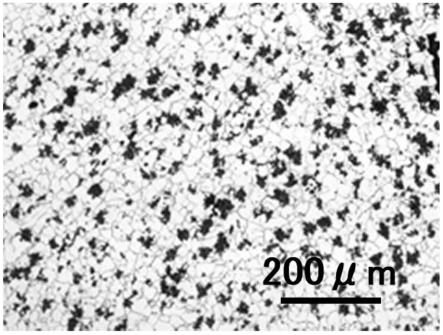
1.本发明涉及黑心可锻铸铁及其制造方法。
背景技术:
2.作为铁系材料的总称表示的铸铁可以根据碳的存在形态分类为片状石墨铸铁、球墨铸铁和可锻铸铁等。可锻铸铁可以进一步分类为白心可锻铸铁、黑心可锻铸铁和珠光体可锻铸铁等。
3.本发明的黑心可锻铸铁也被称为展性铸铁,具有石墨分散存在于由铁素体构成的基质中的形态。黑心可锻铸铁与片状石墨铸铁相比机械强度优异,由于基质为铁素体,因此韧性也优异。因此,黑心可锻铸铁作为构成需要机械强度的汽车部件、管接头等的材料而被广泛使用。
4.在片状石墨铸铁和球墨铸铁中,在铸造后的冷却过程中析出片状或球状的石墨(graphite)。与此相对,在黑心可锻铸铁中,在铸造后进行冷却而得到的铸铁中的碳以作为与铁的化合物的渗碳体(fe3c)的形态存在。然后,通过将铸铁加热至720℃以上的温度并保持,从而渗碳体被分解而石墨析出。在本说明书中,以下将通过热处理使石墨析出的工序称为“石墨化”。另外,在本说明书中,将铸造后且石墨化前的制品(中间品)称为“铸铁”或“石墨化前的铸铁”,将石墨化后的材料(包括最终制品)称为“黑心可锻铸铁”。例如从提高机械强度的观点出发,黑心可锻铸铁中所含的渗碳体优选尽量少。
5.黑心可锻铸铁的制造工序中的铸铁的石墨化需要极长的时间。石墨化有将游离在奥氏体中的渗碳体在900℃以上的温度下分解的第一阶段石墨化、和在第一阶段石墨化之后实施且将珠光体中的渗碳体在720℃左右的温度下分解的第二阶段石墨化。第一阶段石墨化和第二阶段石墨化均伴有基质中的碳的扩散和石墨的析出过程,因此通常需要数小时至数十小时。该长时间的石墨化成为使黑心可锻铸铁的制造成本增大的原因。
6.为了缩短石墨化所需的时间,一直以来研究了各种方法。例如,专利文献1中记载了通过将作为促进石墨化的元素的硅的含量调整为比通常的量多,能够缩短石墨化所需的时间。专利文献2中记载了:通过在100℃~400℃的低温范围内进行至少10小时的热处理,从而与以往相比能够缩短石墨化所需的时间。
7.在本技术人在先申请的专利文献3中记载了一种黑心可锻铸铁和黑心可锻铸铁的制造方法,该黑心可锻铸铁包含铋和锰以及选自铝和氮中的至少一者,基质的结晶粒度以粒度编号计为8.0以上且10.0以下,该黑心可锻铸铁的制造方法具有将包含上述添加元素的铸铁在275℃以上且425℃以下进行预加热后进行石墨化的工序。专利文献3中记载的黑心可锻铸铁由于基质的晶粒微细,所以与现有技术相比能够大幅缩短石墨化所需的时间。另外,记载了在对石墨化前的铸铁实施预加热的情况下,与不实施预加热的情况相比,能够容易地形成晶粒微细的金属组织。现有技术文献专利文献
8.专利文献1:日本特公昭46-17421号公报专利文献2:美国专利第2227217号说明书专利文献3:国际公开第2018/180424号
技术实现要素:
发明要解决的课题
9.在上述专利文献1所记载的方法中,由于增加了促进石墨化的硅的含量,所以根据铸模的形状、刚铸造后的冷却速度和其他冷却条件,容易生成具有在铸造时及其后的冷却过程中结晶的石墨(结晶石墨)的被称为“斑点”的金属组织。铸造时生成的结晶石墨不会因之后的热处理而消失,成为使黑心可锻铸铁的机械强度降低的原因。上述专利文献2中记载的方法中,在比石墨化所需的温度低的温度下进行的热处理所需的时间长至8小时至10小时左右。因此,新进行的热处理与以往的石墨化的合计热处理时间未必变短。
10.上述的专利文献3所记载的黑心可锻铸铁的制造方法中,预加热的工序在275℃以上且425℃以下的温度下进行。另一方面,如上所述,石墨化在720℃以上的温度下进行。这样,例如在对大量的铸铁使用连续式热处理炉等情况下,存在难以在预加热之后以相同的处理速度实施温度条件与预加热大不相同的石墨化这样的课题。
11.另外,在一次处理多个铸铁的情况下,或者在处理大尺寸的铸铁的情况下,难以使预加热中的铸铁的温度均匀而在相同的温度条件下进行处理。因此,存在黑心可锻铸铁的品质有可能不稳定这样的课题。
12.本发明是鉴于上述的各课题而完成的,其目的在于提供一种即使不进行预加热也能够在短时间内完成黑心可锻铸铁的石墨化,并且在铸造时没有生成斑点的危险性,能够以少的成本进行稳定的操作的黑心可锻铸铁及其制造方法。用于解决课题的手段
13.本发明的方式1(第1实施方式)为一种黑心可锻铸铁,其具有铁素体基质和上述基质中所含的块状石墨,所述黑心可锻铸铁以质量比计含有50ppm以上且100ppm以下的硼和65ppm以上且200ppm以下的氮,上述基质的结晶粒度以通过金属组织照片与结晶粒度标准图的比较而数值化的粒度编号计为8.0以上且10.0以下。
14.根据上述第1实施方式,在含有规定量的硼和氮的情况下,与不含有规定量的硼和氮的情况相比,基质的晶粒微细化,容易形成基质的结晶粒度以粒度编号计为8.0以上且10.0以下的金属组织。
15.本发明的方式2为方式1所述的黑心可锻铸铁,以质量比计,在将硼的含量记为b(ppm)、将氮的含量记为n(ppm)时,b和n的值满足以下的数学式(1)。这样,在优选的实施方式中,在本实施方式的黑心可锻铸铁中,在将硼的含量记为b(ppm)、将氮的含量记为n(ppm)时,b和n的值满足以下的数学式(1)。在该情况下,能够有效地防止因添加过量的硼而导致机械强度、特别是伸长率降低。
16.n≥1.3b-10
ꢀꢀ
(1)
17.本发明的方式3为方式1或2所述的黑心可锻铸铁,其还包含钛,在以质量比计将钛的含量设为ti(ppm)、将硼的含量记为b(ppm)、将氮的含量记为n(ppm)时,ti、b和n的值满足以下的数学式(2)。n≥1.3b 0.3ti-10
ꢀꢀ
(2)
18.本发明的方式4为方式1~3中任一项所述的黑心可锻铸铁,其中,上述块状石墨分散存在于上述基质的晶界的位置处。
19.本发明的方式5为方式1~4中任一项所述的黑心可锻铸铁,其中,上述块状石墨的平均粒径为10微米以上且40微米以下。
20.本发明的方式6为方式1~5中任一项所述的黑心可锻铸铁,其中,每1平方毫米截面积的上述块状石墨的颗粒数为200个以上且1200个以下。
21.本发明的方式7为方式1~6中任一项所述的黑心可锻铸铁,其中,所述黑心可锻铸铁以质量比计还包含2.0%以上且3.4%以下的碳和0.5%以上且2.0%以下的硅,剩余部分为铁和不可避免的杂质。
22.本发明的方式8为方式1~7中任一项所述的黑心可锻铸铁,其中,所述黑心可锻铸铁以质量比计还包含大于0%且1.0%以下的锰。
23.本发明的方式9(第2实施方式)为一种黑心可锻铸铁的制造方法,其包括:对将原料熔解而得到的熔融金属的成分组成进行调整的工序;使用调整了成分组成的熔融金属,通过铸造而得到以质量比计含有2.0%以上且3.4%以下的碳、0.5%以上且2.0%以下的硅、50ppm以上且100ppm以下的硼、65ppm以上且200ppm以下的氮、以及作为剩余部分的铁和不可避免的杂质的铸铁的工序;以及在高于680℃的温度下使所述铸铁石墨化的工序。
24.本发明的方式10为方式9所述的黑心可锻铸铁的制造方法,其中,在使上述铸铁石墨化的工序中,在高于680℃的温度下使上述铸铁石墨化的时间合计为1小时以上且6小时以下。
25.本发明的方式11为方式9或10所述的黑心可锻铸铁的制造方法,其中,对上述熔融金属的成分组成进行调整的工序包括:在向第一熔融金属添加含氮化合物之后追加第二熔融金属的工序。
26.本发明的方式12为方式9~11中任一项所述的黑心可锻铸铁的制造方法,其中,对上述熔融金属的成分组成进行调整的工序包括:在铸造前的熔融金属中添加硼铁和氮化锰中的至少一者来调整成分组成的工序。
27.本发明的方式13为方式9~12中任一项所述的黑心可锻铸铁的制造方法,其中,上述原料中包含使用方式9~12中任一项所述的黑心可锻铸铁的制造方法制造出的铸铁或黑心可锻铸铁中的至少一者。发明效果
28.根据本实施方式的黑心可锻铸铁及其制造方法,能够不进行预加热地使基质的晶粒微细化。其结果,在石墨化的工序中由碳的扩散引起的移动距离变短,因此能够大幅缩短铸造后的热处理所需的时间。另外,黑心可锻铸铁的品质稳定,通过基质的晶粒的微细化而机械强度提高。
附图说明
29.图1是本实施方式的黑心可锻铸铁的金属组织照片的例子。图2是现有技术的黑心可锻铸铁的金属组织照片的例子。图3是本实施方式的石墨化前的铸铁的金属组织照片的例子。图4是现有技术的石墨化前的铸铁的金属组织照片的例子。
具体实施方式
30.以下,参照附图和表对用于实施本发明的方式进行详细说明。需要说明的是,在此记载的实施方式只不过是例示,用于实施本发明的方式并不限定于在此记载的方式。
31.<金属组织>对本实施方式的黑心可锻铸铁的金属组织进行说明。
32.在本发明的第一实施方式中,黑心可锻铸铁具有铁素体基质。本说明书中,“铁素体”是指铁-碳系平衡状态图中的α相。另外,在本说明书中,“基质”是指除了石墨以外的其余区域组织,是指合金中所含的相中占据合金的体积(在截面观察中为面积)的大部分的主相或母相。具体而言,例如在对试样的截面进行研磨并用显微镜观察金属组织时,在铁素体占全部组织的面积比为80%以上的情况下,可以说铁素体是占合金的大部分的主相或母相,相当于本实施方式中的基质。石墨化结束后的基质由几乎不固溶碳的铁素体构成。因此,本实施方式的黑心可锻铸铁与以往的黑心可锻铸铁同样地韧性优异。
33.本实施方式的黑心可锻铸铁具有基质中所含的块状石墨。本说明书中,“块状石墨”是指由石墨形成的析出相,是具有多个粒状石墨相互凝聚而形成块状的集合体的形态的析出相。在本实施方式中,块状石墨“包含于基质中”是指块状石墨以被铁素体基质包围的形式被包含,并不是指石墨固溶于铁素体基质中。
34.本实施方式的黑心可锻铸铁的基质的结晶粒度以通过金属组织照片与结晶粒度标准图的比较而数值化的粒度编号计为8.0以上且10.0以下。在本说明书中,“结晶粒度标准图”是指以线图表示具有各种结晶粒度的金属组织的晶界的一组附图。作为结晶粒度标准图,使用日本工业标准jis g0551(“钢-结晶粒度的显微镜试验方法”,一般财团法人日本标准协会,2013年1月21日修订)的“附录b(规定)结晶粒度的测定-结晶粒度标准图”。该日本工业标准中规定的结晶粒度的显微镜试验方法与iso标准(iso643:2019)中规定的试验方法实质上相同。这些标准对测定钢的铁素体或奥氏体的结晶粒度的显微镜试验方法进行规定,但在本发明中,将该方法比照适用于黑心可锻铸铁的铁素体基质的结晶粒度的测定。
35.在本说明书中,“粒度编号”是指使用每1平方毫米截面积的平均晶粒数m,通过以下的数学式(3)计算而得的g的值。在下述数学式(3)中,g是以2为底的幂指数。例如,在m为16的情况下,粒度编号g为1。粒度编号越小,晶体粒度越粗,反过来,粒度编号越大,晶体粒度越细。
36.m=8
×2g
ꢀꢀ
(3)
37.金属组织照片与结晶粒度标准图的比较通过如下方式进行:对表示黑心可锻铸铁的金属组织的显微镜照片和以与其相同的倍率表示的结晶粒度标准图进行对比,目视确定具有与显微镜照片所示的结晶粒度最接近的结晶粒度的结晶粒度标准图的粒度编号。在比较时,与上述标准中规定的方法不同,忽略显微镜照片中所含的块状石墨的部分,仅着眼于
铁素体基质的晶界的尺寸,进行与晶体粒度标准图的对比。在本说明书中,“金属组织照片”不限于将金属组织印刷在纸上的显微镜照片,也可以是使用设置在金属显微镜上的ccd相机得到的图像数据等。
38.在现有技术所涉及的黑心可锻铸铁中,块状石墨未必存在于基质的晶界的位置处,经常存在于远离基质的晶界的中心附近的位置、或者跨越基质的多个晶界而存在。另外,基质的结晶粒度以粒度编号计经常为7.5以下。在为这样的金属组织的情况下,碳原子在石墨化的工序中作为块状石墨析出之前,必须通过扩散而在基质中移动长距离,根据情况,必须跨越基质的多个晶粒而移动。因此,直至石墨化的工序完成为止需要数小时至数十小时这样长的时间。
39.另一方面,在本实施方式的黑心可锻铸铁中,最终产品、即石墨化完成后的基质的结晶粒度以粒度编号计为8.0以上,基质的晶粒比以往的黑心可锻铸铁微细。在具有这样的金属组织的黑心可锻铸铁的制造中,碳原子最长也可以通过扩散而移动从微细化的基质的晶粒的中心至晶界的位置处为止的长度,从而到达晶界的位置,在此作为石墨析出。
40.另外,基质的晶界处的碳原子的扩散速度比晶粒内的碳原子的扩散速度快。本实施方式的黑心可锻铸铁在该黑心可锻铸铁的制造工序中,能够经由基质的晶界高速地进行存在于基质的晶界的位置的块状石墨的析出和生长所需的碳原子的供给。这样,通过缩短基于碳原子的扩散的移动距离,并且能够将晶界用作扩散路径,从而本实施方式的黑心可锻铸铁与现有技术相比,能够大幅缩短石墨化所需的时间。
41.在基质的结晶粒度以粒度编号计为8.0以上时,直至石墨析出为止的碳原子的扩散所致的移动距离短,因此,可得到缩短石墨化时间的效果。基质的结晶粒度越细越好,粒度编号没有上限。但是,一般而言,黑心可锻铸铁中的基质的结晶粒度的粒度编号无论多大都不会超过10.0。因此,本实施方式中的黑心可锻铸铁的基质的结晶粒度以粒度编号计为8.0以上且10.0以下。上述粒度编号优选为8.5以上。
42.使用金属组织照片的实例,一边将本实施方式的黑心可锻铸铁的金属组织与现有技术进行对比一边进行说明。图1是本实施方式的黑心可锻铸铁的金属组织照片的例子。图2是现有技术的黑心可锻铸铁的金属组织照片的例子。图右下方的比例尺的长度均为200微米。在图1和图2中,浅灰色的相是铁素体基质。黑色的相为基质中所含的块状石墨。在基质中出现的线是通过蚀刻而可视化的基质的晶界。图1的基质的结晶粒度以粒度编号计为9.0,包含在本实施方式中的粒度编号的范围内。图2的基质的结晶粒度为7.0,比图1粗。在图1和图2中,块状石墨的存在量看起来没有大的差异。但是,在现有技术中,如图2所示,块状石墨聚集而形成大块。与此相对,在本实施方式中,如图1所示,块状石墨微细地分散。
43.在优选的实施方式中,本实施方式的黑心可锻铸铁中,块状石墨分散存在于基质的晶界的位置处。在本说明书中,“块状石墨存在于基质的晶界的位置处”是指,在作为最终产品的黑心可锻铸铁的金属组织中,块状石墨存在于基质的2个铁素体晶粒之间的晶界的位置、和/或存在于3个铁素体晶粒的晶界三重点的位置。块状石墨几乎不跨越基质的多个晶界而存在。块状石墨只要其大部分存在于基质的晶界的位置即可。例如,在图1所例示的金属组织照片中,优选块状石墨的总面积中的70面积%以上存在于上述基质的晶界的位置。存在于上述晶界的位置的块状石墨的比例更优选为80面积%以上,进一步优选为90面积%以上,最优选为100面积%。上述本发明的优选实施方式中允许少数的块状石墨存在于
远离基质的晶界的基质的晶粒的中心附近的位置、或者少数的块状石墨跨越基质的4个以上的晶界而存在。
44.另外,在本说明书中,“块状石墨分散存在”是指块状石墨不是偏向基质的一部分晶粒的位置而存在,而是均匀地存在于基质的多个晶粒的位置。换言之,是指在基质的大量晶粒中,在该晶粒与周围的晶粒之间的晶界的位置处存在块状石墨。在晶界的位置不存在块状石墨的晶粒是少数的。块状石墨只要存在于基质的大量晶粒中即可。在上述的本发明的优选的实施方式中,允许在少数的晶粒中不存在块状石墨,或者即使存在其位置也不是晶界而是晶粒的中心附近的位置。
45.如果在基质的晶界的位置存在析出物,则在基质与该析出物之间形成异相晶界。通常,异相晶界的晶界能比同一相之间的晶界的晶界能小。在基质小的晶粒与大的晶粒一体化而引起晶粒生长的情况下,需要晶界的移动。但是,为了使晶界远离析出物的位置而移动,必须形成代替异相晶界的新的晶界,与不存在析出物的情况相比,晶界的移动需要更多的能量。因此,晶界不移动而固定于析出物的位置,会妨碍晶粒生长。这样的效果有时被称为由析出物引起的晶界的“钉扎效应”。
46.在本实施方式的黑心可锻铸铁中,在块状石墨分散存在于基质的晶界的位置的情况下,石墨化的工序中的基质的晶粒生长由于钉扎效应而受到阻碍。该钉扎效应对几乎全部的晶粒发生。作为其结果,存在容易形成具有本实施方式的黑心可锻铸铁所固有的基质的结晶粒度的金属组织的趋势。
47.本实施方式的黑心可锻铸铁与现有技术的黑心可锻铸铁相比,存在机械强度提高的趋势。具体而言,存在拉伸强度和伸长率提高的趋势。其理由尚不明确,但认为可能与本实施方式的黑心可锻铸铁与现有技术的黑心可锻铸铁相比铁素体基质的结晶粒度细、以及块状石墨存在于基质的晶界的位置等有关。
48.在优选的实施方式中,本实施方式的黑心可锻铸铁的块状石墨的平均粒径为10微米以上且40微米以下。块状石墨的平均粒径为10微米以上时,块状石墨的数量不会变得过多,存在容易分散存在于基质的晶界的位置的趋势。块状石墨的平均粒径为40微米以下时,块状石墨的数量不会变得过少,块状石墨的生长所需的碳的扩散距离不会变得过长,因此存在容易缩短石墨化所需的时间的趋势。因此,本实施方式的黑心可锻铸铁优选块状石墨的平均粒径为10微米以上且40微米以下。块状石墨的平均粒径更优选为12.0微米以上,进一步优选为15.0微米以上,更优选为19.0微米以下,进一步优选为18.5微米以下,更进一步优选为18.0微米以下。
49.在优选的实施方式中,本实施方式的黑心可锻铸铁的每1平方毫米截面积的块状石墨的颗粒数为200个以上且1200个以下。本实施方式的黑心可锻铸铁中最终包含的石墨的体积大致恒定,因此块状石墨的平均粒径越大则颗粒数越少,平均粒径越小则颗粒数越多。块状石墨的颗粒数为200个以上时,块状石墨的生长所需的碳的扩散距离变短,存在容易缩短石墨化所需的时间的趋势。块状石墨的颗粒数越多越好,颗粒数没有上限。但是,在本发明的优选实施方式中,能够形成的每1平方毫米截面积的块状石墨的颗粒数无论如何也不超过1200个。因此,每1平方毫米截面积的块状石墨的颗粒数优选为200个以上且1200个以下。每1平方毫米截面积的块状石墨的颗粒数更优选为300个以上,进一步优选为500个以上,并且可以为1000个以下。
50.本实施方式中的“块状石墨的平均粒径”和“每1平方毫米截面积的颗粒数”均基于在黑心可锻铸铁的任意切断面中观察到的金属组织来确定。更具体而言,如后述的实施例中记载的那样,使用与表示粒度编号的确定中使用的黑心可锻铸铁的金属组织的显微镜照片相同的显微镜照片,使用扫描仪或ccd相机等将显微镜照片的图像数据化,通过计算机图像解析进行测定而确定。
51.需要说明的是,应留意在与本实施方式的黑心可锻铸铁相关的上述说明中叙述的粒度编号、平均结晶粒径以及颗粒数均是对石墨化的工序完成后的黑心可锻铸铁的金属组织测定的数值。本实施方式中的晶粒生长的抑制、石墨化所需的时间的缩短等作用、效果主要在石墨化的工序进行的中途阶段显现。但是,难以对这样的工序的中途阶段的金属组织进行数值评价。因此,为了方便,用石墨化的工序结束后的金属组织中的数值代替。
52.<黑心可锻铸铁的成分组成>对本实施方式的黑心可锻铸铁的合金组成(成分组成)进行说明。本说明书中,各元素的含量全部以质量比表示。符号“ppm(百万分率)”是指带有该符号的数值以百万分率表示的质量比。符号“%(百分比)”是指带有该符号的数值为以百分率表示的质量比。
53.在优选的实施方式中,本实施方式的黑心可锻铸铁含有2.0%以上且3.4%以下的碳。在碳的含量为2.0%以上时,在黑心可锻铸铁的制造工序中用于铸造的熔融金属的熔点为1400℃以下,因此不需要为了制造熔融金属而将原料加热至高温,存在不需要大规模的熔解设备的趋势。与此同时,熔融金属的粘度也变低,因此熔融金属变得容易流动,存在能够容易地向铸造用铸模浇注熔融金属的趋势。碳的含量为3.4%以下时,有在铸造时及之后的冷却过程中不易生成斑点的趋势。因此,碳的含量优选设定为2.0%以上且3.4%以下。更优选的碳的含量为2.5%以上且3.2%以下。
54.在优选的实施方式中,本实施方式的黑心可锻铸铁含有0.5%以上且2.0%以下的硅。硅的含量为0.5%以上时,可以得到由硅带来的促进石墨化的效果,存在容易在短时间内完成石墨化的趋势。硅的含量为2.0%以下时,由硅带来的石墨化的促进效果不会变得过剩,存在在铸造时及其后的冷却过程中不易生成斑点的趋势。因此,硅的含量优选设为0.5%以上且2.0%以下。更优选的硅的含量为1.0%以上且1.7%以下。
55.本实施方式的黑心可锻铸铁以质量比计含有50ppm以上且100ppm以下的硼以及65ppm以上且200ppm以下的氮。通过同时含有硼和氮,能够使铁素体基质的晶粒微细化。硼的含量为50ppm以上时,在氮的存在下容易发生晶粒的微细化。硼的含量越多,晶粒越微细化。硼的含量优选为60ppm以上。在硼的含量为100ppm以下时,能够防止黑心可锻铸铁的强度及伸长率的降低。硼的含量优选为90ppm以下。
56.氮的含量为65ppm以上时,在硼的存在下容易发生晶粒的微细化。氮的含量优选为80ppm以上。氮的含量为200ppm以下时,石墨化不易受到阻碍。氮的含量优选为170ppm以下。在现有技术中,可溶性氮的增加显著阻碍第一阶段石墨化和第二阶段石墨化的进行。在本实施方式中,相反地,通过将氮与硼一起作为必须含有元素,从而实现了石墨化的时间缩短。
57.在本实施方式中,作为通过同时含有硼和氮而使铁素体基质的晶粒变得微细的理由,可以考虑以下的机理。需要说明的是,以下的机理是本发明人基于所得到的实验结果推测出的,并不限定本发明的技术范围。
58.如果铸铁被加热至800℃至900℃的温度,则固溶于铸铁的硼和氮结合而形成氮化硼。在此形成的氮化硼被认为是在常压下稳定的六方晶系的氮化硼(h-bn)。六方晶系的氮化硼具有与石墨类似的晶体结构。因此,认为在石墨化时该氮化硼成为核,存在大量石墨微细地析出的趋势。如上述的金属组织的说明时所述,如果石墨析出、生长而成为块状石墨,则由于钉扎效应而妨碍基质的晶粒生长。其结果,认为容易形成具有本实施方式的黑心可锻铸铁所固有的基质的结晶粒度的金属组织。
59.硼的含量有可能对石墨化前的铸铁的金属组织也造成影响。接下来对此进行说明。在本实施方式的石墨化前的铸铁的金属组织中,发现了现有技术的铸铁的金属组织所没有的特征。图3是本实施方式的石墨化前的铸铁的金属组织照片的例子。硼的含量为68ppm。图4是现有技术的石墨化前的铸铁的金属组织照片。硼的含量为27ppm。氮的含量在任一铸铁中均为110ppm。图3和图4中的黑色部分表示在铸造的过程中作为初晶析出的奥氏体(γ铁)在之后的冷却过程中相变为珠光体而得到的相。浅灰色的部分是作为奥氏体与渗碳体的共晶组织的被称为莱氏体的相。
60.在图4的铸铁中,初晶奥氏体形成树枝状的组织。与此相对,在硼的含量多的图3的铸铁中,树枝状的组织被细小地分割而以粒状存在。另外,与图4相比,在图3中可见莱氏体的区域粗大化的趋势。图3所示的金属组织是在本实施方式的铸铁中特有地发现的金属组织,与凝固速度快时的白口铁的组织相似。具有专利文献3中记载的成分组成的石墨化前的铸铁具有如图4所示的金属组织,未观察到如图3所示的金属组织。详细情况尚不明确,但认为可能是硼的含量引起的铸铁的金属组织的这样的差异对之后的石墨化后的基质的微细化带来了某种影响。
61.在优选的实施方式中,本实施方式的黑心可锻铸铁以质量比计,在将硼的含量记为b(ppm)、将氮的含量记为n(ppm)时,b和n的值满足以下的数学式(1)。
62.n≥1.3b-10
ꢀꢀ
(1)
63.黑心可锻铸铁中所含的氮和硼的量满足数学式(1)时的石墨化后的金属组织如图1所例示的那样,具有铁素体基质和基质中所含的块状石墨,存在渗碳体不易残留的趋势。如果超过由数学式(1)规定的硼的量而过量地含有硼,则在石墨化后的金属组织中,存在渗碳体容易残留在基质的晶界、或黑心可锻铸铁的伸长率降低的趋势。其详细原因尚不清楚,但据认为可能是由于未参与氮化硼形成的硼阻碍石墨化的进行,或者过度固溶在基质中的硼产生影响。数学式(1)的硼的含量的系数1.3等于将氮的原子量14除以硼的原子量10.8而得到的值。固定值10表示相对于氮化硼的化学计量比允许的过量硼的量。将数学式(1)变形而得到的n-1.3b例如可以为-7以上,进而可以为-5以上,进而可以为0以上,例如可以为50以下,进而可以为30以下。
64.在优选的实施方式中,本实施方式的黑心可锻铸铁在还含有钛的情况下,以质量比计,将钛的含量设为ti(ppm)、将硼的含量记为b(ppm)、将氮的含量记为n(ppm)时,ti、b和n的值满足以下的数学式(2)。在含有钛的情况下,通过使硼和钛相对于氮的含量满足下述数学式(2),能够确保良好的机械特性、特别是良好的伸长率,因此优选。将数学式(2)变形而得到的n-1.3b-0.3ti例如可以为100以下,进一步可以为80以下,进一步可以为50以下。n≥1.3b 0.3ti-10
ꢀꢀ
(2)
65.在优选的实施方式中,本实施方式的黑心可锻铸铁中,作为锰与硫的平衡,以质量
比计,将锰的含量设为mn(%)、将硫的含量设为s(%)时,mn和s的值满足以下的数学式(4)。如下述数学式(4)所示,认为通过使(mn-1.7s)在下述范围内,作为阻碍石墨化的元素的锰和硫发生反应而形成硫化锰,能够以更短时间完成石墨化的工序。0.12≥(mn-1.7s)≥0.35
ꢀꢀ
(4)
66.本实施方式的黑心可锻铸铁除了上述元素以外,还含有铁和不可避免的杂质作为剩余部分。作为本实施方式之一,可举出含有上述碳、硅、硼和氮,剩余部分为铁和不可避免的杂质。铁是黑心可锻铸铁的主要元素。在本发明中,不可避免的杂质是指当然在得到所期望的作为铸铁的最终产品为止的制造过程中,不需要有意导入而存在于铸铁中,而且,虽然不需要其存在,但由于是微量的,不一定对铸铁的特性产生不良影响,所以一直存在的杂质。具体而言,原本在原料中含有的例如铬、硫(例如在利用冲天炉准备熔融金属的情况下,热源的焦炭中含有硫)、氧、钛等微量金属元素、在制造工序中从炉壁混入的氧化物等化合物、以及通过熔融金属与气氛气体的反应而生成的氧化物等化合物相当于本发明中的不可避免的杂质。这些不可避免的杂质即使在黑心可锻铸铁中合计含有1.0质量%以下,也不会大幅改变其性质。优选的不可避免的杂质的合计含量为0.5质量%以下。
67.在本实施方式中,允许含有上述碳、硅、硼、氮以外的元素。该情况下,所含的元素的种类和含量在不大幅妨碍本实施方式中的效果的表现的范围内根据所要求的特性适当决定即可。除了上述碳、硅、硼和氮以外的元素可以以单质和化合物中的至少一种的形式添加。上述单质和化合物的种类和添加量可以根据添加的目的而适当选择。但是,关于添加的元素的种类和添加量,优选在确认不大幅妨碍本实施方式中的效果的表现的基础上决定。作为可包含的元素,优选列举锰。可举出以例如大于0%且1.0%以下的范围包含锰。另外,从充分发挥由上述硼和氮带来的效果的观点出发,优选极力抑制比硼更容易与氮结合的铝和钛的含量。例如,优选列举以质量比计满足铝量为0.10%以下和钛量为200ppm以下中的至少1个。
68.分析黑心可锻铸铁和铸铁中所含的碳、硫的含量的方法为燃烧-红外线吸收法。燃烧-红外线吸收法在能够得到碳、硫的准确的分析值的方面是优选的。分析黑心可锻铸铁和铸铁中所含的硅、硼、锰、钛、铝的含量的方法为电感耦合等离子体发光分光分析法。分析黑心可锻铸铁和铸铁中包含的氮的含量的方法为日本工业标准jis g 1228(“铁和钢-氮定量方法”,一般财团法人日本标准协会,1997年8月20日修订)的附录2中记载的氨蒸馏分离双(1-苯基-3-甲基-5-吡唑啉酮)(简称:双吡唑啉酮)吸光光度法。上述各元素量的分析方法也适用于在黑心可锻铸铁的制造过程中得到的熔融金属的分析。
69.<制造方法>对本实施方式的黑心可锻铸铁的制造方法进行说明。
70.在本发明的第二实施方式中,黑心可锻铸铁的制造方法具有:调整将原料熔解而得到的熔融金属的成分组成的工序,使用调整了成分组成的熔融金属,通过铸造得到以质量比计含有2.0%以上且3.4%以下的碳、0.5%以上且2.0%以下的硅、50ppm以上且100ppm以下的硼、65ppm以上且200ppm以下的氮、作为剩余部分的铁和不可避免的杂质的铸铁的工序,以及在高于680℃的温度下将所述铸铁石墨化的工序。这里规定的各元素的含量与本实施方式的黑心可锻铸铁的情况同样地,表示经过铸造和石墨化的工序的最终制品中所含的含量。关于限定各元素的组成范围的理由已经进行了说明,因此在此省略说明。关于所述铸
铁的成分组成,作为一个实施方式,可举出以质量比计含有2.0%以上且3.4%以下的碳、0.5%以上且2.0%以下的硅、50ppm以上且100ppm以下的硼和65ppm以上且200ppm以下的氮,剩余部分为铁和不可避免的杂质。所述铸铁也可以与黑心可锻铸铁同样地以质量比计还含有大于0%且1.0%以下的锰。另外,所述铸铁优选与黑心可锻铸铁同样地抑制铝和钛的含量。
71.在调整将原料熔解而得到的熔融金属的成分组成的工序中,为了将碳、硅、硼和氮的含量调整为上述的范围,除了对熔融金属添加金属、化合物的形态的物质来进行调整以外,也可以使用钢屑、铸铁的再利用等已经含有上述元素的原料来进行调整。因此,在用于得到铸铁的铸造中使用的原料可以使用碳、硅、硼、氮和铁的单质,关于碳、硅和硼,也可以使用作为各个元素与铁的合金的铁碳、硅铁和硼铁等。
72.需要说明的是,在本说明书中,“对熔融金属添加”上述金属和/或化合物的形态的物质(称为“化合物等”)包括向化合物等中加入熔融金属的方式、向熔融金属中加入化合物等的方式、以及向后述的第一熔融金属中加入化合物等后再加入后述的第二熔融金属的方式中的任一方式。
73.为了添加硼,可以使用在熔融金属中添加单质的硼和/或硼铁的方法。在优选的实施方式中,本实施方式的黑心可锻铸铁的制造方法包括在铸造前的熔融金属中添加硼铁和氮化锰中的至少任一种来调整成分组成的工序。硼铁与单质的硼相比容易溶于熔融金属,因此优选。硼铁中所含的硼的比例以质量比计为16%以上且21%以下的硼,容易获得,因此优选。本实施方式的黑心可锻铸铁的制造方法中,铸造前的熔融金属例如如后述的实施例所示,可以含有与本实施方式的黑心可锻铸铁的硼量接近的、例如20ppm以上且小于50ppm的硼,或者满足本实施方式的黑心可锻铸铁的硼量。高硼量的熔融金属例如可以通过将包含使用本实施方式的黑心可锻铸铁的制造方法制造的铸铁和黑心可锻铸铁中的至少一者作为原料的熔融金属、具体而言例如包含在本实施方式的黑心可锻铸铁的制造方法的实施中产生的含有硼和氮的废料的熔融金属熔解而得到。硼在熔融金属的阶段一旦添加,则其含量在之后的工序中也几乎不变化。
74.为了添加氮,可以使用在熔融金属中鼓泡氮气的方法、添加作为氮与其他元素的化合物的含氮化合物的方法等。例如,在熔融金属的准备中使用电炉的情况下,氮的含量大多为60ppm以上且70ppm以下,因此通常需要调整。分析黑心可锻铸铁和铸铁中包含的氮的含量的方法如上所述,为日本工业标准jis g 1228(“铁和钢-氮定量方法”,一般财团法人日本标准协会,1997年8月20日修订)的附录2中记载的氨蒸馏分离双(1-苯基-3-甲基-5-吡唑啉酮)(简称:双吡唑啉酮)吸光光度法。
75.添加氮的方法中,在熔融金属中鼓泡氮气的方法能够不伴随其他成分的变化地仅添加氮,在这一点上是优选的。但是,由于鼓泡氮气,熔融金属的温度有可能急剧降低。因此,需要注意每单位时间鼓泡的氮气的量不过多。
76.另一方面,在添加氮的方法中,添加氮与其他元素的化合物(含氮化合物)的方法与使氮气鼓泡的方法相比,在熔融金属的温度降低少的方面是优选的。作为氮的添加中使用的含氮化合物,从熔点较低而容易添加、混合的方面出发,优选氮化锰。在熔融金属的准备中使用冲天炉的情况下,如上所述,源自热源的焦炭的硫包含在熔融金属中。硫是阻碍石墨化的元素,因此通常进行与锰化合而制成不影响石墨化的硫化锰。在这种情况下,锰的添
加使用锰铁。在本实施方式中,在使用氮化锰代替锰铁的情况下,氮化锰在熔融金属中分解,氮用于调整熔融金属的氮的含量。另外,锰与硫化合而成为硫化锰,因此优选。但是,如果添加超过参与硫化锰的形成的量的氮化锰,则剩余的锰有可能阻碍石墨化,因此需要注意氮化锰的添加量不要过剩。
77.铁的原料可以使用上述的钢屑等。另外,也可以进行上述铸铁的再利用。在铁的原料中使用钢屑等的情况下,碳和硅已经包含在一般的钢材中,因此在多数情况下,仅通过将钢屑熔解就能够使这些元素适合于本实施方式中规定的成分组成范围。在钢屑、再利用的铸铁中,除了上述碳和硅以外,有时还大量含有铝、钛等。在该情况下,铝、钛等与氮反应而容易形成比氮化硼更稳定的氮化物,因此需要注意氮化硼的合成所需的氮不要不足。
78.在优选的实施方式中,在本实施方式的黑心可锻铸铁的制造方法中,在将铸造前的熔融金属熔解时使用的原料中如上所述那样包含使用本实施方式的黑心可锻铸铁的制造方法制造出的铸铁或黑心可锻铸铁中的至少一方。在此,如上所述,“铸铁”是指铸造后且石墨化前的制品。铸铁和黑心可锻铸铁不仅包括产品,还包括产品以外的被称为浇道、流道等的部分、检查的结果不良的产品等所谓的废料。
79.在通过实施本实施方式的黑心可锻铸铁的制造方法而产生的废料(包含铸铁或黑心可锻铸铁中的至少一方的废料)中含有硼和氮。假设存在于废料中的硼和氮的大部分为六方晶系的氮化硼,则由于六方晶系的氮化硼的熔点约为3000℃,因此存在是否能够完全溶解并再利用的担忧。另外,已知在黑心可锻铸铁中含有超过一定量的硼的情况下,石墨化受到阻碍。因此,还存在废料中所含的硼是否会阻碍石墨化这样的担忧。但是,在钢铁领域中,已知钢铁中的氮化硼在比上述六方晶系的氮化硼的熔点充分低的温度下分解为氮和硼,认为这对于铸铁中的氮化硼也是同样的。另外,根据本发明人的研究可知,即使在将仅由废料构成的原料熔解的情况下,只要硼和氮的含量如本实施方式所示那样被适当地管理,就不会阻碍石墨化,能够制造本实施方式的黑心可锻铸铁。
80.为了将原料熔解而准备熔融金属,可以使用利用冲天炉或电炉等公知的熔解设备(熔解炉)进行熔解的手段。在本实施方式的黑心可锻铸铁的制造方法中,碳的含量为2.0质量%以上,因此熔解所需的温度不会超过1400℃。因此,不需要达到温度高于1400℃的大规模溶解设备。
81.作为得到铸铁的工序,例如可举出:在上述熔解炉中熔解原料而准备熔融金属后,将该熔融金属出炉至浇包,在浇包中进行熔融金属的成分组成和温度的调整后,从浇包向铸模浇注熔融金属而进行铸造。成分组成如上所述,除了利用浇包进行调整以外,还可以利用所使用的原料进行调整。
82.在上述调整熔融金属的成分组成的工序中,在向熔融金属中添加上述的氮化锰等含氮化合物来调整熔融金属的氮量的情况下,优选包括在向第一熔融金属中添加含氮化合物之后追加第二熔融金属的工序。根据该方式,能够抑制含氮化合物(优选氮化锰)与熔融金属接触时的分解和挥发等,能够容易地调整熔融金属中的氮量。例如在利用浇包调整上述熔融金属的成分组成的情况下,可举出将上次向铸模浇注后残留的浇包的残留熔融金属作为第一熔融金属,在向该第一熔融金属添加含氮化合物后,追加从熔解炉流出的熔融金属作为第二熔融金属。所述第一熔融金属可以是如上所述残留于浇包的残留熔融金属,也可以是最初从熔解炉向浇包流出的成分未调整的熔融金属。在使用后者的成分未调整的熔
融金属作为第一熔融金属的情况下,能够省略对第一熔融金属添加含氮化合物并追加第二熔融金属的工序。
83.为了进一步提高上述含氮化合物的分解等的抑制效果,优选第一熔融金属的温度比第二熔融金属的温度低。例如,在第一熔融金属为残留熔融金属的情况下,第一熔融金属的温度可以设为大致1320~1350℃的范围,在第二熔融金属为从熔解炉流出的熔融金属的情况下,第二熔融金属的温度可以设为大致1460~1500℃的范围。此外,第一熔融金属的质量优选小于第二熔融金属的质量。通过使第一熔融金属的质量比第二熔融金属的质量少,容易实现上述第一熔融金属与第二熔融金属的温度的关系。例如可举出第一熔融金属的量以质量比计为总熔融金属的1%以上且小于50%。
84.本实施方式的黑心可锻铸铁的制造方法具有通过铸造得到铸铁的工序。在本实施方式的制造方法中,用于铸造的铸模可以使用将型砂成形而成的铸模、模具等公知的铸模。通过在铸造后将冷却后的铸模拆开,取出浇铸于铸模的铸铁。铸铁进一步分离成产品部分和产品以外的浇道、流道等部分。产品以外的部分可以作为废料进行再溶解。
85.本实施方式的黑心可锻铸铁的制造方法具有在铸造之后以高于680℃的温度对铸铁进行石墨化的工序。本实施方式的制造方法中,进行石墨化的手段可以使用气体燃烧炉、电炉等公知的热处理炉。
86.石墨化是黑心可锻铸铁的制造方法所特有的工序。在石墨化的工序中,通过将由铸造得到的铸铁加热至高于680℃、进而超过相当于a1相变点的720℃的温度,从而使渗碳体分解而使石墨析出,并且通过将由奥氏体形成的基质冷却而使其相变为铁素体,能够对铸铁赋予韧性。将铸铁石墨化的工序分为最初进行的第一阶段石墨化和在第一阶段石墨化之后进行的第二阶段石墨化。石墨化的工序优选包括在超过900℃的温度下进行加热的第一阶段石墨化、和开始温度为720℃以上且800℃以下且结束温度为680℃以上且720℃以下的第二阶段石墨化。
87.第一阶段石墨化是在超过900℃的温度范围内将奥氏体中的渗碳体分解而使石墨析出的工序。在第一阶段石墨化中,通过渗碳体的分解而生成的碳有助于块状石墨的生长。进行第一阶段石墨化的温度优选为950℃以上且1100℃以下。更优选的温度范围为980℃以上且1030℃以下。
88.在本实施方式的黑心可锻铸铁的制造方法中,通过本实施方式的效果,与现有技术相比,能够大幅缩短进行第一阶段石墨化的时间。实际的时间可以根据退火炉的大小、进行处理的铸铁的量等适当确定。关于第一阶段石墨化所需的时间,在现有技术中需要数小时至数十小时,与此相对,在本实施方式中最长为3小时、典型地为1小时以下即可,根据条件,也可以在超过30分钟且45分钟以下完成。
89.第二阶段石墨化是在比进行第一阶段石墨化的温度低的温度范围内将珠光体中的渗碳体分解而使石墨和铁素体析出的工序。第二阶段石墨化为了促进块状石墨的生长、可靠地进行从奥氏体向铁素体的相变,优选一边使温度从第二阶段石墨化开始温度逐渐降低至第二阶段石墨化结束温度一边进行。从第二阶段石墨化开始温度到第二阶段石墨化结束温度为止的平均冷却速度更优选设为1.5℃/分钟以下,进一步优选为1.0℃/分钟以下。需要说明的是,从块状石墨的生长和向铁素体的相变的观点出发,上述平均冷却速度越慢越优选,但从确保生产率的观点出发,上述平均冷却速度的下限可以设为0.20℃/分钟左
右。
90.第二阶段石墨化开始温度优选为720℃以上且800℃以下。第二阶段石墨化开始温度的更优选的温度范围为740℃以上且780℃以下。第二阶段石墨化结束温度为680℃以上且720℃以下的温度,优选为比第二阶段石墨化开始温度低的温度。第二阶段石墨化结束温度的更优选的温度范围为690℃以上且710℃以下。
91.在本实施方式的黑心可锻铸铁的制造方法中,通过本实施方式的效果,与现有技术相比,能够大幅缩短进行第二阶段石墨化的时间。实际的时间可以根据退火炉的大小、进行处理的铸铁的量等适当确定。关于第二阶段石墨化所需的时间,在现有技术中,与第一阶段石墨化同样地需要数小时至数十小时,与此相对,在本实施方式中,最长为3小时、典型地为1小时以下即可,根据条件,也可以在超过30分钟且45分钟以下完成。
92.在优选的实施方式中,本实施方式的黑心可锻铸铁的制造方法在进行石墨化的工序中,将铸铁在高于680℃的温度下进行石墨化的时间合计为1小时以上且6小时以下。在本说明书中,“将铸铁在高于680℃的温度下石墨化的时间”是指将铸铁的温度保持在上述的第一阶段石墨化的温度的时间和保持在第二阶段石墨化的温度的时间的合计时间。上述石墨化的时间的合计优选为5小时以下,更优选为3小时以下。上述时间是铸铁的中心附近达到上述温度范围后的时间。
93.本实施方式的黑心可锻铸铁的制造方法是制造兼具上述化学组成(成分组成)和金属组织的黑心可锻铸铁的方法。通过本实施方式的黑心可锻铸铁的制造方法制造的黑心可锻铸铁、特别是经过石墨化的工序后的黑心可锻铸铁具有铁素体基质和基质中所含的块状石墨,含有上述量的硼和氮,基质的结晶粒度以通过金属组织照片与结晶粒度标准图的比较而数值化的粒度编号计为8.0以上且10.0以下。另外,在优选的实施方式中,块状石墨的平均粒径为10微米以上且40微米以下。
94.<其他>对合金组成(成分组成)和制造方法对本实施方式的黑心可锻铸铁的金属组织的影响进行说明。
95.本实施方式的黑心可锻铸铁具有铁素体基质和基质中所含的块状石墨,作为成分的特征,以质量比计含有50ppm以上且100ppm以下的硼和65ppm以上且200ppm以下的氮。另外,作为金属组织的特征,具有基质的结晶粒度以通过金属组织照片与结晶粒度标准图的比较而数值化的粒度编号计为8.0以上且10.0以下。这些特征是确定第1实施方式所需的事项中的最低限度。
96.为了制造具备上述特征的黑心可锻铸铁,关于制造方法,需要具有在高于680℃的温度下对铸铁进行石墨化的工序。该条件是为了能够实施本实施方式所需的条件。在本实施方式中,不需要进行上述专利文献3中记载的在275℃以上且425℃以下进行的预加热的工序。因此,与需要预加热的现有技术相比,能够缩短热处理所需的时间,或者削减制造成本。然而,在本实施方式中,不排除以低于680℃的温度对铸铁进行热处理。实施例
97.<第1实施例>在第1实施例中,对硼在含有一定量的氮的熔融金属中的添加量对黑心可锻铸铁的金属组织、机械强度造成的影响进行了研究。
98.将按照以质量比计含有3.0%的碳、1.5%的硅、铁和不可避免的杂质作为剩余部分的方式配合的熔融金属出炉至700kg浇包,以56g至336g的范围的6个水准添加含有18%的硼的铁硼后进行搅拌,然后立即注入铸模进行铸造,得到硼的含量不同的6种铸铁。在得到的铸铁中,除了上述量的碳和硅以外,还含有来自原料的110ppm的氮和来自原料的0.35%的锰。
99.接着,将铸造得到的铸铁用45分钟从室温升温至980℃并保持1小时,进行第一阶段石墨化。接着,将试样的温度冷却至760℃后,一边用1小时从760℃冷却至720℃一边进行第二阶段石墨化,制作试样no.1至6这6种黑心可锻铸铁的试样。对于制作的试样,通过燃烧-红外线吸收分析碳的含量,通过电感耦合等离子体发光分光分析法分析硅、硼和锰的含量。任一试样均以质量比计含有3.0%的碳、1.5%的硅、0.35%的源自铁的原料的锰。氮的含量通过日本工业标准jis g 1228(“铁和钢-氮定量方法”,一般财团法人日本标准协会,1997年8月20日修订)的附录2中记载的氨蒸馏分离双(1-苯基-3-甲基-5-吡唑啉酮)(简称:双吡唑啉酮)吸光光度法进行测定。将硼和氮的分析的结果、以及将分析结果代入由数学式(1)导出的n-1.3b而得到的值示于表1。其中,在表1中,关于试样no.2和3的硼含量,用括号记载了根据硼铁的添加量推定的硼含量的推定值。
100.[表1]
[0101]
接着,对制作的试样的切断面进行研磨,用硝酸乙醇溶液对晶界进行蚀刻后,用光学显微镜观察切断面的金属组织,用设置于光学显微镜的ccd照相机拍摄金属组织照片。将试样no.4的金属组织照片的例子示于图1,将试样no.1的金属组织照片的例子示于图2。需要说明的是,在试样no.1至6的试样中,铁素体在金属组织中所占的面积比均为80%以上。
[0102]
接着,通过所拍摄的金属组织照片与日本工业标准jis g 0551(“钢-结晶粒度的显微镜试验方法”,一般财团法人日本标准协会,2013年1月21日修订)的“附录b(规定)结晶粒度的测定-结晶粒度标准图”的比较,测定铁素体基质的结晶粒度。在比较时,忽略金属组织照片中所含的块状石墨的部分,仅着眼于铁素体基质的晶界的尺寸来进行比较。另外,根据金属组织照片判断有无渗碳体的残留。进而,由得到的试样制作拉伸试验用的试验片,利用拉伸试验机测定试验片的强度(拉伸强度)和伸长率。将这些评价结果汇总示于表1。
[0103]
根据表1,试样no.3至6均满足本实施方式的硼和氮的含量的范围。关于试样no.1和2,硼的含量比组成范围的下限即50ppm少。另外,如果对铁素体基质的结晶粒度进行观察,则试样no.3至6均满足本实施方式的粒度编号的范围。关于试样no.1和2,粒度编号小于作为下限的8.0,与试样no.3至6相比结晶粒度粗。即,表1所记载的试样中的试样no.3至6相当于本实施方式的黑心可锻铸铁及其制造方法的实施例。
[0104]
由上述第1实施例可知,根据本实施方式的黑心可锻铸铁及其制造方法,即使不进
行专利文献3所记载的预加热,与现有技术相比也能够大幅缩短石墨化的时间。
[0105]
如图1所例示的那样,在相当于本发明的实施例的试样no.3至6的黑心可锻铸铁的金属组织中,大量的块状石墨存在于基质的2个铁素体晶粒之间的晶界的位置、和/或存在于3个铁素体晶粒的晶界三重点的位置。块状石墨几乎不跨越基质的4个以上的晶界而存在。
[0106]
另外,块状石墨不是偏向基质的一部分晶粒的位置而存在,而是均匀地存在于基质的多个晶粒的位置。在基质的大量晶粒中,在该晶粒与周围的晶粒之间的晶界的位置存在块状石墨、在晶界的位置不存在块状石墨的晶粒为少数。即,块状石墨分散存在于基质的晶界的位置。
[0107]
与此相对,对于试样no.1,如图2所例示的那样,在硼的含量比组成范围的下限即50ppm少的试样no.1和2的黑心可锻铸铁的金属组织中,大量的块状石墨形成大块,在块状石墨中也存在跨越基质的4个以上的晶界的石墨。另外,大量的块状石墨偏向基质的一部分晶粒的位置而存在,在晶界的位置观察到大量不存在块状石墨的晶粒。
[0108]
在相当于本发明的实施例的试样中的试样no.3中,在金属组织中观察到渗碳体的残留,暗示石墨化未完全完成。在硼的含量比试样no.3多的试样no.4中,未观察到渗碳体的残留。在硼的含量更多的试样no.5和6中,再次观察到少量的渗碳体的残留。认为这是由于相对于氮的含量过量地含有硼,所以石墨化受到阻碍。
[0109]
对相当于本发明的实施例的试样的机械强度进行观察时,如表1所示,强度和伸长率在试样no.4中显示出最大值。在观察到渗碳体的残留的试样no.3和5中,强度和伸长率也与试样no.4的强度和伸长率相比几乎没有变化。如上所述,认为强度和伸长率的提高与铁素体基质的结晶粒度变得微细有关。在试样no.6中,机械强度降低,特别是关于伸长率,与其他试样相比大幅降低。试样no.6中的伸长率的降低仅通过渗碳体的残留无法说明。认为有可能固溶于基质的硼的量增加造成影响。
[0110]
如上所述,在优选的实施方式中,本实施方式的黑心可锻铸铁在以质量比计将硼的含量记为b(ppm)、将氮的含量记为n(ppm)时,b和n的值满足数学式(1)。关于第1实施例中的试样no.6,数学式(1)的右边的值为120,大于左边的氮量110,因此不满足数学式(1)。关于试样no.5,数学式(1)的右边的值为107,比左边的氮量110稍小。即,试样no.3至5相当于本发明的优选的实施方式,在这些试样中,可以说抑制了由过剩的硼引起的伸长率的降低。
[0111]
<第2实施例>在第2实施例中,对与第1实施例相比延长了石墨化的时间时的影响进行了研究。将与第1实施例的试样no.3至6相同的石墨化前的铸铁用1小时10分钟从室温升温至980℃并保持1小时20分钟,进行第一阶段石墨化。接着,将铸铁的温度冷却至760℃后,一边用1小时20分钟从760℃冷却至720℃一边进行第二阶段石墨化,制作试样no.8至11这4种黑心可锻铸铁的试样。对所制造的试样进行与实施例1相同的评价。将这些评价结果汇总示于表2。
[0112]
[表2]
[0113]
根据表2,在均满足本实施方式的硼和氮的含量的范围的试样no.8~11中,均满足本实施方式的粒度编号的范围。即,表2所记载的试样no.8~11均相当于本实施方式的黑心可锻铸铁及其制造方法的实施例。
[0114]
另外,对于硼和氮的含量相同的试样,比较表1和表2的结果时,在石墨化的时间长的后者中,存在铁素体基质的粒度编号稍微变大的趋势、以及强度和伸长率稍微提高的趋势。认为这是因为,从室温升温至作为第一阶段石墨化的温度的980℃所花费的时间变长,从而氮化硼的形成进行,铁素体的晶粒进一步微细化。
[0115]
另一方面,从试样no.11与其他试样的比较可知,从确保良好的伸长率的观点出发,硼和氮的含量优选满足数学式(1)。另外,由上述表2的结果可知,为了抑制伸长率的降低,在制造工序中,与延长石墨化的时间来抑制渗碳体的残留相比,满足数学式(1)是有效的。
[0116]
<第3实施例>在第3实施例中,对氮的含量的调整方法、以及是否能够将本实施方式的铸铁和黑心可锻铸铁的废料作为原料进行再利用进行了研究。试样的目标成分组成以质量比计,碳为3.0%、硅为1.5%、硼为70ppm、氮为160ppm。原料的熔解使用电炉,一次熔解中使用的原料的质量设为50kg。
[0117]
第3实施例中的试样no.12使用用电炉制造的合金作为熔解中使用的原料。合金中的硼的含量为33ppm、氮的含量为76ppm。将该合金50kg熔解,为了调整所得到的熔融金属的成分组成,相对于所得到的熔融金属添加硼的含量为16%的硼铁16g、氮的含量为28%的氮化锰100g和单质的铋15g后,搅拌后,立即浇注到铸模中,通过铸造得到铸铁。对所得到的铸铁在与第1实施例相同的条件下进行石墨化,得到试样no.12的黑心可锻铸铁。对所得到的黑心可锻铸铁进行了与第1实施例同样的评价。
[0118]
第3实施例中的试样no.13使用通过本实施方式的黑心可锻铸铁的制造方法制造的石墨化前的铸铁(再利用铸铁)作为用于熔解的原料。再利用铸铁中的硼的含量为69ppm、氮的含量为87ppm。将该再利用铸铁50kg熔解,为了调整所得到的熔融金属的成分组成,对所得到的熔融金属添加氮的含量为28%的氮化锰100g和单质的铋15g后,搅拌后,立即浇注到铸模中,通过铸造得到铸铁。对所得到的铸铁在与第1实施例相同的条件下进行石墨化,得到试样no.13的黑心可锻铸铁。对所得到的黑心可锻铸铁进行了与第1实施例同样的评价。
[0119]
第3实施例中的试样no.14使用通过本实施方式的黑心可锻铸铁的制造方法制造的黑心可锻铸铁(再利用黑心可锻铸铁)作为用于熔解的原料。再利用黑心可锻铸铁中的硼的含量为68ppm、氮的含量为82ppm。另外,再利用黑心可锻铸铁的碳的含量由于石墨化的过程中的脱碳而减少至2.70%。将该再利用黑心可锻铸铁50kg熔解,为了调整所得到的熔融金属的成分组成,通过添加石墨粉而使碳的含量增加至3.04%。然后,对得到的熔融金属添
加氮的含量为28%的氮化锰100g和单质的铋15g后进行搅拌。搅拌后,立即浇注到铸模中,通过铸造得到铸铁。对所得到的铸铁在与第1实施例相同的条件下进行石墨化,得到试样no.14的黑心可锻铸铁。然后,对所得到的黑心可锻铸铁进行了与第1实施例同样的评价。关于试样no.12至14,将成分调整前后的碳、硼和氮的含量(单位为以质量比计的%或ppm)以及黑心可锻铸铁的评价结果汇总示于表3。
[0120]
[表3]
[0121]
根据表3,试样no.12至14的黑心可锻铸铁的成分组成的调整后的硼量和氮量均满足本实施方式的硼和氮的含量的范围,并且满足本实施方式的粒度编号的范围。即,表3所记载的试样no.12至14均相当于本实施方式的黑心可锻铸铁及其制造方法的实施例。另外,对于任一试样均未确认到渗碳体的残留,机械强度也不逊色于第1和第2实施例中的机械强度。由第3实施例的结果可知,可以将氮化锰用于氮的含量的调整。另外可知,作为原料,将本实施方式的铸铁和黑心可锻铸铁的废料(再利用铸铁)熔解,制成熔融金属而再利用的情况下,也能够没有问题地发挥本发明的效果。
[0122]
<第4实施例>在第4实施例中,对氮和硼以外的元素的含量的平衡进行了研究。将按照以质量比计含有3.0%的碳、1.5%的硅、铁和不可避免的杂质作为剩余部分的方式配合的熔融金属出炉至700kg浇包中。在第4实施例中的试样no.15中,对于出炉至浇包的熔融金属,添加氮为5%、锰为70%、剩余部分为铁的合金1400g、和含有18%硼的铁硼135g后进行搅拌,采集用于分析熔融金属的成分组成的试样后,立即浇注至铸模,通过铸造得到铸铁。
[0123]
在第4实施例中的试样no.16中,对于出炉至浇包的熔融金属,添加含有10%的氮、90%的锰的合金1100g和含有18%的硼的铁硼160g后进行搅拌,采集用于分析熔融金属的成分组成的试样后,立即浇注至铸模,通过铸造得到铸铁。
[0124]
在第4实施例中的试样no.17中,对于出炉至浇包的熔融金属,添加氮为5%、锰为70%、剩余部分为铁的合金1400g、和含有18%硼的铁硼200g后进行搅拌,采集用于分析熔融金属的成分组成的试样后,立即浇注至铸模,通过铸造得到铸铁。使用从试样no.15至17的熔融金属采集的试样,与第1实施例同样地分析成分组成,将结果示于表4。硫的含量通过燃烧-红外线吸收法进行分析。
[0125]
[表4]
[0126]
根据表4,第4实施例的试料no.15至17的熔融金属的成分组成中,硼和氮的含量均
落入本实施方式的范围。由此推定,石墨化后的黑心可锻铸铁的成分也落入本实施方式的范围内。另外,在这些试样中,除了所添加的合金中所含的锰、热源的焦炭中所含的硫以外,还包含原料的铁中所含的微量的钛。
[0127]
接着,对于铸造得到的铸铁,以与第1实施例相同的条件进行第一阶段石墨化和第二阶段石墨化,对于石墨化处理后的试样,以与第1实施例相同的方法进行金属组织的观察和机械强度的评价。将评价结果示于表5。需要说明的是,表5中一并示出表4所示的熔融金属的成分分析值中的、以质量比计将氮含量记为n(ppm)、将硼含量设为(ppm)、将钛含量设为(ppm)、将锰含量设为mn(%)、将硫含量设为s(%)时的n-1.3b、n-1.3b-0.3ti和mn-1.7s的计算值。此外,关于观察石墨化前的铸铁的断裂面时的结晶石墨的有无,也示于表5。
[0128]
[表5]
[0129]
根据表5,在试样no.15中,在铸造后的断裂面的金属组织中没有结晶石墨,在石墨化处理后的金属组织中没有观察到渗碳体。需要说明的是,如上所述,上述“结晶石墨”是指熔融金属在铸模的内部被冷却时结晶的石墨,与通过石墨化而在固相内析出的、例如图1所示的石墨化后的金属组织中的块状石墨相区别。另外,机械强度也不逊色于其他实施例的值。认为这是因为,作为阻碍石墨化的元素的锰和硫发生反应而形成硫化锰,石墨化的工序在短时间内完成。另一方面,在试样no.16和17中,在铸造后的断裂面观察到结晶石墨,在石墨化处理后的金属组织中观察到少量渗碳体。另外,由试样no.15与试样no.16及17的对比可知,从可靠地确保良好的机械强度、特别是高的伸长率的观点出发,优选满足数学式(2),相对于氮和钛的含量,硼不会过剩。
[0130]
<第5实施例>在第5实施例中,作为使氮含有的方法之一,对氮化锰的添加方法进行了研究。在上述第4实施例中,在任一试样中,均预先将氮化锰设置于浇包的底部,向其中注入熔融金属并进行混合。与此相对,在第5实施例中,向浇包中的未添加氮化锰等的熔融金属90kg(上次浇注到铸模后的浇包的残留熔融金属、第一熔融金属)的熔融金属面添加含有10%氮、90%锰的合金1100g和含有18%硼的铁硼135g后进行混合,进行下述表6所示的“成分组成调整后的保持时间”的保持。之后,在浇包中添加第二熔融金属直至熔融金属的合计重量达到700kg后进行搅拌,采集用于分析熔融金属的成分的试样。使用采集的试样分析锰、氮和硼的含量。将分析的结果示于表6。需要说明的是,表6和后述的表7中的“原始熔融金属”是指未添加氮化锰等的熔融金属。
[0131]
[表6]
[0132]
根据表6,确认了通过上述的添加方法,也含有与第4实施例的情况同等量的锰和氮。另外,即使在添加氮化锰等后保持10分钟后追加第二熔融金属的情况下,对于各成分的含量也未观察到大的减少。
[0133]
接着,向浇包中的未添加氮化锰的熔融金属的剩余50kg(上次浇注到铸模中后的浇包的残留熔融金属、第一熔融金属)的熔融金属面添加含有10%氮、90%锰的合金1100g和含有18%硼的铁硼135g后进行混合,然后放置5分钟后,将第二熔融金属浇注到浇包中直至熔融金属的合计重量达到700kg,进行下述表7的“第二熔融金属追加后的保持时间”的保持。然后,采集用于分析熔融金属的成分的试样,分析该试样的锰、氮和硼的含量。将分析的结果示于表7。
[0134]
[表7]
[0135]
根据表7,即使在少量的熔融金属中添加氮化锰后加入第二熔融金属,放置一段时间,也未观察到各成分的含量大幅减少。根据该方法可知,即使在连续操作的情况下,也不需要将氮化锰设置于浇包的底面,而能够添加于金属液面。另外可知,即使将添加有氮化锰和硼铁的熔融金属保持10分钟,熔融金属的成分也没有大的变化,对铸造没有障碍。
[0136]
本说明书的公开内容包含作为优先权主张的基础的日本特愿2020-038913号中记载的以下的方式。(方式a1)一种黑心可锻铸铁,其具有铁素体基质和上述基质中所含的块状石墨,以质量比计含有50ppm以上且100ppm以下的硼和65ppm以上且170ppm以下的氮,上述基质的结晶粒度以通过金属组织照片与结晶粒度标准图的比较而数值化的粒度编号计为8.0以上且10.0以下。(方式a2)根据方式a1所述的黑心可锻铸铁,其中,在将硼的含量记为b(ppm)、将氮的含量记为n(ppm)时,b和n的值满足以下的数学式(1)。n≥1.3b-10 (1)(方式a3)根据方式a1或a2中任一项所述的黑心可锻铸铁,其中,上述块状石墨分散存在于
上述基质的晶界的位置。(方式a4)根据方式a1~a3中任一项所述的黑心可锻铸铁,其中,上述块状石墨的平均粒径为10微米以上且40微米以下。(方式a5)根据方式a1~a4中任一项所述的黑心可锻铸铁,其中,每1.00平方毫米截面积的上述块状石墨的颗粒数为200个以上且1200个以下。(方式a6)根据方式a1~a5中任一项所述的黑心可锻铸铁,其中,以质量比计包含2.0%以上且3.4%以下的碳、0.5%以上且2.0%以下的硅、作为剩余部分的铁和不可避免的杂质。(方式a7)一种黑心可锻铸铁的制造方法,其包括:铸造铸件的工序,所述铸件以质量比计含有2.0%以上且3.4%以下的碳、0.5%以上且2.0%以下的硅、50ppm以上且100ppm以下的硼、65ppm以上且170ppm以下的氮、作为剩余部分铁和不可避免的杂质;以及在高于680℃的温度下使上述铸件石墨化的工序。(方式a8)根据方式a7所述的黑心可锻铸铁的制造方法,其中,在上述石墨化的工序中,在高于680℃的温度下对上述铸件进行石墨化的时间合计为1小时以上且6小时以下。(方式a9)根据方式a7或a8中任一项所述的黑心可锻铸铁的制造方法,其包括:在铸造前的熔融金属中添加硼铁和氮化锰中的至少一者来调整组成的工序。(方式a10)根据方式a9所述的黑心可锻铸铁的制造方法,其中,在将铸造前的熔融金属溶解时使用的原料中包含使用方式a7~a9中任一项所述的黑心可锻铸铁的制造方法制造出的铸物或黑心可锻铸铁中的至少一者。
[0137]
本技术基于申请日为2020年3月6日的日本国专利申请即日本特愿2020-038913号基础申请主张优先权。日本特愿2020-038913号通过参照而引入到本说明书中。
再多了解一些
本文用于企业家、创业者技术爱好者查询,结果仅供参考。