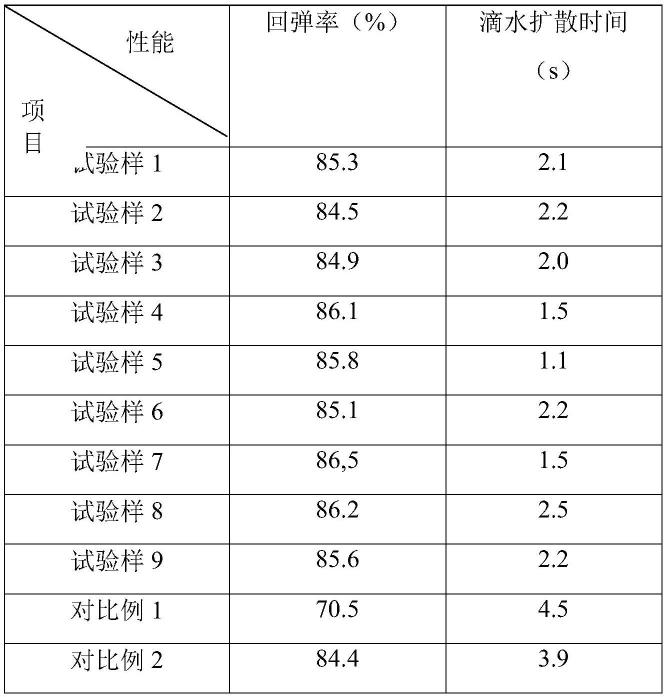
1.本技术涉及纺织技术领域,更具体地说,它涉及一种涤纶纬弹双层充绒布的生产工艺。
背景技术:
2.充绒布是一种线密度值较小而整体密度较大的薄型织物,由于常用做羽绒服装、羽绒被的面料,且能放置羽绒向外钻出,故又称羽绒布、防绒布或防羽布。
3.目前市场上的防羽面料一般是全涤纶或者是在做了涂层来防止羽毛跑毛的,一般仅用于做雨伞或者羽绒服等,由于这种面料手感偏硬,品质不够细腻,面料摩擦声响大,特别是使用几次后,易失去弹性,使得整个服装或被子松垮,并不适合作为羽绒被或者羽绒服面料使用。
4.针对上述中的相关技术,发明人认为传统的涤纶纬弹双层充绒布存在弹性差的问题,因此限制了其使用与发展。
技术实现要素:
5.为了提高涤纶纬弹双层充绒布的弹性,本技术提供一种涤纶纬弹双层充绒布的生产工艺。
6.本技术提供的一种涤纶纬弹双层充绒布的生产工艺,采用如下的技术方案:一种涤纶纬弹双层充绒布的生产工艺,包括以下步骤:s1,纱线选择:选择超细旦涤纶丝作为经纱,选择氨纶包覆纱作为纬纱;所述氨纶包覆纱的制备方法,包括以下步骤:s10,对碱处理后的涤纶纤维浸渍于交联剂溶液中,与1000-5000da分子量的丝素蛋白溶液混合反应得到改性涤纶纤维;s20,以氨纶和改性涤纶纤维为原料,通过混纤工艺,制备得到氨纶包覆涤纶纱;s2,整经:采用分批整经的方式分别对所述经纱和纬纱进行整经;s3,上浆:使用配制好的浆料对整经后的经纱和纬纱进行上浆,并进行烘干处理。
7.s4,织造:将上浆后的经纱和纬纱采用表里换层的双层织造工艺,织造出双层平纹坯布;s5,染色后整理:将坯布进行冷堆处理、退浆、预定型、染色、还原清洗、热定型后整理得到涤纶纬弹双层充绒布。
8.通过采用上述技术方案,涤纶具有断裂强度高,具有良好的耐热性和热塑性,但其作为疏水性纤维其吸湿性极差;而丝素蛋白具有良好的柔韧性和抗拉强度、透气透湿和缓释性等;本技术通过涤纶纤维采用碱处理后使得纤维缝制链上释放出反应位点,同时采用限定1000-5000da相对分子量较小并且集中分布的丝素蛋白介质改性碱处理后的纤维,利用共价结合的原理使得上述特定分子量的丝素蛋白牢固的引入涤纶纤维表面,改善纤维吸湿性;通过具有优异弹性的氨纶和强度高的改性涤纶纤维制成出的氨纶包覆涤纶纱,赋予
面料优异的弹性、结构强度和良好的吸湿效果。本技术通过采用超细旦涤纶和氨纶包覆纱交织制成的双层充绒布,在保留了良好力学性能的同时,利用氨纶包覆纱优异的特性,提高了双层充绒布的弹性和吸湿效果。
9.优选的,所述s10中,1000-5000da分子量的丝素蛋白溶液的制备方法为:将家蚕蚕丝用碳酸钠进行脱胶,然后加入中性盐溶液溶解,制备丝素蛋白溶解液;将丝素蛋白溶解液离心处理,上清液进行透析收集丝素蛋白水溶液中的10kd以下的丝素蛋白,透析后进行冻干得到固体丝素蛋白,再次加入葡聚糖sephadex g25柱中,用灭菌水洗脱丝素蛋白,分管收集,筛选得到1000-5000da的小分子量丝素蛋白后配制成50mg/ml水溶液。
10.通过采用上述技术方案,以家蚕蚕丝为原料,在非强酸强碱等较温和的条件下进行脱胶处理,利用中性盐溶液对脱胶后的丝素蛋白进行降解并用凝胶过滤法对降解后的蛋白进行部分纯化,得到分子量较小的水溶性丝素蛋白,制备方法简单,蛋白活性高,产率高,纯度较高,溶解性好,且未破坏丝素蛋白的内部基团结构。
11.优选的,所述s10中,所述交联剂为聚乙二醇二缩水甘油醚或聚乙二醇二丙烯酸酯,且交联剂与丝素蛋白的质量比为1:(1-5)。
12.通过采用上述技术方案,由于聚乙二醇具有两个不同官能团的异端基双官能团,因此其具有良好的两相溶解能力和生物相容性;而聚乙二醇类交联剂具有的结构特异性与丝素蛋白结合后具有更大的表观分子量,即使得丝素蛋白在一个连接位点上可结合两条聚乙二醇链,减少了丝素蛋白失活的机会,提高了改性后的蛋白活性。通过优化交联剂与丝素蛋白的质量比,使得丝素蛋白中的氨基、羧基和其他可交联基团与交联剂发生交联生成的醛亚胺中的碳氢双键与碳碳双键形成共轭体系,共轭体系使得丝素蛋白形成的网状结构得到增强,而产物的疏水性则提高了蚕丝蛋白的抗水解性,保证了其活性。
13.优选的,所述s10中,所述碱处理时,温度为30-40℃,处理时间为1-3h。
14.通过采用上述技术方案,涤纶表面被碱刻蚀后,表面形成凹坑(反应位点),通过控制涤纶纤维碱处理时的参数,不仅提高了反应位点与丝素蛋白的反应效果,也增加了织物交织点的空隙,使得织物手感柔软,改善了涤纶纤维的吸湿排汗性。
15.优选的,所述s10中,所述中性盐溶液为氯化钙-乙醇、溴化锂-乙醇和碘化钡-乙醇中的一种。
16.通过采用上述技术方案,丝素蛋白不溶于水,可溶于强酸、强碱和一些中性盐溶液中,但是溶于强酸和强碱的丝素蛋白的生物活性已在较大程度上被破坏。中性盐中氯化钙、溴化锂和碘化钡溶液中,只有很少丝素蛋白降解,在乙醇溶液中,丝素蛋白几乎不发生溶解,而在氯化钙-乙醇、溴化锂-乙醇和碘化钡-乙醇溶液中,脱胶丝素蛋白降解速度快且降解量多。
17.优选的,所述s10中,所述中性盐溶液为氯化钙-乙醇溶液,且乙醇与氯化钙的质量比为(2-4):4。
18.通过采用上述技术方案,由于溴化锂和碘化钡对人体有危害,因此不适宜用于降解丝素蛋白;由于丝素蛋白本身的原因和氯化钙降解丝素蛋白的随机性,使得本技术降解得到的丝素蛋白分子量分布广;其中乙醇与氯化钙质量比为1:2时,在低乙醇浓度下,丝素蛋白降解量低,降解速度慢,使得降解的丝素蛋白分子量不能达到10000da以下;当乙醇与氯化钙的质量比为3:4时,形成的氯化钙体系对丝素蛋白的降解能力最强,且产率高,产物
溶解性好,分子量分布集中在5000-10000da;当乙醇与氯化钙的质量比为4:4时,在高乙醇浓度下,丝素蛋白降解后的产物分子链分布变得更为集中,且小分子量蛋白更小,分子量分布集中在1000-5000da。
19.优选的,所述s5中,预定型时,温度为180-190℃,速度为25-35m/min,超喂为10-20%。
20.通过采用上述技术方案,在染色前进行预定型可以防止坯布在染色过程中因收缩严重而影响染色效果;预定型的目的是消除氨纶的内应力,以使织物门幅、平方米克重及织物弹性等质量指标处于一种稳定状态,容易控制,使其在后续工序中不会发生较大变化。预定型温度过高、时间过长会使织物手感发硬、颜色发黄,织物强力及弹性都会有所损伤;温度太低、时间过短则抗皱性不好;同时预定型时给坯布打上正超喂,且在速度较低的状态下进行以便更好的提高制备效果。
21.优选的,所述s5中,染色时以1℃/min将染色浴液升至115-125℃,保温40-60min,然后以2℃/min将染色浴液冷却,排水清洗。
22.通过采用上述技术方案,由于织物中既存在涤纶纤维也存在氨纶纤维,而涤纶纤维必须高温高压染色,氨纶纤维染色时不耐高温,因此,在染整加工时必须兼顾两种纤维的性能;由于氨纶纤维会在高温染色时发生脆化,故而染色浴液的温度为115-125℃,而氨纶经长时间染色后,对其断裂强度和弹性回复率的影响较大,为减小对氨纶的损伤,染色时间控制在40-60min,且染色升温速度应控制在1℃/min以内,过快会因保温时间不足引起色花等瑕疵;而急速降温会造成坯布鸡爪印,甚至色花。
23.优选的,所述s5中,还原清洗时,清洗液以2.5℃/min升至80-90℃,保温25-35min,充分水洗。
24.通过采用上述技术方案,通过控还原清洗时的工艺参数,缩短了工艺流程,节省了时间和资源,防止氨纶沾色效果好,不影响吸湿排汗效果,色变小。
25.优选的,所述s5中,热定型后整理时,温度为180-190℃,速度为25-35m/min,超喂为5-10%。
26.通过采用上述技术方案,织物在染色后不宜存放太久,否则布面风干易产生风干印或鸡爪痕等缺陷;通过对织物进行后整理,并控制后整理时的工艺参数,不仅可以提高织物的制备效果,还可以赋予织物服用性能。
27.综上所述,本技术具有以下有益效果:1、本技术通过采用丝素蛋白对涤纶纤维进行改性使得涤纶纤维的吸湿性得以改善,从而为利用氨纶和改性涤纶纤维制成的氨纶包覆纱不仅具有优异的弹性、强度和良好的吸湿性,进而使得制备的涤纶纬弹双层充绒布具有优异的弹性和吸湿性;2、本技术通过在坯布染色前进行预定型,防止坯布在染色过程中因收缩严重而影响染色效果,且通过控制预定时的温度和时间使得织物的手感更加柔软,且保证了织物的强度和弹性;3、本技术通过对染色后的坯布进行还原清洗,起来通过控制清洗时的各参数,提高了工作效率,且防止氨纶沾色,确保了坯布的吸湿性。
具体实施方式
28.以下结合制备例和实施例对本技术作进一步详细说明。
29.制备例和实施例中所用的相关原材料中:超细旦涤纶丝30d/48f;聚乙二醇二缩水甘油醚的密度为1.14g/ml(25℃),cas:39443-66-8;聚乙二醇二丙烯酸酯密度为1.12g/ml(25℃),cas:26570-48-9;家蚕蚕丝的蛋白质含量为97.34%,纤维含量为0.39%;葡聚糖sehadex g25分子量为272.25,cas:9041-35-4。
30.制备例制备例1本技术制备例公开了一种氨纶包覆纱的制备方法,具体方法如下:s10,改性涤纶纤维的制备方法:s101,将2mg家蚕蚕丝加入100ml0.5%na2co3溶液中,充分混匀后脱气10min,使蚕丝充分浸没在溶液中,密封后置于37℃的摇床中,进行振荡。将混悬液进行过滤,并用0.5%na2co3溶液清洗滤饼,之后加入等体积的0.5%na2co3溶液,混匀后继续置于摇床中脱胶,反复操作3次;s102,将脱胶后的2mg蚕丝置于140ml蒸馏水中,再加入20%乙醇-40%氯化钙溶液,密封置于37℃的摇床中反应,进行振荡,取出降解液后离心30min,上清液用截流分子量为10kd的透析袋透析,除去小分子和盐,透析完毕后把透析液冻干即得固体可溶性丝素蛋白;s103,将固体可溶性丝素蛋白加入葡聚糖sehadex g25柱中,并用霉菌水洗脱实属蛋白,分管收集,筛选得到1000-5000da的小分子量丝素蛋白,并加去离子水将其配制成50mg/ml的丝素蛋白水溶液;s104,将涤纶纤维采用氢氧化钠溶液处理,洗涤后得到碱处理后的涤纶纤维,其中碱处理时的温度为30℃,处理时间为3h,且碱处理时也可选择其他碱性溶液;将5g碱处理后的涤纶纤维浸渍在5l聚乙二醇二缩水甘油醚中,并加入5ml丝素蛋白水溶液混合反应后得到改性涤纶纤维;s20,氨纶包覆纱的制备:以氨纶和改性涤纶纤维为原料,通过混纤工艺,制备得到氨纶包覆涤纶纱,其中氨纶在氨纶包覆纱中的质量分数为10%;以杜邦的50d氨纶为包覆纱,牵伸倍数为3,以80d/24f的改性涤纶纤维为外包覆纱,控制包覆时的超喂率为10%。
31.制备例2本制备例与制备例1基本相同,不同之处在于:s102中,将脱胶后的2mg蚕丝与28ml乙醇和56ml溴化锂溶液混合。
32.制备例3本制备例与制备例1基本相同,不同之处在于:s102中,将脱胶后的2mg蚕丝与28ml乙醇和56ml碘化钡溶液混合。
33.制备例4本制备例与制备例1基本相同,不同之处在于:s102中,将脱胶后的2mg蚕丝与42ml乙醇和56ml氯化钙溶液混合。
34.制备例5本制备例与制备例1基本相同,不同之处在于:s102中,将脱胶后的2mg蚕丝与56ml
乙醇和56ml氯化钙溶液混合。
35.制备例6本制备例与制备例1基本相同,不同之处在于:s104中,碱处理时的温度为40℃,处理时间为1h;将聚乙二醇二缩水甘油醚替换为聚乙二醇二丙烯酸酯。
36.制备例7本制备例与制备例1基本相同,不同之处在于:s104中,将5g碱处理后的涤纶纤维浸渍在15l聚乙二醇二缩水甘油醚中。
37.制备例8本制备例与制备例1基本相同,不同之处在于:s104中,将5g碱处理后的涤纶纤维浸渍在25l聚乙二醇二缩水甘油醚中。
38.制备例9本制备例与制备例1基本相同,不同之处在于:省略s10,s20中,氨纶包覆纱的制备:以氨纶和涤纶纤维为原料,通过混纤工艺,制备得到氨纶包覆涤纶纱,其中氨纶在氨纶包覆纱中的质量分数为10%;以杜邦的50d氨纶为包覆纱,牵伸倍数为3,以80d/24f的涤纶纤维为外包覆纱,控制包覆时的超喂率为10%。实施例
39.实施例1本技术实施例公开了一种涤纶纬弹双层充绒布的生产工艺,具体方法如下:s1,选原料纺丝:选用30d/48f,dty涤纶作为经纱,氨纶包覆纱作为纬纱,其中经纱克重为103g/m,纬纱克重为160g/m,其中氨纶包覆纱采用制备例1所得;s2,整经:采用分批整经的方式,对经纱和纬纱分别进行整经,其中整经速度为300m/min,卷绕密度为0.50g/cm3;s3,上浆:将制备好的浆料泵入上浆机中,开机车速为250m/min,上浆率为10%,浆槽的两根压浆辊压力为:第一根压浆辊为3.5kn,第二根压浆辊为3.0kn,伸长率为0.2%,浆槽温度为50℃,烘房温度最高为145℃,烘筒温度最高为120℃,浆液采用普通浆料即可,在此不做过多赘述;s4,织造:上浆后的经纱和纬纱进行并轴,并轴轴数为13,车速为65m/min,干区张力400n,卷绕张力0.25cn/dtex,退绕张力为0.15cn/dtex,托纱辊压力500n;采用分绞-穿综,穿综时选用16片,穿综后采用喷气织机进行表里换层织造得到双层坯布,其中车速控制在650r/min,上机张力2000n,表组织和里组织为平稳组织,坯布幅宽为132cm;s5,对坯布进行冷堆处理、退浆、预定型、染色、还原清洗、热定型后整理得到涤纶纬弹双层充绒布,其中预定型时的温度为180℃,速度为25m/min,超喂为10%;染色时以1℃/min将染色浴液升至115℃,保温60min,然后以2℃/min将染色浴液冷却,排水清洗;还原清洗时,清洗液以2.5℃/min升至90℃,保温25min,充分水洗;热定型后整理时,温度为180℃,速度为25m/min,超喂为5%,且其中的染料和退浆液均采用常规试剂,在此不再过多赘述。
40.实施例2-8实施例2-8与实施例1基本相同,不同之处在于,s1中,所采用的氨纶包覆纱为制备例2-8所得。
41.实施例9本实施例与实施例的不同之处在于:s5中,预定型时的温度为190℃,速度为35m/min,超喂为20%;染色时以1℃/min将染色浴液升至125℃,保温40min,然后以2℃/min将染色浴液冷却,排水清洗;还原清洗时,清洗液以2.5℃/min升至80℃,保温35min,充分水洗;热定型后整理时,温度为190℃,速度为35m/min,超喂为10%。
42.对比例对比例1本对比例与实施例1不同之处在于,s1中,选用30d/48f,dty涤纶作为经纱和纬纱,其中经纱和纬纱的克重为103g/m;对比例2本对比例与实施例1不同之处在于,s1中,氨纶包覆纱采用制备例9所得。
43.性能检测试验采用相同重量的由实施例1-9获得的涤纶纬弹双层充绒布作为试验样1-9,采用与试验样相同重量的由对比例1-2获得的涤纶纬弹双层充绒布作为对照样1-2。对试验样和对照样进行性能检测,结果如表1。
44.1.回弹性测试参照astmd 3107,其中试样尺寸为64
×
560mm,剪取试样前需将样品置于astm d17756规定的标准环境下调湿平衡(温度为21
±
1℃,相对湿度65
±
2%),对试验样和对照样分别进行测试,并将测试结果记录在表1中。
45.2.吸湿性测试吸湿排汗性能参照gb/t 21655.1-2008《纺织品吸湿速干性的评定第1部分:单项组合试验法》的要求对试验样和对照样分别进行测试,并将测试结果记录在表1中。
46.表1性能检测数据表
参照表1,结合实施例1和对比例1和2,可以看出,当采用涤纶纤维作为制备涤纶纬弹双层充绒布的经纱和纬纱时(对比例1),由于原材料涤纶的弹性比起氨纶较差,且其本身的透气吸湿性极差,故而制备的试验的弹性和吸湿性均较差;当采用氨纶和涤纶合成氨纶包覆纱作为纬纱时(对比例2),由于氨纶具有良好的弹性,但涤纶较差的吸湿性还是会影响试样整体的吸湿效果,因而试样的吸湿性较差。
47.参照表1,结合实施例1-3,可以看出,改变中性盐溶液的种类,制备出的试样均具有良好的弹性和吸湿性,但由于溴化锂和碘化钡对人体有危害,因此不建议在日常生产中使用,故将氯化钙-乙醇溶液作为中性盐溶液是最好的选择。
48.参照表1,结合实施例1、4和5,可以看出,改变氯化钙与乙醇的质量比可以看出,当氯化钙与乙醇的质量比为4:4时,试样的吸湿性达到最优;当氯化钙与乙醇的质量比为4:2时,乙醇相对浓度相对较低,丝素蛋白降解量低,降解速度慢,使得降解的丝素蛋白分子量不能达到10000da以下;当乙醇与氯化钙的质量比为3:4时,形成的氯化钙体系虽对丝素蛋白的降解能力最强,但形成的丝素蛋白的分子量主要集中在5000-10000da,不符合要求;当乙醇与氯化钙的质量比为4:4时,溶液中乙醇含量相对较高,丝素蛋白降解后的产物分子链分布变得更为集中,且分子量蛋白更小,分子量分布主要集中在1000-5000da,更符合要求,制备的小分子丝素蛋白与碱处理后的涤纶反应效果更好,从而对涤纶的吸湿性改善效果更为显著,试验的吸湿性最好。
49.参照表1,结合实施例1、7和8,可以看出,改变交联剂(聚乙二醇二缩水甘油醚)与丝素蛋白的质量比,制备出的试样仍然具有优异的回弹性和良好的吸湿性;但当交联剂与丝素蛋白的质量比为1:3时,丝素蛋白中的氨基、羧基以及其他交联基团与交联剂发生交联
反应的效果更好,从而使得丝素蛋白的网状结构得到进一步增强,形成的产物的疏水性提高了蚕丝蛋白的抗水解性,从而使得丝素蛋白的活性更高,进一步提高了其对涤纶的改性效果,使得试样整体的吸湿性达到最优。
50.本具体实施例仅仅是对本技术的解释,其并不是对本技术的限制,本领域技术人员在阅读完本说明书后可以根据需要对本实施例做出没有创造性贡献的修改,但只要在本技术的权利要求范围内都受到专利法的保护。
再多了解一些
本文用于企业家、创业者技术爱好者查询,结果仅供参考。