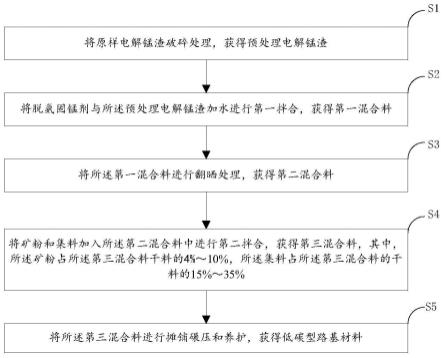
1.本发明涉及固体废弃物资源化利用技术领域,特别涉及一种低碳型路基材料及其制备方法。
背景技术:
2.金属锰是一种重要的金属元素和工业原料,广泛运用于各个行业,中国电解锰的总产量维持在150万吨/年左右,约占世界总产量的98%,电解锰渣的冶炼技术属于湿法冶炼,这种方法每生产1吨电解锰约产生12吨左右的电解锰渣。电解锰渣的年生产约1000万吨左右,累计堆存量已经达到15000万吨。电解锰渣中含有大量的金属污染物锰以及非金属污染物氨氮,严重制约了电解锰渣的资源化利用。多数电解锰渣被随意丢弃在没有防渗处理的堆存场,大量的污染物在降雨淋溶、地表径流以及地下渗流的作用下迁移到周围的土水中,污染周围环境,人们长期暴露在金属超标的环境中容易导致各种疾病的产生,此外,电解锰渣中的非金属污染物氨氮容易裹挟重金属流入周围水体,导致水体富营养化及金属含量超标,这严重制约了电解锰行业的可持续发展,因此,亟需寻求合理的资源化利用方式解决电解锰渣大量堆存现状。
3.目前电解锰渣的资源化利用主要运用在农业、新型材料、建材等方面。锰渣在农业上主要用作土壤改良剂以及肥料,但由于锰渣中含有的硫酸根离子会腐蚀植物根系,另外锰渣中的金属污染物会富集在植物中,这些都制约了其在农业上的运用;此外电解锰渣也可用于生产微晶玻璃、新型陶瓷等材料,但这些方法并不能实现锰渣的大量消减;近年来,废弃尾矿等大宗固废用于生产建筑材料等已成为研究热点,建筑材料具有消耗量大、价格高昂等特点,尾矿用作建材生产可以在实现尾矿大量消减的同时创造一定的经济价值。电解锰渣在建筑材料上的运用有制备水泥、混凝土、免烧砖、路基几个方面,电解锰渣用于制备水泥、混凝土存在用料少效果差等缺点,免烧砖由于缺乏当地市场很难实现电解锰渣的大规模减量,而路基材料则有消耗大,强度要求低等优点,但是传统的电解锰渣制备路基常用石灰、水泥作为固化稳定材料,存在碳排放高、成本大等缺点,因此有必要开发一种利用电解锰渣制备低碳型路基材料的方法。
技术实现要素:
4.本发明目的是提供一种低碳型路基材料的制备方法,将电解锰渣脱氨固锰处理后与矿粉、集料结合,从而增加固化体强度等工程性能,同时实现资源化利用。
5.为了实现上述目的,本发明采用如下技术方案:
6.在本发明的第一方面,提供了一种低碳型路基材料的制备方法,所述方法包括:
7.将原样电解锰渣破碎处理,获得预处理电解锰渣;
8.将脱氨固锰剂与所述预处理电解锰渣加水进行第一拌合,获得第一混合料;
9.将所述第一混合料进行翻晒处理,获得第二混合料;
10.将矿粉和集料加入所述第二混合料中进行第二拌合,获得第三混合料,其中,所述
矿粉占所述第三混合料干料的4%~10%,所述集料占所述第三混合料的干料的15%~35%;
11.将所述第三混合料进行摊铺碾压和养护,获得低碳型路基材料。
12.进一步地,所述预处理电解锰渣的粒径≤5mm。
13.进一步地,所述脱氨固锰剂与所述预处理电解锰渣的质量比为1:(2~16)。
14.进一步地,所述第一混合料的含水率控制在20%~50%。
15.进一步地,所述第一拌合的时间为1~4h。
16.进一步地,所述脱氨固锰剂包括:质量比为(1~2):1的预处理赤泥和碱性固体废弃物;其中,预处理赤泥为将赤泥烘干后经过球磨破碎机破碎至粒径≤200目,筛余量≤2%获得的赤泥。
17.进一步地,所述第二混合料的含水量≤30%。
18.进一步地,所述第二拌合包括:先以60~100转/分的慢速搅拌4~6min,后以160~240转/分的快速搅拌2~4min。
19.进一步地,所述集料由生活垃圾焚烧底渣、建筑垃圾机制砂、尾矿砂,工业废渣颗粒中的一种或多种组成;且所述集料经过破碎且破碎后粒径≤4.75mm。
20.在本发明的第二方面,提供了采用所述方法制备得到的固化体。
21.本发明实施例中的一个或多个技术方案,至少具有如下技术效果或优点:
22.本发明提供的一种低碳型路基材料的制备方法,所述方法包括:将原样电解锰渣破碎处理,获得预处理电解锰渣;将脱氨固锰剂与所述预处理电解锰渣加水进行第一拌合,获得第一混合料;将所述第一混合料进行翻晒处理,获得第二混合料;将矿粉和集料加入所述第二混合料中进行第二拌合,获得第三混合料,其中,所述矿粉占所述第三混合料干料的4%~10%,所述集料占所述第三混合料的干料的15%~35%;将所述第三混合料进行摊铺碾压、养护,获得低碳型路基材料。按上述方法利用氨氮在碱性环境下会溢出以及mn
2
在碱性环境下会生成沉淀的特点,创新性的采用预处理后的碱性固体废弃物对锰渣进行脱氨固锰处理,并利用低碳胶凝材料以及固体废弃物集料对电解锰渣进行固化处理,固化后的材料可用作路基材料,该方法对电解锰渣的资源化利用以及电解锰行业的可持续发展具有长远意义,该低碳型路基材料的固化强度满足路基材料要求且毒性浸出结果满足《gb8978-1996》阈值。具体地:
23.首先经过脱氨处理的电解锰渣在固化时可大大降低孔隙体积从而增加固化体的强度,该方法选用矿粉这种低碳胶凝材料,在碱性环境下可生成aft以及c-s-h凝胶可提高固化体强度,节约了水泥、石灰等传统胶凝材料的使用,降低了碳排放。固化体中增加集料可与胶凝材料结合形成骨架,从而增加固化体强度等工程性能,近些年来,越来越多地区出于环境保护角度考虑开始限制砂石开采,而道路工程又会产生巨大的砂石消耗,因此寻找合适的替代品可节约砂石的使用从而达到环保的目的,该方法选用生活垃圾焚烧底渣、建筑垃圾机制砂,尾矿砂,工业废渣颗粒等制备集料,大量的节约了天然砂石的使用,既节约了生产成本,也消耗了工业废弃物、工业垃圾,实现了变废为宝,以废治废的目的。
附图说明
24.为了更清楚地说明本发明实施例中的技术方案,下面将对实施例描述中所需要使
用的附图作简单地介绍,显而易见地,下面描述中的附图是本发明的一些实施例,对于本领域普通技术人员来讲,在不付出创造性劳动的前提下,还可以根据这些附图获得其它的附图。
25.图1为本发明提供的一种低碳型路基材料的制备方法的流程图;
26.图2为本发明实施例选用的取自广西忻城某堆存场的电解锰渣的主要物相图。
具体实施方式
27.下文将结合具体实施方式和实施例,具体阐述本发明,本发明的优点和各种效果将由此更加清楚地呈现。本领域技术人员应理解,这些具体实施方式和实施例是用于说明本发明,而非限制本发明。
28.在整个说明书中,除非另有特别说明,本文使用的术语应理解为如本领域中通常所使用的含义。因此,除非另有定义,本文使用的所有技术和科学术语具有与本发明所属领域技术人员的一般理解相同的含义。若存在矛盾,本说明书优先。
29.除非另有特别说明,本发明中用到的各种原材料、试剂、仪器和设备等,均可通过市场购买获得或者可通过现有方法获得。
30.本发明实施案例提供一种低碳型路基材料的制备方法,总体思路如下:
31.根据本发明一种典型的实施方式,提供了一种低碳型路基材料的制备方法,如图1所示,所述方法包括:
32.s1、将原样电解锰渣破碎处理,获得预处理电解锰渣;
33.所述步骤s1中,破碎处理后,所述预处理电解锰渣的粒径≤5mm。
34.作为一种具体的实施方式,所述步骤s1包括:将原样电解锰渣破碎使得粒径≤5mm,测算破碎电解锰渣含水率后将其倒入反应釜中。
35.上述技术方案中,所述预处理电解锰渣的粒径≤5mm可以提高脱氨固锰效率,粒径大于5mm的电解锰渣颗粒,其内部可能因为无法接触外界从而影响其脱氨固锰;
36.s2、将脱氨固锰剂与所述预处理电解锰渣加水进行第一拌合,获得第一混合料;
37.所述步骤s2中,
38.所述脱氨固锰剂与所述预处理电解锰渣的质量比为1:(2~16)。
39.所述脱氨固锰剂包括:质量比为(1~2):1的预处理赤泥和碱性固体废弃物;其中,预处理赤泥为将赤泥烘干后经过球磨破碎机破碎至粒径≤200目,筛余量≤2%获得的赤泥;所述碱性固体废弃物经过烘干后破碎,且破碎后粒径≤200目,筛余量≤2%。
40.作为一种具体的实施方式,将赤泥防放置在105℃烘箱中烘干,烘干后含水≤1%。后将烘干后的赤泥经过球磨破碎机破碎至粒径≤200目,筛余量≤2%,获得预处理赤泥。球磨后的赤泥活性更好,脱氨固锰效率更高。
41.同样的球磨破碎可以使碱性固体废弃物获得更好的反应活性。所述碱性固体废弃物应取电石渣、粉煤灰、煤矸石等碱性固废中的一种或者多种。
42.使用单一材料难以获得理想的脱氨固锰效果,因此采用赤泥复合其他碱性固体废弃物制备脱氨固锰材料。预处理赤泥和碱性固体废弃物的质量比为(1~2):1时脱氨效果最好。
43.电解锰渣中氨氮在碱性环境下生成氨气以及mn
2
会在碱性环境下生成沉淀的特
点,主要有以下反应生成:
44.nh
4
oh-=h2o nh3↑
45.mn
2
2oh-=mn(oh)2↓
46.采用球磨破碎的处理方式与处理赤泥和其它碱性固体废弃物,可增加其活性和细度,单独使用赤泥难以获得理想的脱氨固锰效果,利用赤泥复合其他碱性固体废弃物制备脱氨固锰剂,可在与水反应时水解出更多的oh-,从而增加脱氨固锰效率。经过脱氨处理的电解
47.锰渣在固化时可大大降低孔隙体积从而增加固化体的强度。
48.作为一种优选的实施方式,所述脱氨固锰剂与所述预处理锰渣的质量比为1:(2~16)。所述添加比例,脱氨固锰效率更高;所述脱氨固锰剂添加过少不利于提高脱氨固锰效率,添加过多,会使混合料整体ph过高而影响环境;
49.作为一种优选的实施方式,所述第一混合料的含水率控制在20%~50%。该范围的含水率可以提供脱氨固锰剂反应所需必要的溶液,同时限制其高位含水率可以节约反应完成后翻晒的时间。
50.作为一种优选的实施方式,所述第一拌合的时间为1~4h。
51.所述步骤s2在脱氨反应釜中进行。脱氨反应釜中应该配有搅拌装置、加水装置、以及氨气收集装置,其中搅拌装置可以使反应更加充分均匀,加水装置用于调节混合料的含水率,氨气收集装置用于回收氨气避免大气污染。
52.s3、将所述第一混合料进行翻晒处理,获得第二混合料;
53.所述步骤s3中,
54.所述第二混合料的含水率≤30%。该范围的含水率可以保证第三混合料的含水不会过高,第三混合物含水率若过高不利于制样以及实际工程中的摊铺碾压。
55.s4、将矿粉和集料加入所述第二混合料中进行第二拌合,获得第三混合料,其中,所述矿粉占所述第三混合料干料的4%~10%,所述集料占所述第三混合料的干料的15%~35%;
56.所述步骤s4中,
57.所述第二拌合包括:先以60~100转/分的慢速搅拌4~6min,后以160~240转/分的快速搅拌2~4min。这样有利于充分混合各个组分。
58.所述集料由生活垃圾焚烧底渣、建筑垃圾机制砂、尾矿砂,工业废渣颗粒中的一种或多种组成;且所述集料经过破碎且破碎后粒径≤4.75mm。所述集料经过破碎且破碎后粒径≤4.75mm,满足《公路路面基层施工技术细则》jtg/t f20-2015。
59.所述矿粉占所述第三混合料干料的4%~10%,所述集料占所述第三混合料的干料的15%~35%的原因:可在保证必要工程性能的同时节约用料;
60.作为一种具体的实施方式,将矿粉和集料同时加入搅拌站中,拌合得到第三混合料。
61.s5、将所述第三混合料进行静压制样,获得低碳型路基材料。
62.根据本发明另一种典型的实施方式,提供了采用所述方法制备得到的固化体。
63.所用材料都为固体废弃物以及工业垃圾,在节约生产成本的同时实现固废的大量消减;该方法选用矿粉这种低碳胶凝材料,在碱性环境下可生成aft以及c-s-h凝胶可提高
固化体强度,节约了水泥石灰等传统胶凝材料的使用,降低了碳排放。固化体中增加集料可与胶凝材料结合形成骨架,从而增加固化体强度等工程性能,近些年来,越来越多地区出于环境保护角度考虑开始限制砂石开采,而道路工程又会产生巨大的砂石消耗,因此寻找合适的替代品可节约砂石的使用从而达到环保的目的,该方法选用生活垃圾焚烧底渣、建筑垃圾机制砂,尾矿砂,工业废渣颗粒等制备集料,大量的节约了天然砂石的使用,既节约了生产成本,也消耗了工业废弃物、工业垃圾,实现了变废为宝,以废治废的目的。
64.下面将结合实施例、对比例及实验数据对本技术的一种低碳型路基材料的制备方法进行详细说明。
65.本发明实施例选用赤泥、电石渣制备脱氨固锰剂,选用生活垃圾焚烧底渣制备集料,其中赤泥取自河南郑州某炼铝厂,电石渣取山东青岛某乙炔气生产厂,生活垃圾焚烧底渣取自湖北武汉某垃圾焚烧厂,s95矿粉购自宁夏某厂家。
66.实施例1
67.在本实施例提供了一种低碳型路基材料的制备方法,包括以下步骤:
68.s1、将取得的原装电解锰渣破碎至粒径≤5mm,利用酒精燃烧法测量其含水率为22%。
69.本发明实施例选用的电解锰渣取自广西忻城某堆存场,其主要物相如图2所示,主要化学组成如表1所示。
70.表1电解锰渣xrf
[0071][0072]
s2、将赤泥、电石渣、生活垃圾焚烧底渣放置105℃烘箱,烘干至含水率≤1%。将赤泥、电石渣分别球磨破碎,破碎后粒径≤200目,筛余量≤2%。取赤泥500g、电石渣500g混合制备脱氨固锰剂。
[0073]
取破碎后的电解锰渣1220g加入反应釜中。向反应釜中加入250g脱氨固锰剂,电解锰渣与脱氨固锰剂的干重比为1:4。
[0074]
向反应釜中加入180g水,拌合得到第一混合物,第一混合物的含水约为32%。
[0075]
s3、将第一混合物取出翻晒,翻晒后得到第二混合物,第二混合物含水率为25%。
[0076]
s4、将生活垃圾焚烧底渣破碎至粒径≤4.75mm,用作集料。
[0077]
将第二混合物全部加入搅拌锅中,向搅拌锅中加入300g集料以及80g s95矿粉,搅拌得到第三混合料,其中集料约占第三混合料干重的18.40%,s95矿粉约占第三混合料干重的4.9%。
[0078]
s5、准确称取189g第三混合物,使用50mm*50mm的圆柱形模具静压制样,制样后在22℃,98%湿度养护箱中养护7d。所制样品平均无侧线抗压强度2.1mpa,样品经过《hj299-2010》浸出方法浸出,浸出液浓度满足《gb8978-1996》。
[0079]
实施例2
[0080]
本实施例提供了一种低碳型路基材料的制备方法,所述矿粉占所述第三混合料干料的4%,所述集料占所述第三混合料的干料的15%;其他步骤同实施例1。
[0081]
实施例3
[0082]
本实施例提供了一种低碳型路基材料的制备方法,所述矿粉占所述第三混合料干料的10%,所述集料占所述第三混合料的干料的35%;其他步骤同实施例1。
[0083]
对比例1
[0084]
在该对比例中,不加脱氨固锰剂,其他步骤同实施例1。
[0085]
对比例2
[0086]
在该对比例中,不加集料,其他步骤同实施例1。
[0087]
对比例3
[0088]
在该对比例中,不加矿粉,其他步骤同实施例1。
[0089]
对比例4
[0090]
在该对比例中,所述矿粉占所述第三混合料干料的2%,所述集料占所述第三混合料的干料的10%;其他步骤同实施例1。
[0091]
实验例1、样品性能分析
[0092]
将各实施例和各对比例的固化体进行性能分析,结果如表2所示。制样后在22℃,98%湿度养护箱中养护7d。样品经过《hj299-2010》浸出方法浸出,测定浸出液浓度是否满足《gb8978-1996》;
[0093]
表2
[0094][0095][0096]
由表2数据可知:
[0097]
对比例1中,不加脱氨固锰剂,存在氨氮及金属锰的浸出浓度不满足规范要求;
[0098]
对比例2中,不加集料,存在强度偏低的缺点;
[0099]
对比例3中,不加矿粉,存在强度偏低,且浸出液中金属锰浓度超过限值,其原因在于使用脱氨固锰剂短时内很难对锰渣中的金属锰完全固化稳定,而矿粉在碱性环境下可生成胶凝产物对金属锰进行固化稳定,同时还可以降低材料渗透系数,降低锰的迁移速率;
[0100]
对比例4中,集料、矿粉各组分掺量不在本发明实施例的范围内,存在强度偏低,且浸出液中金属锰浓度超过限值;
[0101]
本发明实施例1-实施例3中的固化体在7d无侧限抗压强度最高能够达到2.1mpa,样品经过《hj299-2010》浸出方法浸出,浸出液浓度满足《gb8978-1996》。
[0102]
最后,还需要说明的是,术语“包括”、“包含”或者其任何其他变体意在涵盖非排他性的包含,从而使得包括一系列要素的过程、方法、物品或者设备不仅包括那些要素,而且还包括没有明确列出的其他要素,或者是还包括为这种过程、方法、物品或者设备所固有的
要素。
[0103]
尽管已描述了本发明的优选实施例,但本领域内的技术人员一旦得知了基本创造性概念,则可对这些实施例作出另外的变更和修改。所以,所附权利要求意欲解释为包括优选实施例以及落入本发明范围的所有变更和修改。
[0104]
显然,本领域的技术人员可以对本发明进行各种改动和变型而不脱离本发明的精神和范围。这样,倘若本发明的这些修改和变型属于本发明权利要求及其等同技术的范围之内,则本发明也意图包含这些改动和变型在内。
再多了解一些
本文用于企业家、创业者技术爱好者查询,结果仅供参考。