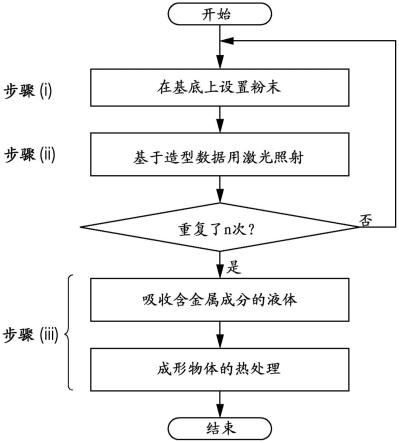
1.本发明涉及使用增材制造技术制造基于氧化硅的陶瓷制品的方法和通过该制造方法生产的陶瓷制品。
背景技术:
2.通过在作为制造目标的模型的三维数据的基础上增加材料以获得期望成形物体的增材制造技术正广泛用于短时间内的原型生产或者少量制品的制造。在金属制品的制造中,广泛使用直接成型系统,其中基于模型的三维数据通过用激光照射粉末使金属粉末凝固和成型。根据这种方法,能够通过有效地熔化并凝固金属粉末来获得精确且多样的制品。
3.近些年,正在努力建立使用陶瓷粉末作为原料的增材制造技术。然而,不同于金属,通用陶瓷例如氧化铝和氧化锆具有低的吸收激光的能力。因此,为了熔化陶瓷粉末,尽管必须使用大量的能量,但激光扩散从而使熔化不均匀,从而导致难以获得所需的成型精度。
4.因此,ptl 1公开了生产具有高精度的成形物体的技术,其通过向原料粉末添加吸收激光的吸收体来防止光的扩散。引用列表专利文献
5.ptl 1:日本专利公开第2019-19051号
技术实现要素:
技术问题
6.在陶瓷中,基于氧化硅的材料广泛用作构成铸芯的材料。铸芯是在制造具有中空内部的铸件时嵌入于对应模具中空部的部分中的模型,并且该模型最终从铸造制品中除去。因为所述芯需要具有优异的耐热性从而不会引起与要铸造的熔融金属的化学变化并在铸造过程结束时容易去除,所以可溶于碱性溶液的基于氧化硅的结构适合作为铸芯。这里,“基于氧化硅”是指二氧化硅为主要成分。在本发明中,术语“主要成分”是指以质量比包含最多的成分(元素或化合物)。
7.如果可通过增材制造技术生产铸芯,则有可能实现以低成本来铸造复杂的形状。因为铸造制品的尺寸或表面的精度受芯的尺寸和表面状态影响,所以要用作芯的基于氧化硅的成形物体需要具有高的成型精度以及能够经受铸造过程的高机械强度。
8.ptl 1描述了基于氧化硅的材料作为有待用于直接成型系统中的成型粉末。然而,基于氧化硅的材料在液相中具有高粘度并且因此通过用激光照射在熔融状态下变成球形,并且固化部分往往是多孔的。另外,因为在激光经过之后熔融部以高的降温速率快速冷却,所以固化部分几乎是非晶的。即使在通过激光照射引起液相烧结的情况下,该部分液相在激光经过之后快速冷却并变为非晶的。由于这些原因,通过ptl 1中公开的方法成型的基于氧化硅的成形物体具有优异的成型精度,但因为存在大量的非晶部分,所以机械强度对于
一些应用例如铸芯而言可能是不足的。
9.做出本发明用于解决以上问题并提供一种通过使用直接成型系统来制造具有高成型精度和优异机械强度的基于氧化硅的陶瓷制品的技术。问题的解决方案
10.制造根据本发明的陶瓷制品的方法的特征在于包括:(i)设置包含吸收预定波长的光的吸收体以及作为主要成分的二氧化硅的粉末的步骤;(ii)通过用包括具有预定波长的光的激光照射所述粉末从而烧结或熔化并凝固所述粉末的步骤;和(iii)在1470℃以上且小于1730℃加热通过重复步骤(i)和(ii)形成的成形物体的步骤。
11.另外,根据本发明的陶瓷制品是含有tb或pr和二氧化硅作为主要成分的陶瓷制品,并且特征在于硅的含量高于80质量%并且70质量%以上的二氧化硅是方石英。发明的有益效果
12.根据本发明,可通过使用直接成型系统来制造具有高成型精度和优异机械强度的基于氧化硅的陶瓷结构。
附图说明
13.图1a是示意说明通过粉末床熔合系统制造成形物体的方法的实施方案的示意性截面图。图1b是示意说明通过粉末床熔合系统制造成形物体的方法的实施方案的示意性截面图。图1c是示意说明通过粉末床熔合系统制造成形物体的方法的实施方案的示意性截面图。图1d是示意说明通过粉末床熔合系统制造成形物体的方法的实施方案的示意性截面图。图1e是示意说明通过粉末床熔合系统制造成形物体的方法的实施方案的示意性截面图。图1f是示意说明通过粉末床熔合系统制造成形物体的方法的实施方案的示意性截面图。图1g是示意说明通过粉末床熔合系统制造成形物体的方法的实施方案的示意性截面图。图1h是示意说明通过粉末床熔合系统制造成形物体的方法的实施方案的示意性截面图。图2a是示意说明通过熔覆系统制造成形物体的方法的实施方案的示意性截面图。图2b是示意说明通过熔覆系统制造成形物体的方法的实施方案的示意性截面图。图2c是示意说明通过熔覆系统制造成形物体的方法的实施方案的示意性截面图。图3是表示可变为共晶的a成分和b成分的组成比和状态之间的关系的相图。图4是显示根据本发明的陶瓷制品的制造流程的实例的图。
图5是显示根据本发明的陶瓷制品的制造流程的另一实例的图。图6a是说明本发明实施例中的激光照射过程的示意性透视图。图6b是说明本发明实施例中的激光照射过程的示意性透视图。
具体实施方式
14.制造根据本发明的陶瓷制品的方法包括以下步骤:(i)设置包含吸收预定波长的光的吸收体以及作为主要成分的二氧化硅的粉末的步骤;(ii)通过用包括具有预定波长的光的激光照射所述粉末从而烧结或熔化并凝固所述粉末的步骤;和(iii)在1470℃以上且小于1730℃加热成形物体的步骤,所述成形物体是通过重复步骤(i)和(ii)形成的。
15.现在参考附图将通过实例描述本发明的实施方案,但是本发明不限于以下实例和附图,并且本发明技术构思范围内的修改是可能的。
16.在直接成型系统之中,本发明适合用于粉末床熔合系统和定向能量层叠系统(所谓的熔覆系统),其中沉积成型材料以便在熔化时被覆盖。本发明的应用可大幅改进所得到的基于氧化硅的成形物体的机械强度,同时实现良好的成型精度。
17.顺便说明,氧化硅是指二氧化硅。氧化硅具有多晶型,但是状态诸如非晶、结晶和晶体结构并不重要。术语“多晶型”是指它能够以多种不同结晶形式存在,虽然具有相同的化学组成。
18.将使用图1a至1h来描述粉末床熔合系统的基本成型的流程。
19.首先,将粉末101放置于安装在台面151上的基底130上,并使用辊子152设置具有预定厚度的粉末(粉末层)102(图1a和1b)。基于由具有期望形状的模型的三维形状数据产生的成型数据(切片数据)利用从激光束源180发射的激光束照射粉末层102的表面,同时用扫描器181扫描。在激光束照射区域182中,粉末被烧结或熔化并凝固从而形成固化部分100(图1c)。随后,降低台面151,并在固化部分100上形成新的粉末层102(图1d)并且基于成型数据用激光束照射该新的粉末层。重复这些步骤系列以形成具有期望形状的成形物体110(图1e和1f)。最后,去除未固化的粉末103,并且在需要时执行成形物体的不必要部分的去除以及成形物体和基底之间的分离来获得成形物体(图1g和1h)。
20.然后将使用图2a至2c来描述熔覆系统。从熔覆喷嘴201的多个粉末供给孔202喷出粉末,同时用激光束203照射在其上聚焦粉末的区域以便基于成型数据在期望位置处渐进地形成固化部分100(图2a)。连续进行该过程以获得具有期望形状的成形物体110(图2b和2c)。最后,在需要时执行执行成形物体的不必要部分的去除以及成形物体和基底之间的分离。
21.在直接成型系统中例如粉末床直接成型系统和熔覆系统,通过激光束照射熔化的主要成分为二氧化硅的粉末通过从周边快速冷却而凝固,并形成主要由非晶氧化硅构成的凝固产物。通过这样的熔化并凝固过程形成的主要由非晶氧化硅构成的成形物体具有低密度从而不能具有高机械强度。
22.氧化硅可采取的结晶形式之一是方石英。方石英是在高温下稳定的结晶形式并因
此可在铸造期间所暴露的高温下维持稳定状态。此外,因为与非晶结构的氧化硅相比密度高,所以高温下的机械强度也优异。因为与其它结晶形式例如石英相比,方石英在碱性溶液中的溶解度高,所以方石英适合作为构成铸芯的结晶形式。
23.因此,在本发明中,用1470℃以上且小于1730℃的热处理通过重复步骤(i)和(ii)产生的成形物体。这样的加热处理实现了在高温下稳定并且具有优异机械强度的成形物体。据推断这是因为在成型之后加热处理将主要由非晶氧化硅制成的成形物体立即改变为方石英,其中成形物体中所含硅的70质量%以上与氧结合。
24.另外,因为取决于进行步骤(i)和(ii)的条件在短时间内用激光束照射的区域暴露于熔化温度和凝固温度,所以在一些情况下由于热应力在所获得的成形物体中形成大量裂纹。裂纹分布在整个成形物体中,即表面和内部。当用扫面电子显微术等检查成形物体的横截面时,在许多裂纹中,宽度为几纳米至几微米,并且长度从几微米至几毫米变化。如果在成形物体中形成大量此类裂纹,则机械强度降低。
25.当考虑因裂纹导致的机械强度降低时,优选在步骤(iii)中的加热处理之前使成形物体的裂纹吸收含金属成分的液体。所述加热将成形物体中含有的非晶氧化硅改变为具有更高机械强度的方石英,并且同时通过含金属成分的液体的作用通过选择性熔化裂纹附近来修复裂纹以减少成形物体中的裂纹。作为结果,能够显著改进成形物体的机械强度。
26.要被裂纹吸收的含金属成分的液体优选是能够向裂纹供应金属氧化物的液体。例如,含金属成分的液体优选是含有金属氧化物的液体或含有通过在吸收含金属成分的液体之后进行的加热处理产生金属氧化物的成分的液体。所述含金属成分的液体优选是可独立供应金属氧化物的组合物,但可以是通过与成形物体中包括的成分化合、固溶或扩散从而产生金属氧化物的组合物。
27.作为含金属成分的液体,例如可使用含有金属元素的溶液、溶胶液或颗粒分散体。含金属成分的液体可以是任何液体,只要调节液体的特性诸如粘度和浓度使得步骤(iii)中的成形物体吸收含金属成分的液体时金属元素遍布整个成形物体。金属元素以例如金属盐、金属醇盐或含金属元素的颗粒的形式包含在所述含金属成分的液体中。含金属元素的颗粒的实例包括金属、氧化物、氮化物、碳化物、硼化物和氢氧化物的颗粒。颗粒分散体除颗粒之外含有例如溶剂、分散剂和稳定剂。溶剂的实例包括水、有机溶剂和油类。分散剂的实例包括ph调节剂、硅烷偶联剂和表面活性剂。稳定剂的实例包括ph调节剂、表面活性剂、螯合剂和自分解抑制剂。然而,实例不限于以上。
28.当使用含有金属元素的颗粒分散在溶剂中的颗粒分散体作为所述含金属成分的液体时,为了使分散体遍布成形物体中的裂纹,颗粒优选具有比裂纹宽度充分更小的直径。认为宽度为1μm以上的裂纹会显著影响成形物体的强度。为了使颗粒渗入具有1μm以上宽度的裂纹,颗粒的平均粒径优选为300nm以下、更优选为50nm以下且进一步优选为30nm以下。使颗粒分散的含金属成分的液体易于通过例如调节颗粒组成或颗粒含量的方法来调节金属元素的浓度,并且可产生含有高浓度金属元素的液体。可通过使用含有高浓度的金属元素的液体作为所述含金属成分的液体来缩短使成形物体吸收所述含金属成分的液体以及进行加热处理的步骤所需的时间。即,可通过少量次数的吸收和加热处理过程的来修复裂纹。
29.另一方面,当使用含有金属元素的溶液或溶胶液时,因为金属元素甚至散布至微
小的裂纹,所以与使用颗粒分散体相比能够修复更细小的裂纹。然而,因为难以产生含有高浓度金属元素的液体,所以修复裂纹所需的时间往往比使用颗粒分散体时更长。
30.含金属成分的液体优选是如下液体:该液体产生可通过加热与构成成形物体的相形成共晶体的相。当成形物体包括多个相时,它足以形成可与成形物体中包括的任何相形成共晶体的相。当通过加热处理由含金属成分的液体形成的相是金属氧化物时并且当该金属氧化物相和成形物体中包括的相处于能够形成共晶体的关系时,金属成分已渗入的裂纹的附近在比成形物体的其它部分的熔点更低的温度下熔化。金属元素或金属氧化物然后随时间扩散到成形物体中,并且在加热之后随着温度降低,晶体以成形物体中包括金属元素的组成再结晶。作为结果,仅裂纹的附近区域软化同时维持成形物体的形状,并可获得减小或消除裂纹的效果。
31.当成分a和另一成分b可形成共晶体时,其可表述为“成分a和成分b处于共晶关系”。共晶体是从包括两种以上成分的液相同时结晶的两种以上晶体的混合物。短语“成分a和成分b可形成共晶”与“成分a和成分b具有共晶状态”同义。在具有共晶状态的情况下,存在共晶点(也称作共熔点)。共晶点是共晶发生的温度并且对应于相图中的液相曲线的最小值,所述相图由纵轴上的温度和横轴上的成分组成比率表示。对应于共晶点的组成被称为共晶组成(或共熔组成)。因此,成分a和成分b的共晶点低于成分a和成分b的熔点。
32.将允许吸收含金属成分的液体的成形物体中包括的化合物成分定义为成分a,并且将含金属成分的液体中包括的金属元素的氧化物定义为成分b。当假设成分a和成分b具有共晶状态的关系时,据推断由裂纹引起的区域熔化是由于以下现象。
33.当使成形物体吸收含金属成分的液体时,液体中包含的金属氧化物或金属元素存在于具有裂纹的成形物体的表面。如果在这种状态下进行加热,金属元素变为金属氧化物。因此,无论是否含金属成分的液体包括金属氧化物或金属元素,成分b存在于具有裂纹的成形物体的表面。如果在这种状态下进一步施加热量,则据推断在成分b存在于成形物体的表面的区域附近,成分a在低于成形物体熔点的温度下以与形成共晶组成或与共晶组成类似的组成的成分b的量相当的量熔化,并再结晶从而有助于修复裂纹。即,据推断因为成分a以与裂纹中存在的成分b的量相当的量熔化,所以仅软化裂纹的附近区域来提供减小或消除获得裂纹的效果同时维持成形物体的形状。
34.可通过调节使裂纹吸收含金属成分的液体的次数和含金属成分的液体中包括的金属元素的浓度来控制具有成形物体的裂纹的成形物体的表面中的成分b的量。在存在成分b的区域附近,成分a在低于成形物体熔点的温度下以与成分b的量相当的量熔化,产生共晶组成或与共晶组成类似的组成的组成比率。较大量的成分b使得能够修复较宽区域中的裂纹。
35.为了熔化裂纹附近,在成形物体吸收含金属成分的液体之后进行的加热处理的温度也是重要的。图3显示当作为成形物体中所含成分的成分a和由含金属成分的液体形成的成分b(金属氧化物)是可形成共晶体的组合时的相图。横轴示出成分a和成分b的组成比率,而纵轴示出每种组成的状态。
36.当成分a的熔点以tm表示,成分b的熔点以ti表示,并且成分a和成分b的共晶温度以te表示时,这些温度满足关系te《tm和te《ti。在这种情况下,优选地设置最大温度ts,其为通过在含金属成分的液体的吸收之后执行的加热处理成形物体达到的温度,以满足以下关
系:te≤ts《tm,更优选te≤ts《t
m-(t
m-te)/2。因此,可通过在低于成形物体的熔点tm的温度下选择性熔化裂纹附近来减小或消除裂纹,并且成形物体的形状可能得以维持。
37.因为本发明的技术构思是通过在成形物体中产生方石英来改进机械强度,所以用于修复裂纹的加热中的最大温度ts为1470℃以上和1730℃以下是必要的,这是在成形物体中产生方石英的温度范围。因此,重要的是适当选择成形物体中包括的成分a和含金属成分的液体的组合。
38.根据待使用的含金属成分的液体的组成,可通过在吸收含金属成分的液体之后多次重复加热处理来进一步减小或消除裂纹。当选择其中成分a和b的熔点满足关系tm《ti的组合时,可通过相对少的次数获得高的效果。这是因为,如图3中显示,当tm《ti时,因为在包括高比率的成分a的组成中成分a和成分b形成共晶体,所以在其中含金属成分的液体中包括的成分b的比率低的状态下,裂纹附近区域可在共晶温度下熔化。顺便提及,tm《ti的条件不是必要的。
39.考虑到以上,当成形物体的主要成分是二氧化硅(sio2,熔点tm=1730℃)时,含金属成分的液体优选是含铝液体(含铝成分的液体)。含铝成分的液体中包括的大多数铝元素通过加热变为氧化铝(al2o3,熔点ti=2070℃)。sio2和al2o3的共晶温度te为1595℃。因为sio2和al2o3分别对应于成分a和成分b,所以满足tm《ti的关系。在使主要成分是二氧化硅的成形物体吸收含铝成分的液体之后进行的加热处理的温度ts可被设定在1595℃以上且小于1730℃的范围内,这允许在成形物体中产生方石英。ts更优选被设定在1595℃以上且1663℃以下的范围内。
40.因此,在主要成分是二氧化硅的成形物体的情况下,可通过使裂纹吸收含铝成分的液体来减少或消除裂纹,即使在比sio2的熔点低100℃以上的温度下进行加热处理。因此,可通过在比作为成形物体的主要成分的sio2的熔点充分更低的温度下进行加热处理来获得具有改进机械强度的成形物体,同时防止成形物体的形状改变。
41.即使在使用含有锆元素的液体(含有锆成分的液体)作为含金属成分的液体的情况下,成分a和成分b分别是sio2(熔点t
mi
=1730℃)和zro2(熔点ti=2715℃),并且满足tm《ti的关系。
42.如上文所述,可通过以下方式获得具有优异机械强度的基于氧化硅的陶瓷制品:使由直接成型系统生产的主要由非晶氧化硅制成的成形物体的裂纹吸收与氧化硅一起形成共晶体的金属成分,并在适当的温度下进行加热处理。
43.顺便提及,即使粉末自身含有待用于修复裂纹的金属元素,也无法获得减少成形物体裂纹的效果。如果待用于成型的粉末包括一定量以上的待用于修复裂纹的金属元素,则在整个成形物体中包括待用于修复裂纹的金属元素,并且不能通过吸收含金属成分的液体局部地降低裂纹附近的熔点。整个成形物体也会被加热熔化,从而导致成形物体变形的风险。即,为了修复裂纹而不减小成形物体的成型精度,重要的是在局部地提高所制造成形物体中产生的裂纹附近的金属元素浓度的状态下进行加热处理。
44.为了在成型之后通过使裂纹吸收含金属成分的液体从而局部地熔化仅裂纹附近,粉末优选不包括3.0质量%以上的所述含金属成分的液体中含有的金属元素的氧化物。即,当成型粉末包括所述含金属成分的液体中含有的金属元素时,其含量优选小于整个粉末的3.0质量%,进一步优选小于2.0质量%。通过使用这样的粉末和含金属成分的液体的组合,
可实现具有高成型精度和改良机械强度的制品。
45.顺便提及,将详细地描述制造根据本发明的陶瓷制品的方法中包括的三个步骤。
46.《步骤(i)》在基底上设置粉末,所述粉末包括吸收光的吸收体和作为主要成分的二氧化硅,所述光具有待照射的激光中包括的波长。可根据待使用的激光的类型选择吸收体,并且氧化铽或氧化镨是特别优选的。
47.二氧化硅(氧化硅)由化学式sio2表示。粉末中含有的sio2的原子之间的结合状态没有特别限制并可为非晶态或结晶状态,例如方石英和石英,或可为它们的混合物。特别地,主要成分是具有高热导率的方石英的粉末可能通过激光照射熔化并因此是特别优选的。因为在步骤(i)中致密地设置粉末,所以构成sio2粉末作为主要成分的sio2颗粒优选具有赋予高流动性的接近球形的形状并且优选具有5μm以上且200μm以下的平均粒径。更优选的平均粒径为10μm以上且150μm以下。在本发明中,平均粒径不是单个颗粒的粒径,而是是具有相同组成的群体的粒径的中值,即累计频率为50%时的粒径(d50)。平均粒径的测量程序没有特别限制,并且平均粒径可由细颗粒粉末的显微图的投影图像以等效圆直径计算得到或者可使用动态光散射方法测定。
48.主要成分是二氧化硅的粉末包括吸收体作为亚成分。术语“吸收体”在本文是指对于具有待用于成型的激光中包括的波长的光显示出高于二氧化硅的吸收能力的成分(元素或化合物)。对于所用激光束中包括的波长的光而言,吸收体的吸收能力优选为10%以上、更优选40%以上且进一步优选60%以上的吸收率。可使用一般的分光镜测量单一吸收体的吸收率。具体地,使用积分球并利用假定波长(接近于制造中待使用的激光波长)照射填充在样品盘中的单一吸收体来测量吸收。对不存在样品时的吸收进行测量作为参比数据,并可从它们的比率计算吸收率。
49.这样的吸收体有效地吸收制造中使用的激光来提高自身的温度,这扩展至对应于激光焦点尺寸的区域中存在的其它组合物从而引起温度提高。因此,实现有效的局部加热,能够使在加工区域(用激光束照射的区域)和未加工区域(未用激光束照射的区域)之间的界面清晰,并改进成型精度。
50.吸收体优选为如下:其通过用激光照射而至少部分地改变为显示相对低吸收的另一组合物。其实例包括如下组合物:其中通过伴随温度升高的氧脱离,金属元素的价态改变为对激光显示相对低吸收的另一金属氧化物。作为替代,吸收体可为如下组合物:其通过与大气中的气体或粉末中包括的另一组合物部分结合或者分解例如氧脱离而改变为不同于粉末状态的组合物并且并入成形物体的组合物。吸收体的实例包括氧化物、过渡金属碳化物、过渡金属氮化物、si3n4、aln、硼化物和硅化物。适合作为吸收体的组合物是tb4o7、pr6o
11
、ti2o3、tio、sio、zno、锑掺杂的氧化锡(ato)、铟掺杂的氧化锡(ito)、mno、mno2、mn2o3、mn3o4、feo、fe2o3、fe3o4、cu2o、cuo、cr2o3、cro3、nio、v2o3、vo2、v2o5、v2o4、co3o4、coo、过渡金属碳化物、过渡金属氮化物、si3n4、aln、硼化物和硅化物。过渡金属碳化物优选是tic或zrc。过渡金属氮化物优选是tin或zrn。硼化物优选是tib2、zrb2或lab6。硅化物优选是tisi2、zrsi2或mosi2。可从这些组合物选择与构成粉末的另一组合物具有高亲和力的组合物作为吸收体。因为粉末是二氧化硅,所以金属氧化物优选作为吸收体。从与二氧化硅的最高亲和力的观点来看,sio优选作为吸收体。顺便提及,吸收体可为单一组合物或者可为两种以上组合
物的组合。
51.对于激光束显示出良好能量吸收的吸收体优选微细且均匀地分散在粉末中。因此,当用激光束照射时在粉末中均匀地发生反应,从而导致成型精度的进一步改进。从这样的观点,粉末中包括的吸收体的平均粒径优选为1μm以上且小于10μm,并且更优选为1μm以上且小于5μm。
52.粉末中包括的吸收体的量优选为0.5体积%以上且10体积%以下。当该量为0.5体积%以上时,在使用激光束的一般条件下在激光束照射区域中随机地存在一个或多个吸收体颗粒,并且可足以实现作为吸收体的功能。此外,当该量为10体积%以下时,可防止由于激光束照射所致的粉末温度的急剧提高,并且可防止熔化材料散射到周围(即成型精度的减小)。
53.当使用nd:yag激光或光纤激光作为成型用的激光时,能够与二氧化硅形成共晶体的氧化铽(tb4o7)或氧化镨(pr6o
11
)特别优选作为吸收体,这是由于以下两个原因。第一个原因在于氧化铽和氧化镨显示出对nd:yag激光(波长:1064nm)或光纤激光(波长:1030至1100nm)的良好能量吸收。当用于成型的粉末包括对于用激光束照射的粉末具有足够能量吸收的吸收体时,粉末中的热量扩散被进一步阻止并变为局域的,并且可减小热量对非成型部的影响,从而导致成型精度的进一步改进。
54.第二个原因在于如果粉末含有氧化铽或氧化镨,则在由氧化硅形成的网络中形成相分离的结构,在该结构中两种以上的相彼此杂乱地交织在一起。如以上所述,因为基于氧化硅的材料在液相中具有高粘度,所以通过用激光束照射熔化成液态的氧化硅变为球形,并且固化部分可能变成其中球体以网络形状连接的结构,即多孔的。然而,当粉末包括氧化铽或氧化镨时,形成其中氧化硅相和包括氧化铽或氧化镨的相的网络彼此杂乱地交织在一起的相分离结构以防止裂纹的扩展,从而导致成形物体的机械强度改进。为了也获得微小的相分离结构,氧化铽和氧化镨的粒径优选为1μm以上且小于10μm、更优选1μm以上且小于5μm。因此,获得具有更高机械强度的成形物体。
55.为了调节所生产的陶瓷制品的物理性质,粉末可以按小于10质量%的比率包括除二氧化硅和吸收体以外的组合物。
56.顺便提及,在本说明书中,虽然可以用化学式表示材料,如上述的sio2和tb4o7,但实际材料的构成元素比不必与所述化学式严格地一致,只要满足本发明的主旨即可。也就是说,构成材料的金属元素的价态可稍微不同于从化学式预期的价态。例如,当吸收体是sio时,即使吸收体的构成元素比率(si:o)为1:1.30,这样的情况也被包括在本发明中。从获得足够光吸收能力的观点来看,更优选地,构成元素比率从化学计量比的偏差在
±
15%内。
57.在基底上进行成型。考虑到成形物体的用途、制造条件等,可从成形物体的制造中通常使用的材料(例如陶瓷、金属和玻璃)中适当选择和使用基底的材料。在步骤(iii)中,当成形物体与基底一起加热时,优选使用具有耐热性的陶瓷作为基底。
58.在粉末床熔合系统中,如图1a至1h中所示,在整个基底上用辊、刮刀等以预定厚度设置粉末。在熔覆系统中,如图2a至2c中显示,从喷嘴向有待用激光束照射的位置注射和供应粉末,并且将粉末设置在基底上或设置在基底上的成形物体上,使得粉末覆盖。
59.《步骤(ii)》
在随后的步骤(ii)中,基于成型数据用激光照射步骤(i)中设置的粉末以便烧结或熔化并凝固所述粉末,所述成型数据是从要生产的模型的三维形状数据产生。
60.在粉末床熔合系统中,如图1a至1h所示,用扫描的激光束照射在步骤(i)中在基底上以预定厚度设置的粉末层的预定区域,以便烧结或熔化并凝固所述粉末。在熔覆系统中,如图2a至2c所示,将粉末选择性地设置在待成型的区域中,使得将粉末注射和供应并覆盖在步骤(i)中的基底上并同时用激光束照射以熔化并凝固粉末。
61.当用激光束照射粉末时,粉末中包括的吸收体吸收能量,并且能量转化为热量从而使粉末熔化。当粉末被烧结时,部分颗粒熔化。在激光束经过以及照射结束之后,熔化部的热量逸散至大气和周围环境从而使粉末冷却,并且形成固化部分。因为在熔化并凝固的过程中发生急剧的温度改变,所以成形物体的大部分变为非晶氧化硅。另外,急剧的温度改变在成形物体的表面层和内部引起应力从而在许多情况下形成裂纹。当形成裂纹时,随后进行的加热步骤可减少裂纹。另外,还可通过引入下文详述的吸收含金属成分的液体的步骤来进一步减少或消除裂纹。
62.如上文所述,当主要成分是二氧化硅的粉末包括氧化铽或氧化镨时,在通过熔化粉末形成的连接球形氧化硅的网络中形成相分离的结构,其中两种或多种相彼此杂乱地交织在一起。当在步骤(iii)中对这样的结构进行加热处理时,氧化硅结晶为方石英,从而导致成形物体的机械强度的改进。
63.激光束的类型没有特别限制,并且例如1μm波长带的yag激光或光纤激光和10μm波长带的co2激光是优选的。特别地,由于氧化铽和氧化镨的高吸收,1μm波长带的yag激光或光纤激光是优选的。
64.《步骤(iii)》如在图4的流程图中所示,在步骤(iii)中,在1470℃以上且小于1730℃下加热通过重复步骤(i)和(ii)多次形成的成形物体。重复次数对应于从待制造的三维物体的三维形状数据产生的切片数据的切片数n。
65.在成形物体中,通过步骤(i)在步骤(i)和(ii)中形成的固化部分上设置新粉末层。基于从成型模型的三维形状数据产生的成型数据用扫描激光束照射所设置的粉末。用激光束照射的区域的粉末熔化并凝聚。这时,之前形成的固化部分的表面层也熔化并由此与随后形成的固化部分成为一体。可根据成型模型的三维形状数据通过交替地重复步骤(i)和(ii)来获得具有期望形状的成形物体。
66.当通过重复步骤(i)和(ii)形成的成形物体中包括大量的裂纹时,如图5的流程图中所示,优选在进行加热处理之前进行使成形物体吸收含金属成分的液体的处理。
67.只要能够以裂纹所需要的量将含金属成分的液体供给到成形物体中包括的裂纹各处,不特别限制使成形物体吸收含金属成分的液体的工序。可将成形物体浸入并浸渍含金属成分的液体,或者可将含金属成分的液体雾化或喷涂到成形物体或者可用刷子等施涂到表面以便吸收。此外,可将这些工序中的两种或更多种组合,或者可将相同工序重复多次。
68.如上所述,在主要成分是氧化硅的成形物体中,例如含铝成分的液体或含锆成分的液体(含锆的液体)可用作含金属成分的液体,并且含铝成分的液体是特别优选的。下文中,将详细描述使用含铝成分的液体作为含金属成分的液体的情形。
69.含铝成分的液体优选由例如以下构成:包括铝元素的原料、溶剂和稳定剂。作为包括铝元素的原料,可使用各种铝化合物,并且可使用铝的金属醇盐或氯化物。
70.在含铝成分的液体包括金属醇盐形式的铝时,其优选包括铝醇盐、有机溶剂和稳定剂。例如,将铝醇盐首先溶解在有机溶剂中来制备铝醇盐的溶液。铝醇盐的实例包括仲丁醇铝、乙醇铝、正丁醇铝、叔丁醇铝和异丙醇铝。待添加到铝醇盐的有机溶剂的量按相对于化合物的摩尔比计优选为5以上且30以下、更优选10以上且25以下。顺便提及,在本发明中,m的量以相对于n的摩尔比计为5的事实是指待添加的m的摩尔量为n的摩尔量的5倍。如果溶液中的铝醇盐浓度过低,则成形物体不能吸收足够量的铝成分。与此相反,如果溶液中的铝醇盐浓度过高,则溶液中的铝成分聚集并且不能将铝成分均匀地设置在成形物体的裂纹部分上。
71.作为用于溶解铝醇盐的有机溶剂,使用醇、羧酸、脂肪烃和脂环烃、芳族烃、酯、酮、醚和这些溶剂中两种以上的溶剂混合物。作为醇,例如甲醇、乙醇、2-丙醇、丁醇、2-甲氧基乙醇、2-乙氧基乙醇、1-甲氧基-2-丙醇、1-乙氧基-2-丙醇、1-丙氧基-2-丙醇、4-甲基-2-戊醇、2-乙基丁醇、3-甲氧基-3-甲基丁醇、乙二醇、二乙二醇和甘油是优选的。作为脂肪烃和脂环烃,例如正己烷、正辛烷、环己烷、环戊烷和环辛烷是优选的。作为芳族烃,例如苯、二甲苯和乙苯是优选的。作为酯,例如甲酸乙酯、乙酸乙酯、乙酸正丁酯、乙二醇单甲醚乙酸酯、乙二醇单乙醚乙酸酯和乙二醇单丁醚乙酸酯是优选的。作为酮,例如丙酮、甲乙酮、甲基异丁基酮和环己酮是优选的。作为醚,可提及例如二甲氧基乙烷、四氢呋喃、二氧六环和二异丙醚。在含铝成分的液体的制备中,从溶液稳定性的角度看,在以上提到的各种溶剂中优选使用醇。
72.因为铝醇盐与水的反应性高,所以铝醇盐通过空气中的水分或通过添加水从而剧烈水解以引起溶液的浑浊或沉淀。为了防止它们发生,优选添加稳定剂用于稳定溶液。稳定剂的实例包括β-二酮化合物,例如乙酰丙酮、3-甲基-2,4-戊二酮、3-乙基-2,4-戊二酮和三氟乙酰丙酮;β-酮酯化合物,例如乙酰乙酸甲酯、乙酰乙酸乙酯、乙酰乙酸丁酯、乙酰乙酸烯丙酯、乙酰乙酸苄酯、乙酰乙酸异丙酯、乙酰乙酸叔丁酯、乙酰乙酸异丁酯、3-氧代己酸乙酯、2-甲基乙酰乙酸乙酯、2-氟乙酰乙酸乙酯和乙酰乙酸2-甲氧基乙酯;和链烷醇胺,例如单乙醇胺、二乙醇胺和三乙醇胺。待添加的稳定剂的量按相对于铝醇盐的摩尔比计优选为0.1以上且3以下,更优选0.5以上且2以下。
73.可通过在室温下反应制备溶液或可在回流下制备溶液。
74.在含铝成分的液体包括氯化物形式的铝时,优选包括铝盐和水。对铝盐没有特别限制,只要它是水溶性的并且特别优选为例如硝酸盐、硫酸盐、乙酸盐和氯化物。在一些类型的铝盐中,其水溶液不稳定。在这样的情况下,可通过添加稳定剂来稳定溶液。作为稳定剂,优选包括有机酸、表面活性剂和螯合剂中的至少一种。作为有机酸,例如丙烯酸、丙烯酸2-羟乙酯、2-丙烯酰氧基乙基丁二酸、2-丙烯酰氧基乙基六氢邻苯二甲酸、2-丙烯酰氧基乙基邻苯二甲酸、2-甲基己酸、2-乙基己酸、3-甲基己酸和3-乙基己酸是优选的。作为表面活性剂,例如优选离子表面活性剂例如油酸钠、脂肪酸钾、烷基磷酸钠、烷基甲基氯化铵和烷基氨基羧酸盐,和非离子酸例如聚氧乙烯月桂脂肪酸酯和聚氧乙烯烷基苯基醚。作为螯合剂,例如羟基酸例如乙醇酸、抗坏血酸、柠檬酸、丙二酸、葡糖酸、草酸、丁二酸、苹果酸、酒石酸和乳酸,氨基酸例如甘氨酸、丙氨酸、甘氨酸、谷氨酸、天冬氨酸、组氨酸、苯丙氨酸、天冬
酰胺、精氨酸、谷氨酰胺、胱氨酸、亮氨酸、赖氨酸、脯氨酸、丝氨酸、色氨酸、缬氨酸和酪氨酸是优选的,氨基羧酸例如二乙三胺五乙酸(dtpa)、羟乙基乙二胺三乙酸(hedta)、三乙四胺六乙酸(ttha)、1,3-丙二胺四乙酸(pdta)、1,3-二氨基-6-羟基丙烷四乙酸(dpta-oh)、羟乙基亚氨基二乙酸(hida)、二羟基乙基甘氨酸(dheg)、乙二醇醚二胺四乙酸(gedta)、二羧基甲基谷氨酸(cmga)和(s,s)-乙二胺二丁二酸(edds),膦酸例如1-羟基亚乙基-1,1-二膦酸(hedp)、2-磷酸丁酮-1,2,4-三羧酸(pbtc)、乙二胺四(亚甲基膦酸)、二乙三胺五(亚甲基膦酸),和次氮基三(亚甲基膦酸),和芳族酸例如水杨酸。
75.制造所述含铝成分的液体的方法没有限制。含铝成分的液体优选通过混合铝盐、水和稳定剂产生,但可通过一次性混合所有成分来产生。作为替代,可通过以下方式产生含铝成分的液体:混合金属盐和稳定剂以及然后添加并混合水,或者混合金属盐和水以及然后添加并混合稳定剂,或者混合稳定剂和水以及然后添加并混合金属盐。
76.作为替代,作为含铝成分的液体,使用由包括铝元素的颗粒、分散剂和溶剂构成的颗粒分散体也是优选的。
77.作为包括铝元素的颗粒,可使用铝颗粒或氧化铝颗粒。铝颗粒或氧化铝颗粒可通过由自上而下的方法粉碎各自材料来产生或者可通过自下而上的方法从例如金属盐、水合物、氢氧化物或碳酸盐使用例如水热反应的工序来合成。作为替代,可使用可商购产品。
78.为了使颗粒渗入裂纹,颗粒的尺寸为300nm以下,更优选为50nm以下,且进一步优选为30nm以下。
79.微细颗粒的形状没有特别限制并且可为球形、粒状、柱状、椭球形、立方体形、长方体形、针状、柱状、板状、鳞片状或角锥形。
80.作为分散剂,优选包括选自有机酸、硅烷偶联剂和表面活性剂中的至少一种。作为有机酸,优选例如丙烯酸、丙烯酸2-羟乙酯、2-丙烯酰氧基乙基丁二酸、2-丙烯酰氧基乙基六氢邻苯二甲酸、2-丙烯酰氧基乙基邻苯二甲酸、2-甲基己酸、2-乙基己酸、3-甲基己酸和3-乙基己酸。作为硅烷偶联剂,优选例如3-丙烯酰氧基丙基三甲氧基硅烷、3-甲基丙烯酰氧基丙基三甲氧基硅烷、己基三甲氧基硅烷、辛基三乙氧基硅烷和癸基三甲氧基硅烷。作为表面活性剂,优选例如离子表面活性剂例如油酸钠、脂肪酸钾、烷基磷酸钠、烷基甲基氯化铵和烷基氨基羧酸盐,和非离子酸例如聚氧乙烯月桂脂肪酸酯和聚氧乙烯烷基苯基醚。
81.作为溶剂,使用醇、酮、酯、醚、酯改性的醚、烃、卤代烃、酰胺、水、油和它们中两种或更多种的溶剂混合物。作为醇,优选例如甲醇、乙醇、2-丙醇、异丙醇、1-丁醇和乙二醇。作为酮,优选例如丙酮、甲乙酮、甲基异丁基酮和环己酮。作为酯,优选例如乙酸乙酯、乙酸丙酯、乙酸丁酯、4-丁内酯、丙二醇单甲醚乙酸酯和3-甲氧基丙酸甲酯。作为醚,优选例如乙二醇单甲醚、二乙二醇单丁醚、丁基卡必醇、2-乙氧基乙醇、1-甲氧基-2-丙醇和2-丁氧基乙醇。作为改性的醚,优选例如丙二醇单甲醚乙酸酯。作为烃,优选例如苯、甲苯、二甲苯、乙苯、三甲基苯、己烷、环己烷和甲基环己烷。作为卤代烃,优选例如二氯甲烷、二氯乙烷和氯仿。作为酰胺,优选例如二甲基甲酰胺、n,n-二甲基乙酰胺和n-甲基吡咯烷酮。作为油,优选例如矿物油、植物油、蜡油和硅油。
82.可通过以下方式产生颗粒分散体:一次性混合铝颗粒或氧化铝颗粒、分散剂和溶剂,或者混合铝颗粒或氧化铝颗粒和分散剂并然后混合溶剂。作为替代,可通过以下方式产生颗粒分散体:混合上述铝或氧化铝的微细颗粒和溶剂并然后混合分散剂,或者混合分散
剂和溶剂并然后混合铝或氧化铝的微细颗粒。
83.在上述步骤(iii)中,为了使成形物体中形成的裂纹吸收含铝成分的液体以及使存在铝元素的区域的附近局部熔化,可调节加热温度和裂纹中的铝元素量。可通过例如以下方式来调节裂纹中的铝元素的量:含铝成分的液体中的铝元素浓度,使裂纹吸收含铝成分的液体的方法及其次数。作为替代,还能够通过按顺序重复吸收含铝成分的液体和加热的过程来调节。特别地,更可能通过提高裂纹中存在的铝元素的量来熔化裂纹附近。因此,通过调节裂纹中存在的铝元素的量可以在不使成形物体的形状塌陷的情况下维持由直接成型系统形成的复杂形状或精密形状,并且能够获得基本上按照设计那样的成形物体形状从而以高的成型精度实现成型。
84.在不低于由氧化硅和氧化铝形成的共晶相的共晶点并且不高于氧化硅的熔点(1710℃)的温度下加热吸收了含铝成分的液体的氧化硅成形物体。因此,在基于氧化硅的成形物体的内部和表面层中的裂纹中存在的氧化硅以对应于从含铝成分的液体产生的氧化铝或从一开始就包括在含铝成分的液体中的氧化铝的量熔化,用以形成共晶组合物。即,因为氧化铝以大于远离裂纹的区域中的量存在于成形物体的与含铝成分的液体接触的表面,所以裂纹附近接近于共晶组成从而可被选择性地熔化。使氧化硅转化为方石英,并且同时,可通过进行加热处理减少或消除裂纹,使得在吸收含铝成分的液体的步骤之后裂纹附近中的氧化硅的最高温度为1595℃以上且小于1730℃。
85.加热时间没有限制,只要裂纹的附近达到上述的最高温度。具体地,可在1595℃以上且小于1730℃下加热成形物体,这是裂纹附近需要达到的温度。
86.加热的方法没有特别限制。可通过用能量束照射来加热或者可通过放入电弧炉来加热所述吸收了含铝成分的液体的成形物体。在用能量束加热的情况下,优选预先用热电偶等来掌握在能量束的热量和成形物体的温度之间的关系,使得成形物体被加热到上述的优选温度。
87.在加热处理步骤中,成形物体可通过表面层或裂纹附近的熔化而粘附至定位器(setter)。因此,当在加热处理步骤中在定位器上设置成形物体时,定位器优选是惰性的。作为惰性定位器,例如铂适用在大气中,以及铟适用在低氧气氛中。
88.在步骤(iii)中,在成形物体中形成包括二氧化硅和铽或镨的相(晶体晶粒)以及包括铝元素的相(晶体晶粒),但是它们的粒度(例如平均粒径)非常不同。由此推断因为裂纹部及其附近熔化从而在减小表面能的方向上移动,所以裂纹被减少或消除。还推断随着加热进一步进行,分布在裂纹部中的铝成分扩散到成形物体的结晶和非晶内部,并且成形物体的晶体在包括铝成分的状态下再结晶。除此之外,成形物体中的裂纹因此被减少或消除,形成由多种相构成的相分离结构,其中晶体晶粒的平均粒径彼此不同。因此,改进成形物体的加工性,并且能够在较少开裂的情况下精密的精加工。
89.《陶瓷制品》本发明的陶瓷制品优选具有包括两种以上,特别是三种以上的相的相分离的结构。三种相的优选组合由以下构成:主要成分是sio2的相、主要成分是包括铽或镨的稀土硅酸盐的相、和主要成分是al2o3的相,其为在含金属成分的液体中包括的金属元素的氧化物。sio2、稀土硅酸盐和al2o3处于彼此形成共晶体的关系,并且可稳定地形成由三种相组成的复杂的相分离的结构。
90.主要成分是sio2的相是在步骤(iii)的加热过程中由非晶氧化硅转化的方石英。作为主要成分是包括铽或镨的稀土硅酸盐的相,具体而言si2tb2o7相和si2pr2o7相是优选的形式。可通过结构分析通过例如x-射线衍射、电子束衍射或ebsd(电子背散射衍射)来识别各种相。每种相的晶体结构根据制造过程而稍微变化,但是形成共晶体的三种相优选由如上述的晶体结构制成。
91.方石英分为α-方石英和β-方石英并且具有约240℃的相转变温度。因为在这个相转变温度下方石英的体积剧烈变化,所以方石英被认为是易受温度改变影响的材料。然而,在本发明中,即使氧化硅转化为方石英,在温度变化时也获得了优异的机械强度。据推断这是因为基于氧化硅的结构除方石英之外还包括由多种相例如tb2si2o7相和pr2si2o7相组成的相分离的结构。据推断当基于氧化硅的结构具有由多种相组成的相分离的结构时,在相转变温度下因热膨胀产生的体积变化变得平缓,从而防止因温度改变所致的急剧体积变化。
92.在用作铸芯时,本发明的陶瓷制品中的si含量以氧化物换算(sio2换算)优选高于80质量%。如果si含量为80质量%以下,则无法获得作为铸芯所需要的在碱性溶液中的溶解性。碱性溶液的实例包括氢氧化钠水溶液和氢氧化钾水溶液。
93.本发明的陶瓷制品中的tb或pr含量以氧化物换算(tb2o3或pr2o3换算)优选为1.0质量%以上且20质量%以下,更优选为3.0质量%以上且15质量%以下。如果tb或pr的含量小于1.0质量%,因为激光能的吸收量小,所以存在无法获得高精度成形物体的风险。如果tb或pr的含量高于20质量%,无法获得作为铸芯所需要的在碱性水溶液中的溶解性。
94.在本发明的陶瓷制品中,70质量%以上的二氧化硅是与氧结合的方石英。如果方石英的量小于70质量%,则存在无法获得作为铸芯所需要的强度的风险。优选地,90质量%以上、更优选95质量%以上的二氧化硅是方石英。
95.本发明的陶瓷制品优选具有10%以上且40%以下的孔隙率。如果孔隙率小于10%,则抗弯强度变得过高,并且当用作铸芯时铸造物可能破裂。如果孔隙率高于40%,则无法获得作为结构的必要强度。顺便提及,本发明中的术语“孔隙率”是指表观孔隙率,这将在下文详细描述。
96.本发明中的陶瓷制品中含有的硼(b)含量优选小于1000ppm。如果b含量高于1000ppm,则软化点降低,并且在一些情况下无法获得作为铸芯所需的耐热性。
97.《评价物理性质的方法》(机械强度)通过基于jis(日本工业标准)r1601的三点弯曲测试来评价成形物体的机械强度,jis r1601是关于在室温下的精细陶瓷的抗弯强度测试。使用当10个测试件中每一个断裂时的最大载荷p[n]、外部支点之间的距离l[mm]、测试件的宽度w[mm]和测试件的厚度t[mm],通过下式计算三点弯曲强度:3
×
p
×
l/(2
×w×
t2)
ꢀꢀꢀꢀꢀꢀ
(式1)并对它们取平均。
[0098]
(孔隙率)通过基于精细陶瓷的密度和表观孔隙率的测量方法的jis r1634的方法来评价成形物体的孔隙率。具体地,对与用于测量机械强度的样品类似的三个陶瓷制品中每一个通过{(w3-w1)/(w3-w2)}
×
100使用成形物体的干质量w1、水中的质量w2、和水饱和质量w3来
计算孔隙率,并对它们取平均。
[0099]
(相对密度)通过成形物体的体积密度(用质量除以体积获得)除以理论密度来计算相对密度[%]。由晶体结构计算理论密度。通过进行x-射线衍射测量并进行rietveld分析来识别晶体结构。
[0100]
(晶体结构)通过对测量物体的中心部的横截面进行抛磨制备的测量表面进行x-射线衍射测量来识别陶瓷制品中包括的相。
[0101]
通过以下方法计算测量物体中包括的每个相的含量。在测量表面的100μm
×
100μm尺寸的视场中的十个不同位置处,进行sem-edx和ebsd的同时分析,并对组成和结晶相进行作图。对于所产生的10幅图,测定由每种相占据的面积比率,并从对其取平均得到的值计算样品中包括的每种相的比率。当包括小的相时,可使用透射电子显微镜(tem)以类似的方式分析组成和晶体结构。
[0102]
通过以下方式计算构成相的晶体晶粒的粒径:对使用ebsd在测量表面中观察到的单一相中的300个以上晶体晶粒进行观察,以及计算晶体晶粒的等效圆直径的平均值。
[0103]
(组成分析)通过感应耦合等离子体原子发射光谱法(icp-aes)测量粉末、成形物体或陶瓷制品中包括的si、tb、pr、al和zr的含量,并且通过gdms或icp-ms测量包括b在内的其它元素的含量。实施例
[0104]
(实施例1)制备并称量平均粒径为约38μm的sio2粉末和平均粒径为4μm的tb4o7粉末,使得si的含量以氧化物换算(sio2换算)为90.0质量%并且tb的含量以氧化物换算(tb4o7换算)为10.0质量%(表1)。顺便提及,在sio2粉末中,方石英是主要成分。使用干式球磨机混合所称量的粉末30分钟以获得粉末混合物。顺便提及,本发明中的平均粒径是中值直径(也被称作中央值)以及累计频率为50%时的粒径(d50)。在通过icp光谱分析的粉末混合物的组成分析中,氧化铝的含量小于1质量%。
[0105]
表1
[0106]
随后,按图1a至1h中所示的步骤生产实施例1的成形物体。产生的成形物体的形状是5mm
×
42mm
×
6mm的长方体。使用配备有50w光纤激光器(束直径:65μm)的3d系统公司的proxdmp 100(商品名)形成所述成形物体。
[0107]
首先,使用辊子在氧化铝基底130上以20μm的厚度形成上述粉末的第一粉末层(图1a和1b)。
[0108]
随后,用具有功率为47.5w的扫描激光束照射粉末层以使5mm
×
42mm的矩形区域中的材料粉末熔化并凝固从而形成固化部分100(图1c)。这时描画速度为60mm/s,并且描画间距为80μm。如图6a中所示,将描画线设定为相对于矩形的每一侧成45度角。
[0109]
随后,用辊子新形成20μm厚度的粉末层从而覆盖固化部分100,并用扫描激光束照射以便使5mm
×
42mm的矩形区域中的材料粉末熔化并凝固从而形成固化部分100(图1d和1e)。这时,如图6b中所示,在与第一层的描画线正交的方向上扫描激光以熔化并凝固粉末。
重复这些过程直至固化部分的高度达到6mm,并产生42mm
×
5mm
×
6mm的14个成形物体。
[0110]
当用光学显微镜观察成形物体的表面时,在避开孔时测量的每个成形物体表面的ra为30μm以下。
[0111]
从氧化铝基底上分离所产生的每个成形物体,并抛磨13个成形物体以获得40mm
×
4mm
×
3mm的成形物体作为用于三点弯曲强度测试和用于孔隙率测量的测试件。
[0112]
在为了孔隙率测量所生产的测试件的孔隙率评价中,孔隙率为18.4%。另外,抛磨表面的x-射线衍射的测量揭示陶瓷制品中的结晶相几乎是非晶的。
[0113]
将除了用于孔隙率测量的测试件之外的成形物体放入电炉中并热处理。具体地,在大气中于2.5小时内升温至1610℃并保持在1610℃持续50分钟,并然后停止通电以便在5.0小时内冷却至200℃以下。
[0114]
当通过icp-aes测量所得陶瓷制品的组成时,si的含量以sio2换算为90.3质量%,和tb的含量以tb2o3换算为9.7质量%。当进行gdms分析时,b的含量为0.4ppm。
[0115]
随后,为了分析陶瓷制品的晶体结构,切割并抛磨陶瓷制品。首先,用线锯切割未抛磨的陶瓷制品的两侧,使得保留中央部分以获得10mm
×
4mm
×
3mm的测试件。然后,在h方向上抛磨约1.5mm,并进一步进行镜面表面抛磨以获得10mm
×
4mm的观察表面。
[0116]
从观察表面的x-射线衍射揭示了陶瓷制品中的结晶相由方石英(sio2)和tb2si2o7相构成。
[0117]
此外,对观察表面进行sem-edx和ebsd的同时分析。分析100μm
×
100μm尺寸的视场中的十个不同位置以获得组成和结晶相的分布。作为结果,几乎所有的sio2部分是方石英,并且其比率为97[质量%]。剩余是非晶氧化硅,在所述非晶氧化硅未通过ebsd未检测到菊池图样。顺便提及,从通过sem-edx和ebsd分布获得的每个区域计算方石英和非晶氧化硅之间的比率,通常方石英的密度为2.3g/cc以及通常非晶氧化硅的密度为2.2g/cc。tb2si2o7相散布在整个视场中,并且由通过作图获得的面积计算平均等效圆直径为2.3μm。
[0118]
用于强度测试的测试件经历三点弯曲测试,并且强度为7.2[mpa]。
[0119]
评价陶瓷制品的si、tb、al、zr和b的含量、孔隙率和三点弯曲强度。结果示于表2中。对以下实施例和比较例也进行相同的评价。结果示于表2中。
[0120]
还有,在显示粉末重量的表1中,si、al和tb的含量以及吸收体中的pr和si分别通过换算为sio2、al2o3、tb4o7、pr6o
11
和sio的数值显示。另外,在显示陶瓷制品的评价结果的表2中,si、tb、pr、al和zr的含量分别通过换算为sio2、tb2o3、pr2o3、al2o3和zro2的数值显示。
[0121]
表2
[0122]
(实施例2)如实施例1中那样产生陶瓷制品,区别在于在进行加热处理之前使产生的成形物体浸渍含铝成分的液体。
[0123]
按以下方式制备所述含铝成分的液体。将仲丁醇铝溶解在2-丙醇(ipa)中,并向其添加乙酰乙酸乙酯(eacac)作为稳定剂。每种成分的摩尔比设定为仲丁醇铝:ipa:eacac=1.04:5:2。然后在室温下搅拌混合物约3小时以制备含铝成分的液体。
[0124]
在实施例2中,为测试而加工的w 40mm
×
d 4mm
×
h 3mm的成形物体被浸入所制备的含铝成分的液体中,在减压下脱气1分钟以便吸收液体至成形物体内部,并然后自然干燥1小时。
[0125]
然后,将吸收了含铝成分的液体的成形物体放入电炉中并加热。在大气中于2.5小时内升温至1610℃并在1610℃下保持50分钟,然后停止通电以便在5.0小时内冷却到200℃以下。
[0126]
抛磨所得陶瓷制品的表面,并通过x-射线衍射和ebsd分析晶体结构。作为结果,sio2是方石英,并且其比率为97质量%。另外,还观察到si2tb2o7相。
[0127]
(实施例3)实施例3与实施例2的不同之处在于使产生的成形物体吸收含铝成分的液体的步
骤以及加热处理的步骤交替重复两次。
[0128]
生产w 40mm
×
d 4mm
×
h 3mm的三个陶瓷制品用于三点弯曲强度测试,并生产一个陶瓷制品(其为与强度测试相同的陶瓷制品)用于组成和结构评价。
[0129]
抛磨所得陶瓷制品的表面,并通过x-射线衍射和ebsd分析晶体结构。作为结果,sio2是方石英,并且其比率为98质量%。另外,还观察到si2tb2o7相。
[0130]
(实施例4)如实施例1中那样生产陶瓷制品,区别在于在加热处理之前进行用含锆成分的液体的浸渍并且加热处理温度为1670℃。
[0131]
如下制备含锆成分的液体。制备85质量%的丁醇锆(丁醇锆(iv),(下文中称作zr(o-n-bu)4))溶解在1-丁醇中的溶液。将zr(o-n-bu)4的溶液溶解在2-丙醇(ipa)中,并向其添加乙酰乙酸乙酯(eacac)作为稳定剂。每种成分的摩尔比设定为zr(o-n-bu)4:ipa:eacac=1:15:2。然后在室温下搅拌混合物约3小时以制备含锆成分的液体。
[0132]
在实施例4中,为测试而加工的成形物体被浸入含锆成分的液体中,在减压下脱气1分钟以使液体浸渍到成形物体中,并然后自然干燥1小时。随后,将浸渍了含锆成分的液体的成形物体放入电炉中并加热。在大气中于2.5小时内升温至1670℃并在1670℃下保持50分钟,并且然后停止通电以便在1.5小时内冷却至200℃以下。
[0133]
随后,抛磨所得陶瓷制品的表面,并通过x-射线衍射和ebsd分析晶体结构。作为结果,sio2是方石英,并且其比率为98质量%。另外,还观察到si2tb2o7相。
[0134]
(实施例5)实施例5与实施例4的不同之处在于使成形物体浸渍含锆成分的液体的步骤以及加热处理的步骤交替重复两次。
[0135]
生产的陶瓷制品是用于三点弯曲强度测试的w 40mm
×
d 4mm
×
h 3mm的三个立方体,用于组成和结构评价的一个立方体(其为与强度测试所用相同的立方体)和用于耐磨测试的w 5mm
×
d 5mm
×
h 5mm的一个立方体。
[0136]
评价所生产的基于氧化硅的结构。作为结果,sio2是方石英,并且其比率为99质量%。另外,还观察到si2tb2o7相。
[0137]
(实施例6至9)通过以下方式生产实施例6至9的陶瓷制品:如实施例3中那样使浸渍含铝成分的液体的步骤以及加热处理的步骤交替重复两次,区别在于改变sio2粉末和tb4o7粉末的质量比。表1示出了这些实施例的粉末混合物中的质量比。
[0138]
(实施例10和11)如实施例1中那样生产实施例10和11的陶瓷制品,区别在于改变sio2粉末和tb4o7粉末的质量比。表1示出这些实施例的粉末混合物中的质量比。
[0139]
(实施例12至14)通过与实施例1中相同的步骤生产实施例12至14的陶瓷制品,区别在于使用表1中所示的质量比通过混合sio2粉末和tb4o7粉末制备的粉末以及改变加热处理温度。表2中示出加热处理温度。
[0140]
(实施例15和16)使用通过如下方式制备的粉末:以表1中所示的质量比率称量sio2粉末和tb4o7粉
末,并向其中添加微量的b2o3粉末,并将它们混合。通过与实施例1中相同的步骤生产实施例15和16的陶瓷制品,区别之处在于加热处理温度为1470℃。
[0141]
(实施例17)通过与实施例1中相同的步骤生产实施例17的陶瓷制品,区别之处在于使用通过将tb4o7粉末变为pr6o
11
粉末作为吸收体并以表1中所示的质量比率混合而制备的粉末。
[0142]
(实施例18)通过与实施例2中相同的步骤获得实施例18的陶瓷制品,区别之处在于使用另一含铝成分的液体。在表1中示出称量的sio2粉末和tb4o7粉末的质量比。
[0143]
如下使用氧化铝颗粒制备含铝成分的液体。将平均粒径为24nm的氧化铝颗粒(由kanto chemical co.,ltd.制造)、作为分散剂的丙烯酸2-羟乙酯和3-丙烯酰氧基丙基三甲氧基硅烷以及作为溶剂的甲乙酮混合,使得氧化铝在分散体中的浓度为70质量%,随后均匀搅拌以获得氧化铝颗粒的分散体。
[0144]
(实施例19)如实施例3中那样生产陶瓷颗粒,区别之处在于以表1中所示的质量比率使用sio粉末作为吸收体。所用sio粉末的平均粒径为5μm。
[0145]
生产w 40mm
×
d 4mm
×
h 3mm的三个基于氧化硅的结构用于三点弯曲强度测试,并且生产一个基于氧化硅的结构(其与用于强度测试的相同)用于组成和结构评价。
[0146]
抛磨所得基于氧化硅的结构的表面,并通过x-射线衍射和ebsd分析晶体结构。作为结果,sio2是方石英,并且其比率为98质量%。
[0147]
(实施例20和21)通过与实施例4中相同的步骤生产实施例20和21的陶瓷制品,区别在于以表1中所示的质量比率称量sio2粉末、al2o3粉末和作为吸收体的sio粉末,使用含锆成分的液体作为含金属成分的液体并且加热处理温度为1680℃。所用al2o3粉末的平均粒径为20μm。作为含锆成分的液体,使用乙酸锆水溶液,制备该溶液使得锆含量为30质量%。
[0148]
除实施例15之外的实施例的陶瓷制品中的b含量小于实施例15中的结构,并且机械强度高,例如为5.0mpa以上。另外,在1600℃下加热实施例15和16的陶瓷颗粒,实施例15的结构的拐角轻微变形。包括大量b的实施例15的耐热性低于其它实施例的耐热性。
[0149]
在实施例1至16和18的陶瓷制品中,观察到si2tb2o7相。然而,在实施例17的陶瓷制品中,观察到si2pr2o7相。因此,推断在结构中形成相分离的结构以改进机械强度。还认为这样的结构防止热膨胀系数的温度改变并且还具有缓和热应力的效果。
[0150]
在吸收含金属成分的液体之后进行加热处理的实施例2至9和18至21中,通过减少或消除裂纹以及al2o3相的形成获得更高的强度。
[0151]
当用显微镜观察陶瓷制品的表面时,在所有实施例的陶瓷制品中,在避开孔时测量的每个结构表面的ra为30μm以下。
[0152]
(比较例1)如表1中所示,如实施例1中那样生产比较例1的陶瓷制品,区别在于待与sio2粉末混合的tb4o7粉末的量增加至约27.0质量%的粉末以及待照射的激光束的描画间距被设定为170μm。获得的陶瓷制品具有45.0%的高孔隙率和1.2mpa的低三点弯曲强度。
[0153]
(比较例2)
如表1中所示,如实施例1中那样成型陶瓷制品时,区别在于成型中使用的粉末中tb4o7粉末的质量比率增加至约27.0质量%,tb2si2o7占成形物体的量提高。陶瓷制品中包括的si以氧化物换算计为80质量%以下。将获得的陶瓷制品放入20ml的浓度为20质量%的氢氧化钠水溶液中,使得比较例2的成形物体的量为0.1g,密封容器,并在100℃下的加热状态保持450分钟。作为结果,0.02g的成形物体保持未溶解。
[0154]
因此,认为比较例2的陶瓷制品在用作铸芯时在氢氧化钠中的溶解度不足。
[0155]
(比较例3)如实施例1中那样生产陶瓷制品,区别在于成型之后用于加热的温度为1440℃。如实施例1中那样评价陶瓷制品的晶体结构时,陶瓷制品主要是非晶氧化硅,和如实施例1中那样评价的三点弯曲强度为2.0mpa的低值。
[0156]
(比较例4)当如实施例1中那样生产陶瓷制品时,区别在于在成型之后加热温度为1740℃,拐角和边缘钝且变形。
[0157]
在比较例4中,推断由于在高于二氧化硅的熔点(1730℃)的1740℃下热处理成形物体,所以二氧化硅变为液相,并且不能维持形状。
[0158]
根据本发明,能够提供制造陶瓷制品的方法,其使用基于氧化硅的材料,同时利用直接成型系统的特性,该直接成型系统能够赋予成形物体复杂形状而且还能够改进成形物体的机械强度。另外,能够提供具有改进的机械强度同时维持形状精度的陶瓷制品。此外,本发明的陶瓷制品可用作金属铸造的芯,其中避免了因热膨胀所致的急剧形状改变。
[0159]
本发明不限于以上实施方案,并且可以在不偏离本发明的精神和范围的情况下进行各种改变和修改。因此,附上以下权利要求以使本发明的范围公开。
[0160]
本技术要求于2019年10月23日提交的日本专利申请第2019-193067号和于2020年10月16日提交的日本专利申请第2020-174681号的权益,通过引用将其整体并入本文。
再多了解一些
本文用于企业家、创业者技术爱好者查询,结果仅供参考。