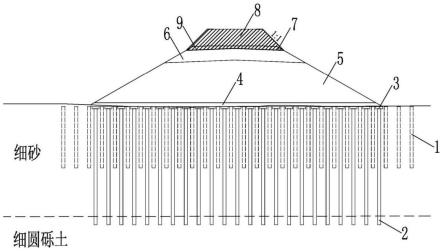
1.本发明涉及铁路工程技术领域,尤其涉及一种高速铁路无砟轨道地基及处理方法。
背景技术:
2.新建川藏铁路,沿线面临着工程环境复杂、不良地质和极端地质灾害等诸多挑战。在理塘至毛垭坝段,线路主要以填方路基通过,段内存在大量较厚的砂土层且存在砂土液化,液化深度0~25m左右。
3.采用传统的砂桩法、碎石桩法等处理地基液化,虽然有效地砂土液化,但是地基后期沉降过大,难以满足高速铁路无砟轨道“零沉降”的严格控制要求,对铁路后期安全运营存在较大的安全隐患。
技术实现要素:
4.本发明的目的在于提供一种高速铁路无砟轨道地基及处理方法,解决了传统的砂桩法、碎石桩法等处理地基液化,会导致地基后期沉降过大的技术问题。
5.为实现上述目的,本发明提供了一种高速铁路无砟轨道地基,包括碎石桩、cfg桩、桩帽、垫层、路堤本体、基床底层和土工布,所述碎石桩的数量为多个,多个所述碎石桩间隔均匀设置于细砂层内,所述cfg桩的数量为多个,多个所述cfg桩间隔均匀设置于细砂层内,并与多个所述碎石桩交错设置,每个所述cfg桩的顶端均设置有所述桩帽,所述垫层铺设于多个所述桩帽的上方,所述路堤本体设置于垫层的上方,所述基床底层设置于所述路堤本体的上方,所述土工布铺设于所述基床底层的上方,所述土工布的上方设置有堆载预压填土。
6.其中,所述垫层包括碎石层和土工格栅,所述碎石层的数量为三层,所述土工格栅的数量为两个,所述碎石层和所述土工格栅交错铺设于多个所述桩帽的上方。
7.其中,所述碎石层的高度为2m,所述堆载预压填土的堆载预压高度为3m。
8.其中,所述土工布回折于所述堆载预压填土的顶面,每侧宽度不小于2.5m。
9.本发明还提供一种高速铁路无砟轨道地基处理方法,采用上述所述的高速铁路无砟轨道地基,包括如下步骤:
10.步骤1:施工准备;
11.步骤2:桩位放样,标记所述碎石桩和所述cfg桩的桩心、桩的外轮廓以及加固区边缘线;
12.步骤3:先施工所述碎石桩,采用振动沉管成桩法,桩机就位时,机架必须水平稳固,沉管垂直对中,振动沉管至设计深度;
13.步骤4:停振灌料加压成桩;
14.步骤5:重复步骤3至步骤4,直至碎石桩施工完成;
15.步骤6:所述碎石桩成桩质量检验;
16.步骤7:施工所述cfg桩,所述cfg桩采用长螺旋钻孔,桩机就位,调整钻杆垂直地面并对准桩位中心,关闭钻头阀门,向下移动钻头至地面开始钻进,先慢后快,钻至设计深度并停钻;
17.步骤8:灌注混合料,钻杆芯管充满混合料后开始拔管,匀速拔管至桩顶;
18.步骤9:重复步骤7至步骤8,直至cfg桩施工完成;
19.步骤10:所述cfg成桩质量检验;
20.步骤11:所述cfg桩的所述桩帽施工;
21.步骤12:铺设所述垫层,分层填筑压实所述路堤本体填土,直至所述基床底层顶面;
22.步骤13:在所述基床底层顶面上铺一层所述土工布,分层填筑压实所述预压荷载填土;
23.步骤14:达到预压期后,通过沉降观测,并进行工后沉降分析,分析结果满足设计要求时,可分层进行预压荷载填土卸载;
24.步骤15:卸载完成后进行基床表层填筑和上部轨道结构施工。
25.其中,所述步骤1具体包括:
26.清除表土,完成临时排水,平整场地,对段内地表水、地下水及施工用水水质进行取样复测,施工影响范围内的管线进行调查核实和迁改,所述cfg桩进行室内配比试验,所述碎石桩和所述cfg桩成桩工艺性试验。
27.其中,所述步骤3具体包括:
28.所述碎石桩施工从两侧向中间进行,中间的桩隔排隔桩跳打施工;沉管在自由状态下对正桩位,利用锤重及沉管自重徐徐静压1~2m后开动振动锤振动下沉,每下沉0.5~1.0m,留振5~10s,直至设计深度。
29.其中,所述步骤13具体包括:
30.堆载预压高度为3m,在所述基床底层顶面上铺一层所述土工布后,以0.4m一层分层填筑分层压实,压实采用中型碾压机具压实,直至填筑完成后,填筑完成后将所述土工布回折于预压土顶面每侧宽度不小于2.5m,并用土压紧固定,避免预压填料流失、污染路基。
31.本发明的一种高速铁路无砟轨道地基及处理方法,采用散体碎石桩和刚性cfg桩组合的地基处理方式,利用碎石桩的置换和挤密作用,解决了砂土的液化特性;利用cfg桩穿透液化的砂土层,提高了地基的刚度和承载力,减少地基变形;最后经过不少于6个月的堆载预压,消除路堤填筑后的工后沉降。该处理方法操作简单,符合环保要求,具有广阔的推广应用前景。
附图说明
32.为了更清楚地说明本技术实施例或现有技术中的技术方案,下面将对实施例或现有技术描述中所需要使用的附图作简单地介绍。
33.图1是本发明提供的一种高速铁路无砟轨道地基的横断面示意图。
34.图2是本发明提供的一种高速铁路无砟轨道地基的桩位放样示意图。
35.图3是本发明提供的一种高速铁路无砟轨道地基的垫层大样图。
36.图4是本发明提供的一种高速铁路无砟轨道地基的堆载预压纵断面设计示意图。
37.图5是本发明提供的一种高速铁路无砟轨道地基施工方法的施工流程图。
38.1-碎石桩、2-cfg桩、3-桩帽、4-垫层、5-路堤本体、6-基床底层、7-土工布、8-堆载预压填土、9-基床表层、401-碎石层、402-土工格栅。
具体实施方式
39.下面详细描述本发明的实施例,所述实施例的示例在附图中示出,下面通过参考附图描述的实施例是示例性的,旨在用于解释本发明,而不能理解为对本发明的限制。
40.请参阅图1-图4,本发明提供一种高速铁路无砟轨道地基,包括碎石桩1、cfg桩2、桩帽3、垫层4、路堤本体5、基床底层6和土工布7,所述碎石桩1的数量为多个,多个所述碎石桩1间隔均匀设置于细砂层内,所述cfg桩2的数量为多个,多个所述cfg桩2间隔均匀设置于细砂层内,并与多个所述碎石桩1交错设置,每个所述cfg桩2的顶端均设置有所述桩帽3,所述垫层4铺设于多个所述桩帽3的上方,所述路堤本体5设置于垫层4的上方,所述基床底层6设置于所述路堤本体5的上方,所述土工布7铺设于所述基床底层6的上方,所述土工布7的上方设置有堆载预压填土8,所述垫层4包括碎石层401和土工格栅402,所述碎石层401的数量为三层,所述土工格栅402的数量为两个,所述碎石层401和所述土工格栅402交错铺设于多个所述桩帽3的上方,
41.在本实施方式中,采用散体碎石桩1和刚性cfg桩2组合的地基处理方式,利用所述碎石桩1的置换和挤密作用,解决了砂土的液化特性;利用所述cfg桩2穿透液化的砂土层,提高了地基的刚度和承载力,减少地基变形;最后经过不少于6个月的堆载预压,消除路堤填筑后的工后沉降。该处理方法操作简单,符合环保要求,具有广阔的推广应用前景。
42.请参阅图5,本发明还提供一种高速铁路无砟轨道地基处理方法,采用上述所述的高速铁路无砟轨道地基,包括如下步骤:
43.s1:施工准备;
44.具体方法包括:清除表土,做好临时排水,平整场地,对段内地表水、地下水及施工用水水质进行取样复测,施工影响范围内的管线进行调查核实和迁改,所述cfg桩2进行室内配比试验,所述碎石桩1和所述cfg桩2成桩工艺性试验等。
45.s2:桩位放样,标记所述碎石桩1和所述cfg桩2的桩心、桩的外轮廓以及加固区边缘线;
46.s3:先施工所述碎石桩1,采用振动沉管成桩法,桩机就位时,机架必须水平稳固,沉管垂直对中,振动沉管至设计深度;
47.具体方法包括:所述碎石桩1施工应从两侧向中间进行,中间的桩隔排隔桩跳打施工;沉管在自由状态下对正桩位,利用锤重及沉管自重徐徐静压1~2m后开动振动锤振动下沉,每下沉0.5~1.0m,留振5~10s,直至设计深度。
48.s4:停振灌料加压成桩;
49.具体方法包括:振动成孔后,停振灌料至满,先振动再开始拔管,边振边拔,每次拔管高度0.5~1.0m,反插深度0.3~0.5m,并停拔振动5~10s。反插数次至桩管内碎石全部投出,第一次投料成桩长度应小于桩管长度的一半。用料斗从空中进行第二次投料直至灌满,振动拔管,数次反插直至管内碎石全部投出。提升桩管高于地面,停止振动,进行孔口投料至地面,反插并补料,数次反复至设计用料用完。反插结束后,将料补满至地面,下落沉管至
桩顶,收紧加压钢丝绳,加压成桩,并控制好桩顶标高。
50.s5:重复s3至s4,直至碎石桩1施工完成;
51.s6:所述碎石桩1成桩质量检验;
52.具体方法包括:所述碎石桩1质量检验内容应包括桩身密实度、单桩承载力试验和桩间土的密实度。桩身密实度采用动力触探进行随机检验,检验数量为桩孔总数的2%,且不少于3根。单桩承载力检验应采用单桩平板载荷实验,检验数量为桩孔总数的2
‰
,且不少于3根。桩间土采用标准贯入试验,试验实测标准贯入锤击数应大于液化临界标准贯入锤击数,检测数量为桩孔总数的2%,且不少于3点,检测位置应设在等边三角形或正方形中心。
53.s7:施工所述cfg桩2,所述cfg桩2采用长螺旋钻孔,桩机就位,调整钻杆垂直地面并对准桩位中心,关闭钻头阀门,向下移动钻头至地面开始钻进,先慢后快,钻至设计深度并停钻;
54.s8:灌注混合料,钻杆芯管充满混合料后开始拔管,匀速拔管至桩顶;
55.s9:重复s7至s8,直至cfg桩2施工完成;
56.s10:所述cfg成桩质量检验;
57.具体方法包括:成桩7天后采用低应变检测桩身完整性,检测数量为总桩数的10%,且不少于3根;成桩28天后,应在桩体中心处、桩长范围内垂直钻孔取芯,观察桩体完整性、均匀性,在桩身上、中、下取不同深度的不少于3个试样做抗压强度试验,检验数量为施工总桩数的2
‰
,且不少于3根;成桩28d后进行强度、单桩承载力试验,检验数量为总桩数的2
‰
,且不少于3根。
58.s11:所述cfg桩2的所述桩帽3施工;
59.具体方法包括:所述桩帽3施工前须先凿除桩头,凿除桩头时必须采取环切工艺。严格按照设计高程放样,标识环切线,采用人工凿开缺口,确保环切作业不会影响桩完整性
60.s12:铺设所述垫层4,分层填筑压实所述路堤本体5填土,直至所述基床底层6顶面;
61.s13:在所述基床底层6顶面上铺一层所述土工布7,分层填筑压实所述堆载预压填土8;
62.具体方法包括:堆载预压高度为3m,在所述基床底层6顶面上铺一层所述土工布7后,以0.4m一层分层填筑分层压实,压实采用中型碾压机具压实,直至填筑完成后,填筑完成后将所述土工布7回折于预压土顶面每侧宽度不小于2.5m,并用土压紧固定,避免预压填料流失、污染路基。
63.s14:达到预压期后,通过沉降观测,并进行工后沉降分析,分析结果满足设计要求时,可分层进行预压荷载填土卸载;
64.s15:卸载完成后进行基床表层9填筑和上部轨道结构施工。
65.其中,在步骤s1中,所述碎石桩1的直径为0.5m,所述碎石桩1应选择有代表性地段进行成桩工艺性试验,确定所述碎石桩1的拔管高度、振密电流、留振时间、分段填碎石量、充盈率等工艺参数,检验成桩效果;所述cfg桩2的直径为0.5m,所述cfg桩2施工前应按设计参数进行室内配比试验,选定混合料配合比。并选择有代表性地段进行成桩工艺性试验,确定所述cfg桩2的混合料施工配合比和坍落度、混合料泵送量、拔管速度、终孔电流等施工工艺和参数。
66.在步骤s3中,所述碎石桩1施工应从两侧向中间进行,中间的桩隔排隔桩跳打施工;要求桩管底板中心与桩位误差≤2cm,沉管垂直度偏差≤1.5h%,并在打桩过程中随时跟踪检查桩管的垂直度。
67.在步骤s4中,桩体材料采用不易风化的干净碎石、卵石、含石砾砂、矿渣等性能稳定的硬质材料,含泥量不得大于5%,粒径宜为20~50mm。
68.在步骤s6中,所述碎石桩1施工结束后,对砂土段应间隔7天以上方可进行质量检验。所述碎石桩1质量检验内容应包括桩身密实度、单桩承载力试验和桩间土的密实度。
69.在步骤s7中,所述cfg桩2施工宜从中间向外围进行,避免后续桩施工对已施工桩的损坏。
70.在步骤s8中,桩体材料采用碎石、石屑或砂、粉煤灰、水泥加水配合而成,桩身水泥采用p.o 42.5级普通硅酸盐水泥,桩身混合料按照c15混凝土配比,混合料28天标准立方体无侧限抗压强度不小于15mpa,掺加优质粉煤灰(等级不低于ⅲ级),粉煤灰掺量为70~90kg/m3。碎石最大粒径不大于25mm。
71.在步骤s10中,所述cfg桩2的桩身质量检验内容应包括桩身完整性、均匀性、桩身强度、单桩或复合地基承载力等。
72.在步骤s11中,所述桩帽3的尺寸为1.1m
×
1.1m,厚0.35m。所述桩帽3施工前须先凿除桩头,凿除桩头时必须采取环切工艺。
73.在步骤s12中,所述垫层4采用0.6m碎石夹二层土工格栅402,垫层4中碎石采用干净且级配良好的砂砾石或碎石,其最大粒径不得大于30mm,含泥量不得大于5%,且不含草根、垃圾等杂质;垫层4中土工格栅402型号为ggr/pet/bw80-80,极限抗拉强度≥80kn/m,单位面积质量≥600g/
㎡
,内孔尺寸为30~60mm,幅宽3~5m,纵横向2%伸长率时的拉伸强度≥36kn/m,纵横向5%伸长率时的拉伸强度≥64kn/m,纵横向标称伸长率≤8%,焊接点极限剥离力≥100kn,抗紫外线强度保持率≥80%。通过铺设垫层4,有利于水平排水的作用,使得施工后土层加快固结,其次可以起到明显的应力扩散作用,从而提高复合地基承载力,减少地基变形。
74.在步骤s13中,预压土填筑横断面边坡坡率为1:1,纵向边坡坡率为1:5。填筑完成后将土工布7回折于预压土顶面每侧宽度不小于2.5m,并用土压紧固定,避免预压填料流失、污染路基;预压土填筑每层厚度不大于0.4m,堆载预压高度为3m,预压期一般宜不小于6个月。
75.以上所揭露的仅为本技术一种或多种较佳实施例而已,不能以此来限定本技术之权利范围,本领域普通技术人员可以理解实现上述实施例的全部或部分流程,并依本技术权利要求所作的等同变化,仍属于本技术所涵盖的范围。
再多了解一些
本文用于企业家、创业者技术爱好者查询,结果仅供参考。