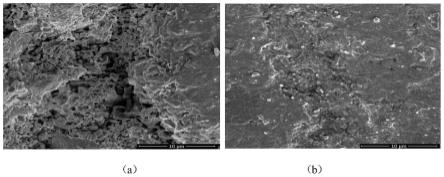
1.本发明属于土木工程施工建筑材料技术领域,具体涉及一种高抗碳化性能绿色铁尾矿混凝土,并进一步公开其制备方法。
背景技术:
2.混凝土作为建筑领域广泛应用的材料,其耐久性一直是重点关注的性能,而在影响混凝土耐久性的诸多因素中,抗碳化性能是其中最重要的一个指标。通常情况下,经浇筑、养护完成后的混凝土,在其内部会形成有微裂缝且多孔隙的结构,空气中二氧化碳通过这些裂缝和孔隙可以很容易的深入至混凝土内部,使混凝土发生碳化,进而导致混凝土的碱性降低,失去对内部钢筋的保护作用,并造成钢筋锈蚀。在建筑或道路工程中,在混凝土结构的使用年限内,因碳化造成钢筋锈蚀,而使建筑物破坏的工程实例数不胜数。
3.传统的提高混凝土抗碳化性能的方式主要是利用粉煤灰作为矿物掺合料,以碎石、河砂作为粗、细骨料来配制混凝土,以粉煤灰作掺合料在一定程度上改善了混凝土的抗碳化性能,但是并不理想。而且,随着混凝土在建筑行业的大规模应用,水泥、河砂、碎石等原材料的需求量成倍增加,使河道采砂、开山碎石的规模增大,破坏山体及河道的生态环境,造成严重的环境污染。另外,多个省市已经发布混凝土行业风险提示,水泥、粉煤灰、砂石等原材料价格都有不同程度的上涨,且这些原材料十分紧缺,不能满足目前混凝土行业的供求量。另有如中国专利cn104446217a等部分方案使用碱激发偏高岭土部分取代粉煤灰作为矿物掺合料配制混凝土,可以一定程度上实现高抗碳化性能,但是却依然不能解决目前粉煤灰、河砂及碎石材料短缺,以及采集河砂及碎石破坏环境的现状。再者,如中国专利cn109748553a中方案采用矿山生产碎石时经振动筛筛分后的残留物取代河砂,通过外加剂使混凝土强度达到c45强度等级,但是并没有寻找粉煤灰和碎石的替代品,依然没有解决粉煤灰、碎石材料紧缺以及由此带来的环境问题,也没有对其抗碳化性能进行研究。可见,如何低成本的实现混凝土的抗碳化性能的优化,依然存在技术难题。
4.目前,铁尾矿在混凝土领域的应用已经有了一定的进展,但仍然主要集中于将铁尾矿单独作为掺合料或细骨料或粗骨料来配制混凝土,综合利用性仍然不理想。因此,本方案尝试基于铁尾矿废弃物制备高抗碳化性能绿色混凝土,既解决混凝土抗碳化性能不足的问题,同时实现铁尾矿废弃物的充分利用。
技术实现要素:
5.为此,本发明所要解决的技术问题在于提供一种强度等级为c30和 c40的高抗碳化性能绿色铁尾矿混凝土,不仅有效降低由于混凝土抗碳化性能较低而造成的建筑物破坏现象的发生,且选择铁尾矿作为混凝土掺合料和粗、细骨料,在实现混凝土高抗碳化性能的同时,充分利用铁尾矿,解决铁尾矿大量堆积导致的可利用土地减少、周围环境污染等问题;
6.本发明所要解决的第二个技术问题在于提供上述高抗碳化性能绿色铁尾矿混凝
土的制备方法。
7.为解决上述技术问题,本发明所述的一种高抗碳化性能绿色铁尾矿混凝土,每立方米所述混凝土的原料包括:水泥290-361kg、铁尾矿粉 124-155kg、铁尾矿砂746-785kg、铁尾矿石1030-1084kg、减水剂2.07-2.58kg、水170kg。
8.具体的,每立方米所述混凝土的原料中,所述水泥和铁尾矿粉的质量比为1:0.43。
9.具体的,所述铁尾矿粉的比表面积450m2/kg-550m2/kg。
10.具体的,所述铁尾矿砂为ⅱ区中砂料。
11.具体的,所述铁尾矿石为5-25mm连续级配。
12.具体的,所述水泥为普通硅酸盐水泥,优选所述水泥为p
·
o 42.5r普通硅酸盐水泥。
13.具体的,所述减水剂为聚羧酸高效减水剂,优选固含量40%、减水率 25%的聚羧酸高效减水剂。
14.本发明还公开了所述高抗碳化性能绿色铁尾矿混凝土的制备方法,包括取选定配比量的所述水泥、铁尾矿粉、铁尾矿砂、铁尾矿石、减水剂和水进行充分混匀搅拌的步骤。
15.本发明还公开了所述高抗碳化性能绿色铁尾矿混凝土在建筑及道路工程领域的应用。
16.本发明所述高抗碳化性能绿色铁尾矿混凝土,以铁尾矿粉作为掺合料部分取代水泥形成胶凝材料,并以铁尾矿砂和铁尾矿石分别作为细骨料和粗骨料,制得混凝土材料不仅强度性能符合标准,且抗碳化性能得到提升。本发明所述混凝土中,所述铁尾矿粉具有较低的火山灰活性,可以使混凝土发生二次水化反应所消耗的ca(oh)2的量较少,制得混凝土的碱度较高,同时借助于铁尾矿粉较好的填充效应,可以使混凝土的密实性得到提高;而且,由于铁尾矿砂、铁尾矿石具有较高的吸水率,可以使周围浆体的水胶比降低,混凝土密实性得到提高,同时借助于铁尾矿砂较小的细度模数和铁尾矿石较低的压碎值指标,均有助于提高混凝土的耐久性。可见,本发明所述混凝土不仅具有较好的的强度性能和抗碳化性能,且可以将铁尾矿废料完全取代河砂、碎石等高成本物料,具有较高的经济价值。
17.本发明所述高抗碳化性能绿色铁尾矿混凝土,优选以铁尾矿粉作为混凝土矿物掺合料取代30%的水泥,铁尾矿砂、铁尾矿石分别完全取代河砂、碎石作为细骨料、粗骨料,制得强度等级为c30、c40的混凝土材料具有较高的抗碳化性能。本发明所述高抗碳化性能绿色铁尾矿混凝土,与同水胶比粉煤灰混凝土相比,c30强度等级铁尾矿混凝土28d抗碳化性能提高了1.27倍、c40强度等级铁尾矿混凝土28d抗碳化性能提高了2.06倍;与同强度等级的粉煤灰混凝土相比,c30强度等级铁尾矿混凝土28d抗碳化性能提高了2.5倍,c40强度等级铁尾矿混凝土28d抗碳化性能提高了4.81 倍。本发明中高抗碳化性能绿色铁尾矿混凝土具有较高的碱含量、较好的密实性,大大提高了混凝土的抗碳化性能。
18.本发明所述混凝土以铁尾矿粉作为掺合料取代水泥形成胶凝材料,并以铁尾矿砂和铁尾矿石分别作为细骨料和粗骨料,所得混凝土材料不仅强度性能完全达标,且抗碳化性能得到较大提高。本发明所述混凝土基于铁尾矿废料为原料,可完全取代传统混凝土材料中使用的河砂和碎石等高成本原料,整个混凝土材料中,铁尾矿废料的使用率可达到90%左右,极大程度的提高了铁尾矿废料的利用率,有效减少了因铁尾矿大量堆积带来的一系列问题,不仅缓解了粉煤灰、河砂及碎石较为缺乏的现状,且有效解决了开采河砂及碎
石带来的环境破坏和污染问题,具有绿色环保的工艺优势。
附图说明
19.为了使本发明的内容更容易被清楚的理解,下面根据本发明的具体实施例并结合附图,对本发明作进一步详细的说明,其中,
20.图1为本发明所述混凝土与现有技术中相同水胶比的粉煤灰混凝土在不同龄期碳化深度的对比结果;其中,图1中(a)为实施例1与对比例1 中混凝土产品的对比结果(水胶比为0.41),图1中(b)为实施例2与对比例3中混凝土产品的对比结果(水胶比为0.33);
21.图2为本发明所述混凝土与现有技术中相同强度等级的粉煤灰混凝土在不同龄期碳化深度的对比结果;其中,图2中(a)为实施例1与对比例 2中混凝土产品的对比结果(强度等级c30),图2中(b)为实施例2与对比例4中混凝土产品的对比结果(强度等级c40);
22.图3为实施例2制备的高抗碳化性能绿色铁尾矿混凝土与对比例3中同水胶比粉煤灰混凝土(水胶比为0.33)在标准养护28d的扫描电镜图;其中,图3中(a)为对比例3产品,图3中(b)为实施例2产品。
具体实施方式
23.为使本发明实施例的目的、技术方案和优点更加清楚,下面将结合本发明实施例,对本发明实施例中的技术方案进行清楚、完整地说明。
24.本发明下述实施例中,选用的原料包括:
25.水泥:普通硅酸盐水泥p
·
o 42.5r水泥,实测28d抗压强度为52.5mpa;
26.所述铁尾矿粉、铁尾矿砂、铁尾矿石均取自河北省迁安市蔡园镇,均为选矿后的工业废渣,经过水洗、筛分后获得;
27.铁尾矿粉:经球磨机粉磨后,其比表面积在450m2/kg-550m2/kg范围内的粉料,本发明方案中,所述铁尾矿粉作为掺合料之用;
28.铁尾矿砂:细度模数为2.4、吸水率为2.36%、ⅱ区中砂,本发明方案中,所述铁尾矿砂作为细骨料之用;
29.铁尾矿石:5-25mm连续级配,压碎指标为6%,吸水率为0.8%,本发明方案中,所述铁尾矿石作为粗骨料之用;
30.减水剂:固含量40%、减水率25%的聚羧酸高效减水剂;
31.水:市政用水。
32.实施例1
33.本实施例所述高抗碳化性能绿色铁尾矿混凝土,每立方米混凝土的原料包括:水泥290kg、铁尾矿粉124kg、铁尾矿砂785kg、铁尾矿石1084kg、减水剂2.07kg、水170kg。上述原料中,水泥与作为掺合料的铁尾矿粉形成凝胶材料(共计414kg),各原料经充分混合搅拌即得所需混凝土。
34.经检测,所述混凝土的强度等级为c30,铁尾矿粉对水泥的取代比例为30%。
35.实施例2
36.本实施例所述高抗碳化性能绿色铁尾矿混凝土,每立方米混凝土的原料包括:水泥361kg、铁尾矿粉155kg、铁尾矿砂746kg、铁尾矿石1030kg、减水剂2.58kg、水170kg。上述
原料中,水泥与作为掺合料的铁尾矿粉形成凝胶材料(共计516kg),各原料经充分混合搅拌即得所需混凝土。
37.经检测,所述混凝土的强度等级为c40,铁尾矿粉对水泥的取代比例为30%。
38.对比例1
39.本对比例所述混凝土的原料及制备方法同实施例1,其区别在于,以粉煤灰替代所述铁尾矿粉,并以河砂、普通碎石分别替代所述铁尾矿砂、铁尾矿石。
40.对比例2
41.本对比例所述混凝土的原料及制备方法同实施例1,其区别仅在于,以粉煤灰替代所述铁尾矿粉,并以河砂、普通碎石分别等量替代所述铁尾矿砂、铁尾矿石,在且控制水泥与粉煤灰的质量比为保持1:0.43的情况下,对水泥和粉煤灰的用量进行同比调整,即在保持水的用量一致的情况下,通过改变体系的水胶比,调整产品的强度值与实施例1方案基本相同,即控制所得混凝土的强度等级为c30。
42.对比例3
43.本对比例所述混凝土的原料及制备方法同实施例2,其区别仅在于,以粉煤灰替代所述铁尾矿粉,并以河砂、普通碎石分别完全取代铁尾矿砂、铁尾矿石。
44.对比例4
45.本对比例所述混凝土的原料及制备方法同实施例2,其区别仅在于,以粉煤灰替代所述铁尾矿粉,并以河砂、普通碎石分别等量替代所述铁尾矿砂、铁尾矿石,在且控制水泥与粉煤灰的质量比为保持1:0.43的情况下,对水泥和粉煤灰的用量进行同比调整,即在保持水的用量一致的情况下,通过改变体系的水胶比,调整产品的强度值与实施例2方案基本相同,即控制所得混凝土的强度等级为c40。
46.实验例
47.将按上述实施例1-2及对比例1-4方案制得的混凝土依据gb/t 50082-2009《普通混凝土长期性能和耐久性能试验方法标准》中快速碳化试验规定,制作若干100mm
×
100mm
×
400mm棱柱体试块,在相对温度20
±
2℃,相对湿度不小于95%的环境中标准养护28d后,在60℃恒温烘干箱内连续烘48h,然后在试块表面涂抹石蜡后放入快速碳化箱,碳化箱内保持温度为 20
±
2℃,相对湿度为70
±
5℃,co2浓度为20
±
3%;到规定龄期(3d、7d、 14d、28d)后,将试块拿出,测其碳化深度,试验结果如下表1及附图1-2 所示。
48.表1碳化试验结果
49.50.由上表中实施例1及对比例1的数据可见,相比于现有技术中同水胶比(0.41:1)的粉煤灰混凝土,本发明制备的高抗碳化性能绿色铁尾矿混凝土的强度等级达到c30,且28d碳化深度降低了21.47%,抗碳化性能提高1.27倍。
51.由上表中实施例1及对比例2的数据可见,相比于现有技术中同强度等级(c30)的粉煤灰混凝土,本发明制备的高抗碳化性能绿色铁尾矿混凝土,28d加速碳化深度降低了60%,抗碳化性能提高了2.5倍。
52.由上表中实施例2及对比例3的数据可见,相比于现有技术中同水胶比(0.33:1)的粉煤灰混凝土,本发明制备的高抗碳化性能绿色铁尾矿混凝土的强度等级达到c40,且28d加速碳化深度降低了50.73%,抗碳化性能提高2.06倍。
53.由上表中实施例2及对比例4的数据可见,相比于现有技术中同强度等级(c40)的粉煤灰混凝土,本发明制备的高抗碳化性能绿色铁尾矿混凝土,28d碳化深度降低了79.24%,抗碳化性能提高了4.81倍。
54.对上述本发明对标准养护28d的强度等级为c40的高抗碳化性能绿色铁尾矿混凝土进行扫描电镜试验,结果如图3所示,试验结果表明,本发明的高抗碳化性能绿色铁尾矿混凝土中孔隙大小及数量均小于对比例方案中相同水胶比的粉煤灰混凝土,证明本发明制备的混凝土的密实性较高。
55.综上,本发明所述混凝土以铁尾矿粉作为掺合料取代水泥形成胶凝材料,并以铁尾矿砂和铁尾矿石分别作为细骨料和粗骨料,所得混凝土材料不仅强度性能完全达标,且抗碳化性能得到较大提高。本发明所述混凝土基于铁尾矿废料为原料,可完全取代传统混凝土材料中使用的河砂和碎石等高成本原料,整个混凝土材料中,铁尾矿废料的使用率可达到90%左右,极大程度的提高了铁尾矿废料的利用率,有效减少了因铁尾矿大量堆积带来的一系列问题,不仅缓解了粉煤灰、河砂及碎石较为缺乏的现状,且有效解决了开采河砂及碎石带来的环境破坏和污染问题,具有绿色环保的工艺优势。
56.以上对本发明实施例进行了详细介绍,本文中应用了具体个例对本发明的原理及实施方式进行了阐述,以上实施例的说明只是用于帮助理解本发明的方法及其核心思想;同时,对于本领域的一般技术人员,依据本发明的思想,在具体实施方式及应用范围上均会有改变之处,综上所述,本说明书内容不应理解为对本发明的限制。
再多了解一些
本文用于企业家、创业者技术爱好者查询,结果仅供参考。