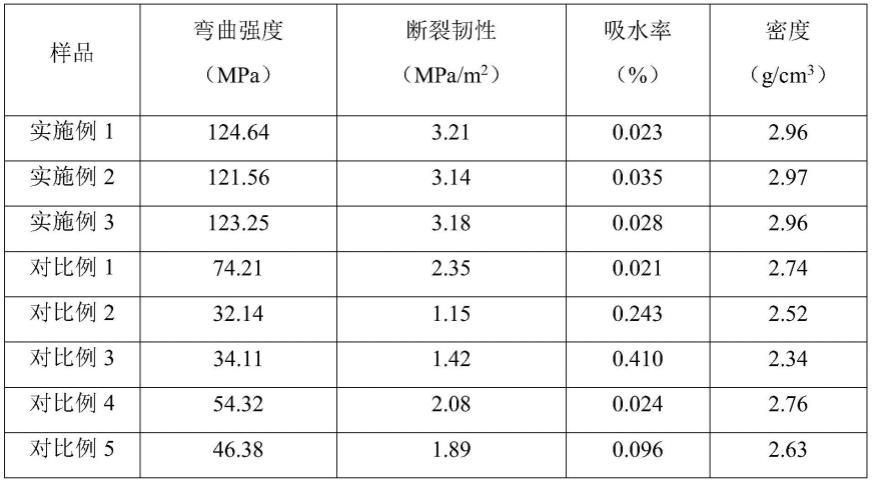
1.本发明属于复合陶瓷板技术领域,具体涉及一种基于两步式球磨制备高强度纤维复合陶瓷板的方法及获得的复合陶瓷板。
背景技术:
2.建筑陶瓷板是一种源自矿物资源、可灵活应用在家装领域和安全防护领域的重要材料。建筑陶瓷板的潜在市场极其广阔。据报道2020年的建筑陶瓷板国际市场估值高达3000亿元。当前我国对建筑陶瓷板的绿色化生产提出了更高、更严格的要求,旨在降低生产过程中的烟气排放、能源损耗,提升矿物材料的资源利用率。鉴于此,陶瓷板轻薄化因可节约原材料用量、减少生产排放和降低生产能耗,而逐渐成为建筑陶瓷板未来发展的重要出路。但是,随着普通建筑陶瓷板厚度的降低,陶瓷板尤其是大规格陶瓷板生坯的力学强度骤降,致使其成型困难,难以满足日常的家装、安全防护要求。因此,如何提升陶瓷板的力学强度,进而对建筑陶瓷板进行减薄,成为该研究领域的重要技术难点。
3.作为陶瓷板轻薄化的概念产品,高强度纤维复合陶瓷板是纤维增强相和陶瓷基体复合的产物。高强度纤维复合陶瓷板已在国外实现了产业化利用,但国内因技术不足难以实现产业化,具体存在以下两点技术壁垒:(1)引入的增强相在高温下易和成分复杂的基体相发生不可控性的界面反应,破坏增强体的力学结构,致使材料变脆,大大降低其力学性能;(2)引入的纤维等增强相难以通过传统球磨工艺在基体中均匀分散,团聚的纤维体也会致使复合陶瓷板内部出现不均匀的力学缺陷,降低材料的力学性能和使用安全性。因此,高强度纤维复合陶瓷板具有较大的发展潜力,有望替代当今的主流产品,但由于存在较大的技术壁垒而难以取得较好的技术突破,针对其进行制备工艺的优化迫在眉睫。
技术实现要素:
4.基于以上背景技术,本发明通过优化球磨、快速烧结工艺,开发出一种基于两步式球磨制备高强度纤维复合陶瓷板的方法及获得的复合陶瓷板,可以实现纤维在基体中的均匀分散,降低增强体在高温下的结构性破坏,制备出的复合型薄型陶瓷板空位缺陷少,具有较高的力学强度。该方法工艺简单,选用原料成本低廉,产物力学性能优异,有望打破国外的技术壁垒,为建筑陶瓷大板的薄型化提供重要技术依据,具有极大的发展潜力和市场应用前景,应用于建筑陶瓷、安全防护材料等领域。
5.第一方面,本发明提供一种基于两步式球磨制备高强度纤维复合陶瓷板的方法,包括以下步骤:将化学成分质量比为al2o3:sio2:cao:mgo:tio2:na2o:k2o:la2o3:fe2o3=(40-45):(35-40):(5-10):(5-10):(1-6):(1-5):(2-6):(0.2-0.5):(0.5-1.5)的陶瓷粉料置于三辊研磨机中进行研磨,过筛、干燥,得到粉状固体;将氧化铝纤维浸润到包含聚丙烯酰胺和三聚磷酸钠的混合溶液中进行预分散,氧
化铝纤维界面的负电子电位和电子排布被调控使得团聚状的氧化铝纤维自发解散,收集解散的氧化铝纤维并将其烘干,之后进行第一次球磨,得到经第一次球磨分散的氧化铝纤维;将所述粉状固体与经第一次球磨分散的氧化铝纤维交替布料并放置于球磨罐中进行第二次球磨,过筛、烘干,得到纤维/粉体混合物;将所述纤维/粉体混合物成型为坯体,将坯体干燥并烧结,得到所述高强度纤维复合陶瓷板。
6.较佳地,所述氧化铝纤维的长度为200-210μm,直径为3-4μm,长径比为50-70。
7.较佳地,包含聚丙烯酰胺和三聚磷酸钠的混合溶液中,聚丙烯酰胺:三聚磷酸钠:氨水的体积比=(30-40):(20-30):(40-50);优选地,所述混合溶液的ph为7.5-8.0;更优选地,氧化铝纤维与混合溶液的用量比为1g:50-100ml。
8.较佳地,三辊研磨机研磨后的粉状固体粒径为40-60μm。
9.较佳地,所述第一次球磨采用酒精和粒径1-3mm的球石作为柔性研磨助剂以促进自发解散的氧化铝纤维柔性解离理为单根纤维,其中,氧化铝纤维:球石:酒精的质量比=(12-15):(20-22):(18-20)。
10.较佳地,所述第二次球磨以水为球磨介质,粉状固体:氧化铝纤维:球石:水的质量比=(10-15):(2-4):(18-20):(20-30)。
11.较佳地,交替布料时,先称取质量分数5-10%的粉状固体平铺在球磨罐底部,然后称取质量分数5-10%的第一次球磨分散的氧化铝纤维平铺在粉状固体表面,交替重复上述过程,直至将粉状固体和氧化铝纤维全部送入球磨罐中。
12.较佳地,所述纤维/粉体混合物的含水率为5-10wt%。
13.较佳地,所述烧成的最高烧成温度为1200-1250℃,烧成周期为20-30min,最高温度的保温时间为10-12min。
14.第二方面,本发明提供了一种根据上述方法制备得到的高强度纤维复合陶瓷板。所述复合陶瓷板的综合力学性能优异。一些技术方案中,弯曲强度为120-135mpa,断裂韧性为3.15-3.25mpa/m2。
15.有益效果当前国内无法制备出高强度纤维复合薄型陶瓷板的技术难点主要体现在:(1)纤维在球磨过程中结构损坏,降低力学强度;(2)纤维在基体中部分团聚、分散不均匀,内部缺陷较多;(3)高温下纤维和基体发生严重界面反应,致使双相脆化,力学强度降低。本发明基于传统薄型陶瓷板生产方案,创新性地提出了一种基于两步式球磨工艺制备高强度纤维复合陶瓷板的方法:一方面,通过引入低成本助研剂,开创出两步式球磨工艺,技术操作简单,基于现有生产体系的工艺替代性较高,解决了短切纤维难以在陶瓷坯体中均匀分布的技术难题,具有较大的产业化应用潜力;另一方面,通过开发高温、快烧的烧结制度,合理提升窑炉烧结温度至1200-1250℃,降低烧成周期至20-30min,避免因长时间烧结致使纤维和基体发生严重界面反应,从而保证了复合型薄型陶瓷板的力学强度。
附图说明
16.图1为实施例1中氧化铝短切纤维原料的扫描电镜测试图;图2为实施例1中纤维/粉体混合物的扫描电镜测试图;
图3为实施例2中纤维复合陶瓷板的xrd测试图;mullite指的是莫来石,corundum指的是刚玉,quartz指的是石英,alumina fiber指的是氧化铝纤维;图4为实施例3中纤维复合陶瓷板断面的扫描电镜测试图;图5为对比例1中纤维复合薄型陶瓷板断面的扫描电镜测试图;图6为对比例2中纤维复合陶瓷板断面的扫描电镜测试图;图7为对比例3中纤维/粉体混合物的扫描电镜测试图;图8为对比例5中纤维经第一次球磨后的光学显微镜测试图;图9为对比例6中纤维和基体经第二次球磨混合后的扫描电镜测试图。
具体实施方式
17.通过具体实施方式进一步说明本发明,应理解,下述实施方式仅用于说明本发明,而非限制本发明。
18.以下示例性说明本发明所述的基于两步式球磨制备高强度纤维复合陶瓷板的方法。
19.按照化学成分质量比al2o3:sio2:cao:mgo:tio2:na2o:k2o:la2o3:fe2o3=(40-45):(35-40):(5-10):(5-10):(1-6):(1-5):(2-6):(0.2-0.5):(0.5-1.5)称取煅烧氧化铝、高岭土、黑滑石、钠长石、高钙熔块、内蒙白云母、韶关球土和膨润土等矿物原料,均匀混合得到混合物。混合物的烧失可为5.0-10.0wt%。将混合物置于三辊研磨机中进行研磨,设置研磨时间为2-3h,研磨转速为50-80r/min。随后,将经研磨的混合物粉体过250-300目筛网,收集筛下料并在烘箱中于150-180℃下干燥12-18h,得到粉状固体。粉状固体的粒径优选为48-58μm。
20.粉状固体作为陶瓷板的基体相。本发明依据特定析晶路线设计基体相组成,选用煅烧氧化铝、高岭土等资源丰富、廉价的原料作为基体相的矿物组成。与此同时,如实施例3及附图4可知,通过合理设置配方中al2o3、sio2等组分,诱导内部在高温下生成更多熔融玻璃态物质,进而在烧成过程中原位析出纤维状莫来石等增强相,协同al2o3纤维、弥散相增强颗粒共同减缓内部微裂纹尖端的应力集中,延缓内部裂纹扩散速率,提升材料的综合力学性能。如实施例3、对比例1及对应强度测试数据可知,对比例1样品的弯曲强度为74.21mpa,而实施例3样品的弯曲强度为131.25mpa,力学性能提升幅度高达76.87%。
21.其中,本发明选择高钙熔块作为配方中硅相的重要原料,其仅在500-700℃下即可转化为纳米级熔融玻璃态物质,并可均匀分散至坯体中微孔洞结构中并充当液相传质载体,协同推动内部物质传质、坯体致密化进程,进而大大降低烧结温度。与此同时,控制硅相、铝相等原料比例在前述特定范围内,可以使得al2o3、sio2等组分以单一微纳米级液态熔融玻璃态的形式存在,否则sio2会和al2o3等组分以化合态形式存在,大大影响制备薄型陶瓷板的力学性能。控制基体配方中al、si相组成,调控玻璃相生成温度区间,可以促进基体相提前致密,从而达到优化复合陶瓷板力学性能的目的。
22.另外,本发明根据原料硬度、粒度等物理性质,选用三辊研磨机对原料矿物进行粉碎处理,相较于传统原料处理工艺而言,在保证原料质量、细度的同时,可以精简球磨混料、喷雾造粒等传统工艺步骤,大大降低生产成本和周期。此外,传统原料球磨工艺效率较低,原料粒径仅可以降低到100-200μm,而三辊研磨机可以根据不同原料的加工需求,将原料粒
径迅速降低到40-60μm。较小的原料粒径有助于提升第二次球磨时纤维和基体的混合效率,颗粒的高表面活化能也可促进烧结过程中的致密化进程,烧成温度可降低120-180℃,生产能耗降低5-10%。
23.本发明采用“化学-物理”协同的方式进行纤维的分散。首先,将氧化铝纤维浸润到ph为7.5-8.0的聚丙烯酰胺混合溶液中。在一些实施方式中,氧化铝纤维与聚丙烯酰胺混合溶液的用量比可以为1g:50-100ml;借助超声波分散仪将其在60-80℃下分散1-2h,设置超声频率为10-12khz。随后,把经收集、烘干后的氧化铝纤维移至球磨罐中进行第一次球磨,设置转速为30-50r/min,球磨时间为5-8min,球磨原料的质量比为氧化铝纤维:球石:酒精=(12-15):(20-22):(18-20),选用球石的粒径为1-3mm。最后,将球磨后的混合物过80目筛网,收集筛下料、烘干得到经第一次球磨分散的氧化铝纤维。其中,选用的氧化铝纤维长度范围为200-210μm,纤维直径范围为3-4μm,纤维长径比为50-70;聚丙烯酰胺混合溶液的各组分体积比为聚丙烯酰胺:三聚磷酸钠:氨水=(30-40):(20-30):(40-50)。
24.选用聚丙烯酰胺、三聚磷酸钠混合溶液作为氧化铝纤维化学预分散介质,无毒无害,廉价易得,而且聚丙烯酰胺含有丰富的氨基和羰基,在ph=7.5-8.0的微碱性环境下可以加速其水解,附着在氧化铝纤维界面附着点位,调控界面的负电子电位,从而使团聚状纤维出现自发解散。同时,三聚磷酸钠可以调控氧化铝纤维界面的电子排布,协同聚丙烯酰胺对纤维进行化学分散,不仅对纤维无损害,而且可高效分散呈团聚状的氧化铝纤维。
25.本发明在第一次球磨工艺中引入成本低廉的酒精、小粒径球石颗粒作为柔性研磨助剂,可防止纤维因过度磨损而发生不可控式破坏。同时,酒精易挥发,不会因氢键作用致使纤维发生团聚,可有效保障纤维增强体的力学结构及增强效果。
26.本发明将纤维液相分散工艺和第一次球磨工艺相结合,先将纤维进行液相分散,使原本呈团聚状态的纤维絮柔性解理为单根纤维。通过设置第一次球磨时间、转速等保护纤维的力学结构,同时进一步调控纤维分散性、长径比等关键参数。纤维增强体的长径比、分散性是否合适直接决定高强度纤维复合陶瓷板的力学性能,适配的纤维增强体长径比、分散性有助于纤维在基体中发挥处裂纹偏转、“断裂-拔出”等强韧化机理,提升复合薄型陶瓷板的综合力学性能,根据不同纤维结构特点调整关键生产参数,具有很强的工艺适应性。本发明公开的技术方案,解决了短切纤维难以充分解理并在陶瓷坯体中均匀分布的技术难题,具有较大的产业化应用潜力。
27.在一些实施方式中,可以控制所述第一次球磨后的氧化铝纤维的长径比为40-60。
28.氧化铝纤维具有优异的力学强度及弹性模量,不会因微小磨损作用而破坏力学结构并引发断裂,因此可以通过对纤维点位长时间施加磨损作用,实现纤维长径比调控。然而,低弹性模量纤维,如木质纤维、棉纤维等,则难以达到前述有益效果。氧化铝纤维种类较多,不同的纤维晶相组成、力学强度决定了不同的球磨工艺参数。在一些实施例中,可以选择成分质量分数组成为al2o3:sio2:y2o3:b2o3:zro2=(65-95):(5-35):(0-1):(0-1):(0-1)的氧化铝纤维。在保护纤维力学结构的同时,具有很强的工艺适应性。
29.接着,将上述粉状固体与经第一次球磨后得到的氧化铝纤维先后依次交替平铺在球磨罐底部,直至将粉状固体、氧化铝纤维全部送至球磨罐中,之后进行第二次球磨。在一些实施方式中,可以控制每一层粉状固体的质量为各层粉状固体总质量的5-10%,每一层氧化铝纤维的质量为各层氧化铝纤维总质量的5-10%,也即控制粉状固体与氧化铝纤维最
终的层数范围均为10-20层。
30.所述第二次球磨过程中控制质量比为粉状固体:氧化铝纤维:球石:水=(10-15):(2-4):(18-20):(20-30);设置球磨转速为60-80r/min,球磨时间为1-3min。将经第二次球磨混散的混合物过60目筛网,收集筛下料并将其烘干,得到分散均匀的纤维/粉体混合物。筛下料经烘干处理后,控制其含水率为5-10wt%。在一些实施方式中,可以控制所述纤维/粉体混合物的平均粒径为20-100μm,第二次球磨后纤维的长径比为30-50。
31.通过调控第二次球磨的时间和转速,可以保障纤维和基体的混合效率,低成本地实现纤维于基体相中的均匀分布,同时也可以避免长时间球磨对纤维力学机构造成损伤,保障纤维在陶瓷板中的强韧化效果。传统球磨工艺为湿法球磨,得到的浆料经过筛、烘干和过筛才可获得陶瓷粉体,工艺复杂,且易使原本分散均匀的纤维和基体发生重排及团聚,因此不适用于本发明。本工艺优化传统湿法球磨工艺,严格控制含水率以便于混合原料直接参与成型工序,可规避传统生产工艺不足,步骤简单易操作。
[0032]“纤维-基体交替布料”的高效布料模式可以在布料阶段即实现纤维和基体粉料的预混散,大大提升了第二次球磨混散的效率,降低20-30%的生产周期,避免因长时间磨损作用而致使纤维的力学结构受到损伤。此外,该布料工艺简单易行,产业化的可替代性较强,具有很强的应用潜力。
[0033]
将上述纤维/粉体混合物平铺在成型模具中,借助千吨级压力成型机将其成型为纤维复合陶瓷板坯体,将坯体在80-120℃下干燥10-20min,随后送至辊道窑烧结,即可得到一种基于两步式球磨制备的高强度纤维复合陶瓷板。其中,成型压力为60-80mpa,最大压力加压时间为20-30s。纤维复合陶瓷板坯体的长、宽、高分别为850-950mm、1750-1850mm、2.5-3.5mm。辊道窑烧成温度为1200-1250℃,烧成周期为20-30min,最高温度保温时间为10-12min。通过合理提升窑炉烧结温度至1200-1250℃,降低烧成周期至20-30min,可以避免因长时间烧结致使纤维和基体发生严重界面反应,从而保证了复合型薄型陶瓷板的力学强度。界面反应通常发生于高温阶段烧结,而本发明设置的烧结温度低、高温段时间短,且通过对比例中sem图可以看出纤维界面无明显烧蚀形貌。基体相配方比例、基体颗粒粒径和特定种类纤维的选择协同降低了坯体的致密化温度,实现了低温快烧。
[0034]
如实施例3及附图4所示,相较于传统烧结制度而言,本发明中开发出的高温段快烧烧结制度不仅可以有效保护纤维的力学结构,而且可减少10-20%生产能源损耗,降低生产成本。基于此,对比例4中普通建筑陶瓷大板的弯曲强度为54.32mpa,而复合型薄型陶瓷板的最大弯曲强度为131.25mpa,强度提升幅度高达141.63%。
[0035]
在成型阶段,本发明采用了“精确混料-直接成型”一体化工艺,借助烘箱等简易设备,控制纤维/基体混合物筛下料的含水率在5-10wt%,而后直接用于压制成型。相较于传统成型工艺而言,“精确混料-直接成型”一体化工艺不仅可以精简造粒、球磨、过筛等复杂工序,而且可以避免因重复造粒而致使纤维的二次团聚,进一步保证纤维在基体中的分散性,减少内部力学缺陷,提高薄型陶瓷板的综合力学性能。
[0036]
在实施例中使用的聚丙烯酰胺的分子量为2000-4000。
[0037]
实施例1基于两步式球磨制备高强度纤维复合陶瓷板的方法包括以下步骤:
[0038]
步骤一:按照化学成分质量比al2o3:sio2:cao:mgo:tio2:na2o:k2o:la2o3:fe2o3=
43:36:6:5:2:3:4:0.2:0.8称取煅烧氧化铝、高岭土、黑滑石、钠长石、高钙熔块、内蒙白云母、韶关球土和膨润土,均匀混合,得到固体混合物a。固体混合物a的烧失为5.0wt%。将固体混合物a置于三辊研磨机中,设置研磨时间为3h、研磨转速为80r/min。随后将经研磨的混合物粉体过250目筛网,收集筛下料并在烘箱中于180℃下干燥18h,得到粉状固体b。
[0039]
步骤二:将氧化铝纤维浸润到聚丙烯酰胺混合溶液中,氧化铝纤维与聚丙烯酰胺混合溶液的用量比为1g:50ml。聚丙烯酰胺混合溶液ph为7.5,组分体积比为聚丙烯酰胺:三聚磷酸钠:氨水=30:20:50。借助超声波分散仪将其在80℃下分散1h,设置超声频率为12khz。随后,把经收集、烘干后的氧化铝纤维置于球磨罐中,设置转速为50r/min,球磨时间为5min,最后将球磨后的混合物过80目筛网,收集筛下料、烘干得到经第一次球磨分散的氧化铝纤维c。其中,选用的氧化铝纤维长度为210μm,纤维直径为3μm,纤维长径比为70。球磨原料的质量比为氧化铝纤维:球石:酒精=12:20:18,选用球石的粒径为1mm。
[0040]
步骤三:将粉状固体b和氧化铝纤维c送至球磨罐中,设置转速为60r/min、球磨时间为1min,进行第二次球磨;将经第二次球磨混散的混合物过60目筛网,随后收集筛下料并将其烘干,得到分散均匀的纤维/粉体混合物d。其中,先称取质量分数为10%的粉状固体b平铺在球磨罐底部,然后称取质量分数为10%的氧化铝纤维c平铺在粉状固体b表面,交替重复上述流程,直至将粉状固体b、氧化铝纤维c全部送至球磨罐中,球石均匀分布在最上层,之后再进行第二次球磨;球磨过程中控制质量比为粉状固体b:氧化铝纤维c:球石:水=10:2:18:20。筛下料经烘干处理后,控制其含水率为5wt%。
[0041]
步骤四:将纤维/粉体混合物d平铺在成型模具中,借助千吨级压力成型机将其成型为纤维复合陶瓷板坯体,随后将坯体在80℃下干燥20min后送至辊道窑烧成,即可得到基于两步式球磨制备的高强度纤维复合陶瓷板。其中,成型压力为60mpa,最大压力加压时间为20s。纤维复合陶瓷板坯体的长、宽、高分别为850mm、1750mm、2.5mm。辊道窑最高烧成温度为1250℃,烧成周期为20min,最高温度保温时间为10min。
[0042]
实施例2基于两步式球磨制备高强度纤维复合陶瓷板的方法包括以下步骤:
[0043]
步骤一:按照化学成分质量比al2o3:sio2:cao:mgo:tio2:na2o:k2o:la2o3:fe2o3=40:40:5:10:1:1:2:0.2:0.8称取煅烧氧化铝、高岭土、黑滑石、钠长石、高钙熔块、内蒙白云母、韶关球土和膨润土,均匀混合,得到固体混合物a。固体混合物a的烧失为10.0wt%。将固体混合物a置于三辊研磨机中,设置研磨时间为2h、研磨转速为50r/min。随后将经研磨的混合物粉体过250目筛网,收集筛下料并在烘箱中于150℃下干燥12h,得到粉状固体b。
[0044]
步骤二:将氧化铝纤维浸润到聚丙烯酰胺混合溶液中,氧化铝纤维与聚丙烯酰胺混合溶液的用量比为1g:100ml。聚丙烯酰胺混合溶液ph为8.0,组分体积比为聚丙烯酰胺:三聚磷酸钠:氨水=40:20:40。借助超声波分散仪将其在60℃下分散2h,设置超声频率为10khz。随后把经收集、烘干后的氧化铝纤维置于球磨罐中,设置转速为30r/min,球磨时间为8min,最后将球磨后的混合物过80目筛网,收集筛下料、烘干得到经第一次球磨分散的氧化铝纤维c。其中,选用的氧化铝纤维长度为200μm,纤维直径为4μm,纤维长径比为50。球磨原料的质量比为氧化铝纤维:球石:酒精=15:22:20,选用球石的粒径为3mm。
[0045]
步骤三:将粉状固体b和氧化铝纤维c送至球磨罐中,设置转速为80r/min、球磨时间为3min,进行第二次球磨;将经第二次球磨混散的混合物过60目筛网,随后收集筛下料并
将其烘干,得到分散均匀的纤维/粉体混合物d。其中,先称取质量分数为5%的粉状固体b平铺在球磨罐底部,然后称取质量分数为5%的氧化铝纤维c平铺在粉状固体b表面,交替重复上述流程,直至将粉状固体b、氧化铝纤维c全部送至球磨罐中。球磨过程中控制质量比为粉状固体b:氧化铝纤维c:球石:水=15:4:20:30。筛下料经烘干处理后,控制其含水率为10wt%。
[0046]
步骤四:将纤维/粉体混合物d平铺在成型模具中,借助千吨级压力成型机将其成型为纤维复合陶瓷板坯体,随后将坯体在120℃下干燥10min后送至辊道窑烧成,即可得到基于两步式球磨制备的高强度纤维复合陶瓷板。其中,成型压力为80mpa,最大压力加压时间为30s。纤维复合陶瓷板坯体的长、宽、高分别为950mm、1850mm、3.5mm。辊道窑最高烧成温度为1200℃,烧成周期为30min,最高温度保温时间为12min。
[0047]
实施例3基于两步式球磨制备高强度纤维复合陶瓷板的方法包括以下步骤:
[0048]
步骤一:按照化学成分质量比al2o3:sio2:cao:mgo:tio2:na2o:k2o:la2o3:fe2o3=42:38:6:5:3:3:2:0.4:0.6称取煅烧氧化铝、高岭土、黑滑石、钠长石、高钙熔块、内蒙白云母、韶关球土和膨润土,均匀混合,得到固体混合物a。固体混合物a的烧失为8.3wt%。将固体混合物a置于三辊研磨机中,设置研磨时间为2.5h、研磨转速为60r/min。随后将经研磨的混合物粉体过250目筛网,收集筛下料并在烘箱中于170℃下干燥16h,得到粉状固体b。
[0049]
步骤二:将氧化铝纤维浸润到聚丙烯酰胺混合溶液中,氧化铝纤维与聚丙烯酰胺混合溶液的用量比为1g:75ml。聚丙烯酰胺混合溶液ph为7.8,组分体积比为聚丙烯酰胺:三聚磷酸钠:氨水=35:23:42。借助超声波分散仪将其在70℃下分散1.2h,设置超声频率为11khz。随后把经收集、烘干后的氧化铝纤维置于球磨罐中,设置转速为40r/min,球磨时间为7min,最后将球磨后的混合物过80目筛网,收集筛下料、烘干得到经第一次球磨分散的氧化铝纤维c。其中,选用的氧化铝纤维长度为208μm,纤维直径为4μm,纤维长径比为52。球磨原料的质量比为氧化铝纤维:球石:酒精=13:21:19,选用球石的粒径为1.8mm。
[0050]
步骤三:将粉状固体b和氧化铝纤维c送至球磨罐中,设置转速为70r/min、球磨时间为2min,进行第二次球磨;将经第二次球磨混散的混合物过60目筛网,随后收集筛下料并将其烘干,得到分散均匀的纤维/粉体混合物d。其中,先称取质量分数为8%的粉状固体b平铺在球磨罐底部,然后称取质量分数为8%的氧化铝纤维c平铺在粉状固体b表面,交替重复上述流程,直至将粉状固体b、氧化铝纤维c全部送至球磨罐中。球磨过程中控制质量比为粉状固体b:氧化铝纤维c:球石:水=13:3:19:28。筛下料经烘干处理后,控制其含水率为8wt%。
[0051]
步骤四:将纤维/粉体混合物d平铺在成型模具中,借助千吨级压力成型机将其成型为纤维复合陶瓷板坯体,随后将坯体在100℃下干燥16min后送至辊道窑烧成,即可得到基于两步式球磨制备的高强度纤维复合陶瓷板。其中,成型压力为70mpa,最大压力加压时间为26s。纤维复合陶瓷板坯体的长、宽、高分别为880mm、1780mm、2.8mm。辊道窑最高烧成温度为1220℃,烧成周期为26min,最高温度保温时间为11min。
[0052]
对比例1
[0053]
与实施例1基本相同,区别主要在于:步骤一中的固体混合物化学成分不同。
[0054]
步骤一:按照化学成分质量比al2o3:sio2:cao:mgo:tio2:na2o:k2o:la2o3:fe2o3=
65:10:7:6:3:4:4:0.2:0.8称取煅烧氧化铝、高岭土、黑滑石、钠长石、高钙熔块、内蒙白云母、韶关球土和膨润土,均匀混合,烧失为7.6wt%,得到固体混合物a。
[0055]
对比例2
[0056]
与实施例1基本相同,区别主要在于:步骤四中的烧成制度不同。
[0057]
步骤四中辊道窑最高烧成温度为1300℃,烧成周期为80min,最高温度保温时间为25min。
[0058]
对比例3
[0059]
与实施例1基本相同,区别主要在于:未进行步骤二中氧化铝纤维的分散与第一次球磨过程。
[0060]
对比例4制备复合陶瓷板的方法包括以下步骤:
[0061]
步骤一:按照化学成分质量比al2o3:sio2:cao:mgo:tio2:na2o:k2o:la2o3:fe2o3=41:37:6:8:5:5:5:0.5:1.2称取煅烧氧化铝、高岭土、黑滑石、钠长石、高钙熔块、内蒙白云母、韶关球土和膨润土,均匀混合,烧失为6.2wt%,得到固体混合物a。将固体混合物a置于三辊研磨机中,设置研磨时间为2h、研磨转速为78r/min。随后将经研磨的混合物粉体过250目筛网,收集筛下料并在烘箱中于165℃下干燥16h,可得到粉状固体b。
[0062]
步骤二:将粉状固体b送至球磨罐中,设置转速为68r/min、球磨时间为2.5min,然后将其过60目筛网,随后收集筛下料并将其烘干,得到粉体混合物c。球磨过程中控制质量比为粉状固体b:球石:水=13:18:30。筛下料经烘干处理后,控制其含水率为7wt%。
[0063]
步骤三:粉体混合物c平铺在成型模具中,借助千吨级压力成型机将其成型为普通建筑陶瓷板坯体,随后将坯体在100℃下干燥18min后送至辊道窑烧成,即可得到普通建筑陶瓷板样品。其中,成型压力为78mpa,最大压力加压时间为22s。普通建筑陶瓷大板坯体的长、宽、高分别为880mm、1790mm、3.2mm。辊道窑最高烧成温度为1210℃,烧成周期为28min。
[0064]
对比例5
[0065]
与实施例1基本相同,区别主要在于:步骤二中第一次球磨的转速和时间不同。
[0066]
步骤二中设置第一次球磨转速为10r/min,球磨时间为2min。
[0067]
对比例6
[0068]
与实施例1基本相同,区别主要在于:步骤三中第二次球磨的转速和时间不同。
[0069]
步骤三中设置第二次球磨转速为120r/min、球磨时间为10min。
[0070]
表1列举了实施例1-3和对比例1-6的力学性能测试数据。
[0071]
复合陶瓷板在万能拉伸试验机上进行力学实验。吸水率采用常用的煮沸饱和法进行测试。密度采用排液法进行测试。表1实施例和对比例样品的力学性能数据对比
[0072]
图1为实施例1中氧化铝短切纤维原料的扫描电镜测试图。从图1可以看出,氧化铝短切纤维呈团聚的状态,纤维之间相互交联,整体分散性较差。
[0073]
图2为实施例1中纤维/粉体混合物的扫描电镜测试图。从图2可以看出,氧化铝纤维未呈现团聚的形貌,在球磨作用下纤维的分散性得以大大提升,表明两步式分散球磨工艺可以高效率地改善氧化铝纤维的分散性。
[0074]
图3为实施例2中纤维复合陶瓷板的xrd测试图。从图中的衍射峰位置可以看出,样品的主晶相为al2o3、sio2、mgo,伴随有莫来石相在基体中生成。
[0075]
图4为实施例3中纤维复合陶瓷板断面的扫描电镜测试图。从图中可以看出,纤维和基体的界面整体较光滑,未见熔融的孔洞或破碎状纤维结构,表明经优化的高温、快烧的烧结制度可以有效保护纤维和基体的界面,避免纤维在长时间高温下发生结构性蠕变,从而降低增强体、复合体的综合力学性能。此外,基体中原位生长出细纤维状物质,结合图3的xrd分析结果可知,其为莫来石相。表明经合理设计的配方体系,可以诱导内部在高温下生成更多熔融玻璃态物质,进而原位析出纤维状莫来石等增强相,协同al2o3纤维、弥散相增强颗粒共同减缓内部微裂纹尖端的应力集中,延缓内部裂纹扩散速率,提升了材料的综合力学性能。
[0076]
图5为对比例1中纤维复合薄型陶瓷板断面的扫描电镜测试图。对比图4可以看出,对比例1样品的断面结构中无可见纤维状莫来石物质,这说明对比例1的坯料配方设置不能够原位析出纤维状莫来石等内部增强相,仅依靠宏观存在的al2o3纤维、弥散相增强颗粒偏转内部裂纹扩散,无法将受到的外界载荷均匀传递到整个基体,难以全面增强内部微观基体相,因此其增强、增韧的效果有限。该工艺制度下复合材料的弯曲强度仅有74.21mpa,断裂韧性仅为2.35mpa/m2。
[0077]
图6为对比例2中纤维复合陶瓷板断面的扫描电镜测试图。从图6可以看出,纤维和基体的相界面不光滑,尤其是纤维的界面出现了晶粒变大的现象。此外,部分纤维呈破碎的颗粒状,原有的纤维状结构被损坏。表明对比例2中的高温慢烧工艺和长时间保温制度致使
纤维的表面发生了蠕变,破坏了纤维原有的紧密结构,致使纤维变脆、力学性能大幅度降低,难以起到增强基体相的作用。因此,该工艺制度下复合材料的弯曲强度仅有32.14mpa,断裂韧性仅为1.15mpa/m2。
[0078]
图7为对比例3中纤维/粉体混合物的扫描电镜测试图。从图7可以看出,对比例3中,未经两步式球磨工艺的纤维增强体呈团聚状,纤维整体的分散性较差。而团聚的纤维体易致使成型后的坯体内部出现不规则的空隙,即力学结构缺陷,降低了复合材料的密度和综合力学性能。因此,该工艺制度下复合材料的弯曲强度仅有34.11mpa,断裂韧性仅为1.42mpa/m2。
[0079]
图8为对比例5中纤维经第一次球磨后的光学显微镜测试图。从图8可以看出,纤维仍呈明显团聚状态,表明该对比例中纤维第一次球磨工艺设置难以调控其长径比和分散性。而团聚的纤维在基体中会造成力学性能缺陷,不利于提升复合陶瓷板的综合力学性能,其弯曲强度仅有46.38mpa。
[0080]
图9为对比例6中纤维和基体经第二次球磨混合后的扫描电镜测试图。从图9可以看出,纤维原有柱状结构被磨损作用破坏严重。结合表1可知,该对比例中第二次球磨工艺设置形成的失去合理长径比的纤维强韧化效果较差,其弯曲强度仅有50.11mpa。
再多了解一些
本文用于企业家、创业者技术爱好者查询,结果仅供参考。