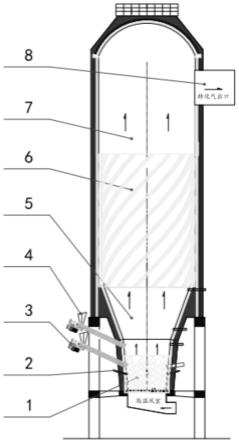
1.本发明属于工业废渣资源化利用技术领域,具体涉及一种煤气化细渣的脱碳处理工艺方法及其应用。
背景技术:
2.公开该背景技术部分的信息仅仅旨在增加对本发明的总体背景的理解,而不必然被视为承认或以任何形式暗示该信息构成已经成为本领域一般技术人员所公知的现有技术。
3.煤气化细渣(也称气化煤泥,或称气化滤饼),是煤气化生产过程中产生的细渣,在气化炉内高温燃烧、反应后转化不完全的细煤颗粒和细灰,其细煤颗有点类似半焦,通常气化细渣含水25-60%,含有一定量的玻璃胶体,发粘,无挥发分,残碳含量16-28%(干基),气化细渣的低位发热值为500-1800kcal/kg。
4.煤气化细渣的产生量,随着煤气化工业的规模扩大与升级,气化细渣的生成量也逐年增加,每年的新产生量超亿吨,如此之大的数量目前的利用率很低,只能筑坝存放,占用大量的土地,渗透污染地下水,形成了一个很大的危险污染源;风干后的干细粉随风飞扬,污染大气环境;雨季的雨水冲刷渗透扩散有害物质,这些现象亟待解决。
技术实现要素:
5.针对现有技术的不足,本发明提供一种煤气化细渣的脱碳处理工艺方法及其应用。本发明通过优化煤气化细渣的脱碳工艺,加入2-3%生物质含氧转化催化剂,使煤气化细渣迅速脱碳,煤气化细渣在不添加任何煤碳热量的前提下,依靠自身的能量和转化催化剂来实现脱碳,转变为粉煤灰(建材)从而便于使用,因此具有良好的实际应用特别是大规模工业化及产业化应用的价值。
6.为了实现上述目的,本发明涉及以下技术方案:
7.本发明的第一个方面,提供一种煤气化细渣的脱碳处理工艺方法,所述方法包括:将煤气化细渣在含氧转化催化剂的作用下,高温配空气的条件下,脱碳转化成粉煤灰,同时释放热能。
8.其中,所述煤气化细渣其含水量控制为25-60%,进一步优选为30-35%,在含氧转化催化剂的作用下,使得气化细渣迅速脱碳过程顺利进行。
9.所述高温环境为700-980℃(优选为850-950℃),富氧或多氧转化催化剂配入量2-3%(w/w)。
10.其中,所述富氧或多氧转化催化剂是由含铜基材料制成;
11.所述催化剂,其具体制备方法如下:
12.将醋酸铜与2,2'-联嘧啶溶于有机溶剂中,然后向其中加入堇青石质多孔陶瓷,在加热条件下混合均匀,然后再高温去除有机溶剂,将残留产物粉碎后进行高温煅烧处理。
13.其中,所述醋酸铜与2,2'-联嘧啶的摩尔比控制为4~6:1,优选为5:1;
14.所述有机溶剂可以为乙醇;
15.所述醋酸铜与堇青石质多孔陶瓷的质量比为0.1~3:90-110,优选为1:100;
16.所述堇青石质多孔陶瓷可以是废弃堇青石质多孔陶瓷,从而进一步降低生产和使用成本;
17.所述加热条件可以为在:50-70℃下搅拌混合均匀;
18.所述高温条件可以为在高于溶剂沸点(如80℃以及以上)的温度下蒸发去除有机溶剂;去除的有机溶剂(乙醇)可重复使用,从而节约成本。
19.所述高温煅烧具体工艺为:以3-5℃/min(优选为4℃)升温至800-900℃(优选为850℃)持续时间为1-3小时。
20.上述含氧转化催化剂粒径控制为不小于1mm,优选为2-5mm。
21.本发明采用上述富氧或多氧转化催化剂能够有效缩短反应时间,同时,上述富氧或多氧转化催化剂热稳定性能极佳,在高温燃烧过程中能够保持长时间催化活性(至少维持100h以上),铜金属没有明显流失,从而极大降低生产成本。
22.上述催化转化脱碳过程持续时间可以为2-12秒,进一步优选为5-8秒,从而即可实现脱碳过程,使得固相碳转变成气相co2排出,从而使得煤气化细渣脱碳成功。
23.本发明的第二个方面,提供上述工艺方法在如下任意一种或多种中的应用:
24.1)粉煤灰制备,副产可发电的蒸汽;
25.2)煤气化细渣资源化/无害化处理;
26.3)煤气化细渣固废的减量化处理(缩减率60-80%)。
27.以上一个或多个技术方案的有益技术效果:
28.上述技术方案首次提供一种煤气化细渣的转化催化脱碳处理工艺方法,通过将从煤化工生产中的煤气化细渣输送至催化转化装置炉的炉内,同时配入2-3%含氧转化催化剂,通过炉内底部蓄热物料引燃,催化转化气化细渣中的碳,在高温气固相均匀接触成功实现脱碳的过程,使固相碳转变成气相co2,使其煤气化细渣脱碳成功。上述技术方案在不添加任何煤碳热量的前提下,依靠煤气化细渣自身的能量和催化剂的催化作用,实现催化脱碳过程,是将煤化工生产过程产生的气化细渣的固废污染物进行资源化利用的过程,具有良好的实际应用特别是大规模工业化及产业化应用的价值。
附图说明
29.构成本发明的一部分的说明书附图用来提供对本发明的进一步理解,本发明的示意性实施例及其说明用于解释本发明,并不构成对本发明的不当限定。
30.图1为本发明煤气化细渣的脱碳处理装置(立式)示意图;
31.图2为本发明煤气化细渣的脱碳处理装置(门式)示意图;
32.其中,1-蓄热催化引燃区;2-原始开车加热口;3-催化剂入口;4-给泥铰刀;5-催化转化扩张区;6-蓄能催化转化区;7-催化完全转化区;8-出口连接锅炉。
具体实施方式
33.应该指出,以下详细说明都是例示性的,旨在对本发明提供进一步的说明。除非另有指明,本文使用的所有技术和科学术语具有与本发明所属技术领域的普通技术人员通常
理解的相同含义。
34.需要注意的是,这里所使用的术语仅是为了描述具体实施方式,而非意图限制根据本发明的示例性实施方式。如在这里所使用的,除非上下文另外明确指出,否则单数形式也意图包括复数形式,此外,还应当理解的是,当在本说明书中使用术语“包含”和/或“包括”时,其指明存在特征、步骤、操作、器件、组件和/或它们的组合。应理解,本发明的保护范围不局限于下述特定的具体实施方案;还应当理解,本发明实施例中使用的术语是为了描述特定的具体实施方案,而不是为了限制本发明的保护范围。
35.如前所述,煤气化细渣的产生量,随着煤气化工业的规模扩大与升级,气化细渣的生成量也逐年增加,每年的新产生量超亿吨,如此之大的数量目前的利用率很低,只能筑坝存放,占用大量的土地,渗透污染地下水,形成了一个很大的危险污染源;风干后的干细粉随风飞扬,污染大气环境;雨季的雨水冲刷渗透扩散有害物质,这些现象亟待解决。
36.煤气化细渣来源,包括多种煤气化炉:气流床煤气化炉和流化床煤气化炉;气流床煤气化炉又分为干煤粉气化炉和水煤浆气化炉两大类;以干煤粉为气化用煤的煤气化炉型,包括有航天炉、壳牌炉、宁煤炉、晋煤炉等等多种气化炉;以水煤浆为原料的炉型有德士古水煤浆气化炉和多喷嘴水煤浆气化炉等;均产生大量的气化细渣(或称气化滤饼,又称气化煤泥)。
37.流化床式煤气化炉(含恩德炉)其含水浴流程的也含有大量的气化煤泥。
38.气化滤饼或气化煤泥本文通称煤气化细渣。
39.有鉴于此,本发明的一个典型具体实施方式中,提供一种煤气化细渣的脱碳处理工艺方法,所述方法包括:将煤气化细渣在含氧转化催剂的作用下,高温脱碳转化成粉煤灰,同时释放热能。
40.本发明的又一具体实施方式中,所述煤气化细渣其含水量控制为25-60%,进一步优选为30-35%左右,在含氧转化催化剂的作用下,使得气化细渣脱碳过程快速顺利进行。
41.所述高温环境为700-980℃(优选为850-950℃),含氧转化催化剂配入量2-3%(w/w)。
42.其中,所述富氧或多氧转化催化剂是由含铜基材料制成;
43.所述催化剂,其具体制备方法如下:
44.将醋酸铜与2,2'-联嘧啶溶于有机溶剂中,然后向其中加入堇青石质多孔陶瓷,在加热条件下混合均匀,然后再高温去除有机溶剂,将残留产物粉碎后进行高温煅烧处理。
45.其中,所述醋酸铜与2,2'-联嘧啶的摩尔比控制为4~6:1,优选为5:1;
46.所述有机溶剂可以为乙醇;
47.所述醋酸铜与堇青石质多孔陶瓷的质量比为0.1~3:90-110,优选为1:100;
48.所述堇青石质多孔陶瓷可以是废弃堇青石质多孔陶瓷,从而进一步降低生产和使用成本;
49.所述加热条件可以为在:50-70℃下搅拌混合均匀;
50.所述高温条件可以为在高于溶剂沸点(如80℃以及以上)的温度下蒸发去除有机溶剂;去除的有机溶剂(乙醇)可重复使用,从而节约成本。
51.所述高温煅烧具体工艺为:以3-5℃/min(优选为4℃)升温至800-900℃(优选为850℃)持续时间为1-3小时。
52.上述含氧转化催化剂粒径控制为不小于1mm,优选为2-5mm。
53.本发明采用上述富氧或多氧转化催化剂能够有效缩短反应时间,同时,上述富氧或多氧转化催化剂热稳定性能极佳,在高温燃烧过程中能够保持长时间催化活性,从而降低生产成本。
54.上述催化转化过程持续时间可以为2-12秒,进一步优选为5-8秒,从而即可实现脱碳过程,使得固相碳转变成气相co2排出,从而使得煤气化细渣脱碳成功。
55.需要说明的是,即使不使用上述催化剂,煤气化细渣同样可以在高温条件下实现脱碳转化成粉煤灰(建材),因此,不使用催化剂进行上述反应过程同样属于本发明的保护范围。
56.本发明的又一具体实施方式中,所述脱碳处理工艺方法可以在催化转化装置内进行:
57.所述催化转化装置可以为催化转化炉,所述催化转化炉为立式结构,由下至上依次包括:蓄热催化引燃区、催化转化扩张区、蓄能催化转化区和催化完全转化区;
58.其中,所述蓄热催化引燃区通过风力扰动,在转化催化剂的作用下,传热引燃气化细渣催化脱碳,更具体的,所述蓄热催化引燃区下方设置高温风室,所述高温风室释放高温空气(高温含氧气体或高温富氧空气)100-600℃,所述高温空气(高温含氧气体或高温富氧空气)自下而上运动,从而为蓄热催化引燃区等区域提供高温空气,并为煤气化渣提供风动力支持,使得煤气化细渣可以在装置内向上运动,从而进入上述各区域内。需要说明的是,直接加入生物质燃料,或其它助燃燃料(如柴油、天然气、甲醇、煤粉、煤或水煤浆等其它燃料)同样属于本发明的保护范围。
59.需要说明的是,上述催化转化炉虽然是以立式结构为例(见图1),但是还可以使用包括但不限于门式(见图2)、卧式或其它方式的锅炉回收热量,只要能够实现煤气化细渣的脱碳功能即可。同时,即使是立式结构,但是从下至上变径或不变径、或圆型变方型或方型变圆型等形式也适用于本发明,因此同样属于本技术的保护范围。
60.所述蓄热催化引燃区选用物料可以为石英砂、焦宝石和流化床锅炉炉渣中的任意一种或多种;
61.所述催化转化扩张区用于尽快扩张面积,用于降低煤气化细渣的上浮速度;
62.所述蓄热催化转化区用于将煤气化细渣有限的转化热留在炉膛内,因此所述蓄热催化转化区作蓄热保温处理,因此,现有已知蓄热方式均在本发明保护范围之内,如使用蓄热格子砖、多个蓄热拱型并排、多个蓄热柱等,更具体的,该区域内炉壁内侧墙体砖采用异型蓄热式高铝砖,从而防止或减少热量损失和被带走。
63.所述催化完全转化区用于将进入该区域煤气化细渣中的少量的碳,进一步转化彻底。在本发明中,在进入该催化完全转化区之前,煤气化细渣的转化时间已达3-8秒,转化率已达70-80%。从而使得进入该区域内,进一步转化从而实现对煤气化细渣的完全转化,得到粉煤灰(建材)产品。
64.为便于将煤气化细渣输送至上述催化转化装置中,在所述蓄热催化引燃区与催化转化扩张区之间设置有煤气化细渣输送机构,所述煤气化细渣输送机构用于将外界煤气化细渣送入上述催化转化装置,优选的,所述输送机构可以为铰刀式输送机构。煤气化细渣输送机构的输入口位置不做具体限定,可依据催化转化炉的整体规格而定,具体的,输入口位
置可以为距底端向上3-18m开口。
65.本发明的又一具体实施方式中,在所述催化完全转化区上部设置有转化气出口,从而用于排出转化气体,进入热量回收装置或余热锅炉。
66.为保证反应充分进行,所述煤气化细渣粒径为不大于1mm,进一步优选为250~500μm。通过控制煤气化细渣粒径,有利于后期与热流气体的充分混合,促进反应的进行。
67.本发明的又一具体实施方式中,提供上述工艺方法在如下任意一种或多种中的应用:
68.1)粉煤灰制备,副产可发电的蒸汽;
69.2)煤气化细渣资源化/无害化处理;
70.3)煤气化细渣固废的减量化处理。
71.以下通过实施例对本发明做进一步解释说明,但不构成对本发明的限制。应理解这些实施例仅用于说明本发明而不用于限制本发明的范围。
72.实施例1
73.一种煤气化细渣的脱碳处理工艺方法,所述方法包括:将煤气化细渣在配入3%含氧转化催化剂的情况下,脱碳转化成粉煤灰,同时释放热能。
74.所述煤气化细渣其含水量控制为30-35%左右,煤气化细渣粒径为250~500μm。
75.所述高温环境为900-950℃。
76.所述脱碳处理工艺方法在催化转化装置内进行:
77.所述催化转化装置可以为催化转化炉,所述催化转化炉为立式结构,由下至上依次包括:蓄热催化引燃区、催化转化扩张区、蓄能催化转化区和催化完全转化区;
78.其中,所述蓄热催化引燃区通过风力扰动,在转化催化剂的作用下,传热引燃气化细渣脱碳,更具体的,所述蓄热催化引燃区下方设置高温风室,所述高温风室释放高温空气约500-600℃,所述高温空气自下而上运动,从而为蓄热催化引燃区等区域提供高温空气,并为煤气化渣提供风动力支持,使得煤气化细渣可以在装置内向上运动,从而进入上述各区域内。
79.所述蓄热催化引燃区选用物料为石英砂。
80.所述催化转化扩张区用于尽快扩张面积,用于降低煤气化细渣的上浮速度;
81.所述蓄能催化转化区用于将煤气化细渣有限的转化热留在炉膛内,因此所述蓄能催化转化区作蓄热保温处理,该区域内炉壁内侧墙体砖采用异型蓄热式高铝砖,从而防止或减少热量和被带走。
82.所述催化完全转化区用于将进入该区域煤气化细渣中的少量的碳,进一步转化彻底。在本实施例中,在进入该催化完全转化区之前,煤气化细渣的转化时间已达约4秒,转化率已达约80%。从而使得进入该区域内,进一步脱碳从而实现对煤气化细渣的完全转化,得到粉煤灰(建材)产品。
83.为便于将煤气化细渣(同时混入含氧转化催化剂)输送至上述催化转化装置中,在所述蓄热催化引燃区与催化转化扩张区之间设置有煤气化细渣输送机构,所述输送机构为铰刀式输送机构。
84.在所述催化完全转化区上部设置有转化气出口,从而用于排出转化气体进入余热回收装置回收热量。
85.其中,所述含氧转化催化剂制备方法如下:将醋酸铜与2,2'-联嘧啶溶按摩尔比5:1置于乙醇中,然后向其中加入堇青石质多孔陶瓷(其质量为醋酸铜的100倍),在60℃条件下混合均匀,然后80℃去除乙醇,将残留产物粉碎后进行高温煅烧处理。所述高温煅烧具体工艺为:以4℃速率升温至850℃,持续时间为2小时。控制含氧转化催化剂粒径为2-5mm。
86.实施例2
87.一种煤气化细渣的脱碳处理工艺方法,所述方法包括:将煤气化细渣在含氧转化催化剂的作用下,高温脱碳转化成粉煤灰,同时释放热能。
88.所述煤气化细渣其含水量控制为30-35%左右,煤气化细渣粒径为300~800μm。。
89.所述高温环境为900-950℃,配入含氧转化催化剂2%。
90.所述脱碳处理工艺方法可以在催化转化装置内进行:
91.所述催化转化装置可以为催化转化炉,所述催化转化炉为立式结构,由下至上依次包括:蓄热催化引燃区、催化转化扩张区、蓄能催化转化区和催化完全转化区;
92.其中,所述蓄热催化引燃区通过风力扰动,转化催化剂的作用下,传热引燃催化脱碳,更具体的,所述蓄热催化引燃区下方设置高温风室,所述高温风室释放高温空气约500-600℃,所述高温空气自下而上运动,从而为蓄热催化引燃区等区域提供高温空气,并为煤气化渣提供风动力支持,使得煤气化细渣可以在装置内向上运动,从而进入上述各区域内。
93.所述蓄热催化引燃区选用物料为焦宝石。
94.所述催化转化扩张区用于尽快扩张面积,用于降低煤气化细渣的上浮速度;
95.所述蓄能催化转化区用于将煤气化细渣有限的转化热留在炉膛内,因此所述蓄能催化转化区作蓄热保温处理,更具体的,该区域内炉壁内侧墙体砖采用异型蓄热式高铝砖,从而防止或减少热量损失和被带走。
96.所述催化完全转化区用于将进入该区域煤气化细渣中的少量的碳,进一步转化彻底。在本实施例中,在进入该催化完全转化区之前,煤气化细渣的转化时间已达5秒,转化率已达约75%。从而使得进入该区域内,进一步氧化从而实现对煤气化细渣的完全转化,得到粉煤灰产品。
97.为便于将煤气化细渣(同时混入含氧转化催化剂)输送至上述催化转化装置中,在所述蓄热催化引燃区与催化转化扩张区之间设置有煤气化细渣输送机构,所述输送机构为铰刀式输送机构。
98.在所述催化完全转化区上部设置有转化气出口,从而用于排出转化气体,进入余热锅炉回收热量。
99.其中,所述含氧转化催化剂制备方法同实施例1。
100.实施例3
101.一种煤气化细渣的脱碳处理工艺方法,所述方法包括:将煤气化细渣在含氧转化催化剂的作用下,脱碳转化成粉煤灰,同时释放热能。
102.所述煤气化细渣其含水量控制为30-35%左右,煤气化细渣粒径为1mm。
103.所述高温环境为800-850℃,配入含氧转化催化剂2%。
104.所述脱碳处理工艺方法可以在催化转化装置内进行:
105.所述催化转化装置可以为催化转化炉,所述催化转化炉为立式结构,由下至上依次包括:蓄热催化引燃区、催化转化扩张区、蓄能催化转化区和催化完全转化区;
106.其中,所述蓄热催化引燃区通过风力扰动,在转化催化剂的作用下,传热引燃催化脱碳,更具体的,所述蓄热催化引燃区下方设置高温风室,所述高温风室释放高温空气300-400℃,所述高温空气自下而上运动,从而为蓄热催化引燃区等区域提供高温空气,并为煤气化渣提供风动力支持,使得煤气化细渣可以在装置内向上运动,从而进入上述各区域内。
107.所述蓄热催化引燃区选用物料可以为流化床锅炉炉渣。
108.所述催化转化扩张区用于尽快扩张面积,用于降低煤气化细渣的上浮速度。
109.所述蓄能催化转化区用于将煤气化细渣有限的转化热留在炉膛内,因此所述蓄能催化转化区作蓄热保温处理,更具体的,该区域内炉壁内侧墙体砖采用异型蓄热式高铝砖,从而防止或减少热量损失和被带走。
110.所述催化完全转化区用于将进入该区域煤气化细渣中的少量的碳,进一步转化彻底。在本实施例中,在进入该催化完全转化区之前,煤气化细渣的转化时间已达6秒,转化率已达80%。从而使得进入该区域内,进一步氧化从而实现对煤气化细渣的完全转化,得到粉煤灰产品。
111.为便于将煤气化细渣(同时混入含氧转化催化剂)输送至上述催化转化装置中,在所述蓄热催化引燃区与催化转化扩张区之间设置有煤气化细渣输送机构,所述输送机构为铰刀式输送机构。
112.在所述催化完全转化区上部设置有转化气出口,从而用于排出转化气体,进入余热锅炉回收热量。
113.其中,所述含氧转化催化剂制备方法同实施例1。
114.应该注意的是,以上实例仅用于说明本发明的技术方案而非对其进行限制。尽管参照所给出的实例对本发明进行了详细说明,但是本领域的普通技术人员可根据需要对本发明的技术方案进行修改或者等同替换,而不脱离本发明技术方案的精神和范围。
再多了解一些
本文用于企业家、创业者技术爱好者查询,结果仅供参考。