得到的复合海绵的性能对比,由表可以看出,本发明制
备的pi/af/anfs/粉体复合海绵与轻质pi海绵、冷冻干燥制备pi气凝胶及超临界干燥pi气凝胶相比,表现出密度与导热系数相接近,而吸音性能较优的特点;与航空用pi泡沫相比,在隔热吸音性能方面仍存在一定的差距,但与船舶用轻质pi泡沫性能需求对比发现,本发明制备的轻质聚酰亚胺复合海绵已经满足船舶用pi泡沫的性能需求,这极大的证明了本发明方法在聚酰亚胺轻质多孔材料高效、绿色、可回收制备方面的成功,对材料的进一步可持续发展具有重要意义。
[0112]
图2所示为本发明所用的层状多孔硅酸钙的扫描电镜图,可以看出,硅酸钙具有明显的多孔结构。
[0113]
图3所示为本发明制备得到的良好隔热吸音特性的轻质聚酰亚胺复合海绵的隔热吸音机理示意,由图3可以看出,本发明成功构筑了多尺度增强的轻质聚酰亚胺复合海绵,并使得z向分布的聚酰亚胺纤维承担了复合材料部分轴向压缩强度,其原因不仅与高模量的聚酰亚胺纤维在受力时表现出“韧性”有关,同时,芳纶沉析纤维对聚酰亚胺纤维结合处的包覆缠绕与芳纶纳米纤维的界面增强作用共同赋予了复合海绵良好的力学强度。同时,利用产生的水基泡沫对纤维实现分散,并塑造了丰富孔隙结构,且芳纶纳米纤维的显著增强作用与多孔粉体自身丰富的孔道结构,在引入复合海绵内部后,由于自身的增强特性与微纳米孔径与团聚作用,使得复合海绵内部孔隙率与比孔体积发生改变,比孔体积的与孔隙率的增大使得复合海绵内部固体界面增大,进而增强了固固界面和气固界面的声子反射与散射,同时,多孔粉体孔壁与空气的摩擦作用,进一步削弱了热量的传递并提升了复合海绵的隔热性能。此外,由于多孔粉体自身特殊的层状多孔结构,使得声波在传播过程中,多次受到复合海绵内部纤维界面、多孔粉体界面及粉体孔径的摩擦与碰撞,声波能量部分转化为内能,多次的反射、折射与阻尼振动作用使得声波振动被削弱,大幅削弱了材料中的声波穿透,保证了复合海绵良好的吸音性能。
[0114]
图4所示为不同实施例制备得到的复合海绵的力学性能对比示意图,由图中可以看到,加入二氧化硅气凝胶后,复合海绵的压缩强度均呈现下降趋势。这是由于制备过程中水基泡沫对纤维产生分隔与分散作用,使得纤维及二氧化硅气凝胶在泡沫悬浮体系中实现良好的分散,同时,二氧化硅气凝胶干燥后“团聚”,且团聚体主要分布在纤维表面、纤维骨架与纤维界面结合处,使得加入的二氧化硅气凝胶对纤维间界面结合产生了一定的破坏作用,随着多孔粉体用量增多,对纤维间界面结合程度破坏越大,进一步证实了复合海绵压缩强度变化趋势。而复合海绵的压缩强度随着多孔硅酸钙用量增多而增大,这可能是由于芳纶纳米纤维及芳纶沉析纤维与硅酸钙产生化学结合作用,保证了硅酸钙均匀分布在复合海绵内部,且芳纶纳米纤维通过成膜作用对固固界面结合处进行加固,使得芳纶沉析纤维与多孔硅酸钙强有力的结合在一起,当硅酸钙用量逐渐增多,复合海绵受到外力被压缩时,纤维与硅酸钙共同承担应力载荷,使得可承受的压应力载荷逐渐增大。
[0115]
图5所示为不同实施例制备得到的复合海绵的吸音性能对比示意图,由图中可以看到,添加二氧化硅气凝胶后,复合海绵的吸音系数整体呈下降趋势,但在1400~2000hz的频率范围内,二氧化硅气凝胶对其吸音性能影响略微提升。添加二氧化硅气凝胶对复合海绵吸音系数影响较小,原因可能与其在海绵内部的形态与分布有关,二氧化硅气凝胶干燥后主要团聚在纤维表面并沉积在纤维骨架结合处,团聚体的形貌与分布不利于声波的多次反射与折射,故对音波的吸收性能影响较小。而随着硅酸钙用量的增多,复合海绵吸音系数
在中低频范围逐渐增大,在高频范围减小,这可能与硅酸钙自身结构有关,层状的多孔结构使得声波在穿透材料内部时,产生多次反射与折射,使得声波在多孔结构内部与空气分子剧烈摩擦并转化为热能,削弱了声波的穿透进而提升复合海绵的吸音系数,且在1300~2800hz的中低频范围内,添加硅酸钙的复合海绵表现出良好的吸音性能。从二氧化硅气凝胶和硅酸钙对复合材料nrc影响图中可以看出,随着二氧化硅气凝胶用量增大,其对复合材料在工程应用中的nrc改善效果较小,而硅酸钙用量增大复合材料nrc效果提升较为明显,当硅酸钙用量为24%时,nrc由0.41增大到0.53,可作为轻质、高效的吸音材料应用于减重吸音材料领域。
[0116]
图6所示为不同实施例制备得到的复合海绵的隔热性能对比示意图,由图中可以看到,未添加多孔粉体的复合海绵导热系数为0.0349w/(m
·
k),添加二氧化硅气凝胶复合海绵的隔热性能优于添加硅酸钙复合海绵隔热性能。添加6%二氧化硅气凝胶和6%硅酸钙后,复合海绵的导热系数分别下降至0.0304w/(m
·
k)和0.0328w/(m
·
k)。这可能与多孔粉体在复合海绵中的分布有特点及内部结构有关,在芳纶纳米纤维的增强改善作用及多孔粉体自身的孔径结构协同作用下,多孔材料内部界面增多,增加了固固界面和气固界面的声子反射与声子散射,致使界面热阻上升。同时,添加的多孔粉体孔壁与空气分子发生摩擦,通过摩擦作用降低空气热分子的动能,这两种效应协同作用,进一步削弱了固体传热,使得二氧化硅气凝胶复合海绵导热系数下降。随着多孔粉体用量增大,其导热系数也逐渐增大,这是由于复合海绵比孔体积均逐渐减小,即复合海绵部内部实际的固相物质在逐渐增多,此时,界面热阻效应远小于固相热传导对热量传递过程中的贡献,因此,复合海绵的导热系数随多孔粉体用量的增大而逐渐增大。
[0117]
以上内容仅为说明本发明的技术思想,不能以此限定本发明的保护范围,凡是按照本发明提出的技术思想,在技术方案基础上所做的任何改动,均落入本发明权利要求书的保护范围之内。
再多了解一些
本文用于企业家、创业者技术爱好者查询,结果仅供参考。