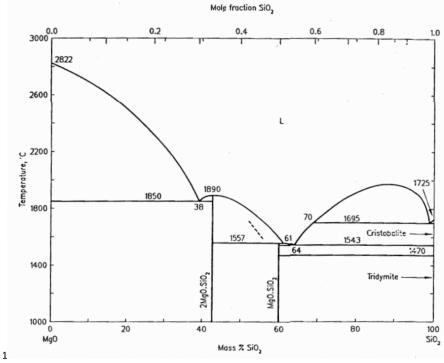
1.本发明属于耐火材料技术领域,具体涉及一种稀土钢连铸水口用镁硅质涂层及其制备方法。
背景技术:
2.稀土在钢中具有净化、变质夹杂物、微合金、细化晶粒和弥散强化等作用,具有“工业味精”的称号,但在实际冶炼稀土钢的连铸过程中水口结瘤问题是阻碍稀土元素在钢中应用的重要问题。
3.水口结瘤是由于连铸时钢中稀土元素和水口耐火材料中氧化物,如氧化镁、氧化铝、二氧化硅等发生化学反应和烧结反应,从而侵蚀水口内壁,导致水口内壁粗糙,进一步反应生成的稀土氧化物、硫化物等,以及钢水中的夹杂物不断附着堆积在粗糙的内壁上,尤其是浸入式水口处于特殊的位置和作用,其尤为严重,最终会导致水口结瘤堵塞。
4.为了避免出现稀土导致的堵浸入式水口的问题,采用的方法是将稀土金属在结晶器中加入,并且通过喂丝、喂线和喂带的形式插入钢水。但这些方法存在的问题是稀土金属进入钢水后与钢水中的氧及夹杂物进行反应,没有充足的时间进行均匀化和上浮,从而导致稀土反应产物滞留在钢水中,且分布不均匀,进而造成钢水的均匀性差,性能不稳定。因此,在稀土钢连铸的过程中,如何避免水口结瘤堵塞是一个急需解决的技术问题。
技术实现要素:
5.鉴于以上分析,针对现有技术中的不足,本发明旨在提供一种稀土钢连铸水口用镁硅质涂层及其制备方法,用以解决目前稀土钢连铸过程中,水口结瘤堵塞的问题。
6.本发明的目的主要是通过以下技术方案实现的:
7.一方面,本发明提供了一种稀土钢连铸水口用镁硅质涂层,涂层组分为镁硅氧化物和稀土氧化物,镁硅氧化物和稀土氧化物的质量比为84.54-91:1.98-10;
8.镁硅氧化物为2mgo
·
sio2或以2mgo
·
sio2为主,含有微量的mgo;
9.稀土钢为含稀土铈和/或镧的钢,稀土氧化物的种类与稀土钢中的稀土种类相同。
10.进一步的,镁硅氧化物中,以2mgo
·
sio2为主,含有微量的mgo,其中2mgo
·
sio2含量为94.21%-100%,mgo含量为5.79%-0%。
11.另一方面,本发明还提供了一种涂层的制备方法,以氧化镁材料、二氧化硅材料、氧化铈材料和/或氧化镧材料为原料,制备方法包括如下步骤:
12.步骤1、将氧化镁材料、二氧化硅材料、氧化铈材料和/或氧化镧材料,以及粘结剂分别磨制成200目以下的粉剂;
13.以质量百分含量计,氧化镁材料中mgo≥98%;二氧化硅材料中sio2≥96%;氧化铈材料中ceo2≥99%;氧化镧材料中la2o3≥99%;粘结剂为粉末状有机物;
14.步骤2、将步骤1中不同材料的粉剂按比例混合均匀;
15.以质量百分含量计为:氧化镁材料51-53%,二氧化硅材料36-38%,氧化铈材料
和/或氧化镧材料2-10%,粘结剂3-5%;
16.步骤3、将步骤2中混合均匀的粉剂烘干后备用;
17.进一步的,步骤1中,氧化镁材料为镁砂;二氧化硅材料为硅石。
18.进一步的,步骤1中,粘结剂为糊精、淀粉、酚醛树脂、环氧树脂中的一种或几种的组合。
19.进一步的,步骤2中,氧化镁材料51%,二氧化硅材料38%,氧化铈材料和/或氧化镧材料2-10%,粘结剂3-5%;氧化镁材料中mgo≥99%;二氧化硅材料中sio2≥99%。
20.进一步的,上述涂层的制备方法,在步骤3之后还包括如下步骤:
21.步骤4、将步骤3得到的粉剂,加入粉剂质量5-10%的水混匀,得到混匀的涂料;
22.步骤5、将步骤4中混匀的涂料,均匀的刷涂在水口的内壁上形成涂层;
23.步骤6、将涂好涂层的水口放进加热炉内进行加热,并保温;
24.步骤7、保温结束后,从加热炉内取出水口自然冷却,最后得到具有镁硅氧化物和稀土氧化物涂层的水口。
25.进一步的,步骤5中,所述涂层厚度为5-20mm。
26.进一步的,涂层厚度优选10-20mm。
27.进一步的,步骤6中,所述加热温度为1300-1500℃;所述保温时间为20-50min。
28.与现有技术相比,本发明有益效果如下:
29.1、本发明的水口涂层可以减少稀土钢连铸过程中浸入式水口的结瘤,使得浸入式水口的更换频次平均减小50%以上,从平均连铸1700吨稀土钢更换一次变为平均连铸2600吨稀土钢更换一次,保证了稀土钢连铸的顺行。
30.2、通过在水口内壁涂覆本发明的材料制备的涂层,可以有效保护连铸过程中水口被含稀土钢水的侵蚀,对于净化钢液,减少钢中外来夹杂物有明显的效果。
31.3、通过本发明的技术方案,使得稀土金属这种宝贵资源的利用效率得到了提高,为稀土合金的生产开辟了新的方向。
附图说明
32.图1为连铸时钢包、中间包和结晶器的位置关系以及各水口示意图;
33.图2为稀土ce和la与mgo、al2o3、sio2及2mgo
·
sio2反应的吉布斯自由能-温度关系图;
34.图3为mgo-sio2二元相图;
35.图中1-钢包,2-钢包座砖,3-钢包滑动水口,4-钢包下水口,5-钢包长水口,6-塞棒,7-中间包,8-第一浸入式水口,9-定径水口,10-中间墙,11-中间包盖,12-挡渣坝,13-冲击板,14-结晶器,15-结晶器保护渣层,16-中间包座砖,17-中间包上水口,18-中间包滑动水口,19-中间包下水口,20-第二浸入式水口。
具体实施方式
36.以下结合具体实施例对一种稀土钢连铸水口用镁硅质涂层及其制备方法作进一步的详细描述,这些实施例只用于解释的目的,本发明不限定于这些实施例中。
37.图1为连铸时钢包、中间包和结晶器的位置关系以及各水口示意图,从图中可以看
出,钢包中的钢水通过中间包进入连铸的结晶器,而在钢包和中间包之间、中间包和结晶器之间通过各种水口,实现对钢水的导流和密封,水口不仅是钢水流动的通路,也起到隔绝空气,减少钢水氧化的作用。水口包括钢包下水口4、钢包长水口5、第一浸入式水口8、第二浸入式水口20、定径水口9、中间包上水口17和中间包下水口19。
38.目前钢厂使用的水口的材质是刚玉质,其化学成分中al2o3含量大于57.59%,其他成分为烧失量。稀土钢中的稀土ce和la元素具有很强的反应特性,不仅与钢中元素,如al,c,o,s,n等反应,而且与水口耐火材料中氧化铝和氧化镁反应,可能的反应如下:
39.[ce] 3/2mgo
(s)
=1/2ce2o
3(s)
3/2[mg]
ꢀꢀ
δg
10
=677505-296.14t
ꢀꢀꢀꢀꢀ
(1)
[0040]
[ce] 1/2al2o3(s)=1/2ce2o
3(s)
[al]
ꢀꢀ
δg
20
=171045-133.89t
ꢀꢀꢀꢀꢀꢀ
(2)
[0041]
[la] 3/2mgo(s)=1/2la2o
3(s)
3/2[mg]
ꢀꢀ
δg
30
=778080-390.595t
ꢀꢀꢀꢀ
(3)
[0042]
[la] 1/2al2o
3(s)
=1/2la2o
3(s)
[al]
ꢀꢀ
δg
40
=456645-322.62t
ꢀꢀꢀꢀꢀꢀꢀ
(4)
[0043]
当钢水温度为1400-1600℃时,δg1=132478~192859(j/mol),δg2=-109228~-85976(j/mol),δg3=56139~135411(j/mol),δg4=-177119~-116121(j/mol)。
[0044]
由以上分析可见,钢水温度在1400-1600℃左右时,钢水中的稀土元素与水口耐火材料中的al2o3反应剧烈,加剧了水口的侵蚀,并降低钢中稀土的收得率;而稀土ce、la元素与mgo的δg1>0、δg3>0,所以不反应。
[0045]
需要说明的是,由于连铸过程中,中间包和结晶器之间通过浸入式水口连接,浸入式水口是钢水结晶之前的最后关口,浸入式水口内一直存在高速流动的钢液;且在精炼结束后钢水中的夹杂物会不断累积;在保护浇铸方面,若保护不好,浇铸过程中负压吸氧,造成钢水的二次氧化,易产生氧化铝夹杂物。同时,钢液温度逐渐下降打破了al-o平衡,使得钢液中al2o3增加,al2o3不能充分上浮而聚集在浸入式水口内;尤其在连铸稀土钢时耐材中al2o3与钢液稀土元素反应生成外来夹杂;更为特殊的是,由于受限于铸坯外形尺寸,乃至结晶器的尺寸,因此浸入式水口的内、外径较其他水口狭小,最终使得浸入式水口侵蚀、黏附和堵塞的现象较其他水口更为严重。
[0046]
一方面,本发明提供了一种稀土钢连铸水口用镁硅质涂层,涂层组成为镁硅氧化物和稀土氧化物,镁硅氧化物和稀土氧化物的质量比为84.54-91:1.98-10。其中镁铝氧化物为2mgo
·
sio2或以2mgo
·
sio2为主,含有微量的mgo,具体的2mgo
·
sio2的含量在94.21%-100%之间,相应的mgo含量在5.79%-0%之间;稀土氧化物为氧化铈和/或氧化镧。
[0047]
需要说明的是,本发明涂层组成成分的选择,在于在钢液浇铸的温度范围内,mgo和2mgo
·
sio2与钢水中的稀土[ce]和[la]不发生化学反应,同时涂层中掺杂的稀土氧化物也不与[ce]和[la]不发生化学反应,而sio2与稀土元素ce和la反应较为强烈。mgo作为耐材和钢中稀土的反应情况已在前文论述,这里不在赘述,下面就sio2、2mgo
·
sio2与钢中稀土[ce]和[la]的反应情况做具体分析。
[0048]
sio2、2mgo
·
sio2与钢水中的稀土元素ce和la的反应方程式如下:
[0049]
[ce] 3/4sio
2(s)
=1/2ce2o
3(s)
3/4[si]
ꢀꢀꢀ
δg
50
=187142-132.1075t
ꢀꢀꢀꢀ
(5)
[0050]
[la] 3/4sio
2(s)
=1/2la2o
3(s)
3/4[si]
ꢀꢀꢀ
δg
60
=472742-320.838t
ꢀꢀꢀꢀꢀ
(6)
[0051]
[ce] 3/4(2mgo
·
sio2)
(s)
=1/2ce2o
3(s)
3/2[mg] 3/4sio
2(s)
[0052]
δg
70
=727905-299.3725t
ꢀꢀꢀꢀꢀꢀꢀꢀꢀꢀꢀꢀꢀꢀꢀꢀꢀꢀꢀꢀꢀꢀꢀꢀꢀꢀꢀꢀꢀꢀꢀꢀꢀꢀꢀꢀꢀ
(7)
[0053]
[la] 3/4(2mgo
·
sio2)
(s)
=1/2la2o
3(s)
3/2[mg] 3/4sio
2(s)
[0054]
δg
80
=1013505-488.1025t
ꢀꢀꢀꢀꢀꢀꢀꢀꢀꢀꢀꢀꢀꢀꢀꢀꢀꢀꢀꢀꢀꢀꢀꢀꢀꢀꢀꢀꢀꢀꢀꢀꢀꢀꢀꢀ
(8)
[0055]
当钢水温度为1400-1600℃时,δg5=-57759~-31034(j/mol),δg6=-125652~-61180(j/mol),δg7=176823~237851(j/mol),δg8=108932~207706(j/mol)。
[0056]
可见,钢水温度在1400-1600℃左右时,二氧化硅与钢中稀土的反应强烈,而δg7>0、δg8>0,钢水中的稀土元素ce和la元素与2mgo
·
sio2不反应。
[0057]
图2为稀土ce和la与sio2、mgo、al2o3及2mgo
·
sio2反应的吉布斯自由能-温度关系图,从图中也可以看出,1400-1600℃时稀土镧、铈与sio2、al2o3反应的吉布斯自由能在0度线以下(<0),反应能够进行;相反稀土镧、铈与mgo和2mgo
·
sio2的吉布斯自由能在0度线以上(>0),反应不能进行,而且2mgo
·
sio2的吉布斯自由能曲线在mgo吉布斯自由能曲线之上,较mgo更为稳定。
[0058]
此外,2mgo
·
sio2具有较高的熔点为1890℃,在连铸浇铸温度1500-1600℃下是不会熔化的,氧化镁也是钢铁冶炼的常规耐火材料,所以两者都比较适合做涂层。
[0059]
需要说明的是,本发明稀土钢中的稀土元素为铈和/或镧。稀土氧化物的种类与稀土钢中的稀土种类相同,即当稀土钢中只有铈时,上述涂层中也只有氧化铈;当稀土钢中只有镧时,涂层中也只有氧化镧;当稀土钢中含有铈和镧时,则涂层中相应含有氧化铈和氧化镧。氧化铈的熔点为2600℃、氧化镧的熔点为2315℃,熔点都较高,能够一定程度改善镁质耐材的性能,而且不与钢中稀土元素反应,因此符合本发明对涂层性能的设计要求。
[0060]
综上,由于1400-1600℃时稀土镧、铈与2mgo
·
sio2的不反应,2mgo
·
sio2抗稀土铈和镧的能力较更强。因此,本发明利用此特性设计了水口的涂层材料,来遮蔽水口表面,阻止水口耐材和钢水中的铈和镧发生化学反应。
[0061]
以上的涂层材料适用于稀土钢连铸工艺中的各种水口,尤其是浸入式水口,在浸入式水口内壁刷涂一层抗稀土氧化的物质,能够有效地抑制稀土镧和铈与浸入式水口的al2o3耐材反应,从而减少水口的结瘤,保证稀土钢连铸的顺行。此外,对于含铝钢而言,铝质耐材的水口更适合浇铸,所以本发明的水口涂层不建议在连铸含铝钢时使用,即本发明的涂层材料不适合含铝钢的浇铸。
[0062]
另一方面,本发明提供了制备以上涂层所用材料的制备方法,制备方法包括如下步骤:
[0063]
步骤1、将二氧化硅材料、氧化镁材料、氧化铈材料和/或氧化镧材料,以及粘结剂分别磨制成200目以下(《0.075mm)的粉剂;
[0064]
步骤2、将上述材料按比例混合均匀;
[0065]
步骤3、将上述混合后的粉剂烘干后备用。
[0066]
具体的,在步骤1中,按照质量百分含量计,二氧化硅材料中sio2≥96%;氧化镁材料中mgo≥98%;氧化铈材料中ceo2≥99%;氧化镧材料中la2o3≥99%;粘结剂为耐火喷补料所用结合剂,粘结剂为粉末状有机物,如天然有机物:糊精、淀粉等;合成有机物:酚醛树脂、环氧树脂等。
[0067]
具体的,在步骤2中,按照质量百分含量计组成为:二氧化硅材料36-38%,氧化镁材料51-53%,氧化铈材料和/或氧化镧材料2-10%,粘结剂3-5%。
[0068]
进一步的,在上述材料的含量范围内,按照质量百分含量计,优选二氧化硅材料
38%,氧化镁材料51%,氧化铈材料和/或氧化镧材料2-10%,粘结剂3-5%。其中,二氧化硅材料中sio2≥99%;氧化镁材料中mgo≥99%;氧化铈材料中ceo2≥99%;氧化镧材料中la2o3≥99%。
[0069]
需要说明的是,由于涂层材料为各种氧化物,所以破碎、磨制、筛分和烘干工艺不需要特别的保护工艺,制粉可以采取成本较低的球磨制粉,筛分采取常规的机械筛分或气流分级,烘干的目的在于去除水分,100℃以上即可,因此适合以上破碎、磨制、筛分和烘干工艺的设备均可使用,当然,也不局限于以上常规的工艺方式和设备。
[0070]
进一步的,以上涂层的制备方法,在步骤3之后还包括如下步骤:
[0071]
步骤4、把上述磨细、混匀、烘干制备好的粉剂,按照质量百分含量计加入粉剂总质量5-10%的水混匀;
[0072]
步骤5、将步骤4中混匀的涂料,均匀的刷涂在水口的内壁上,涂层厚度为5-20mm,优选10-20mm;
[0073]
步骤6、将步骤5中做好涂层的水口放进加热炉内进行加热,加热温度为1300-1500℃,保温时间为20-50min;
[0074]
步骤7、从加热炉内取出水口自然冷却,最后得到具有镁硅氧化物和稀土氧化物涂层的水口。
[0075]
需要说明的是,在步骤5中,由于水口的内径一般在100mm以下,尤其是浸入式水口的内径更为狭窄为50mm左右,为了保持添加涂层后的水口内径不变,所以涂层处理前的水口内径较正常的水口内径大5-20mm。
[0076]
需要说明的是,在步骤6中,由于涂层材料为各种氧化物,所以烧结不需要特别的保护,只要常规的加热炉即可,如依靠各种燃料提供热量的火焰炉,电炉等,当然,也不局限于以上常规的工艺方式和设备。
[0077]
涂层的粘结剂选择有机粘结剂,是因为在高温烧结工艺中,有机粘结剂易于烧损、挥发,从而对涂层材料的组分设计影响较小,使得涂层成分更为稳定。
[0078]
需要说明的是,在步骤7中,得到的镁硅氧化物涂层为2mgo
·
sio2或以mg
2 sio4为主,含有微量的mgo。
[0079]
从图3中的mgo-sio2二元相图可知,2mgo
·
sio2相的生成取决于mgo和sio2的比值,按照质量百分含量mgo:sio2=57:43=1.326时,sio2和mgo相互作用生成2mgo
·
sio2相;当mgo:sio2的比值>1.326时,除了生成2mgo
·
sio2相外,还含有过量的mgo;当mgo:sio2的比值<1.326时,除了生成2mgo
·
sio2相外,还含有过量的mgo
·
sio2相。本发明涂层材料成分mgo:sio2=60.5-56.8:39.5-43.2,即本发明镁硅氧化物涂层为2mgo
·
sio2单相,或者为绝大多数的2mgo
·
sio2相和微量的mgo相,具体的2mgo
·
sio2的含量在94.21%-100%之间,相应的mgo含量在5.79%-0%之间。另外,由于2mgo
·
sio2在与钢中稀土元素反应方面较mgo更为稳定,所以较高比例的2mgo
·
sio2含量更有利于延长水口的使用寿命。
[0080]
另外,从图3的相图可以看出mgo
·
sio2的熔点为1557℃,明显是不适于在炼钢工艺中做耐火材料的,而2mgo
·
sio2以及mgo如前述具有较高的熔点,因此本发明的涂层选择在上述范围之内。
[0081]
此外,为了保证mgo和sio2在结合过程中的烧结性,在涂层中加入与稀土铈和镧不反应的氧化铈和氧化镧,这些稀土氧化物熔点高,化学活性大,有较好的抗侵蚀性,对
2mgo
·
sio2的合成均有一定的促进作用,烧结后在涂层中形成相应的稀土氧化物相。另外,出于对稀土氧化物成本,以及对烧结作用、耐材综合性能的影响,稀土氧化物的数量按照质量百分含量计在涂层中不超过10%。
[0082]
需要说明的是,由于所用原料纯度较高,烧失量主要是有机粘结剂和水分的蒸发,以及烧结致密度上升导致的体积收缩,烧结后的涂层厚度大约较烧结前收缩10%以下,即烧结后的涂层厚度是烧结前涂层厚度的90%以上。
[0083]
使用本发明的涂层使得浸入式水口的更换频次平均减小50%以上,从平均连铸1700吨稀土钢更换一次变为平均连铸2600吨稀土钢更换一次。
[0084]
对比例1
[0085]
生产的钢种为耐磨钢nm400,生产流程为转炉
→
lf炉
→
rh炉
→
连铸。目标成分为:c 0.19-0.21%;si 0.55-0.65%;mn 1.45-1.60%;p≤0.015%;s≤0.005%;cr 0.35-0.45%;ti 0.01-0.02%;ce 0.005%;la 0.005%。
[0086]
水口耐材为铝质耐材,al2o3质量百分含量为78%。
[0087]
平均6.5炉更换一次浸入式水口,即平均连铸1690吨耐磨钢nm400更换一次浸入式水口。
[0088]
实施例1
[0089]
生产的钢种为耐磨钢nm400,生产流程为转炉
→
lf炉
→
rh炉
→
连铸。目标成分为:c 0.19-0.21%;si 0.55-0.65%;mn 1.45-1.60%;p≤0.015%;s≤0.005%;cr 0.35-0.45%;ti 0.01-0.02%;ce 0.005%;la 0.005%。
[0090]
采用的原料是硅石、镁砂、氧化铈、氧化镧和糊精。其中硅石的化学成分为:sio
2 98.6%;al2o
3 0.35%,fe2o
3 0.58%,cao 0.09%,k2o 0.1%;na2o 0.2%;镁砂的化学成分为mgo占99%;氧化铈和氧化镧是纯试剂,稀土氧化物含量99%。糊精作为粘结剂。具体组成为:硅石36%,镁砂51%,氧化铈3%,氧化镧5%,糊精5%。
[0091]
粉剂的制备方法:
[0092]
步骤1、将硅石、镁砂、氧化铈、氧化镧和糊精,分别磨制成200目以下的粉剂;
[0093]
步骤2、将步骤1中不同材料的粉剂按上述比例混合均匀;
[0094]
步骤3、将步骤2中混合均匀的粉剂烘干后备用。
[0095]
涂层的制备方法:
[0096]
步骤1、将制备好的粉剂,按照质量百分含量计加入粉剂总质量5%的水混匀,;
[0097]
步骤2、将步骤1中混匀的涂料,均匀的刷涂在浸入式水口的内壁上形成涂层,涂层厚度10mm;
[0098]
步骤3、将涂好涂层的浸入式水口放进电阻炉内,加热温度为1300℃,保温时间为50min;
[0099]
步骤4、保温结束后,从电阻炉内取出浸入式自然冷却,最后在水口内壁形成厚度为9mm、具有镁硅氧化物和稀土氧化物的涂层,其中镁硅氧化物和稀土氧化物的质量比为85.99:7.92,镁硅氧化物中2mgo
·
sio2占97.07%,mgo占2.93%。
[0100]
平均10炉更换一次浸入式水口,即平均连铸2600吨耐磨钢nm400更换一次浸入式水口。
[0101]
实施例2
[0102]
生产的钢种为耐磨钢nm400,生产流程为转炉
→
lf炉
→
rh炉
→
连铸。目标成分为:c 0.19-0.21%;si 0.55-0.65%;mn 1.45-1.60%;p≤0.015%;s≤0.005%;cr 0.35-0.45%;ti 0.01-0.02%;ce 0.005%;la 0.005%。
[0103]
采用的原料是硅石、镁砂、氧化铈、氧化镧和淀粉。其中硅石的化学成分为:sio
2 98.6%;al2o
3 0.35%,fe2o
3 0.58%,cao 0.09%,k2o 0.1%;na2o 0.2%。镁砂的化学成分为mgo占98.5%;氧化铈和氧化镧是纯试剂,稀土氧化物含量99%。淀粉作为粘结剂。具体组成为:硅石38%,镁砂53%,氧化铈3%,氧化镧3%,淀粉3%。
[0104]
粉剂的制备方法:
[0105]
步骤1、将硅石、镁砂、氧化铈、氧化镧和淀粉,分别磨制成200目以下的粉剂;
[0106]
步骤2、将步骤1中不同材料的粉剂按上述比例混合均匀;
[0107]
步骤3、将步骤2中混合均匀的粉剂烘干后备用。
[0108]
涂层的制备方法:
[0109]
步骤1、将制备好的粉剂,按照质量百分含量计加入粉剂总质量10%的水混匀,;
[0110]
步骤2、将步骤1中混匀的涂料,均匀的刷涂在钢包下水口内壁,厚15mm;钢包长水口内壁,厚20mm;中间包上水口内壁,厚10mm;中间包下水口内壁,厚10mm;浸入式水口的内壁,厚10mm;
[0111]
步骤3、将涂好涂层的水口放进电阻炉内,加热温度为1500℃,保温时间为20min;
[0112]
步骤4、保温结束后,从电阻炉内取出水口自然冷却,最后在水口内壁形成一定厚度的涂层,其中钢包下水口涂层厚14mm;钢包长水口涂层厚19mm;中间包上水口涂层厚9mm;中间包下水口涂层厚9mm;浸入式水口涂层厚9mm;涂层为由镁硅氧化物和稀土氧化物组成,其中镁硅氧化物和稀土氧化物的质量比为89.67:5.94,镁硅氧化物中2mgo
·
sio2占97.91%,mgo占2.09%。
[0113]
平均10.1炉更换一次浸入式水口,即平均连铸2626吨耐磨钢nm400更换一次浸入式水口。
[0114]
对比例2
[0115]
生产的钢种为耐蚀钢q450nrq1,生产流程为转炉
→
lf炉
→
连铸。目标成分为:c≤0.12%;si≤0.75%;mn≤1.5%;p≤0.025%;s≤0.008%;cr 0.30-1.25%;cu 0.20-0.55%;ni 0.12-0.65%;ce 0.01%或la 0.01%。
[0116]
水口耐材为铝质耐材,al2o3质量百分含量为82%。
[0117]
平均6.5炉更换一次浸入式水口,即平均连铸1690吨耐蚀钢q450nrq1更换一次浸入式水口。
[0118]
实施例3
[0119]
生产的钢种为耐蚀钢q450nrq1,生产流程为转炉
→
lf炉
→
连铸。目标成分为:c≤0.12%;si≤0.75%;mn≤1.5%;p≤0.025%;s≤0.008%;cr 0.30-1.25%;cu 0.20-0.55%;ni 0.12-0.65%;ce 0.01%。
[0120]
涂层材料:
[0121]
采用的原料是硅石、镁砂、氧化铈和环氧树脂。其中硅石的化学成分为:sio
2 99.9%;al2o
3 0.15%,fe2o
3 0.28%,cao 0.07%。镁砂的化学成分为mgo占99.0%;氧化铈是纯试剂,稀土氧化物含量99%。环氧树脂作为粘结剂。具体组成为:硅石38%,镁砂51%,
氧化铈6%,环氧树脂5%。
[0122]
粉剂的制备方法:
[0123]
步骤1、将硅石、镁砂、氧化铈和环氧树脂,分别磨制成200目以下的粉剂;
[0124]
步骤2、将步骤1中不同材料的粉剂按上述比例混合均匀;
[0125]
步骤3、将步骤2中混合均匀的粉剂烘干后备用。
[0126]
涂层的制备方法:
[0127]
步骤1、将制备好的粉剂,按照质量百分含量计加入粉剂总质量8%的水混匀,;
[0128]
步骤2、将步骤1中混匀的涂料,均匀地刷涂在浸入式水口的内壁上,涂层厚度5mm;
[0129]
步骤3、将涂好涂层的浸入式水口放进电阻炉内,加热温度为1400℃,保温时间为35min;
[0130]
步骤4、保温结束后,从电阻炉内取出水口自然冷却,最后在水口内壁形成厚度为4.6mm、具有镁硅氧化物和氧化铈的涂层,其中镁硅氧化物和氧化铈的质量比为88.45:5.94,镁硅氧化物为2mgo
·
sio2。
[0131]
平均10.1炉更换一次浸入式水口,即平均连铸2626吨耐蚀钢q450nrq1更换一次浸入式水口。
[0132]
实施例4
[0133]
生产的钢种为耐蚀钢q450nrq1,生产流程为转炉
→
lf炉
→
连铸。目标成分为:c≤0.12%;si≤0.75%;mn≤1.5%;p≤0.025%;s≤0.008%;cr 0.30-1.25%;cu 0.20-0.55%;ni 0.12-0.65%;la 0.01%。
[0134]
采用的原料是硅石、镁砂、氧化镧和酚醛树脂。其中硅石的化学成分为:sio
2 98.6%;al2o
3 0.35%,fe2o
3 0.58%,cao 0.09%,k2o 0.1%;na2o 0.2%。镁砂的化学成分为mgo占98.7%;氧化镧是纯试剂,稀土氧化物含量99%。酚醛树脂作为粘结剂。具体组成为:硅石37%,镁砂52%,氧化镧7%,酚醛树脂4%。
[0135]
粉剂的制备方法:
[0136]
步骤1、将硅石、镁砂、氧化镧和酚醛树脂,分别磨制成200目以下的粉剂;
[0137]
步骤2、将步骤1中不同材料的粉剂按上述比例混合均匀;
[0138]
步骤3、将步骤2中混合均匀的粉剂烘干后备用。
[0139]
涂层的制备方法:
[0140]
步骤1、将制备好的粉剂,按照质量百分含量计加入粉剂总质量6%的水混匀,;
[0141]
步骤2、将步骤1中混匀的涂料,均匀的刷涂在浸入式水口的内壁上形成涂层,涂层厚度15mm;
[0142]
步骤3、将涂好涂层的浸入式水口放进电阻炉内,加热温度为1450℃,保温时间为40min;
[0143]
步骤4、保温结束后,从电阻炉内取出浸入式水口自然冷却,最后在水口内壁形成厚度为14mm、具有镁硅氧化物和氧化镧的涂层,其中镁硅氧化物和氧化镧的质量比为87.81:6.93,镁硅氧化物中mgo
·
al2o3占97.52%,mgo占2.48%。
[0144]
平均10炉更换一次浸入式水口,即平均连铸2600吨耐蚀钢q450nrq1更换一次浸入式水口。
再多了解一些
本文用于企业家、创业者技术爱好者查询,结果仅供参考。