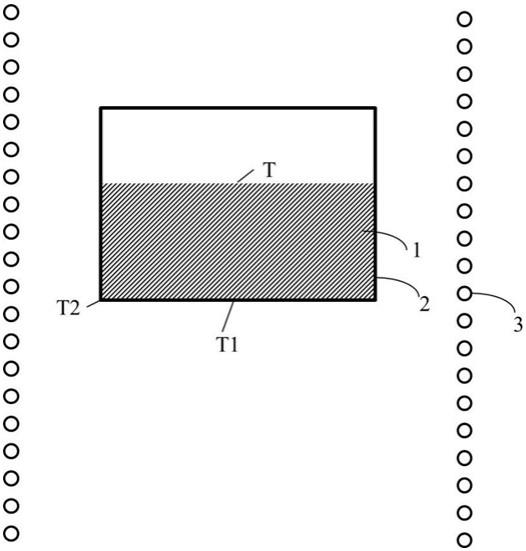
1.本发明涉及半导体单晶材料生长技术,特别是涉及一种改变氧化镓熔体流动性的原料掺杂方法。
背景技术:
2.作为一种超宽禁带半导体(eg~4.9 ev)的β-ga2o3单晶材料,其理论击穿场强可达8 mv/cm,远远超过了gan、sic等材料的极限,并且在相同耐压的情况下,氧化镓基功率器件具有更低的导通电阻,从而拥有更高的功率转换效率和更低的导通损耗,有望应用在飞机、飞船、轨道交通及新能源汽车的电子电力系统中。此外,β-ga2o3单晶衬底也可通过表面氮化,与gan外延层实现晶格零失配,制备高功率led器件。
3.与氮化铝、金刚石等超宽禁带半导体相比,氧化镓可采用熔体法生长,具有尺寸大、成本低的优势。目前国际上生长大尺寸氧化镓单晶的方法主要有导模法、直拉法和垂直布里奇曼法,这几种方法都属于熔体法,也就是说氧化镓原料首先要在坩埚中完全熔化,再进行晶体生长。由于坩埚边缘和中心、坩埚底和顶部处于加热器的不同位置,这几个位置必然存在温差,随着氧化镓晶体尺寸的不断扩大,坩埚直径和高度均在增加,那么坩埚边缘和中心、坩埚底和顶部的温差也会大大增加,采用原有的原料和工艺进行晶体生长,会面临原料熔化不充分、流动性差的问题,而氧化镓原料呈粉末状,其中包含较多气体,熔体流动性差就会导致气泡无法排除,从而影响晶体质量,如果采用原有的原料通过升高功率来使气泡充分排除,就会导致坩埚底部和边缘温度过高,增加铱损耗。
技术实现要素:
4.更大尺寸β-ga2o3晶体生长,必然需要更多的原料和更大的坩埚,此时就会存在一个问题,坩埚各部位温度如图1所示,在2英寸坩埚中,要使坩埚中装填原料的顶部中心位置温度达到氧化镓熔点t,坩埚边缘温度t2≥t 15k,坩埚底部温度t1≥t 10k,这样才能保证坩埚内装填氧化镓原料完全熔化,流动性较好,可以将粉末状原料中的气体在熔融过程中排除,而不会在晶体中形成孔洞。目前氧化镓单晶生长所用坩埚大多为铱金材质,铱在高温有氧环境下会生成iro3并挥发,因此坩埚边缘和底部过热就会增加铱损耗,在2英寸单晶生长过程中,其损耗量约为0.5~1g/炉次。但是当生长4英寸氧化镓单晶时,铱坩埚直径和高度均要扩大2~2.5倍,此时要使坩埚中装填原料的顶部中心位置温度达到氧化镓熔点t,坩埚边缘温度t2≥t 40k,坩埚底部温度t1≥t 30k,这样才能保证坩埚内装填氧化镓原料完全熔化,流动性较好,但是就会造成坩埚边缘和底部过热,这两个位置铱损耗明显增加,经统计损失量约为2.5~3g/炉次。由于铱是一种贵金属,其损耗率的增加会大大增加成本,而且缩短坩埚使用寿命。
5.鉴于现有技术存在的问题,本发明的目的是从氧化镓原料的角度出发,通过掺杂碱金属元素改变氧化镓熔体流动性,使坩埚边缘温度t2≥t 20k,坩埚底部温度t1≥t 15k时,氧化镓原料就可以很好地熔化,将其中的气体排出,坩埚底部和边缘温度降低,在很大
程度上实现降低铱坩埚损耗的目的。
6.本发明采取的技术方案是:一种改变氧化镓熔体流动性的原料掺杂方法有以下步骤:步骤一、 溶解取一定量的ga单质溶于稀盐酸溶液中,形成gacl3溶液。
7.步骤二、掺杂掺杂元素为li、na、k中任意一种,对应的掺杂剂分别为li2co3、na2co3、k2co3中任意一种,按照所述一定量的ga单质的质量计算掺杂剂的质量,将掺杂剂放入所述gacl3溶液中。
8.步骤三、干燥将掺杂好的gacl3溶液进行烘干处理,得到干燥的gacl3固体。
9.步骤四、氧化将干燥好的gacl3固体进行烧结,通入动态氧气使其充分氧化,烧结氧化过程保持10~15h,使所述gacl3固体完全转化为氧化镓。
10.步骤五、破碎将烧结好的氧化镓取出进行球磨,得到粉末状氧化镓原料。
11.步骤一中,所述稀盐酸溶液质量浓度为10%
±
0.5%;所述稀盐酸溶液由浓盐酸溶液与去离子水按照1:2.5~1:2.9的质量比均匀混合而成;所述的浓盐酸溶液的质量浓度为37%。所述浓盐酸溶液与ga单质的质量比为5.5:1~6.5:1。
12.步骤二中,所述掺杂元素的掺杂浓度控制在0.5mol%~1.5mol%之间。
13.步骤三中,所述gacl3溶液进行烘干处理的温度为150~200℃,恒温时间为20~25h。
14.步骤四中,所述动态氧气通入流量为0.5~1l/min。
15.步骤五中,所述粉末状氧化镓原料粒径为2μm~3μm。
16.本发明所产生的有益效果和优点如下:a、采用掺杂li、na、k等碱金属的氧化镓原料进行氧化镓单晶生长,使氧化镓原料完全熔化,且流动性较好,气泡很好地被排除。
17.b、铱坩埚边缘和底部温度明显降低,铱金损耗相比原有工艺减少40%以上,降低了成本,延长了坩埚寿命。
18.c、采用本发明进行氧化镓单晶生长,虽然氧化镓原料中掺杂了碱金属元素,但是该类元素的分凝系数极小,几乎不会进入晶体中,不会影响晶体质量和电学性能。
19.d、降低了坩埚边缘和底部的温度,就相当于降低了单晶炉的使用功率,每炉次节约能源10%。
附图说明
20.图1为熔体法生长氧化镓晶体的坩埚各部位温度示意图。
具体实施方式
21.以下结合附图和实施例对本发明作进一步说明:实施例1:制备500g 1%mol元素na掺杂的氧化镓原料(粉末),纯度为5n,并用氧化
镓原料进行4英寸氧化镓单晶生长。具体步骤如下:a、溶解,首先取372.34g纯度为6.5n的ga单质,然后取纯度为5n的质量浓度为37%的浓盐酸溶液2050g,溶于5200g去离子水中,获得质量浓度为10.46%的稀盐酸溶液;将ga单质放入稀盐酸溶液中,全部溶解得到gacl3溶液。
22.b、掺杂,要获得500g 1mol%元素na掺杂的氧化镓粉末,掺杂剂为na2co3,掺杂量为2.82g,将掺杂剂na2co3放入溶解好的gacl3溶液中。
23.c、干燥,将掺杂好的gacl3溶液升温至200℃进行烘干处理,时间为25h,将其中的水分充分排除,gacl3溶液变为gacl3固体。
24.d、氧化,将干燥好的gacl3固体升温至580℃,以0.5l/min的流量通入动态氧气气氛,保持11h,使gacl3固体完全转化为氧化镓。
25.e、破碎,将烧结的氧化镓取出进行球磨,得到粉末状氧化镓原料,粒径为2μm。
26.f、采用导模法进行4英寸氧化镓晶体生长,加热方式为感应加热,首先将氧化镓原料装入直径为110mm的带有模具的铱金坩埚2中(如图1所示),坩埚底在加热线圈3的中心位置(如图1所示);采用导模法进行实验是因为这种方法需要在坩埚中放置一个带缝的模具,原料熔化后通过毛细力被吸至模具表面,装炉时可以在模具缝上均匀的放置一排氧化镓粉末,更容易观察化料情况。
27.g、抽真空并充入二氧化碳保护气,升温化料,当模具中心的氧化镓原料完全熔化时,即认为得到完全熔融的氧化镓熔体1(如图1所示),此时测量得到模具中心处温度t为2063k,坩埚边缘温度t2约为2085k,坩埚底部温度t1约为2079k。
28.h、引晶,进行晶体生长,生长方向为[010],提拉速率为10mm/h,降温速率为10k/h。
[0029]
i、得到4英寸氧化镓单晶质量良好,强光灯下观测表面无气泡,经加工得到氧化镓晶片在显微镜下观察无孔洞,铱金损耗约1g/炉次,比原有工艺减少50%~60%。
[0030]
实施例2:制备1000g 0.5mol%元素k掺杂的氧化镓原料(粉末),纯度为5n,并用氧化镓原料进行4英寸氧化镓单晶生长。具体步骤如下:a、溶解,首先取744.60g纯度为6.5n的ga单质,然后取纯度为5n的质量浓度为37%的浓盐酸4460g,溶于11600g去离子水中,获得质量浓度为10.28%的稀盐酸溶液;将ga单质放入稀盐酸溶液中,全部溶解得到gacl3溶液。
[0031]
b、掺杂,要获得1000g 0.5%mol元素k掺杂的氧化镓粉末,掺杂剂为k2co3,掺杂量为3.67g,将掺杂剂k2co3放入溶解好的gacl3溶液中。
[0032]
c、干燥,将掺杂好的gacl3溶液升温至200℃进行烘干处理,时间为22h,将其中的水分充分排除,gacl3溶液变为gacl3固体。
[0033]
d、氧化,将干燥好的gacl3固体升温至550℃,以0.8l/min的流量通入动态氧气气氛,保持15h,使gacl3固体完全转化为氧化镓。
[0034]
e、破碎,将烧结的氧化镓取出进行球磨,得到粉末状氧化镓原料,粒径为2.5μm。
[0035]
f、采用导模法进行4英寸氧化镓晶体生长,加热方式为感应加热,首先将氧化镓原料装入直径为110mm的带有模具的铱金坩埚2中(如图1所示),坩埚底在加热线圈3的中心位置(如图1所示);采用导模法进行实验是因为这种方法需要在坩埚中放置一个带缝的模具,原料熔化后通过毛细力被吸至模具表面,装炉时可以在模具缝上均匀的放置一排氧化镓粉末,更容易观察化料情况。
[0036]
g、抽真空并充入二氧化碳保护气,升温化料,当模具中心的氧化镓原料完全熔化时,即认为得到完全熔融的氧化镓熔体1(如图1所示),此时测量得到模具中心处温度t为2062k,坩埚边缘温度t2约为2086k,坩埚底部温度t1约为2079k。
[0037]
h、引晶,进行晶体生长,生长方向为[010],提拉速率为10mm/h,降温速率为10k/h。
[0038]
i、得到4英寸氧化镓单晶质量良好,强光灯下观测表面无气泡,经加工得到氧化镓晶片在显微镜下观察无孔洞,铱金损耗约1.2g/炉次,比原有工艺减少40%~52%。
[0039]
实施例3:制备800g 1.5mol%元素li掺杂的氧化镓原料(粉末),纯度为5n,并用氧化镓原料进行4英寸氧化镓单晶生长。具体步骤如下:a、溶解,首先取595.68g纯度为6.5n的ga单质,然后取纯度为5n的质量浓度为37%的浓盐酸3340g,溶于9350g去离子水中,获得质量浓度为9.74%的稀盐酸溶液;将ga单质放入稀盐酸溶液中,全部溶解得到gacl3溶液。
[0040]
b、掺杂,要获得800g 1.5%mol元素li掺杂的氧化镓粉末,掺杂剂为li2co3,掺杂量为4.72g,将掺杂剂li2co3放入溶解好的gacl3溶液中。
[0041]
c、干燥,将掺杂好的gacl3溶液升温至170℃进行烘干处理,时间为24h,将其中的水分充分排除,gacl3溶液变为gacl3固体。
[0042]
d、氧化,将干燥好的gacl3固体升温至560℃,以0.9l/min的流量通入动态氧气气氛,保持13h,使gacl3固体完全转化为氧化镓。
[0043]
e、破碎,将烧结的氧化镓取出进行球磨,得到粉末状氧化镓原料,粒径为3μm。
[0044]
f、采用导模法进行4英寸氧化镓晶体生长,首先将氧化镓原料装入直径为110mm的带有模具的铱金坩埚2中(如图1所示),坩埚底在加热线圈3的中心位置(如图1所示);采用导模法进行实验是因为这种方法需要在坩埚中放置一个带缝的模具,原料熔化后通过毛细力被吸至模具表面,装炉时可以在模具缝上均匀的放置一排氧化镓粉末,更容易观察化料情况。
[0045]
g、抽真空并充入二氧化碳保护气,升温化料,当模具中心的氧化镓原料完全熔化时,即认为得到完全熔融的氧化镓熔体1(如图1所示),此时测量得到模具中心处温度t为2062k,坩埚边缘温度t2约为2085k,坩埚底部温度t1约为2078k。
[0046]
h、引晶,进行晶体生长,生长方向为[010],提拉速率为10mm/h,降温速率为10k/h。
[0047]
i、得到4英寸氧化镓单晶质量良好,强光灯下观测表面无气泡,经加工得到氧化镓晶片在显微镜下观察无孔洞,铱金损耗约0.9g/炉次,比原有工艺减少64%~70%。
[0048]
本发明在溶解步骤中,稀盐酸溶液是通过质量浓度为37%的浓盐酸溶液与去离子水按照1:2.5~1:2.9的质量比均匀混合稀释得到的,要求ga的纯度不低于6n,盐酸的纯度不低于5n,浓盐酸溶液与ga单质的质量比为5.5.:1~6.5:1,能够保证ga全部溶解成为gacl3且酸不会过量太多。
[0049]
本发明在掺杂步骤中,选择li、na、k这几种碱金属是因为它们可以有效地改善氧化镓熔体的流动性,在氧化镓原料熔化之后流动性增强使得原料中的气体很容易地被排除,这样就可以消除晶体中的孔洞,并且li、na、k元素在氧化镓中的分凝系数小于0.01,几乎不会掺杂到晶体中,也就不会影响晶体质量和电学性能。选择li2co3、na2co3、k2co3是因为该类物质可以与上一步中过量的酸反应,生成二氧化碳气体,不会引入其他杂质。
[0050]
本发明在干燥步骤中,将掺杂好的gacl3溶液进行烘干处理,将其中的水分充分排
除得到干燥的gacl3固体。
[0051]
本发明在氧化步骤中,将干燥好的gacl3固体进行烧结,通入动态氧气使其充分氧化,动态气氛可以随时带走该过程中产生的杂质和气体。
再多了解一些
本文用于企业家、创业者技术爱好者查询,结果仅供参考。