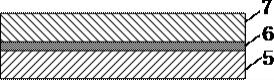
1.本发明涉及半导体工艺技术领域,具体涉及一种磁铁阵列加工方法。
背景技术:
2.在霍尔传感器中,半导体霍尔传感器用来探测垂直于芯片平面的磁场强度,如需要准确的探测位置,则需要微型的永磁体磁源来标定位置。通常切割成小块的永磁体(0.1-1毫米尺度)镶嵌或者粘贴在机加工的导轨中或者标定的位置,贴近用来读取磁场信号的半导体霍尔传感器。这种方式会有定位精度低,机加工难度大耗时多,磁间隙不均匀的问题。而高精度的位置传感器和采用差分方式的霍尔传感器阵列对磁铁阵列的分布精度有更高的微米级的误差要求。
3.现有的磁铁定位方式与霍尔传感器所需要的精度不匹配,这导致霍尔传感器中所需要的磁铁阵列无法满足精度上的要求,进而导致测量精度不够的问题。
技术实现要素:
4.因此,本发明要解决的技术问题是由于现有技术中磁铁阵列定位加工精度不够导致霍尔传感器的测量精度不够的问题,从而提供一种磁铁阵列加工方法。
5.本发明实施例的一方面,提供了一种磁铁阵列加工方法,包括:在晶圆掩膜版上生成第一隔离层;在所述第一隔离层上涂覆第一光刻胶层;对所述第一光刻胶层进行光刻,得到用于进行磁铁颗粒定位的图案,其中,所述图案包括大小相同且均匀分布的凹槽;对所述图案暴露出的第一隔离层刻蚀至所述晶圆掩膜版;对暴露出晶圆掩膜版的位置进行深刻,获得带有刻槽的晶圆掩膜版,其中每个刻槽与所述凹槽的位置对应;将磁铁颗粒填充到每个刻槽中,得到带有磁铁阵列的晶圆,其中,所有磁铁颗粒的极性方向相同。
6.可选地,所述将磁铁颗粒填充到每个刻槽中,得到带有磁铁阵列的晶圆,包括:制作磁铁薄片;将所述磁铁薄片贴附在衬底上,得到待加工的磁铁层;对所述磁铁层带有磁铁薄片的一侧进行刻蚀,获得带有磁铁凸起的磁铁层,其中,所述磁铁凸起的数量与所述刻槽的数量相等,并且位置相对应;将所述带有磁铁凸起的磁铁层与所述带有刻槽的晶圆掩膜版对齐,使得每个磁铁凸起对应到相应的刻槽上,将所述带有磁铁凸起的磁铁层与所述带有刻槽的晶圆掩膜版压紧贴合;将所述衬底去除,得到所述带有磁铁阵列的晶圆。
7.可选地,所述对所述磁铁层带有磁铁薄片的一侧进行刻蚀,获得带有磁铁凸起的磁铁层,包括:在磁铁层带有磁铁薄片的一侧生成第二隔离层;在所述第二隔离层上涂覆第二光刻胶层;对所述第二光刻胶层进行光刻,得到用于刻蚀出磁铁凸起的图案;对所述用于刻蚀出磁铁凸起的图案暴露出的第二隔离层刻蚀至所述磁铁层;对暴露出所述磁铁层的位置进行深刻,获得带有磁铁凸起的磁铁层。
8.可选地,所述制作磁铁薄片,包括对所述磁铁薄片在厚度方向进行极化。
9.可选地,所述磁铁凸起的侧壁坡度与所述刻槽的侧壁坡度相应。
10.可选地,所述将所述磁铁薄片贴附在衬底上,得到待加工的磁铁层,包括:将所述
磁铁薄片用可剥离胶水粘贴在具有相同尺寸的衬底上;所述将所述衬底去除包括:将所述可剥离胶水溶解,然后剥离所述衬底。
11.可选地,所述将磁铁颗粒填充到每个刻槽中,得到带有磁铁阵列的晶圆,包括:对极化后的磁铁进行加工,得到磁铁棒;对所述磁铁棒进行切割,得到多个磁铁颗粒;利用精密机械将所述磁铁颗粒填充到所述刻槽内,得到带有磁铁阵列的晶圆。
12.可选地,在对所述磁铁棒进行切割,得到多个磁铁颗粒之后,还包括:将所述磁铁颗粒极性一致地平放在基底上;向磁铁颗粒上表面涂覆抗刻蚀的涂层;对所述磁铁颗粒进行刻蚀,得到上宽下窄的磁铁颗粒,其中,刻蚀后的磁铁颗粒的侧壁坡度与所述刻槽的坡度对应。
13.可选地,所述磁铁棒的直径为100-1000微米,所述磁铁颗粒的长度为100-1000微米。
14.可选地,在将磁铁颗粒填充到每个刻槽中之后,还包括:对晶圆掩膜版带有磁铁颗粒的一侧进行打磨抛光。
15.根据本发明实施例,通过采用半导体工艺,光刻形成用于进行磁铁颗粒定位的凹槽,再利用高纵深比深刻实现容纳磁铁颗粒的刻槽的刻蚀,其无论是磁铁颗粒定位和间距以及深度均能够达到微米级别,提高了磁铁阵列中磁铁颗粒定位加工精度,进而能够提高相应的霍尔传感器的测量精度。
附图说明
16.为了更清楚地说明本发明具体实施方式或现有技术中的技术方案,下面将对具体实施方式或现有技术描述中所需要使用的附图作简单地介绍,显而易见地,下面描述中的附图是本发明的一些实施方式,对于本领域普通技术人员来讲,在不付出创造性劳动的前提下,还可以根据这些附图获得其他的附图。
17.图1为本发明实施例中磁铁阵列加工方法的一个具体示例的流程图;图2为本发明实施例中磁铁阵列加工过程中晶圆掩膜版的结构示意图;图3为本发明实施例中磁铁阵列加工过程中获得第一隔离层后的结构示意图;图4为本发明实施例中磁铁阵列加工过程中获得第一光刻胶层后的结构示意图;图5为本发明实施例中磁铁阵列加工过程中获得凹槽阵列后的结构示意图;图6为本发明实施例中磁铁阵列加工过程中刻蚀第一隔离层后的结构示意图;图7为本发明实施例中磁铁阵列加工过程中带有刻槽的晶圆掩膜版的结构示意图;图8为本发明实施例中磁铁阵列加工过程中再次刻蚀第一隔离层后的结构示意图;图9为本发明实施例中磁铁阵列加工过程中填充磁铁颗粒后的结构示意图;图10为本发明实施例中磁铁阵列加工过程中打磨后的结构示意图;图11为本发明实施例中一种磁铁颗粒加工过程中磁铁薄片贴附在衬底上的结构示意图;图12为本发明实施例中一种磁铁颗粒加工过程中获得第二光刻胶层后的结构示意图;
图13为本发明实施例中一种磁铁颗粒加工过程中刻蚀第二光刻胶层后的结构示意图;图14为本发明实施例中一种磁铁颗粒加工过程中刻蚀部分磁铁层后的结构示意图;图15为本发明实施例中一种磁铁颗粒加工过程中带有磁铁凸起的磁铁层的结构示意图;图16为本发明实施例中一种磁铁颗粒加工过程中带有刻槽的晶圆掩膜版与带有磁铁凸起的磁铁层对齐贴合后的结构示意图;图17为本发明实施例中一种可选的带刻槽的晶圆掩膜版的示意图;图18为本发明实施例中磁铁棒的示意图;图19为本发明实施例中另一种磁铁颗粒刻蚀过程中将磁铁颗粒摊平于基底上的示意图;图20为本发明实施例中另一种磁铁颗粒刻蚀过程中获得磁铁颗粒上宽下窄的结构示意图;图21为本发明实施例中将磁铁颗粒放置于每一个对应的凹槽内的结构示意图。
具体实施方式
18.下面将结合附图对本发明的技术方案进行清楚、完整地描述,显然,所描述的实施例是本发明一部分实施例,而不是全部的实施例。基于本发明中的实施例,本领域普通技术人员在没有做出创造性劳动前提下所获得的所有其他实施例,都属于本发明保护的范围。
19.在本发明的描述中,需要说明的是,术语“中心”、“上”、“下”、“左”、“右”、“竖直”、“水平”、“内”、“外”等指示的方位或位置关系为基于附图所示的方位或位置关系,仅是为了便于描述本发明和简化描述,而不是指示或暗示所指的装置或元件必须具有特定的方位、以特定的方位构造和操作,因此不能理解为对本发明的限制。此外,术语“第一”、“第二”、“第三”仅用于描述目的,而不能理解为指示或暗示相对重要性。
20.在本发明的描述中,需要说明的是,除非另有明确的规定和限定,术语“安装”、“相连”、“连接”应做广义理解,例如,可以是固定连接,也可以是可拆卸连接,或一体地连接;可以是机械连接,也可以是电连接;可以是直接相连,也可以通过中间媒介间接相连,还可以是两个元件内部的连通,可以是无线连接,也可以是有线连接。对于本领域的普通技术人员而言,可以具体情况理解上述术语在本发明中的具体含义。
21.此外,下面所描述的本发明不同实施方式中所涉及的技术特征只要彼此之间未构成冲突就可以相互结合。
22.本发明实施例提供了一种磁铁阵列加工方法,具体用于加工用于霍尔传感器的磁铁阵列。具体地,如图1所示,该加工方法包括:步骤s101,在晶圆掩膜版上生成第一隔离层。
23.晶圆掩膜版可以是通过选取特定晶向的单晶硅片,然后设计制作成的掩膜版(photo mask),如图2所示。然后在该掩膜版上采用涂覆或者沉积的方式,得到第一隔离层,如图3所示。该隔离层可以是金属、氧化物或者聚合物等,用来隔离刻蚀液或者等离子体的侵蚀。
24.步骤s102,在所述第一隔离层上涂覆第一光刻胶层。
25.在生成第一隔离层之后,再在上面涂覆第一光刻胶层。如图4所示,晶圆掩膜版1上依次生成第一隔离层2和第一光刻胶层3。
26.步骤s103,对所述第一光刻胶层进行光刻,得到用于进行磁铁颗粒定位的图案,其中,所述图案包括大小相同且均匀分布的凹槽。
27.利用光刻板对第一光刻胶层进行曝光和显影,实现光刻胶层的光刻作用,从而得到相应的光刻结构,如图5所示,图案具体包括多个大小相等且均匀分布的凹槽4,形成的凹槽阵列(图中仅仅示出了部分结构),该凹槽4的位置就是后续需要嵌入磁铁颗粒的位置。该凹槽也可以称为定位凹槽。
28.步骤s104,对所述图案暴露出的第一隔离层刻蚀至所述晶圆掩膜版。具体地,如图6所示,刻蚀第一隔离层,直至露出晶圆掩膜版。
29.步骤s105,对暴露出晶圆掩膜版的位置进行深刻,获得带有刻槽的晶圆掩膜版,其中每个刻槽与所述凹槽的位置对应。
30.在刻蚀出晶圆掩膜版之后,再用刻蚀液按照特定晶向进行刻蚀,或者用大功率等离子体(induction coupled plasma rie)对晶圆进行高纵深比深刻,刻蚀深度可以是100-1000微米,从而获得带有刻槽的晶圆掩膜版。如图6和7所示,刻槽的位置与上述凹槽的位置保持一致。可选地,深刻可以采用成熟的mems制作工艺加工高纵深比,大深度的刻蚀槽。进一步地,刻蚀晶圆掩膜版上的所有第一隔离层,直至露出所有晶圆掩膜版,如图8所示。
31.步骤s106,将磁铁颗粒填充到每个刻槽中,得到带有磁铁阵列的晶圆,其中,所有磁铁颗粒的极性方向相同。
32.在刻蚀出刻槽之后,将加工完成的磁铁颗粒填充到相应的刻槽中,从而得到带有磁铁整列的晶圆。填充到刻槽中的磁铁颗粒的极性方向相同。
33.具体地,可将晶圆加工成阳模,在用较低温的铸造金属(例如铝)或者聚合物进行翻模,得到高精度的凹槽阵列,镶嵌磁铁颗粒。同时金属和聚合物载体有一定的柔性,可以弯曲成具有一定弧度的磁铁阵列,用来测量角位移及其他非直线位移传感。
34.可选地,在将磁铁颗粒填充到每个刻槽中之后,还包括:对晶圆掩膜版带有磁铁颗粒的一侧进行打磨抛光,如图9和图10所示。将带有磁铁颗粒填充之后,进行打磨抛光,既不影响磁铁颗粒的极性,也能够保证磁铁阵列的表面光滑。加工打磨之后的晶圆可以根据需要进行切割,形成所需要的磁铁阵列,用于各类传感器中。通过打磨抛光晶圆的方式平面化上表面, 得到一致的厚度和与霍尔传感器的磁间隙。
35.根据本发明实施例,通过采用半导体工艺,光刻形成用于进行磁铁颗粒定位的凹槽,再利用高纵深比深刻实现容纳磁铁颗粒的刻槽的刻蚀,其无论是磁铁颗粒定位和间距以及深度均能够达到微米级别,提高了磁铁阵列中磁铁颗粒定位加工精度,进而能够提高相应的霍尔传感器的测量精度。
36.另一方面,本发明实施例中,单次一个晶圆, 万至百万级的定位槽的大规模并行化的低成本制作方式。
37.作为一种可选实施方式,本发明实施例中,上述步骤s106,所述将磁铁颗粒填充到每个刻槽中,得到带有磁铁阵列的晶圆,可以包括:步骤s1061,制作磁铁薄片。
38.该磁铁薄片可以与晶圆掩膜版尺寸相同,也即是制作出与晶圆掩膜版相对应的磁铁薄片。该磁铁薄片的厚度可以根据需要设置,优选100-1200微米。进一步可选地,所述制作磁铁薄片,包括对所述磁铁薄片在厚度方向进行极化。本发明实施例中,极化的方向可以是垂直与磁铁薄片平面。
39.步骤s1062,将所述磁铁薄片贴附在衬底上,得到待加工的磁铁层。
40.具体地,如图11所示,将磁铁薄片7贴附在衬底5上。可以是通过可剥离胶水层6将将磁铁薄片7粘在在衬底5上。
41.步骤s1063,对所述磁铁层带有磁铁薄片的一侧进行刻蚀,获得带有磁铁凸起的磁铁层,其中,所述磁铁凸起的数量与所述刻槽的数量相等,并且位置相对应。
42.对应磁铁层,通过对磁铁薄片的一侧进行刻蚀,将磁铁薄片刻蚀成磁铁凸起,从而形成与上述刻槽相应的磁铁凸起阵列,磁铁层上每个磁铁凸起对应一个刻槽。也即是说,对磁铁薄片刻蚀出具有与上述图案相反的磁体凸起。
43.本实施例中,对于磁铁凸起的加工方式,可以与上述刻槽的加工方式一致,区别仅在于,图案相反,并形成对应。
44.可选地,本发明实施例中,所述磁铁凸起的侧壁坡度与所述刻槽的侧壁坡度相应。这样,能够使得带有磁铁凸起的磁铁层与所述带有刻槽的晶圆掩膜版对齐时,更容易使磁铁凸起与刻槽进行对应,方便进行加工对齐。
45.步骤s1064,将所述带有磁铁凸起的磁铁层与所述带有刻槽的晶圆掩膜版对齐,使得每个磁铁凸起对应到相应的刻槽上,将所述带有磁铁凸起的磁铁层与所述带有刻槽的晶圆掩膜版压紧贴合。
46.步骤s1065,将所述衬底去除,得到所述带有磁铁阵列的晶圆。
47.在刻蚀形成磁铁凸起之后,将磁铁层与晶圆掩膜版对应,使得磁铁凸起与刻槽相对应,完成将磁铁凸起放置在刻槽内,从而形成磁铁颗粒阵列。然后去除磁铁层上的衬底,形成带有磁铁阵列的晶圆。
48.本发明实施例中,通过采用集成半导体的刻蚀工艺制作高精度的磁铁颗粒,从而实现磁铁颗粒的极化方向的一致性,实现磁铁颗粒放置到晶圆上的工艺流程。
49.作为一种可选实施方式,所述将所述磁铁薄片贴附在衬底上,得到待加工的磁铁层,包括:将所述磁铁薄片用可剥离胶水粘贴在具有相同尺寸的衬底上。相应地,所述将所述衬底去除包括:将所述可剥离胶水溶解,然后剥离所述衬底。
50.通过可剥离胶水进行衬底的粘附,在实现磁铁颗粒的生成之后,方便进行去除,既保证了磁铁颗粒的加工过程采用半导体工艺,同时,又不留有其他非磁性材料,提高了工艺精度。
51.进一步可选地,如上所述,对磁铁薄片的加工过程,可以与刻槽的加工过程相同,具体地,所述对所述磁铁层带有磁铁薄片的一侧进行刻蚀,获得带有磁铁凸起的磁铁层,包括:在磁铁层带有磁铁薄片的一侧生成第二隔离层;在所述第二隔离层上涂覆第二光刻胶层,如图12所示(图中未示出第二隔离层的设置和刻蚀过程,其原理同上,这里不在赘述);对所述第二光刻胶层进行光刻,得到用于刻蚀出磁铁凸起的图案,如图13所示;对所述用于刻蚀出磁铁凸起的图案暴露出的第二隔离层刻蚀至所述磁铁层;对暴露出所述磁铁层的位置进行深刻,获得带有磁铁凸起的磁铁层。具体地,进行深刻之后,再去除光刻胶层,从而得
到带有磁铁凸起的磁铁层,如图14和15所示。
52.进一步地,在获得带有磁铁凸起的磁铁层(图15所示)之后,将其与上述带有刻槽的晶圆掩膜版与其进行对齐贴合,如图16所示,然后再将底部的衬底通过可剥离胶水层进行剥离,从而获得带有磁铁阵列的晶圆。
53.作为另一可替换的实施方式,磁铁颗粒的填充方式,也可以采用逐个添加的方式。可选地,所述将磁铁颗粒填充到每个刻槽中,得到带有磁铁阵列的晶圆,包括:对极化后的磁铁进行加工,得到磁铁棒;对所述磁铁棒进行切割,得到多个磁铁颗粒;利用精密机械将所述磁铁颗粒填充到所述刻槽内,得到带有磁铁阵列的晶圆。
54.本发明实施例中,加工形成磁铁棒,再有磁铁棒进行切割,形成磁铁颗粒,再用精密机械将其填充到刻槽内,保证极性一致。
55.进一步地,在对所述磁铁棒进行切割,得到多个磁铁颗粒之后,还包括:将所述磁铁颗粒极性一致地平放在基底上;向磁铁颗粒上表面涂覆抗刻蚀的涂层;对所述磁铁颗粒进行刻蚀,得到上宽下窄的磁铁颗粒,其中,刻蚀后的磁铁颗粒的侧壁坡度与所述刻槽的坡度对应。
56.本发明实施例中,通过对磁铁颗粒进行半导体工艺刻蚀,将其形状制作成与刻槽相适配的形状结构,这样,能够方便添加磁铁颗粒的时候,进行极性方向的对准,避免出现极性不一致的问题。
57.可选地,所述磁铁棒的直径为100-1000微米,所述磁铁颗粒的长度为100-1000微米。
58.具体地,下面进行详细介绍,该实施例中,可以将上述实施例中的刻槽做出截面为圆形的槽结构,如图17所示。然后,用车床将已极化的磁铁棒(如图18所示)用高速精密车床加工成直径100-1000微米的细棒,将此极化细棒切割成长度100-1000微米的小段;再将这些磁铁颗粒摊平放置于平整磁铁(或电磁铁)基底上,如图19所示,使其平摊随机但是极性一致的散布于基底表面;在磁铁颗粒上表面上用cvd方式涂敷抗刻蚀的涂层,如图20所示;对磁铁颗粒进行等离子体或者腐蚀液刻蚀,形成略微上宽下窄的形状,与之前的圆形凹槽的直径和侧壁斜度对应;用精密pick and place机器将磁铁颗粒放置于每一个对应的凹槽内,并压紧和粘接,如图21所示。
59.显然,上述实施例仅仅是为清楚地说明所作的举例,而并非对实施方式的限定。对于所属领域的普通技术人员来说,在上述说明的基础上还可以做出其它不同形式的变化或变动。这里无需也无法对所有的实施方式予以穷举。而由此所引伸出的显而易见的变化或变动仍处于本发明创造的保护范围之中。
再多了解一些
本文用于企业家、创业者技术爱好者查询,结果仅供参考。