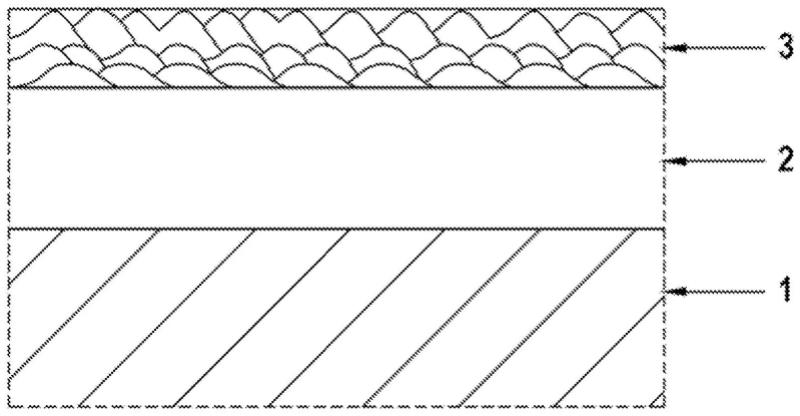
复合基材的涂覆方法
1.本发明涉及复合材料基材,特别是有机基质复合材料(omc)的湿表面处理领域。
2.目前,omc基材上的金属部件主要是通过制造粘合锻造部件来制造的。然而,这种方法在粘合和匹配部件方面存在限制和问题。
3.为了解决这些问题,文献介绍了通过不同的热喷涂方法(例如冷喷涂或悬浮等离子喷涂(sps))对沉积物(主要是金属)进行测试。事实上,热喷涂是金属航空部件上的一种常用方法,它可以产生涂层,最常见的是金属涂层。冷喷涂或悬浮等离子喷涂(sps)或空气等离子喷涂(aps)或火焰喷涂(高速氧燃料(hvof))喷涂等热喷涂方法的原理包括高速喷涂加热至高温(即,取决于方法,从180℃到颗粒熔化温度)的颗粒。
4.然而,为了不改变omcs的机械性能,omcs在加工过程中受到温度和机械暴露极限的限制。因此,最近在文献中发表的通过热喷涂在有机基质复合基材上进行沉积的尝试几乎总是导致基材的侵蚀,这可能会破坏表面线或极低附着性(即《1mpa)的沉积。事实上,在omc基材上使用这些方法主要导致由于热和侵蚀以及喷涂颗粒的动力学和热量输入而造成的损坏。omc第一层的这种损坏反映在增强纤维和非粘性涂层的暴露上。
5.发明人惊奇地意识到,通过使用在通过热喷涂沉积之前沉积的溶胶-凝胶底涂层,特别是有机/无机杂化溶胶-凝胶,可以保护有机基质复合材料。在通过热喷涂沉积后续涂层之前,该底涂层可被视为表面准备层或结合层。
6.因此,该底涂层具有三个功能:
[0007]-1保护omc基材免受喷涂颗粒的侵蚀;
[0008]-2增加涂层的附着性:
[0009]-与omc基材(界面1)的附着性,主要是由于化学相容性
[0010]-以及与通过热喷涂(界面2)产生的沉积物的附着性,主要通过表面粗糙度和可能与配方相关的化学相互作用产生的机械锚定;
[0011]-3由于适当的热膨胀系数,omc基材和通过热喷涂获得的上层之间的附着性提高。
[0012]
发明人还意识到,这种底涂层还可以保护其他类型的复合材料,例如陶瓷基复合材料(cmc)或金属基复合材料(mmc)。
[0013]
他们还意识到,在其他类型的涂层沉积(例如浸涂)期间,这种底涂层可以提高复合材料的附着性。
[0014]
因此,本发明涉及一种复合基材的涂覆方法,其特征在于包括以下步骤:
[0015]
a-通过在水性介质中混合制备溶胶-凝胶组合物,特别是在水或水/醇混合物中,更特别是酸化水,例如通过乙酸或硝酸酸化的水:
[0016]
1-至少一种式(i)的金属醇盐m(or1)
x
,其中
[0017]
r1是c
1-c4烷基,特别是丙基或丁基,
[0018]
m是选自由过渡金属、镧系元素、磷、镁、锡、锌、铝和锑组成的组中选择的金属,有利地选自cu、mn、sn、fe、mg、zn、al、p、sb、zr、ti、hf、ce、nb、v和ta组成的组中,更有利地选自zr、ti、al和sb组成的组中,甚至更有利地选自zr、ti和al组成的组中,更特别地,金属与后续涂层的金属相同,特别是通过喷涂沉积(参见下面的步骤c)),和
[0019]
x是代表金属化合价的整数,
[0020]
有利地,搅拌所需的时间以水解和浓缩有机-无机杂化网络,特别是几分钟至几小时,更特别是15分钟至5小时;
[0021]
2-在至少一种式(ii)r
3m
si(or2)
4-m
的有机烷氧基硅烷的存在下,其中
[0022]
r2代表c
1-c4烷基,特别是甲基、乙基或异丙基,
[0023]
m代表在1、2和3之间选择的整数,特别是1,
[0024]
并且每个r3彼此独立地代表选自聚二甲基硅氧烷、c
1-c
18
烷基、c
2-c4烯基、c
2-c4炔基、c
6-c
10
芳基、甲基丙烯基、甲基丙烯基(c
1-c
10
烷基)(例如甲基丙烯酰丙基)或甲基丙烯酰氧基(c
1-c
10
烷基)(例如甲基丙烯酰氧基丙基)、环氧烷基或环氧烷氧基烷基,其中烷基为直链、支链或环状c
1-c
10
烷基,烷氧基为直链或支链c
1-c
10
烷氧基(例如缩水甘油基和缩水甘油氧基(c
1-c
10
烷基),特别是缩水甘油氧基丙基)、c
2-c
10
卤代烷基(例如,3-氯丙基)、c
2-c
10
全卤代烷基(例如全氟丙基)、c
2-c
10
巯基烷基(例如巯基丙基)、c
2-c
10
氨基烷基(例如氨基丙基)、(c
2-c
10
氨基烷基)氨基(c
2-c
10
烷基)(例如3-[(2-氨基乙基)氨基]丙基)、二(c
2-c
10
亚烷基)三氨基(c
2-c
10
烷基)(例如3-[二亚乙基三氨基]丙基)、咪唑基-(c
2-c
10
烷基)和c
2-c
10
亚氨基烷基,特别是每个r3彼此独立地代表不可水解基团,选自环氧烷基或环氧烷氧基烷基,其中烷基是直链、支链或环状c
1-c
10
烷基并且烷氧基是直链或支链c
1-c
10
烷氧基(例如缩水甘油基和缩水甘油氧基(c
1-c
10
烷基),特别是缩水甘油氧基丙基)和c
2-c
10
氨基烷基(例如氨基丙基),
[0025]
有机烷氧基硅烷可以有利地预先与水性介质混合,特别是与水或水/醇混合物,更特别是酸化的水,同时搅拌水解和缩合有机-无机杂化网络所需的时间,
[0026]
3-并且存在任选的氧化物或金属颗粒,例如sio2、zro2、tio2、ag、al、ti及其混合物,特别是来自zro2和tio2;
[0027]
4-通过混合组合物,特别是几分钟至几小时,更特别是在搅拌下,以允许有机-无机杂化网络的缩合;
[0028]
b-将步骤a)中获得的溶胶-凝胶组合物在复合基材上沉积至少一个底涂层;
[0029]
c-以及在涂覆有在步骤b)中获得的底涂层的复合基材上沉积至少一个后续涂层,特别是通过喷涂。
[0030]
根据本发明的方法还可以包括步骤d),即回收在步骤c)中获得的涂覆的复合基材。
[0031]
在本发明的一个具体实施方式中,根据本发明的式(i)的金属醇盐在被带入根据本发明的式(ii)的有机烷氧基硅烷存在之前,预先与水性介质反应,反应时间特别为有机-无机杂化网络的缩合所需的时间。
[0032]
在本发明的含义内,“c
1-c4烷基”是指任何包含1-4个碳原子的直链或支链烷基。因此它可以是甲基、乙基、正丙基、异丙基、正丁基、仲丁基或叔丁基,优选甲基、乙基或异丙基,特别是乙基或甲基。
[0033]
在本发明的含义内,“c
1-c
18
烷基”是指任何包含1-18个碳原子的直链或支链烷基。因此它可以是甲基、乙基、正丙基、异丙基、正丁基、仲丁基、叔丁基、正戊基、正己基、庚基、辛基、壬基、癸基、十一烷基、十二烷基、十三烷基、十四烷基,十五烷基、十六烷基、十七烷基或十八烷基,优选甲基、乙基或异丙基,特别是乙基或甲基。
[0034]
在本发明的含义内,“c
1-c
10
烷基”是指任何包含1-10个碳原子的直链或支链烷基。因此它可以是甲基、乙基、正丙基、异丙基、正丁基、仲丁基、叔丁基、正戊基、正己基、庚基、辛基、壬基或癸基,优选甲基、乙基或丙基,特别是乙基或丙基。
[0035]
在本发明的含义内,“c
2-c4烯基”是指具有2至4个碳原子的直链或支链的任何烯基,特别是乙烯基、烯丙基、1-丙烯基、2-丙烯基和丁烯基。
[0036]
在本发明的含义内,“c
2-c4炔基”是指具有2至4个碳原子、直链或支链的任何炔基,特别是乙炔基、乙炔基或炔丙基。
[0037]
在本发明的含义内,“不可水解基团”是指不能与水反应产生-oh基团的任何基团。式ii的有机烷氧基硅烷中这种不可水解基团的存在使得可以在溶胶-凝胶材料(溶胶-凝胶底涂层)的si-o-m、si-o-si或m-o-m氧化物键网络内引入有机功能,该有机功能是非反应性(如烷基),或反应性和可聚合(甲基丙烯酰氧基、环氧树脂等),这将导致材料的某些部分完全有机化。因此得到的溶胶-凝胶材料(溶胶-凝胶底涂层)是所谓的“有机/无机杂化溶胶-凝胶”。因此,这些功能可以调节最终溶胶-凝胶材料(溶胶-凝胶底涂层)的机械和热性能(比简单的si-o-m、si-o-si或m-o-m基团更不易损和不易碎),还可以控制层的厚度。此外,确保溶胶-凝胶底涂层与复合树脂,特别是omc之间的化学键的非水解基团,也确保了与基材,特别是omc的附着性。
[0038]
在本发明的含义内,“c
6-c
10
芳基”是指一个或多个具有6至10个碳原子的芳环,可以连接或稠合。特别地,芳基可以是单环或双环基团,优选苯基或萘基。
[0039]
在本发明的含义内,术语“缩合有机-无机杂化网络”是指将每种金属醇盐聚合在一起,每种有机烷氧基硅烷一起聚合在一起和/或每种金属醇盐与每种有机烷氧基硅烷聚合在一起,即形成氧代桥,例如si-o-m或si-o-si或m-o-m。
[0040]
在一个有利的实施方式中,步骤a)中获得的溶胶-凝胶组合物中的si/m摩尔比介于0.1和0.5之间,有利地介于0.2和0.5之间,特别是0.3≤si/m≤0.5。
[0041]
在另一个有利的实施方式中,式(i)的金属醇盐选自异丙醇铝(iii)、丁醇钛(iv)和丙醇锆(iv)。
[0042]
在另一个有利的实施方式中,式(ii)的有机烷氧基硅烷选自3-氨基丙基三烷氧基硅烷(r2o)3si-(ch2)
3-nh2、3-(2-氨基乙基)氨基丙基三烷氧基硅烷(r2o)3si-(ch2)
3-nh-(ch2)
2-nh2,3-(三烷氧基甲硅烷基)丙基二亚乙基三胺(r2o)3si-(ch2)
3-nh-(ch2)
2-nh-(ch2)
2-nh2,3-氯丙基三烷氧基硅烷(r2o)3si-(ch2)3cl,3-巯基丙基三烷氧基硅烷(r2o)3si-(ch2)3sh,(3-环氧丙氧基丙基)三烷氧基硅烷,甲基丙烯酸(三烷氧基甲硅烷基)丙酯,氨基丙基三烷氧基硅烷;n-(3-三烷氧基甲硅烷基丙基)-4,5-二氢咪唑有机甲硅烷基唑及其混合物,r2具有与上述相同的含义。特别地,它选自(3-环氧丙氧基丙基)三甲氧基硅烷、甲基丙烯酸(三甲氧基甲硅烷基)丙酯、氨基丙基三乙氧基硅烷及其混合物。
[0043]
根据本发明的溶胶-凝胶组合物可以包含或不包含氧化物或金属颗粒。在另一个有利的实施方式中,在步骤a)中得到的溶胶-凝胶组合物的氧化物或金属颗粒的含量相对于组合物的总质量为0-50%,特别是相对于组合物的总质量为3-40%,有利地相对于组合物的总质量为5-30%,更有利地相对于组合物的总质量为5-15%。因此,有利地,溶胶-凝胶组合物包含氧化物或金属颗粒。
[0044]
颗粒可具有2nm至80μm,特别是2至100nm的尺寸,特别是直径,有利地它们是纳米
颗粒,更有利地具有10至60nm,更优选20至50nm的尺寸,特别是直径。这些颗粒的直径可以通过透射电子显微镜(tem)、x射线衍射和小角x射线散射或光散射来测量。
[0045]
有利地,金属醇盐和/或颗粒的金属m与在根据本发明的方法的步骤c)的后续涂层的沉积,特别是喷涂沉积中所含的那些具有相同的性质。
[0046]
根据本发明的基材是复合材料。它可以有利地是有机基复合材料(omc)、陶瓷基复合材料(cmc)或金属基复合材料(mmc)。特别地,基材是有机基质复合物。实际上,由于式ii的有机烷氧基硅烷中存在不可水解基团r3,导致溶胶-凝胶底涂层中存在某些部分的全有机材料,因此溶胶-凝胶层的附着性在该类型的基材上得到增强。
[0047]
有机基质复合基材是本领域技术人员熟知的。它们通常由通过有机基质致密的纤维增强物组成,例如热固性或热塑性树脂,特别是选自环氧树脂、聚酰亚胺和聚氨酯(热固性树脂)或聚醚醚酮(peek)树脂、聚醚酮酮(pekk)树脂、聚醚酰亚胺、聚碳酸酯、聚烯烃(聚乙烯或聚丙烯)、聚氯乙烯(pvc)和聚苯乙烯(热塑性树脂),或双马来酰亚胺或氰酸酯树脂,更特别是环氧树脂。它们主要是有机的。
[0048]
这些基材的制造是众所周知的,首先是制造一种可以呈不同形式的纤维结构,例如:-二维(2d)织物,-通过3d或多层编织获得的三维(3d)织物,-编织物,-针织物,-毛毡,-纱线或缆绳的单向(ud)网,或通过在不同方向叠加多个ud网并将ud网结合在一起(例如,通过缝合、通过化学粘合剂或通过针织)获得的多向(nd)网。还可以使用由织物、编织物、针织物、毛毡、网或其他的几个叠加层形成的纤维结构,所述层例如通过缝合、通过植入纱线或刚性元件或通过针织结合在一起。构成纤维结构的纤维尤其是耐火纤维,即通常是碳纤维、聚合物纤维或玻璃纤维,特别是碳纤维。
[0049]
在任选的成型和固结之后,纤维结构然后被致密化。纤维结构的致密化包括用构成基质的材料在其全部或部分体积中填充结构的孔隙。复合材料基质以本身已知的方式获得,例如通过遵循液体方法。液体方法包括用含有基质材料前体的液体树脂浸渍纤维结构。前体通常以任选稀释在溶剂中的聚合物形式存在。将纤维结构放置在模具中,该模具可以用具有最终模制部件形状的凹槽紧密闭合。接下来,关闭模具并将树脂注入整个凹槽中以浸渍纤维结构。前体向基质的转变,即其聚合,通过热处理进行,通常通过加热模具,在消除任何溶剂并使聚合物交联之后,预制件仍保持在模具中。基质是有机基质,例如热塑性或热固性树脂。有机基质可以特别从环氧树脂中获得,例如cytec公司以参考号pr 520出售的高性能环氧树脂。
[0050]
根据本发明的一个方面,纤维预制件可以通过树脂传递模塑(rtm)的公知方法来致密化。根据rtm方法,纤维预制件被放置在具有要制造的部件的外形的模具中。将热固性树脂注入到包括纤维预制件的模具的内部空间中。通常在注入树脂的位置与其排放孔之间的该内部空间中建立压力梯度,以控制和优化树脂对预制件的浸渍。
[0051]
纤维预制件也可以通过化学气相渗透(cvi)以已知方式致密化。将对应于要产生的基材的纤维增强物的纤维预制件放置在允许反应气相进入的烘箱中。选择烘箱中的压力和温度以及气相的组成,以允许气相在预制件的孔隙内扩散,从而通过沉积在与纤维接触的材料芯中形成基质,与化学气相沉积(cvd)方法所特有的压力和温度条件不同,化学气相沉积(cvd)方法只会在材料表面形成沉积物,而气相组分分解或几种组分之间的反应会产生固体材料。
[0052]
陶瓷基质复合基材是本领域技术人员众所周知的。它们通常由通常基于碳纤维或碳化硅纤维的纤维增强材料组成,有时是氧化铝或氧化铝纤维(al2o3),或称为莫来石(3al2o3,2sio2)的氧化铝和氧化硅(sio2)的混合晶体,由陶瓷基质致密化,例如基于氧化铝、莫来石、碳或碳化硅的基质。
[0053]
可以制造纤维结构并且可以如前面针对有机基质复合材料所指出的那样进行致密化。
[0054]
金属基质复合基材也是本领域技术人员熟知的。它们通常由通常基于陶瓷纤维(例如碳化硅)或金属纤维(例如不锈钢丝)的纤维增强物组成,由轻金属基质(例如基于铝、镁、锌或钛的基质)致密化。
[0055]
可以制造纤维结构并且可以如前面针对有机基质复合材料所指出的那样进行致密化。
[0056]
在本发明的一个有利实施方式中,复合基材是用于航空的部件,特别是发动机或机舱部件,更特别是反应器或涡轮发动机部件,有利地是风扇叶片、风扇外壳或出口导向叶片(ogv)。
[0057]
步骤b)的溶胶-凝胶底涂层通过本领域技术人员熟知的方法沉积,例如浸涂、喷涂、旋涂、刮涂(spatula)、拉膜机或刷涂,特别是通过浸涂或喷涂。
[0058]
在本发明的一个有利实施方式中,步骤b)中获得的溶胶-凝胶底涂层的厚度至少为5μm,特别是介于5μm和200μm之间(包括边界),更特别是介于10μm和200μm之间。该厚度取决于满足功能需要(防止侵蚀、霜冻、冰、雷电、火灾等)的步骤c)的后续涂层的沉积物的性质。
[0059]
沉积根据本发明的方法的后续涂层的步骤c)可以通过本领域技术人员熟知的方法来实施。因此它可以是浸涂或喷涂的步骤。有利地,它是热喷涂步骤,例如冷喷涂或悬浮等离子喷涂(sps)或空气等离子喷涂(aps)或火焰喷涂(例如高速氧燃料(hvof))喷涂。它也可以是压缩热处理。它可以有利地是冷喷雾,特别是在低压下。这些方法为本领域技术人员所熟知。
[0060]
有利地,步骤c)的后续涂层是金属层(纯金属或金属合金)、陶瓷、金属陶瓷或增强或未增强聚合物或混合物,有利地它是金属层(纯金属或金属合金),特别是钛、铝或铜或金属的混合物,例如锡和铜的混合物。在根据本发明的方法的步骤c)期间沉积,特别是喷涂的颗粒因此有利地是金属颗粒(纯金属或金属合金)、陶瓷颗粒、金属陶瓷颗粒、增强或未增强聚合物颗粒或混合物颗粒,特别是金属,例如钛、铝或铜或金属混合物,例如锡和铜的混合物。根据本发明的随后的金属陶瓷层可以是高度填充的金属陶瓷层(优选高于12重量%)和金属元素,例如co、ni、cu、al或这些元素的合金,例如wc12co、wc17co。根据本发明的后续金属涂层可以是ni、al或ti,或ni、co、al或ti基合金。例如,它可以是:
[0061]-nial、nicral或nicraly类型的ni基合金,特别是包含5至20%重量的al的ni基合金,例如ni5al、nicr-6al;
[0062]-铝合金,包含最多12%重量的si;
[0063]-基于镍或钴的金属合金(称为“抗性”),高度填充附加金属元素,例如comocrsi、conicraiy;
[0064]-弱合金化的钛合金,例如ta6v、ti6242或tiβ21s。
[0065]
此类金属或合金具有良好的机械性能,尤其是令人感兴趣的延展性,因此具有良好的减震性,这使得它们可以用作例如基材,特别是omc的保护性增强件,更特别是当基材是叶片(例如风扇或定子叶片)的前缘时。铝、铜和锌以及sn-zn和sn-cu合金和铝合金可用于形成防雷层。tio2和sio2可用于形成防冰层(防冰)。ti和tin可用于形成侵蚀保护层。
[0066]
后续涂层的厚度取决于其性质和功能(防止侵蚀、冰、雷、火等)。它可以在例如50μm和200μm之间变化,甚至可以达到几毫米,例如在0.5mm和20mm之间。
[0067]
在一个有利的实施方式中,根据本发明的方法包括在沉积溶胶-凝胶底涂层的步骤b)之前制备复合基材表面的在先步骤α),有利地通过脱脂然后喷砂或砂磨。该步骤提高了步骤b)的底涂层在基材上的附着性。因此,步骤b)在如此制备的复合基材上实施,即,在该步骤结束时获得。
[0068]
在另一个有利的实施方式中,根据本发明的方法包括热处理的中间步骤b1)。该中间步骤b1)位于步骤b)和c)之间,是在200℃的最高温度,特别是110℃的温度下对步骤b)中获得的涂覆的复合基材进行热处理的步骤,有利地持续2小时,特别是1小时,因此在步骤b1)中获得的基材上实施步骤c)。因此,该热处理步骤是可选的,并且如果需要的话,可以加速溶胶-凝胶底涂层的聚合。
[0069]
在另一个有利的实施方式中,根据本发明的方法包括在步骤c)之后或在任选的步骤d)之后的附加精加工步骤e)。这是机械或化学表面精加工步骤,可导致确保所需功能所需的最终表面状态。它尤其可以通过本领域技术人员熟知的方法进行,例如喷砂、喷丸、激光纹理化、压制、冲压、打磨(abrasion)(纸或磨石)、机械加工、化学蚀刻或水力喷射(water jet)。
[0070]
在一个实施方式的变体中,根据本发明的方法包括中间步骤b2)。位于步骤b)和c)之间或可选步骤b1)和c)之间的该中间步骤b2)是增加步骤b)或步骤b1)中获得的涂覆的复合基材表面粗糙度的步骤,因此步骤c)在步骤b2)中获得的基材上实施。该步骤b2)尤其可以通过本领域技术人员熟知的方法来实施,例如喷砂、激光纹理化、压制、冲压、打磨(纸或磨石)、机械加工、化学蚀刻或水力喷射。它改善了步骤c)的后续涂层在根据本发明的溶胶-凝胶底涂层上的附着性。因此,根据本发明的方法的这种变体包括如上所述的步骤a)、α)、b)、b1)、b2)、c)、d)和e),步骤α)、b1)、d)和e)是可选的。
[0071]
在实施方式的另一个变体中,将易熔颗粒,即可通过加热或化学处理去除颗粒印记的颗粒,例如聚苯乙烯颗粒,添加到步骤a)的溶胶-凝胶组合物中,并且根据本发明的方法包括中间步骤b3)。该中间步骤b3)位于步骤b)和c)之间,是热处理步骤(例如,聚苯乙烯颗粒在170℃下,特别是30分钟)或化学蚀刻,以去除步骤b)中获得的基材的孔隙率,步骤c)因此在步骤b3)中获得的基材上实施。因此,根据本发明的方法的该变体包括如上所述的步骤a)、α)、b)、b3)、c)、d)和e),步骤α)、d)和e)是可选的。
[0072]
在另一个实施方式的变体中,在步骤a)中获得的溶胶-凝胶组合物具有受控的凝胶状态,即有机-无机网络的最终聚合状态,使得该层有可能具有变形性,允许沉积的、特别是喷涂的颗粒被嵌入(因此聚合没有完成),并且在步骤c)中沉积的、特别是喷涂的颗粒渗透到溶胶-凝胶底涂层,从而形成嵌入底涂层的颗粒的浓度梯度。实际上,在该变体中,溶胶-凝胶底涂层将具有良好的在步骤c)期间在沉积的,特别是喷涂的颗粒的冲击下变形的能力。为此,特别选择步骤a)的溶胶-凝胶组合物的化学组成及其干燥参数,以允许沉积的,
特别是喷涂的颗粒渗透。特别地,可以具体选择化学前体(溶胶-凝胶组合物的式(i)的金属醇盐和式(ii)的有机烷氧基硅烷)、它们的比例和它们的可水解功能,以及组合物的粒度。底涂层的这种状态将允许:
[0073]-嵌入沉积的,特别是喷涂的颗粒,并获得热膨胀系数梯度;
[0074]-增加底涂层表面状态的粗糙度,从而提高沉积层,特别是喷涂层,更特别是热喷涂层的附着性;
[0075]-保护组合物基材免受沉积的,特别是喷涂的颗粒的侵蚀;
[0076]-通过在喷涂步骤期间沉积的,特别是喷涂的颗粒所输入的卡路里的贡献来控制溶胶-凝胶底涂层的聚合速率。
[0077]
该颗粒嵌入梯度还可以在使用部件时控制基材和最终涂层之间的热膨胀系数差异。
[0078]
在另一个实施方式的变体中,根据本发明的方法包括中间步骤b4)。该中间步骤位于步骤b)和c)之间或可选步骤b1)和步骤c)之间,是通过在水性介质中混合获得的溶胶-凝胶组合物的附加底涂层来涂覆在步骤b)或可选步骤b1)中获得的复合基材的步骤:
[0079]
1-至少一种式(i)的金属醇盐m(or1)
x
,其中
[0080]
r1代表c
1-c4烷基,
[0081]
m代表选自由过渡金属、镧系元素、磷、镁、锡、锌、铝和锑组成的组中的金属,
[0082]
x是代表金属化合价的整数,
[0083]
特别是如上文所定义的,
[0084]
2-在至少一种式(ii)r
3m
si(or2)
4-m
的有机烷氧基硅烷的存在下,其中
[0085]
r2代表c
1-c4烷基,
[0086]
m代表在1、2和3之间选择的整数,
[0087]
并且每个r3彼此独立地代表不可水解基团,选自聚二甲基硅氧烷、c
1-c
18
烷基、c
2-c4烯基、c
2-c4炔基、c
6-c
10
芳基、甲基丙烯基、甲基丙烯基(c
1-c
10
烷基)或甲基丙烯酰氧基(c
1-c
10
烷基)、环氧烷基或环氧烷氧基烷基,其中烷基为直链、支链或环状c
1-c
10
烷基,并且烷氧基为c
1-c
10
烷氧基、c
2-c
10
卤代烷基、c
2-c
10
全卤代烷基、c
2-c
10
巯基烷基、c
2-c
10
氨基烷基(c
2-c
10
氨基烷基)氨基(c
2-c
10
烷基)、二(c
2-c
10
亚烷基)三氨基(c
2-c
10
烷基)、咪唑基-(c
2-c
10
烷基)和c
2-c
10
亚氨基烷基,特别是如上文所定义的,
[0088]
有机烷氧基硅烷可以有利地预先与酸化的水混合,同时搅拌水解和缩合有机-无机杂化网络所需的时间,
[0089]
3-并且在任选的氧化物或金属颗粒的存在下,特别是如上文所定义的,
[0090]
4-通过混合组合物以使有机-无机杂化网络缩合,该方法有利地如上所述;
[0091]
并且所述溶胶-凝胶组合物具有受控的凝胶化状态,因此在步骤b4)中获得的基材上实施步骤c),使得在步骤c)期间沉积的,特别是喷涂的颗粒由此渗透到附加溶胶-凝胶底涂层中,从而产生嵌入附加底涂层的颗粒的浓度梯度。在该变体中,可选步骤b1)可以在步骤b)之后和/或在步骤b4)之后实施。因此,根据本发明的方法的该变体包括如上文所述的步骤a)、α)、b)、b1)、b4)、b1)c)、d)和e),步骤α)、b)、b1)、d)和e)是可选的。因此,第一底涂层(步骤b)主要确保与基材的化学粘附和保护基材免受侵蚀,而第二底涂层(步骤b4)可以获得热膨胀系数梯度和粘附沉积的(尤其是通过喷涂(步骤c))后续涂层所需的粗糙度。第
一和第二底涂层的溶胶-凝胶混合物的组成可以相同或不同;有利地,它们是不同的。
[0092]
本发明还涉及可通过根据本发明的方法(特别是如上所述)获得的涂覆的复合基材,特别是涂覆的有机基质复合材料。因此,它包括由至少一个溶胶-凝胶底涂层(特别是如上所述)和后续涂层(特别是通过喷涂,特别是通过热喷涂,特别是如上所述)构成的涂层。
[0093]
在本发明的一个有利实施方式中,涂覆的复合基材是用于航空的部件,特别是发动机或机舱部件,更特别是反应器或涡轮发动机部件,有利地是风扇叶片、风扇外壳或出口导向叶片(ogv)。
[0094]
有利地,溶胶-凝胶底涂层的厚度有利地至少为5μm,更有利地介于5μm和200μm之间,更特别地介于在10μm和200μm之间。该厚度取决于后续涂层的沉积物的性质,特别是热喷涂层,其满足功能需要(防止侵蚀、冰、雷、火等)。
[0095]
有利地,基材的后续涂层是金属层(纯金属或金属合金)、陶瓷、金属陶瓷或增强或未增强聚合物或其混合物,有利地它是金属层(纯金属或金属合金),特别是钛、铝或铜或金属的混合物,例如锡和铜的混合物。根据本发明的后续的金属陶瓷层可以是高度填充的金属陶瓷层(优选高于12重量%)和金属元素,例如co、ni、cu、al或这些元素的合金,例如wc12co、wc17co。根据本发明的后续金属涂层可以是ni、al或ti,或ni、co、al或ti基合金。例如,它可以是:
[0096]-nial、nicral或nicraly类型的ni基合金,特别是包含5至20%重量的al的ni基合金,例如ni5al、nicr-6al;
[0097]-铝合金,包含最多12%重量的si;
[0098]-基于镍或钴的金属合金(称为“抗性”),高度填充附加金属元素,例如comocrsi、conicraiy;
[0099]-弱合金化的钛合金,例如ta6v、ti6242或tiβ21s。
[0100]
此类金属或合金具有良好的机械性能,尤其是令人感兴趣的延展性,因此具有良好的减震性,这使得它们可以用作例如基材的保护性增强件,特别是当基材是叶片(例如风扇或定子叶片)的前缘时。铝、铜和锌以及sn-zn和sn-cu合金和铝合金可用于形成防雷层。tio2和sio2可用于形成防冰层。ti和tin可用于形成侵蚀保护层。
[0101]
后续涂层的厚度取决于其性质和功能(防止侵蚀、冰、雷、火等)。它可以在例如50μm和200μm之间变化,甚至可以达到几毫米,例如在0.5mm和20mm之间。
[0102]
本发明还涉及通过在水性介质中混合获得的溶胶-凝胶组合物的用途:
[0103]
1-至少一种式(i)的金属醇盐m(or1)
x
,其中
[0104]
r1代表c
1-c4烷基,
[0105]
m代表选自由过渡金属、镧系元素、磷、镁、锡、锌、铝和锑组成的组中的金属,
[0106]
x是代表金属化合价的整数,
[0107]
特别是如上文所定义的,
[0108]
2-在至少一种式(ii)r
3m
si(or2)
4-m
的有机烷氧基硅烷的存在下,其中
[0109]
r2代表c
1-c4烷基,
[0110]
m代表在1、2和3之间选择的整数,
[0111]
并且每个r3彼此独立地代表不可水解基团,选自聚二甲基硅氧烷、c
1-c
18
烷基、c
2-c4烯基、c
2-c4炔基、c
6-c
10
芳基、甲基丙烯基、甲基丙烯基(c
1-c
10
烷基)或甲基丙烯酰氧基
(c
1-c
10
烷基)、环氧烷基或环氧烷氧基烷基,其中烷基为直链、支链或环状c
1-c
10
烷基,并且烷氧基为c
1-c
10
烷氧基、c
2-c
10
卤代烷基、c
2-c
10
全卤代烷基、c
2-c
10
巯基烷基、c
2-c
10
氨基烷基(c
2-c
10
氨基烷基)氨基(c
2-c
10
烷基)、二(c
2-c
10
亚烷基)三氨基(c
2-c
10
烷基)、咪唑基-(c
2-c
10
烷基)和c
2-c
10
亚氨基烷基,
[0112]
特别是如上文所定义的
[0113]
有机烷氧基硅烷可以有利地预先与酸化的水混合,同时搅拌水解和缩合有机-无机杂化网络所需的时间,
[0114]
3-并且在任选氧化物或金属颗粒的存在下,特别是如上文所定义的,
[0115]
4-通过混合组合物以使有机-无机杂化网络缩合,该方法有利地如上所述;
[0116]
作为复合基材,特别是有机基质复合材料的底涂层,以在沉积后续涂层期间,特别是通过喷涂,更特别是通过热喷涂,保护所述基材和/或改善所述基材上的附着性。特别地,溶胶-凝胶组合物、复合基材和/或后续涂层如上所述。
[0117]
因此,其用途可以是改善沉积过程中后续涂层在基材上的附着性和/或使用过程中基材与后续涂层之间的附着性。
[0118]
通过阅读以非限制性指示方式给出的以下附图和实施例的描述,将更好地理解本发明。
附图说明
[0119]
图1是通过本发明的方法获得涂覆有溶胶-凝胶底涂层(2)和后续涂层(3)的复合基材(1)的竖直截面的代表性图。
[0120]
图2是复合基材(1)的竖直截面的代表性图,该复合基材(1)涂覆有具有受控凝胶状态的溶胶-凝胶底涂层,包含颗粒梯度(4),并具有通过本发明方法变体获得的后续涂层(3)。
[0121]
实施例1:热喷涂沉积前的si-zr溶胶-凝胶底涂层和zro2颗粒
[0122]
在磁力搅拌下将以下化合物依次加入烧杯中:70%质量的丙醇锆(iv)溶液和冰醋酸,使得zr/h
=2。均化后,边搅拌边加入蒸馏水,使zr/h2o=15。
[0123]
将溶液保持搅拌约1小时,直到获得均匀透明的溶液。
[0124]
在搅拌下向该溶液中加入(3-环氧丙氧基丙基)三甲氧基硅烷,使得si/zr=0.3。保持搅拌约1小时,直到获得均匀透明的溶液。
[0125]
在搅拌和/或超声下将5%质量的zro2颗粒(平均直径50nm)添加到该混合物中。
[0126]
然后制备有机基复合材料(omc)基材,所述omc由碳纤维增强的环氧基复合材料制成,根据本领域技术人员已知的方法,例如磨沙或喷砂,然后依次清洗去除表面上的灰尘。
[0127]
然后通过喷涂或浸涂将底涂层的配方沉积在omc基材上以完全覆盖表面,然后在几分钟至一小时的时间内将如此涂覆的基材置于110
°
的烘箱中1小时。
[0128]
然后用低压冷喷涂法获得的金属铝层涂覆所得基材。
[0129]
实施例2:热喷涂沉积前的si-ti溶胶-凝胶底涂层和tio2颗粒
[0130]
在磁力搅拌下将以下化合物依次加入烧杯中:丁醇钛(iv)和冰醋酸,使得ti/h
=2,然后在搅拌下加入蒸馏水,使得ti/h2o=8。
[0131]
将溶液保持搅拌约30分钟,然后在搅拌下加入甲基丙烯酸3-(三甲氧基甲硅烷基)
丙酯(γ-mps)和氨基丙基三乙氧基硅烷(aptes),使得si/ti=0.2,γ-mps/aptes=3。保持搅拌约1小时。
[0132]
在搅拌和/或超声下将5%质量的tio2颗粒(平均直径20nm)添加到该混合物中。
[0133]
然后制备有机基复合材料(omc)基材,所述omc由碳纤维增强的环氧基复合材料制成,根据本领域技术人员已知的方法,例如磨沙或喷砂,然后依次清洗去除表面上的灰尘。
[0134]
然后通过喷涂或浸涂将底涂层的配方沉积在omc基材上以完全覆盖表面,然后在几分钟至一小时的时间内将如此涂覆的基材置于110
°
的烘箱中1小时。
[0135]
然后用低压冷喷涂法获得的金属钛层涂覆所得基材。
[0136]
实施例3:喷铝前的si-al底涂层
[0137]
将异丙醇铝(iii)前体与蒸馏水混合(使得h2o/al摩尔比=10)。将混合物在80℃搅拌保持1小时。
[0138]
通过添加浓硝酸(68%)将ph值调节至3,以形成氧化物网络。在80℃下剧烈搅拌1小时后,得到澄清、蓝色和稳定的溶胶。使溶液恢复至环境温度并向其中加入(3-环氧丙氧基丙基)三甲氧基硅烷,使得si/al=0.3。将溶液保持搅拌2小时。
[0139]
然后制备有机基复合材料(omc)基材,所述omc由碳纤维增强的环氧基复合材料制成,根据本领域技术人员已知的方法,例如磨沙或喷砂,然后依次清洗去除表面上的灰尘。
[0140]
然后通过喷涂或浸涂将底涂层的配方沉积在omc基材上以完全覆盖表面,然后在几分钟至一小时的时间内将如此涂覆的基材置于110
°
的烘箱中1小时。
[0141]
然后用低压冷喷涂法获得的金属铝层涂覆所得基材。
[0142]
实施例4:热喷涂沉积前的si-ti溶胶-凝胶底涂层和可熔聚苯乙烯颗粒
[0143]
在磁力搅拌下将以下化合物依次加入烧杯中:丁醇钛(iv)和冰醋酸,使得ti/h
=2,然后在搅拌下加入蒸馏水,使得ti/h2o=8。
[0144]
将溶液保持搅拌约30分钟,然后在搅拌下加入(3-环氧丙氧基丙基)三甲氧基硅烷(gptms)和氨基丙基三乙氧基硅烷(aptes),使得si/ti=0.2,gptms/aptes=5。保持搅拌约2小时。
[0145]
在搅拌和/或超声下将5%质量的聚苯乙烯颗粒(平均直径5nm)添加到混合物中。
[0146]
然后制备有机基复合材料(omc)基材,所述omc由碳纤维增强的环氧基复合材料制成,根据本领域技术人员已知的方法,例如磨沙或喷砂,然后依次清洗去除表面上的灰尘。
[0147]
然后通过喷涂或浸涂将底涂层的配方沉积在omc基材上以完全覆盖表面,然后在几分钟到一小时内,将如此涂覆的基材在110℃的烘箱中放置1小时,然后在170℃下保持30分钟,以去除表面上聚苯乙烯颗粒的孔隙。
[0148]
然后用低压冷喷涂法获得的金属钛层涂覆所得基材。
[0149]
实施例5:在通过热喷涂铝层沉积之前,双si-ti溶胶-凝胶底涂层和tio2颗粒,然后是si-al底涂层
[0150]
第一底涂层:
[0151]
在磁力搅拌下将以下化合物依次加入烧杯中:丁醇钛(iv)和冰醋酸,使得ti/h
=2,然后在搅拌下加入蒸馏水,使得ti/h2o=8。
[0152]
将溶液保持搅拌约30分钟,然后在搅拌下加入甲基丙烯酸3-(三甲氧基甲硅烷基)丙酯(γ-mps)和氨基丙基三乙氧基硅烷(aptes),使得si/ti=0.2,γ-mps/aptes=3。保持
搅拌约1小时。
[0153]
在搅拌和/或超声下将5%质量的tio2颗粒(平均直径20nm)添加到该混合物中。
[0154]
然后制备有机基复合材料(omc)基材,所述omc由碳纤维增强的环氧基复合材料制成,根据本领域技术人员已知的方法,例如磨沙或喷砂,然后依次清洗去除表面上的灰尘。
[0155]
然后通过喷涂或浸涂将底涂层的配方沉积在omc基材上以完全覆盖表面,然后在几分钟至一小时的时间内将如此涂覆的基材置于80
°
的烘箱中45分钟。
[0156]
第二底涂层:
[0157]
此外,用蒸馏水制备异丙醇铝(iii)混合物(使得h2o/al摩尔比=10)。将混合物在80℃搅拌保持1小时。
[0158]
通过添加浓硝酸(68%)将ph值调节至3,以形成氧化物网络。在80℃下剧烈搅拌1小时后,得到澄清、蓝色和稳定的溶胶。使溶液恢复至环境温度并向其中加入(3-环氧丙氧基丙基)三甲氧基硅烷,使得si/al=0.3。将溶液保持搅拌2小时。
[0159]
然后通过喷涂将该底涂层的配方沉积在覆盖有前述底涂层的omc基材上,以完全覆盖表面,然后将如此涂覆的基材置于110℃的烘箱中1小时。
[0160]
然后用低压冷喷涂法获得的金属铝层涂覆所得基材。
再多了解一些
本文用于企业家、创业者技术爱好者查询,结果仅供参考。