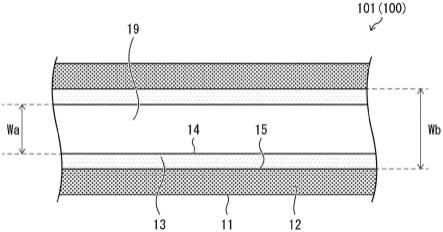
1.本发明涉及三氯硅烷的制造方法以及该制造方法中使用的配管。
背景技术:
2.一直以来,高纯度的三氯硅烷(sihcl3)被用于多晶硅(si)制造用原料。多晶硅被用作如半导体或太阳能发电用晶片的原料。例如通过以下的方法来获取三氯硅烷。首先,在催化剂的存在下使金属硅与含氯化氢(hcl)的原料气体进行反应,由此生成含三氯硅烷及四氯化硅(sicl4)等氯硅烷化合物的排出气体。其次,将该排出气体冷却、冷凝得到冷凝液之后,回收对该冷凝液进行蒸馏而提高了纯度的精炼液,由此得到作为多晶硅制造用原料的三氯硅烷。
3.另外,因对冷凝液进行蒸馏而排出的排出液中也含有氯硅烷化合物。因此,通过回收该排出液并使其与金属硅进行反应生成含氯硅烷化合物的排出气体,从而也能得到作为多晶硅制造用原料的三氯硅烷。
4.因对冷凝液进行蒸馏而排出的排出液中,除了氯硅烷化合物以外,还含有来自未反应金属硅粉及金属硅的杂质。由于该杂质含铝(al),因此杂质中的铝与氯硅烷化合物进行反应从而生成氯化铝(alcl3)。该氯化铝及未反应金属硅粉对于三氯硅烷制造设备中排出液所流动的配管会产生不良影响。具体而言,原因在于:氯化铝会析出于未反应金属硅粉的表面及所述配管的侧壁内表面而使该侧壁内表面产生腐蚀。
5.特别是在与排出液接触的侧壁内表面中温度降低到80℃以下的部分,氯化铝的析出变得激烈,明显地产生了腐蚀。进而,在侧壁内表面中温度降低到70℃以下的部分,氯化铝的析出变得更加激烈,更明显地产生了腐蚀。因此,在以往的三氯硅烷的制造方法中,存在因氯化铝析出而导致排出液所流动的配管的寿命变短的问题。
6.作为用于防止上述那样的配管寿命缩短的技术,例如在专利文献1中公开了,关于在含三氯硅烷的排出气体的冷却工序中使用的配管,将配管的侧壁中与排出气体接触的表面设定为规定温度以上的技术。根据该技术,通过使流体在从流化床式反应装置排出的排出气体所流动的配管的侧壁内形成的空间中流动,从而使侧壁中与排出气体接触的表面的温度在110℃以上,同时对排出气体进行冷却。
7.现有技术文献
8.专利文献
9.专利文献1:国际公开第2019/098343号公报(2019年5月23日公开)
技术实现要素:
10.发明所要解决的技术问题
11.然而,专利文献1所公开的技术减少了在排出气体所流通的配管内的氯化铝析出及凝固。另一方面,关于减少因对冷凝液进行蒸馏而排出的排出液所流动的配管内的氯化铝析出的技术,专利文献1中并未公开。因此,即使使用专利文献1所公开的技术,在减少排
出液所流动的配管内的氯化铝析出这一点上也未必充分。
12.本发明的一个方面是鉴于上述问题而完成的,其目的在于降低含氯硅烷化合物等的排出液在配管中流动时产生的、因氯化铝析出于配管的侧壁内表面而引起的所述内表面的腐蚀。
13.用于解决技术问题的手段
14.为了解决上述技术问题,本发明的一个方面所涉及的三氯硅烷的制造方法,包括蒸馏工序,在蒸馏工序中,通过蒸馏装置对含三氯硅烷的第1液体进行蒸馏,该三氯硅烷是基于含0.10质量%以上铝的金属硅与含氯化物的原料气体之间的反应生成的,从所述蒸馏装置回收氯化铝的摩尔浓度比所述金属硅中的所述铝的摩尔浓度高的、含所述三氯硅烷的第2液体,其中,在所述蒸馏工序中,使从所述蒸馏装置排出的所述第2液体流过侧壁的内表面被陶瓷层覆盖的配管的内部,由此从所述蒸馏装置回收所述第2液体。
15.本发明的一个方面所涉及的配管,用于供含三氯硅烷的第2液体流动,所述第2液体是从对含所述三氯硅烷的第1液体进行蒸馏的蒸馏装置中排出的,所述三氯硅烷是通过含0.10质量%以上铝的金属硅与含氯化物的原料气体之间的反应生成的,所述配管在从所述蒸馏装置回收的所述第2液体中的氯化铝的摩尔浓度比所述金属硅中的所述铝的摩尔浓度高的条件下使用,其中,所述配管的侧壁的内表面被陶瓷层覆盖。
16.发明的效果
17.根据本发明的一个方面,可以减少因第2液体中的氯化铝析出从而导致配管的侧壁内表面产生腐蚀的情况。
附图说明
18.图1是表示本发明的一个实施方式所涉及的三氯硅烷的制造方法的一个例子的流程图。
19.图2是表示本发明的一个实施方式所涉及的三氯硅烷的制造设备的一个例子的框图。
20.图3是表示本发明的一个实施方式所涉及的第2配管的直管部分的概略结构的剖视图。
21.图4是表示所述第2配管的弯管部分的概略结构的剖视图。
22.图5是表示本发明的一个实施方式的第1变形例所涉及的第2配管的直管部分的概略结构的剖视图。
23.图6是表示本发明的一个实施方式的第2变形例所涉及的第2配管的直管部分的概略结构的剖视图。
24.图7是表示本发明的一个实施方式的第3变形例所涉及的第2配管的直管部分的概略结构的剖视图。
25.图8是表示本发明的实施例所涉及的第2配管的直管部分的概略结构的剖视图。
具体实施方式
26.〔三氯硅烷的制造方法〕
27.如图1所示,本发明的一个实施方式所涉及的三氯硅烷的制造方法包括:反应工序
(s1)、冷凝液生成工序(s2)以及蒸馏工序(s3)。另外,如图2所示,本发明的一个实施方式所涉及的三氯硅烷的制造设备1具备:流化床式反应装置2、吸尘装置3、蒸馏塔4、第1配管5以及第2配管100。此外,关于到达流化床式反应装置2的金属硅6及原料气体7(均后述)的流动,例如记载于国际公开第2019/098344号公报中,因此根据需要引用该记载,并省略说明。
28.<反应工序>
29.首先,在图1所示的反应工序(s1)中,使金属硅6与原料气体7进行反应,从而生成未图示的三氯硅烷。作为用于生成三氯硅烷的金属硅6,可列举出冶金制金属硅、硅铁或多晶硅(si)等金属状态的包含硅元素的固体物质,可不受任何限制地使用公知的物质。
30.另外,金属硅6含有铝、铁化合物等杂质。金属硅6中铝的浓度为0.10质量%以上、更优选为0.15质量%以上且0.50质量%以下。对于铝以外的杂质的成分和含量没有特别的限制,另外,金属硅6中也可以不含铝以外的杂质。金属硅6通常是以平均粒径约为150μm以上且350μm以下的微细粉末的形态来使用的。
31.作为用于生成三氯硅烷的原料气体7,本实施方式中使用的是含氯化氢的气体(以下称为氯化氢气体)。氯化氢气体是本发明所涉及的第1原料气体的一个例子,氯化氢是本发明所涉及的氯化物的一个例子。对于用作原料气体7的氯化氢气体的种类没有任何限制,可以使用工业上能够获得的各种氯化氢气体。
32.如图2所示,在三氯硅烷的生成中使用流化床式反应装置2。流化床式反应装置2是一种用于使金属硅6与原料气体7进行反应从而生成三氯硅烷的反应装置,是本发明所涉及的反应装置的一个例子。作为流化床式反应装置2,可使用公知的反应装置,并无特别限制。由于流化床式反应装置2可连续地供给金属硅6及原料气体7,因此通过使用流化床式反应装置2,可以连续地制造三氯硅烷。此外,用于生成三氯硅烷的反应装置并不局限于流化床式反应装置2。例如,可不受任何限制地使用公知的非流化床式反应装置。
33.关于金属硅6及原料气体7的供给量,只要能够以达到可形成流动层的流量的速度来供给金属硅6及原料气体7即可,并无特别限制。另外,从加快金属硅6与原料气体7之间的反应的反应速度并且高效地制造三氯硅烷的观点出发,在使金属硅6和原料气体7进行反应时,优选使用催化剂。作为用于该反应的催化剂,例如可列举出铜粉、氯化铜、铜硅化物等铜系催化剂。
34.金属硅6与原料气体7反应时的反应温度是斟酌流化床式反应装置2的材质和能力以及催化剂等而适当确定的。所述反应温度一般设定在200℃以上且500℃以下的范围,优选设定在250℃以上且450℃以下的范围。
35.通过下述式(1)及式(2)来表示反应工序(s1)中流化床式反应装置2内发生的主要反应。
36.si 3hcl
→
sihcl3 h2ꢀꢀ
式(1)
37.si 4hcl
→
sicl4 2h2ꢀꢀ
式(2)
38.由流化床式反应装置2所生成的三氯硅烷作为未图示的排出气体而排出。该排出气体中,除了三氯硅烷以外,还含有氢气、副产物四氯化硅、未反应的金属硅6、其他氯硅烷化合物以及氯化铝。在本说明书中,氯硅烷化合物是指含氯元素和硅元素的化合物。作为氯硅烷化合物,除了三氯硅烷和四氯化硅以外,还可列举出二氯硅烷(sih2cl2)、五氯二硅烷(si2hcl5)以及六氯二硅烷(si2cl6)等。
39.此外,在本实施方式所涉及的三氯硅烷的制造方法中,反应工序(s1)中的三氯硅烷生成方法并不局限于使金属硅6与作为原料气体7的氯化氢气体进行反应的方法。例如,还可采用如下方法:将多晶硅析出工序中作为副产物生成的四氯化硅转换为三氯硅烷(stc还原反应)并进行再利用。采用该方法时的四氯化硅也是本发明的氯化物的一个例子。
40.具体而言,将在上述多晶硅析出工序中生成的含四氯化硅和氢气的气体作为原料气体,使该原料气体与金属硅6在流化床式反应装置2中进行反应,由此将四氯化硅转换为三氯硅烷。含四氯化硅和氢气的气体是本发明所涉及的第2原料气体的一个例子。通过下述式(3)来表示三氯硅烷的转换。
41.si 3sicl4 2h2→
4sihcl3ꢀꢀ
式(3)
42.另外,在反应工序(s1)中,还可以并用将四氯化硅转换为三氯硅烷并进行再利用的方法与使金属硅6和原料气体7进行反应的方法。
43.<冷凝液生成工序>
44.接着,在图1所示的冷凝液生成工序(s2)中,对从流动床式反应装置2排出的排出气体实施各种处理,生成含三氯硅烷的冷凝液8(参照图2)。冷凝液8是本发明所涉及的第1液体的一个例子。
45.具体而言,首先,使从流化床式反应装置2排出的排出气体通过图2所示的吸尘装置3,由此除去排出气体中的固体物。排出气体中的固体物例如是反应工序(s1)中未反应的金属硅6。作为吸尘装置3,例如可使用过滤器、离心力式吸尘装置。如果使用离心力式吸尘装置,优选使用例如旋风式粉状分离器。原因如下:作为旋风式粉状分离器,即使固体物等粒子很微细也能将其除去,设置和维护管理比其他离心力式吸尘装置容易,而且可以在高压、高温下使用。
46.接着,对从吸尘装置3得到的排出气体进行冷却。该冷却是为了通过将清洗后的排出气体中的三氯硅烷冷凝分离来生成冷凝液8而进行的。作为排出气体的冷却方法,只要能冷却到使各种氯硅烷化合物冷凝的温度以下即可,并无特别限制,可采用公知的冷却方法。
47.<蒸馏工序>
48.(蒸馏工序的概要)
49.然后,在图1所示的蒸馏工序(s3)中,对由冷凝液生成工序(s2)生成的如图2所示的冷凝液8在蒸馏塔4中进行蒸馏。蒸馏塔4是本发明所涉及的蒸馏装置的一个例子。此外,用于对冷凝液8进行蒸馏的蒸馏装置并不局限于蒸馏塔4,可不受任何限制地使用公知的各种蒸馏装置。
50.冷凝液8中,除了三氯硅烷以外,还含有在冷凝液生成工序(s2)中未能除去的金属硅6、金属硅6中的铝与氯硅烷化合物进行反应而生成的氯化铝等杂质。因此,通过对冷凝液8进行蒸馏以从该冷凝液8中分离除去所述杂质,从而回收精炼冷凝液8而得到的含三氯硅烷的精炼液9。然后,从回收的精炼液9中得到作为多晶硅制造用原料的三氯硅烷。
51.具体而言,在蒸馏工序(s3)中,通过在蒸馏塔4的塔底部直接加热冷凝液8,从而使三氯硅烷、四氯化硅等氯硅烷化合物蒸发并从蒸馏塔4的塔顶部排出。或者,通过将冷凝液8的一部分吹出并用再沸器加热后使其返回蒸馏塔4中等方式,从而使氯硅烷化合物蒸发并从蒸馏塔4的塔顶部排出。冷凝液8的蒸馏温度一般在60℃以上、更优选在70℃以上且90℃以下。从塔顶部排出的氯硅烷化合物在通过与塔顶部连通的第1配管5的内空部的过程中被
冷却,最终作为精炼液9被回收。
52.另外,如图2所示,因对冷凝液8进行蒸馏而导致排出液10从蒸馏塔4的塔底部排出。排出液10中,除了三氯硅烷及其他氯硅烷化合物以外,还含有氯化铝、氯化铁(fecl3)、氯化钙(cacl2)和氯化钛(ticl4)等来自金属硅6的杂质和未反应的金属硅粉。未反应的金属硅粉的含量通常在数十ppmwt以下。另外,未反应的金属硅粉的平均粒径在1μm以下。排出液10是本发明所涉及的第2液体的一个例子。
53.塔底部与第2配管100连通,第2配管是本发明所涉及的配管的一个例子。从塔底部排出的排出液10流过第2配管100的内空部19(参照图3等),由此回收排出液10。另外,在取出冷凝液8的一部分并使用未图示的再沸器加热的情况下,也可以使用中途分支的未图示的第2配管100将该冷凝液8的一部分输送至所述再沸器。关于第2配管100的结构详情将在下文进行描述。
54.由于所回收的排出液10含有四氯化硅,因此例如通过进一步对排出液10进行蒸馏来回收四氯化硅。所回收的四氯化硅例如储存在未图示的罐中,再利用以制造三氯硅烷。具体而言,在流化床式反应装置2中使用含有所回收的四氯化硅和氢气的气体以及金属硅6进行stc还原反应,由此将四氯化硅转换为三氯硅烷。所回收的四氯化硅是本发明的氯化物的一个例子,含有所回收的四氯化硅和氢气的气体是本发明所涉及的第2原料气体的一个例子。
55.另外,也可以将所回收的四氯化硅用于其他工业用途,而不是再利用以制造三氯硅烷。或者,还可以将所回收的四氯化硅的一部分进行再利用以制造三氯硅烷,并将剩余部分用于其他工业用途。进而,也可以不从排出液10中回收四氯化硅。
56.(第2配管的结构)
57.本实施方式所涉及的三氯硅烷的制造方法是在流化床式反应装置2中与原料气体7进行反应之前的金属硅6中的铝达到0.10质量%以上的条件下实施的。而且,所述制造方法是在通过了第2配管100并被回收的排出液10中的氯化铝的摩尔浓度比所述铝的摩尔浓度高的条件下实施的。
58.这里,对于本说明书中各种摩尔浓度的定义进行说明。首先,金属硅6中的铝的摩尔浓度是指每单位质量的金属硅6中所含的铝的摩尔数(原子数)相对于每单位质量的金属硅6中所含的硅等各金属的总摩尔数(总原子数)的比率。其次,排出液10中的氯化铝的摩尔浓度是指每单位质量的排出液10所含的氯化铝的摩尔数(分子数)相对于每单位质量的排出液10中所含的金属化合物的总摩尔数(总分子数)的比率。以下,将摩尔浓度表示为“mol%”。
59.通过使规定量的金属硅6溶解在硝酸氟酸混合液中,从而求出金属硅6中的各金属的总摩尔数。具体而言,当金属硅6溶解在硝酸氟酸混合液中时,金属硅6中所含的硅转换成四氟化硅(sif4),变为挥发性成分。当在120℃下对该溶解液进行加热蒸发时,在蒸发残渣中其他金属成分会作为氧化物而残留。接下来,通过将该蒸发残渣溶解在硝酸中并使用icp-ms(电感耦合等离子体质谱仪)进行测量,可以求出除硅以外的各金属的摩尔数。接着,将除此以外的摩尔数用作硅的摩尔数。然后,对除硅以外的各金属的摩尔数和硅的摩尔数进行合计,从而求出金属硅6中各金属的总摩尔数。
60.另外,可以通过以下方法求出排出液10中的各金属化合物的总摩尔数。首先,使用
具有tcd(热导型)检测器的气相色谱对排出液10进行测量,从而求出各种氯硅烷化合物的摩尔数。接着,在70℃下加热排出液10,从而使排出液10中的挥发性成分蒸发。然后,在使该蒸发残渣溶解于硝酸之后,通过icp-ms进行测量,从而求出排出液10中的各金属化合物的总摩尔数。
61.另外,在计算上述的总摩尔数时,关于除硅以外的金属,以铝、铁、钙、钛、磷、硼、铜、铬、锰、镁、钠及锂作为测量对象。
62.如果在上述条件下使侧壁12的内表面15(参照图3等)暴露于内空部19,则在蒸馏工序(s3)中使排出液10流过内空部19时,排出液10中的氯化铝容易析出于未反应的金属硅粉的表面及侧壁12的内表面15。该氯化铝为侧壁12的内表面15产生腐蚀的原因。
63.因此,关于本实施方式所涉及的第2配管100,为了降低所述腐蚀,该第2配管100的至少一部分设为如下结构:侧壁12的内表面15如图3及图4所示那样被陶瓷层13覆盖。也就是说,第2配管100可以说是在从蒸馏塔4所回收的排出液10中的氯化铝的mol%比在流化床式反应装置2中与原料气体7进行反应之前的金属硅6中的铝的mol%高的条件下使用的配管。并且,第2配管100构成为如下结构:在被陶瓷层13覆盖的地方,即使多少出现了氯化铝向未反应的金属硅粉的表面及侧壁12的内表面15析出的情况,也能降低腐蚀。
64.此外,关于第2配管100,通过在排出液10中的氯化铝的mol%被浓缩为与原料气体7进行反应之前的金属硅6中的铝的mol%的2倍以上且10倍以下的条件下使用,其意义将变得明确。特别地,通过在排出液10中的氯化铝的mol%被浓缩为与原料气体7进行反应之前的金属硅6中的铝的mol%的3倍以上且8倍以下的条件下使用,第2配管100的意义将变得更加明确。这也适用于排出液10中所含的氯化铝的mol%的绝对值在0.3mol%以上、特别是0.4mol%以上且1.2mol%以下的情况。
65.原因如下:如果在上述各条件下使用侧壁的内表面未被陶瓷层13覆盖的常规的配管,则氯化铝向未反应的金属硅粉的表面及侧壁的内表面析出的情况将变得相当激烈。因此,在某些情况下,侧壁的内表面会明显产生腐蚀,直至配管难以继续使用。另一方面,在上述各条件下使用第2配管100的情况下,由于陶瓷层13的存在,即使多少出现了氯化铝向未反应的金属硅粉的表面及侧壁12的内表面15析出的情况,也能降低腐蚀。因此,能够将侧壁12的内表面15的腐蚀降低至至少能维持第2配管100继续使用的水平,第2配管100的腐蚀降低效果显著化。
66.另外,在第2配管100中,可以将从与蒸馏塔4的塔底部的连接处开始直到通到排出液10的输送目的地的末端(以下称为“第2配管100主体”)为止全部用陶瓷层13覆盖,或者也可以将其中一部分用陶瓷层13覆盖。进而,在第2配管100构成为管路从中途部分开始分支的结构且设置有经由再沸器返回蒸馏塔4的未图示的循环路径的情况下,也可以将第2配管100主体和循环路径全部用陶瓷层13覆盖。或者也可以将第2配管100主体和循环路径的一部分用陶瓷层13覆盖。
67.在第2配管100中与蒸馏塔4的塔底部间隔一段距离的部分,未反应的金属硅粉的表面及侧壁12的内表面15的温度容易变为80℃以下,进而氯化铝的析出容易变得激烈。另外,根据第2配管100周围的情况等,在所述部分,侧壁12的内表面15的温度有时也会变为70℃以下,进而氯化铝的析出将变得更加激烈。因此,优选将第2配管100中与蒸馏塔4的塔底部间隔一段距离的部分用陶瓷层13覆盖。
68.如图3及图4所示,第2配管100具备金属配管11及陶瓷层13。金属配管11例如是不锈钢(sus)、铁等公知的金属制成的配管,由圆筒形状的侧壁12形成。因此,覆盖侧壁12的内表面15的陶瓷层13也呈圆筒形状。
69.另外,在第2配管100中,由陶瓷层13的接触面14包围而为形成圆筒形状的空间的内空部19。内空部19是本发明所涉及的配管的内部的一个例子。从蒸馏塔4的塔顶部排出的排出液10流过该内空部19。接触面14是陶瓷层13与流过内空部19的排出液10接触的面。
70.图3示出了第2配管100的直管部分101的一部分,图4示出了第2配管100的弯管部分102。直管部分101是指第2配管100中没有弯折的部分,弯管部分102是指第2配管100中弯折的部分。第2配管100由直管部分101和弯管部分102连接而形成。此外,第2配管100及内空部19的形状、大小等并不局限于本实施方式的示例,可以任意地进行设计变更。
71.如上所述,由于侧壁12的内表面15被陶瓷层13覆盖,因此流过第2配管100的内空部19的排出液10中的氯化铝大部分析出到未反应的金属硅粉的表面和陶瓷层13的接触面14。也就是说,侧壁12的内表面15上几乎没有所述氯化铝析出。因此,能够降低因氯化铝析出而导致的侧壁12的内表面15的腐蚀。
72.另外,作为陶瓷层13的形成材料的陶瓷具有氯化铝难以附着的性质。因此,即使流过第2配管100的内空部19的排出液10中的氯化铝析出到陶瓷层13的接触面14上,该氯化铝也不太附着在接触面14上。进而,陶瓷硬度较高,具有优异的耐磨性。因此,即使氯化铝析出并附着在接触面14上,接触面14也不会太磨损。由此,陶瓷层13的接触面14很难发生腐蚀。根据以上所述,通过用陶瓷层13覆盖侧壁12的内表面15,第2配管100的寿命会延长。
73.作为陶瓷层13的形成材料即陶瓷,例如可列举出氧化铝、二氧化硅、氧化锆、硅酸锆、氧化铬等一般的金属陶瓷。在这些材料中,优选将氧化铝用作陶瓷层13的形成材料。当陶瓷层13的形成材料为氧化铝时,即使因氯化铝析出而导致在陶瓷层13的接触面14上产生腐蚀,混入流过第2配管100的内空部19的排出液10中的也仅为铝。因此,具有铝以外的物质不会混入流过第2配管100的内空部19的排出液10中的优点。
74.另外,在侧壁12的内表面15上形成陶瓷层13的方法并不特别限定,例如可以使用粘接法、cvd法、熔射法等公知的方法。进而,关于陶瓷层13的厚度,优选为1mm以上且小于5mm,更优选为2mm以上且4mm以下。
75.当陶瓷层13的厚度小于1mm时,例如容易出现如下问题:由于所要形成的陶瓷层13的厚度过于薄,导致陶瓷层13的形成作业难以进行,且形成作业结束后出现形成不均。另外,当陶瓷层13的厚度为5mm以上时,为了使第2配管100的内径wa与常规的金属配管的内径大致相同,必须使金属配管11的内径wb相当大。因此,第2配管100会过度地大型化,从而导致高成本。因此,通过使陶瓷层13的厚度在1mm以上且小于5mm,可以降低所述的形成不均和高成本。当陶瓷层13的厚度为3mm时,所述的形成不均和高成本可以降为最低。
76.〔变形例〕
77.使用图5至图7对本发明的一个实施方式所涉及的第2配管100的变形例进行说明。此外,为了便于说明,对于与在上述实施方式中说明过的部件具有相同功能的部件标注相同的符号,并且不重复其说明。
78.<第1变形例>
79.首先,如图5所示,将侧壁12的内部形成有空间16的第2配管200假定为第2配管100
的变形例。此外,在图5中,为了便于说明,仅示出了第2配管200中的直管部分。在仅示出直管部分这一点上,图6至图8也是同样的。
80.空间16是供空气20在第2配管200的侧壁12的内部流动的空间。空气20是本发明所涉及的热介质的一个例子。侧壁12上形成有用于将空气20导入空间16中的第1开口部121,第1开口部121与空间16连通。另外,侧壁12上形成有用于将空气20从空间16排出到第2配管200外侧的第2开口部122,第2开口部122与空间16连通。
81.空气20的温度在120℃以上且150℃以下,更优选在130℃以上且140℃以下,通过使空气20在空间16中流动,从而使陶瓷层13的接触面14的温度在100℃以上、更优选在110℃以上且120℃以下。例如,通过在接触面14上设置k热电偶等并进行温度测量,从而确认接触面14的温度是否在100℃以上。关于该温度确认方法,在后述的第2配管300中也以同样的方式进行。
82.这样,通过使接触面14的温度在100℃以上,可以降低排出液10中的氯化铝析出于未反应的金属硅粉的表面及接触面14上的量。因此,可以延缓接触面14的腐蚀进度。就接触面14的温度而言,若其过高则需要大量的加热用能量,因此更优选为120℃以下。
83.另外,通过使接触面14的温度在100℃以上,可以降低在第2配管200的内空部19中流动的排出液10中的氯化铝的粘度。因此,由于当排出液10中的氯化铝与接触面14接触时作用于该接触面14的摩擦力降低,因此可以降低接触面14的腐蚀。
84.此外,在侧壁12的空间16中流动的热介质并不局限于空气20。例如,油或高温水也可以代替空气20在空间16中流动。当高温水在空间16中流动时,与流动空气20的情况相比,可以缩短第2配管200的全长,从而可以使三氯硅烷的制造设备1(参照图2)小型化。
85.<第2变形例>
86.接着,如图6所示,还将侧壁12的内部形成有空间16且侧壁12的外表面123被保温层17覆盖的第2配管300假定为第2配管100的变形例。保温层17用于将陶瓷层13的接触面14的温度保持在100℃以上。关于保温层17的种类、材质等,只要能将接触面14的温度保持在100℃以上则不受限定,但优选陶瓷棉。附带说明,陶瓷棉中,特别优选石棉。这种保温层的厚度一般在20mm以上且40mm以下,更优选在25mm以上且35mm以下。通过像这样将侧壁12的外表面123用保温层17覆盖,在使排出液10在第2配管300的内空部19中流动期间,能够持续降低排出液10中的氯化铝析出到接触面14上的量。另外,能够持续保持排出液10中的氯化铝的低粘度。
87.进而,由于将侧壁12的外表面123用保温层17覆盖,而且在侧壁12的空间16中流动空气20,所以能够更可靠地将接触面14的温度保持在100℃以上。因此,能够更可靠地持续降低排出液10中的氯化铝的量,并持续保持低粘度,从而能够更有效地降低侧壁12的内表面15的腐蚀。
88.此外,即使如图7所示的第2配管400那样在侧壁12的内部没有形成空间16,只要将侧壁12的外表面123用保温层17覆盖,就能持续降低排出液10中的氯化铝的量,并持续保持低粘度。
89.〔综述〕
90.本发明的一个方面所涉及的三氯硅烷的制造方法,包括蒸馏工序,在蒸馏工序中,通过蒸馏装置对含三氯硅烷的第1液体进行蒸馏,该三氯硅烷是基于含0.10质量%以上铝
的金属硅与含氯化物的原料气体之间的反应生成的,从所述蒸馏装置回收氯化铝的摩尔浓度比所述金属硅中的所述铝的摩尔浓度高的、含所述三氯硅烷的第2液体,其中,在所述蒸馏工序中,使从所述蒸馏装置排出的所述第2液体流过侧壁的内表面被陶瓷层覆盖的配管的内部,由此从所述蒸馏装置回收所述第2液体。
91.根据上述构成,由于配管的侧壁的内表面被陶瓷层覆盖,所以即使含氯化铝的第2液体在配管的内部流动且该氯化铝的量可导致腐蚀成问题,氯化铝也不易析出到未反应的金属硅粉的表面及侧壁的内表面上。因此,能够降低因第2液体中的氯化铝析出而导致的侧壁的内表面的腐蚀。
92.本发明的一个方面所涉及的三氯硅烷的制造方法,可以为:使所述陶瓷层与所述第2液体接触的接触面的温度在100℃以上。根据上述构成,由于使陶瓷层的接触面的温度在100℃以上,所以可以降低第2液体在配管的内部流动期间第2液体中的氯化铝析出到未反应的金属硅粉的表面及接触面上的量。因此,导致接触面腐蚀的原因物质减少,接触面腐蚀的进度变慢。
93.另外,可以降低在配管内部流动的第2液体中的氯化铝的粘度。因此,当在配管内部流动的第2液体中的氯化铝与接触面接触时,作用于接触面的摩擦力降低。根据以上所述,由于陶瓷层的接触面的腐蚀降低,因此可以进一步降低因第2液体中的氯化铝析出而导致的侧壁内表面的腐蚀。
94.本发明的一个方面所涉及的三氯硅烷的制造方法,可以为:在所述侧壁的内部形成有供热介质流动的空间,通过使所述热介质在所述空间中流动,从而使所述接触面的温度在100℃以上。
95.根据上述构成,通过使热介质在形成于侧壁的内部的空间中流动从而使接触面的温度在100℃以上,可以进一步降低因第2液体中的氯化铝析出而导致的侧壁内表面的腐蚀。
96.本发明的一个方面所涉及的三氯硅烷的制造方法,可以为:用于将所述陶瓷层与所述第2液体接触的接触面的温度保持在100℃以上的保温层覆盖所述侧壁的外表面。
97.根据上述构成,由于侧壁的外表面被保温层覆盖,所以在第2液体流动于配管内部的期间,可以将接触面的温度保持在100℃以上。因此,在第2液体流动于配管内部的期间,可以持续降低第2液体中的氯化铝析出到未反应金属硅粉的表面及接触面上的量,并可以持续保持第2液体中的氯化铝的低粘度。由此,可以更有效地降低因第2液体中的氯化铝析出而导致的侧壁内表面的腐蚀。
98.本发明的一个方面所涉及的三氯硅烷的制造方法,可以为:所述陶瓷层含有氧化铝。根据上述构成,由于陶瓷层含有氧化铝,所以即使因氯化铝析出导致陶瓷层的接触面产生腐蚀,混入第2液体中的陶瓷层的磨损成分大多为铝。因此,可以减少流过配管的第2液体中新混入从前就含有的铝以外的杂质的情况。
99.本发明的一个方面所涉及的三氯硅烷的制造方法,可以为:所述陶瓷层的厚度为1mm以上且小于5mm。根据上述构成,由于陶瓷层的厚度在1mm以上,所以能够降低在侧壁内表面出现没有形成陶瓷层的地方的情况(以下称为“形成不均”)。具体而言,可以减少如下问题的发生:由于所要形成的陶瓷层的厚度过于薄,导致例如陶瓷层的形成作业难以进行,且形成作业结束后出现形成不均。
100.另外,在配管的侧壁内表面上形成有陶瓷层的情况下,优选将在俯视配管时由陶瓷层的接触面形成的圆的直径设为与没有陶瓷层的常规配管的内径大致相同。这里,在陶瓷层的厚度为5mm以上的情况下,为了使所述圆的直径与常规配管的内径大致相同,俯视本发明所涉及的配管时由侧壁的内表面形成的圆的直径必须相当大。因此,本发明所涉及的配管会过度地大型化,从而导致高成本。
101.在这一点上,根据上述构成,由于陶瓷层的厚度小于5mm,所以在俯视本发明所涉及的配管时由侧壁的内表面形成的圆的直径不会过大,从而可以降低因配管的大型化而导致的高成本。
102.本发明的一个方面所涉及的三氯硅烷的制造方法,可以为:所述原料气体是含氯化氢的第1原料气体或含氢气及四氯化硅的第2原料气体中的任一种。根据上述构成,通过金属硅与含氯化氢的第1原料气体或者含氢气及四氯化硅的第2原料气体之间的反应,能够高效生成三氯硅烷。因此,当含有高效生成的三氯硅烷的第2液体在配管中流动时,能够降低因第2液体中的氯化铝析出而导致的侧壁内表面的腐蚀。
103.本发明的一个方面所涉及的配管,用于供含三氯硅烷的第2液体流动,所述第2液体是从对含所述三氯硅烷的第1液体进行蒸馏的蒸馏装置中排出的,所述三氯硅烷是通过含0.10质量%以上铝的金属硅与含氯化物的原料气体之间的反应生成的,所述配管在从所述蒸馏装置回收的所述第2液体中的氯化铝的摩尔浓度比所述金属硅中的所述铝的摩尔浓度高的条件下使用,其中,所述配管的侧壁的内表面被陶瓷层覆盖。
104.根据上述构成,能够实现降低因第2液体中的氯化铝析出而导致的侧壁内表面的腐蚀的配管。
105.〔附注事项〕
106.本发明不限于上述的各实施方式以及变形例,在权利要求所示的范围内可以进行各种变更。例如,通过适当地组合分别在上述实施方式以及不同的变形例中公开的技术手段而获得的实施方式也包括在本发明的技术范围内。
107.〔实施例1〕
108.使用图8对本发明的实施例1进行说明。在本实施例1中,作为反应工序(s1)中用于生成三氯硅烷的金属硅6,使用的是含0.15mol%(换算为质量%为0.145质量%)铝的金属硅。另外,作为反应工序(s1)中用于生成三氯硅烷的原料气体7,使用的是含100mol%(100质量%)氯化氢的原料气体。此外,蒸馏温度为80℃。
109.另外,在本实施例1中,在蒸馏工序(s3)中使用的第2配管100中,使用的是如图8所示那样内径wa=42mm的第2配管500。第2配管500是将内径wa=42mm、厚度3mm的氧化铝制套管作为陶瓷层13粘接在内径wb=53mm的sus制的金属配管11的内表面15上而得到的配管。所述粘接中使用的是环氧树脂制的耐热性粘接剂18。
110.在第2配管500的两端中的一端,设置有从金属配管11的外表面向外侧突出的sus制的法兰124。另外,在法兰124上形成有多个用于将第2配管500与其他配管等连接的螺栓孔125。进而,在第2配管500中形成有法兰124的一侧的前端,施加了用于保护耐热性粘接剂18的层的氧化铝制的泥粉30。具体而言,在上述前端中以第2配管500的中心轴(未图示)为中心且直径wc=48mm附近的地方施加了泥粉30。
111.使用上述金属硅、原料气体以及第2配管500进行了反应工序(s1)、冷凝液生成工
序(s2)以及蒸馏工序(s3)。其结果,在蒸馏塔4中,通过对冷凝液8进行蒸馏,冷凝液8中的铝和未反应的金属硅粉被浓缩为约5倍。另外,流过第2配管500的内空部19的排出液10中的铝为0.96mol%。进而,所述排出液10中的三氯硅烷与四氯化硅的成分比基于mol为三氯硅烷:四氯化硅=5:95=1:19。未反应的金属硅粉的含量为220ppmwt,未反应的金属硅粉的平均粒径为0.7μm。
112.在使用侧壁内表面未被陶瓷层13覆盖的常规配管制造三氯硅烷的情况下,通过3个月的运转,配管的一部分产生了腐蚀,且发生了漏液。另一方面,使用本实施例1的第2配管500制造三氯硅烷,结果为能够稳定运转1年。另外,在运转1年后打开第2配管500进行检查,即使在侧壁12的内表面15的温度降低到70℃以下的第2配管500的下游部分,陶瓷层13的接触面14上也几乎看不到氯化铝析出。
113.〔实施例2〕
114.关于本发明的实施例2进行以下说明。在本实施例2中,使用的是实施例1中使用的第2配管500中具有侧壁12的内部形成有空间的结构的未图示的第2配管。然后,使蒸汽作为热介质在所述空间中流动,从而将侧壁12的内表面15的温度保持在130℃进行运转。其他实施方法等与实施例1相同。
115.使用本实施例2的第2配管制造三氯硅烷,结果为能够稳定地使用1年。另外,在上述那样使用1年后打开第2配管600进行检查,陶瓷层13的接触面14(参照图8)上,遍及整个第2配管也未发现氯化铝析出。
116.符号说明
117.4 蒸馏塔(蒸馏装置)
118.6 金属硅
119.7 原料气体(第1原料气体)
120.8 冷凝液(第1液体)
121.10 排出液(第2液体)
122.12 侧壁
123.13 陶瓷层
124.14 接触面
125.15 内表面
126.16 空间
127.17 保温层
128.19 内空部(配管的内部)
129.20 空气(热介质)
130.123 外表面
131.100、200、300、400、500 第2配管(配管)
再多了解一些
本文用于企业家、创业者技术爱好者查询,结果仅供参考。