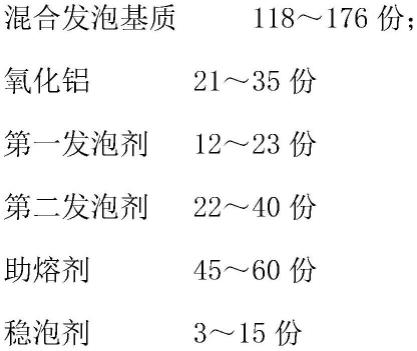
1.本发明涉及多孔发泡材料技术领域,尤其涉及一种基于高炉灰为发泡剂的多孔材料及其制备方法。
背景技术:
2.高炉灰又俗称高炉瓦斯灰,也叫炉尘,是高炉煤气带出的炉料粉末。高炉除尘灰随高炉操作工艺及炉矿的不同,其含铁含碳的品位也不相同,其数量除了与高炉冶炼强度、炉顶压力有关外,还与炉料的性质有很大关系。炉料粉末多,带出的炉尘量就大。一般每吨生铁有100~120kg炉尘产生,炉尘中含铁的质量份数30%~45%,含碳的质量份数10%~40%,并含有较多的碳和碱性氧化物,其主要成份是焦末和矿粉。
3.高炉灰的主要成份包括铁、碳、硅、钙、锌等氧化物。根据化验,布袋灰含铁品位30%~40%,碳含量20%~30%;重力灰含铁量35%~45%,碳含量15%~23%。布袋灰、重力灰的铁、碳总和都为55%~65%,有用成份基本相当。高炉灰的处置方法有三种:
⑴
延续传统方法,对含锌高炉除尘灰的利弊认识不足,直接配入烧结矿中循环使用,为高炉的顺行埋下隐患;(2)充份认识到高炉除尘灰中富集锌对高炉运行危害的事实,除尘灰直接外排堆放,回收工艺处于研发阶段;
⑶
将除尘灰进行在处理后回收使用,因除尘灰含铁品位较低,单纯磁选精粉经济性不强,尾矿量大,外排困难,影响了钢铁厂回收的经济性,多数是外包,少数厂家进行了铁、碳联选。但上述三种高炉灰材料的处理方法成本较高,且不能对高炉灰材料进行全资源利用。
技术实现要素:
4.为解决上述技术问题,本发明的目的在于提供一种基于高炉灰为发泡剂的多孔材料及其制备方法,所述基于高炉灰为发泡剂的多孔材料可对高炉灰进行有效地利用,且制备方法简单,制备得到的多孔材料孔隙均匀、孔隙率大且强度高,适宜用作保温材料。
5.为达到上述技术效果,本发明采用了以下技术方案:
6.第一方面,本发明提供的一种基于高炉灰为发泡剂的多孔材料,包括以下质量份数的原料:
[0007][0008]
其中,所述第一发泡剂为高炉灰。
[0009]
进一步地,所述高炉灰为布袋捕集高炉灰或重力沉降高炉灰。
[0010]
进一步地,所述第二发泡剂为碳化硅和碳粉的混合物。
[0011]
进一步地,所述第二发泡剂的组成为:碳化硅12~25份,碳粉10~15份。
[0012]
进一步地,所述混合发泡基质为石英砂、碳酸钙、粉煤灰、碳酸钡的混合物。
[0013]
进一步地,所述混合发泡基质的组成为:石英砂34~60份、碳酸钙32~56份、粉煤灰40~45份、碳酸钡12~15份。
[0014]
进一步地,述混合发泡基质的组成为:石英砂45份、碳酸钙40份、高炉灰43份、碳酸钡14份。
[0015]
进一步地,所述助熔剂为氟硅酸钠和碳酸钡的混合物。
[0016]
进一步地,所述稳泡剂为磷酸钠和氧化锌的混合物。
[0017]
第二方面,本发明提供的一种基于高炉灰为发泡剂的多孔材料的制备方法,包括以下步骤:
[0018]
s1:取各发泡基质进行初步粉碎并过筛,按照配方量混合成为混合发泡基质;
[0019]
s2:取混合发泡基质与氧化铝、第一发泡剂、第二发泡剂、助熔剂以及稳泡剂进行混合,并向混合物中加水进行研磨,得到混合浆料;
[0020]
s3:对混合浆料进行干燥、粉碎以得到混合胚料,采用上述混合胚料装入模具中进行烧结,即得。
[0021]
进一步地,所述研磨方法采用湿法球磨法。
[0022]
与现有技术相比,本发明的有益效果为:
[0023]
第一方面,本发明提供的一种基于高炉灰为发泡剂的多孔材料将高炉灰作为发泡剂用于制备多孔材料,可对高炉灰资源进行有效地利用,并且产生较大的经济效益。
[0024]
第二方面,本发明提供的一种基于高炉灰为发泡剂的多孔材料的制备条件和方法简单,设备和人力成本较低,且制备得到的多孔材料孔隙均匀、孔隙率大、强度高、导热系数小、吸声系数较大,及其适宜作为保温材料使用。
[0025]
第三方面,本发明提供的一种基于高炉灰为发泡剂的多孔材料在制备过程中采用高炉灰作为第一发泡剂、并将该第一发泡剂与第二发泡剂进行复配使用,进一步提高了该保温材料的各种性能,利于消耗废弃的高炉灰资源,可产生较大的社会经济效益。
[0026]
第四方面,本发明提供的一种基于高炉灰为发泡剂的多孔材料在制备过程中通过
对加工该多孔材料的各原料组分在现有技术的基础上进行合理地调整,并以第一发泡剂与第二发泡作为复配发泡剂使用,制备得到的多孔材料性能优异。
具体实施方式
[0027]
以下实施例仅用于更加清楚地说明本发明的技术方案,因此只作为示例,而不能以此来限制本发明的保护范围。需要说明的是,下述实施方案中所述实验方法,如无特殊说明,均为常规方法,所述试剂和材料,如无特殊说明,均可从商业途径获得。
[0028]
实施例1
[0029]
本实施例为本发明的第一制备实施例,该基于高炉灰为发泡剂的多孔材料的制备原料如下;
[0030]
石英砂34份、碳酸钙32份、粉煤灰40份、碳酸钡12份;
[0031]
氧化铝21份;
[0032]
高炉灰12份;
[0033]
碳化硅12份、碳粉10份;
[0034]
氟硅酸钠23份、碳酸钡22份;
[0035]
磷酸钠2份、氧化锌1份。
[0036]
实施例2
[0037]
本实施例为本发明的第二制备实施例,该基于高炉灰为发泡剂的多孔材料的制备原料如下:
[0038]
石英砂45份、碳酸钙40份、高炉灰43份、碳酸钡14份;
[0039]
氧化铝25份;
[0040]
高炉灰15份;
[0041]
碳化硅16份、碳粉15份;
[0042]
氟硅酸钠26份、碳酸钡32份;
[0043]
磷酸钠3份、氧化锌5份。
[0044]
实施例3
[0045]
本实施例为本发明的第三制备实施例,该基于高炉灰为发泡剂的多孔材料的制备原料如下:
[0046]
石英砂54份、碳酸钙45份、粉煤灰43份、碳酸钡13份;
[0047]
氧化铝32份;
[0048]
高炉灰17份;
[0049]
碳化硅21份、碳粉14份;
[0050]
氟硅酸钠32份、碳酸钡15份;
[0051]
磷酸钠5份、氧化锌10份。
[0052]
实施例4
[0053]
本实施例为本发明的第四制备实施例,该基于高炉灰为发泡剂的多孔材料的制备原料如下:
[0054]
石英砂60份、碳酸钙56份、粉煤灰45份、碳酸钡15份;
[0055]
氧化铝35份;
[0056]
高炉灰23份;
[0057]
碳化硅25份、碳粉15份;
[0058]
氟硅酸钠26份、碳酸钡34份;
[0059]
磷酸钠7份、氧化锌8份。
[0060]
对比例1
[0061]
本实施例为本发明的第一对比实施例,该实施例所提供的一种多孔材料的制备原料如下:
[0062]
石英砂45份、碳酸钙40份、高炉灰43份、碳酸钡14份;
[0063]
高炉灰40份;
[0064]
碳化硅16份、碳粉15份;
[0065]
氟硅酸钠26份、碳酸钡32份;
[0066]
磷酸钠3份、氧化锌5份。
[0067]
对比例2
[0068]
本实施例为本发明的第二对比实施例,该实施例所提供的一种多孔材料的制备原料如下:
[0069]
石英砂45份、碳酸钙40份、高炉灰43份、碳酸钡14份;
[0070]
氧化铝25份;
[0071]
高炉灰40份;
[0072]
碳粉31份;
[0073]
氟硅酸钠26份、碳酸钡32份;
[0074]
磷酸钠3份、氧化锌5份。
[0075]
对比例3
[0076]
本实施例为本发明的第三对比实施例,该实施例所提供的一种多孔材料的制备原料如下:
[0077]
石英砂45份、碳酸钙40份、高炉灰43份、碳酸钡14份;
[0078]
氧化铝25份;
[0079]
高炉灰40份;
[0080]
碳化硅16份;
[0081]
氟硅酸钠26份、碳酸钡32份;
[0082]
磷酸钠3份、氧化锌5份。
[0083]
实施例5
[0084]
将实施例1-实施例4、对比例1-对比例3中的组分原料制备为多孔材料,具体的制备方法如下:
[0085]
s1:取各发泡基质进行初步粉碎并过500目筛,按照配方量混合成为混合发泡基质;
[0086]
s2:取配方量的混合发泡基质与氧化铝(对比例1不加入)、第一发泡剂、第二发泡剂、助熔剂以及稳泡剂进行混合的混合物,并向上述混合物中加水,采用湿法球磨法进行研磨,得到混合浆料,该混合浆料的研磨粒度小于300目;
[0087]
s3:对混合浆料进行干燥、粉碎以得到混合胚料,采用上述混合胚料装入耐高温模
具中进行烧结,烧结条件为:炉体预热至750-760℃,然后将装有混合胚料的耐高温模具置入炉体内,升温至800-820℃进行保温烧结,烧结时间为30-35min,取出至600-650℃进行保温,保温时长为40-45min,后取出冷却至室温,分别获得样品1-样品4、对照品1-对照品3。
[0088]
实施例6
[0089]
本实施例为本发明的测试实施例,本实施例分别对样品1-样品4、对照品1-对照品3进行性能测试,测试方法及测试结果如表1所示;
[0090]
表1多孔材料样品1-样品4、对照品1-对照品3的性能测试方法及测试结果
[0091][0092]
以上实施例仅用以说明本发明的技术方案而非限制,尽管参照较佳实施例对本发明进行了详细说明,本领域的普通技术人员应当理解,可以对本发明的技术方案进行修改或者等同替换,而不脱离本发明技术方案的宗旨和范围,其均应涵盖在本发明的权利要求范围当中。本发明未详细描述的技术、形状、构造部份均为公知技术。
再多了解一些
本文用于企业家、创业者技术爱好者查询,结果仅供参考。