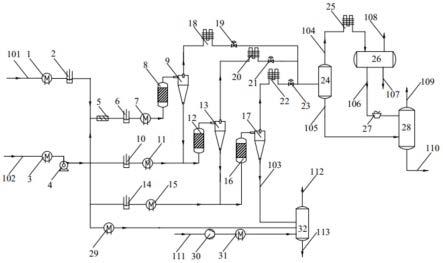
1.本发明涉及稠油改质的技术领域,具体涉及一种利用近临界水、超临界水和超超临界水分级改质稠油的处理方法。
背景技术:
2.全球石油资源中,超过70%的地质储量为稠油资源,随着轻质原油的可采储量不断下降,稠油资源对世界能源安全的逐渐显得更加重要。对于委内瑞拉和加拿大等稠油资源丰富的国家来说,稠油资源的开采、加工和运输技术的开发被高度重视。我国的新疆油田、辽河油田和渤海油田也有大量的稠油资源尚未大规模开采,目前的开采成本高,开采难度大,加工过程存在能耗高、污染环境和掺稀油用量大等问题。稠油资源普遍具有粘度高、硫氮含量高、残炭量高和镍等杂质含量多等特点,这些特点使得稠油在管输和船运之前必须做减粘处理。
3.传统的稠油减粘方法主要有加氢和脱碳两种方式,包括减粘热裂化、加氢裂化和掺稀释剂减粘等。掺稀释剂减粘能够显著降低稠油的粘度,但是需要消耗大量的稀释剂或轻质油品,而很多稠油油田缺少稀释剂或轻质油品,同时,掺入稀释剂之后会增大管道输送量,增大输送成本(重油供氢减粘改质技术概述.化工进展2014,33,128-133;重油减黏热裂化工艺研究进展.化学与黏合2015,37,218-221)。
4.早在1982年,加拿大学者hyne率先提出水热裂解反应的概念,发现油砂能与高温水蒸汽发生脱硫、脱氮、加氢、开环和水煤气转换等一系列反应。进一步研究发现稠油中发生水热裂解的化合物主要是有机硫化物,高含硫原油的水热裂解效果更好(hyne j b,greidanus j w.aquathermolysis of heavy oil[j].proceeding of the 2nd international conference on heavy crude and tar sands,1982,12(7):189-193)。
[0005]
自上世纪九十年代以来,超临界水技术在稠油改质领域得到了广泛关注,主要因为超临界水与有机质的互溶性强,使传统的多相反应转化为均相反应,增加了反应速度,传质能力强,抑制或减轻热解反应中常见的结焦或积炭现象,同时显著改善产物的选择性和收率。超临界水处理油品可以实现初步改质,脱除部分的金属、残炭、硫和氮等杂质。超临界水对一般的油品或稠油有较好的改质效果,但是,特稠油中含有大量的多环结构,沥青质分子量巨大,在常规的超临界水裂解反应中难以实现快速分解转化为轻质油。用超临界水处理过的超稠油粘度偏高,仍然需要掺稀或改质后才能管输。
[0006]
cn109097101运行超临界水石油提质加工系统,向上升流超临界水反应器中引入石油原料、水和辅助原料,提质加工和脱硫的石油产品与石油原料之间的重力差在8度以上。工艺采用超临界水和辅助原料对石油原料进行提质加工,以催化材料、烷烃硫和轻质烃等为辅助原料。cn108495915a公开了一种用于由包含长链芳族化合物的石油基组合物制备链烷烃的方法,包括将超临界水与石油基组合物混合,依次经由在超临界压力和温度下运转的第一反应器和第二反应器发生裂化反应,生产包含链烷烃和短链芳族化合物。上述两个专利中,利用超临界水对石油直接进行改质,反应时间长易造成结焦堵塞反应器,若控制
反应在较短时间内完成会影响转化率和改质效果。
[0007]
cn104039434公开了利用含有水和起始烃的引物流来防止设备工艺管线的堵塞,同时用超临界水改质石油原料的方法,反应器维持在介于380℃至550℃的温度,石油原料在反应器中的停留时间介于约10秒至60分钟。在实施例中,采用所述超临界改质工艺处理阿拉伯重质原油,两个串联连接的反应器的温度控制在390℃,在操作过程中,维持约250bar的压力,最终产物的总硫含量比阿拉伯重质原油原料少30%,并且总金属含量(即,镍和钒的含量之和)降至初始含量的85%,产物的api比重上升了5。此专利通过利用含有水和起始烃的引流物来防止管线堵塞,只是预防了装置正常运转之前可能造成的堵塞,并未解决超临界改质中形成焦碳颗粒造成管线或反应器堵塞的问题。
[0008]
可见,关于超临界水热解改质稠油技术,尚无利用近临界水、超临界水和超超临界水的不同热解作用对稠油进行分级处理的工艺技术,并且通过分级处理,缩短了每级反应的停留时间,控制了生焦量。
技术实现要素:
[0009]
本发明的目的是提供一种利用热解反应进行稠油改质的方法,具体地说,是一种利用近临界水、超临界水和超超临界水分级热解稠油改质的方法。该方法通过三级水热解改质工艺,依次通过串联的三个反应器对稠油进行水热解反应,发生烷基侧链的断链反应和多环芳烃的缩合反应等,可以大幅度轻质化转化稠油,使其粘度显著降低,并且产品油收率高,稠油中的硫、镍和钒等杂质含量也大幅减少,从而提高稠油改质现有技术的经济性。
[0010]
本发明提供的分级改质稠油的方法,包括:
[0011]
1)将稠油加热到60~100℃,增压到1~5mpa,输送至混合器,将去离子水加热到60~80℃并增压到1~5mpa后,分成四路,分别为一路水、二路水、三路水和四路水,一路水的质量流量为稠油的质量流量的0.5~5倍,稠油与一路水在混合器内形成油水混合液,将油水混合液增压到5~22.1mpa,加热到200~374℃,然后输送到近临界水反应器内,稠油在近临界水作用下发生热解反应,稠油在近临界水反应器内的停留时间为10s~30min,近临界水反应器排出流体被旋流分离,得到气相流和重组分油,气相流降温到240~260℃,降压到14~16mpa后输送至热高压分离器;
[0012]
2)将步骤1)得到的二路水增压到22.1~30mpa,加热到374~450℃后,与步骤1)中旋分出的重组分油混合,输送到超临界水反应器内,二路水的质量流量为重组分油的质量流量的0.5~5倍,在超临界水反应器内注入供氢剂和催化剂,重组分油在超临界水、供氢剂和催化剂的作用下发生热解反应,重组分油在超临界水反应器内的停留时间为10s~30min,对超临界水反应器排出流体进行旋流分离,得到气相流和混有催化剂的超重组分油,气相流降温到240~260℃,降压到14~16mpa后输送至热高压分离器;
[0013]
3)将步骤1)得到的三路水增压30~50mpa,加热到450~600℃后,与步骤2)中旋分出的混有催化剂的超重组分油混合,输送到超超临界水反应器内,三路水的质量流量为超重组分油的质量流量的0.5~5倍,超重组分油在超超临界水的作用下发生热解反应,超重组分油在超超临界水反应器内的停留时间为10s~30min,对超超临界水反应器排出流体进行旋流分离,得到气相流和混有催化剂的残渣,气相流降温到240~260℃和降压到14~16mpa后,输送至热高压分离器;
[0014]
4)步骤1)所述的气相流、步骤2)所述的气相流和步骤3)所述的气相流经热高压分离器分离为高分气和热高分油,热高分油连通至冷低压分离器,高分气降温至40~60℃后连通至冷高压分离器,在冷高压分离器内分离为冷高分油、裂化气和高分水,冷高分油降压至2~4mpa后连通至冷低压分离器,冷低压分离器排出裂化气和改质油;
[0015]
5)步骤1)得到的四路水加热至650~1200℃后输送至气化器的水蒸气入口,氧气增压至0.1~1.2mpa,输送至气化器的氧气入口,步骤3)得到的混有催化剂的残渣输送至气化器的原料入口,在气化器内烧焦气化生成合成气。
[0016]
在上述改质方法中,根据不同稠油的性质特点,该方法不限于利用近临界水、超临界水和超超临界水三级热解反应改质以及与烧焦气化工艺组合处理稠油,也不限于利用近临界水热解反应改质处理稠油,也不限于利用超临界水热解反应改质处理稠油,也不限于利用超超临界水热解反应改质处理稠油,也不限于利用近临界水和超临界水两级热解反应改质处理稠油,也不限于利用近临界水和超超临界水两级热解反应改质处理稠油,也不限于利用超临界水和超超临界水三级热解反应改质处理稠油,也不限于利用近临界水热解反应改质以及与烧焦气化工艺组合处理稠油,也不限于利用超临界水热解反应改质以及与烧焦气化工艺组合处理稠油,也不限于利用超超临界水热解反应改质以及与烧焦气化工艺组合处理稠油,也不限于利用近临界水和超临界水两级热解反应改质以及与烧焦气化工艺组合处理稠油,也不限于利用近临界水和超超临界水两级热解反应改质以及与烧焦气化工艺组合处理稠油,也不限于利用超临界水和超超临界水三级热解反应改质以及与烧焦气化工艺组合处理稠油。
[0017]
在上述改质方法中,优选地,步骤1)所述的近临界水反应器内的温度为350~374℃,压力为18~22mpa。
[0018]
在上述改质方法中,优选地,步骤1)所述的一路水的质量流量为所述的稠油的质量流量的1~2倍。
[0019]
在上述改质方法中,优选地,步骤1)所述的稠油在近临界水反应器内的停留时间为1~5min。
[0020]
在上述改质方法中,优选地,步骤2)所述的超临界水反应器内的温度为400~420℃,压力为22.1~25mpa。
[0021]
在上述改质方法中,优选地,步骤2)所述的二路水的质量流量为所述的重组分油的质量流量的1~2倍。
[0022]
在上述改质方法中,优选地,步骤2)所述的重组分油在超临界水反应器内的停留时间为2~10min。
[0023]
在上述改质方法中,优选地,步骤3)所述的超超临界水反应器内的温度为450~470℃,压力为30~35mpa。
[0024]
在上述改质方法中,优选地,步骤3)所述的三路水的质量流量为所述的超重组分油的质量流量的1~2倍。
[0025]
在上述改质方法中,优选地,步骤3)所述的超重组分油在超超临界水反应器内的停留时间为2~10min。
[0026]
在上述改质方法中,优选地,步骤2)所述的供氢剂为氢气、甲烷、合成气中的一种或几种。
[0027]
在上述改质方法中,优选地,步骤2)所述的供氢剂为甲酸、甲苯、环烷基馏分油中的一种或几种,加入质量比为供氢剂:油=0.01~1:1。所述的环烷基馏分油为四氢萘、十氢萘、二氢蒽、环烷基石油馏分中的一种或几种。
[0028]
在上述改质方法中,优选地,步骤2)所述的催化剂为氢氧化钾、氢氧化钠、过渡金属的氧化物、过渡金属的硫酸盐或过渡金属的硫化物中的一种或几种,加入质量比为供氢剂:油=0.001~0.5:1。优选地,所述的过渡金属为v、fe、co、ni、cu或mo中的一种或几种。
[0029]
本发明改质方法处理稠油生产的改质油的产品油的收率为≥85%,优选≥90%。
[0030]
本发明方法与现有技术相比,其有益效果是:本发明的处理方法能够利用近临界水、超临界水和超超临界水与稠油形成混合均相,抑制缩合反应的进行和结焦现象的发生。利用多级旋分和残渣气化技术可以解决生成的焦炭等固体颗粒易造成管线堵塞的问题。可以最大限度实现稠油轻质化转化,生成更多的轻质油品,其粘度显著降低,可以满足管道输送和船运要求。本发明改质方法针对高粘、密度大和高凝的稠油,结合近临界水、超临界水和超超临界水三级热解改质工艺,可以最大限度的转化稠油和超稠油,生成更多的轻质油品,达到大幅度转化稠油和超稠油的目的,可以满足管道输送和船运要求,粘度显著降低,同时脱除稠油中的部分硫杂质,镍和钒等金属杂质,对炼油加工环节催化剂的毒害作用减小。
附图说明
[0031]
图1为本发明方法中分级改质稠油的方法的一个实施方案的总体示意图。
[0032]
附图标记说明
[0033]
图1中,1为原料预热炉,2为原料增压泵,3为水预热炉,4为水增压泵,5为混合器,6为近临界水增压泵,7为近临界水加热器,8为近临界水反应器,9为近临界旋流分离器,10为超临界水增压泵,11为超临界水加热器,12为超临界水反应器,13为超临界水旋流分离器,14为超超临界水增压泵,15为超超临界水加热器,16为超超临界水反应器,17为超超临界水旋流分离器,18、20和22为冷却器,19、21和23为背压阀,24为热高压分离器,25为高压空冷器,26为冷高压分离器,27为能量回收透平,28为冷低压分离器,29为水加热器,30为压缩机,31为气体加热器,32为气化器
[0034]
101为稠油原料流,102为去离子水流,103为混有催化剂的残渣,104为高分气,105为热高分油,106为冷高分油,107为高分水,108和109为裂化气,110为改质油,111为氧气,112为合成气,113为炉渣
具体实施方式
[0035]
本发明一种分级改质稠油的方法针对稠油和特稠油高粘、密度大和重组分多的组成特点,采用三级水热解改质工艺,利用近临界水、超临界水和超超临界水分级热解稠油改质。在此过程中,以稠油为原料,其组成特点是胶质和沥青质含量高,还含有硫、残炭、镍和钒等杂质,常温下流动性质差,必须掺稀或改质减粘后才能管输。
[0036]
如果将稠油进行改质减粘,首先需要对稠油原料流和去离子水流进行加热和增压,因为常温下的稠油粘度大,进料时粘滞力大,稠油加热后可以从一定程度上降低稠油的粘度。将稠油加热到60~100℃,增压到1~5mpa,输送至混合器。将去离子水加热到60~80
℃并增压到1~5mpa后,分成四路,分别为一路水、二路水、三路水和四路水。去离子水加热的目的是使去离子水和稠油更易混合。一路水的质量流量为稠油的质量流量的0.5~5倍。所述的一路水的质量流量优选为所述的稠油的质量流量的1~2倍。
[0037]
稠油与一路水在混合器内形成油水混合液,将油水混合液增压到5~22.1mpa,加热到200~374℃,然后输送到近临界水反应器内,稠油在近临界水作用下发生热解反应,稠油在近临界水反应器内的停留时间为10s~30min。所述的稠油在近临界水反应器内的停留时间优选为1~5min。近临界水反应器排出流体被旋流分离,得到气相流和重组分油,气相流降温到240~260℃,降压到14~16mpa后输送至热高压分离器;
[0038]
将二路水增压到22.1~30mpa,加热到374~450℃后,与旋分出的重组分油混合,输送到超临界水反应器内。二路水的质量流量为重组分油的质量流量的0.5~5倍。所述的二路水的质量流量为所述的重组分油的质量流量的1~2倍。在超临界水反应器内注入供氢剂和催化剂,重组分油在超临界水、供氢剂和催化剂的作用下发生热解反应。所述的超临界水反应器内的温度优选为400~420℃,压力优选为22.1~25mpa。供氢剂和催化剂可以起到抑制结焦的作用,而且难以发生反应的多环芳烃等组分在超超临界水作用下可以发生热解反应。重组分油在超临界水反应器内的停留时间为10s~30min。所述的重组分油在超临界水反应器内的停留时间优选为2~10min。对超临界水反应器排出流体进行旋流分离,得到气相流和混有催化剂的超重组分油。气相流降温到240~260℃,降压到14~16mpa后输送至热高压分离器。
[0039]
将三路水增压30~50mpa,加热到450~600℃后,与混有催化剂的超重组分油混合,输送到超超临界水反应器内。三路水的质量流量为超重组分油的质量流量的0.5~5倍。所述的三路水的质量流量为所述的超重组分油的质量流量的1~2倍。超临界水反应器内的温度为450~600℃,压力为30~50mpa。所述的超超临界水反应器内的温度优选为450~470℃,压力优选为30~35mpa。超重组分油在超超临界水的作用下发生热解反应,超重组分油在超超临界水反应器内的停留时间为10s~30min。所述的超重组分油在超超临界水反应器内的停留时间优选为2~10min。对超超临界水反应器排出流体进行旋流分离,得到气相流和混有催化剂的残渣。气相流降温到240~260℃和降压到14~16mpa后,输送至热高压分离器,被分离为高分气和热高分油。热高分油连通至冷低压分离器,高分气降温至40~60℃后连通至冷高压分离器,在冷高压分离器内分离为冷高分油、裂化气和高分水。冷高分油经能量回收透平或角阀降压至2~4mpa后连通至冷低压分离器,冷低压分离器排出裂化气和改质油。
[0040]
四路水加热至650~1200℃后输送至气化器的水蒸气入口,氧气增压至0.1~1.2mpa,输送至气化器的氧气入口,混有催化剂的残渣输送至气化器的原料入口,在气化器内烧焦气化生成合成气。
[0041]
根据不同稠油的性质特点,上述方法不限于利用近临界水、超临界水和超超临界水三级热解反应改质以及与烧焦气化工艺组合处理稠油,也不限于利用近临界水热解反应改质处理稠油,也不限于利用超临界水热解反应改质处理稠油,也不限于利用超超临界水热解反应改质处理稠油,也不限于利用近临界水和超临界水两级热解反应改质处理稠油,也不限于利用近临界水和超超临界水两级热解反应改质处理稠油,也不限于利用超临界水和超超临界水三级热解反应改质处理稠油,也不限于利用近临界水热解反应改质以及与烧
焦气化工艺组合处理稠油,也不限于利用超临界水热解反应改质以及与烧焦气化工艺组合处理稠油,也不限于利用超超临界水热解反应改质以及与烧焦气化工艺组合处理稠油,也不限于利用近临界水和超临界水两级热解反应改质以及与烧焦气化工艺组合处理稠油,也不限于利用近临界水和超超临界水两级热解反应改质以及与烧焦气化工艺组合处理稠油,也不限于利用超临界水和超超临界水两级热解反应改质以及与烧焦气化工艺组合处理稠油。
[0042]
本发明所述的供氢剂优选为氢气、甲烷、合成气中的一种或几种。
[0043]
本发明所述的供氢剂还优选为甲酸、甲苯、环烷基馏分油中的一种或几种,加入质量比为供氢剂:油=0.01~1:1。所述的环烷基馏分油为四氢萘、十氢萘、二氢蒽、环烷基石油馏分中的一种或几种。
[0044]
本发明所述的催化剂为氢氧化钾、氢氧化钠、过渡金属的氧化物、过渡金属的硫酸盐、过渡金属的硫化物中的一种或几种,加入质量比为供氢剂:油=0.001~0.5:1。所述的过渡金属优选为v、fe、co、ni、cu、mo中的一种或几种。
[0045]
下面结合附图详细说明本发明。
[0046]
图1中,将稠油原料流101经原料预热炉1加热到60~100℃,经原料增压泵2增压输送至混合器5。将去离子水流102经水预热炉3加热到60~80℃,并经水增压泵4增压后,分成四路,分别为一路水、二路水、三路水和四路水。一路水的质量流量为稠油的质量流量的0.5~5倍。稠油与一路水在混合器5内形成油水混合液,经过近临界水增压泵6增压和近临界水加热器7加热,油水混合液输送到近临界水反应器8内,近临界水反应器8内的温度为200~374℃,压力为5~22.1mpa。稠油在近临界水作用下发生热解反应,稠油在近临界水反应器8内的停留时间为10s~30min,近临界水反应器8排出流体在近临界旋流分离器内被旋流分离,得到气相流和重组分油。气相流经冷却器18降温到240~260℃,经背压阀19降压到14~16mpa后输送至热高压分离器24。
[0047]
二路水经超临界水增压泵10增压和超临界水加热器11加热后,与重组分油混合,输送到超临界水反应器12内。二路水的质量流量为重组分油的质量流量的0.5~5倍。在超临界水反应器12内注入供氢剂和催化剂,超临界水反应器12内的温度为374~450℃,压力为22.1~30mpa。重组分油在超临界水、供氢剂和催化剂的作用下发生热解反应,重组分油在超临界水反应器12内的停留时间为10s~30min。超临界水反应器12排出流体在超临界水旋流分离器13内进行旋流分离,得到气相流和混有催化剂的超重组分油。气相流降温到240~260℃,降压到14~16mpa后输送至热高压分离器24。
[0048]
三路水经超超临界水增压泵14增压和超超临界水加热器15加热后,与混有催化剂的超重组分油混合,输送到超超临界水反应器16内。三路水的质量流量为超重组分油的质量流量的0.5~5倍。超临界水反应器16内的温度为450~600℃,压力为30~50mpa。超重组分油在超超临界水的作用下发生热解反应,超重组分油在超超临界水反应器16内的停留时间为10s~30min。对超超临界水反应器16排出流体超超临界水旋流分离器17内进行旋流分离,得到气相流和混有催化剂的残渣103。气相流降温到240~260℃和降压到14~16mpa后,输送至热高压分离器24。
[0049]
降温和降压后的三路气相流经热高压分离器24分离为高分气104和热高分油105,热高分油105连通至冷低压分离器28,高分气104经过高压空冷器25降温至40~60℃后连通
至冷高压分离器26,在冷高压分离器26内分离为冷高分油106、裂化气108和高分水107,冷高分油106经能量回收透平27降压后连通至冷低压分离器28。冷低压分离器28排出裂化气109和改质油110。四路水经过水加热器29加热后输送至气化器32的水蒸气入口,氧气经压缩机30增压和经气体加热器31加热后,输送至气化器32的氧气入口,混有催化剂的残渣103输送至气化器的原料入口,在气化器32内烧焦气化生成合成气112,气化器32下方排出炉渣113。
[0050]
下面通过实施例进一步说明本发明,但本发明并不限于此。
[0051]
实施例1
[0052]
按本发明方法分级热解稠油改质。使用一套立管式三级热解反应设备,它由三个热解反应器串联构成,第一级热解反应器为近临界水反应器,第二级热解反应器为超临界水反应器,第三级热解反应器为超超临界水反应器,每个热解反应器后各有一个旋流分离器。热解反应器主体为单根的立管,从下端入口进料,从上端出口出料。通过三个背压阀分别控制三个热解反应器内的压力。
[0053]
接入去离子水流,去离子水加热温度为60℃。控制近临界水反应器的温度为340℃,压力为10mpa,超临界水反应器的温度为400℃,压力为23mpa,超超临界水反应器的温度为460℃,压力为31mpa。以油砂沥青为原料,油品性质见表1。当系统压力和温度稳定之后,稠油加热温度达到60℃,开始输入稠油原料,稠油的质量流量为30kg/h,一路水的质量流量为15kg/h,二路水的质量流量为重组分油的质量流量的0.5倍,三路水的质量流量为超重组分油的质量流量的0.5倍。稠油在近临界水反应器内的停留时间为1min,重组分油在超临界水反应器内的停留时间为1min,超重组分油在超超临界水反应器内的停留时间为1min。超临界水反应器内使用的供氢剂为四氢萘,加入质量比为四氢萘:油=0.2:1。超临界水反应器内使用的催化剂为油酸镍,剂油比为0.05:1。产品分析结果见表3。
[0054]
实施例2
[0055]
按本发明方法分级热解稠油改质。使用一套立管式三级热解反应设备,它由三个热解反应器串联构成,第一级热解反应器为近临界水反应器,第二级热解反应器为超临界水反应器,第三级热解反应器为超超临界水反应器,每个热解反应器后各有一个旋流分离器。热解反应器主体为单根的立管,从下端入口进料,从上端出口出料。通过三个背压阀分别控制三个热解反应器内的压力。
[0056]
与实施例1的不同之处在于,同时接入去离子水流和稠油原料流,稠油加热温度60℃,去离子水加热温度为80℃。以油砂沥青为原料,油品性质见表1。控制近临界水反应器的温度为340℃,压力为10mpa,超临界水反应器的温度为400℃,压力为23mpa,超超临界水反应器的温度为460℃,压力为31mpa。稠油的质量流量为30kg/h,一路水的质量流量为15kg/h,二路水的质量流量为重组分油的质量流量的0.5倍,三路水的质量流量为超重组分油的质量流量的0.5倍。稠油在近临界水反应器内的停留时间为1min,重组分油在超临界水反应器内的停留时间为1min,超重组分油在超超临界水反应器内的停留时间为1min。超临界水反应器内使用的供氢剂为氢气,氢气流量为80m3/h。超临界水反应器内使用的催化剂为硫酸铁,剂油比为0.03:1。产品分析结果见表3。
[0057]
实施例3
[0058]
按本发明方法分级热解稠油改质。使用一套立管式三级热解反应设备,它由三个
热解反应器串联构成,第一级热解反应器为近临界水反应器,第二级热解反应器为超临界水反应器,第三级热解反应器为超超临界水反应器,每个热解反应器后各有一个旋流分离器。热解反应器主体为单根的立管,从下端入口进料,从上端出口出料。通过三个背压阀分别控制三个热解反应器内的压力。
[0059]
通入去离子水流,去离子水加热温度为70℃。控制近临界水反应器的温度为350℃,压力为16mpa,超临界水反应器的温度为420℃,压力为27mpa,超超临界水反应器的温度为480℃,压力为35mpa。以减渣为原料,油品性质见表1。当系统压力和温度稳定之后,稠油加热温度达到80℃,开始输入稠油原料,稠油的质量流量为30kg/h,一路水的质量流量为30kg/h,二路水的质量流量为重组分油的质量流量的1.5倍,三路水的质量流量为超重组分油的质量流量的1.5倍。稠油在近临界水反应器内的停留时间为20min,重组分油在超临界水反应器内的停留时间为15min,超重组分油在超超临界水反应器内的停留时间为13min。超临界水反应器内使用的供氢剂为甲苯,加入比例为甲苯:油=0.4:1。超临界水反应器内使用的催化剂为硫化镍,剂油比为0.01:1。产品分析结果见表3。
[0060]
实施例4
[0061]
按本发明方法分级热解稠油改质。使用一套立管式三级热解反应设备,它由三个热解反应器串联构成,第一级热解反应器为近临界水反应器,第二级热解反应器为超临界水反应器,第三级热解反应器为超超临界水反应器,每个热解反应器后各有一个旋流分离器。热解反应器主体为单根的立管,从下端入口进料,从上端出口出料。通过三个背压阀分别控制三个热解反应器内的压力。
[0062]
以油砂沥青为原料,油品性质见表1。接入去离子水流和稠油原料流,稠油加热温度100℃,去离子水加热温度为70℃。控制近临界水反应器的温度为360℃,压力为21mpa,超临界水反应器的温度为430℃,压力为25mpa,超超临界水反应器的温度为500℃,压力为35mpa。稠油的质量流量为30kg/h,一路水的质量流量为30kg/h,二路水的质量流量为重组分油的质量流量的2倍,三路水的质量流量为超重组分油的质量流量的2倍。稠油在近临界水反应器内的停留时间为5min,重组分油在超临界水反应器内的停留时间为5min,超重组分油在超超临界水反应器内的停留时间为5min。超临界水反应器内使用的供氢剂为环烷基石油馏分,加入比例为环烷基石油馏分:油=0.3:1。超临界水反应器内使用的催化剂为氢氧化钾,剂油比为0.03:1。产品分析结果见表3。
[0063]
表1油品原料性质
[0064][0065]
表2操作条件
[0066][0067]
表3油品改质后数据
[0068]
项目实施例1实施例2实施例3实施例4降黏率,%98.799.499.599.9气相产物,wt%5.05.76.17.4轻油,wt%38.246.147.055.8重油,wt%56.848.246.936.8
再多了解一些
本文用于企业家、创业者技术爱好者查询,结果仅供参考。